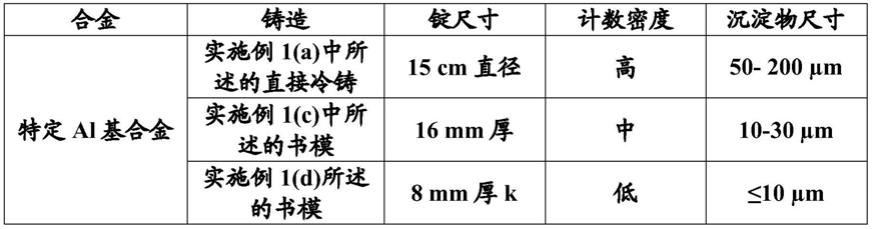
用于包括再熔工艺的应用的具有低沉淀物密度的合金及其制备方法
1.相关应用
2.本技术根据适用法律要求2019年2月7日提交的美国临时申请62/802.498的优先权,出于所有目的,其内容通过引用整体并入本文。
技术领域
3.本技术领域一般涉及铸造合金,特别是具有低沉淀物密度的铸造合金、生产这种具有低沉淀物密度的铸造合金的方法,以及它们在包括再熔或烧结的应用中的用途。
4.发明背景
5.与合金锭的生产相关的一个缺点是在铸造或再固化过程中会形成沉淀物。例如,在四元铝
‑
镁
‑
钪
‑
锆合金锭的正常冷却条件下会形成al3(sc,zr)稳定的沉淀物(或金属间化合物颗粒)。这些沉淀物会在进一步的处理和转变过程中引起复杂化,特别是在锭需要再熔或烧结时。因此,希望使沉淀物的尺寸最小化,使得这些沉淀物在固化过程中可以均匀分布,从而基本上不受与其与静止液相不同的密度(基于质量)相关的沉淀或浮选力的影响。作为进一步转变的实例,铸造合金锭可以再熔,随后雾化和固化以形成金属基粉末。金属基粉末可用于金属增材制造工艺。在这样的实例中,金属基粉末的物理或机械性能会对金属增材制造工艺以及最终的金属产品产生重大影响。因此,合金原料中沉淀物的存在与各种挑战有关。
6.在一个实例中,沉淀物可不均匀地分散在合金锭中,从而产生在锭中从一个位置到另一位置化学物种的不均匀空间分布或组成变化(例如径向变化或轴向变化或其任何组合)。例如,合金锭可表现出各向异性行为,或者可以是方向相关的,或者可以在不同方向具有不同的特性。在另一个实例中,沉淀物可不均匀地分散在合金锭中,导致同一锭批次的等分试样之间化学组成不一致的几何变化。
7.在另一个实例中,沉淀物可包含合金元素(例如,上述al、sc和/或zr),如果在再熔步骤中沉淀物没有完全溶解或熔化,则可以得到这些合金元素在溶体中的较低浓度。换言之,合金的主要α相可能倾向于具有富含未沉淀的合金元素(例如镁)的区域或贫含已沉淀的合金元素(例如铝、钪和/或锆)的区域。
8.在另一个实例中,原料组成的变化会导致后续转化产品(例如,金属粉末,如在金属增材制造工艺中使用的那些)的组成和/或不均匀材料特性的变化。例如,在金属部件的增材制造中使用具有各向异性或不均匀材料特性的粉末原料可能会导致不理想的机械特性、不均匀的层或增加数量的缺陷。
9.作为另一个实例,熔融合金中固体沉淀物的存在也会产生问题,包括但不限于堵塞在再熔步骤中使用的过滤器。这种堵塞会导致熔体中至少一种合金元素的浓度较低,并且会影响任何后续的转变过程或处理。
10.因此,仍然存在许多技术挑战,并且需要克服传统铸造合金及其制备方法的一个或多个缺点的铸造合金及其制造方法。
技术实现要素:11.根据一个方面,本技术涉及一种用于生产用于金属增材制造的金属基粉末的方法,该方法包括:
12.将合金金属前体在其液相线温度以上的温度下熔化,直到所有合金金属前体都处于液态,以产生熔融合金;
13.通过将熔融合金转移到铸机中来铸造熔融合金;
14.将熔融合金以约50℃/s以上的冷却速率冷却至至少固相线温度的温度,以生产具有低沉淀物密度的铸造合金;
15.将具有低沉淀物密度的铸造合金再熔以产生熔融合金;和
16.由该再熔合金形成金属基粉末。
17.在一个实施方案中,冷却熔融合金的温度比固相线温度低至少约70℃以抑制沉淀物的生长速率。
18.在另一个实施方案中,冷却熔融合金的温度为固相线温度的约50%以抑制沉淀物的生长速率。
19.在另一个实施方案中,该方法还包括具有低沉淀物密度的铸造合金的均化步骤,以进一步降低铸造合金中沉淀物的密度。在一个实例中,均化步骤包括在一段时间内将具有低沉淀物密度的铸造合金热处理到温度t。
20.在另一个实施方案中,冷却速率为约50℃/s至约110℃/s,包括端点。
21.在另一个实施方案中,熔融合金的铸造通过直接冷铸、书模铸造(book mold casting)或双辊铸造进行。
22.在另一个实施方案中,再熔以小于约10℃/s的加热速率进行。
23.在另一个实施方案中,再熔以约0.01℃/s至约10℃/s的加热速率进行,包括端点。
24.在另一个实施方案中,由再熔合金形成金属基粉末是通过雾化进行的。
25.根据另一方面,本技术涉及一种生产适合增材制造应用的具有低沉淀物密度的铸造合金的方法,该方法包括:
26.将合金金属前体在其液相线温度以上的温度下熔化,直到所有合金金属前体都处于液态,以产生熔融合金;
27.通过将熔融合金转移到铸机中而铸造熔融合金;
28.将熔融合金以约50℃/s以上的冷却速率冷却至至少固相线温度的温度,以生产具有低沉淀物密度的铸造合金。
29.在一个实施方案中,冷却熔融合金的温度比固相线温度低至少约70℃以抑制沉淀物的生长速率。
30.在另一个实施方案中,冷却熔融合金的温度为固相线温度的约50%以抑制沉淀物的生长速率。
31.在另一个实施方案中,该方法还包括具有低沉淀物密度的铸造合金的均化步骤,以进一步降低铸造合金中沉淀物的密度。在一个实例中,均化步骤包括在一段时间内将具有低沉淀物密度的铸造合金热处理到温度t。
32.在另一个实施方案中,冷却速率为约50℃/s至约110℃/s,包括端点。
33.在另一个实施方案中,熔融合金的铸造通过直接冷铸、书模铸造或双辊铸造进行。
34.根据另一方面,本技术涉及一种生产适合增材制造应用的具有均匀分散的沉淀物的再熔合金的方法,该方法包括:
35.将合金金属前体在其液相线温度以上的温度下熔化,直到所有合金金属前体都处于液态,以产生熔融合金;
36.通过将熔融合金转移到铸机中而铸造熔融合金;
37.以高于约50℃/s的冷却速率将熔融合金冷却至至少固相线温度的温度,以生产具有低沉淀物密度的铸造合金;和
38.将具有低沉淀物密度的铸造合金再熔以产生再熔合金。
39.在一个实施方案中,冷却熔融合金的温度比固相线温度低至少约70℃以抑制沉淀物的生长速率。
40.在另一个实施方案中,冷却熔融合金的温度为固相线温度的约50%以抑制沉淀物的生长速率。
41.在另一个实施方案中,该方法还包括具有低沉淀物密度的铸造合金的均化步骤,以进一步降低铸造合金中沉淀物的密度。在一个实例中,均化步骤包括在一段时间内将具有低沉淀物密度的铸造合金热处理到温度t。
42.在另一个实施方案中,冷却速率为约50℃/s至约110℃/s,包括端点。
43.在另一个实施方案中,熔融合金的铸造通过直接冷铸、书模铸造或双辊铸造进行。
44.在另一个实施方案中,再熔以小于约10℃/s的加热速率进行。
45.在另一个实施方案中,再熔以约0.01℃/s至约10℃/s的加热速率进行,包括端点。
46.根据另一方面,本技术涉及通过本文定义的方法生产的具有低沉淀物密度的铸造合金。
47.在一个实施方案中,铸造合金包含铝(al)和镁(mg)中的至少一种。
48.在另一个实施方案中,铸造合金还包含钪(sc)。
49.在另一个实施方案中,铸造合金还包含锆(zr)。
50.在另一个实施方案中,铸造合金是三元合金或四元合金。
51.在另一个实施方案中,铸造合金中包含的沉淀物包括式al3(sc1‑
x
zr
x
)的al3(sc,zr),其中x为0≤x≤1.0。
52.在另一个实施方案中,沉淀物的平均尺寸小于约50μm。在一个实例中,沉淀物的平均尺寸小于约10μm。在另一个实例中,沉淀物的平均尺寸小于约5μm。
53.在另一个实施方案中,沉淀物基本上均匀地分散在铸造合金中。
54.在另一个实施方案中,铸造合金的化学组成从一个径向位置到另一个径向位置,和/或从一个轴向位置到另一个轴向位置是基本均匀的。
55.在另一个实施方案中,铸造合金的化学组成从一批到另一批是均匀的。
56.根据另一方面,本技术涉及通过本文所定义的方法生产的具有均匀分散的沉淀物的再熔合金。
57.在一个实施方案中,再熔合金包含(al)和镁(mg)中的至少一种。
58.在另一个实施方案中,再熔合金还包含钪(sc)。
59.在另一个实施方案中,再熔合金还包含锆(zr)。
60.在另一个实施方案中,再熔合金是三元合金或四元合金。
61.在另一个实施方案中,再熔合金的化学组成从一个径向位置到另一个径向位置,和/或从一个轴向位置到另一个轴向位置是基本均匀的。
62.在另一个实施方案中,再熔合金的化学组成从一批到另一批是均匀的。
63.根据另一方面,本技术涉及本文所定义的铸造合金在包括后续再熔工艺的应用中的用途。
64.根据另一方面,本技术涉及本文所定义的再熔合金作为金属合金原料在生产适合后续金属增材制造的金属基粉末中的用途。
65.根据又一方面,本技术涉及一种用于生产具有低沉淀物密度的铸造合金的方法,该方法包括以下步骤:
66.将合金金属前体在其液相线温度以上的温度下熔化,直到所有合金金属前体都处于液态,以产生熔融合金;
67.通过将熔融合金转移到铸机中而铸造熔融合金;
68.将熔融合金以高于50℃/s的冷却速率冷却至至少在固相线温度以下的温度,以生产具有低沉淀物密度的铸造合金;和
69.将具有低沉淀物密度的铸造合金再熔。
70.在一个实施方案中,将熔融合金冷却至比固相线温度低至少约70℃的温度以抑制沉淀物的生长。
71.在另一个实施方案中,熔融合金的铸造通过直接冷铸、书模铸造或双辊铸造进行。
72.根据另一方面,本技术涉及通过本文所述方法生产的具有低沉淀物密度的铸造合金。
73.在一个实施方案中,所述合金包含铝(al)和镁(mg)中的至少一种。
74.在另一个实施方案中,所述合金还包含钪(sc)和/或锆(zr)。
75.在另一个实施方案中,沉淀物包含式al3(sc1‑
x
zr
x
)的al3(sc,zr),其中x为0≤x≤1.0。
76.在另一个实施方案中,沉淀物的平均尺寸小于约50μm。
77.在另一个实施方案中,铸造合金的组成在化学组成上从一个位置到另一个位置(例如,径向和轴向)是基本均匀的。
78.在另一个实施方案中,铸造合金的化学组成从一批到另一批是均匀的。
79.在另一个实施方案中,铸造合金用于包括后续再熔工艺的应用中。
80.在另一个实施方案中,铸造合金在用于增材制造的金属合金粉末的生产中用作金属合金原料。
81.附图的简要说明
82.图1是实施例1(a)中所述的13cm直径圆柱形al
‑
mg
‑
sc
‑
zr铸造合金锭的上表面的光学显微照片,放大率为50x。比例尺代表200μm。
83.图2是实施例1(a)中所述的13cm直径圆柱形al
‑
mg
‑
sc
‑
zr铸造合金锭的下表面的光学显微照片,放大率为50x。比例尺代表200μm。
84.图3是实施例1(b)中所述的5cm直径圆柱形al
‑
mg
‑
sc
‑
zr铸造合金锭的上表面的光学显微照片,放大率为50x。比例尺代表200μm。
85.图4是实施例1(b)中所述的5cm直径圆柱形al
‑
mg
‑
sc
‑
zr铸造合金锭的下表面的光
学显微照片,放大率为50x。比例尺代表200μm。
86.图5是展现实施例1(c)中所述的16mm厚al
‑
mg
‑
sc
‑
zr铸造合金锭的上表面的微观结构的光学显微照片,放大率为50x。比例尺代表200μm。
87.图6是展现实施例1(c)中所述的16mm厚al
‑
mg
‑
sc
‑
zr铸造合金锭的下表面的微观结构的光学显微照片,放大率为50x。比例尺代表200μm。
88.图7是展现实施例1(c)中所述的16mm厚al
‑
mg
‑
sc
‑
zr铸造合金锭的下表面的微观结构的光学显微照片,放大率为500x。比例尺代表20μm。
89.图8是展现8mm厚al
‑
mg
‑
sc
‑
zr铸造合金锭的上表面的微观结构的光学显微照片,放大率为50x。比例尺代表200μm。
90.图9是展现8mm厚al
‑
mg
‑
sc
‑
zr铸造合金锭的下表面的微观结构的光学显微照片,放大率为50x。比例尺代表200μm。
91.图10是实施例3中所述的al
‑
mg
‑
sc
‑
zr四元合金的多组分相图。
92.图11显示了图10中所示相图的750℃和600℃之间的部分的放大图,如实施例3中所述。
93.图12是20μm直径al3sc金属间化合物沉淀物在800℃温度下获得的沉淀图,如实施例4所述。
94.图13是20μm直径al3sc金属间化合物沉淀物在900℃温度下获得的沉淀图,如实施例4所述。
95.图14是20μm直径al3sc金属间化合物沉淀物在1000℃温度下获得的沉淀图,如实施例4所述。
96.发明详述
97.以下详细说明和实例是说明性的,不应被解释为进一步限制本发明的范围。相反,它旨在涵盖如本说明书所定义的可包括的所有替代、修改和等同物。通过参考附图阅读以下非限制性描述,本技术的目的、优点和其他特征将变得更加明显和更好理解。
98.当涉及本技术时,本文使用的所有技术和科学术语和表达具有与本领域技术人员通常理解的相同的定义。然而,为了清楚起见,下文提供了在此使用的一些术语和表达的定义。
99.当在本文中使用术语“约”或其等效术语“大约”时,其意思是约或在该区域内和附近。当术语“约”或“大约”用于与数值相关时,它会对其进行修饰;例如,在其标称值上下10%变化。该术语还可以考虑数字的舍入或实验测量中随机误差的概率;例如,由于设备限制。
100.当在此提及值的范围时,除非另有说明,该范围的下限和上限始终包括在定义中。当本技术中提及值的范围时,则旨在包括所有中间范围和子范围以及包括在该范围中的单个值。
101.值得一提的是,在下面的描述中,冠词“一”用于介绍元素时,并不是“只有一个”的意思,而是“一个或多个”的意思。应当理解的是,如果说明书规定步骤、组件、特征或特性时包括“可以”、“可能”或“可”,则不需要包括该特定组件、特征或特性。
102.与根据使用约10
‑3℃/s至约1℃/s的冷却速率的常规方法获得的铸造合金相比,本文所述的各种技术涉及具有低沉淀物密度的铸造合金的生产。
103.为更清楚起见,本文所用的表述“计数密度”或其等效表述“数量密度”是指体积密度或每单位体积的特定物质(例如,沉淀物或颗粒)的数量。或者,本文所用的表述“计数密度”或其等效表述“数量密度”是指表面密度或每单位表面积的特定物质的数量。
104.如本文所用,表述“低沉淀物密度”是指与根据使用约10
‑3℃/s至约1℃/s的冷却速率的常规方法获得的铸造合金相比,沉淀物尺寸减小、沉淀物计数密度降低和沉淀物分散度增加中的至少一种。
105.为更清楚起见,本文所用的表述“沉淀物尺寸减小”是指与根据使用约10
‑3℃/s至约1℃/s的冷却速率的常规方法获得的铸造合金相比,非球形沉淀物的平均沉淀物直径显著减小或平均费雷特直径减小,或针状沉淀物的平均半径和/或半长减小。
106.如本文所用,表述“沉淀物计数密度降低”是指与根据使用约10
‑3℃/s至约1℃/s的冷却速率的常规方法获得的铸造合金相比,每单位表面或单位体积的沉淀物计数减少,或者给定表面或体积内的沉淀物数量减少。
107.如本文所用,表述“沉淀物分散度增加”是指与根据使用约10
‑3℃/s至约1℃/s的冷却速率的常规方法获得的铸造合金相比,沉淀物之间的平均距离增加。例如,当铸造合金不同位置的沉淀物之间的平均距离或数量密度均匀时,可以认为沉淀物是分散的。因此,分散度或分散可以由沉淀物之间的平均距离来定义。
108.工艺和方法实施
109.根据一个方面,本技术涉及一种用于生产具有低沉淀物密度的铸造合金的冷却速率相关工艺。这意味着在铸造或再固化之后,在铸造合金中存在的沉淀物的量,例如al3(sc1‑
x
zr
x
),其中x为0≤x≤1.0,随着再固化或冷却速率的增加而减少。
110.生产具有低沉淀物密度的铸造合金的方法包括将合金金属前体熔化至其液相线温度以上的温度,直到所有合金金属前体都处于它们的液态(即,合金是均质的并且处于平衡的液态),从而产生熔融合金。
111.该方法还包括通过将熔融合金转移到铸机中而铸造熔融合金。任选地,可以通过将熔融合金倒入铸机中来进行铸造。
112.该方法还包括以约50℃/s以上的冷却速率将熔融合金冷却至固相线温度以下,以生产具有低沉淀物密度的铸造合金。
113.在一些实施方案中,铸造和冷却步骤可以顺序地、同时地或在时间上彼此部分重叠地进行。例如,铸造和冷却步骤可以同时进行,或者它们可以在时间上彼此部分重叠。例如,冷却步骤可以在铸造步骤开始后立即进行。
114.在一些实施方案中,可以基于相图上液相线和固相线的延伸以及合金组成来选择冷却速率。在这样的条件下,通过沉淀过程的动力学抑制来减少所述合金中的沉淀,以产生具有低沉淀物密度的铸造合金。在一些实施方案中,本文所述方法的冷却步骤可以在约50℃/s至约110℃/s的冷却速率下进行。例如,冷却步骤可以在约50℃/s至约100℃/s,或约50℃/s至约90℃/s的冷却速率下进行,包括端点。为了比较,工业中常规铸造的标准冷却速率为约10
‑3℃/s至约1℃/s。例如,传统的直接冷铸方法的典型平均冷却速率是约0.1℃/s至约1℃/s。
115.还应注意,本文考虑了任何相容的冷却方法来操作熔融合金的冷却。例如,可以根据其提供本文定义的快速冷却的能力来选择冷却方法。在一些实施方案中,冷却方法可包
括使用淬火剂或冷却介质。例如,冷却方法可包括但不限于制冷剂冷却、液冷、水冷、强制风冷、风水冷等类似的冷却方法。在一些实施方案中,可以根据其与熔融合金的相容性(或不反应的能力)(即,其惰性)来选择冷却方法。例如,熔融合金可以通过非接触式冷却方法固化,例如通过模具。在一个实例中,模具的至少一个外侧可以在冷却介质和熔融合金之间没有直接接触的情况下通过循环冷却介质来冷却。在另一个实例中,非接触式冷却介质可以在模具的外侧和内侧内循环。在一些实施方案中,可以使用二次冷却方法来进一步冷却合金。例如,一旦合金的至少外层固化就可以使用二次冷却方法。任选地,二次冷却方法可以是直接冷却方法,例如直接冷铸。
116.还应该注意的是,任何相容的测量方法都可以用于测量冷却过程中的冷却速率。在一些实施方案中,冷却速率可以是平均冷却速率并且可以通过测量穿过模具的热传递来评估,例如,通过测量从合金到冷却系统(例如,水冷系统)的热传递。例如,可以通过测量从合金到冷却系统的入口或出口的热传递来评估平均冷却速率。在一些实施方案中,冷却速率可以通过使用热分析仪或热量计来获得。例如,热分析仪或热量计可以选自热电偶、差示扫描量热仪、同步热分析仪和其他合适的热分析仪和热量计。在其他实施方案中,可以通过在预定时间记录合金的温度以获得冷却步骤期间的温度
‑
时间测量点来获得冷却速率。例如,冷却速率可以从使用几个温度
‑
时间测量点获得的冷却曲线推导出来。在冷却步骤期间可以使用数据采集系统来监测温度序列。可以在铸造合金的一个或多个位置记录温度
‑
时间测量点。例如,可以在合金的轴心处,或在合金外围的一个或多个位置处,或在合金的轴心处和合金外围的一个或多个位置处记录温度
‑
时间测量点。应当理解,观察到的冷却曲线和/或冷却速率也可以根据各种冷却模型进行分析,例如,可以考虑任何相容的冷却模型或数学冷却模型。
117.应当理解,在液相线温度以上的温度下,合金是均质的并且在平衡状态下是液体。还应理解,在固相线温度以下的温度下,合金在平衡状态下完全是固体。因此,在液相线温度以下的温度下,固化点可以在熔融合金中开始形成和生长。在一些实施方案中,在液相线温度以下的温度下,沉淀物可根据合金金属前体的性质形成和生长。应当理解,主要α相的本体固化(bulk solidification)在固相线温度开始并且生长速率开始降低。例如,沉淀物停止生长的温度取决于合金元素的原子尺寸和基体。事实上,固相线以下的生长是受扩散控制的,在给定温度下的扩散主要受原子尺寸控制。因此,固相线温度主要取决于成分并且取决于合金。
118.例如,对于给定的合金组成,沉淀物(或颗粒)的平均尺寸、它们在铸造合金中的计数密度和分散度中的至少一个可以与用于将熔融合金从液相线温度冷却至至少固相线温度的冷却速率直接相关。这意味着沉淀物(或颗粒)的平均尺寸、它们在铸造合金中的计数密度和分散度或沉淀物的形成中的至少一个可取决于冷却速率。
119.在一些实施方案中,为了减少或抑制沉淀物的形成(沉淀或浮选)并降低沉淀物的生长速率(即沉淀物尺寸的增加),可在固相线温度的约50%的温度下进行熔融合金的冷却。例如,如果特定合金的固相线温度为约650℃,则可以以本文定义的冷却速率将熔融合金冷却至约325℃的温度。例如,熔融合金可以以本文定义的冷却速率从液相线温度以下和低于固相线温度约70℃之间的温度冷却,以抑制沉淀物的生长速率。
120.还应注意的是,可以选择任何合适的铸造方法,只要所选择的铸造方法与本文所
述方法的冷却速率和铸造条件相容。常规铸造方法的非限制性实例包括直接冷铸、书模铸造和双辊铸造。任选地,铸造方法可以是直接冷却。进一步任选地,铸造方法可以是书模铸造。
121.本文所定义的方法的实施使得熔融合金由于高冷却速率而快速固化,同时显著抑制或阻止沉淀物的形成,和/或显著减小沉淀物的粒度,和/或铸造合金中的沉淀物的分散显著增加,和/或沉淀物的计数密度显著降低——这意味着,通过使用本文定义的工艺实施,沉淀物密度可因此降低,与通过常规工艺生产的铸造合金相比。
122.在一些实施方案中,该方法任选进一步包括均化步骤。例如,均化步骤可以包括热处理或老化(例如,受控老化)具有低沉淀物密度的铸造合金,如上所述,至温度t直到总能量足以至少部分溶解沉淀物并生产出比未均化时沉淀物密度更低的铸造合金。例如,沉淀物可以在不超过固相线温度且不完全熔化合金的情况下以固态溶解。均化步骤中的温度t取决于合金的组成。在一些实例中,对于特定合金,温度t可以在400℃以上。例如,温度t可以在450℃以上,或在500℃以上,或在550℃以上,或在600℃以上,或在650℃以上。在一些实例中,对于特定合金,温度t可以为约450℃
‑
约650℃。例如,对于特定合金,温度t可以在650℃以上超过24小时的时间。
123.根据本文所定义的制备方法生产的具有低沉淀物密度的铸造合金可以适用于包括后续再熔工艺的应用中。在一个感兴趣的变型中,根据本文定义的制备方法生产的具有低沉淀物密度的铸造合金适用于进一步的增材制造应用并且有利地用于形成金属基粉末。
124.根据另一方面,提供了一种用于生产适用于增材制造应用的具有均匀分散的沉淀物的再熔合金的方法,该方法包括将本文所述的具有低沉淀物密度的铸造合金再熔以生产再熔合金。在一些实施中,再熔步骤的再熔速率会受到所用熔炉类型的限制。应该注意的是,任何相容类型的熔炉都被考虑在内。例如,从基本为固体的铸造合金开始并使用电阻或感应加热,再熔速率可为约10℃/s以下。任选地,再熔速率可以为约0.01℃/s至约10℃/s。
125.在一些实施方案中,沉淀物可以均匀地分散在铸造合金中,从而产生化学物质在再熔合金中从一个位置到另一个位置的均匀空间分布(例如径向变化或轴向变化或其任何组合)。在另一个实例中,沉淀物可以均匀地分散在铸造合金锭中,从而在来自相同再熔合金批次的等分试样之间具有基本相当的化学组成。
126.具有均匀分散的沉淀物的再熔合金可用作金属合金原料,用于生产适合后续金属增材制造的金属基粉末。如上所述,金属基粉末是金属增材制造的重要部分,因为它们的质量会影响生产过程的稳定性以及最终产品的质量。
127.根据另一方面,提供了一种用于生产用于金属增材制造的金属基粉末的方法,该方法包括根据本文所述的技术形成具有低沉淀物密度的铸造合金,根据本文所述的技术将允许具有低沉淀物密度的铸件再熔以形成再熔合金,以及根据本文所述的技术和本领域技术人员容易理解的本领域可用的其他技术由再熔合金形成金属基粉末。
128.在一些实施方案中,可以根据本领域中可用的方法由再熔合金形成金属基粉末。例如,由再熔合金形成金属基粉末可以通过常规的物理化学方法或常规的机械方法进行。在感兴趣的变型中,由再熔合金形成金属基粉末是通过机械方法进行的,包括但不限于各种类型的研磨工艺和通过气体或液体的高压喷射分散熔体(雾化)。
129.铸造合金实施
130.根据另一方面,本文提供了一种具有低沉淀物密度的铸造合金,其根据本文定义的制备方法生产。
131.在一些实施方案中,铸造合金中沉淀物的尺寸可取决于冷却速率。例如,使用本文所述方法获得的铸造合金中沉淀物的平均尺寸可以小于约50μm。例如,使用本文所述方法获得的铸造合金中沉淀物的平均尺寸可以小于约40μm,或小于约30μm,或小于约20μm,或小于约10μm。例如,使用本文所述方法获得的铸造合金中沉淀物的平均尺寸可以为约5μm至约50μm,或约5μm至约40μm,或约5μm至约30μm,或约5μm至约20μm,约5μm至约10μm,或约10μm至约30μm,或约15μm至约30μm,或约20μm至约30μm,包括端点。
132.出于比较的目的,用常规制备方法和典型冷却速率获得的铸造合金中沉淀物的平均尺寸为约50μm至约200μm。
133.在一些实施方案中,沉淀物的计数密度和分散度也可取决于冷却速率。在一些实例中,使用本文所述方法获得的铸造合金中沉淀物的分散度可以为约20个沉淀物/mm2至约200个沉淀物/mm2。然而,应当理解,沉淀物的计数密度和分散度也可取决于光学显微照片的清晰度和/或放大率,因为可能需要较高的放大率来计数较小的颗粒。在一个实例中,在50x的放大率下,使用本文所述方法获得的铸造合金中沉淀物的分散度可以小于约30个沉淀物/mm2。例如,在50x的放大率下,使用本文所述方法获得的铸造合金中沉淀物的分散度可以为约20
‑
约30个沉淀物/mm2,包括端点。在另一个实例中,在500x的放大率下,使用本文所述方法获得的铸造合金中沉淀物的分散度可高达约600个沉淀物/mm2。因此,必须使用在相同放大率下获得的图像并使用相同的边界条件来比较以不同冷却速率获得的沉淀物的分散度,例如,通过计数具有特定尺寸的沉淀物或通过排除较低和/或较大量级的事件。
134.应注意的是,与通过常规制备方法生产的铸造合金中的沉淀物的尺寸相比,无论使用何种放大率,使用本文所述方法获得的铸造合金中的沉淀物的尺寸都可以减小。
135.在一些实施方案中,本文所述铸造合金可包含铝和镁中的至少一种。例如,铸造合金可以包含铝和镁并且可以是al
‑
mg基合金。例如,铸造合金可包含至少约0.5重量%的镁和至少约93.8重量%的铝。
136.在一些实施方案中,铸造合金可以仅由两种成分组成。或者,铸造合金可包含两种或更多种成分。例如,铸造合金可以是二元、三元或四元合金。
137.在一些实施方案中,铸造合金中可存在至少一种额外合金元素以改进其物理和/或机械性能。例如,该至少一种额外合金元素可以是过渡金属。例如,该额外合金元素可以是钪、锆、另一种类似的过渡金属或其组合。任选地,铸造合金可包含铝、镁、钪和锆。例如,铸造合金可包含约0.001重量%至约0.4重量%的锆、约0.2重量%至约0.8重量%的钪、约0.5重量%至约5.0重量%的镁和约93.8重量%至约99.3重量%的铝。
138.在一些实施方案中,铸造合金可包含式al3(sc1‑
x
zr
x
)的al3(sc,zr)的沉淀物,其中x为0≤x≤1.0。
139.在一些实施方案中,通过本文所述方法制备的铸造合金可基本上不含沉淀物。在一些实施方案中,通过本文所述方法制备的铸造合金可包含尺寸相对于用常规铸造方法制备的沉淀物的尺寸显著减小的沉淀物。例如,在一些实施方案中,沉淀物的尺寸可以小于约50μm。在一些实施方案中,通过本文所述方法制备的铸造合金的特征在于与用常规铸造方法制备的铸造合金相比显著降低的沉淀物计数密度。在一些实施方案中,与用常规铸造方
法制备的铸造合金相比,通过本文所述方法制备的铸造合金的特征在于沉淀物的尺寸和计数密度均降低。
140.在一些实施方案中,沉淀物可基本上均匀分散。更具体地,铸造合金从一个位置到另一个位置(例如,径向和轴向)的组成可以是基本均匀的。例如,径向和/或轴向组成可以在10mm的步长内基本均匀并且可以达到标称组成。这意味着铸造合金的平均整体组成可以在10mm的步长内保持不变。例如,径向和轴向组成可以通过与扫描电子显微镜结合使用的火花光发射光谱、火花原子发射光谱和能量分散x射线光谱中的至少一种来测定。在其他实施方案中,铸造合金可以表现出各向同性行为(即,在所有方向上的均匀性)。在一些实施方案中,铸造合金的化学组成可以从一个批次到另一批次是基本均匀的。
141.在一些实施方案中,沉淀物的尺寸、计数密度和分散度可以从光学显微照片中获得。例如,可以手动或自动测量沉淀物的尺寸、计数密度和分散度。在一个实例中,沉淀物的尺寸、计数密度和分散度可以通过手动沉淀物计数和/或通过手动测量沉淀物的尺寸和沉淀物之间的距离来测量。在一个实例中,沉淀物的尺寸、计数密度和分散度可以通过使用图像分析软件(或图像处理程序)例如fiji
tm
或imagej
tm
自动测量。
142.用途
143.根据另一方面,提供本文所定义的具有低沉淀物密度的铸造合金在包括后续再熔工艺的各种应用中的用途。例如,本文所定义的具有低沉淀物密度的铸造合金可以是后续快速再熔工艺的主题。然而应该注意的是,任何相容的应用都是可以预期的。
144.在一些实施方案中,铸造合金可用于受益于基本上不存在沉淀物或沉淀物密度低的应用。在一些实施方案中,铸造合金可用于需要包含小尺寸沉淀物的合金的应用。在一些实施方案中,铸造合金可用于需要合金的特征在于沉淀物的计数密度基本上小的应用。在一些实施方案中,铸造合金可用于需要包含基本上均匀分散的沉淀物的合金的应用。在一个感兴趣的变型中,本文所定义的具有低沉淀物密度的铸造合金可用作金属原料以制备适合金属增材制造的金属基粉末。例如,本文所定义的具有低沉淀物密度的铸造合金可用于通过再熔形成再熔合金并进一步形成适合金属增材制造的金属基粉末。
145.在一些实施方案中,可以通过使用本文所述方法的实施方案获得具有低沉淀物密度的铸造合金。例如,铸造合金可包含尺寸显著减小的沉淀物。在一些实施方案中,沉淀物的尺寸或平均尺寸可以小于约50μm,或小于约10μm,或小于约5μm。例如,沉淀物的尺寸或平均尺寸可以为约0.5μm至约50μm,包括端点。
146.如上所述,液相线温度是合金在平衡状态下完全为液态的温度,在恒定压力下取决于合金的组成。例如,在铸造合金是al
‑
mg基合金的一些实施方案中,液相线温度可以例如在约620℃以上。例如,液相线温度可以为约620℃至约1100℃,或约620℃至约1000℃,或约620℃至约950℃,或约620℃至约900℃,或约660℃至约850℃,包括端点。
147.如上所述,固相线温度是合金在平衡时完全为固态的温度,并且也取决于合金的组成。例如,在铸造合金是al
‑
mg基合金的一些实施方案中,固相线温度可以例如小于约640℃。例如,固相线温度可以为约640℃至约350℃,或约640℃至约400℃,或约640℃至约450℃,或约640℃至约500℃,包括端点。
实施例
148.以下非限制性实施例是说明性实施方案并且不应被解释为进一步限制本发明的范围。结合附图将更好地理解这些实施例。
149.实施例1:al
‑
mg
‑
sc
‑
zr基铸造合金的表征
150.实施例1(c)和1(d)涉及通过本技术所述方法制备al
‑
mg
‑
sc
‑
zr铸造合金锭,而实施例1(a)和1(b)用于对比。
151.a)冷却速率对圆柱形al
‑
mg
‑
sc
‑
zr铸造合金锭(直径13cm)中沉淀物的存在、计数密度和尺寸的影响(对比)
152.圆柱形al
‑
mg
‑
sc
‑
zr铸造合金锭是通过使用直接冷铸方法固化液态金属合金而制备的。
153.为了生产圆柱形al
‑
mg
‑
sc
‑
zr铸造合金锭,将合金金属前体称重以获得所需的化学计量并混合。在混合之后,然后将合金金属前体加热到液相线温度以上直到所有合金金属前体都处于它们的液态,从而产生熔融合金。然后将熔融合金倒入模具(直径13cm)中,该模具底部有起子
‑
挤压垫(starter
‑
dummy block),其在浇注过程中半连续地向下移动,在底部从模具中取出铸锭。将模具壁的侧面水冷,使金属合金外层固化,冷却速率为约0.1℃/s至约1℃/s。
154.图1是以50x的放大率拍摄的在实施例1(a)中制备的直径为13cm的圆柱形al
‑
mg
‑
sc
‑
zr铸造合金锭的上表面的光学显微照片(比例尺代表200μm)。
155.图2是以50x的放大率拍摄的在实施例1(a)中制备的直径为13cm的圆柱形al
‑
mg
‑
sc
‑
zr铸造合金锭的下表面的光学显微照片(比例尺代表200μm)。
156.图1和图2都显示了al3(sc1‑
x
zr
x
)沉淀物的不均匀分散。通过比较图1和图2可以看出,圆柱形al
‑
mg
‑
sc
‑
zr铸造合金锭的上表面包含比下表面更高的al3(sc1‑
x
zr
x
)沉淀物计数密度,后者冷却得更快。图1中al3(sc1‑
x
zr
x
)沉淀物的平均尺寸也明显大于图2中al3(sc1‑
x
zr
x
)沉淀物的平均尺寸。
157.b)冷却速率对圆柱形al
‑
mg
‑
sc
‑
zr基铸造合金锭(5cm直径)中沉淀物的存在、计数密度和尺寸的影响(对比)
158.圆柱形al
‑
mg
‑
sc
‑
zr铸造合金锭是通过直接冷铸固化液态金属合金制备的。
159.为了生产圆柱形al
‑
mg
‑
sc
‑
zr铸造合金锭,将合金金属前体称重以获得所需的化学计量并混合。混合后,然后将合金金属前体加热到液相线温度直到所有合金金属前体都处于它们的液态,从而产生熔融合金。然后将熔融合金倒入模具(直径5cm)中,该模具在底部具有起子
‑
挤压垫,其在浇注过程中半连续地向下移动,在底部从模具中取出铸锭。将模具外壁水冷,使金属合金外层固化,冷却速率为约10℃/s至约50℃/s。
160.图3是以50x的放大率拍摄的在实施例1(b)中制备的直径为5cm的圆柱形al
‑
mg
‑
sc
‑
zr铸造合金锭的上表面的光学显微照片(比例尺代表200μm)。
161.图4是以50x的放大率拍摄的在实施例1(b)中制备的直径为5cm的圆柱形al
‑
mg
‑
sc
‑
zr铸造合金锭的下表面的光学显微照片(比例尺代表200μm)。
162.图3和图4都显示了al3(sc1‑
x
zr
x
)沉淀物的不均匀分散。与实施例1(a)类似,通过比较图3和图4,可以观察到圆柱形al
‑
mg
‑
sc
‑
zr铸造合金锭的上表面包含比下表面更高的al3(sc1‑
x
zr
x
)沉淀物计数密度,后者冷却得更快。上表面的al3(sc1‑
x
zr
x
)沉淀物的平均尺寸(如
图3所示)也明显大于在下表面上发现的那些(如图4所示)。
163.c)冷却速率对16mm厚的al
‑
mg
‑
sc
‑
zr铸造合金锭板中沉淀物的存在、计数密度和尺寸的影响
164.16mm厚的al
‑
mg
‑
sc
‑
zr铸造合金锭板是通过书模铸造而固化液态金属合金制备的。
165.为了生产16mm厚的al
‑
mg
‑
sc
‑
zr铸造合金锭板,将合金金属前体称重以获得所需的化学计量并混合。混合后,将合金金属前体加热至液相线温度直至所有的合金金属前体都处于它们的液态,从而产生熔融合金。然后将熔融合金倒入书模(尺寸约20cm x约15cm x约16mm深)中。冷却速率为约100℃/s。
166.图5是在50x放大率下拍摄的在实施例1(c)中制备的16mm厚al
‑
mg
‑
sc
‑
zr铸造合金锭的上表面的光学显微照片(比例尺代表200μm)。
167.图6是在50x放大率下拍摄的在实施例1(c)中制备的16mm厚al
‑
mg
‑
sc
‑
zr铸造合金锭的下表面的光学显微照片(比例尺代表200μm)。
168.图3和图4都显示了al3(sc1‑
x
zr
x
)沉淀物的不均匀分散。通过比较图5和图6可以观察到,16mm厚的al
‑
mg
‑
sc
‑
zr铸造合金锭的上表面包含更高的al3(sc1‑
x
zr
x
)沉淀物计数密度。与实施例1(a)和(b)中制备的圆柱形铸造合金锭相比,使用实施例1(c)中所述方法制备的16mm厚al
‑
mg
‑
sc
‑
zr基铸造合金锭看起来具有较低的沉淀物计数密度、改进的分散度和较小尺寸的沉淀物。
169.图7是在500x放大率下拍摄的光学显微照片,显示了实施例1(c)中制备的16mm厚al
‑
mg
‑
sc
‑
zr铸造合金锭的表面微观结构(比例尺代表20μm)。图7显示较大的沉淀物具有小于20μm的尺寸。例如,在这张光学显微照片中,位于左下角的最大沉淀物的宽度为约11μm。
170.d)冷却速率对8mm厚al
‑
mg
‑
sc
‑
zr铸造合金锭板中沉淀物的存在、计数密度和尺寸的影响
171.8mm厚al
‑
mg
‑
sc
‑
zr铸造合金锭板是通过书模铸造而固化液态金属合金制备的。
172.为了生产8mm厚的al
‑
mg
‑
sc
‑
zr合金锭板,将合金金属前体称重以获得所需的化学计量并混合。混合后,将合金金属前体加热至液相线温度直至所有的合金金属前体都处于它们的液态,从而产生熔融合金。然后将熔融合金倒入书模(尺寸约20cm x约15cm x约8mm深)中。冷却速率为约100℃/s。
173.图8是在50x放大率下拍摄的在实施例1(d)中制备的8mm厚al
‑
mg
‑
sc
‑
zr铸造合金锭的上表面的光学显微照片(比例尺代表200μm)。
174.图9是在50x放大率下拍摄的在实施例1(d)中制备的8mm厚al
‑
mg
‑
sc
‑
zr铸造合金锭的下表面的光学显微照片(比例尺代表200μm)。图8和图9都显示了al3(sc1‑
x
zr
x
)沉淀物的不均匀分散。通过比较图8和图9可以看出,8mm厚的al
‑
mg
‑
sc
‑
zr铸造合金锭的上表面包含更高的al3(sc1‑
x
zr
x
)沉淀物计数密度。
175.当与实施例1(a)中制备的圆柱形铸造合金锭和使用实施例1(c)中使用的方法制备的16mm厚铸造合金锭比较时,实施例1(d)中制备的8mm厚的al
‑
mg
‑
sc
‑
zr铸造合金锭板具有较低的沉淀物计数密度、改进的分散度和较小尺寸的沉淀物。因此,较高的冷却速率和较薄的模具会导致较低的沉淀物计数密度。
176.实施例2:al
‑
mg
‑
sc
‑
zr铸造合金锭中的沉淀物和沉淀行为
177.使用实施例1(a)、(c)和(d)中所述方法制备包含al
‑
mg
‑
sc
‑
zr的铸造合金锭。
178.使用实施例1(d)中所述方法获得具有分散的al3(sc,zr)沉淀物和低沉淀物密度的8mm厚合金锭。沉淀物的尺寸比用实施例1(a)和1(c)中所述方法获得的那些小得多(≤10μm)。
179.表1显示了在相同合金组成下使用两种不同的铸造工艺、不同的铸锭厚度和冷却速率获得的结果。
[0180][0181]
与通过常规方法获得的铸造合金相比,使用本文所述方法获得的结果表明所生产的铸造合金中存在的沉淀物的计数密度降低。这可能是由于在本方法中使用了显著更高的冷却速率。因此,较高的冷却速率可能会导致较低的沉淀物密度。
[0182]
使用本方法生产的铸造合金锭非常适用于以下应用或后续加工,包括但不限于涉及铸造合金再熔的应用或后续加工,因为较小的沉淀物(<10μm或<5μm)在再熔步骤中容易溶解,即使在较低温度下且无需搅拌。
[0183]
实施例3:温度对al
‑
mg
‑
sc
‑
zr基铸造合金的影响
[0184]
研究了温度对al
‑
mg
‑
sc
‑
zr铸造合金物理状态的影响。
[0185]
图10显示了al
‑
mg
‑
sc
‑
zr四元合金的多组分相图,图11显示了图10所示相图750℃和600℃之间部分的放大图。
[0186]
图10和图11显示,在图的第一区(1)中,al
‑
mg
‑
sc
‑
zr基合金的所有组分都处于它们的液态。在第二区(2)中可以观察到al3zr的形成。图10和11有效地表明,在合金中锆含量为0.24重量%时,形成了<0.05重量%的al3zr(图(3)上的第三点)。可以看出,这些al3zr颗粒在约100℃在主要α
‑
al
‑
mg相的本体固化开始之前开始形成。此外,al
‑
mg
‑
sc
‑
zr基合金必须再冷却约70℃,以达到一个点,在这个点要考虑固化al
‑
mg基体的一致性程度,以停止任何沉淀(或浮选)以及al3zr金属间化合物的生长。在将铸造合金锭熔化时可能会出现相反的现象。例如,这可能有助于在显著低的温度下溶解al3zr沉淀物(即,不必熔化本体α
‑
al
‑
mg相)以减少沉淀物的存在。它还可能有助于在相同的显著低温下以更短的均化时间溶解al3zr沉淀物。在图10和11中,α
‑
al
‑
mg相由第四区(4)表示,al8mg5的形成发生在图(5)右侧的第五区。
[0187]
实施例4:溶解al
‑
sc基合金的动力学
[0188]
图12
‑
14分别显示了在800℃、900℃和1000℃的温度下获得的20μm直径al3sc金属间化合物沉淀物的沉淀图,如实施例4所述。图12
‑
14有效地证明了20μm直径al3sc金属间化合物沉淀物在三种不同的再熔温度下的溶解速率。溶解速率计算是使用thermo
‑
calc softwaretm获得的。用常规方法获得的较大沉淀物需要更多时间来溶解。
[0189]
在不脱离本发明范围的情况下,可以对上述任何实施方案进行多种修改。本专利申请中提及的任何参考文献、专利或科学文献文件出于所有目的通过引用整体并入本文。