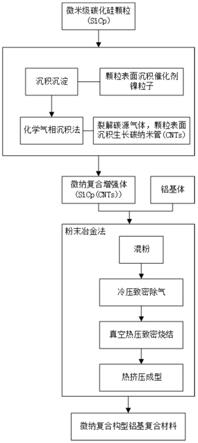
1.本发明涉及颗粒增强铝基复合材料技术领域,特别涉及到一种微纳复合构型铝基复合材料及其制备方法。
背景技术:2.颗粒增强金属基复合材料由于其具有优异的力学性能和物理性能,在空间技术、航空航天、电子封装、汽车工业等高技术领域有很大的应用潜力。现阶段中应用的颗粒增强金属基复合材料,所用的增强相大小基本为微米级,刚性好的脆性相加入到塑性基体后,引起基体内部力学环境的变化,界面处于复杂的三轴应力状态,限制了基体的塑性流变能力,因此,裂纹容易在界面处形成并扩展。如果增强相的尺寸为纳米级,与微米级颗粒相比,由于尺寸上的差别,可以减少两相界面的微区应力集中,基体的加工硬化相对较弱,复合材料可以获得比微米级颗粒增强更好的塑韧性。但是,纳米增强相极易出现团聚现象,在基体中不易分散均匀,使得增强效果不明显,性能远远达不到预期。
3.碳纳米管由于其优异的力学性能和物理性能,成为一种非常重要的复合材料增强相,但由于碳纳米管的纳米尺度效应,在作为增强相时容易团聚,在基体中分散不均,起不到增强相的作用;现阶段多采用的方法是高能球磨法使碳纳米管在基体中均匀的分散开,但是这种方法由于球磨的高能不可避免的造成了碳纳米管结构的损坏,对最后的性能造成影响
技术实现要素:4.为了克服现有技术中存在的缺点和不足,本发明的目的是提供一种微纳复合构型铝基复合材料及其制备方法。
5.本发明的目的通过下述技术方案实现:
6.本发明一方面提供一种微纳复合构型铝基复合材料,该材料包括铝基体和微纳复合增强体(sicp(cnts)),所述微纳复合增强体包括微米级碳化硅颗粒(sicp)和纳米级碳纳米管(cnts)。
7.进一步的,所述微纳复合增强体中的微米级碳化硅颗粒、纳米级碳纳米管与所用的铝基体粉末的质量配比在13:2:85~14.5:0.5:85之间。
8.进一步的,所述的铝基体为纯铝、铝镁铜系、铝镁硅系、铝锌镁铜系中的任意一种。
9.进一步的,所述微米级碳化硅颗粒大小范围在2~50μm之间,纳米级碳纳米管的质量分数在0.5~2wt%之间。
10.本发明另一方面提供一种上述微纳复合构型铝基复合材料的制备方法,其技术原理是:通过在微米级碳化硅表面沉积一层催化剂镍粒子,并在催化粒子的催化下裂解碳源气体,使得碳原子在碳化硅表面沉积生长为碳纳米管。然后通过粉末混粉,使得微纳复合增强体能均匀分散到铝基体中,经过冷压致密除气、真空热压、热挤压等工艺获得致密的块体复合材料。
11.本发明所述制备方法具体包括如下步骤:
12.1)碳化硅颗粒表面原位自生碳纳米管:采用微米级碳化硅颗粒为载体,通过沉积沉淀的方法在颗粒表面制得一层催化剂镍粒子(可通过调节镍颗粒的尺寸(一般50nm以下为宜)及含量(优选5wt%,可根据实际情况选择),来调节碳纳米管的生长状况)。采用化学气相沉积法在颗粒表面催化剂催化裂解的作用下,在碳化硅颗粒表面制得碳纳米管,得到微纳复合增强体;
13.本步骤中可以通过选用尺寸为2~50μm的碳化硅颗粒,并控制催化裂解的反应时间(如在5~60min之间),可得到含不同质量分数(也可转换为体积分数)碳纳米管的微纳复合增强体;而且制得的这种新型微纳复合增强体表面的碳纳米管分布均匀,无相互缠绕,适合作为复合材料的增强相。
14.2)粉末冶金法制备微纳复合构型复合材料:通过混粉,将微纳复合增强体与铝基体粉末混合均匀,进行粉末致密成型得到微纳米颗粒混杂增强的微纳复合构型复合材料。
15.本步骤中,选用的颗粒大小为10~50μm铝基体材料粉末和以尺寸为2~50μm的碳化硅颗粒为载体制备出的微纳复合增强体,以一定质量比或体积比进行混粉(如体积比85:15,可根据实际需要调整)。采用微纳复合增强体的优势在于,由于碳化硅颗粒为微米级,可通过混粉实现碳化硅颗粒在铝基体粉末中的均匀分散,而碳化硅表面的碳纳米管便随着碳化硅颗粒的分散而均匀分散到铝基体中,这使得碳纳米管的易成团问题得到很好的解决;混粉后的复合增强粉末与铝基体粉末进行致密成型得到微纳复合构型铝基复合材料的强韧性,也优于同时外加碳化硅颗粒及碳纳米管所制备的铝基复合材料。
16.进一步的,所述混粉的工艺条件:转速100~200r/min,时间1~8h。
17.进一步的,所述粉末致密成型包括冷压致密除气、真空热压致密烧结和热挤压成型。
18.进一步的,所述冷压致密除气的工艺条件:冷压压力400~800mpa,保压时间5~30min。冷压压力优选600~700mpa,可根据实际条件进行选择。
19.进一步的,所述真空热压致密烧结的工艺条件:真空度为6pa以下,热压温度480~600℃,热压压力200~400mpa。热压温度优选550~580℃,可根据实际条件进行选择,选择合适的真空度可以避免碳纳米管被氧化,合适的热压温度可以获得更加致密的材料。
20.进一步的,所述热挤压成型的工艺条件:挤压温度200~450℃。
21.与现有技术相比,本发明产生的有益效果在于:
22.本发明中,采用原位自生的方法在微米级碳化硅颗粒表面制备一层分散均匀的纳米级碳纳米管,应用微米级碳化硅颗粒作为制备碳纳米管的载体省去载体分离的步骤,同时使碳化硅和碳纳米管作为金属基体增强相,强化效果更好,解决了常规外加法制备碳纳米管增强铝基复合材料中碳纳米管难分散的难题;混粉工艺避免了高能球磨对碳纳米管结构的损伤,保证其结构完整性和强化效果。混杂跨尺度(如从纳米级到微米级)的增强相同时加入到基体中,发挥不同增强相的各自优势,获得综合性能良好的复合材料。铝基体中微纳复合增强体的引入,可以发挥复合增强体中碳化硅颗粒和碳纳米管协同增强的效果,较外加两种增强体的复合材料而言,微纳复合构型铝基复合材料不仅在强度上有所提升,在塑性上也有优势;在微纳复合构型铝基复合材料的制备过程中,制备方法简单可行,可实现大规模的生产。
23.本发明在微米级碳化硅颗粒表面原位自生碳纳米管,不仅实现了微纳复合增强体的制备,而且解决了碳纳米管在金属基复合材料中分散不均、容易团聚的难题;突破传统金属基复合材料的设计理念,提出了碳纳米管/碳化硅复合增强相体的概念,该复合增强体可充分发挥两种增强相的韧化和强化效果,为高性能金属基复合材料的制备提供新的技术原型。
附图说明
24.通过阅读参照以下附图对非限制性实施例所作的详细描述,本发明的其它特征、目的和优点将会变得更明显:
25.图1为本发明微纳复合构型铝基复合材料制备方法的全部工艺流程图;
26.图2为本发明微纳复合构型铝基复合材料制备方法的工艺流程示意图;
27.图3为本发明微纳复合增强体在不同ni含量(wt%)时的扫描电镜图:其中,ni含量分别为:(a)1%、(b)5%、(c)10%、(d)20%;
28.图4为本发明微纳复合增强体的形貌与结构表征:其中(a)为sem图片、(b)为拉曼光谱、(c)为tem图片、(d)为hrtem图片,复合增强体中ni含量为5wt%;
29.图5为本发明微纳复合构型铝基复合材料及同时外加两种增强体的铝基复合材料的金相组织图:其中,(a)为微纳复合构型铝基复合材料,记作sicp(cnt)/al,(b)为同时外加两种增强体的铝基复合材料,记作sicp/cnt/al;二者混粉及复合材料制备工艺完全一致;
30.图6为本发明微纳复合构型铝基复合材料及同时外加两种增强体的铝基复合材料的力学性能对比图:其中(a)为基体材料及复合材料的拉伸应力应变曲线;(b)为al基体及两种复合材料的力学性能对比;
31.图7为本发明微纳复合构型铝基复合材料及同时外加两种增强体的铝基复合材料的断口形貌对比图:其中(a
‑
b)为sicp(cnt)/al断口;(c
‑
d)为sicp/cnt/al断口;
32.图8为本发明微纳复合构型铝基复合材料的扫描电镜照片,其中(a)复合增强体与纯铝粉混合前的扫描电镜照片;(b)复合增强体与纯铝粉混合后的扫描电镜照片。
具体实施方式
33.下面结合附图和具体实施例对本发明进行详细说明。以下实施例将有助于本领域的技术人员进一步理解本发明,但不以任何形式限制本发明。应当指出的是,对本领域的普通技术人员来说,在不脱离本发明构思的前提下,还可以做出若干变形和改进。这些都属于本发明的保护范围。
34.以下实施例中所述的微米级碳化硅颗粒(sicp)均为粉末状绿碳化硅,通过沉积沉淀在其表面制得一层催化剂前驱体,然后通过高温氢气还原,得到生长碳纳米管所需的催化剂颗粒镍粒子。通过化学气相沉积的方法在碳化硅颗粒表面原位自生出分散均匀的纳米级碳纳米管(cnts)得到微纳复合增强体(sicp(cnts)),微纳复合增强体和铝基体通过粉末冶金法制备得到。下表为本发明实施例1~4涉及到的部分工艺条件和效果,实施例1~4的制备流程参照图1和图2所示。
[0035][0036][0037]
实施例1
[0038]
取粒度为5μm表面附有不同含量催化剂的碳化硅粉末,放入石英舟后,置于石英管式炉中,在700℃反应15min,制得的复合增强体图片如图3所示。其中,ni含量为5%时,制得的碳纳米管在复合增强相中的体积分数7%,按复合增强体与al基体粉末体积比为15:85进行混粉,将上述增强相加入到球磨罐中,与10μm的纯al基体粉末混合,得到混合粉末中碳化硅、碳纳米管与所用的基体粉末的体积配比为14.5:0.5:85;然后将混合均匀的粉末加入φ37mm的模具中,在500mpa压力下冷压成型,然后在6pa以下真空状态下580℃,300mpa热压致密,制得的复合材料致密度达到99.5%;进一步复合,将热压后的材料进行热挤压,挤压比22.5,挤压温度300℃,挤压后的样进行常温拉伸实验,复合材料的抗拉强度比纯铝基提高了37%。
[0039]
实施例2
[0040]
取粒度为2.5μm表面附有催化剂的碳化硅粉末,放入石英舟后,置于石英管式炉中,在700℃反应20min,制得的碳纳米管在复合增强相中的体积分数10%,按复合增强体与al基体粉末体积比为15:85进行混粉,将上述增强相加入到球磨罐中,与10μm的纯al基体粉末混合,得到混合粉末中碳化硅、碳纳米管与所用的基体粉末的体积配比为13.5:1.5:85;然后将混合均匀的粉末加入φ37mm的模具中,在700mpa压力下冷压成型,在6pa以下真空状态下580℃,300mpa热压致密,制得的复合材料致密度达到99.2%;进一步复合,将热压后的材料进行热挤压,挤压比22.5,挤压温度300℃,挤压后的样进行常温拉伸实验,复合材料的抗拉强度比纯铝基提高了63%。
[0041]
实施例3
[0042]
取粒度为5μm表面附有催化剂的碳化硅粉末,放入石英舟后,置于石英管式炉中,在700℃反应5min,制得的碳纳米管在复合增强相中的体积分数3%,按复合增强体与基体粉末体积比为15:85进行混粉,将上述增强相加入到球磨罐中,与10μm的6061al合金基体粉混合,得到混合粉末中碳化硅、碳纳米管与所用的基体粉末的体积配比为14.5:0.5:85;然后将混合均匀的粉末加入φ39mm的模具中,在400mpa压力下冷压成型,将冷压坯体放入φ40mm的热压模具中,在6pa以下真空状态下550℃,200mpa热压致密,制得的复合材料致密度达到99.6%;进一步复合,将热压后的材料进行热挤压,挤压比22.5,挤压温度380℃,挤压后的样进行常温拉伸实验,复合材料的抗拉强度比纯铝基提高了27%。
[0043]
实施例4
[0044]
取粒度为13μm表面附有催化剂的碳化硅粉末,放入石英舟后,置于石英管式炉中,在700℃反应30min,制得的碳纳米管在复合增强相中的体积分数13%,按复合增强体与基体粉末体积比为15:85进行混粉,将上述增强相加入到球磨罐中,与10μm的al基体粉混合,得到混合粉末中碳化硅、碳纳米管与所用的铝基体粉末的体积配比为13:2:85;然后将混合均匀的粉末加入φ37mm的模具中,在700mpa压力下冷压成型,在6pa以下真空状态下580℃,400mpa热压致密,制得的复合材料致密度达到99%;进一步复合,将热压后的材料进行热挤压,挤压比22.5,挤压温度300℃,挤压后的样进行常温拉伸实验,复合材料的抗拉强度比纯铝基提高了42%。
[0045]
图4中(a)所示为实施例4的中所制备的复合增强相的扫描电镜照片,从图中可以看到,制备的碳纳米管在碳化硅颗粒表面分布均匀,图8中(b)为复合增强相与纯铝粉混合后的扫描电镜照片,从图中可以看到,经过混粉后,复合增强相基本保持原样,表面的碳纳米管没有脱落;图5为微纳复合构型铝基复合材料及同时外加两种增强体的金相组织图,从图中得知,微纳复合构型铝基复合材料中复合增强体可在基体中均匀分布,而外加的增强体在铝基体中则存在着明显的团聚现象;图7为同时外加两种增强体的金相组织图断口形貌,从图中看出,碳纳米管依附于碳化硅,在复合材料中主要存在于碳化硅与铝的界面出,且与两者结合良好,保证了碳纳米管有较好的增强效果,并且cnts可均匀分散到铝基体中,而外加的cnts则存在明显的团聚现象。图6为本发明微纳复合构型铝基复合材料及同时外加两种增强体的铝基复合材料的力学性能,从图中可知,微纳复合构型复合材料的强韧性均优于外加两种增强体的复合材料,表明复合增强体可以良好的发挥复合增强效果,实现复合材料的强韧化。本发明中其他实施例效果也很好,因此,本发明能够获得碳纳米管分布均匀,且与碳化硅协同增强的铝基复合材料。
[0046]
本发明以铝基复合材料中应用广泛的微米碳化硅颗粒为载体,通过化学气相沉积的方法在其表面原位自生分散均匀的碳纳米管,形成复合增强体
‑
碳纳米管/碳化硅,然后通过粉末冶金的方法,将碳纳米管/碳化硅复合增强体复合到铝基体中。本发明不仅实现了微米/纳米复合增强的目的,还通过微米级碳化硅在铝基体中好分散的特性,使得碳纳米管在碳化硅的帮助下能均匀分散在铝基体中,最终获得性能优异的微纳复合构型铝基复合材料。
[0047]
以上对本发明的具体实施例进行了描述。需要理解的是,本发明并不局限于上述特定实施方式,本领域技术人员可以在权利要求的范围内做出各种变形或修改,这并不影
响本发明的实质内容。