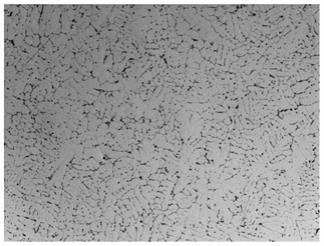
1.本发明属于铝合金技术领域,具体涉及一种废铝再生高强韧铝合金及其制备方法。
背景技术:2.铸造铝合金具有良好的铸造性能、机械加工性能和耐磨性能,广泛应用于汽车、摩托车、电子电器、机械装备等领域。随着汽车轻量化的发展,大量零部件,如汽车转向节、减震塔、悬挂支架、气囊支撑臂、控制臂、制动器卡钳等,都需要“以铝代钢”,已到达汽车轻量化的目的。这些零部件在汽车上都属于安全系统的受力结构件,因此,汽车轻量化的发展对这些铝合金零部件的综合力学性能也要求越来越高,如高的强度和优良的塑性,以提高汽车的安全性和使用寿命。
3.现有铸造铝合金,如adc10、adc12等,虽然具有很好的铸造流动性和机械加工性能,但普遍存在强度偏低、塑性较差的问题,严重制约了铸造铝合金在汽车零部件上的应用。另外,现有铸造铝合金主要以纯铝为主要原材料,在熔炼过程中再加入硅、镁等合金元素来制备,导致铸造铝合金的生产成本高。因此,现有铸造铝合金及其制备生方法仍有待改进和发展。
技术实现要素:4.本发明的目的在于提供一种废铝再生高强韧铝合金,该废铝再生铝合金以废铝为主要原材料,通过优化铝合金的成分组成,提高了铝合金的强度和塑性,并降低了铝合金的生产成本。
5.本发明的目的还在于提供上述废铝再生高强韧铝合金的制备方法,该方法工艺简洁,易于工业化生产。
6.本发明的上述第一个目的可以通过以下技术方案来实现:一种废铝再生高强韧铝合金,由以下质量百分含量的组分组成:si 8.52~8.74%,mg 0.35~0.38%,fe 0.63~0.64%,cr 0.037~0.043%,ti 0.012~0.016%,mn 0.034~0.035%,ni 0.020~0.030%,ba 0.030~0.040%,c 0.004~0.006%,b 0.005~0.010%,余量为al和杂质元素,杂质元素单个含量≤0.05%,总量≤0.15%。
7.所述杂质元素为本领域公知的常规杂质元素。
8.在本发明的废铝再生铝合金的各组分组成中:
9.其中,si是铝合金的主要合金元素,si与al可形成al+si共晶液相,提高铝合金的流动性。si还能与mg可形成mg2si强化相,增强铝合金的强度。另外,当共晶si相呈细小均匀的颗粒状或短纤维状弥散分布在α
‑
al基体上,还能提高铝合金的强度、耐热性能和机械加工性能。
10.mg元素在铝合金中既有固溶强化作用,还能与si形成mg2si强化相,进一步增强铝合金的强度。mg含量越高,铝合金的强度也越高,但mg含量太高也会引起铝合金的塑性下
降。
11.fe是铝合金中不可避免的元素,适量的fe含量可以提高铝合金的脱模性能,有利于铝合金从铸造模具中分离,另外,当富铁相呈细小均匀的颗粒状并弥散分布在铝基体内部时,还能提高铝合金的强度、耐磨和耐热性能。
12.元素cr、ti、mn在铝合金中可以直接固溶进铝基体,增大铝原子间的结合力,减慢铝原子的扩散过程和固溶体的分解速度,提高铝合金强度。cr、ti、mn还能与al形成多种弥散质点并分布在铝基体和晶界上,阻碍晶界、亚晶界的迁移和位错运动,增大铝基体内位错运动的阻力,阻碍高温下晶界的流变,进一步提高铝合金的强度和耐热性能。
13.元素ni和c是以铝镍碳合金的形式加入到铝合金液中,铝镍碳合金中含有大量nic粒子,可以充当α
‑
al铝晶粒的异质形核质点,主要作用是细化α
‑
al铝晶粒,改善流动性和组织均匀性,提高铝合金的强度和塑性。传统铝钛系晶粒细化剂,在铝合金中,其晶粒细化效果会被si“毒化”而失去晶粒细化效果。
14.本申请发明人通过大量的实验研究后发现,铝镍碳合金晶粒细化剂对si的“毒化”有免疫作用,可明显细化铝合金的α
‑
al晶粒组织,改善流动性和组织均匀性,提高强度和塑性。
15.ba元素在铝合金中的作用是细化变质共晶si相。si除了形成mg2si强化相外,大部分的si是以共晶si形式存在铝合金中,当这些共晶si呈通常呈粗大针片状,会严重割裂铝基体,降低铝合金的强度,特别是塑性。通过加入铝钡合金引入元素ba,对共晶si相具有显著的细化变质作用,可使粗大针片状共晶si转变为细小均匀的颗粒状或短纤维状并弥散分布在铝基体上,消除其对塑性的危害,提高铝合金的强度和塑性。
16.b元素在铝合金中的作用主要是细化变质粗大针状富铁相。由于铝合金废料中通常含有较多的杂质元素fe,fe在铝合金中通常以粗大针状feal3、fesial3等粗大针状β
‑
fe富铁相形式存在于铝合金中,这些粗大针状β
‑
fe富铁相为硬脆相,会严重割裂铝基体,成为铝合金断裂的裂纹源和裂纹扩展方向,危害铝合金的强度和塑性。另外,这些针状β
‑
fe富铁相还会与铝基体形成微电偶腐蚀,降低铝合金的耐腐蚀性能。
17.本申请发明人对这个问题进行大量实验探索研究后发现,添加微量的b元素,在合金凝固过程中可吸附在feal3、fesial3等富铁相的生长前沿,抑制β
‑
fe富铁相的按针状生长,最终可使粗大针状β
‑
fe富铁相转变为细小均匀的颗粒状α
‑
fe富铁相,并弥散分布在铝基体内部,可消除粗大针状β
‑
fe富铁相对铝合金强度、塑性和耐腐蚀性能的危害,同时提高铝合金的强度、塑性和耐磨耐热性能。
18.本发明的上述第二个目的可以通过以下技术方案来实现:上述的废铝再生高强韧铝合金的制备方法,包括以下步骤:
19.(1)选取废旧汽车电机壳、废旧摩托车轮毂、废旧船舶铝板、废旧手机外壳、铝镍碳合金、铝钡合金和铝硼合金作为原材料;
20.(2)将废旧汽车电机壳、废旧摩托车轮毂、废旧船舶铝板和废旧手机外壳在740~750℃加热熔化成铝合金液;
21.(3)在铝合金液中加入铝镍碳合金、铝钡合金和铝硼合金进行细化变质处理;
22.(4)用氮气和铝合金精炼剂对细化变质处理后的铝合金液喷吹精炼10~15分钟进行除气除杂处理,扒渣后再静置20~30分钟;
23.(5)将除气除杂处理后的铝合金液在温度为680~690℃条件下铸造成铝合金;
24.(6)将铝合金在430~440℃先加热1~2小时,然后继续升温到520~530℃加热0.5~1小时进行固溶处理,然后淬水冷却至室温;
25.(7)将淬水后的铝合金在80~90℃先加热1~2小时,然后继续升温到185~195℃加热5~6小时进行时效处理,随炉冷却至室温后,得到废铝再生铝合金。
26.优选的,步骤(1)中,以原材料总质量计,所述原材料包含以下质量百分比的各成分:67~68%的废旧汽车电机壳,21~22%的废旧摩托车轮毂,6~7%的废旧船舶铝板,3~4%的废旧手机外壳,0.4~0.6%的铝镍碳合金,0.3~0.4%的铝钡合金,0.1~0.2%的铝硼合金。
27.优选的,所述废旧汽车电机壳的化学成分及质量百分比为:si 8.42%,mg 0.36%,fe 0.72%,余量为al和杂质元素,杂质元素单个含量≤0.05%,总量≤0.15%。
28.所述杂质元素为废旧汽车电机壳领域公知的常规杂质元素。对于废旧汽车电机壳没有什么特别的限定,只要化学成分及质量百分比满足上述要求即可。
29.优选的,所述废旧摩托车轮毂的化学成分及质量百分比为:si 13.71%,mn 0.16%,fe 0.64%,余量为al和杂质元素,杂质元素单个含量≤0.05%,总量≤0.15%。
30.所述杂质元素为废旧摩托车轮毂领域公知的常规杂质元素。对于废旧摩托车轮毂没有什么特别的限定,只要化学成分及质量百分比满足上述要求即可。
31.优选的,所述废旧船舶铝板的化学成分及质量百分比为:mg 0.92%,cr 0.61%,fe 0.17%,余量为al和杂质元素,杂质元素单个含量≤0.05%,总量≤0.15%。
32.所述杂质元素为废旧船舶铝板领域公知的常规杂质元素。对于废旧船舶铝板没有什么特别的限定,只要化学成分及质量百分比满足上述要求即可。
33.优选的,所述废旧手机外壳的化学成分及质量百分比为:mg 1.82%,ti 0.41%,fe 0.11%,余量为al和杂质元素,杂质元素单个含量≤0.05%,总量≤0.15%。
34.所述杂质元素为废旧手机外壳领域公知的常规杂质元素。对于废旧手机外壳没有什么特别的限定,只要化学成分及质量百分比满足上述要求即可。
35.优选的,所述铝镍碳合金的化学成分及质量百分比为:ni 5.02%,c 1.01%,余量为al和杂质元素,杂质元素单个含量≤0.05%,总量≤0.15%。
36.优选的,所述铝钡合金的化学成分及质量百分比为:ba 10.03%,余量为al和杂质元素,杂质元素单个含量≤0.05%,总量≤0.15%。
37.优选的,所述铝硼合金的化学成分及质量百分比为:b 4.95%,余量为al和杂质元素,杂质元素单个含量≤0.05%,总量≤0.15%。
38.铝镍碳合金、铝钡合金、铝硼合金为市售产品,只要能满足上述化学成分及质量百分比即可,杂质元素也是所属领域的公知杂质元素。
39.优选的,步骤(2)中,在对废旧汽车电机壳、废旧摩托车轮毂、废旧船舶铝板、废旧手机外壳进行加热熔化成铝合金液时,为了提高铝合金液成分的均匀性,防止合金元素产生偏析,需要对铝合金液的充分搅拌。
40.优选的,步骤(3)中,加入铝镍碳合金的目的是细化α
‑
al晶粒,改善铝合金的流动性和组织均匀性,提高铝合金的强度和塑性。
41.优选的,步骤(3)中,加入铝钡合金的目的是细化变质粗大的针片状共晶si相,消
除其对塑性和韧性的危害,提高铝合金的强度和塑性。
42.优选的,步骤(3)中,加入铝硼合金的目的是细化变质粗大的针状富铁相,提高铝合金的强度、塑性和耐磨耐蚀性能。
43.优选的,步骤(4)中,所述氮气的纯度为99.99%,所述铝合金精炼剂的用量为原材料总质量的0.5~0.6%。
44.其中铝合金精炼剂为本领域常规使用的铝合金精炼剂。
45.优选的,步骤(4)中,用纯度99.99%的氮气和占原材料总重量0.5~0.6%的铝合金精炼剂对铝合金液喷吹精炼10~15分钟,扒渣后再静置20~30分钟,目的是除去铝合金液中的气体和夹杂物,消除气孔和夹杂物对铝合金性能的危害,提高铝合金的强度、塑性和耐腐蚀性能。
46.优选的,步骤(5)中,合理的铸造工艺是保证铸造成型的关键,温度太低,会导致无法铸造成型,无法获得致密的铝合金,会严重降低铝合金的力学性能。发明人经过大量的实验研究后发现,在温度为680~690℃条件下,可以铸造成型内部致密的铝合金,确保铝合金获得优良的力学性能。
47.优选的,步骤(6)中,固溶处理的目的是使铝合金中合金元素和过剩相充分溶解进入铝基体,然后通过淬水方式快速冷却,以得到过饱和固溶体。
48.本申请发明人经过大量的实验研究后发现,将本发明铝合金在430~440℃先加热1~2小时,然后升温到520~530℃继续加热0.5~1小时进行固溶处理,可使合金元素和过剩相充分溶解进入铝基体,得到过饱和固溶体,有利于时效后获得废铝再生高强韧铝合金。
49.优选的,步骤(7)中,时效是提高铝合金力学性能的重要手段。
50.本申请发明人通过大量实验研究后发现,采用双级时效工艺,即将淬水后的铝合金在80~90℃先加热1~2小时,然后继续升温到185~195℃加热5~6小时进行时效处理,随炉冷却至室温,可获得高强度、高塑性和优良耐磨耐蚀性能的铝合金,即高强韧铝合金。
51.与现有技术相比,本发明具有如下有益效果:
52.(1)本发明通过优化铝合金的成分组成,添加少量的铝镍碳合金、铝钡合金和铝硼合金进行细化变质处理,使元素之间相互配合产生固溶强化、析出强化和弥散相强化,消除粗大针片状共晶si相和富fe相对铝合金强度和塑性的危害,显著提高了铝合金的强度和塑性;
53.(2)本发明以铝合金废料为主要原材料,通过优化设计铝合金废料的组成,充分利用铝合金废料中含有的硅、镁等金属元素,直接制备强韧铝合金,既没有使用纯铝,也没有额外添加硅、镁等金属元素,可显著降低铝合金的生产成本,同时也节约了大量宝贵的金属资源;
54.(3)本发明铝合金的抗拉强度≥390mpa,屈服强度≥360mpa,断后伸长率≥14%,具有强度高、塑性好的优点,可以铸造成型各种对强度和塑性要求较高的受力结构件,具有广阔的市场应用前景。
附图说明
55.图1为实施例1铝合金的光学显微镜组织;
56.图2为实施例1铝合金的扫描电镜显微组织;
57.图3为对比例1铝合金的光学显微镜组织;
58.图4为对比例2铝合金的扫描电镜显微组织;
59.图5为对比例3铝合金的扫描电镜显微组织。
具体实施方式
60.下面将结合附图和本发明实施例,对本发明实施例中的技术方案进行清楚、完整地描述,显然,所描述的实施例仅仅是本发明实施例的一部分,而不是全部的实施例。基于本发明中的实施例,本领域普通技术人员在没有作出创造性劳动前提下所获得的所有其他实施例,都属于本发明保护的范围。以下所采用的原料,如无特殊说明,均为市售产品。
61.以下实施例和对比例所用原材料的化学成分及质量百分比如下:
62.废旧汽车电机壳的化学成分及质量百分比为:si 8.42%,mg 0.36%,fe 0.72%,余量为al和杂质元素,杂质元素单个含量≤0.05%,总量≤0.15%。
63.废旧摩托车轮毂的化学成分及质量百分比为:si 13.71%,mn 0.16%,fe 0.64%,余量为al和杂质元素,杂质元素单个含量≤0.05%,总量≤0.15%。
64.废旧船舶铝板的化学成分及质量百分比为:mg 0.92%,cr 0.61%,fe 0.17%,余量为al和杂质元素,杂质元素单个含量≤0.05%,总量≤0.15%。
65.废旧手机外壳的化学成分及质量百分比为:mg 1.82%,ti 0.41%,fe 0.11%,余量为al和杂质元素,杂质元素单个含量≤0.05%,总量≤0.15%。
66.铝镍碳合金的化学成分及质量百分比为:ni 5.02%,c 1.01%,余量为al和杂质元素,杂质元素单个含量≤0.05%,总量≤0.15%。
67.铝钡合金的化学成分及质量百分比为:ba 10.03%,余量为al和杂质元素,杂质元素单个含量≤0.05%,总量≤0.15%。
68.铝硼合金的化学成分及质量百分比为:b 4.95%,余量为al和杂质元素,杂质元素单个含量≤0.05%,总量≤0.15%。
69.实施例1
70.铝合金由以下质量百分比的成分组成:si 8.74%,mg 0.36%,fe 0.64%,cr 0.037%,ti 0.013%,mn 0.035%,ni 0.020%,ba 0.030%,c 0.004%,b 0.005%,余量为al和杂质元素,杂质元素单个含量≤0.05%,总量≤0.15%。
71.该铝合金的废铝再生方法,依次包括以下步骤:
72.(1)选取废旧汽车电机壳、废旧摩托车轮毂、废旧船舶铝板、废旧手机外壳、铝镍碳合金、铝钡合金和铝硼合金作为原材料;
73.(2)将占原材料总重量68%的废旧汽车电机壳、22%的废旧摩托车轮毂、6%的废旧船舶铝板和3.2%的废旧手机外壳在740℃加热熔化成铝合金液;
74.(3)在铝合金液中加入占原材料总重量0.4%的铝镍碳合金、0.3%的铝钡合金和0.1%的铝硼合金进行细化变质处理;
75.(4)用纯度99.99%的氮气和占原材料总重量0.5%的铝合金精炼剂(本领域常规铝合金精炼剂均可)对铝合金液喷吹精炼10分钟进行除气除杂处理,扒渣后再静置20分钟;
76.(5)将除气除杂处理后的铝合金液在温度为680℃条件下铸造成铝合金;
77.(6)将铝合金在440℃先加热1小时,然后继续升温到530℃加热0.5小时进行固溶
处理,然后淬水冷却至室温;
78.(7)将淬水后的铝合金在90℃先加热1小时,然后继续升温到185℃加热6小时进行时效处理,随炉冷却至室温,得到所述铝合金。
79.实施例2
80.铝合金由以下质量百分比的成分组成:si 8.52%,mg 0.37%,fe 0.63%,cr 0.043%,ti 0.016%,mn 0.034%,ni 0.030%,ba 0.040%,c 0.006%,b 0.010%,余量为al和杂质元素,杂质元素单个含量≤0.05%,总量≤0.15%。
81.该铝合金的废铝再生方法,依次包括以下步骤:
82.(1)选取废旧汽车电机壳、废旧摩托车轮毂、废旧船舶铝板、废旧手机外壳、铝镍碳合金、铝钡合金和铝硼合金作为原材料;
83.(2)将占原材料总重量67%的废旧汽车电机壳、21%的废旧摩托车轮毂、7%的废旧船舶铝板和3.8%的废旧手机外壳在750℃加热熔化成铝合金液;
84.(3)在铝合金液中加入占原材料总重量0.6%的铝镍碳合金、0.4%的铝钡合金和0.2%的铝硼合金进行细化变质处理;
85.(4)用纯度99.99%的氮气和占原材料总重量0.6%的铝合金精炼剂对铝合金液喷吹精炼15分钟进行除气除杂处理,扒渣后再静置30分钟;
86.(5)将除气除杂处理后的铝合金液在温度为690℃条件下铸造成铝合金;
87.(6)将铝合金在430℃先加热2小时,然后继续升温到520℃加热1小时进行固溶处理,然后淬水冷却至室温;
88.(7)将淬水后的铝合金在80℃先加热2小时,然后继续升温到195℃加热5小时进行时效处理,随炉冷却至室温后,得到所述铝合金。
89.实施例3
90.铝合金由以下质量百分比的成分组成:si 8.74%,mg 0.35%,fe 0.64%,cr 0.037%,ti 0.012%,mn 0.035%,ni 0.025%,ba 0.035%,c 0.005%,b 0.007%,余量为al和杂质元素,杂质元素单个含量≤0.05%,总量≤0.15%。
91.该铝合金的废铝再生方法,依次包括以下步骤:
92.(1)选取废旧汽车电机壳、废旧摩托车轮毂、废旧船舶铝板、废旧手机外壳、铝镍碳合金、铝钡合金和铝硼合金作为原材料;
93.(2)将占原材料总重量68%的废旧汽车电机壳、22%的废旧摩托车轮毂、6%的废旧船舶铝板和3%的废旧手机外壳在745℃加热熔化成铝合金液;
94.(3)在铝合金液中加入占原材料总重量0.5%的铝镍碳合金、0.35%的铝钡合金和0.15%的铝硼合金进行细化变质处理;
95.(4)用纯度99.99%的氮气和占原材料总重量0.55%的铝合金精炼剂对铝合金液喷吹精炼12分钟进行除气除杂处理,扒渣后再静置25分钟;
96.(5)将除气除杂处理后的铝合金液在温度为685℃条件下铸造成铝合金;
97.(6)将铝合金在435℃先加热1.5小时,然后继续升温到525℃加热0.8小时进行固溶处理,然后淬水冷却至室温;
98.(7)将淬水后的铝合金在85℃先加热1.5小时,然后继续升温到190℃加热5.5小时进行时效处理,随炉冷却至室温后,得到所述铝合金。
99.实施例4
100.铝合金由以下质量百分比的成分组成:si 8.52%,mg 0.38%,fe 0.63%,cr 0.043%,ti 0.016%,mn 0.034%,ni 0.020%,ba 0.040%,c 0.004%,b 0.010%,余量为al和杂质元素,杂质元素单个含量≤0.05%,总量≤0.15%。
101.该铝合金的废铝再生方法,依次包括以下步骤:
102.(1)选取废旧汽车电机壳、废旧摩托车轮毂、废旧船舶铝板、废旧手机外壳、铝镍碳合金、铝钡合金和铝硼合金作为原材料;
103.(2)将占原材料总重量67%的废旧汽车电机壳、21%的废旧摩托车轮毂、7%的废旧船舶铝板和4%的废旧手机外壳在740℃加热熔化成铝合金液;
104.(3)在铝合金液中加入占原材料总重量0.4%的铝镍碳合金、0.4%的铝钡合金和0.2%的铝硼合金进行细化变质处理;
105.(4)用纯度99.99%的氮气和占原材料总重量0.6%的铝合金精炼剂对铝合金液喷吹精炼10分钟进行除气除杂处理,扒渣后再静置30分钟;
106.(5)将除气除杂处理后的铝合金液在温度为690℃条件下铸造成铝合金;
107.(6)将铝合金在430℃先加热2小时,然后继续升温到530℃加热1小时进行固溶处理,然后淬水冷却至室温;
108.(7)将淬水后的铝合金在90℃先加热2小时,然后继续升温到185℃加热6小时进行时效处理,随炉冷却至室温后,得到所述铝合金。
109.对比例1
110.铝合金由以下质量百分比的成分组成:si 8.70%,mg 0.37%,fe 0.64%,cr 0.037%,ti 0.016%,mn 0.035%,ba 0.030%,b 0.010%,余量为al和杂质元素,杂质元素单个含量≤0.05%,总量≤0.15%。
111.该铝合金的废铝再生方法,依次包括以下步骤:
112.(1)选取废旧汽车电机壳、废旧摩托车轮毂、废旧船舶铝板、废旧手机外壳、铝钡合金和铝硼合金作为原材料;
113.(2)将占原材料总重量67.5%的废旧汽车电机壳、22%的废旧摩托车轮毂、6%的废旧船舶铝板和4%的废旧手机外壳在750℃加热熔化成铝合金液;
114.(3)在铝合金液中加入占原材料总重量0.3%的铝钡合金和0.2%的铝硼合金进行细化变质处理;
115.(4)用纯度99.99%的氮气和占原材料总重量0.6%的铝合金精炼剂对铝合金液喷吹精炼15分钟进行除气除杂处理,扒渣后再静置30分钟;
116.(5)将除气除杂处理后的铝合金液在温度为690℃条件下铸造成铝合金;
117.(6)将铝合金在440℃先加热1小时,然后继续升温到530℃加热0.5小时进行固溶处理,然后淬水冷却至室温;
118.(7)将淬水后的铝合金在90℃先加热1小时,然后继续升温到195℃加热5小时进行时效处理,随炉冷却至室温后,得到所述铝合金。
119.对比例2
120.铝合金由以下质量百分比的成分组成:si 8.56%,mg 0.38%,fe 0.64%,cr 0.043%,ti 0.016%,mn 0.034%,ni 0.030%,c 0.006%,b 0.005%,余量为al和杂质元
素,杂质元素单个含量≤0.05%,总量≤0.15%。
121.该铝合金的废铝再生方法,依次包括以下步骤:
122.(1)选取废旧汽车电机壳、废旧摩托车轮毂、废旧船舶铝板、废旧手机外壳、铝镍碳合金和铝硼合金作为原材料;
123.(2)将占原材料总重量67%的废旧汽车电机壳、21.3%的废旧摩托车轮毂、7%的废旧船舶铝板和4%的废旧手机外壳在745℃加热熔化成铝合金液;
124.(3)在铝合金液中加入占原材料总重量0.6%的铝镍碳合金和0.1%的铝硼合金进行细化变质处理;
125.(4)用纯度99.99%的氮气和占原材料总重量0.55%的铝合金精炼剂对铝合金液喷吹精炼13分钟进行除气除杂处理,扒渣后再静置28分钟;
126.(5)将除气除杂处理后的铝合金液在温度为682℃条件下铸造成铝合金;
127.(6)将铝合金在432℃先加热1.3小时,然后继续升温到527℃加热0.9小时进行固溶处理,然后淬水冷却至室温;
128.(7)将淬水后的铝合金在82℃先加热1.4小时,然后继续升温到189℃加热5.5小时进行时效处理,随炉冷却至室温后,得到所述铝合金。
129.对比例3
130.铝合金由以下质量百分比的成分组成:si 8.74%,mg 0.36%,fe 0.64%,cr 0.037%,ti 0.013%,mn 0.035%,ni 0.020%,ba 0.040%,c 0.004%,余量为al和杂质元素,杂质元素单个含量≤0.05%,总量≤0.15%。
131.该铝合金的废铝再生方法,依次包括以下步骤:
132.(1)选取废旧汽车电机壳、废旧摩托车轮毂、废旧船舶铝板、废旧手机外壳、铝镍碳合金和铝钡合金和作为原材料;
133.(2)将占原材料总重量68%的废旧汽车电机壳、22%的废旧摩托车轮毂、6%的废旧船舶铝板和3.2%的废旧手机外壳在740℃加热熔化成铝合金液;
134.(3)在铝合金液中加入占原材料总重量0.4%的铝镍碳合金和0.4%的铝钡合金进行细化变质处理;
135.(4)用纯度99.99%的氮气和占原材料总重量0.5%的铝合金精炼剂对铝合金液喷吹精炼10分钟进行除气除杂处理,扒渣后再静置20分钟;
136.(5)将除气除杂处理后的铝合金液在温度为680℃条件下铸造成铝合金;
137.(6)将铝合金在440℃先加热1小时,然后继续升温到530℃加热0.5小时进行固溶处理,然后淬水冷却至室温;
138.(7)将淬水后的铝合金在90℃先加热1小时,然后继续升温到185℃加热6小时进行时效处理,随炉冷却至室温后,得到所述铝合金。
139.验证例
140.将实施例1
‑
4和对比例1
‑
3的铝合金在arl
‑
4600型光电直读光谱仪上进行化学成分分析,分析结果如表1所示。
141.表1实施例1
‑
4和对比例1
‑
3铝合金的成分组成(质量百分比,%)
[0142][0143][0144]
按国家标准gb/t16865
‑
2013,将实施例1
‑
4和对比例1
‑
3的铝合金加工成标准拉伸试样,在dns200型电子拉伸试验机上进行室温拉伸,拉伸速度为2mm/min,检测铝合金的抗拉强度、屈服强度和断后伸长率,检测结果如表2所示。
[0145]
表2实施例1
‑
4和对比例1
‑
3铝合金的室温拉伸力学性能
[0146] 抗拉强度/mpa屈服强度/mpa断后伸长率/%实施例1398.5364.816.5实施例2408.1376.914.5实施例3391.8368.415.3实施例4414.9381.714.1对比例1349.4315.812.5对比例2356.7320.611.3对比例3339.8309.210.8
[0147]
从表2可看到,实施例1
‑
4的铝合金的抗拉强度≥390mpa,屈服强度≥360mpa,断后伸长率≥14%。
[0148]
对比例1的铝合金由于没有添加铝镍碳合金进行晶粒细化,对比例2的铝合金由于没有添加铝钡合金对共晶si相进行细化变质,对比例3的铝合金由于没有添加铝硼合金对富铁相进行细化变质,使对比例1
‑
3的铝合金的抗拉强度低于390mpa,屈服强度低于360mpa,断后伸长率低于14%。
[0149]
通过表2的数据比较可以看到,本发明通过科学优化设计铝合金废料的组成,并添加少量铝镍碳合金、铝钡合金和铝硼合金进行细化变质处理,显著提高了铝合金的强度和塑性,制备的铝合金具有优异的力学性能。
[0150]
在实施例1和对比例1
‑
3的铝合金上分别取样,试样经磨制、抛光和腐蚀后,在leik
‑
dmi3000m型光学显微镜上进行组织观察,在wrnm
‑
jb2000型扫描电镜上进行观察。
[0151]
图1为实施例1铝合金的光学显微镜组织,从图1可看到,通过添加少量铝镍碳合金进行晶粒细化,铝合金的显微组织为细小的α
‑
al树枝晶。
[0152]
图2为实施例1铝合金的扫描电镜显微组织,从图2可看到,通过添加少量铝钡合金和铝硼合金进行细化变质处理,铝合金的显微组织为细小均匀的共晶si相和富fe相。
[0153]
图3为对比例1铝合金的光学显微镜组织,从图3可看到,由于对比例1未添加铝镍碳合金进行晶粒细化,铝合金的显微组织为粗大的α
‑
al树枝晶。
[0154]
图4和图5分别为对比例2和对比例3铝合金的扫描电镜显微组织,从图4和图5可看到,由于对比例2和对比例3分别未添加铝钡合金和铝硼合金进行细化变质处理,铝合金内部为粗大针片状的共晶si相和富fe相。
[0155]
以上具体实施方式部分对本发明所涉及的分析方法进行了具体的介绍。应当注意的是,上述介绍仅是为了帮助本领域技术人员更好地理解本发明的方法及思路,而不是对相关内容的限制。在不脱离本发明原理的情况下,本领域技术人员还可以对本发明进行适当的调整或修改,上述调整和修改也应当属于本发明的保护范围。