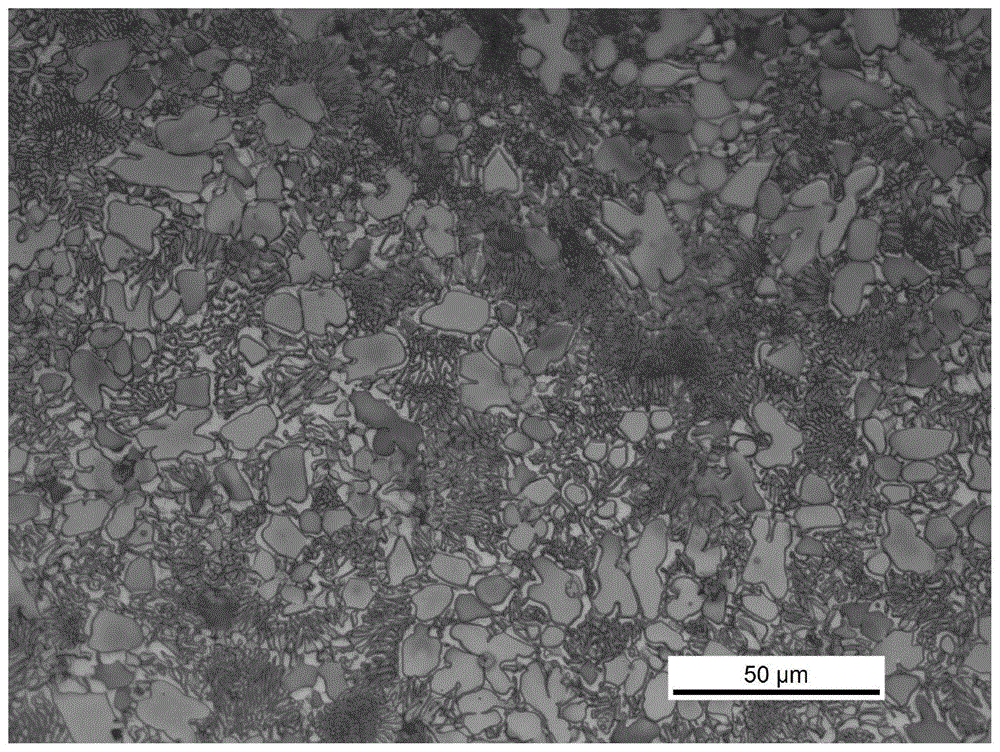
本发明涉及导电铝合金加工制备
技术领域:
,特别涉及一种高强度铝镁硅钙导电铝合金及制备方法。
背景技术:
:随着我国经济的不断发展,各个行业对用电的需求逐年增加,迫切需要一种具备轻质、高导电性、高强度特性的导线材料。6xxx系铝镁硅合金因为电导率、比强度高、耐蚀性好且使用寿命长,常被用做架空输电导线。目前工业上制备铝镁硅合金导线常采用传统工艺,包括固溶处理、固溶后水淬、冷拉以及人工时效。以此法制得的铝镁硅合金抗拉强度为255~325mpa,电导率为52.5~57.5%iacs(国际退火铜标准)。由此可见,目前工业中使用的铝镁硅合金导线存在的问题是电导率稍高,但强度低,二者互为矛盾,这就大大限制了其在远距离输电领域的应用。如何获得兼具高强度、高导电性能的铝合金导线,成为了当前电力能源行业亟需解决的技术问题。目前提高铝镁硅合金强度的方法主要有:(1)合金化,如添加ca、mn、sc等元素合金化,但一般情况下,通过合金化提高强度的同时,必然会损失其电导率;(2)加工变形,如等通道转角挤压、轧制变形等,若变形后的铝合金基体晶粒细化,且第二相的析出能使得溶质原子含量降低,则加工变形可使强度和电导率同时提高;(3)热处理,如固溶、时效处理,改善合金微观组织,提高其强度和电导率。经检索,cn201810208279.0专利介绍了“一种高强度高导电性铝镁硅钙合金的制备方法”,通过真空熔炼、等通道转角挤压方法所制备的合金导电性达到57.2%iacs,抗拉强度为370mpa。cn201811445500.0专利介绍了“一种高强度高导电铝合金导线的制备方法”,制备的铝合金导线电导率为55.5%~58.5%iacs,伸长率为2.0~4.0%,其抗拉强度为310~350mpa。cn201711465441.9专利介绍了“一种高强高导的耐热铝合金导线及其制备方法”,其制备的耐热铝导线电导率高达62%iacs,但其抗拉强度最高为322mpa。因此,为使铝镁硅合金在输电领域得到更为广泛而有效的应用,迫切需要在高电导率下大幅提高其强度。技术实现要素:本发明的目的在于制备高强度导电铝合金,提供一种高强度铝镁硅钙导电铝合金及制备方法。为实现上述目的,本发明提供了如下技术方案:本发明的技术方案之一:提供一种各元素质量百分比为mg0.59~0.9%,si0.5~0.9%,ca0.253~0.386%,余量为al,杂质含量≤0.1%的高强度铝镁硅钙导电铝合金。优选的,所述高强度铝镁硅钙导电铝合金的原料包括al块、al-12si中间合金、mg-10al-27ca共晶型中间合金。更优选的,所述al块的纯度为99.8%以上。优选的,所述mg-10al-27ca共晶型中间合金的制备方法为:按元素比例配制al块(纯度为99.8%以上)、mg-30ca中间合金;在惰性气体的保护下,先将al块在700~720℃的温度下保温20min,待al块熔化后,扒去浮渣,然后加入mg-30ca中间合金,并将覆盖剂(rj-2熔剂)撒到熔体表面,继续在720~740℃的温度下保温20min,保温结束后扒渣,添加rj-2熔剂进行精炼,最后在690~700℃保温20min制得熔体,所得熔体浇注,制得mg-10al-27ca中间合金。mg-10al-27ca是共晶型中间合金,其基体组织中存在细小、均匀分散的金属间化合物,当其作为原料加入铝合金中,根据组织遗传原理,在铸态铝合金凝固组织中可形成细小、均匀分散的(mg,al)2ca颗粒增强相。而高密度细小的(mg,al)2ca颗粒增强相可促进铝基体中mg2si颗粒增强相大量析出,从而显著降低mg原子在铝基体中的固溶度,同时提高铝镁硅钙合金的强度和导电性。si以al-12si中间合金的形式加入,可以显著降低si的熔点,使原料更易于熔化,还能减少熔炼过程中的氧化。本发明的技术方案之二:提供一种高强度铝镁硅钙导电铝合金的制备方法,以al块、al-12si中间合金、mg-10al-27ca共晶型中间合金为原料制备铸态合金,铸态合金经过两道次轧制,制得所述高强度铝镁硅钙导电铝合金。优选的,铸态合金轧制前进行固溶处理,固溶后水淬和预时效处理,两道次轧制后进行时效处理。固溶处理能够确保合金元素充分固溶、铸态合金成分均匀;预时效处理则可预先析出一定量的纳米析出相。更优选的,所述固溶处理的温度为500~560℃,时间为3~5h;所述预时效处理的温度为150~180℃,时间为1~2h;所述时效处理的温度为130~150℃,时间为18~30h。优选的,所述两道次轧制具体为第一道次冷轧和第二道次热轧。第一道次冷轧后,合金基体内部产生高密度位错,析出相与位错发生交互作用(析出相钉扎位错),从而促进高强度铝镁硅钙导电铝合金基体晶粒中大角度晶界的快速形成,加速晶粒细化、抑制胞状拉长晶粒形成、降低织构,使高强度铝镁硅钙导电铝合金的强度和塑韧性得以提升。优选的,所述两道次轧制的第一道次轧制压下量为46%,第二道轧制压下量为37.8%,两道次总压下量为66.6%。仅进行两道次常规轧制,总变形量远小于ecap强塑性变形(ecap每道次应变量约为100%),就能够实现铝镁硅钙合金的高强韧性。此工艺操作简单,设备常规,易于工业化生产。更优选的,所述固溶、预时效态合金板材经第一道次室温轧制后,在通氩气保护的情况下,放入已加热至250~350℃的真空管式炉中,保温5~10min后取出,立即进行第二道次轧制。短时加热可部分消除位错、促进回复、降低残余应力,利于第二道次轧制的进行;第二道次轧制则可继续促进高密度第二相析出,细化铝基体晶粒。优选的,制备铸态合金的方法包括:按元素比例配制al块、al-12si中间合金、mg-10al-27ca共晶型中间合金;在惰性气体的保护下,先将al块和al-12si中间合金在740~760℃的温度下保温30~40min,待原料熔化后,扒去浮渣,然后加入mg-10al-27ca共晶型中间合金,并将覆盖剂撒到熔体表面,继续在720~740℃的温度下保温20~30min,保温结束后扒渣,添加精炼剂进行精炼,最后在700~720℃的温度下保温20~30min制得熔体,所得熔体浇注,制得铸态合金。本发明的有益技术效果如下:本发明采用在6201合金中添加设计制备的mg-10al-27ca共晶型中间合金,并且结合固溶、预时效处理、轧制变形以及之后的时效处理,使高强度铝镁硅钙导电铝合金基体晶粒细化,平均晶粒尺寸≤0.2μm,基体中均匀弥散分布着细小的mg2si、(mg,al)2ca第二相,从而使得制备的高强度铝镁硅钙导电铝合金在较高电导率下,强度得到大幅度提升。本发明制得的高强度铝镁硅钙导电铝合金屈服强度达到348mpa、抗拉强度高达523mpa、伸长率为5.4%,电导率为46.77%iacs。本发明提供的高强度导电铝合金制备方法工艺简单、设备常规,易于工业化生产,所用合金体系成本低廉、综合性能优异。附图说明图1为实施例及对比例2-3中所用到的mg-10al-27ca中间合金的铸态om图。图2为对比例1中所用到的mg-30ca中间合金的铸态om图。图3为实施例1制得的高强度铝镁硅钙导电铝合金的om图。图4为实施例1制得的高强度铝镁硅钙导电铝合金的tem组织图。图5为实施例1制得的高强度铝镁硅钙导电铝合金的拉伸应力-应变曲线图。具体实施方式现结合附图详细说明本发明的多种示例性实施方式,该详细说明不应认为是对本发明的限制,而应理解为是对本发明的某些方面、特性和实施方案的更详细的描述。应理解本发明中所述的术语仅仅是为描述特别的实施方式,并非用于限制本发明。另外,对于本发明中的数值范围,应理解为还具体公开了该范围的上限和下限之间的每个中间值。在任何陈述值或陈述范围内的中间值以及任何其他陈述值或在所述范围内的中间值之间的每个较小的范围也包括在本发明内。这些较小范围的上限和下限可独立地包括或排除在范围内。除非另有说明,否则本文使用的所有技术和科学术语具有本发明所述领域的常规技术人员通常理解的相同含义。虽然本发明仅描述了优选的方法和材料,但是在本发明的实施或测试中也可以使用与本文所述相似或等同的任何方法和材料。关于本文中所使用的“包含”、“包括”、“具有”、“含有”等等,均为开放性的用语,即意指包含但不限于。本发明实施例及对比例中所用到的mg-10al-27ca共晶型中间合金的制备方法为:按元素比例配制al块(纯度为99.8%以上)、mg-30ca中间合金;在惰性气体的保护下,先将al块在700~720℃的温度下保温20min,待al块熔化后,扒去浮渣,然后加入mg-30ca中间合金,并将覆盖剂(rj-2熔剂)撒到熔体表面,继续在720~740℃的温度下保温20min,保温结束后扒渣,添加rj-2熔剂进行精炼,最后在690~700℃保温20min制得熔体,所得熔体浇注,制得mg-10al-27ca中间合金。实施例1高强度铝镁硅钙导电铝合金中各元素质量百分比为mg0.59%,si0.54%,ca0.253%,余量为al,杂质含量≤0.1%,制备方法包括以下步骤:(1)熔炼铸态合金此合金的制备是在坩埚电阻炉内且在氩气保护下采用普通重力铸造方法完成的:①将称取并且打磨好的472.82gal块(纯度为99.8%以上),22.5gal-12si中间合金,4.68gmg-10al-27ca共晶型中间合金与称量好的覆盖剂和精炼剂一起放入干燥箱干燥。②刷料:将石墨坩埚放入电阻炉内加热,当温度达到400℃时开始刷料,将配置好的涂料均匀牢固地附着在坩埚内壁,至少刷三遍。③加料:刷料完毕之后,向坩埚内加入干燥好的al块和al-12si中间合金,同时通入氩气保护,待炉温升到760℃后保温30min,等待原料熔化。④扒渣,加料:原料完全熔化后,关闭电源,打开炉门,用工具扒去表面浮渣,再加入用铝箔包裹的mg-10al-27ca共晶型中间合金,之后再将干燥过的覆盖剂撒到熔体表面,关闭炉门,打开电源,待温度升到740℃后保温20min。⑤精炼:保温过后,关闭电源,进行扒渣,然后将干燥过的精炼剂倒入熔体中并充分搅拌。搅拌完成后,关闭炉门,打开电源,升温至720℃后保温20min。⑥浇注:开炉扒渣完后,取出熔炼坩埚,对准钢模浇口进行浇注,浇满为止。(2)线切割铸件将步骤(1)得到的铸件从模具中取出后,用线切割机床将铸件切割成矩形块,尺寸为50mm×20mm×4mm。(3)固溶、预时效处理固溶处理:将矩形块表面涂抹凡士林后用铝箔包裹并埋于装有石墨粉的铁盒中,置于箱式电阻炉内,在550℃下固溶处理5h;固溶处理后立即用20℃冷水淬火,淬火时间≤10s。预时效处理:将淬火后的矩形块再放入温度为180℃的箱式电阻炉中保温2h,取出后在空气中冷却至室温。(4)轧制采用二辊平轧轧机,实验之前先用废料调试辊缝,将辊缝调到预期的厚度。轧制之前,先将步骤(3)处理过的矩形块用240目的砂纸打磨去除表面缺陷。一道次轧制:转动开关,让轧辊转动,进行轧制。一道次轧制后,矩形块被轧成薄板,厚度从3.65mm轧到1.96mm,压下量达到46%。二道次轧制:在二道次轧制前,先将一道次轧制后的薄板放入300℃的管式加热炉中保温5min(通氩气保护),并且调试好辊缝厚度,5min后,将薄板从炉中迅速取出,立即进行轧制,薄板厚度从1.96mm轧到1.22mm,压下量为37.8%。两道次总压下量为66.6%。(5)时效处理将步骤(4)得到的薄板用铝箔包裹,放入管式加热炉中进行时效处理,温度为130℃,时间为24h。时效处理后,让试样在空气中冷却至室温。实施例2高强度铝镁硅钙导电铝合金中各元素质量百分比为mg0.59%,si0.50%,ca0.253%,余量为al,杂质含量≤0.1%,制备方法包括以下步骤:(1)熔炼铸态合金此合金的制备是在坩埚电阻炉内且在氩气保护下采用普通重力铸造方法完成的:①将称取并且打磨好的474.49gal块(纯度为99.8%以上),20.83gal-12si中间合金,4.68gmg-10al-27ca共晶型中间合金与称量好的覆盖剂和精炼剂一起放入干燥箱干燥。②刷料:将石墨坩埚放入电阻炉内加热,当温度达到400℃时开始刷料,将配置好的涂料均匀牢固地附着在坩埚内壁,至少刷三遍。③加料:刷料完毕之后,向坩埚内加入干燥好的al块和al-12si中间合金,同时通入氩气保护,待炉温升到750℃后保温40min,等待原料熔化。④扒渣,加料:原料完全熔化后,关闭电源,打开炉门,用工具扒去表面浮渣,再加入用铝箔包裹的mg-10al-27ca共晶型中间合金,之后再将干燥过的覆盖剂撒到熔体表面,关闭炉门,打开电源,待温度升到730℃后保温30min。⑤精炼:保温过后,关闭电源,进行扒渣,然后将干燥过的精炼剂倒入熔体中并充分搅拌。搅拌完成后,关闭炉门,打开电源,升温至710℃后保温20min。⑥浇注:开炉扒渣完后,取出熔炼坩埚,对准钢模浇口进行浇注,浇满为止。(2)线切割铸件将步骤(1)得到的铸件从模具中取出后,用线切割机床将铸件切割成矩形块,尺寸为50mm×20mm×4mm。(3)固溶、预时效处理固溶处理:将矩形块表面涂抹凡士林后用铝箔包裹并埋于装有石墨粉的铁盒中,置于箱式电阻炉内,在560℃下固溶处理3h;固溶后立即用20℃冷水淬火,淬火时间≤10s。预时效处理:将淬火后的矩形块再放入温度为150℃的箱式电阻炉中保温2h,取出后在空气中冷却至室温。(4)轧制采用二辊平轧轧机,实验之前先用废料调试辊缝,将辊缝调到预期的厚度。轧制之前,先将步骤(3)处理过的矩形块用240目的砂纸打磨去除表面缺陷。一道次轧制:转动开关,让轧辊转动,进行轧制。一道次轧制后,矩形块被轧成薄板,厚度从3.65mm轧到1.96mm,压下量达到46%。二道次轧制:在二道次轧制前,先将一道次轧制后的薄板放入250℃的管式加热炉中保温10min(通氩气保护),并且调试好辊缝厚度,10min后,将薄板从炉中迅速取出,立即进行轧制,薄板厚度从1.96mm轧到1.22mm,压下量为37.8%。两道次总压下量为66.6%。(5)时效处理将步骤(4)得到的薄板用铝箔包裹,放入管式加热炉中进行时效处理,温度为150℃,时间为18h。时效处理后,让试样在空气中冷却至室温。实施例3高强度铝镁硅钙导电铝合金中各元素质量百分比为mg0.59%,si0.9%,ca0.253%,余量为al,杂质含量≤0.1%,制备方法包括以下步骤:(1)熔炼铸态合金此合金的制备是在坩埚电阻炉内且在氩气保护下采用普通重力铸造方法完成的:①将称取并且打磨好的457.82gal块(纯度为99.8%以上),37.5gal-12si中间合金,4.68gmg-10al-27ca共晶型中间合金与称量好的覆盖剂和精炼剂一起放入干燥箱干燥。②刷料:将石墨坩埚放入电阻炉内加热,当温度达到400℃时开始刷料,将配置好的涂料均匀牢固地附着在坩埚内壁,至少刷三遍。③加料:刷料完毕之后,向坩埚内加入干燥好的al块和al-12si中间合金,同时通入氩气保护,待炉温升到760℃后保温35min,等待原料熔化。④扒渣,加料:原料完全熔化后,关闭电源,打开炉门,用工具扒去表面浮渣,再加入用铝箔包裹的mg-10al-27ca共晶型中间合金,之后再将干燥过的覆盖剂撒到熔体表面,关闭炉门,打开电源,待温度升到720℃后保温30min。⑤精炼:保温过后,关闭电源,进行扒渣,然后将干燥过的精炼剂倒入熔体中并充分搅拌。搅拌完成后,关闭炉门,打开电源,升温至700℃后保温30min。⑥浇注:开炉扒渣完后,取出熔炼坩埚,对准钢模浇口进行浇注,浇满为止。(2)线切割铸件将步骤(1)得到的铸件从模具中取出后,用线切割机床将铸件切割成矩形块,尺寸为50mm×20mm×4mm。(3)固溶、预时效处理固溶处理:将矩形块表面涂抹凡士林后用铝箔包裹并埋于装有石墨粉的铁盒中,置于箱式电阻炉内,在500℃下固溶处理5h;固溶后立即用20℃冷水淬火,淬火时间≤10s。预时效处理:将淬火后的矩形块再放入温度为180℃的箱式电阻炉中保温1h,取出后在空气中冷却至室温。(4)轧制采用二辊平轧轧机,实验之前先用废料调试辊缝,将辊缝调到预期的厚度。轧制之前,先将步骤(3)处理过的矩形块用240目的砂纸打磨去除表面缺陷。一道次轧制:转动开关,让轧辊转动,进行轧制。一道次轧制后,矩形块被轧成薄板,厚度从3.65mm轧到1.96mm,压下量达到46%。二道次轧制:在二道次轧制前,先将一道次轧制后的薄板放入350℃的管式加热炉中保温5min(通氩气保护),并且调试好辊缝厚度,5min后,将薄板从炉中迅速取出,立即进行轧制,薄板厚度从1.96mm轧到1.22mm,压下量为37.8%。两道次总压下量为66.6%。(5)时效处理将步骤(4)得到的薄板用铝箔包裹,放入管式加热炉中进行时效处理,温度为130℃,时间为30h。时效处理后,让试样在空气中冷却至室温。对比例1与实施例1相比,不同之处在于,没有使用mg-10al-27ca共晶型中间合金,加入的原料为al块473.29g,al-12si中间合金22.5g,mg-30ca中间合金4.21g。mg-30ca中间合金的加入步骤同mg-10al-27ca共晶型中间合金的加入步骤,其他步骤、参数同实施例1。对比例2与实施例1相比,不同之处在于,第一道次冷轧压下量为35.2%;第二道次热轧压下量为31.0%,两道次轧制总压下量为55.3%;其他步骤、参数同实施例1。对比例3与实施例1相比,不同之处在于,第一道次冷轧压下量为49.2%;第二道热轧压下量为49.5%,两道次轧制总压下量为74.3%;其他步骤、参数同实施例1。图1为实施例及对比例2-3中所用到的mg-10al-27ca中间合金的铸态om图。从图1可以看出,mg-10al-27ca为共晶型中间合金,除初生(mg,al)2ca相外,基体中的共晶mg2ca相更为细密。图2为对比例1中所用到的mg-30ca中间合金的铸态om图。从图2中可以看出其基体中的mg2ca相比较粗大。图3为实施例1制得的高强度铝镁硅钙导电铝合金的om图。从图3可以看出,经过轧制和时效处理的高强度铝镁硅钙导电铝合金基体内均匀弥散分布mg2si颗粒相、(mg,al)2ca颗粒相。图4为实施例1制得的高强度铝镁硅钙导电铝合金的tem组织图。从图4可以看出,经过轧制和时效处理的高强度铝镁硅钙导电铝合金基体内平均晶粒尺寸≤0.2μm,并且在基体内存在大量位错。图5为实施例1制得的高强度铝镁硅钙导电铝合金的拉伸应力-应变曲线图。从图中可以看出其屈服强度达到348mpa,抗拉强度达到523mpa,伸长率达到5.4%。在室温下,采用sigma2008b手持式涡流电导率仪并选取试样的五个位置进行测量,取其平均值,最终测得实施例1、对比例1、对比例2、对比例3制得的铝镁硅钙合金电导率分别为46.77%iacs、52.4%iacs、47.80%iacs、47.45%iacs。对实施例1及对比例1-3制备的铝合金的力学性能和导电性能进行测定,结果见表1。表1铝合金力学性能和导电性能性能屈服强度/mpa抗拉强度/mpa伸长率/%电导率/iacs实施例13485235.446.77对比例11332485.852.40对比例21553314.347.80对比例32833535.747.45从表1中可以看出,对比例1制得的铝镁硅钙合金强度低于实施例1,原因在于:根据组织遗传原理,实施例1的铸态凝固组织中有细小均匀分散的(mg,al)2ca颗粒相,它促进了铝基体中mg2si增强相的大量析出,所以在相同压下量下实施例1强度更高、电导率降低。对比例2制得的铝镁硅钙合金强度低于实施例1,原因在于:实施1因为轧制压下量更大,其变形后基体晶粒尺寸更加细小,并且有更多细小的mg2si颗粒相弥散分布在铝基体中,使得其强度更高。对比例3制得的铝镁硅钙合金强度低于实施例1,原因在于:对比例3中合金在大压下量轧制过程中发生了动态回复和再结晶,使其与实施例1相比,基体晶粒尺寸变大,位错密度降低,析出相长大、数量减少,强度下降。以上所述的实施例仅是对本发明的优选方式进行描述,并非对本发明的范围进行限定,在不脱离本发明设计精神的前提下,本领域普通技术人员对本发明的技术方案做出的各种变形和改进,均应落入本发明权利要求书确定的保护范围内。当前第1页12