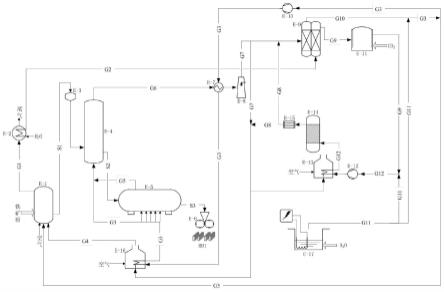
1.本发明属于冶金、化工技术领域,特别涉及采用流化床对铁矿粉进行直接还原的系统和方法,具体涉及一种碳排放低于零的热压铁块生产方法。
背景技术:2.为了人类社会的可持续发展,2015年全球170多个国家共同签订了《巴黎协定》,该协定设定了在本世纪未全球平均气温较工业化之前上升幅度控制在1.5℃以内的挑战性目标,以降低不可逆转的气候变化风险。基于该目标,世界各国纷纷制订了各自的碳中和时间表。2020年中国政府正式对外宣布力争在2060年实现碳中和。据统计,全球钢铁工业的碳排放约占co2排放总量的7%,而中国钢铁工业的碳排放占全国co2排放总量的比例超过世界平均水平的一倍以上,达到15%。因此,中国钢铁工业在2060年之前实现co2的净零排放是达成全社会碳中和目标的重要前提。
3.据世界钢协的统计数据,2019年全球超过70%的粗钢由高炉-转炉流程生产,而现代高炉生产一吨铁水至少消耗350kg焦炭。在找到其它材料替代焦炭之前,高炉工艺不可能做到co2净零排放。在所有非高炉炼铁工艺中,直接还原工艺的生产规模仅次于高炉。直接还原工艺按还原介质可分为煤基和气基两大类,其中气基直接还原被认为是最有可能在可预见的未来替代高炉、实现净零碳排放的大规模炼铁技术。气基直接还原工艺按反应器类型又可分为竖炉和流化床两种方式。气基竖炉的代表有midrex工艺以及tenove开发的energiron工艺。目前气基竖炉主要采用天然气或煤制合成气作为铁矿还原反应的热源和还原剂,还没有做到净零碳排放。以midrex竖炉-电炉生产流程为例,吨钢的co2排放约为500kg/tls(高炉-转炉流程约为1.8t/tls)。(l.m.germeshuizen,p.w.blom.international journal of hydrogen energy,2013,vol38:10671-10682)。理论上气基竖炉可以采用纯氢还原铁矿石从而实现co2净零排放,但目前尚无纯氢竖炉的应用实绩。另外,竖炉炉料中要使用一定比例的球团,因此必须同时实现球团生产的净零排放才能保证最终直接还原产品的净零排放。相比之下,流化床直接还原由于直接以铁矿粉为原料,完全消除了铁矿粉造球工序产生的碳排放。在已开发的各种流化床直接还原工艺中,fior工艺(美国专利us5082251)、finmet工艺(gerhard deimek.钢铁,2000,第12期:13-15)以及finex工艺(张寿荣、张绍贤.钢铁,2009,第5期:1-5)等也都采用天然气或煤制合成气为反应和加热气源,co2排放强度与竖炉相当。另外,这些工艺的一个共同技术特征是全部采用四级鼓泡流化床的串联结构,铁矿粉依靠重力从上到下依次通过四个流化床反应器完成整个还原反应过程,四个流化床反应器的垂直叠加抬高了整套装置的高度,极大增加了建设成本。另外,为了达到理想的还原反应条件以获得金属化率超过92%的合格产品,finmet将操作压力提高到1.1~1.4mpa,对设备提出了较高要求,增加了运行成本。finex将流化床的操作压力降到0.4~0.5mpa,相应地金属化率降到80%以下,产品不能直接用于电炉冶炼,需再经过熔融气化炉以完成铁水冶炼。
4.迄今为止,唯一实现了纯氢还原铁矿粉的直接还原工艺是由鲁奇公司开发的
circored(steven a.elmquist,peter weber,heinz eichberger.stahl und eisen,2002,第2期:59-64)。该工艺采用一个循环流化床与一个鼓泡流化床的串联组合完成铁矿粉的还原反应,相比四个鼓泡流化床的串联方式具有设备数量少、操作压力低、厂房投资小等优点。该工艺虽然做到了100%去碳化,但技术上仍存以下不足:(1)铁矿石与h2的氧化还原反应是强吸热过程,反应所吸收的热量完全由铁矿粉和h2带入的显热提供。为了保证反应所需热量,必须先将铁矿粉加热到850~900℃,同时将h2加热到750℃以上。热的铁矿粉和h2在流化床反应器中发生铁的还原反应。反应大量吸热将反应器的温度降低至650℃。由铁的还原反应动力学可知,反应温度越高反应速度越快。如此低的反应温度使circored需要较长的反应时间(约4小时)才能完成铁矿粉的还原,大大降低了装置的生产效率,这意味着单位产量的生产成本较高。为了提高流化床的反应温度只能进一步提高铁矿粉和h2的预热温度。但在现有技术条件下,进一步提高铁矿粉和h2温度的技术难度非常高,而且存在相当高的安全风险;(2)采用全氢还原得到的最终产品热压铁块中不含碳,后续炼钢过程中还要另外加入增碳剂;(3)还原铁矿粉所用的h2全部来自天然气(ch4)重整,碳排放强度与传统竖炉工艺基本相当。
技术实现要素:5.本发明充分利用circored工艺使用循环流化床和鼓泡流化床的组合还原铁矿粉的技术优点,在circored工艺的基础上提出一种新的工艺流程,在实现铁矿粉直接还原过程碳排放低于零的前提下,降低铁矿粉的预热温度从而减少能源消耗,同时提高流化床的反应温度以改善铁矿石还原的动力学条件,加快反应速度,缩短反应时间,提高生产效率并降低生产成本。另外,生产具有一定碳含量的直接还原热压铁块,产品质量优于circored工艺。
6.为实现本发明的目的,本发明采用的技术方案如下:
7.一种生产过程碳排放低于零的热压铁块生产方法,以铁矿粉、水和co2为生产原料,以可再生能源发电提供生产过程所需的能量,整个生产过程中不使用任何化石能源;具体包括如下步骤:
8.(1)将粒度为0~1mm的铁矿粉加入到循环流化床预热器e-1进行预热;循环流化床预热器e-1的流化和加热介质为还原气加热炉e-16的高温烟气g4,以及经脱碳装置e-9脱除co2并加氢后的还原气g3和空气;
9.(2)被预热到750~800℃的铁矿粉s1从循环流化床预热器e-1排出后进入加料装置e-3,在此被加压到0.4~0.5mpa后进入循环流化床预还原反应器e-4;循环流化床预还原反应器e-4中通入由鼓泡流化床终还原反应器e-5排出的终还原反应后气体g5,同时通入经脱碳、加氢并加热至800~850℃的热还原气g3;
10.(3)经预还原的铁矿粉s2从循环流化床预还原反应器e-4排出后进入鼓泡流化床终还原反应器e-5,鼓泡流化床终还原反应器e-5中通入经脱碳、加氢并加热至800~850℃的热还原气g3;完成终还原反应后的热直接还原铁s3排出鼓泡流化床终还原反应器e-5,送入热压成型机e-6,经热压成型得到碳含量为0.6~1.4%的产品热压铁块hbi,以质量百分比计。
11.本发明整个生产过程中,从外部输入的co2中一部分以固态进入产品热压铁块hbi
中,这部分固态的碳会一直存在于钢铁产品的全生命周期中,而以气态形式排放进入大气中的碳少于输入的碳,所以生产过程的碳排量低于零,或者说净碳排放为负
12.进一步,在步骤(1)中还原气g3和空气在循环流化床预热器e-1内发生燃烧反应并放出热量用于加热铁矿粉。
13.进一步,在步骤(1)中完成铁矿粉加热过程从循环流化床预热器e-1排出的热烟气进入余热锅炉e-2,将锅炉中的水加热产生蒸汽以回收烟气所携带的热量,产生的蒸汽g2送往脱碳装置e-9用于co2吸收液的再生;回收热量以后的烟气作为尾气排出。
14.进一步,在步骤(3)中鼓泡流化床终还原反应器e-5排出的热反应后气体g5送入循环流化床预还原反应器e-4,参与铁矿粉的预还原反应。
15.进一步,循环流化床预还原反应器e-4排出的热的炉顶气g6进入换热器e-7,与经压缩机e-10加压后的还原气g3进行热交换;换热后的炉顶气经过洗涤装置e-8进一步降温,同时去除还原过程产生的水;经过洗涤装置e-8降温净化后的炉顶气g7送入脱碳装置e-9,脱除其中的co2,得到co+h2含量大于95%的脱碳气g10,以体积百分比计。
16.更进一步,上述脱碳可以采用benfield法、改良mdea法或低温甲醇洗成熟技术。
17.更进一步,上述脱碳气与电解水装置e-17产生的纯氢g11混合,以补充在预还原反应器e-4、终还原反应器e-5用于铁矿粉还原所消耗的氢,同时调整、控制混合后的还原气g3中co与h2的含量分别为10~45%(体积百分比)和50~85%(体积百分比)。
18.更进一步,上述加氢后的还原气g3经压缩机e-10加压、换热器e-7预热后,再由还原气加热炉e-16进一步加热至800~850℃;热还原气g3分别送至鼓泡流化床反应器终还原e-5、循环流化床预还原反应器e-4,参与铁矿粉的直接还原。
19.根据本发明所述一种碳排放低于零的热压铁块生产方法,由脱碳装置e-9脱除的co2气体g9送入缓冲罐e-11中存贮;由外部输入的纯co2气体也加入到缓冲罐e-11之中;缓冲罐e-11向外输出的co2气体g9先与电解水装置e-17制备的纯氢g11混合,作为逆变换反应的原料气g12;逆变反应原料气g12经压缩机e-12加压,再由逆变反应原料气加热炉e-13加热至400~450℃,然后进入逆变换反应器e-14,在此发生逆水煤气变换反应:
20.co2+h2=co+h2o
21.反应产物经冷凝器e-15分离反应中生成的水,然后将反应后的co/co2/h2混合气体g8与净化后的炉顶气g7一起送往脱碳装置e-9,以补充还原气中的co和h2。
22.根据本发明所述一种碳排放低于零的热压铁块生产方法,还原气加热炉e-16、逆变反应原料气加热炉e-13所用的燃料气是来自净化后的炉顶气g7,也可以配入一定比例的逆水煤气变换后的混合气体g8。
23.发明详述:
24.一种碳排放低于零的热压铁块生产方法:
25.首先将粒度为0~1mm的铁矿粉加入到循环流化床预热器e-1进行预热。循环流化床预热器e-1的流化和加热介质为还原气加热炉e-16的高温烟气g4,以及经脱碳装置e-9脱除co2并加氢后的还原气g3和空气。还原气g3和空气在循环流化床预热器e-1内发生燃烧反应并放出热量用于加热铁矿粉。完成铁矿粉加热过程从循环流化床预热器e-1排出的热烟气进入余热锅炉e-2,将锅炉中的水加热产生蒸汽以回收烟气所携带的热量,产生的蒸汽g2送往脱碳装置e-9用于co2吸收液的再生。回收热量以后的烟气作为尾气排出。
26.被预热到750~800℃的铁矿粉s1从循环流化床预热器e-1排出后进入加料装置e-3,在此被加压到0.4~0.5mpa后进入循环流化床预还原反应器e-4。在反应器e-4内铁矿粉被预还原到金属化率达到70%左右。循环流化床预还原反应器e-4中通入由鼓泡流化床终还原反应器e-5排出的终还原反应后气体g5,同时通入经脱碳、加氢并加热至800~850℃的热还原气g3。经预还原金属化率达到70%以上的铁矿粉s2从循环流化床预还原反应器e-4排出后进入鼓泡流化床终还原反应器e-5,鼓泡流化床终还原反应器e-5中通入经脱碳、加氢并加热至800~850℃的热还原气g3。铁矿粉在终还原反应器中被还原到金属化率超过93%。完成终还原反应后的热直接还原铁s3排出鼓泡流化床终还原反应器e-5,送入热压成型机e-6,经热压成型得到产品热压铁块hbi(hotbriquettediron)。鼓泡流化床终还原反应器e-5排出的热反应后气体g5送入循环流化床预还原反应器e-4,参与铁矿粉的预还原反应。
27.循环流化床预还原反应器e-4排出的热的炉顶气g6进入换热器e-7,与经压缩机e-10加压后的还原气g3进行热交换。换热后的炉顶气经过洗涤装置e-8进一步降温,同时去除还原过程产生的水。经过洗涤装置e-8降温净化后的炉顶气g7送入脱碳装置e-9,脱除其中的co2,得到co+h2含量大于95%(体积百分比)的脱碳气g10。脱碳可以采用benfield法、改良mdea法或低温甲醇洗等成熟技术。脱碳气与电解水装置e-17产生的纯氢g11混合,以补充在预还原反应器e-4、终还原反应器e-5用于铁矿粉还原所消耗的氢,同时调整、控制混合后的还原气体中co与h2的比例。加氢后的还原气g3经压缩机e-10加压、换热器e-7预热后,再由还原气加热炉e-16进一步加热至800~850℃。热还原气g3分别送至鼓泡流化床反应器终还原e-5、循环流化床预还原反应器e-4,参与铁矿粉的直接还原。
28.由脱碳装置e-9脱除的co2气体g9送入缓冲罐e-11中存贮。由外部输入的纯co2气体也加入到缓冲罐e-11之中。缓冲罐e-11向外输出的co2气体g9先与电解水装置e-17制备的纯氢g11混合,作为逆变换反应的原料气g12。逆变反应原料气g12经压缩机e-12加压到2.5mpa,再由逆变反应原料气加热炉e-13加热至400~450℃,然后进入逆变换反应器e-14,在此发生逆水煤气变换反应:
29.co2+h2=co+h2o
30.反应产物经冷凝器e-15分离反应中生成的水,然后将反应后的co/co2/h2混合气体g8与净化后的炉顶气g7一起送往脱碳装置e-9,以补充还原气中的co和h2。
31.还原气加热炉e-16、逆变反应原料气加热炉e-14所用的燃料气是来自净化后的炉顶气g7,也可以配入一定比例的逆水煤气变换后的混合气体g8。
32.整个系统所用的氢气全部来自电解水装置e-17。当电解水装置所用电能都源自可再生能源,比如光伏发电、风力发电或水力发电等,则本发明的铁矿石还原过程可实现co2净排放小于零。
33.本发明具有以下技术特征:
34.(1)采用常压循环流化床将0~1mm的铁矿粉预热到750~800℃,循环流化床预热装置的流化和加热介质一部分来自还原气加热炉的热烟气,另一部分由(co+h2)混合气体和空气的燃烧反应补充。(co+h2)混合气体由工艺自身提供,优选取自脱碳、加氢后的还原气。预热装置排出的高温烟气经余热锅炉回收显热,锅炉产生的蒸汽用于脱碳装置中co2吸收液的再生。
35.(2)采用加压循环流化床进行铁矿粉的预还原。循环流化床预还原反应器的压力为0.4~0.5mpa,温度750~800℃。循环流化床预还原反应器通入的气体分别为鼓泡流化床终还原反应器排出的终还原反应后尾气,以及经脱碳、加氢并加热至800~850℃的还原气。铁矿粉经预还原后金属化率达到70%以上。
36.(3)循环流化床预还原反应器排出的热炉顶气与冷还原气进行热交换回收炉顶气中的热量,同时预热还原气。
37.(4)换热后的预还原炉顶气进一步净化并分离铁矿石还原生成的水,净化后的炉顶气通过脱碳单元脱除其中的co2,得到co+h2含量超过95%(体积百分比)的脱碳气。脱碳可以采用benfield法、改良mdea法或低温甲醇洗等成熟技术。
38.(5)向脱碳气中配入一定比例h2得到还原气。还原气中h2含量50~85%(体积百分比),co含量10~45%(体积百分比)。
39.(6)采用加压鼓泡流化床完成铁矿粉的终还原。鼓泡流化床终还原反应器的压力为0.4~0.5mpa,温度750~800℃。鼓泡流化床终还原反应器通入经脱碳、加氢并加热至800~850℃的还原气。铁矿粉经终还原后金属化率达到93%以上。
40.(7)金属化率93%以上的直接还原铁热压成型得到产品热压铁块(hbi)。热压铁块的碳含量在0.6~1.4%(质量百分比)。
41.(8)将脱碳单元脱除的co2气体与纯h2混合,作为逆变换反应的原料气。将逆变反应原料气加压到2.5mpa、加热至400~450℃,通过逆水煤气变换反应将(co2+h2)转换成为(co+h2o)。分离反应中生成的水。将反应后的co/co2/h2混合气体与净化后的循环流化床预还原炉顶气一起送回脱碳单元,以补充还原气中的co和h2。
42.(9)加热还原气和逆变原料气所用的燃料气为净化后的循环流化床预还原炉顶气,也可以配入一定比例的逆水煤气变换后并脱除水分的co/co2/h2混合气体。
43.(10)生产过程中所用的h2全部由电解水制氢装置产生。电解水制氢装置所消耗的电能都源自可再生能源,比如光伏发电、风力发电或水力发电等。
44.(11)本发明所用的物料仅包括铁矿粉、水和co2。其中co2可以是其它生产过程的排放产物,也可以从大气中分离得到。一部分碳元素进入到最终的直接还原铁中,所以整个生产过程的co2净排放小于零。
45.本发明有益效果:
46.本发明所用的全部物料仅包括铁矿粉、水和co2。其中co2可以是其它生产过程的排放产物,也可以从大气中分离得到。一部分碳元素进入到最终的直接还原铁中,所以整个生产过程的co2净排放小于零。
47.本发明采用co/h2的混合气体实现铁矿粉的直接还原,利用其中co与铁矿粉反应放出的热量补充h2与铁矿粉反应所吸收的热量,实现降低铁矿粉预热温度的同时提高流化床反应器的反应温度,加快铁矿粉直接还原的反应速度,可以在较短的时间内(3小时以内)完成铁矿粉的直接还原,提高生产效率。
48.本发明所生产的直接还原热压铁块金属化率超过93%,碳含量在0.6~1.4%左右,以质量百分比计,是优质的炼钢原料。
附图说明
49.图1为本发明提供的一种碳排放低于零的热压铁块生产方法的工艺流程示意图。
50.其中:e-1:循环流化床预热器
51.e-2:余热锅炉
52.e-3:加料装置
53.e-4:循环流化床预还原反应器
54.e-5:鼓泡流化床终还原反应器
55.e-6:热压成型机
56.e-7:换热器
57.e-8:洗涤装置
58.e-9:脱碳装置
59.e-10:还原气压缩机
60.e-11:co2缓冲罐
61.e-12:逆水煤气变换反应原料气压缩机
62.e-13:逆水煤气变换反应原料气加热炉
63.e-14:逆水煤气变换反应器
64.e-15:冷凝器
65.e-16:还原气加热炉
66.e-17:电解水制氢装置
67.g1:循环流化床预热器烟气
68.g2:蒸汽
69.g3:还原气
70.g4:还原气加热炉烟气
71.g5:终还原反应后气体
72.g6:预还原炉顶气
73.g7:净化后炉顶气
74.g8:逆变换反应后混合气
75.g9:co276.g10:脱碳气
77.g11:h278.g12:逆变换反应原料气
79.s1:预热后铁矿粉
80.s2:预还原后铁矿粉
81.s3:直接还原铁粉
具体实施方式
82.为了更好地理解本发明,下面结合附图和实施例进一步阐明本发明的内容,但发明的内容不仅仅局限于下面的实施例。
83.以下结合附图对实施例作进一步描述:
84.实施例1:
85.如图1所示,将tfe为67.5%、粒度为0~1mm的铁矿粉加入到循环流化床预热器e-1进行预热。循环流化床预热器的流化和加热介质为还原气加热炉e-16的高温烟气g4,以及经脱碳装置e-9脱除co2并加氢后的还原气g3和空气。还原气g3和空气在循环流化床预热器e-1内发生燃烧反应并放出热量。完成铁矿粉加热过程从循环流化床预热器e-1排出的热烟气g1进入余热锅炉e-2,将锅炉中的水加热产生蒸汽以回收烟气所携带的热量,产生的蒸汽g2送往脱碳装置e-9用于co2吸收液的再生。回收热量以后的烟气作为尾气排出。
86.预热到800℃的铁矿粉s1从循环流化床预热器e-1排出后进入加料装置e-3,在此被加压到0.4mpa后进入循环流化床预还原反应器e-4。循环流化床预还原反应器e-4中通入由鼓泡流化床终还原反应器e-5排出的终还原反应后气体g5,同时通入经脱碳、加氢并加热至850℃的还原气g3。还原气中co体积百分比为30%,h2体积百分比为65%,其余为co2和n2。循环流化床预还原反应器e-4的反应温度控制在750~800℃。
87.经预还原金属化率达到70%的铁矿粉s2从循环流化床预还原反应器e-4排出后进入鼓泡流化床终还原反应器e-5。鼓泡流化床终还原反应器e-5中通入经脱碳、加氢并加热至850℃的还原气g3。还原气中co体积百分比为30%,h2体积百分比为65%,其余为co2和n2。鼓泡流化床终还原反应器e-5的反应温度控制在780~800℃。铁矿粉在鼓泡流化床终还原反应器e-5中经过2.5~3小时的反应被还原到金属化率达到93%。完成终还原反应后的热直接还原铁s3排出鼓泡流化床终还原反应器e-5,送入热压成型机e-6,经热压成型得到产品热压铁块hbi。鼓泡流化床终还原反应器e-5排出的热反应后气体g5送入循环流化床预还原反应器e-4,参与铁矿粉的预还原反应。
88.循环流化床预还原反应器e-4排出的热的炉顶气g6进入换热器e-7,与经压缩机e-10加压后的还原气g3进行热交换。换热后的炉顶气经过洗涤装置e-8进一步降温,同时去除还原过程产生的水。经过洗涤装置e-8降温净化后的炉顶气g7送入脱碳装置e-9,脱除其中的co2。脱碳采用改良mdea法。脱碳后得到co+h2含量大于95%(体积百分比)的脱碳气g10。脱碳气g10与电解水装置e-17产生的纯氢g11混合,以补充在预还原反应器e-4、终还原反应器e-5用于铁矿粉还原所消耗的氢,同时调整混合后的还原气体中co与h2的比例分别达到30%(体积百分比)和65%(体积百分比)。加氢后的还原气g3经压缩机e-10加压、换热器e-7预热后,再由还原气加热炉e-16进一步加热至850℃。热还原气g3分别送至鼓泡流化床反应器终还原e-5、循环流化床预还原反应器e-4,参与铁矿粉的直接还原。
89.由脱碳装置e-9脱除的co2气体g9送入缓冲罐e-11中存贮。由外部输入的纯co2气体也加入到缓冲罐e-11之中。缓冲罐e-11向外输出的co2气体g9先与电解水装置e-17制备的纯氢g11混合,作为逆变换反应的原料气g12。逆变反应原料气g12经压缩机e-12加压到2.5mpa,再由逆变反应原料气加热炉e-13加热至400℃,然后进入逆变换反应器e-14,在此发生逆水煤气变换反应:
90.co2+h2=co+h2o
91.反应产物经冷凝器e-15分离反应中生成的水,然后将反应后的co/co2/h2混合气体g8与净化后的炉顶气g7一起送往脱碳装置e-9,以补充还原气中的co和h2。
92.还原气加热炉e-16、逆变反应原料气加热炉e-14所用的燃料气全部来自净化后的炉顶气g7。
93.整个系统所用的氢气全部来自电解水装置e-17。电解水装置所用电能源自光伏发电、风力发电或水力发电。
94.最终热压铁块hbi的产品指标如下:
[0095][0096]
生产1吨hbi的co2净排放为-36.7kg。
[0097]
实施例2:
[0098]
实施例2与实施例1不同的是,还原气加热炉e-16、逆变反应原料气加热炉e-14所用的燃料气由来自净化后的炉顶气g7和逆水煤气变换后的混合气体g8共同构成,二者各占50%。
[0099]
热压铁块hbi的产品指标如下:
[0100][0101]
当然,本技术领域内的一般技术人员应当认识到,上述实施例仅是用来说明本发明,而非用作对本发明的限定,只要在本发明的实质精神范围内,对上述实施例的变换、变形都将落在本发明权利要求的范围内。