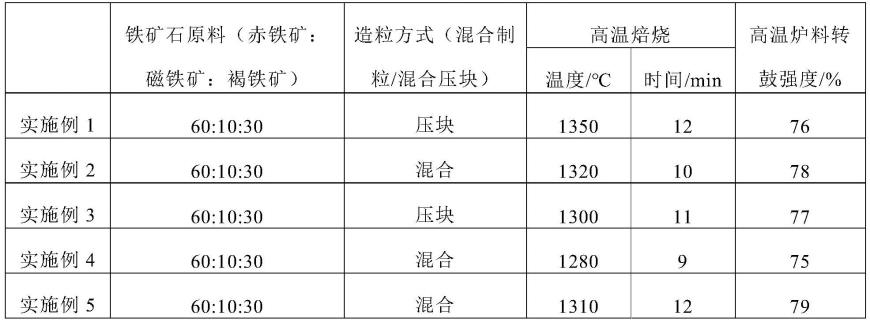
1.本发明属于钢铁冶炼领域的黑色金属冶金原材料预处理技术,尤其涉及一种铁矿石微波高温烧结氢冷还原装置及方法。
背景技术:2.作为全流程重要的工序,炼铁的能源消耗和碳排放占全流程70-80%,碳在炼铁工序中主要作为热源和还原剂。因此,如何寻找替代能源和还原剂,是降低炼铁流程的碳排放的关键;业内普遍认为,随着电力行业逐渐转向以新能源发电,中国的用能方式将向碳中和的方向积极推进,因此,采用电加热代替化石燃料的燃烧,是钢铁行业实现低碳发展的技术方向之一;除此之外,采用氢还原代替碳还原,是降低碳排放的重要技术方向。
3.相关研究者在炼钢领域内,开展了大量研究,比如一些以微波加热代替焦炉煤气或碳加热的技术:中国专利cn100547091c公开了一种铁矿石烧结点火的方法,采用微波高温热风代替焦炉煤气,用于烧结点火,可大幅降低烧结能耗,提高烧结矿强度和成品率。
4.中国专利cn 110273065 b公开了一种铁矿石微波烧结方法,采用微波电加热代替焦粉燃烧,完成铁矿石烧结造块,可彻底解决铁矿石烧结工艺的污染物排放和降低能源消耗,实现绿色环保生产。
5.中国专利cn 103290159b公开了一种微波加热生产直接还原铁粉的方法,采用铁原料60~73%,煤焦类还原剂22~30%,脱硫剂3~7%,膨润土2~3%;加水混合、造球、筛分,得球径为10~15mm的生球;干燥后,送入微波加热炉中升温至 1050~1150℃,还原160~180min,得金属化球团;经破碎、磨细成粒度小于0.2mm 的细粉;经磁选得直接还原铁粉;该技术克服煤基隧道窑罐装外配碳法生产直接还原铁工艺存在的还原时间长、产品质量难以控制、投资大,占地面积大等不足;但是该技术介绍的工业微波炉为料盘装料,间断生产,生产效率方面未介绍。
6.公布号cn 112410546 a公开了一种氢能介质联合微波烧结方法及烧结加热系统将铁矿石、煤、熔剂混合,通过微波点燃混合料内燃料,产生的二氧化碳和水蒸气进入气化炉,转换成co和h2,然后通到烧结罩内燃烧,提高烧结效果,节省能源消耗。产品为常规的烧结矿,废气外排量大幅度减少。上述技术均采用微波电加热技术代替焦炉煤气或碳加热,具有减少造块过程中温室气体排放的作用,有利于环境保护。
7.还有一些以竖炉作为还原装置:公开号cn 112159880a公开了一种氢气炼铁的方法及装置,采用含铁矿石原料在氢气或富氢气体气氛下,采用微波照射实现含铁矿石的富氢或纯氢冶炼,得到直接还原铁;该技术以微波提供热源,以纯氢或富氢气体为还原剂,将样品置于坩埚中,采用kg级规模的微波炉作为核心装备,处理规模有限。
8.中国专利cn103261446b公开了一种用含氢和co的还原气体源生产直接还原铁的方法和装置,使用煤制气制备的含有co和氢的高氧化(co2和h2o)的还原气体生产dri(直接还原铁),突破了以往气基直接还原竖炉使用天然气的限制。
9.中国专利cn 103608468b公开了使用焦炉气和氧气炼钢炉气将氧化铁还原为金属
铁的系统和方法,使得长流程钢铁企业内部的煤气可用于生产直接还原铁,解决了天然气匮乏区域发展直接还原铁的瓶颈。中国专利cn103898265b公开了一种焦炉煤气改质直接还原铁矿石系统装置及方法利用炼焦过程产生的焦炉煤气,将其改质转化制成富氢还原气(h2和co),然后将其引入竖炉直接还原铁矿石;该技术可以减少铁矿石还原过程中的二氧化碳排放,与天然气进行直接还原铁的路线不同,可更好的适用中国的能源资源特点。
10.公开号cn110484672a公开了一种气基竖炉生产直接还原铁的方法,采用气基竖炉生产直接还原铁的方法,利用高炉筛下碎焦与co2的布多尔反应吸收热量,可有效降低竖炉内温度,减少炉料热结产生,同时有效利用还原放热能量,提高了整体能量利用率,生成的co提高了炉内还原势,促进了铁矿还原,有利于促进气基竖炉直接还原铁矿技术的应用;其铁矿石为球团或块矿,及两者的混合物。上述技术以竖炉作为还原装置,具有处理量大、效率高等优点,铁矿石常温加入泸定后,与高温还原气进行热交换、升温并达到还原所需的温度,逐步还原至较高的金属化率,然后作为电炉的原料,搭配废钢,得到钢;此类处理方法存在固有的热力学限制环节,主要在于氧化铁的比热容大,加之以天然气或焦炉煤气重整后,主要以氢为还原剂,还原过程中大量吸热,其维持还原温度比较困难,因此需要对气体进行多次加热、循环,整个流程中,氢的利用率比较低,通常在30%左右,使得气基直接还原流程难以在世界范围内推广,只在天然气价格便宜的中东、南美等国家有一定发展;
11.鉴于上述情况,业界亟待研究新的铁矿石烧结还原技术,能够解决传统的铁矿石造块过程因化石燃料燃烧带来的污染物排放量大、直接还原氢还原利用率偏低以及烧结还原过程中能耗偏高的三大技术难题,从而降低传统钢铁流程的碳排放,为传统流程的绿色发展创造有利的条件。
技术实现要素:12.针对现有技术中存在的上述缺陷,本发明的目的是提供一种铁矿石微波高温烧结氢冷还原装置及方法,将铁矿石氧化焙烧过程与炉料还原有机结合,利用微波加热将铁矿石烧结,然后再利用铁矿石本身的高温提供还原过程所需热量,得到具有一定金属化率的预还原炉料,解决了传统的铁矿石造块过程因化石燃料燃烧带来的污染物排放量大、直接还原氢还原利用率偏低以及烧结还原过程中能耗偏高的三大技术难题,从而降低传统钢铁流程的碳排放,为传统流程的绿色发展创造有利的条件。
13.为实现上述目的,本发明采用如下技术方案:
14.本发明的第一方面提供了一种铁矿石微波高温烧结氢冷还原装置,包括连续带式焙烧系统和氢基竖炉还原系统;
15.所述连续带式焙烧系统用于含铁矿石原料的干燥、预热、焙烧;所述连续带式焙烧系统采用微波电加热,该连续带式焙烧系统沿含铁矿石原料运动方向上设有干燥段、预热段和高温焙烧段;
16.所述氢基竖炉还原系统用于将经所述连续带式焙烧系统焙烧得到的高温炉料还原;该氢基竖炉还原系统包括氢基竖炉、上料系统、还原气系统、冷却系统以及下料系统;所述上料系统设于所述氢基竖炉上部;所述还原气系统用于提供还原处理所需的还原气;所述冷却系统用于将还原后的预还原炉料进行冷却处理;所述下料系统设于所述氢基竖炉底部。
17.优选地,所述连续带式焙烧系统的高温焙烧段的上方设有进气口,所述干燥段的上方设有排气口;所述排气口通过风机与布袋除尘器连接;和/或
18.所述上料系统包括上部料斗、中部料斗以及下部料斗;所述上部料斗、中部料斗以及下部料斗之间均设有阀门;和/或
19.所述还原气系统包括余热锅炉/管式换热器、第一洗涤器、循环风机以及加压风机;所述余热锅炉/管式换热器的一端与所述氢基竖炉顶部的烟气出口连接,另一端与所述第一洗涤器的进气口连接;所述循环风机一端与所述第一洗涤器的出气口连接,另一端与所述氢基竖炉中部的环形风口连通;所述加压风机为所述循环风机出来的还原气加压;和/或
20.所述冷却系统包括补氧燃烧单元、余热回收单元、第二洗涤器以及冷却风机;所述补氧燃烧单元与所述氢基竖炉下部的出气口连接;所述余热回收单元一端与所述补氧燃烧单元连接,另一端与所述第二洗涤器的进气口连接;所述冷却风机一端与所述第二洗涤器的出气口连接,另一端与所述氢基竖炉下部的进气口连通;所述出气口设于所述进气口上部。
21.优选地,所述上部料斗上设有通气管道;所述中部料斗上设有均压装置;所述下部料斗上设有万向布料器。
22.本发明的第二方面提供了一种铁矿石微波高温烧结氢冷还原方法,该铁矿石微波高温烧结氢冷还原方法使用本发明第一方面所述的铁矿石微波高温烧结氢冷还原装置,所述铁矿石微波高温烧结氢冷还原方法将含铁矿石原料装入连续带式焙烧系统中,通过微波电加热进行高温焙烧后,直接送入氢基竖炉还原系统进行还原。
23.优选地,所述铁矿石微波高温烧结氢冷还原方法包括以下步骤:
24.(1)向铁矿石原料中配入白云石、石灰石、生石灰/消石灰,加水,混合制粒或混合压块后得到所述含铁矿石原料;
25.(2)将所述含铁矿石原料装入铺好底料的连续带式焙烧系统中,利用微波电加热进行干燥、预热和高温焙烧处理得到高温炉料;
26.(3)所述高温炉料进入氢基竖炉还原系统中,与还原气发生还原反应,再经冷却气进行冷却处理后得到预还原炉料或热压块铁。
27.优选地,所述步骤(1)中,所述铁矿石原料选自磁铁矿、赤铁矿和褐铁矿中一种或几种;和/或
28.所述步骤(2)中,所述底料的厚度为20-50mm,装入所述含铁矿石原料后,料层总高度为200-300mm;和/或
29.所述底料采用粒度小于5mm、熔点大于1300℃的赤铁矿粉;和/或
30.所述含铁矿石原料中含有磁铁矿时,在所述含铁矿石原料上方补入空气,控制氧含量大于14%;和/或
31.所述高温焙烧过程中,控制高温焙烧温度为1250-1350℃,高温焙烧时间为 5-10min。
32.优选地,所述步骤(3)中,所述氢基竖炉还原系统的氢基竖炉的压力为 200-250kpa;和/或
33.所述还原气采用纯氢或焦炉煤气;和/或
34.所述还原反应过程中,所述还原气的消耗量为800-1200m3/t,还原反应时间为 40-100min;和/或
35.所述冷却气采用氮气和少量天然气;和/或
36.所述冷却处理过程中,所述冷却气流量为1200-1800m3/t;和/或
37.所述预还原炉料或热压块铁的出料温度低于150℃;
38.所述预还原炉料或热压块铁的金属化率≥40%。
39.优选地,所述步骤(3)中,所述还原气为纯氢,所述还原反应过程中,氢利用率达到55%以上;
40.所述预还原炉料或热压块铁的金属化率为40-66%。
41.优选地,所述步骤(3)中,所述还原反应过程中,氢利用率达到60%以上;和/或
42.所述高温炉料通过耐高温料罐进入所述氢基竖炉还原系统的上料系统中,再经所述上料系统布料进入所述氢基竖炉还原系统的氢基竖炉中,在所述氢基竖炉的中部参与还原反应;
43.所述还原气通过还原气系统参与还原反应,还原反应后的烟气从所述氢基竖炉顶部的烟气出口进入所述还原气系统,经余热回收、洗涤后,再进入所述氢基竖炉的中部参与还原反应;
44.所述冷却气通过冷却系统参与冷却处理,冷却处理后的混合气体从所述氢基竖炉下部的出气口进入所述冷却系统,经补氧燃烧、余热回收、洗涤后,再进入所述氢基竖炉的下部参与冷却处理。
45.优选地,所述步骤(3)中,所述上料系统的布料方式为:
46.所述高温炉料进入所述上料系统后,依次通过上料系统的上部料斗、中部料斗和下部料斗后再布入所述氢基竖炉中;
47.所述高温炉料装入所述上部料斗后,通入高温高压蒸汽或高温高压氮气进行置换,确保所述上部料斗内的氧含量≤1%后,打开所述上部料斗下方的阀门,所述高温炉料完全进入所述中部料斗后,关闭所述上部料斗下方的阀门,采用与所述氢基竖炉内顶煤气成分相同的煤气完成均压过程,所述均压完成后,打开所述中部料斗下方的阀门,所述高温炉料完全进入所述下部料斗后,关闭所述中部料斗下方的阀门,打开所述下部料斗下部的阀门,将所述高温炉料布入到所述氢基竖炉中。
48.本发明的有益效果为:
49.1、本发明所提供的铁矿石微波高温烧结氢冷还原装置及方法,先利用微波电加热将铁矿石烧结得到高温炉料,然后再利用高温炉料本身的高温提供还原过程所需热量,得到金属化率为40-66%的预还原炉料,解决了传统的铁矿石造块过程因化石燃料燃烧带来的污染物排放量大、直接还原氢还原利用率偏低以及烧结还原过程中能耗偏高的三大技术难题,从而降低传统钢铁流程的碳排放,为传统流程的绿色发展创造有利的条件;
50.2、本发明所提供的铁矿石微波高温烧结氢冷还原装置及方法,将铁矿石氧化焙烧过程与炉料还原有机结合,取消炉料冷却和直接还原炉料升温过程,利用纯氢或富氢气体冷却还原,流程更简洁,能源利用效率提高;
51.3、本发明所提供的铁矿石微波高温烧结氢冷还原装置及方法,利用高温炉料的物理热,满足氢还原和气体升温所需热量,使得氢还原热力学条件更合理,能大幅度提高氢利
用率;
52.4、本发明所提供的铁矿石微波高温烧结氢冷还原装置及方法,利用微波穿透深度大、温度均匀性好、整体加热的特点,用于炉料干燥、预热和高温焙烧,彻底消除铁矿石氧化焙烧工艺因燃料燃烧产生的污染物和温室气体,环境更为友好;
53.5、本发明所提供的铁矿石微波高温烧结氢冷还原装置及方法,全流程采用微波电加热和纯氢或富氢气体还原的方式,可以实现无碳生产预还原炉料;将该预还原炉料用于传统高炉或转炉,可大幅度减少钢铁流程的碳排放。
54.6、本发明所提供的铁矿石微波高温烧结氢冷还原装置及方法,可简化氢基竖炉气体处理系统,提高氢气利用率,将制备的预还原炉料作为高炉炉料,可大幅度降低高炉燃料消耗和碳排放,是一种低碳、绿色的铁矿石烧结还原工艺。
附图说明
55.通过阅读参照以下附图对非限制性实施例所作的详细描述,本发明的其它特征、目的和优点将会变得更明显:
56.图1为本发明的铁矿石微波高温烧结氢冷还原装置的结构示意图。
具体实施方式
57.为了能更好地理解本发明的上述技术方案,下面结合附图和实施例进一步说明本发明的技术方案。
58.结合图1所示,本发明所提供的铁矿石微波高温烧结氢冷还原装置,包括连续带式焙烧系统1和氢基竖炉还原系统2;
59.结合图1所示,连续带式焙烧系统1用于含铁矿石原料的干燥、预热、焙烧;该连续带式焙烧系统1采用微波电加热,其沿含铁矿石原料运动方向上依次设有干燥段a、预热段b和高温焙烧段c;在进一步的优选方案中,该连续带式焙烧系统 1的高温焙烧段c的上方设有进气口,干燥段a的上方设有排气口;排气口通过风机11与布袋除尘器12连接;连续带式焙烧系统1焙烧后得到的高温炉料通过耐高温料罐输送至上料系统21中。
60.结合图1所示,氢基竖炉还原系统2用于将经连续带式焙烧系统1焙烧得到的高温炉料还原;该氢基竖炉还原系统2包括氢基竖炉22、上料系统21、还原气系统23、冷却系统24以及下料系统;上料系统21设于氢基竖炉22上部;还原气系统23用于提供还原反应中所需的还原气,另外该还原气系统23还可处理还原反应中产生的烟气;冷却系统24用于将还原后的预还原炉料进行冷却处理,提供冷却处理所需的冷却气,另外还可处理冷却后产生的混合气体;下料系统设于氢基竖炉 22底部。
61.结合图1所示,上料系统21包括上部料斗211、中部料斗212以及下部料斗 213;为了便于各个部分料斗内保持封闭环境,上部料斗211、中部料斗212以及下部料斗213之间均设有阀门;在具体实施例中,上部料斗211内装入高温炉料(~ 1200℃)后,为了确保上部料斗211内氧含量≤1%,上部料斗211还设有通气管道,便于通入高温高压蒸汽或高温高压氮气置换空气中的氧气。为了保证中部料斗内压力均衡,中部料斗212上设有均压装置,可采用与竖炉内顶煤气成分相同的煤气完成均压过程。为了方便将高温炉料布入氢基竖炉22中,下部料斗213的下方设有万向布料器。
62.结合图1所示,还原气系统23用于提供还原反应中所需的还原气,其包括余热锅炉/管式换热器231、第一洗涤器232、循环风机233以及加压风机234;余热锅炉/管式换热器231一端与氢基竖炉22顶部的烟气出口连接,另一端与第一洗涤器232的进气口连接;循环风机233一端与第一洗涤器232的出气口连接,另一端与氢基竖炉22中部的环形风口连通;加压风机234为循环风机233出来的还原气加压;在具体使用时,还原气从氢基竖炉22的环形风口进入,在氢基竖炉22中部与来自上料系统21的高温炉料接触,还原气一边被高温球团加热(吸收高温炉料的温度,将高温炉料冷却),一边与高温炉料发生还原反应,反应后从氢基竖炉22 顶部的烟气出口经余热锅炉/管式换热器231回收预热、第一洗涤器232洗涤后,再在循环风机233和加压风机234作用下通过环形风口参与还原反应。
63.结合图1所示,冷却系统24包括补氧燃烧单元241、余热回收单元242、第二洗涤器243以及冷却风机244;补氧燃烧单元241与氢基竖炉22下部的出气口连接;余热回收单元242一端与补氧燃烧单元241连接,另一端与第二洗涤器243的进气口连接;冷却风机244一端与第二洗涤器243的出气口连接,另一端与氢基竖炉22 下部的进气口连通;其中出气口设于进气口上部;在具体使用时,冷却气从氢基竖炉22下部的进气口进入,在氢基竖炉22下部将还原反应后的预还原炉料冷却,冷却处理后的混合气体经补氧燃烧单元241补氧燃烧、余热回收单元242回收预热、第二洗涤器243洗涤后,再在冷却风机244的作用下通过氢基竖炉22下部的进气口参与冷却处理。
64.下料系统,将冷却后的预还原炉料或热压块铁hbi进行出料。
65.结合图1所示,本发明所提供的铁矿石微波高温烧结氢冷还原方法,使用上述的铁矿石微波高温烧结氢冷还原装置,该方法为:在连续带式焙烧系统1中含铁矿石原料通过微波电加热进行高温焙烧后,直接送入氢基竖炉还原系统2进行还原;具体包括以下步骤:
66.(1)向铁矿石原料中配入白云石、石灰石、生石灰/消石灰,加水,混合制粒或混合压块后得到含铁矿石原料;
67.具体过程如下:将磁铁矿、赤铁矿和褐铁矿中一种或几种进行搭配得到铁矿石原料,然后配入白云石、石灰石、生石灰/消石灰等熔剂,调至适合的碱度和mgo 含量(碱度和mgo含量根据高炉造渣需要,来调节白云石、石灰石、生石灰/消石灰配入量),加水,混合制粒或者混合压块得到粒度均匀的含铁矿石原料(混合料或团块)。
68.(2)将含铁矿石原料装入铺好底料的连续带式焙烧系统1中,利用微波电加热进行干燥、预热和高温焙烧处理得到高温炉料;
69.具体过程如下:将步骤(1)中制备的含铁矿石原料铺好底料的连续带式焙烧系统1的台车上,控制底料的厚度为20-50mm,装入含铁矿石原料后,料层总高度为200-300mm,其中底料采用粒度小于5mm、熔点大于1300℃的赤铁矿粉;然后采用微波电加热将含铁矿石原料进行干燥、预热和高温焙烧得到高温炉料,在微波电加热过程中,料层中无气流穿透,以保持料层中高温状态,若含铁矿石原料中配入磁铁矿,为保证其完全氧化,料层上部补入少量空气,使氧含量大于14%,利用铁氧化物强吸波性,和微波穿透性,使得含铁矿石原料在台车上快速升温,控制高温焙烧温度为1250-1350℃,高温保持时间5-10min,以高温炉料(烧结矿或团块) 冷态转鼓强度大于75%为目标,调节微波功率,从而调节焙烧温度和焙烧时间;在微波电加热过程中,含铁矿石原料排除的少量水蒸气、co2进入废气中,通过风机 11,经布袋除尘器12除尘,满足超低排放标准后,通过烟囱13外排。
70.(3)高温炉料进入氢基竖炉还原系统2中,与还原气发生还原反应,再经冷却气进行冷却处理后得到预还原炉料或热压块铁:高温炉料通过耐高温料罐进入氢基竖炉还原系统2的上料系统21,然后通过上料系统21进入氢基竖炉还原系统2 的氢基竖炉22中,在氢基竖炉22的中部进行还原反应,还原反应后在氢基竖炉22 的下部进行冷却处理得到预还原炉料;其中还原反应后的烟气从氢基竖炉22顶部的烟气出口进入还原气系统23,经余热回收、洗涤后再通过还原气系统23进入氢基竖炉22的中部参与还原反应;冷却处理后的混合气体从氢基竖炉22下部的出气口进入冷却系统24,经补氧燃烧、余热回收、洗涤后再通过冷却系统24进入氢基竖炉22的下部参与冷却处理;具体过程如下:
71.(3.1)布料:步骤(2)中制备的高温炉料通过耐高温料罐进入氢基竖炉还原系统2的上料系统21,依次进入上料系统21的上部料斗211、中部料斗212和下部料斗213后再布入氢基竖炉22中,在此过程中高温炉料装入上部料斗211后,通入高温高压蒸汽或高温高压氮气进行置换,确保上部料斗211内的氧含量≤1%后,打开上部料斗211下方的阀门,高温炉料进入完全中部料斗212后,关闭上部料斗 211下方的阀门,采用与氢基竖炉22内顶煤气成分相同的煤气完成均压过程,均压完成后,打开中部料斗212下方的阀门,高温炉料完全进入下部料斗213后,关闭中部料斗212下方的阀门,打开下部料斗213下部的阀门,通过万向布料器将高温炉料布入到氢基竖炉22中。
72.(3.2)还原反应:高温炉料在氢基竖炉22的中部进行还原反应,其中还原气采用纯氢或焦炉煤气,优选纯氢;还原气从氢基竖炉22中部的环形风口进入,与 500℃左右的热态高温炉料接触后,还原气一边被高温球团加热(吸收高温炉料的温度,将高温炉料冷却),一边与高温炉料发生还原反应,随着气体上升,还原气的浓度逐渐降低,但由于高温炉料的温度逐渐升高,故还原反应一直在进行,待还原反应后的烟气从氢基竖炉22顶部的烟气出口排出后,其温度被加热到1000℃以上,通过管式换热器或余热锅炉进行余热回收,利用顶煤气中的物理热,之后再用第一洗涤器232脱出烟气中的h2o和粉尘,也可根据工艺需要,在第一洗涤器232中喷入少量氨水,脱除烟气中co2和so2,使得烟气经简单洗涤处理后,变成以h2和 co为主高还原势气体,该还原气再通过循环风机233,再次参与到还原反应中;在还原反应过程中,还原气的消耗量为800-1200m3/t,还原反应时间为40-100min,氢基竖炉还原系统2的氢基竖炉22的压力为200-250kpa。
73.(3.3)冷却处理:高温炉料经还原反应后在氢基竖炉22的下部采用冷却气进行冷却处理,冷却处理后的混合气体从氢基竖炉22下部的出气口进入冷却系统24,经补氧燃烧、余热回收、洗涤后再通过冷却系统24通过氢基竖炉22下部进气口参与到冷却处理中;在冷却处理中,采用氮气和少量天然气,在冷却的同时,还原后的物料中含有海绵铁(dri)可催化ch4裂解,并可形成少量fe3c,完成渗碳过程,以防止dri再度氧化;在上述过程中,冷却气流量为1200-1800m3/t;最终氢基竖炉 22出料为预还原炉料或热压块铁,其出料温度低于150℃,根据后道工序的要求确定产品的金属化率。
74.在上述的铁矿石微波高温烧结氢冷还原方法中,制得的预还原炉料或热压块铁的金属化率≥40%,氢利用率达到40%以上。在进一步的方案中,预还原炉料或热压块铁的金属化率为40-66%,氢利用率达到50%以上。
75.下面结合具体的例子对本发明的铁矿石微波高温烧结氢冷还原装置及方法进一步介绍;下面所实施例的铁矿石微波高温烧结氢冷还原装置及方法采用上述的装置和方
法;
76.实施例1-5
77.实施例1-5中的铁矿石原料如表1所示,配入白云石、石灰石、生石灰/消石灰后,加水,混合制粒或压块得到含铁矿石原料,然后转入连续带式焙烧系统内经干燥、预热、高温焙烧后制得高温炉料,其焙烧参数如表1所示;
78.表1铁矿石原料及高温焙烧参数
[0079][0080]
将高温炉料转入氢基竖炉还原系统中进行还原,采用纯氢或焦炉煤气进行还原后经氮气和甲烷冷却、渗碳得到预还原炉料或热压块铁,其中还原参数如表2所示;
[0081]
表2高温炉料及还原参数
[0082][0083]
实施例1中,含铁矿石原料的碱度为1.8,采用压块方式制成,团块尺寸为 35*50*20mm椭球型,1350℃焙烧12min,得到高温炉料的冷态转鼓强度为76%,高温炉料通纯氢进行还原,氢利用率为54%,冷却后得到的预还原炉料金属化率可达66%。
[0084]
实施例2中,含铁矿石原料的碱度为1.9,采用强力混合机/圆筒混合机混合制粒,1320℃焙烧10min,得到高温炉料的冷态转鼓强度达到78%,高温炉料通氢气还原,氢利用率为62%,冷却后得到的预还原炉料金属化率为51%。
[0085]
实施例3中,含铁矿石原料的碱度为0.9,采用压块方式制成,团块尺寸 35*50*20mm椭球型,1300℃焙烧11min,得到高温炉料的冷态转鼓强度达到77%,高温炉料通纯氢还原,氢利用率为65%,冷却后得到的预还原炉料的金属化率为64%。
[0086]
实施例4中,含铁矿石原料的碱度为1.8,采用强力混合机/圆筒混合机混合制粒,1280℃焙烧9min,得到高温炉料的冷态转鼓强度达到75%,高温炉料通富氢气还原,氢利用
率为45%,冷却后得到的预还原炉料的金属化率为53%。
[0087]
实施例5中,含铁矿石原料的碱度为1.9,采用强力混合机/圆筒混合机混合制粒,1310℃焙烧12min,得到高温炉料的冷态转鼓强度达到79%,高温炉料通富氢气还原,氢利用率为43%,冷却后得到的预还原炉料的金属化率为52%。
[0088]
综上所述,本发明所提供的铁矿石微波高温烧结氢冷还原装置及方法,将铁矿石氧化焙烧过程与炉料还原有机结合,先利用微波电加热将铁矿石烧结得到高温炉料,然后再利用高温炉料本身的高温提供还原过程所需热量,得到金属化率为40-66%的预还原炉料,解决了传统的铁矿石造块过程因化石燃料燃烧带来的污染物排放量大、直接还原氢还原利用率偏低以及烧结还原过程中能耗偏高的三大技术难题,从而降低传统钢铁流程的碳排放,为传统流程的绿色发展创造有利的条件;将铁矿石氧化焙烧过程与炉料还原有机结合,取消炉料冷却和直接还原炉料升温过程,利用纯氢或富氢气体冷却还原,流程更简洁,能源利用效率提高;该铁矿石微波高温烧结氢冷还原装置及方法,利用高温炉料的物理热,满足氢还原和气体升温所需热量,使得氢还原热力学条件更合理,能大幅度提高氢利用率;利用微波穿透深度大、温度均匀性好、整体加热的特点,用于炉料干燥、预热和高温焙烧,彻底消除铁矿石氧化焙烧工艺因燃料燃烧产生的污染物和温室气体,环境更为友好;全流程采用微波电加热和纯氢或富氢气体还原的方式,可以实现无碳生产预还原炉料;将该预还原炉料用于传统高炉或转炉,可大幅度减少钢铁流程的碳排放。该铁矿石微波高温烧结氢冷还原装置及方法,可简化氢基竖炉气体处理系统,提高氢气利用率,将制备的预还原炉料作为高炉炉料,可大幅度降低高炉燃料消耗和碳排放,是一种低碳、绿色的铁矿石烧结还原工艺。
[0089]
本技术领域中的普通技术人员应当认识到,以上的实施例仅是用来说明本发明,而并非用作为对本发明的限定,只要在本发明的实质精神范围内,对以上所述实施例的变化、变型都将落在本发明的权利要求书范围内。