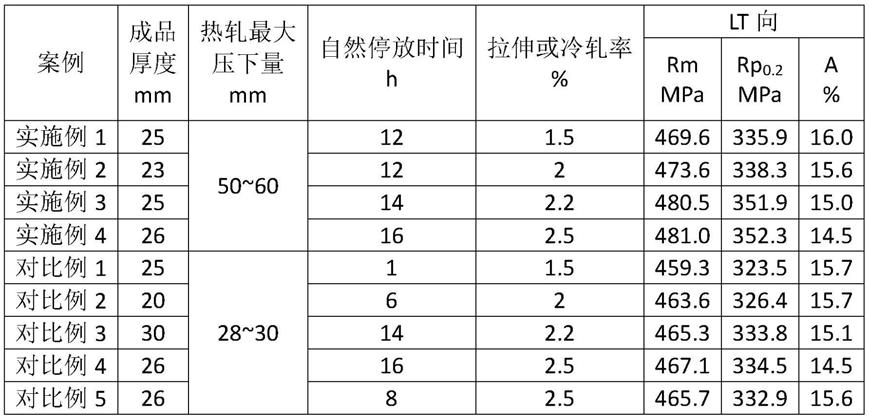
一种提高2024
‑
t3板材强度的方法
技术领域
1.本发明属于铝合金加工领域,涉及一种具有高折弯性能的5052铝合金及其制备方法。
背景技术:2.2024铝合金属al
‑
cu
‑
mg系高强硬铝合金,以其高强、高韧、耐热、低比重等良好的综合性能,广泛应用于军用与民用工业上。2024常用的状态为t3态,其传统工艺流程为:铸锭
‑
加热
‑
热轧
‑
固溶
‑
拉伸
‑
自然时效。
3.传统2024
‑
t3厚板生产采用多道次、小压下量的热轧方式,心部粗大第二相不能充分破碎,固溶阶段不能充分回溶;固溶淬火后进行1.5%~3%的拉伸以提高合金强度,拉伸虽然能提高合金的强度,但由于其横向变形较小,导致横向强度提高幅度有限。
技术实现要素:4.有鉴于此,本发明的目的在于提供一种提高2024
‑
t3板材强度的方法,以解决当前2024
‑
t3板材生产工艺的不足。
5.为达到上述目的,本发明提供如下技术方案:
6.一种提高2024
‑
t3板材强度的方法,包括以下步骤:
7.s1.配料:按照以下合金元素及质量百分比配制铝合金原料,si≤0.08%、fe≤0.15%、cu:4.4~4.7%、mn:0.5~0.7%、mg:1.3~1.6%、cr≤0.05%、zn≤0.06%、ti:0.018~0.032%,单个杂质≤0.05%,杂质合计≤0.15%,余量为al;
8.s2.熔铸:将配置好的铝合金原料加入到半连续铸造炉熔铸成铝合金铸锭;
9.s3.均匀化:将熔铸得到的铝合金铸锭进行均匀化热处理,均匀化温度为490~500℃,保温时间为15~25h;
10.s4.锯切:将均匀化后的铝合金铸锭切头尾,并用铣床铣去表面凝壳层;
11.s5.加热:将锯切后的铝合金铸锭在加热炉中加热到炉气温度420~460℃,保温2~6h出炉;
12.s6.热轧:将加热后的铝合金铸锭热轧成板材,最大压下量为50~60mm;
13.s7.固溶:将板材在辊底炉中进行固溶处理,固溶制度为(496
±
3)℃
×
(120+200)min;
14.s8.自然停放:将固溶后的板材进行12~16h的自然停放;
15.s9.冷轧:将自然停放后的板材在轧件上按照纵向上1.5~2.5%压下率经一道次冷轧成成品厚度;
16.s10.自然时效:将冷轧后的板材自然时效96h。
17.进一步,步骤s2中,将配置好的铝合金原料加入到半连续铸造炉经熔炼
‑
扒渣
‑
除气
‑
静置
‑
过滤
‑
铸造工序生产出铝合金铸锭。
18.进一步,步骤s3中,均匀化热处理后,风冷4~8h。
19.进一步,步骤s7中,固溶后进行喷淬。
20.进一步,还包括以下步骤:
21.s11.定尺:将自然时效后的板材用精密锯进行锯切定尺,验收包装。
22.进一步,成品板材的屈服强度在336~352mpa之间,抗拉强度在470~481mpa之间。
23.本发明的有益效果在于:
24.(1)对于2024
‑
t3板材生产,现有工艺热轧采用多道次、小压下量(≤35mm)方式,心部粗大第二相不能完全破碎,固溶阶段不能充分回溶,导致最终强度不高。本发明采用少道次、大压下量的方式,最大压下量控制在50~60mm,在保证热轧板坯不过烧情况下,充分破碎第二相,使第二相在后续固溶阶段更容易回溶到基体。
25.(2)现有工艺在固溶后会进行1.5~3%的拉伸,达到消除内应力和提高力学性能的目的,拉伸是单一方向变形,对横向强度贡献并不明显。本发明用冷轧代替拉伸,冷轧压下率控制在1.5~3%;在相同的变形率下,横向屈服强度大幅度提高。这是因为冷轧过程中会产生沿纵向和厚度方向的分量,内部金属受到压缩产生横向的流变,在横向产生轻微宽展变形,造成加工强化,使横向抗拉和屈服产生不同程度的提高。
26.(3)过饱和固溶体在室温下停放会形成纳米级的析出相,析出相的尺寸、分布会对最终性能产生影响,析出相的尺寸、分布与自然停放时间有关。如果自然停放时间过短,析出相不能形成大量有效的形核质点,冷变形后最终强度较低;自然停放时间过长,第二相析出过多,尺寸过大,冷变形后自然时效驱动力不足,强度降低,还会造成最终塑性有所降低。本发明将自然停放时间控制在12~16h,生产出横向高强度板材。
27.本发明的其他优点、目标和特征在某种程度上将在随后的说明书中进行阐述,并且在某种程度上,基于对下文的考察研究对本领域技术人员而言将是显而易见的,或者可以从本发明的实践中得到教导。本发明的目标和其他优点可以通过下面的说明书来实现和获得。
具体实施方式
28.以下通过特定的具体实例说明本发明的实施方式,本领域技术人员可由本说明书所揭露的内容轻易地了解本发明的其他优点与功效。本发明还可以通过另外不同的具体实施方式加以实施或应用,本说明书中的各项细节也可以基于不同观点与应用,在没有背离本发明的精神下进行各种修饰或改变。
29.实施例1:
30.一种提高2024
‑
t3板材强度的方法,包括以下步骤:
31.s1.配料:按照以下合金元素及质量百分比配制铝合金原料,si≤0.08%、fe≤0.15%、cu:4.4~4.7%、mn:0.5~0.7%、mg:1.3~1.6%、cr≤0.05%、zn≤0.06%、ti:0.018~0.032%,单个杂质≤0.05%,杂质合计≤0.15%,余量为al;
32.s2.熔铸:将配置好的铝合金原料加入到半连续铸造炉熔铸成铝合金铸锭,铝合金铸锭规格450mm
×
1580mm
×
4500mm;
33.s3.均匀化:将熔铸得到的铝合金铸锭进行均匀化热处理,均匀化温度为490~500℃,保温时间为15~25h,出炉风冷4~8h;
34.s4.锯切:将均匀化后的铝合金铸锭切头尾,并用铣床铣去表面凝壳层;
35.s5.加热:将锯切后的铝合金铸锭在加热炉中加热到炉气温度420~460℃,保温2~6h出炉;
36.s6.热轧:将加热后的铝合金铸锭热轧成板材,最大压下量为50~60mm;
37.s7.固溶:将板材在辊底炉中进行固溶处理,固溶制度为(496
±
3)℃
×
(120+200)min,然后进行喷淬;
38.s8.自然停放:将固溶后的板材进行12h的自然停放;
39.s9.冷轧:将自然停放后的板材在轧件上按照纵向上1.5%压下率经一道次冷轧成成品厚度;
40.s10.自然时效:将冷轧后的板材自然时效96h。
41.实施例2:
42.实施例2与实施例1的主要区别在于:冷轧压下率控制在2%。
43.实施例3:
44.实施例3与实施例1的主要区别在于:自然停放时间14h,冷轧压下率2.2%。
45.实施例4:
46.实施例4与实施例1的主要区别在于:自然停放时间16h,冷轧压下率2.5%。
47.对比例1:
48.对比例1与实施例1的主要区别在于:步骤s6中,热轧的最大压下量为28~30mm。步骤s8中,自然停放1h。步骤s9中,对板材按照纵向上1.5%的拉伸变形,而非冷轧。
49.对比例2:
50.对比例2与实施例1的主要区别在于:步骤s6中,热轧的最大压下量为28~30mm。步骤s8中,自然停放6h。步骤s9中,对板材按照纵向上2%的拉伸变形,而非冷轧。
51.对比例3:
52.对比例3与实施例1的主要区别在于:步骤s6中,热轧的最大压下量为28~30mm。步骤s8中,自然停放14h。步骤s9中,对板材按照纵向上2.2%的拉伸变形,而非冷轧。
53.对比例4:
54.对比例4与实施例1的主要区别在于:步骤s6中,热轧的最大压下量为28~30mm。步骤s8中,自然停放16h。步骤s9中,对板材按照纵向上2.5%的拉伸变形,而非冷轧。
55.对比例5:
56.对比例6与实施例1的主要区别在于:步骤s6中,热轧的最大压下量为28~30mm。步骤s8中,自然停放8h。步骤s9中,对板材按照纵向上2.5%的拉伸变形,而非冷轧。
57.实施例与对比例的检测标准按照astm b557进行,lt向拉伸试样取样位置在板材宽度中心、厚度1/4处,力学测试结果如表1所示。
58.表1实施例1~4与对比例1~5的力学测试结果
[0059][0060]
从对比例结果可以看出:在小压下量及拉伸的情况下,lt向(横向)屈服强度在323.5~335mpa,抗拉强度在459~467mpa之间。本发明采用大压下量(最大压下量50~60mm),将自然停放时间控制在12~16h,冷轧加工率控制在1.5~2.5%之间,得到了综合力学性能更佳的板材,其屈服强度在336~352mpa之间,抗拉强度在470~481mpa之间,相较于对比例而言,提高了板材强度。
[0061]
从结果可看出,采用道次大压下量(50~60mm)的热轧方式,控制自然停放时间12~16h、冷轧加工率在1.5~2.2%之间,得到了拉伸性能比现有工艺高10~18mpa的板材。
[0062]
最后说明的是,以上实施例仅用以说明本发明的技术方案而非限制,尽管参照较佳实施例对本发明进行了详细说明,本领域的普通技术人员应当理解,可以对本发明的技术方案进行修改或者等同替换,而不脱离本技术方案的宗旨和范围,其均应涵盖在本发明的权利要求范围当中。