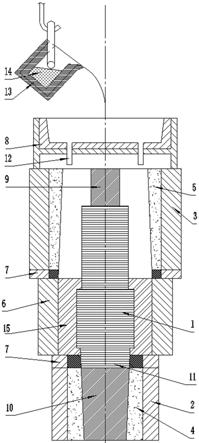
1.本发明属于冶金技术领域,尤其涉及一种节能型细晶无限冷硬轧辊的制备方法。
背景技术:2.在冶金企业中,铸造轧辊的生产方式一般采用整体铸造或离心复合铸造,前者由于外层、芯部为同材质,生产成本相对较高,后者虽然芯部材质为球墨铸铁,成本相对降低,但轧辊工作层使用完毕,剩余芯部及辊颈主轴作为废料处理,造成极大浪费,增大了企业的运行成本。因此,急需研发一种新技术、新方法,将报废轧辊剩余的芯部及辊颈主轴得以重复利用,来降低生产成本,提高企业产品市场竞争力。
技术实现要素:3.本发明的目的是提供一种节能型细晶无限冷硬轧辊的制备方法,旨在解决上述现有技术中报废轧辊废弃造成浪费的技术问题。
4.为解决上述技术问题,本发明所采取的技术方案是:一种节能型细晶无限冷硬轧辊的制备方法,包括以下步骤:步骤a:将达到报废直径的报废轧辊重新加工成符合要求尺寸的芯轴,所述报废轧辊为无限冷硬铸铁轧辊;步骤b:根据需要生产的轧辊规格尺寸选择底箱及冒口箱,并在底箱内壁预制底颈砂型,及在冒口箱内壁预制冒颈砂型;步骤c:根据需要生产的轧辊规格尺寸选择冷型,将冷型加热至挂砂温度并进行挂砂操作,冷型的内腔直径比轧辊的辊身直径大30
‑
35mm,对冷型的内腔表面进行清理,清理完毕装入电阻炉加热至250
‑
350℃开始挂砂,挂砂厚度3
‑
15mm;步骤d:待浇注的芯轴利用电阻炉加热至500
‑
900℃,并恒温5
‑
8小时;步骤e:根据需要生产的轧辊进行轧辊外层的无限冷硬材质配料,并根据轧辊外层的铁水量选择中频炉进行熔炼;步骤f:将底箱、中圈、冷型及冒口箱组装为铸造工装, 将芯轴垂直置于铸造工装内腔中部,组装时保持芯轴与冷型、底箱及冒口箱内腔同轴且垂直于地平面;步骤g:将熔炼好的铁水浇入铸造工装顶部的浇注漏斗内,通过浇注漏斗流入铸造工装中,铁水浇注至与冷型上端平齐,凝固形成轧辊外层。
5.优选的,在步骤c中,所述冷型的挂砂温度为190
‑
220℃。
6.优选的,在步骤d中,所述芯轴在电阻炉内加热时水平放置,并在芯轴的下部放置至少4
‑
5个支撑垫,防止加热过程芯轴变形。
7.优选的,在步骤e中,所述轧辊外层的无限冷硬材质中化学成分及重量百分比为:c:3.2
‑
3.5%,si:0.9
‑
1.1%,mn:0.55
‑
0.85%,p:≤0.08%,s:≤0.03%,cr:1.6
‑
1.8%,ni:3.5
‑
4.0%,mo:0.3
‑
0.7%,余量为fe及不可避免的杂质元素。
8.优选的,在步骤f中,所述冒口箱内冒颈砂型内壁与冷型的内腔平滑过渡。
9.优选的,在步骤f中,所述芯轴的下端辊颈主轴与底箱的上端内腔紧密接触;所述芯轴设置于冒颈与底颈之间,所述冒颈设置于冒口箱的内腔上部,所述底颈设置于底箱底颈砂型内。
10.优选的,在步骤f中,所述冷型的上下两端分别通过中圈与冒口箱及底箱相连。
11.优选的,在步骤g中,所述浇注漏斗的底部设有多个浇注管,且多个浇注管周向布置于芯轴四周的内腔顶部,保证铁水进入芯轴四周内腔时周向均匀分布。
12.采用上述技术方案所产生的有益效果在于:与现有技术相比,本发明利用达到报废直径的铸铁轧辊重新加工生产无限冷硬轧辊,可大幅降低生产成本,提高生产效率;同时,利用中频炉熔炼符合要求的无限冷硬材质铁水,并注入由底箱、冷型及冒口箱组装好的铸造工装内,外部依靠冷型、内部依靠芯轴实现双向快速凝固,可实现轧辊辊身内的晶粒细化,保证整个工作层处于细晶状态,进而提高轧辊工作层耐磨性,与同材质轧辊相比,毫米过钢量提高10%以上。
附图说明
13.下面结合附图和具体实施方式对本发明作进一步详细的说明。
14.图1是本发明实施例中提供的一种cr5合金铸钢轧辊的浇注状态图;图中:1
‑
芯轴,2
‑
底箱,3
‑
冒口箱,4
‑
底颈砂型,5
‑
冒颈砂型,6
‑
冷型,7
‑
中圈,8
‑
浇注漏斗,9
‑
冒颈,10
‑
底颈;11
‑
辊颈主轴,12
‑
浇注管,13
‑
铁水包,14
‑
铁水,15
‑
轧辊外层。
具体实施方式
15.下面结合本发明实施例中的附图,对本发明实施例中的技术方案进行清楚、完整地描述,显然,所描述的实施例仅仅是本发明的一部分实施例,而不是全部的实施例。基于本发明中的实施例,本领域普通技术人员在没有做出创造性劳动前提下所获得的所有其他实施例,都属于本发明保护的范围。
16.本发明提供的一种节能型细晶无限冷硬轧辊的制备方法,具体步骤见如下所示实施例:实施例1:步骤a:将达到报废直径的报废轧辊重新加工成符合要求尺寸的芯轴1,芯轴1的中间辊身直径大于两端辊颈主轴直径;所述报废轧辊为无限冷硬铸铁轧辊,报废轧辊为镍铬无限冷硬材质。
17.步骤b:根据需要生产的轧辊规格尺寸选择底箱2及冒口箱3,并在底箱2内壁预制底颈砂型4,及在冒口箱3内壁预制冒颈砂型5。
18.步骤c:根据需要生产的轧辊规格尺寸选择冷型6,将冷型6加热至挂砂温度并进行挂砂操作,冷型6的内腔直径比轧辊的辊身直径大32mm,鉴于辊身表面铁水凝固组织与正常凝固组织不一致,铁水最后凝固部分组织性能差、且可能存在疏松夹渣缺陷,后期需要将这部分组织加工去除,以保持轧辊所使用的工作层组织一致,过大造成浪费,过小则异常组织不能完全去除。
19.对冷型6的内腔表面进行清理,去除油污、玻璃渣、杂物等,清理完毕装入电阻炉加热至350℃开始挂砂,冷型6的挂砂温度为220℃,挂砂厚度3.5mm。考虑铁水激冷性,挂砂过
厚组织粗大,挂砂过薄产生裂纹的可能性增大。
20.步骤d:待浇注的芯轴1利用电阻炉加热至650℃,并恒温5小时;芯轴1在电阻炉内加热时水平放置,并在芯轴1的下部放置5个支撑垫,防止加热过程芯轴变形。通过加热芯轴可确保芯轴和工作层的铁水能够良好融合,芯轴温度低不融合,温度高产生较大氧化易在芯轴与工作层的结合处存在夹渣类缺陷。
21.步骤e:根据需要生产的轧辊进行轧辊外层15的无限冷硬材质配料,并根据轧辊外层15的铁水量选择中频炉进行熔炼;铁水熔清后微调合金成分满足要求,轧辊外层15的无限冷硬材质中化学成分及重量百分比为:c:3.35%,si:0.95%,mn:0.65%,p:≤0.08%,s:≤0.03%,cr:1.65%,ni:3.63%,mo:0.44%,余量为fe及不可避免的杂质元素。
22.步骤f:将底箱2、中圈7、冷型6及冒口箱3分别提前在其内腔造型,然后与挂砂后的冷型6组装为铸造工装, 所述冷型6的上下两端分别通过中圈7与冒口箱3及底箱2相连,将芯轴1垂直置于铸造工装内腔中部,组装时保持芯轴1与冷型6、底箱2及冒口箱3内腔同轴且垂直于地平面。其中,冒口箱3内冒颈砂型5内壁与冷型6的内腔平滑过渡。
23.如图1所示,具体安装时,使芯轴1的下端辊颈主轴11与底箱2的上端内腔紧密接触,避免浇注铁水时流入底箱内;所述芯轴1设置于冒颈9与底颈10之间,所述冒颈9设置于冒口箱3的内腔上部,所述底颈10设置于底箱2的底颈砂型4内。
24.步骤g:将熔炼好的铁水浇入铸造工装顶部的浇注漏斗8内,通过浇注漏斗8流入铸造工装中,铁水浇注至与冷型6上端平齐,凝固形成轧辊外层15。如图1所示,浇注漏斗8的底部设有多个浇注管12,且多个浇注管12周向布置于芯轴1四周的内腔顶部,铁水经多孔浇注管呈雨淋状注入,保证铁水进入芯轴1四周内腔时周向均匀分布。
25.实施例2:步骤a:将达到报废直径的报废轧辊重新加工成符合要求尺寸的芯轴1,所述报废轧辊为无限冷硬铸铁轧辊,报废轧辊为镍铬无限冷硬材质。
26.步骤b:根据需要生产的轧辊规格尺寸选择底箱2及冒口箱3,并在底箱2内壁预制底颈砂型4,及在冒口箱3内壁预制冒颈砂型5。
27.步骤c:根据需要生产的轧辊规格尺寸选择冷型6,将冷型6加热至挂砂温度并进行挂砂操作,冷型6的内腔直径比轧辊的辊身直径大35mm。鉴于铁水最后凝固部分组织性能差、且可能存在疏松夹渣缺陷,后期需要将这部分组织加工去除,以保持轧辊所使用的工作层组织一致。因此,选取冷型内腔直径大于轧辊辊身外径35mm,过大造成浪费,过小则异常组织不能完全去除。
28.对冷型6的内腔表面进行清理,去除油污、玻璃渣、杂物等,清理完毕装入电阻炉加热至350℃开始挂砂,冷型6的挂砂温度为220℃,挂砂厚度3.3mm,考虑铁水激冷性,挂砂过厚组织粗大,挂砂过薄产生裂纹的可能性增大。
29.步骤d:待浇注的芯轴1利用电阻炉加热至650℃,并恒温6小时;芯轴1在电阻炉内加热时水平放置,并在芯轴1的下部放置4个支撑垫,防止加热过程芯轴变形。通过加热芯轴可确保芯轴和工作层的铁水能够良好融合,芯轴温度低不融合,温度高产生较大氧化易在芯轴与工作层的结合处存在夹渣类缺陷。
30.步骤e:根据需要生产的轧辊进行轧辊外层15的无限冷硬材质配料,并根据轧辊外
层15的铁水量选择中频炉进行熔炼;铁水熔清后微调合金满足成分要求,轧辊外层15的无限冷硬材质中化学成分及重量百分比为:c:3.45%,si:0.93 %,mn:0.85%,p:≤0.08%,s:≤0.03%,cr:1.8%,ni:4.0%,mo:0.55%,余量为fe及不可避免的杂质元素。
31.步骤f:将底箱2、中圈7、冷型6及冒口箱3分别提前在其内腔造型,然后与挂砂后的冷型6组装为铸造工装, 所述冷型6的上下两端分别通过中圈7与冒口箱3及底箱2相连,将芯轴1垂直置于铸造工装内腔中部,组装时保持芯轴1与冷型6、底箱2及冒口箱3内腔同轴且垂直于地平面。其中,冒口箱3内冒颈砂型5内壁与冷型6的内腔平滑过渡。
32.如图1所示,具体安装时,使芯轴1的下端辊颈主轴11与底箱2的上端内腔紧密接触;所述芯轴1设置于冒颈9与底颈10之间,所述冒颈9设置于冒口箱3的内腔上部,所述底颈10设置于底箱2的底颈砂型4内。
33.步骤g:将熔炼好的铁水浇入铸造工装顶部的浇注漏斗8内,通过浇注漏斗8流入铸造工装中,铁水浇注至与冷型6上端平齐,凝固形成轧辊外层15。如图1所示,浇注漏斗8的底部设有多个浇注管12,且多个浇注管12周向布置于芯轴1四周的内腔顶部,保证铁水进入芯轴1四周内腔时周向均匀分布。
34.采用本发明生产节能型细晶无限冷硬轧辊,首先将使用至报废直径的铸铁轧辊重新加工成符合要求尺寸的芯轴,可大幅降低生产成本,提高生产效率;利用底箱制作底颈砂型,将芯轴的辊颈主轴与底颈砂型内壁紧密接触,同时在芯轴下端放置底颈,可避免铁水进入底箱内;选择合适冷型加热至挂砂温度并进行内腔挂砂,将准备浇注的芯轴加热至500
‑
900℃并恒温一定时间;将熔炼好的无限冷硬材质铁水浇入组装好浇注漏斗,通过浇注漏斗流入组装好的工装造型中,完成浇注。可借助冷型及芯轴的双向激冷来实现轧辊外层15铁水的快速凝固,可实现轧辊辊身内的晶粒细化。利用本发明能够大幅降低生产成本,提高生产效率,轧辊整个工作层处于细晶状态,能够提高轧辊工作层的耐磨性,与同材质轧辊相比,毫米过钢量提高10%以上。
35.在上面的描述中阐述了很多具体细节以便于充分理解本发明,但是本发明还可以采用其他不同于在此描述的其它方式来实施,本领域技术人员可以在不违背本发明内涵的情况下做类似推广,因此本发明不受上面公开的具体实施例的限制。