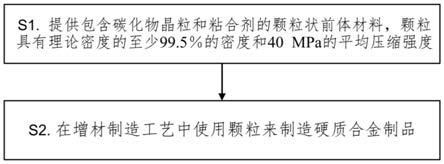
1.本公开总体上涉及通过增材制造来制造硬质合金制品的方法以及用于硬质合金制品的前体材料。
背景技术:2.增材制造是用于快速原型制造和制造具有复杂几何形状的金属制品的有力工具。已知这方法几乎只用于制造由纯金属和合金(例如钢和钛合金组成)的制品。顾等人,《激光增材制造金属部件:材料、工艺和机制》,international materials reviews,2012,v.57,n.3,133综述了金属部件的增材制造工艺。
3.增材制造工艺很少用于工业上生产由包含多于一个相的复合材料组成的制品。特别是,增材制造不用于生产硬质合金(cemented carbide)材料。硬质合金材料包括分散在包含诸如钴(co)、镍(ni)的金属或金属合金的粘合剂材料内的诸如碳化钨(wc)或碳化钛(tic)的碳化物(carbide)颗粒。据说粘合剂相可以将碳化物颗粒作为烧结坯块粘结在一起。增材制造工艺不用于硬质合金可能是由于与材料的致密化相关的困难,所述材料在增材制造工艺期间仅短时间部分熔化。获得硬质合金的高密度所需的极高能量和因而需要的高温的使用受限于未进行液相烧结的硬质合金颗粒的低密度和强度,所述硬质合金颗粒通常用作增材制造硬质合金的前体。这种颗粒不能在增材制造所需的短时间内烧结成高密度的散装材料(bulk material),并且容易被增材制造期间由高能电子或激光束的影响引起的热冲击所导致的“爆炸”破坏。
4.wo2015/162206a2公开了使用通过液相烧结获得的完全烧结的硬质合金颗粒以解决上述问题。为了降低将生坯(green)硬质合金颗粒烧结在一起的风险,添加了“烧结抑制剂粉末”。这些粉末由在液相烧结之前添加到生坯颗粒中的氧化物陶瓷或石墨组成。然而,这种方法的缺点是烧结抑制剂粉末对硬质合金颗粒造成污染的风险很大。此外,添加这种粉末降低了硬质合金颗粒的强度。
技术实现要素:5.本文目的是提供使用增材制造工艺制造硬质合金制品的方法。
6.根据第一方面,提供了通过增材制造来制造硬质合金制品的方法。提供了包含颗粒的前体材料,所述颗粒包含碳化物晶粒和包含钴、镍和铁中的任一种的粘合剂。每个颗粒具有理论密度的至少99.5%的密度,并且前体材料的颗粒具有至少40兆帕(mpa)的平均压缩强度。使用了增材制造工艺通过建立从前体材料衍生的材料的连续层来制造制品。
7.作为选项,前体材料的每个颗粒具有选自理论密度的至少99.7%、理论密度的至少99.9%以及理论密度的100%中的任一个的密度。
8.前体材料的颗粒可选地具有选自至少60mpa和至少100mpa中的任一个的平均压缩强度。
9.前体材料的颗粒可选地具有选自20微米至200微米、30微米至120微米以及40微米
至90微米中的任一个的尺寸。
10.根据第一示例性选择,提供前体材料的颗粒包括在具有增塑剂的有机流体中研磨硬质合金粉末混合物以获得浆料,干燥浆料以获得硬质合金粉末,以及将硬质合金粉末颗粒化以获得硬质合金颗粒。在真空或保护气氛中,在1000℃至1250℃的温度下将颗粒固态烧结1至60分钟以获得预烧结的粒状粉末。筛选预烧结的颗粒(例如通过筛分)以获得预烧结的颗粒的所需尺寸级分。在真空或保护气氛中,在1260℃至1330℃的温度下,将预烧结的颗粒烧结2至20分钟以获得烧结的颗粒的聚集体。将聚集体破碎成单独的完全烧结的颗粒。筛选完全烧结的颗粒以获得所需的尺寸级分。
11.作为选项,方法包括对浆料进行喷雾干燥以干燥并颗粒化硬质合金颗粒。替代地,可选地通过在高于50℃的温度下在旋转的滚筒中滚动来将硬质合金粉末颗粒化。
12.根据第二示例性选择,提供前体材料的颗粒包括在具有增塑剂的有机流体中研磨硬质合金粉末混合物以获得浆料,干燥浆料以获得硬质合金粉末,压制硬质合金粉末以形成生坯体,破碎生坯体以形成生坯体颗粒,筛选生坯体颗粒以获得生坯体颗粒的所需尺寸级分,在真空或保护气氛中,在1260℃至1330℃的温度下将生坯体颗粒烧结2至20分钟以获得完全烧结的颗粒的聚集体,破碎聚集体以获得单独的完全烧结的颗粒,以及筛选完全烧结的颗粒以获得所需的尺寸级分。
13.根据第三示例性选择,提供前体材料的颗粒包括在具有增塑剂的有机流体中研磨硬质合金粉末混合物以获得浆料,干燥浆料以获得硬质合金粉末,将硬质合金粉末颗粒化以获得硬质合金颗粒,筛选颗粒以获得颗粒的所需尺寸级分,在真空或保护气氛中,在1260℃至1330℃的温度下将颗粒烧结2至20分钟以获得完全烧结的颗粒的聚集体,破碎聚集体以获得单独的完全烧结的颗粒,以及筛选完全烧结的颗粒以获得所需的尺寸级分。
14.作为选项,方法包括在烧结预烧结的颗粒之后,在氩气中,在0.5至10mpa的压力下热等静压完全烧结的颗粒。
15.硬质合金制品可选地具有选自理论密度的至少97%、理论密度的至少98%、理论密度的至少99%以及理论密度的至少99.5%中的任一个的密度。
16.作为选项,方法包括在真空或保护气氛中,在1300℃至1350℃的温度下对硬质合金制品进行液相烧结2至15分钟。作为进一步选项,方法包括在真空或保护气氛中,在1300℃至1350℃的温度下对硬质合金制品进行液相烧结2至15分钟,以及在氩气中,在0.5至10mpa的压力下热等静压硬质合金制品。
17.增材制造工艺可选地选自直接金属激光烧结(dmls)、选择性激光烧结(sls)和电子束熔化(ebm)中的任一种。
18.颗粒可选地在粘合剂中包含选自ti、v、mn、zr、nb、mo、hf、ta的金属的碳化物、碳氮化物和/或氮化物,和/或粘合剂中固溶体形式的这些金属。
19.颗粒可选地包含选自re、os、ir、ce、y、cu的金属。
20.方法可选地进一步包括在硬质合金制品的表面上设置多晶金刚石(pcd)层。
21.根据第二方面,提供了用于通过增材制造来制造硬质合金制品的颗粒状前体材料,所述颗粒状前体材料包括颗粒,所述颗粒包含碳化物晶粒和包含钴、镍和铁中的任一种的粘合剂,并且其中每个颗粒具有理论密度的至少99.5%的密度,并且前体材料的颗粒具有至少40mpa的平均压缩强度。
22.作为选项,前体材料的每个颗粒具有选自理论密度的至少99.7%、理论密度的至少99.9%以及理论密度的100%中的任一个的密度。
23.作为选项,前体材料的颗粒具有选自至少60mpa和至少100mpa中的任一个的平均压缩强度。
24.作为选项,前体材料的颗粒具有选自20微米至200微米、30微米至120微米以及40微米至90微米中的任一个的尺寸。
附图说明
25.参照附图描述说明本公开的非限制性示例性布置,其中:
26.图1以框图示意性地示出了示例性增材制造设备;
27.图2是示出制造硬质合金制品的示例性步骤的流程图;
28.图3是示出制备前体材料颗粒的第一示例性方法的示例性步骤的流程图;
29.图4是示出用于制备前体材料颗粒的第二示例性方法的示例性步骤的流程图;
30.图5是示出用于制备前体材料颗粒的第三示例性方法的示例性步骤的流程图;和
31.图6是示出示例性烧结的前体颗粒的显微照片。
具体实施方式
32.转到图1,示出了示例性增材制造设备1。进料粉末2位于进料容器3中可移动进料平台4上。耙臂5周期性地扫过进料粉末2的顶部以将薄层粉末6推入建筑容器7中。建筑容器7中的粉末6位于可移动的建筑平台8上。
33.计算机9控制能量源10以将能量引导到粉末6的层上。能量可以由任何合适的源提供,例如激光或电子束。在这个示例中,能量是激光11。这操作可以在惰性环境中执行。
34.激光11扫过建筑平台上的粉末6并提供例如0.5至25ms的短脉冲。这能量使粉末6在非常小的区域熔化并开始在粉末中建立制品12。激光11根据计算机9发送的指令在栅格(raster)上移动。一旦激光11在垂直方向上扫过栅格,建筑平台则向下索引所需粉末厚度的距离。耙臂5将粉末从进料容器3中扫出并扫入建筑容器7中,并且进料平台4向上索引所需粉末厚度的距离,准备为下一层增材制造提供粉末。以这种方式,可以建立具有复杂形状的制品12。一旦完成操作并且创建了制品12,多余的粉末会从制品12中被去除,并且可以在新操作中被回收。
35.如上所述,由于诸如硬质合金的复合材料在短时间施加能量时仅部分熔化,并且难以实现完全致密化,因此增材制造通常用于单相材料,例如金属和合金。
36.现在惊人地发现,粘合剂中碳化物晶粒的完全烧结的颗粒可用于通过增材制造来制造高密度的硬质合金制品。为了做到这一点,颗粒需要接近理论密度的高密度和高压缩强度。理论密度是没有孔隙的“完美”材料的密度。
37.在增材制造工艺期间施加高能量所需的短时间内可以实现完全烧结的颗粒的致密化以获得高密度制品。由于颗粒的高压缩强度,在增材制造工艺期间可以使用高能电子或激光束,而没有显著的损伤、破坏或可能由热冲击引起对这种颗粒的“爆炸风险”。此外,已经发现使用尺寸小于200μm的细硬质合金颗粒允许它们在增材制造工艺期间被快速烧结,使得通过增材制造制备的硬质合金制品12具有与理论密度相比的高密度。
38.上述技术可用于粘合剂中的任何类型的碳化物晶粒,并且在碳化物晶粒为碳化钨且粘合剂是基于钴、镍、铁或这些金属的混合物的情况下具有特定应用。
39.图2是示出通过增材制造来制造硬质合金制品的示例性步骤的流程图。以下编号对应于图1的编号:
40.s1.提供颗粒形式的硬质合金的前体材料。颗粒包括分散在粘合剂中的碳化物晶粒。粘合剂包含诸如钴、镍和铁的材料(单独或以任何组合)。每个颗粒具有理论密度的至少99.5%的密度,并且前体材料的颗粒具有至少40mpa的平均压缩强度。较高的压缩强度(例如至少60mpa或至少100mpa)可以提供改善的特性。前体材料的颗粒通常具有20μm至200μm的尺寸。在一些应用中,可能优选30μm至120μm,以及40μm至90μm的尺寸。在增材制造工艺期间,颗粒的大小不应大于每一层,以确保当耙臂5将粉末从进料容器3散布到建筑容器7时,颗粒被均匀地散布并且不会拖曳或卡在耙臂5和容器壁之间。例如,如果每层期间的厚度为100μm,最大颗粒尺寸则不应超过100μm。请注意,颗粒可以略大于层厚度,因为每个层在工艺期间由于形成块(cake)的工艺的温度以及从颗粒密度到最终制品密度的增加而被压制。
41.s2.使用了增材制造工艺通过建立从前体材料衍生的材料的连续层来制造制品。这可能涉及高能电子束或激光脉冲。这能量足以熔化粘合剂相而不是碳化物相,这使得制品12中可以实现完全致密化。一旦制品12已经被制造出来,多余的粉末被去除并且可以在进一步的操作中被再循环。
42.有几种方法可以制备具有所需特性的前体材料颗粒。
43.图3是示出制备前体材料颗粒的第一示例性方法的示例性步骤的流程图。以下编号对应于图3的编号。
44.s3.在具有增塑剂的有机流体中研磨硬质合金粉末混合物以获得浆料。进行研磨以获得期望的粒径和碳化物粉末与粘合剂之间的紧密混合物。在粘合剂是金属或合金(例如钴)的情况下,研磨的能量将粘合剂“涂抹”在碳化物晶粒上,以确保紧密混合。
45.s4.干燥浆料以获得硬质合金粉末。
46.s5.将硬质合金粉末颗粒化以获得硬质合金颗粒。注意,步骤s4和s5可以在喷雾干燥操作中一起进行。
47.s6.在真空或保护气氛中,在1000℃至1250℃的温度下将颗粒固态烧结1至60分钟以获得预烧结的粒状粉末。预烧结改善了颗粒的机械强度,这使得处理更容易。然后将预烧结的颗粒破碎成更小的颗粒。
48.s7.筛选预烧结的颗粒以获得预烧结的颗粒的期望的级分。期望的级分可以包括最大粒径、最小粒径和平均粒径以帮助粉末处理。筛选可以通过筛分进行,并且颗粒尺寸可以是例如40至100μm。
49.s8.在真空或保护气氛中,在1260℃至1330℃的温度下,将预烧结的颗粒液相烧结2至20分钟以获得烧结的颗粒的聚集体。注意,颗粒几乎完全烧结,但不希望聚集体完全烧结,因为这会使得它们更难破碎。
50.s9.破碎聚集体以获得单独的完全烧结的前体材料颗粒。
51.s10.筛选几乎完全烧结的前体材料颗粒以获得用于增材制造工艺的期望的级分。同样,期望的级分可以包括最大粒径以确保颗粒在增材制造工艺期间被耙臂5均匀地移动,并且可以包括最小粒径和平均粒径以允许粉末处理。最大粒径也可能是必需的,因为太大
的颗粒在增材制造工艺期间可能不会完全烧结。筛选可以通过筛分进行,并且颗粒尺寸可以是例如40至100μm。前体材料颗粒具有用于如上所述的增材制造工艺中的所需特性。
52.图4是示出用于制备前体材料颗粒的第二示例性方法的示例性步骤的流程图。以下编号对应于图4的编号。
53.s11.如上述步骤s3中研磨硬质合金粉末混合物。
54.s12.如上述步骤s4中干燥浆料。
55.s13.将干燥的粉末在没有粘合剂的情况下进行干压,以形成生坯体。
56.s14.通过轻磨(light milling)破碎生坯体以形成颗粒。
57.s15至s18.以与上述步骤s7至s10相同的方式进一步处理颗粒。
58.图5是示出用于制备前体材料颗粒的第三示例性方法的示例性步骤的流程图。以下编号对应于图3的编号。
59.s19.如上述步骤s3中研磨硬质合金粉末混合物。
60.s20.如上述步骤s4中干燥浆料。
61.s21.如上述步骤s5将干燥的粉末颗粒化。
62.s22.如上述步骤s7中所述,筛分颗粒以获得期望的尺寸级分。
63.s23至s25.以与上述步骤s8至s10相同的方式进一步处理颗粒。
64.本领域技术人员将会理解,可以使用其他已知的粉末制备技术来获得具有用于增材制造的所需特性的硬质合金颗粒。
65.以下示例显示了如何制备前体颗粒材料并随后将其用于增材制造工艺。
66.示例1
67.通过将174kg的wc粉末和26kg的co粉末一起研磨来制备wc
‑
co粉末的生产批次(200kg)。wc粉末的平均晶粒尺寸为1.3μm。co粉末具有约1μm的平均晶粒尺寸。另外,加入4公斤的醇中石蜡。将这些组分与1000kg碳化物球在磨碎机中一起研磨3小时。
68.研磨后,在约90℃的温度下干燥所得浆料。通过使用来自netzsch
tm
的单元在约80℃的温度下在旋转的滚筒中滚动来将粉末混合物颗粒化。将所得颗粒筛分成40至400μm的晶粒尺寸级分。
69.将筛分的颗粒置于50
×
50
×
10cm的石墨盒中至约10cm的最大高度,并在1080℃的温度下预烧结30分钟。将预烧结的颗粒筛分成50至100μm的晶粒尺寸级分。
70.将预烧结和筛分的颗粒置于石墨盒中,最后在真空中在1310℃的温度下烧结45分钟,然后在氩气中在50巴的压力下(热等静压)烧结30分钟。最终烧结后,颗粒形成由聚集的颗粒组成的“烧结块”。通过轻磨将聚集的颗粒破碎。首先通过500μm尺寸的筛子筛分所得的烧结的颗粒。然后将烧结的颗粒筛分成60至100μm的晶粒尺寸级分。
71.图6示出了如上所述生产的颗粒的横截面的微观结构。可以看出,颗粒被烧结到接近理论密度,因为在横截面上没有可见的孔隙。温度足够高以使颗粒完全致密化,但不能太高,以免它们烧结在一起。
72.随机选取五个颗粒样品进行破坏性机械测试。将每个颗粒放置在刚性台上,并且将刚性板以恒定的速度缓慢地压在颗粒上,从而用从50毫牛顿(mn)增加至最大2,000牛顿(n)的力压缩它,直到颗粒破碎。由于每个颗粒的机械性能都部分取决于颗粒的尺寸,因此所测试的颗粒全部具有100至120μm的直径尺寸。发现颗粒的平均压缩强度为270
±
50兆帕
(mpa)。
73.通过使用30ma的电流和5m/s的电子束速度的电子束熔化增材制造工艺,将颗粒用于制造直径约15mm和高度约10mm的圆柱体。在进行增材制造工艺之前,将2mm厚的颗粒层放置在尺寸为100
×
100
×
10mm的wc
‑
20%co硬质合金的板上,通过电子束将该板预热至1100℃。当增材制造工艺完成时,通过使用压缩空气将烧结的碳化物制品中的未烧结的颗粒吹走而将其去除。烧结制品的密度为14.0g/cm3,相当于理论密度的98.6%。烧结的制品的矫顽磁力为10.5ka/m,磁矩为18.2gcm3/g,硬度为1190维氏单位,断裂韧性为14.0mpam
1/2
。
74.在随后的研磨之后,将烧结的圆柱体用作通过在高压高温(hpht)条件下加压烧结获得的多晶金刚石(pcd)的基底。当hpht加压烧结完成时,切下一个碳化物圆柱体的样品并检查它。发现其密度为14.24g/cm3,这相当于100%的密度。矫顽磁力降低至10.1ka/m,磁矩降至17.8gcm3/g,硬度提高至1290维氏单位,断裂韧性提高至14.2mpa m
1/2
。
75.示例2
76.通过示例1中所述的增材制造工艺制造的碳化物圆柱体在真空中在1320℃的温度下进行液相烧结2分钟,并在氩气中在40巴的压力下进行热等静压10分钟。发现其密度为14.22g/cm3,这相当于100%密度(理论密度为14.2
±
0.1g/cm3)。矫顽磁力下降到10.4ka/m,磁矩下降到18.1gcm3/g,硬度增加到1220维氏单位,断裂韧性增加到14.1mpa m
1/2
。
77.在上面的示例中,通过用已知筛孔尺寸的筛子来确保不存在大颗粒,从而获得期望的晶体尺寸。这些可能导致粉末处理问题和烧结问题。
78.上文已经描述了硬质合金的各种示例性实施例、用于生产硬质合金的方法,以及包括硬质合金的工具。本领域技术人员将理解,在不脱离所附权利要求的范围的情况下,可以对那些示例进行改变和修改。例如,上述实施例涉及烧结碳化钨制品,但将理解的是,相同的技术可应用于其他类型的硬质合金制品。