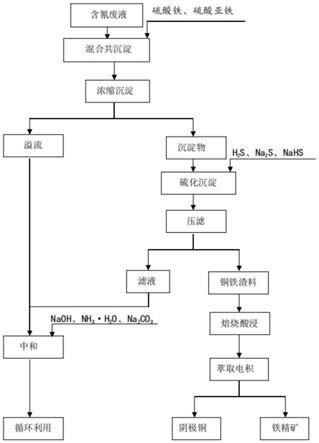
1.本发明涉及废水处理技术领域,尤其涉及一种含氰废液的净化与循环利用的方法。
背景技术:2.目前,世界黄金产量70%以上是采用氰化提金技术获得的,氰化提金工艺占据黄金生产领域的主导地位,黄金冶炼在生产过程中会产生大量的含氰废液,这部分含氰废液不仅含有一定量的剧毒氰化物,而且常伴有铜、锌、铅、砷等离子,如果得不到有效的处理,将会产生重大的环保隐患。
3.现有技术中处理含氰废液常用的方法有酸化回收法、半酸化法、碱氯法、so2‑
空气法、过氧化氢氧化法、臭氧法、生物氧化法等。采用碱氯法、so2‑
空气法、过氧化氢氧化法、臭氧法虽能使含氰废液达标排放,但这些方法的原理都是破坏氰根,使其变成其他无毒产物,氰根无法回收利用,同时这些方法都不能有效回收废水中的有价元素;而采用酸化回收法虽然能够回收一定量的氰化物,但由于回收氰化物不彻底,废水中会残余一定量的氰化物,一般需要再次消毒处理后才能达标排放;半酸化法可回收部分重金属离子,氰化物循环使用,其缺点是重金属离子去除不彻底、溶液中as不断累积影响生产指标、产生的尾渣难于过滤等。
技术实现要素:4.根据以上现有技术的不足,本发明的目的在于提供一种含氰废液的净化与循环利用方法,该方法工艺流程简单、处理效率高、能有效回收含氰废液中的各种有价元素,实现含氰废液的除杂回用。
5.针对以上目的,本发明提供的方法是根据黄金冶炼含氰废液中含有氰化物、铜、铅、锌、砷等多种污染物的特征,采用硫酸铁共沉淀、硫化转化法,将废水中的污染物去除沉淀,同时活化氰根,除杂后的含氰废液经中和后返回氰化系统继续循环利用,含有铜铁的共沉淀物采用焙烧酸浸、萃取电积工艺分别产出阴极铜与铁精矿产品。
6.具体的技术方案如下:
7.一种含氰废液的净化与循环利用方法,包括以下步骤:
8.1)将待处理的含氰废液送入混合共沉淀反应槽,往所述混合共沉淀反应槽中添加硫酸铁、硫酸亚铁试剂进行沉淀反应;
9.2)混合共沉淀反应后,进入浓密机进行浓缩沉淀,所述浓密机溢流自流到中和搅拌槽,底流浓缩沉淀物矿浆进入硫化反应槽,往所述硫化反应槽中添加硫酸、硫化物,控制反应ph值;
10.3)硫化反应后,经压滤机压滤后,得到含有cu、fe的多元素的渣料,滤液返回所述浓密机溢流中和搅拌槽;
11.4)向含有cu、fe的多元素渣料中添加硫铁矿,配成含硫46~48%的混合固体物料,
采用常规焙烧酸浸工艺、萃取电积工艺回收阴极铜,酸浸渣为铁精矿;
12.5)步骤2)所述浓密机溢流与步骤3)所述硫化反应压滤滤液一并送入中和搅拌槽,往所述中和搅拌槽添加中和试剂,中和反应后经泵返回氰化系统。
13.进一步,所述混合共沉淀反应槽、硫化反应槽、中和搅拌槽、浓密机均采用密闭式设计,并在顶盖设有排风管,由引风机将溢出的气体引至尾气吸收塔,并采用10
‑
20%质量浓度的氢氧化钠溶液吸收。
14.再进一步,步骤1)中所述硫酸铁、硫酸亚铁试剂的配比为1:1~1:5,所述ph值在3.5~4.5之间,共沉淀反应时间为30~60min。
15.进一步,步骤2)所述硫化物为h2s、na2s和nahs中的至少一种,过程中同时添加硫酸,并控制硫化反应过程终点的ph值在3~4。
16.进一步,步骤4)中所述酸浸渣为含铁62~65%的铁精矿。
17.进一步,步骤5)中所述中和试剂为naoh、nh3·
h2o、na2co3中的至少一种,中和反应终点的ph值在9~11。
18.本发明的有益效果在于:
19.(1)将铁盐共沉淀法与硫化法相结合,可有效的去除含氰废液中的重金属与砷。
20.(2)处理后的含氰废液杂质少,溶液中的氰根得到活化,直接返回氰化系统,减少企业氰化物的消耗。
21.(3)结合铁盐共沉淀、硫化法产出的铜铁渣料,对接硫铁矿焙烧酸浸、萃取电积工艺产出阴极铜与铁精矿,实现了铜铁的有效综合回收。
22.(4)该方法综合回收废水中的有价元素,不对外排放废水,符合国家环境保护政策。
23.(5)该方法工艺简单,整改过程密闭环保、固废零产出零排放,且便于实现工业化应用。
附图说明
24.图1为本发明所提供含氰废液的净化与循环利用方法的流程示意图。
具体实施方式
25.以下结合附图与实例对本发明进行描述,所述附图与实例只用于解释本发明,并非用于限定本发明的范围。
26.实施例1
27.将待处理的含氰废液送入混合共沉淀反应槽,往所述混合共沉淀反应槽中添加配比为1:1的硫酸铁、硫酸亚铁试剂,进行沉淀反应;在进行混合共沉淀反应的过程中,添加硫酸铁、硫酸亚铁控制ph值在3.5,反应时间为30min;混合共沉淀反应后,进入浓密机进行浓缩沉淀,浓密机溢流自流到中和搅拌槽,底流浓缩沉淀物矿浆进入硫化反应槽,往所述硫化反应槽中添加硫酸、硫化氢,控制硫化反应过程终点的ph值在3;硫化反应后,经压滤机压滤后,得到含有铜15%,含铁20%的渣料,滤液返回浓密机溢流的中和搅拌槽;将含有cu、fe的渣料添加硫铁矿,配成含硫46%的混合固体物料,采用常规焙烧酸浸工艺、萃取电积工艺回收阴极铜,酸浸渣为含铁62%的铁精矿;浓密机溢流与硫化反应压滤滤液一并送入中和搅
拌槽,往中和搅拌槽添加氢氧化钠,中和反应终点的ph值在9中和反应后经泵返回氰化系统。
28.混合共沉淀反应槽、硫化反应槽、中和搅拌槽、浓密机均采用密闭式,并在顶盖设有排风管,由引风机将溢出的气体引至尾气吸收塔,采用10%质量浓度的氢氧化钠溶液吸收。
29.实施例2
30.将待处理的含氰废液送入混合共沉淀反应槽,往所述混合共沉淀反应槽中添加硫酸铁、硫酸亚铁试剂,试剂配比为1:3,进行沉淀反应;在进行混合共沉淀反应的过程中,添加硫酸铁、硫酸亚铁控制ph值在4.0,反应时间为45min;混合共沉淀反应后,进入浓密机进行浓缩沉淀,浓密机溢流自流到中和搅拌槽,底流浓缩沉淀物矿浆进入硫化反应槽,往所述硫化反应槽中添加硫酸、硫化钠,控制反应过程终点的ph值在3.5;硫化反应后,经压滤机压滤后,得到含有铜18%、含铁22%的渣料,滤液返回浓密机溢流的中和搅拌槽;含有cu、fe的渣料添加硫铁矿,配成含硫47%的混合固体物料,采用常规焙烧酸浸工艺、萃取电积工艺回收阴极铜,酸浸渣为含铁63.5%的铁精矿;浓密机溢流与硫化反应压滤滤液一并送入中和搅拌槽,往所述中和搅拌槽添加氢氧化钠、氨水,中和反应后反应终点的ph值在10,中和反应后经泵返回氰化系统。
31.混合共沉淀反应槽、硫化反应槽、中和搅拌槽、浓密机均采用密闭式,并在顶盖设有排风管,由引风机将溢出的气体引至尾气吸收塔,采用15%质量浓度的氢氧化钠溶液吸收。
32.实施例3
33.将待处理的含氰废液送入混合共沉淀反应槽,往所述混合共沉淀反应槽中添加硫酸铁、硫酸亚铁试剂,试剂配比为1:5进行沉淀反应;在进行混合共沉淀反应的过程中,添加硫酸铁、硫酸亚铁控制ph值在4.5,反应时间为60min;混合共沉淀反应后,进入浓密机进行浓缩沉淀,浓密机溢流自流到中和搅拌槽,底流浓缩沉淀物矿浆进入硫化反应槽,往硫化反应槽中添加硫酸、硫氢化钠,并控制硫化反应过程终点的ph值在4;硫化反应后,经压滤机压滤后,得到含有铜20%,含铁22%的多元素的渣料,滤液返回浓密机溢流的中和搅拌槽;含有cu、fe的渣料添加硫铁矿,配成含硫48%的混合固体物料,采用常规焙烧酸浸工艺、萃取电积工艺回收阴极铜,酸浸渣为含铁65%的铁精矿;浓密机溢流与硫化反应压滤滤液一并送入中和搅拌槽,往中和搅拌槽添加氢氧化钠、碳酸钠,反应终点的ph值在11,中和反应后经泵返回氰化系统。
34.混合共沉淀反应槽、硫化反应槽、中和搅拌槽、浓密机均采用密闭式,并在顶盖设有排风管,由引风机将溢出的气体引至尾气吸收塔,采用20%质量浓度的氢氧化钠溶液吸收。
35.经过上述实施例工艺处理后的含氰废液中铜、砷去除率达99﹪以上,氰化物的回收率可达95%以上,除杂后的含氰滤液返回氰化系统,使氰化物循环利用不对外排放,同时对接常规焙烧酸浸、萃取电积工艺产出阴极铜与铁精矿。
36.以上所述仅为本发明的较佳实施例,并不用以限制本发明,凡在本发明是的精神和原则之内,所作的任何修改、等同替换、改进等,均应包含在本发明的保护范围之内。