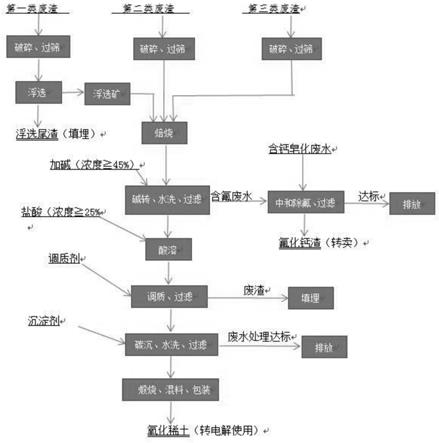
1.本发明涉及稀土熔盐电解技术领域,特别涉及一种从稀土熔盐废渣中高效回收稀土的方法。
背景技术:2.目前国内的稀土金属的制备一般采用的是稀土氧化物在氟盐体系下的熔盐电解的方式进行制备,在制备稀土金属的过程中难免会产生含有稀土的废渣,在氧化稀土-氟盐体系下熔盐电解制备稀土合金的过程中产生的含有有价稀土的废渣组成复杂,其中含有部分稀土金属合金、稀土氧化物、氟化稀土和大量的非稀土杂质,因此需要对其进行稀土回收处理。
3.目前,现有从稀土熔盐废渣中回收稀土的工艺主要为以下几种:(1)将废渣进行破碎后直接用盐酸浸出、过滤,得到酸浸液和滤渣,再将滤渣进行碱转、水洗、酸溶回收有价稀土;该回收工艺的稀土收率在83%左右,达不到回收有价稀土的利润预期,同时在酸浸过程中存在部分金属合金和酸发生反应生成氢气,在反应罐中散热条件差的情况下容易爆炸,发生安全事故,所以在生产上该工艺并没有广泛应用;(2)将废渣进行破碎后与氢氧化钠混合,然后高温焙烧,再进行水洗,并用盐酸浸出,除杂之后得到氯化混合稀土,例如中国专利cn110453098a、cn111534701a、cn107630143a等;该方法虽然简化了生产工艺,并被广泛研究,但在生产过程中,废渣与氢氧化钠在高温焙烧的情况下容易结块,并且对设备的腐蚀严重,在生产过程中不实用。
技术实现要素:4.本发明的发明目的在于:针对上述存在的问题,提供一种从稀土熔盐废渣中高效回收稀土的方法,本发明通过氧化焙烧+碱转+酸溶+碳沉的方式,在对生产设备要求不高的情况下,使稀土的回收率达到了95%以上,回收率高,该工艺流程并不复杂,物料成本不高,还避免了现有技术中存在的安全隐患,产生的含氟废水能够直接用来生产氟化钙产品,企业利润空间可观,克服了现有技术在生产实际中不适用的问题。
5.本发明采用的技术方案如下:一种从稀土熔盐废渣中高效回收稀土的方法,包括以下步骤:
6.s1、根据稀土氧化物-复盐体系电解产生熔盐废渣的性质,将废渣进行分类,将分类完成的废渣分别进行破碎,然后过150-250目筛(实际生产中,过150-200目筛的生产效果较为理想),得到原料;
7.s2、将分类的原料分别送至转窑中进行氧化焙烧,焙烧温度控制在450-550℃(熔盐废渣的最佳活化温度),焙烧时间为2-3h,得到焙烧物;
8.s3、合并焙烧物,然后加碱进行碱转,碱转温度控制至碱转料浆沸腾即可,碱转时间为3-5h,碱的加入量为氧化稀土重量的1.2-1.5倍,得到碱转好的料浆;
9.s4、对碱转好的料浆进行水洗,直至ph值为7-9为止,然后过滤得到水洗液和水洗
物;
10.s5、对水洗物进行酸溶处理,酸为盐酸,盐酸浓度最好不要小于25%,优选为31%,然后向酸溶液中加入调质剂进行调质处理,过滤后得到酸溶渣和酸溶料液;
11.s6、向酸溶料液中加入沉淀剂,沉淀完全后过滤,得到滤渣(碳酸稀土)和滤液,取滤渣进行煅烧,即得到氧化稀土,氧化稀土可作为电解车间的稀土原料使用。
12.在上述的步骤1中,将发生槽体渗漏被炉体填充物污染的电解质回收的废渣,以及电解槽炉体中的填充物出现玻璃化的情况而回收的废渣,此类废渣稀土含量在2-4%(%表示质量分数)之间,收集并分类为第一类废渣,第一类废渣主要是氟化稀土和含硅、铝、钙等杂质;在生产中更换阳极和拆除电解炉的过程中阳极材料表面回收的熔盐渣,收集并分类为第二类废渣,第二类废渣主要是氟化稀土、氧化稀土和含碳的熔盐渣;从除尘系统中回收的粉尘和在金属抛光过程中产生的含有氧化稀土、氟化稀土、金属和硅等粉尘杂质的废渣,收集并分类为第三类废渣。
13.进一步,对于第一类废渣,将其破碎并进行筛分后,采用现有稀土浮选工艺对其进行浮选,以得到稀土品位在65%以上的原料,一般情况下,现有稀土浮选工艺的稀土收率在75%左右,当然,也可以进行多次富集和浮选,以进一步提高稀土的收率和减少原料中的杂质,但是这样会使得成本显著升高,不建议采用。
14.在对原料进行氧化焙烧,可以对原料进行活化,由于原料的晶粒比较致密,经过氧化焙烧之后,可以将致密的晶粒焙烧成松散有裂缝的晶粒,其发生的主要反应方程式为:
15.①
:2c+o2=2co;c+o2=co216.②
:pr+o2→
pr6o
11
;nd+o2→
nd2o317.注:以镨钕泛指稀土re。
18.进一步,碱转过程中,其发生的主要反应方程式为:
19.③
:ref3+oh
-
=re(oh)3+f
-
20.④
:reo+h2o+oh
-
=re(oh)321.在s4中,水洗液即为含氟碱水,将水洗液和萃取钙皂化废水混合,通过调节ph值来回收混合液中的氟和钙,产出绿色环保的氟化钙产品。对水洗物进行酸溶时,其发生的主要反应方程式为:
22.⑤
:re(oh)3+3hcl=recl3+3h2o
23.调质处理时,其发生的主要反应方程式为:
24.⑥
:fe(oh)3+3hcl=fecl3+3h2o
25.在进行酸溶时,要先将部分盐酸(加入量为盐酸总加入量的1/3左右)加入反应槽中,再投加水洗渣,然后再补加剩余盐酸,将酸度控制在0.3mol/l以下,待反应完全后,升温至80℃以上,加调质剂调质待ph为4-4.5为止,主要是除去氯化稀土中的铁和铝等影响沉淀的杂质。调质剂一般为碳酸钠、碳酸钾等,优选为碳酸钠。
26.在上述方法中,沉淀剂一般为可溶性碳酸盐,以得到碳酸稀土沉淀物,例如碳酸钠、碳酸钾等,优选为碳酸钠。沉淀过滤后的废水排放至废水处理工序中,经处理后达标排放。
27.进一步,碱转时,料浆的固液比为1:(4-6),料浆碱度控制在2.5-4mol/l。
28.综上所述,由于采用了上述技术方案,本发明的有益效果是:本发明通过氧化焙烧
+碱转+酸溶+碳沉的方式,在对生产设备要求不高的情况下,使稀土的回收率达到了95%以上,回收率高,同时该工艺流程并不复杂,物料成本不高,还避免了现有技术中存在的安全隐患,产生的含氟废水能够直接用来生产氟化钙产品,企业利润空间可观,克服了现有技术在生产实际中不适用的问题,该工艺已成功应用于申请人的企业生产中。
附图说明
29.图1是本发明的一种从稀土熔盐废渣中高效回收稀土的方法流程示意图。
具体实施方式
30.下面结合附图,对本发明作详细的说明。
31.为了使本发明的目的、技术方案及优点更加清楚明白,以下结合附图及实施例,对本发明进行进一步详细说明。应当理解,此处所描述的具体实施例仅仅用以解释本发明,并不用于限定本发明。
32.如图1所示,一种从稀土熔盐废渣中高效回收稀土的方法,包括以下步骤:
33.s1、根据稀土氧化物-复盐体系电解产生熔盐废渣的性质,将废渣进行分类,将分类完成的废渣分别进行破碎,然后过150-250目筛,得到原料;
34.s2、将分类的原料分别送至转窑中进行氧化焙烧,焙烧温度控制在450-550℃,焙烧时间为2-3h,得到焙烧物;
35.s3、合并焙烧物,然后加碱进行碱转,一般加入浓度不小于45%的液碱,碱转温度控制至碱转料浆沸腾即可,碱转时间为3-5h,碱的加入量为氧化稀土重量的1.2-1.5倍,料浆的固液比为1:5,料浆碱度控制在2.5-4mol/l,得到碱转好的料浆;
36.s4、对碱转好的料浆进行水洗,直至ph值为7-9为止,然后过滤得到水洗液和水洗物;
37.s5、对水洗物进行酸溶处理,酸为盐酸,盐酸浓度最好不要小于25%,优选为31%,然后向酸溶液中加入调质剂进行调质处理,过滤后得到酸溶渣和酸溶料液,酸溶渣可直接填埋处理;
38.s6、向酸溶料液中加入沉淀剂,沉淀完全后过滤,得到滤渣(碳酸稀土)和滤液,取滤渣进行煅烧,即得到氧化稀土,氧化稀土可作为电解车间的稀土原料使用。
39.在上述的步骤1中,将发生槽体渗漏被炉体填充物污染的电解质回收的废渣,以及电解槽炉体中的填充物出现玻璃化的情况而回收的废渣,此类废渣稀土含量在2-4%(%表示质量分数)之间,收集并分类为第一类废渣,第一类废渣主要是氟化稀土和含硅、铝、钙等杂质;在生产中更换阳极和拆除电解炉的过程中阳极材料表面回收的熔盐渣,收集并分类为第二类废渣,第二类废渣主要是氟化稀土、氧化稀土和含碳的熔盐渣;从除尘系统中回收的粉尘和在金属抛光过程中产生的含有氧化稀土、氟化稀土、金属和硅等粉尘杂质的废渣,收集并分类为第三类废渣。对于第一类废渣,将其破碎并进行筛分后,采用现有稀土浮选工艺对其进行浮选,以得到稀土品位在65%以上的原料,浮选尾渣则填埋处理。一般情况下,现有稀土浮选工艺的稀土收率在75%左右,当然,也可以进行多次富集和浮选,以进一步提高稀土的收率和减少原料中的杂质,但是这样会使得成本显著升高,不建议采用。
40.在s4中,水洗液即为含氟碱水,将水洗液和萃取钙皂化废水混合,通过调节ph值来
回收混合液中的氟和钙,产出绿色环保的氟化钙产品,废水经处理后达标排放。
41.在进行酸溶时,要先将部分盐酸加入反应槽中,再投加水洗渣,然后再补加盐酸,将ph值控制在1-2之间,待反应完全后,升温至80℃以上,加调质剂调质待ph为4-4.5为止。调质剂一般为碳酸钠、碳酸钾等,优选为碳酸钠。
42.在上述方法中,沉淀剂一般为可溶性碳酸盐,以得到碳酸稀土沉淀物,例如碳酸钠、碳酸钾等,优选为碳酸钠。沉淀过滤后的废水排放至废水处理工序中,经处理后达标排放。
43.为了更好地突出本发明的技术优势,以下列举生产实例:
44.实例1
45.采用酸碱联合法回收金属工段废渣,包括如下步骤:
46.s1、一次酸浸,将金属工段的废渣品位较低的废渣,直接丢弃,将品位较高的废渣,破碎过筛,直接加酸溶解,然后澄清过滤,澄清液直接转移至除杂罐,废渣转至下一工序;
47.s2、二次酸浸,将一次酸浸渣中加入液碱进行碱转,然后在水洗,得到碱转渣,在将碱转渣加酸溶解,后再次澄清过滤,滤液和一次酸溶液合并,二次过滤渣同生产上的铈富集物渣混合烘干,打包出售。
48.将金属废渣通过酸碱联合法处理,生产上稀土的收率一般只有65-75%,达不到预期的83%的收率,同时采用该工艺在生产过程中存在安全隐患,主要是在酸溶过程中会产生氢气,酸溶过程属于放热反应,因此,在反应过程中如果加料过快则会影响散热,进而存在发生爆炸的危险。所以,该工艺已经停用。
49.实例2
50.采用本发明的工艺,其包括如下步骤:
51.s1、将氧化镨钕-氟盐体系熔盐电解的废渣按以下条件分类:将发生槽体渗漏被炉体填充物污染的电解质回收的废渣,以及电解槽炉体中的填充物出现玻璃化的情况而回收的废渣,收集并分类为第一类废渣;在生产中更换阳极和拆除电解炉的过程中阳极材料表面回收的熔盐渣,收集并分类为第二类废渣;从除尘系统中回收的粉尘和在金属抛光过程中产生的粉尘杂质,收集并分类为第三类废渣;
52.s2、第一类废渣中镨钕氧化物的含量一般在2.5%(经多批次采样分析后所得平均值),由于品位较低,将废渣破碎过筛之后再经浮选,得到品位为67.3%的稀土废渣,将二类和三类废渣分别破碎后过筛;
53.s3、将三类渣分别在回转窑中进行氧化焙烧,焙烧时间为2.5小时,焙烧温度为高温区540℃,将三种渣焙烧之后混合;
54.s4、将混合渣按照稀土总重量的1.3倍加入液碱(液碱的质量分数大于等于45%),再补加水,按照固液比1:5补加水溶液,碱转4小时,然后进行水洗,将碱转渣水洗至ph=8为止,洗水和萃取钙皂化废水中和,除氟、除重金属后达标排放;
55.s5、将水洗后的碱转渣进行酸溶,将酸溶液调质、碳沉、煅烧后根据要求进行混料交金属工段使用,酸熔渣中reo的含量为1.5%左右;
56.根据此工艺今年上半年处理废渣15吨(此重量包括浮选后的一类渣、二类渣和三类渣的总重量),其中镨钕氧化物的平均品位为57.2%,得到氧化镨钕8.35吨,按照此计算上半年处理废渣回收的氧化镨钕的收率为97.31%,如果加上浮选损失的部分稀土,折算后
的氧化镨钕的收率为95.32%。
57.综合实例1和实例2进行对比,采用本发明的工艺所回收稀土的收率比酸碱联合法回收废渣的收率要高,并且比采用酸碱联合法处理废渣要安全,从经济效果来说本发明更具有经济实用价值。
58.以上所述仅为本发明的较佳实施例而已,并不用以限制本发明,凡在本发明的精神和原则之内所作的任何修改、等同替换和改进等,均应包含在本发明的保护范围之内。