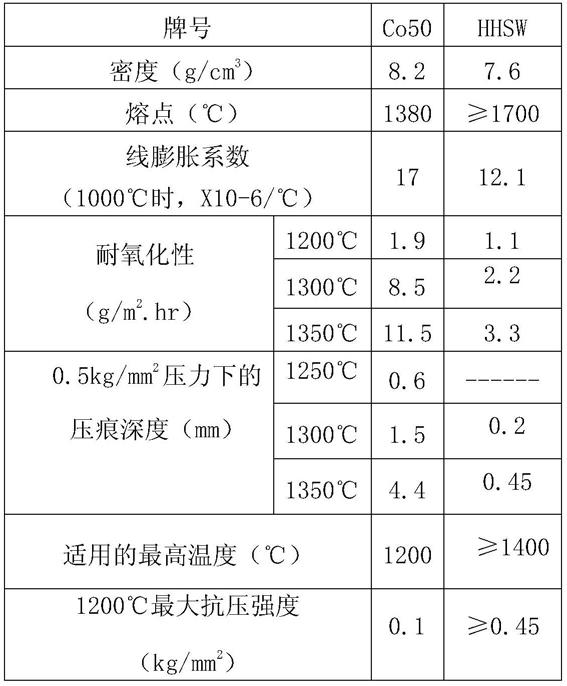
一种轧钢加热炉加热段垫块材料的生产工艺
【技术领域】
1.本发明涉及钢铁生产技术领域,是一种垫块材料的生产工艺。
背景技术:2.目前,推钢式加热炉和步进式加热炉高温加热段垫块材材料主要为co50,其熔点为1380℃
‑
1420℃,1200℃最大使用强度为0.1kg/mm2,加热炉垫块的损坯主要原因不是磨损、烧蚀氧化而造成的,垫块损坏主要原因是被钢坯压坏的,加热炉内不是所有的垫块都承受压力,设计时考虑的是全部垫块都承压,由于垫块承压超过了它的最大使用强度,垫块表面产生塑性变形出现凹坑,钢坯脱落的氧化皮在凹坑聚集并迅速长大,这些凸出的氧化皮会在钢坯下表面顶出凹坑,钢坯进入轧钢工序高压水很难清除凹坑内的氧化皮,会导致热轧材出现质量问题,而且会影响后期冷轧材的质量。
3.为解决这一问题通过在钴合金中加入大量w(≥10%wt),提高合金熔点约40
‑
50℃,性能得到了较大提高,使用效果良好,但由于机体还是奥氏体,高温下还是会出现塑性变形,迫切需要出现一种新的材料,使得在高温下具有高的硬度、强度、及耐磨性。
技术实现要素:4.本发明的目的是要提供一种具有高硬度、耐磨性强的轧钢加热炉加热段垫块材料的生产工艺。
5.本发明解决技术问题的方案是采用硅、锰、钼、钨、铁和铬做为原材料,通过以下步骤完成操作:
6.1、在中频感应电炉
7.中(带氩气保护)顺序加入纯铁、钨、钼、总重25
‑
35﹪的金属铬,待材料开始熔化后陆续加入剩余金属铬,升温到1800℃加入锰铁、硅铁,熔化;
8.2、出钢前,进行炉前取样检测化学成分,根据检测结果进行微调至成分合格;
9.3、浇包温度烘烤到600℃至630℃;
10.4、加入总重量2﹪硅
‑
钙合金脱氧剂进行炉内脱氧,升温到1900℃出钢,浇注前静置钢水,液面除渣,在浇包底部加入总重量1
‑2‰
的块状(粒度6
‑
10mm)重钇(y)变质剂,采用包内变质处理,同时把精密铸造模壳放到高频振动平台上,振动浇注,振动频率f≥20khf;浇注温度1780
‑
1800℃;其中步骤2中碳c≤0.08、磷p≤0.020、硫s≤0.020,硅si 0.6/1.00,锰mn 0.4/0.50,钼mo 2.5/4.5,钨w 5.0/7.0,铁fe7.0/11.0,其余为铬cr,作为基体,上述的份数是重量份数,按总份数100份计算,原材料中,锰和硅是以锰铁和硅铁状态存在的。
11.所述的硅
‑
钙合金脱氧剂进行炉内脱氧,采用钟罩法将硅
‑
钙合金脱氧剂压入熔炼炉的底部,使炉内合金进行充分脱氧。
12.具体物理性能参数如下。
[0013][0014]
本发明材料高温新材料垫块材质hhsw,熔点达1650℃,该材料在熔点前基本没有塑性变形,抗氧化性能提高,极限使用温度可达1500℃,最大承压能力是传统钴合金的4.5倍。
【具体实施方式】
[0015]
例1、本发明采用硅、锰、钼、钨、铁和铬做为原材料,通过以下步骤完成操作:
[0016]
1、在中频感应电炉中(带氩气保护)顺序加入纯铁、钨、钼、总重30﹪的金属铬,待材料开始熔化后陆续加入剩余金属铬,升温到1800℃加入锰铁、硅铁,熔化;
[0017]
2、出钢前,进行炉前取样检测化学成分,根据检测结果进行微调至成分合格;
[0018]
3、浇包温度烘烤到610℃;
[0019]
4、加入总重量2﹪硅
‑
钙合金脱氧剂进行炉内脱氧,升温到1900℃出钢,浇注前静置钢水,液面除渣,在浇包底部加入2
‰
的块状(粒度6
‑
10mm)重钇(y)变质剂,采用包内变质处理,同时把精密铸造模壳放到高频振动平台上,振动浇注(振动频率);浇注温度1780
‑
1800℃;其中步骤2中碳c≤0.08、磷p≤0.020、硫s≤0.020,硅si0.8,锰mn0.4,钼mo3.5,钨w6,铁fe9.0,其余为铬cr,原材料中,锰和硅是以锰铁和硅铁状态存在的。
[0020]
例2、本发明采用硅、锰、钼、钨、铁和铬做为原材料,通过以下步骤完成操作:
[0021]
1、在中频感应电炉中(带氩气保护)顺序加入纯铁、钨、钼、总重25﹪的金属铬,待材料开始熔化后陆续加入剩余金属铬,升温到1800℃加入锰铁、硅铁,熔化;
[0022]
2、出钢前,进行炉前取样检测化学成分,根据检测结果进行微调至成分合格;
[0023]
3、浇包温度烘烤到630℃;
[0024]
4、加入总重量2﹪硅
‑
钙合金脱氧剂进行炉内脱氧,升温到1900℃出钢,浇注前静置钢水,液面除渣,在浇包底部加入1
‰
的块状(粒度6
‑
10mm)重钇(y)变质剂,采用包内变质处理,同时把精密铸造模壳放到高频振动平台上,振动浇注(振动频率);浇注温度1780℃;其中步骤2中碳c≤0.08、磷p≤0.020、硫s≤0.020,硅si1.00,锰mn0.4,钼mo4.5,钨w5.0,铁fe11.0,其余为铬cr,原材料中,锰和硅是以锰铁和硅铁状态存在的。
[0025]
例3、本发明采用硅、锰、钼、钨、铁和铬做为原材料,通过以下步骤完成操作:
[0026]
1、在中频感应电炉中(带氩气保护)顺序加入纯铁、钨、钼、总重35﹪的金属铬,待材料开始熔化后陆续加入剩余金属铬,升温到1800℃加入锰铁、硅铁,熔化;
[0027]
2、出钢前,进行炉前取样检测化学成分,根据检测结果进行微调至成分合格;
[0028]
3、浇包温度烘烤到600℃;
[0029]
4、加入总重量2﹪硅
‑
钙合金脱氧剂进行炉内脱氧,升温到1900℃出钢,浇注前静置钢水,液面除渣,在浇包底部加入2
‰
的块状(粒度6
‑
10mm)重钇(y)变质剂,采用包内变质处理,同时把精密铸造模壳放到高频振动平台上,振动浇注(振动频率);
[0030]
浇注温度1780
‑
1800℃;其中步骤2中碳c≤0.08、磷p≤0.020、硫s≤0.020,硅si0.6,锰mn0.50,钼mo2.5,钨w7.0,铁fe7.0,其余为铬cr,原材料中,锰和硅是以锰铁和硅铁状态存在的。
技术特征:1.一种轧钢加热炉加热段垫块材料的生产工艺,其特征在于:采用硅、锰、钼、钨、铁和铬做为原材料,通过以下步骤完成操作:(1)在带氩气保护的中频感应电炉中顺序加入纯铁、钨、钼、总重25
‑
35﹪的金属铬,待材料开始熔化后陆续加入剩余金属铬,升温到1800℃加入锰铁、硅铁,熔化;(2)出钢前,进行炉前取样检测化学成分,根据检测结果进行微调至成分合格;(3)浇包温度烘烤到600℃至630℃;(4)加入总重量2﹪硅
‑
钙合金脱氧剂进行炉内脱氧,升温到1900℃出钢,浇注前静置钢水,液面除渣,在浇包底部加入总重量1
‑2‰
的块状重钇变质剂,其粒度为6
‑
10mm,采用包内变质处理,同时把精密铸造模壳放到高频振动平台上,振动浇注,振动频率f≥20khf;浇注温度1780
‑
1800℃;其中步骤(2)中碳c≤0.08、磷p≤0.020、硫s≤0.020,硅si 0.6/1.00,锰mn 0.4/0.50,钼mo 2.5/4.5,钨w 5.0/7.0,铁fe7.0/11.0,其余为铬cr,作为基体,上述的份数是重量份数,按总份数100份计算,原材料中,锰和硅是以锰铁和硅铁状态存在的。2.根据权利要求1所述的垫块材料的生产工艺,其特征在于:硅
‑
钙合金脱氧剂进行炉内脱氧,是采用钟罩法将硅
‑
钙合金脱氧剂压入熔炼炉的底部。3.根据权利要求1所述的垫块材料的生产工艺,其特征在于:采用硅、锰、钼、钨、铁和铬做为原材料,通过以下步骤完成操作:(1)在带氩气保护中频感应电炉中顺序加入纯铁、钨、钼、总重30﹪的金属铬,待材料开始熔化后陆续加入剩余金属铬,升温到1800℃加入锰铁、硅铁,熔化;(2)出钢前,进行炉前取样检测化学成分,根据检测结果进行微调至成分合格;(3)浇包温度烘烤到610℃;(4)加入总重量2﹪硅
‑
钙合金脱氧剂进行炉内脱氧,升温到1900℃出钢,浇注前静置钢水,液面除渣,在浇包底部加入2
‰
的块状重钇变质剂,其粒度为6
‑
10mm,采用包内变质处理,同时把精密铸造模壳放到高频振动平台上,振动浇注(振动频率);浇注温度1780
‑
1800℃;其中步骤2中碳c≤0.08、磷p≤0.020、硫s≤0.020,硅si0.8,锰mn0.4,钼mo3.5,钨w6,铁fe9.0,其余为铬cr,原材料中,锰和硅是以锰铁和硅铁状态存在的。
技术总结一种轧钢加热炉加热段垫块材料的生产工艺,涉及钢铁生产技术领域,是将硅、锰、钼、钨、铁和铬做为原材料,顺序加入中频感应电炉中,高温溶化,进行浇注,其中硅Si 0.6/1.00,锰Mn 0.4/0.50,钼Mo 2.5/4.5,钨W 5.0/7.0,铁Fe7.0/11.0,其余为铬Cr,作为基体。本发明材料高温新材料垫块材质HHSW,熔点达1650℃,该材料在熔点前基本没有塑性变形,抗氧化性能提高,极限使用温度可达1500℃,最大承压能力是传统钴合金的4.5倍。传统钴合金的4.5倍。
技术研发人员:韦先平 王孟先 徐永晓 范伟光
受保护的技术使用者:烟台百思特炉管厂
技术研发日:2021.08.05
技术公布日:2021/11/8