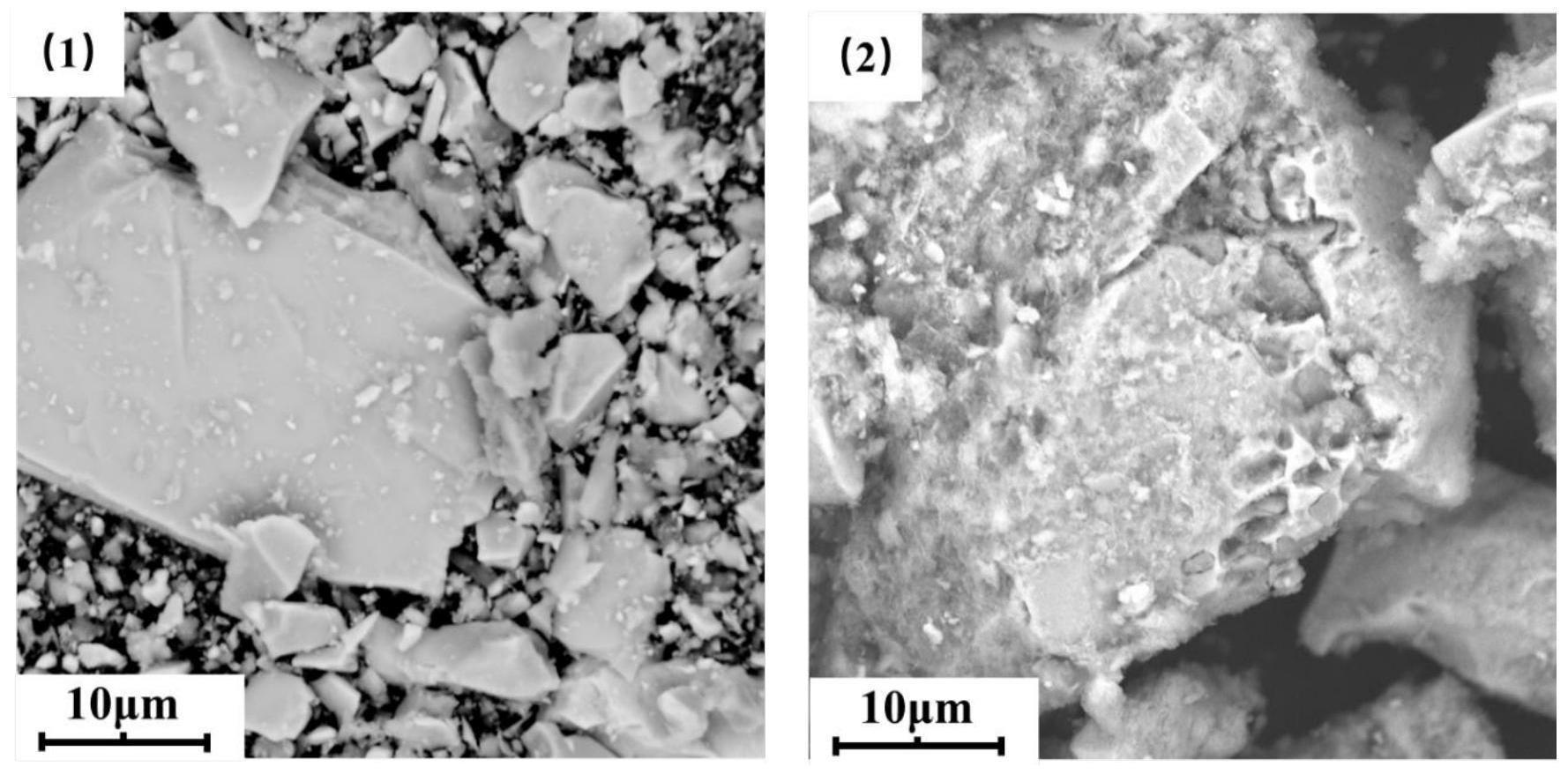
1.本发明涉及一种超声强化低浓度臭氧高效预氧化硫化金精矿的方法,属于金精矿处理技术领域。
背景技术:2.目前在工业上主要采用预氧化
‑
氰化提金工艺。采用预氧化使金的包裹矿物
‑
硫化物氧化,形成多孔状物料,增大氰化物与细粒、微细粒金的接触机会和表面积;并去除砷、锑、炭等妨碍氰化浸出、降低回收率的有害杂质,或改变有害杂质的理化性能。现有各类预处理工艺针对不同难处理金矿,均可利用各自优势提高黄金的回收率,然而采用焙烧、加压氧化等预处理工艺会直接增加生产成本、固定资产投入,成本过高致使整个提取工艺失效;而采用常规化学氧化由于操作条件温和很难达到理想的预处理效果。
技术实现要素:3.本发明针对现有技术中硫化金精矿中金提取的问题,提供一种超声强化低浓度臭氧高效预氧化硫化金精矿的方法,即利用超声强化低浓度臭氧,提高黄铁矿包裹体氧化效果,超声空化作用促使溶液中溶解的低浓度臭氧与水反应产生高氧化性的中间产物(
·
oh),利用超声的机械效应提高溶液的传质效率,破坏包裹体,降低矿石粒度,提高后续浸出效率。
4.一种超声强化低浓度臭氧高效预氧化硫化金精矿的方法,具体步骤如下:
5.(1)将硫化金精矿细磨至
‑
150目占95%以上得到硫化金精矿粉;
6.(2)将硫化金精矿粉、氢氧化钠和水混合均匀得到金矿矿浆;
7.(3)在超声波和机械搅拌条件下,往金矿矿浆中通入含臭氧的空气并进行超声强化预氧化处理,固液分离,固体经洗涤、烘干得到预处理金矿矿粉;其中含臭氧的空气中臭氧体积浓度为5.5~10.5%,臭氧的通入速率为1.7~5.1g/h;
8.(4)预处理金矿矿粉和氰化钠加入到水中混合均匀,通入空气,在搅拌条件下进行超声波强化浸出得到金浸出液和浸出渣;
9.所述步骤(2)硫化金精矿粉与水的固液比g:ml为1:1~1:5,金矿矿浆中氢氧化钠的浓度为0.5~5mol/l;
10.所述步骤(3)超声波频率为20~40khz,超声功率为100~800w,超声强化预氧化处理的温度为20~50℃,时间为2~4h;搅拌速率为300~700rpm;
11.以预处理金矿粉计,步骤(4)氰化钠的加入量为2~10kg/t;预处理金矿矿粉与水的固液比g:ml为1:2~1:4,超声波强化浸出的温度为20~50℃,时间为4~18h,超声波频率为20~40khz,超声功率为200~1000w,空气通入速率为50~200l/h,ph值为10.5~11.5,搅拌速率为300~700rpm。
12.超声强化低浓度臭氧高效预氧化硫化金精矿的原理:超声强化低浓度臭氧氧化过程,同时破坏金包裹体(黄铁矿)结构,暴露被包裹的金
[0013][0014][0015][0016]
臭氧分解后产生新生态氧原子,在水中可形成具有强氧化作用基团
‑
羟基自由基,可在较低温度下把水溶液中大多数单质和化合物氧化到最高氧化态,超声与低浓度臭氧协同浸出过程中,经过超声的分散剪切作用,低浓度臭氧的气泡被粉碎成更小的微气泡,从而增加了与矿物的接触面积,增加了混合程度,提高了臭氧的传质速率,强化了臭氧和矿物的反应,增强了臭氧的氧化能力。
[0017]
本发明的有益效果是:
[0018]
(1)本发明在矿粉、氢氧化钠和水充分混合所得的矿浆中通入低浓度臭氧,利用低浓度臭氧、超声和氢氧化钠的协同作用,进行氧化还原反应,其反应温度较低,且可以在常温常压下进行,既可以节约能源,又降低了对设备的材质要求;
[0019]
(2)本发明利用超声强化低浓度臭氧预处理硫化金精矿,可缩短后续浸出时间,提高了对金矿石的预处理和浸出效果,在超声的过程中破碎矿石,使被包裹的金暴露出来,矿石粒度可比超声处理前降低20%~50%;同时超声可以促进低浓度臭氧分解为氧化性更强的自由基,促进氧化反应的进行,提高臭氧的利用率,降低臭氧消耗。
附图说明
[0020]
图1为实施例1硫化金精矿处理前和处理后的sem图;
[0021]
图2为实施例1超声强化低浓度臭氧预氧化处理金矿的浸出率;
[0022]
图3为实施例2超声强化低浓度臭氧预氧化处理金矿的浸出率;
[0023]
图4为实施例3超声强化低浓度臭氧预氧化处理金矿的浸出率;
[0024]
图5为实施例4超声强化低浓度臭氧预氧化处理金矿的浸出率;
[0025]
图6为实施例1不同预处理后粒度变化图。
具体实施方式
[0026]
下面结合具体实施方式对本发明作进一步详细说明,但本发明的保护范围并不限于所述内容。
[0027]
实施例1:本实施例硫化金精矿的金品位3.23g/t,银品位24.5g/t,常规直接氰化浸出金浸出率仅为49.1%,银浸出率为9.8%,平均粒度为33.75μm;
[0028]
一种超声强化低浓度臭氧高效预氧化硫化金精矿的方法,具体步骤如下:
[0029]
(1)将硫化金精矿细磨至
‑
150目占95%以上得到硫化金精矿粉;
[0030]
(2)将硫化金精矿粉、氢氧化钠和水混合均匀得到金矿矿浆;其中硫化金精矿粉与水的固液比g:ml为1:4,金矿矿浆中氢氧化钠的浓度为0.5mol/l;
[0031]
(3)在超声波和机械搅拌条件下,往金矿矿浆中通入含臭氧的空气并进行超声强化预氧化处理,固液分离,固体经洗涤、烘干得到预处理金矿矿粉;其中含臭氧的空气中臭氧体积浓度为5.7%,臭氧的通入速率为2.0g/h;固液比g:ml为1:4;超声波频率为20khz,超
声功率分别为240w、360w、480w、600w、720w,超声强化预氧化处理的温度为30℃,时间为3h;搅拌速率为300rpm;
[0032]
硫化金精矿处理前和处理后的sem图见图1,(1)为处理前硫化金精矿sem图,(2)为处理后硫化金精矿sem图,从图1中可知,预处理前硫化物包裹体结构完整,表面光滑,超声臭氧预处理后硫化物包裹体表面产生明显孔洞及裂缝,颗粒尺寸减小,有利于金的浸出;
[0033]
不同预处理后粒度变化图见图6,从图6可知,未处理硫化金精矿粉的平均粒度为33.75μm,由于常规臭氧氧化后铁氧化物包覆在硫化物表面,形成二次包裹,并会产生团聚,常规臭氧预处理(常规臭氧浓度)的硫化金精矿粉的平均粒度为49.67μm,经超声强化低浓度臭氧预处理的硫化金精矿粉的平均粒度为18.69μm;
[0034]
(4)预处理金矿矿粉和氰化钠加入到水中混合均匀,通入空气,在搅拌条件下进行超声波强化浸出5h得到金浸出液和浸出渣;以预处理金矿粉计,氰化钠的加入量为3kg/t;预处理金矿矿粉与水的固液比g:ml为1:2,超声波强化浸出的温度为25℃,超声波频率为28khz,超声功率为0.5kw,空气通入速率为150l/h,ph值为11
±
0.5,搅拌速率为500rpm;
[0035]
超声强化低浓度臭氧预氧化处理金矿的浸出率随超声强化预氧化处理中超声功率的变化见图2,从图2可知,随着超声功率的提高,金银浸出率均在提高,金浸出率在720w时达到最高,浸出率为87.23%,银浸出率在480w时达到最高,为46.84%。
[0036]
实施例2:本实施例硫化金精矿的金品位27.5g/t,银品位107.4g/t,直接常规氰化浸出工艺所获得的金浸出率仅为49.1%,银浸出率为9.8%,平均粒度39.77μm;
[0037]
一种超声强化低浓度臭氧高效预氧化硫化金精矿的方法,具体步骤如下:
[0038]
(1)将硫化金精矿细磨至
‑
250目占95%以上得到硫化金精矿粉;
[0039]
(2)将硫化金精矿粉、氢氧化钠和水混合均匀得到金矿矿浆;其中硫化金精矿粉与水的固液比g:ml为1:5,金矿矿浆中氢氧化钠的浓度为4mol/l;
[0040]
(3)在超声波和机械搅拌条件下,往金矿矿浆中通入含臭氧的空气并进行超声强化预氧化处理,固液分离,固体经洗涤、烘干得到预处理金矿矿粉;其中含臭氧的空气中臭氧体积浓度为8.2%,臭氧的通入速率为4.3g/h;超声波频率为20khz,超声功率为480kw,超声强化预氧化处理的温度分别为15℃、30℃、50℃、65℃和85℃,时间为4h;搅拌速率为500rpm;
[0041]
本实施例预处理金矿矿粉的平均粒度为14.47μm;
[0042]
(4)预处理金矿矿粉和氰化钠加入到水中混合均匀,通入空气,在搅拌条件下进行超声波强化浸出8h得到金浸出液和浸出渣;以预处理金矿粉计,氰化钠的加入量为10kg/t;预处理金矿矿粉与水的固液比g:ml为1:2,超声波强化浸出的温度为25℃,超声波频率为28khz,超声功率为0.5kw,空气通入速率为200l/h,ph值为11
±
0.5,搅拌速率为500rpm;
[0043]
超声强化低浓度臭氧预氧化处理金矿的浸出率随超声强化预氧化处理中超声温度的变化见图3,从图3可知,金银浸出率均随着温度的提高而提高,金浸出率在50℃时即可达到最佳,浸出率为89.32%;银浸出率在65℃时达到最高,浸出率为61.24%。
[0044]
实施例3:本实施例硫化金精矿的金品位35.2g/t,银品位73.42g/t,直接常规氰化浸出工艺所获得的金浸出率仅为32.53%,银浸出率为17.24%,平均粒度41.34μm;
[0045]
一种超声强化低浓度臭氧高效预氧化硫化金精矿的方法,具体步骤如下:
[0046]
(1)将硫化金精矿细磨至
‑
200目占95%以上得到硫化金精矿粉;
[0047]
(2)将硫化金精矿粉、氢氧化钠和水混合均匀得到金矿矿浆;其中硫化金精矿粉与水的固液比g:ml为1:4,金矿矿浆中氢氧化钠的浓度为3mol/l;
[0048]
(3)在超声波和机械搅拌条件下,往金矿矿浆中通入含臭氧的空气并进行超声强化预氧化处理,固液分离,固体经洗涤、烘干得到预处理金矿矿粉;其中含臭氧的空气中臭氧体积浓度为8.0%,臭氧的通入速率分别为1.7g/h、2.4g/h、3.2g/h、4.1g/h和5.1g/h;超声波频率为30khz,超声功率为800w,超声强化预氧化处理的温度为50℃,时间为5h;搅拌速率为500rpm;
[0049]
本实施例预处理金矿矿粉平均粒度为18.25μm;
[0050]
(4)预处理金矿矿粉和氰化钠加入到水中混合均匀,通入空气,在搅拌条件下进行超声波强化浸出8h得到金浸出液和浸出渣;以预处理金矿粉计,氰化钠的加入量为10kg/t;预处理金矿矿粉与水的固液比g:ml为1:5,超声波强化浸出的温度为30℃,超声波频率为20khz,超声功率为600w,空气通入速率为120l/h,ph值为11
±
0.5,搅拌速率为400rpm;
[0051]
超声强化低浓度臭氧预氧化处理金矿的浸出率随超声强化预氧化处理中超声温度的变化见图4,从图4可知,臭氧流量为1.7g/l时,金浸出率为66.74%,银浸出率为34.25%;随着臭氧流量的提高,金银浸出率均不同程度的提高;金浸出率在臭氧浓度达到2.4g/l时达到最大,为84.24%;银浸出率在5.1g/l时达到最大,为57.74%。
[0052]
实施例4:本实施例硫化金精矿的金品位7.82g/t,银品位52.52g/t,直接常规氰化浸出工艺所获得的金浸出率仅为27.42%,银浸出率为7.45%,平均粒度52.43μm;
[0053]
一种超声强化低浓度臭氧高效预氧化硫化金精矿的方法,具体步骤如下:
[0054]
(1)将硫化金精矿细磨至
‑
150目占95%以上得到硫化金精矿粉;
[0055]
(2)将硫化金精矿粉、氢氧化钠和水混合均匀得到金矿矿浆;其中硫化金精矿粉与水的固液比g:ml为1:3,金矿矿浆中氢氧化钠的浓度分别为0mol/l、0.5mol/l、1.5mol/l、2mol/l、3mol/l和4mol/l;
[0056]
(3)在超声波和机械搅拌条件下,往金矿矿浆中通入含臭氧的空气并进行超声强化预氧化处理,固液分离,固体经洗涤、烘干得到预处理金矿矿粉;其中含臭氧的空气中臭氧体积浓度为4.7%,臭氧的通入速率为4.7g/h;超声波频率为20khz,超声功率为550w,超声强化预氧化处理的温度为40℃,时间为5h;搅拌速率为600rpm;
[0057]
本实施例预处理金矿矿粉的平均粒度为27.52μm;
[0058]
(4)预处理金矿矿粉和氰化钠加入到水中混合均匀,通入空气,在搅拌条件下进行超声波强化浸出6h得到金浸出液和浸出渣;以预处理金矿粉计,氰化钠的加入量为7.5kg/t;预处理金矿矿粉与水的固液比g:ml为1:3,超声波强化浸出的温度为40℃,超声波频率为20khz,超声功率为700w,空气通入速率为180l/h,ph值为11
±
0.5,搅拌速率为750rpm;
[0059]
超声强化低浓度臭氧预氧化处理金矿的浸出率随超声强化预氧化处理中超声温度的变化见图5,从图5可知,氢氧化钠浓度为0mol/l时,金浸出率为46.23%,银浸出率为33.25%;当加入氢氧化钠后,金浸出率上升至80%以上,银浸出率上升至48%以上。金银最大浸出率均为氢氧化钠浓度为0.5mol/l时,金浸出率为90.34%,银浸出率为50.48%。
[0060]
以上结合附图对本发明的具体实施方式作了详细说明,但是本发明并不限于上述实施方式,在本领域普通技术人员所具备的知识范围内,还可以在不脱离本发明宗旨的前提下作出各种变化。