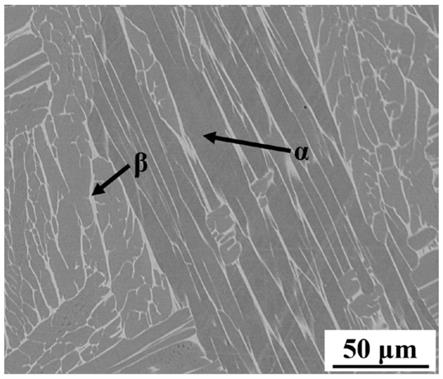
一种高塑性原位网状tic增强钛基复合材料及其制备方法
技术领域
1.本发明涉及金属基复合材料材料的粉末冶金技术领域,尤其涉及一种高塑性原位网状tic增强钛基复合材料及其制备方法。
背景技术:2.钛合金具有高强度、低密度和优异的抗腐蚀性,广泛应用于航空航天、生物医学及化工机械等领域。在钛及钛合金中引入陶瓷增强相形成不连续增强钛基复合材料,能有效改善基体组织,提高材料的强度、硬度与耐磨性,进一步拓宽其应用领域。然而,复合材料强度提升的同时,塑性会显著下降。根据hashin-shtrikman(h-s)理论中性能上限对应的硬相包围软相结构,使增强相呈三维网状分布,有效解决钛基复合材料塑性差的问题。
3.drtmcs中增强相的引入方式有外加法和原位生成法,原位drtmcs中的增强相和基体具有更好的界面结合。其中原位tic被广泛认为是钛基复合材料最优的增强体之一,碳源主要来自石墨粉、烃类气体(ch4)、纳米碳材料(石墨烯、碳纳米管、纳米金刚石)。
4.在网状原位tic增强钛基复合材料方面,huang等采用石墨做碳源,热压烧结制备了网状结构5vol.%tic/tc4复合材料,但是由于基体完全被tic墙割断连接,表现出较低的塑性。zhang等分别采用纳米金刚石与石墨烯做碳源,sps制备了混杂增强网状结构钛基复合材料,材料强度提升的同时维持较好的塑性。lu等通过sps制备的gnps/ti复合材料抗拉强度由基体的647.96mpa提升至820.97mpa,而塑性仅仅从24.4%降至21.5%。
5.采用金属碳化物作为碳源,既可以原位生成tic,金属原物又可以起到固溶强化的作用。然而,目前还未有通过金属碳化物作为碳源,制备网状tic/tc4复合材料。
技术实现要素:6.本发明的目的在于克服上述现有技术的缺点和不足,提供一种高塑性原位网状tic增强钛基复合材料及其制备方法。本发明制备的金属碳化物作为碳源的原位tic增强钛基复合材料,同时具有较高的强度和较好的塑性,满足工程中多样化的需求。
7.本发明首次采用金属碳化物vc作为碳源来制备原位网状tic增强tc4复合材料。制备的tic增强钛基复合材料中,tic呈非均匀的准连续网状分布分布,基体未被割裂,其塑性得到很好的发挥,同时,基体组织较tc4合金大幅细化,材料强度也较tc4合金大幅提高。本发明制备的网状tic增强tc4复合材料,tic呈网状分布,基体组织细小,抗拉强度1058~1097mpa,延伸率19.3~20.3%,远高于均匀分布的tic增强tc4复合材料。
8.本发明通过下述技术方案实现:
9.一种高塑性原位网状tic增强钛基复合材料的制备方法,包括如下步骤:
10.步骤一:将金属碳化物粉末、tc4合金粉末、不锈钢球装入密闭容器中,向容器充入保护气体后机械混合,得到金属碳化物/钛合金混合粉末;
11.步骤二:将步骤一混合得到金属碳化物/钛合金混合粉末,装入石墨模具中,随后将石墨模具放入真空热压烧结炉中进行热压烧结,热压烧结完成后随炉冷却至室温。
12.步骤一中,金属碳化物粉末为mo2c或vc粉末(颗粒呈无规则形状),平均颗粒尺寸0.8~2μm。
13.步骤一中,tc4合金粉末呈球形,采用等离子旋转电极雾化法制备,粒径尺寸为40~60μm。
14.步骤一中,金属碳化物粉末和钛合金粉末的质量比为1:99~3:97。
15.步骤一中,不锈钢球直径为10mm,不锈钢球总质量为粉末总质量的3~7倍。
16.步骤一中,机械混合所采用的密闭容器为滚筒式球磨罐,保护气体为纯度》99.9%的氩气,机械混合的设备为滚筒式混料机,转速60~90转/min,混粉时间10~15h。
17.步骤二中,热压烧结温度为1050~1200℃,压力为20~30mpa,保温保压45~60min。
18.步骤二中,真空热压烧结炉的升温速率为10~20℃/min,真空度5
×
10-3
pa以下。
19.采用本发明上述制备方法,即可获得高塑性原位网状tic增强钛基复合材料。
20.本发明相对于现有技术,具有如下的优点及效果:
21.力学性能优异。尤其是塑性远超传统的均匀分布tic增强钛复合材料;传统的tic增强钛基复合材料强度提升的同时,塑性会急剧下降。本发明制备的tic增强钛基复合材料中,tic呈非均匀的准连续网状分布,基体未被割裂,其塑性得到很好的发挥。
22.工艺流程短。目前网状tic增强钛基复合材料多采用纳米碳材料作为碳源,由于纳米材料容易团聚,一般混粉流程比较复杂。本发明材料微米vc最为碳源,只要简单的不锈钢辅助混粉即可使增强相均匀分布在tc4粉末表面,大大降低了材料的制备难度。
23.本发明显著提高了原位网状tic增强钛基复合材料的塑性,获得了优异的综合力学性能,对拓宽钛基复合材料的应用范围具有重大意义。
附图说明
24.图1为对比例1中tc4材料的背散射电子图像。
25.图2为实施例1的步骤(2)中所得复合材料的背散射电子图像。
26.图3为对比例1中tc4合金与实施例1中复合材料的室温拉伸应力应变曲线。
27.图4为实施例1中钛基复合材料的拉伸断口。
具体实施方式
28.下面结合具体实施例对本发明作进一步具体详细描述。
29.对比例1
30.(1)将粒径为40~80μm的tc4粉末装入石墨模具中进行热压烧结,烧结温度1200℃,压力30mpa,保温保压50min,真空热压烧结炉的升温速率为20℃/min,真空度5
×
10-3
pa,冷却后得到tc4材料。
31.(2)图1是对比例1中tc4材料的背散射电子图像。可以看出,tc4基体由层片状α相及相间β组成,是典型的魏氏体组织。
32.(3)本对比例步骤(1)得到的复合材料试样的室温拉伸应力应变曲线见图3。采用电子万能试验机测试其力学性能,检测得到其室温屈服强度为736mpa,抗拉强度为820mpa,延伸率为8.4%。
33.实施例1
34.(1)选用平均粒径尺寸为0.8μm的无规则形状vc粉末及粒径范围为40~80μm的球形tc4粉末,质量比为2:98,不锈钢球直径10mm,球料比3:1,将粉末和不锈钢球装入球磨罐中抽真空后充入高纯氩气,将球磨罐装在滚筒式混料机上混粉,混料机转速为60转/min,运行时间10h。
35.目的是为了使细小的vc粉末均匀粘附在粗大的tc4合金粉末表面,这是烧结后tic呈网状分布的关键。
36.(2)将混合粉末装入石墨模具中进行热压烧结,烧结温度1050℃,压力20mpa,保温保压45min,真空热压烧结炉的升温速率为10℃/min,真空度5
×
10-3
pa,冷却后得到高塑性原位网状tic增强tc4复合材料。
37.目的是为了使tc4粉末发生冶金结合,使vc与基体发生原位反应生成tic增强相起到限制晶粒长大的作用;使v固溶到基体中起到固溶强化的作用,从而获得优异的综合力学性能。
38.(3)本实施例步骤(2)中所得复合材料的背散射扫面电子形貌如图2所示。可以看出,tic颗粒呈准连续网状分布在原始颗粒的界面,其基体组织较tc4合金明显细化。
39.(3)本实施例步骤(2)得到的复合材料试样的室温拉伸应力应变曲线如图3所示。采用电子万能试验机测试其力学性能,检测得到其室温屈服强度为944mpa,抗拉强度为1098mpa,延伸率为20.3%。与不含增强相的tc4试样相比,复合材料的室温屈服强度提高了208mpa,抗拉强度提高了278mpa,而延伸率提高了11.9%。
40.(4)本实施例步骤(2)中复合材料的拉伸断口如图4所示。拉伸试样经打磨后进行室温拉伸性能测试,对断后的试样采用扫描电镜观察其断口形貌,发现复合材料的拉伸断口上表现为大量尺寸大且深浅不一的韧窝,其断裂方式为明显的韧性断裂。
41.(5)实验结果表明,按所述工艺制备的原位网状tic增强tc4复合材料,tic颗粒呈准连续网状分布在原始颗粒的界面,其基体组织较tc4合金明显细化,室温力学性能大幅提升,并且塑性远高于均匀分布tic增强tc4复合材料,可满足工程中多样化的需求。
42.实施例2
43.(1)选用平均粒径尺寸为2μm的无规则形状vc粉末及粒径范围为40~80μm的球形tc4粉末,质量比为3:97,不锈钢球直径10mm,球料比7:1,将粉末和不锈钢球装入球磨罐中抽真空后充入高纯氩气,将球磨罐装在滚筒式混料机上混粉,混料机转速为90转/min,运行时间15h。
44.目的是为了使细小的vc粉末均匀粘附在粗大的tc4合金粉末表面,这是烧结时tic呈网状分布的关键。
45.(2)将混合粉末装入石墨模具中进行热压烧结,烧结温度1200℃,压力30mpa,保温保压60min,真空热压烧结炉的升温速率为20℃/min,真空度5
×
10-3
pa,冷却后得到高塑性原位网状tic增强tc4复合材料。
46.目的是为了使tc4粉末发生冶金结合,使vc与基体发生原位反应生成tic增强相起到限制晶粒长大的作用;使v固溶到基体中起到固溶强化的作用,从而获得优异的综合力学性能。
47.(3)在步骤(2)获得的复合材料中线切割获得拉伸试样,采用电子万能试验机测试
其力学性能,检测得到其室温屈服强度为938mpa,抗拉强度为1056mpa,延伸率为19.3%。
48.综上所述,本发明所制备的纯钛金属材料,组织均匀细化,其室温屈服强度为938~944mpa,抗拉强度为1056~1098mpa,断后伸长率为19.3~20.3%,综合性能远高于基体tc4合金。
49.如上所述,便可较好地实现本发明。
50.本发明的实施方式并不受上述实施例的限制,其他任何未背离本发明的精神实质与原理下所作的改变、修饰、替代、组合、简化,均应为等效的置换方式,都包含在本发明的保护范围之内。