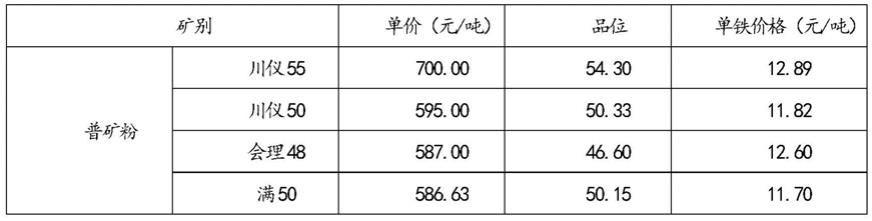
1.本发明涉及一种提高混匀矿中钢渣配比的方法,属于炼钢技术领域。
背景技术:2.混匀矿作为烧结生产的主要原料,其质量与烧结、高炉生产稳定息息相关,混匀矿生产就是将符合要求的不同品种的铁原料,根据高炉对烧结矿的要求按照一定的比例准确配料,采用连续均匀布料堆积而形成大堆混匀矿。钢渣是炼钢工艺生产过程中产生的含铁废料,可作为冶炼溶剂参与混匀矿的配料得到循环利用。但在实际混匀矿生产中,由于钢渣存在粒度不均匀、含有明铁、化学成份波动大、烧损较高等情况,在烧结机“一拖三”(一台烧结机供应三座高炉的用料)严峻保产稳质的压力情况下,钢渣的使用配比仅能维持在最高2.5%左右,导致其综合回收利用率仅为65%左右,剩余钢渣的堆积不仅占用了工厂有限的场地资源,也给公司环保管控带来了较大的难度。
3.以钢铁产业为主的钢铁联合生产企业每年需要大量矿石,以年产200万吨钢规模的钢铁厂为例,年需铁矿石420万吨,其中烧结用铁矿粉251万吨。而铁矿石随国际矿石价格的升高而逐年上涨,造成了采购成本上升,原料配料成本大幅增加。而现有钢铁厂每年却有大量含铁废料的富余,比如钢渣,其堆积不仅占用了工厂有限的场地资源,也提高了工厂生产管控的难度,若采用外运渣场处理外卖的方式,铁元素又会流失,造成极大的浪费。
技术实现要素:4.有鉴于此,针对上述现有技术的不足,本发明提供了一种提高混匀矿中钢渣配比的方法,以解决现有生产过程中的钢渣利用率低、铁元素流失浪费的问题。
5.为解决以上技术问题,本发明的技术方案提供了一种提高混匀矿中钢渣配比的方法,它包括下述步骤:(1)对钢渣进行破碎处理,要求破碎后钢渣的粒度≤10mm;(2)对钢渣进行磁选处理,要求磁选后钢渣的全铁含量为18%≤tfe≤23%;(3)根据炼钢冶炼不同钢种对铁水p含量的要求,调整参与混匀配矿的配料结构;(4)混匀矿的烧结方式为“厚料层、慢机速”。
6.其中,所述炼钢冶炼不同钢种对铁水p含量的要求为:
7.(1)对于优钢钢种,要求铁水p≤0.1%;
8.(2)对于板、型钢种,要求铁水p≤0.12%;
9.(3)对于普钢钢种,要求铁水p≤0.14%。
10.所述调整参与混匀配矿的配料结构的方法为:在钢渣配比为5%的条件下,调整高磷矿粉与低磷矿粉的比例,保证铁水中的p含量在要求范围内。高磷矿粉中全磷含量为25~35%,低磷矿粉中全磷含量为5~10%。
11.优选的是,钢渣参与混匀矿的配料由配料室单独装仓下料。本发明通过优化变更钢渣参与混匀矿配料方式,由预配料粗配变更为配料室单独装仓、稳定下料,提高了混匀矿的混匀度。
12.优选的是,针对混匀矿中提高钢渣的配比后,含有明铁、烧损较高的状况,烧结生产过程中应勤清理台车篦条,具体为混匀矿在烧结生产过程中台车篦条的清理频率为每2~3小时一次。因为钢渣含有明铁,烧结生产过程中容易糊死台车篦条,从而造成台车抽风压力提高、大烟道负压上升;而钢渣烧损达到6%,在一台烧结机供应三座高炉用料情况下,保产压力会上升。
13.针对钢渣的使用,坚持“厚料层、慢机速”原则,以首保烧结矿质量为前提,摸索出不同钢渣配比情况下的产量与经济指标的最佳平衡。即钢渣配比提至5%,混匀矿烧结时控制烧结终点温度≥480℃,烧结机的机速控制为2.01~2.09m/mi n,料层厚度控制为750~780mm。
14.与现有技术相比,本发明对钢渣进行了磁选处理,去除了其中的大块明铁,收窄了化学成分波动区间;优化变更了钢渣参与混匀矿的配料方式,由预配料粗配变更为配料室单独装仓、稳定下料,提高了混匀矿的混匀度;针对钢渣粒度不均匀的状况,对钢渣进行了破碎处理,要求破碎后钢渣的粒度≤10mm,保证了混合料的制粒效果;针对钢渣含有明铁、烧损较高状况,烧结生产过程中勤清理台车篦条,以稳定大烟道负压在工艺控制范围内为核心,摸索出了机速、料层厚度与终点温度控制的合理匹配范围。
15.通过上述步骤,本发明有效将混合矿中钢渣的配比由现有技术的2.5%提升至5%,既节约了混匀矿生产的配料成本,又解决了钢渣利用率低带来的钢渣堆积占用资源和钢渣外卖铁元素流失浪费的问题。
具体实施方式
16.为了使本领域的技术人员更好地理解本发明的技术方案,下面结合具体实施方式对本发明作进一步的详细说明。
17.下述实施例所用钢渣均为本发明申请人四川德胜集团钒钛有限公司炼钢过程中产生的,其具体化学成分为:
18.sio2%cao%mgo%al2o3%tio2%v2o5%p
205
%全铁(tfe)%8-1337-426-72-31.8-2.52.5-41.8-2.445-52
19.混匀矿生产所用配料如下表所示:
20.[0021][0022]
理论上,钢渣配比每提高1%,即可降低普矿粉或钒精粉配比1%。从单铁价格性价比上考虑,选取最优太和钒精粉作对比,钢渣配比每提高1%,混匀矿配料成本最少可降低:(586.6-200)/100≈3.9元/吨。
[0023]
一、提高混匀矿钢渣配比的实施过程:
[0024]
2020.06.02-2020.07.02,混匀矿总体配料结构基本稳定,钢渣配比2.5%,钒钛比58%(不含钢渣),总精粉比70%。
[0025]
2020.07.03-2020.08.03,对钢渣和混匀矿进行如下处理,将混匀矿钢渣配比提升到了5%:
[0026]
(1)对钢渣进行了破碎处理,破碎后钢渣的粒度≤10mm;
[0027]
(2)对钢渣进行了磁选处理,磁选后钢渣的全铁含量为18%≤tfe≤23%;
[0028]
(3)以铁水含p≤0.140%倒推混匀矿配料结构调整,高磷矿粉与低磷矿粉均衡搭配,在混匀矿钢渣配比提升的同时,始终维持铁水含p≤0.140%;
[0029]
(4)针对钢渣的使用,坚持“厚料层、慢机速”原则,以首保烧结矿质量为前提,摸索出不同钢渣配比情况下的产量与经济指标的最佳平衡。即钢渣配比提至5~8%,混匀矿烧结时控制烧结终点温度≥480℃,烧结机的机速控制为2.01~2.09m/mi n,料层厚度控制为750~780mm。
[0030]
二、六、七月份生产过程数据对比如下:
[0031]
表1.混匀矿成分对比(单位:%)
[0032][0033]
表2.烧结矿成分对比
[0034]
月份tfefeocaosio2mgoal2o3stio
2v2
o5pr6月47.48.4715.25.533.132.780.1274.860.4020.0562.757月48.048.5314.685.463.062.890.1184.870.430.0692.69对比0.640.06-0.52-0.07-0.070.11-0.0090.010.0280.013-0.06
[0035]
根据申请人长期生产摸索经验,在现行原辅料条件下,生石灰配比每升降0.25%,影响烧结矿碱度
±
0.05倍,烧结矿品位波动0.15-0.2%;通过成分对比发现:
[0036]
①
转化为同等烧结矿碱度对比,提高钢渣配比后虽混匀矿品位下降,但由于烧结生产生石灰配比下降(钢渣氧化钙含量高,其碱度达到3.90倍,远远高于烧结矿碱度控制),烧结矿品位并未有下降。
[0037]
②
钢渣含钒量高,烧结矿含钒上升。按炼铁钒收得率65%、炼钢钒回收率75%计,在同等炉料结构下,理论钒应上涨:0.028
×
53%
×
65%
×
75%=0.007%。按以往钒效益测算(钒渣价格1万元/吨上下),0.001%钒大约可产生1元效益。即,钢渣配比提高2.5%钒上涨0.007%,产生效益为7元。折算成1%钢渣产生2.8元钒效益(7月铁水含钒为0.337%,入炉钒钛比68.34%,同比6月分别上升0.026%和0.39%)。
[0038]
③
钢渣含磷高,烧结矿含磷上升。由于烧结、炼铁工序均不能脱除磷元素,按烧结矿(混匀矿)磷上升100%造成铁水磷上升计,提高钢渣配比2.5%,铁水磷上升0.014%。按炼钢前期测算数据,在铁水p:0.110-0.140%情况下,p每上升0.001%影响炼钢生产成本0.36元左右。即,每提高1%钢渣配比,影响炼钢生产成本上升:14*0.36/2.5=2.0元。
[0039]
三、烧结矿物理指标(产量指标)对比:
[0040]
表3.烧结矿物理指标对比
[0041][0042]
通过对比,钢渣配比由2.5%提高至5.0%后:
[0043]
①
烧结矿物理指标略有提高。与理论“钢渣可作为烧结矿的增强剂,利于烧结矿转鼓指数高”相符。
[0044]
②
烧结机利用系数上升,产量提高。与理论“钢渣可提高烧结矿结块率”相符。但由于钢渣含明铁较重,烧损高。一是用向下开口抛物线作比喻,在此仅能证明钢渣配比≤5.0%仍处于前半部分向上爬升阶段,即钢渣配加量与产量关系为正比;二是明铁对运输皮带、宽皮带等摩擦力上升。同时,烧结过程中熔化易糊篦条,造成烧结台车透气性下降,篦条使用寿命缩短等。因此造成辅料消耗上升等对烧结生产成本的影响需进一步跟踪。
[0045]
四、烧结矿原熔燃料消耗指标
[0046]
月份矿粉单耗生石灰单耗白云石单耗燃料单耗6月8601494855.227月8821343854.94对比22-15-10-0.28
[0047]
通过对比,钢渣配比由2.5%提高至5.0%后,一是钢渣中的氧化钙可代替生石灰、氧化镁可代替白云石配加,节约了熔剂消耗;二是钢渣中fe和feo的氧化放热,使烧结燃料消耗降低:
[0048]
①
按上述0.25%生石灰配比影响烧结矿碱度0.05倍计,套入“配料测算表”,可得0.25%生石灰配比影响生石灰单耗约3kg/t。即还原为同等烧结矿控制碱度对比,生石灰单耗同比下降12kg/t、白云石单耗同比下降10kg/t。按生石灰单价500元/吨、白云石单价190
元/吨计,熔剂单耗合计降本:500
×
12/1000+190
×
10/1000=7.9元。
[0049]
②
按生石灰烧失15%、白云石烧失42%计,熔剂单耗下降,理论上在不考虑混匀矿烧损情况下生产吨烧结矿矿耗应上升:12
×
15%+10
×
42%=6kg/t;按690元/吨混匀矿计,影响生产成本上升:6
×
690/1000=4.14元。
[0050]
③
燃料单耗下降0.28kg/t,按焦粉单价1150元/吨计,影响生产成本降低:0.28
×
1150/1000=0.32元。
[0051]
即每提高1%钢渣配比,烧结原熔燃料消耗可降低:(7.9-4.14+0.32)/2.5=1.63元。
[0052]
五、结论
[0053]
综上,在同等工况、同样原熔燃料价格体系下,混匀矿每提高1%钢渣配比可产生效益:3.9+2.8-2.0+1.63=6.33元;若不考虑钒效益,产生效益为3.9-2.0+1.63=3.53元。
[0054]
从2020年7月份开始,申请人生产的混匀矿钢渣配比由原先的2.5%左右大幅提升至4.61%,期间生产混匀矿粉约108万吨,按每提高1%钢渣节约成本3.53元计,共计节约配料成本108
×
(4.61-2.5)
×
3.53≈804万元
[0055]
因此本发明有效将混合矿中钢渣的配比由现有技术的2.5%提升至5%,既节约了混匀矿生产的配料成本,又解决了钢渣利用率低带来的钢渣堆积占用资源和钢渣外卖铁元素流失浪费的问题。
[0056]
以上实施例显示和描述了本发明的基本原理和主要特征和本发明的优点,对于本领域技术人员而言,显然本发明不限于上述示范性实施例的细节,而且在不背离本发明的精神或基本特征的情况下,能够以其他的具体形式实现本发明;因此,无论从哪一点来看,均应将实施例看作是示范性的,而且是非限制性的,本发明的范围由所附权利要求而不是上述说明限定,因此旨在将落在权利要求的等同要件的含义和范围内的所有变化囊括在本发明内,对于本领域的普通技术人员而言,可以理解在不脱离本发明的原理和精神的情况下可以对这些实施例进行多种变化、修改、替换和变型,本发明的范围由所附权利要求及其等同物限定。