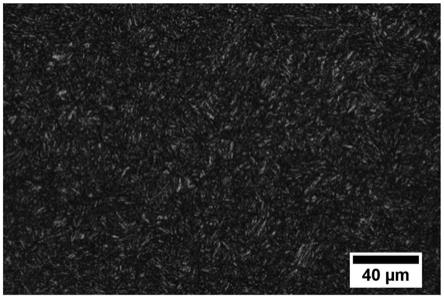
1.本发明涉及一种低合金铸钢材料,具体涉及一种高速列车制动盘低合金铸钢及其热处理方法。
背景技术:2.近年来,世界高速铁路发展迅猛,高速化程度越来越高,高铁时速从1964年日本东海道新干线的210km逐渐向350km乃至更高发展。我国铁路也正在向高速化方面发展,不断开始建设时速300-350公里的高速铁路网。时速的提升,与之带来的是对制动盘材料提出了更高的要求。
3.制动盘材料采用过普通铸钢、普通铸铁、低合金铸铁,此后,由于列车速度不断提高和轻量化的需要,又相继研发了特殊合金铸钢、低合金锻钢、铸铁-铸钢(锻钢)组合材料、碳/碳纤维复合材料和铝合金基复合材料,列车的时速的不断提升,从制动盘的使用上看,其功能就是通过与制动闸片进行摩擦,将高速行驶车辆的动能转换成热能,其中大部分热能被制动盘本身吸收,还有一部分从散热孔通过热辐射传导的方式传导到空气中,减少盘体本身的热能吸收,因此列车运行速度越快,刹车越急,其动能变化就越大,制动盘瞬时升温也就越高,巨大的热冲击导致制动盘材料的要求越来越高,未来我国的高速列车再次提速,制动盘的材料与形状都需要进一步研究,为了保证制动盘的使用寿命,降低热冲击对于盘体的寿命的影响,会加多散热孔,形成复杂性状,因此需采用铸造的一体成型的工艺来制备复杂形状的制动盘盘体结构,同时铸钢材料价格低廉、工艺简单,因此铸钢的制动盘材料在未来的高铁行业的发展中会起到主导位置。
4.专利cn103215523b公开了一种高速列车制动盘低合金铸钢组分以及其热处理方法。该合金铸钢主要成分为0.25-0.28c、0.48-0.52si、1-1.03mn、0.8-0.85cr、0.95-1ni、0.54-0.6mo、0.07-0.08v、0.05-0.06nb、0.005-0.01w、<0.01ti、<0.02al、0.01-0.015co、0.07-0.09cu、0.01-0.02zr、0.007p、0.007s,其余为fe和不可避免的杂质。该合金的处理方法为通过酸性的高频或中频感应电炉进行熔炼,通过正火加调质处理后,抗拉强度为1100-1200mpa,屈服强度1000-1100mpa,伸长率为7%,硬度为39-45hrc,具有良好的冲击韧性和耐磨性。但是随着高速列车的进一步提升,对材料提出了更高的性能要求,如根据标准性技术文件编号:tj/cl310-2014动车组制动盘暂行技术条件。对于铸钢制动盘的要求:室温抗拉强度≥1050mpa,规定塑性延伸率强度≥900mpa,断后延伸率≥8%,冲击吸收能量j(20℃)≥27j,硬度hbw≥290。由此可以看出,当前技术还无法满足相关要求,其中延伸率低于要求,同时室温冲击并未公开。
技术实现要素:5.本发明的目的为针对当前技术中存在的不足,提供一种高速列车制动盘用稀土系低合金铸钢及其热处理方法。该合金铸钢含有微量元素nb、v、ti以及稀土元素铈,在材料中起到细晶强化的作用。制备中,采取真空熔炼的方法,通过恰当的熔炼、真空参数来实现变
质处理的效果。本发明得到的材料与当前技术相比,力学性能得到了大幅度提升,可以满足国家2014年tj/cl310-2014动车组制动盘暂行技术条件中制动盘盘体铸钢材料要求。
6.本发明的技术方案为:
7.一种高速列车制动盘用稀土系低合金铸钢,其各组分的重量百分含量为:0.1%-0.3%c,0.4%-0.8%si,0.5%-1.0%mn,0.4%-0.8%cr,0.4%-0.7%mo,0.3%-0.7%ni,0.02%-0.08%v,0.02%-0.08%nb,0.02%-0.08%ti,0.01%-0.05%cu,0.02%-0.1%ce,s≤0.01%,p≤0.01%,余量为fe。
8.所述的高速列车制动盘用稀土系低合金铸钢的制备方法,该方法包括以下步骤:
9.步骤一:配料,按照配比称量原料,所述的原料包括:工业纯铁、纯硅、电解锰、电解镍、电解铜、金属铬、海绵钛、钼铁、钒铁、铌铁、纯铈;
10.步骤二:熔炼,利用真空熔炼炉熔炼,先合炉抽真空,真空度≤1pa,依次放入各合金原料,融化后在1550℃-1700℃下精炼5min-20min;
11.步骤三:浇铸,真空炉炉内浇注,1520℃-1620℃,连续稳定地将钢液浇铸至准备好的模具中进行成型,整个浇铸过程在2~3分钟内完成,在真空状态下随炉冷却至室温,得到铸钢;
12.所述的高速列车制动盘用稀土系低合金铸钢的制备方法,还包括:
13.步骤四:热处理,将步骤三得到的铸钢在800℃-900℃下正火保温60-120min,然后空冷;然后再升温到820℃-940℃下保温30min-120min,然后水冷淬火;最后再调整温度至560℃-620℃回火,保温90min-150min,再空冷。
14.所述的步骤四中,正火温度优选为ac3温度点以上30℃-60℃,淬火温度优选为ac3温度以上50℃-100℃。所述的ac3温度点为加热时转变为奥氏体的终了温度。
15.本发明的实质性特点为:
16.(1)传统的合金成分优化,大多以经验式进行元素种类以及含量的搭配。而复合微合金化,需要对元素间的相互作用进行搭配,同时需要对平衡相以及平衡析出相进行预测。本发明通过大量分析、实验,结合thermo-calc软件的相图计算,发现了适合的合金元素以及含量搭配,能够更好地发挥合金元素的相互作用,能有效的结合后续的热处理工艺,得到正火+调制处理后的最佳相组织,有利于对合金钢进行强化。另外,成分上通过复合-微元合金化的方式进行强化,同时添加适量稀土元素(铈)也可以达到变质处理的效果;
17.(2)制备过程方面:制备过程中采用真空熔炼炉熔炼,重要的步骤为:
18.1)真空熔炼过程中真空度小于1pa,实际真空度控制在0.5-0.9pa,可以有效的减少气体在金属熔体中的溶解度,从而达到除气的作用,同时有利于气泡上浮,能够有效的吸附非金属夹杂物带出金属熔体,达到除杂作用。在0.5-0.9pa下,具有最佳的防氧化作用,尤其是针对本发明合金成分中添加的mo、nb、ti元素;
19.2)在1620℃下精炼10min(1550℃-1700℃下精炼5min-20min)为最佳的精炼方案,可以有效地达到除气、除杂的作用,充分将合金原料溶解。
20.(3)热处理工艺:采用正火+调质处理的方式,通过正交实验得到最佳的热处理工艺,通过相变强化的同时,利用细小合金碳化物颗粒均匀分布在基体上,进行第二相强化,保证合金钢的力学性能。
21.本发明的有益效果为:
22.(1)本发明上诉的技术方案为全新的方案:从成分设计、熔炼过程、热处理工艺均有所改变。成分设计:通过软件进行相图模拟,充分发挥各个元素间的作用,通过相组成对后续的热处理工艺做出指导,同时突出第二相强化作用机制。利用微量元素nb、v、ti以及稀土元素ce进行细化晶粒,达到细晶强化的作用,同时利用强碳化物的元素,在热处理过程中,得到细小的合金碳化物,并均匀分布在基体上,突出第二相强化的作用;熔炼过程:采用真空熔炼,控制真空度、精炼、浇铸过程参数,保证铸坯的质量;热处理:通过正交实验,最大化的发挥合金间的相互作用,利用相变强化、细晶强化与第二相强化,提高合金钢的力学性能。
23.(2)在本发明的技术背景中,提到的公开号cn103215523b的中国专利中公开的一种高速列车合金铸钢制动盘材料,室温状态下的抗拉强度为1100-1200mpa,屈服强度为1000-1100mpa,延伸率为7%。而本发明中实施例1中,室温抗拉强度为1260mpa,屈服强度为1220mpa,延伸率为13.8%,冲击功为39j,硬度为330hbw。通过比较发现,力学性能得到了大幅度提升,同时如表1所示,满足国家2014年tj/cl310-2014动车组制动盘暂行技术条件中制动盘盘体铸钢材料要求。
附图说明
24.图1为实施例1得到的高强韧性低合金铸钢正火+调质处理后的金相组织放大500倍的图片。
25.图2为实施例2得到的正交实验各方案回火组织碳化物形貌照片;
具体实施方式
26.为使本发明实施例的目的、技术方案和优点更加清楚明了,下面将对本发明实施例中的技术方案进行清楚、完成地描述,同时所描述的实施例是本发明一部分实施例,而不是全部的实施例。基于本发明中的实施例,本领域普通技术人员在没有创造性劳动前提下所获得所有其他实施例,都属于本发明保护的范围。
27.实施例1
28.本实施例提供一种高强韧性低合金铸钢及其制造方法,其组分及其各组分质量百分比为:0.22%c,0.47%si,0.76%mn,0.73%cr,0.68%mo,0.55%ni,0.05%v,0.06%nb,0.04%ti,,0.04%cu,0.05%ce,余量为fe,0.007%p、0.006s(s、p源自工业纯铁等中含有微量的s、p元素)。
29.采用真空熔炼炉进行熔炼,熔炼工艺步骤如下:
30.(1)根据成分配比准备合金原料以及模具,本次实验选用的原料如表1所示,其中纯度代表的含义为:目标元素的含量。
31.表1.合金种类及纯度
[0032][0033]
浇铸模具为70kg,根据设计的成分,进行配料,实施例1中,每种原料的质量如表2所示:
[0034]
表2.合金种类以及质量
[0035][0036]
(2)真空熔炼炉内熔炼,真空度为1pa以下,在炉内加入纯铁、纯硅、电解锰、电解镍、电解铜、金属铬、海绵钛、钼铁、钒铁、铌铁,全程在真空下熔炼。
[0037]
(3)在1620℃下精炼,待合金全部融化后,充氩加碳,调节功率静置,然后降温到1580℃。
[0038]
(4)在1580℃左右,进行炉内浇铸,控制浇注速度,时刻保证高真空度(在0.5pa-0.9pa之间状态,完成浇注后,铸坯炉内凝固。真空状态可以有效地去除合金中的气体和非金属夹杂物,提高合金的纯净度。
[0039]
(5)热处理:将上步得到的铸钢正火加调质处理:先进行正火处理:正火温度为ac3温度点(ac3温度点为加热时转变为奥氏体的终了温度,是通过热膨胀实验得到,实例1具体的温度为823℃)。以上30℃-60℃,正火保温时间为60min-120min,然后空冷;再进行淬火处理:淬火温度在ac3温度以上50℃-100℃,淬火保温时间为30min-120min,然后水冷;最后进行回火处理:回火温度为560℃-620℃,回火保温时间为90min-150min,然后空冷。
[0040]
实施例2
[0041]
其他步骤同实施例1,不同之处为其组分及其各组分质量百分比为:0.24%c,0.33%si,0.63%mn,0.68%cr,0.68%mo,0.59%ni,0.07%v,0.05%nb,0.001%ti,0.03%cu,0.07%ce,余量为fe。0.005%s、0.005%p。
[0042]
实施例3
[0043]
其他步骤同实施例1,不同之处为其组分及其各组分质量百分比为:0.27%c,0.47%si,0.63%mn,0.71%cr,0.57%mo,0.71%ni,0.06%v,0.04%nb,0.01%ti,0.04%cu,0.03%ce,余量为fe。0.004%s、0.006%p。
[0044]
力学性能测试:
[0045]
室温拉伸实验参照国家标准gb/t228.1-2010,在纵横三思电子万能实验机上进行,拉伸速率为0.5mm/min,入口力为10n,每组试验进行三次,取平均值。
[0046]
表3力学性能对比
[0047][0048][0049]
性能提高的机理:由于微量元素nb、v、ti以及稀土元素铈的添加,起到细晶强化的作用,同时强碳化物元素的添加(mo、mn、cr、ni、nb、v),导致在热处理后,合金碳化物颗粒细小,且均匀分布基体上起到了第二相强化。
[0050]
实施例2中不同的实验方案回火组织碳化物形貌中发现,合金碳化物主要分布于
原奥氏体晶界处以及少量处于铁素体板条间,随着回火过程的进行,碳原子不断地与合金元素结合以合金碳化物的形式析出,析出的碳化物作为强化相可以起到强化作用。
[0051]
图片中可以看出:实施例2中加入的合金元素形成与奥氏体中c原子相结合形成高熔点、细小的合金碳化物。通过组织图像可以看出,合金碳化物主要分布于原始奥氏体晶界处以及少量处于铁素体板条间,随着回火过程的进行,碳原子不断地于合金元素结合以合金碳化物的形式析出,分布于结晶处以及铁素体板条间,在一个晶粒内部,
ɑ
相中的碳原子不断地由原来过饱和的马氏体板条中析出,性成果合金碳化物分布于铁素体板条间,析出的碳化物作为强化相可以起到强化作用。
[0052]
高温回火过程中随着保温温度升高以及回火时间延长,马氏体基本分解完毕,分解过程中产生的各类碳化物也完全转变为细粒状的碳化物。从图中(c)、(d)、(e)、(f)、(g)中可以明显的看出,在铁素体内分布着大量的碳化物,碳化物呈百色细小颗粒,分布较为均匀。实施例2中在奥氏体化之后采用水冷的方式,快速冷却,发生切变相变碳原子为发生扩散主要固溶于马氏体中,随着回火过程的进行,原来奥氏体晶界处对晶界起到钉扎以及阻碍碳原子扩散的碳化物不断的析出,随着碳原子从马氏体中析出,与强碳化物元素结合形成合金碳化物,随着保温时间的不断延续,碳化物不断的聚集长大,由原来的线条状逐渐变变成消息的颗粒状,很好的起到了钉扎的作用,实现了强化。
[0053]
通过以上实施例可以看出,由于微量元素的nb、v、ti复合微元化的添加到低合金铸钢材料中,相对对比例的单一添加,细化晶粒的效果更加明显,同时产生的合金碳化物的尺寸与形貌对提高铸钢的性能有很强的作用,本发明的实施例1、实施例2、实施例3得到的力学性能均远超tj/cl310-2014动车组制动盘暂行技术条件中制动盘盘体铸钢材料要求。
[0054]
对比例1
[0055]
其他步骤同实施例1,不同之处为加了0.04%nb,没有添加v、ti。
[0056]
得到的铸钢的性能室温抗拉强度为1129mpa,屈服强度为1050mpa,延伸率为9.2%,室温冲击功为29j。
[0057]
对比例2
[0058]
其他步骤同实施例1,不同之处为加了0.01%nb,0.01%v、0.01%ti。
[0059]
得到的铸钢的性能室温抗拉强度为1022mpa,屈服强度为950mpa,延伸率为10.1%,室温冲击功为22j;
[0060]
对比例3
[0061]
其他步骤同实施例1,不同之处为加了0.10%nb,0.11%v、0.09%ti。
[0062]
得到的铸钢的性能室温抗拉强度为998mpa,屈服强度为750mpa,延伸率为8.9%,室温冲击功为23j;
[0063]
本发明未尽事宜为公知技术。