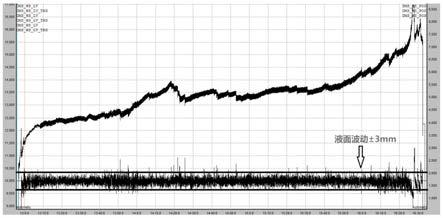
1.本发明属于冶金生产技术领域,具体涉及一种超低碳钢的炼钢方法。
背景技术:2.汽车用钢的质量要求日益严格,高附加值高表面汽车面板的质量要求更加严格,这就需要炼钢提供稳态浇注的高表面质量铸坯。
3.由于高表面汽车o5面板为无间隙原子钢,对碳含量要求极低,一般要求碳含量≤0.002%,炼钢冶炼为铝脱氧,结合其本身工艺特点,根据碳氧积平衡原理,极低的碳含量对应氧含量相对较高,钢水中氧含量极易与钢水中铝反应生成al2o3夹杂,在连铸浇注过程中al2o3不规律的集聚在塞棒头部或浸入式水口内壁造成塞棒掉块或水口偏流,紊乱结晶器流场引起结晶器液面波动,影响铸坯稳态浇注,当出现塞棒头堵塞涨死,液面波动连续超过
±
20mm时必须被迫停浇,这将严重影响连铸顺行和铸坯质量。目前国内外研究主要集中在结晶器流场的优化和控制,或仅对设备进行改进。
4.申请号为201310356746.1的中国专利公开了一种防止超低碳钢铝脱氧钢水浇注过程水口堵塞的控制方法,该专利是采用铁水脱硫处理
ꢀ‑ꢀ
转炉冶炼
ꢀ‑ꢀ
转炉出钢
ꢀ‑
rh 真空处理
ꢀ‑ꢀ
双流板坯连铸浇铸的工艺路径冶炼超低碳钢,提出了一种防止超低碳钢水口堵塞的方法,其特点是:合理控制转炉吹炼终点钢水氧含量、终点碳含量和温度,为 rh 真空脱碳提供有利条件;连铸保护浇铸采用长水口、浸入式水口吹氩密封保护,防止钢水二次氧化;使用碱性覆盖剂,防止钢水二次氧化,更好的吸附钢水中的夹杂物;提高超低碳铝脱氧钢水的可浇性。但是该专利对转炉终点氧和顶渣改质的对应关系未做描述,对连铸浸入式水口插入深度和采用抖塞棒减少水口堵塞未做涉及。
5.申请号为201811324962.7的中国专利公开了一种改善塞棒控流al脱氧钢水口堵塞的浇注方法,该专利通过塞棒抖动减少水口结瘤堵塞几率,但是对浇注过程中换水口后塞棒抖动幅度和抖动频率未做研究。
6.论文《if钢板坯连铸结晶器液面波动原因及控制》通过对结晶器内流场、塞棒吹氩、扇形段设备精度和结晶器液面检测系统进行研究并制定相应的措施改善结晶器液面波动,但是对钢水中氧含量和连铸保护浇注未做研究。
7.论文《高磷if钢结晶器液面波动原因分析与控制》针对钢水过热度、塞棒吹氩量和设备精度等进行了分析和研究,但是对浸入式水口插入深度和中间包保护浇注等方面未做过多涉及。
技术实现要素:8.本发明提供一种超低碳钢的炼钢方法,解决的技术问题是改善超低碳钢连铸过程结晶器液面波动,减少水口结瘤堵塞现象。
9.本发明技术方案为:一种超低碳钢的炼钢方法,生产过程包括转炉冶炼工序、rh精炼工序、连铸工序,所述连铸工序,一个浇次的前期、中期、后期,中包浸入式水口插入液面
深度分别为145~155mm、175~185mm、160~170mm。
10.与以上技术方案属于同一个发明构思的另一个技术方案为:一种超低碳钢的炼钢方法,生产过程包括转炉冶炼工序、rh精炼工序、连铸工序,所述连铸工序,一个浇次的第1~3炉、第4~6炉、第7~8炉,中包浸入式水口插入液面深度分别为145~155mm、175~185mm、160~170mm。
11.进一步的,所述连铸工序,塞棒采用抖动模式,抖动幅度0.5~1.5mm,抖动频率0.5~1.5hz。
12.进一步的,所述连铸工序,采用中间包钟式长水口液面下浸入式开浇。
13.进一步的,所述转炉冶炼工序,转炉出钢后,采用铝渣和石灰对顶渣进行改质,所述铝渣和石灰加入量如下:当o
终点
≤400ppm时,铝渣和石灰加入量分别为440~460kg/吨钢、610~630kg/吨钢;当400ppm<o
终点
≤600ppm时,铝渣和石灰加入量分别为460~650kg/吨钢、680~820kg/吨钢;当600ppm<o
终点
≤850ppm时,铝渣和石灰加入量分别为650~900kg/吨钢、820~1050kg/吨钢;所述o
终点
为转炉冶炼终点钢液中氧含量。
14.进一步的,所述转炉冶炼工序,转炉冶炼终点钢液中碳含量为0.035wt%~0.065wt%。
15.以下对本发明进行详细说明:[连铸工序,一个浇次的前期、中期、后期,中包浸入式水口插入液面深度分别为145~155mm、175~185mm、160~170mm。][连铸工序,一个浇次的第1~3炉、第4~6炉、第7~8炉,中包浸入式水口插入液面深度分别为145~155mm、175~185mm、160~170mm。]为稳态控制连铸结晶器内流场,将浸入式水口插入深度优化为动态跳跃式插入方式。具体方法:连续浇铸前期由于结晶器液面相对稳定,此时将浸入式水口插入深度设定为145~155mm;连铸浇注中期由于此时钢水会受到一些污染,连铸结晶器液面较前期稳定性略差,将浸入式水口插入深度调整为175~185mm;连续浇注后期将浸入式水口插入深度调整为160~170mm。由于浇注汽车o5板用钢时,一般安排整浇次6炉或8炉钢,所以浇次的第1~3炉、第4~6炉、第7~8炉,中包浸入式水口插入液面深度分别为145~155mm、175~185mm、160~170mm。
[0016]
[连铸工序,塞棒采用抖动模式,抖动幅度0.5~1.5mm,抖动频率0.5~1.5hz]为减少水口粘接、堵塞,对塞棒开启抖动模式,目的在连铸浇注过程中通过塞棒抖动减少水口结瘤堵塞现象。塞棒抖动功能方法:连铸开浇时钢水处于紊流状态,暂不开启塞棒抖动模式;当拉速涨到目标拉速并稳定后,开启塞棒上下抖动模式,抖动幅度0.5~1.0mm,抖动频率0.5~1.0hz;当浇注到第4炉时,由于此时钢水已连续开浇120min左右,钢水会受到一些污染,容易堵塞水口,所以一个浇次的中后期,将塞棒抖动幅度增大到1.0~1.5mm,抖动频率增大到1.0~1.5hz。另外,在连铸浇注过程中如需要换水口,在换水口后塞棒抖动模式重复上述阶梯式抖动模式。
[0017]
[连铸工序,采用中间包钟式长水口液面下浸入式开浇]对长水口保护浇注进行改进优化,将原来的中间包直筒型长水口液面上开浇优化为中间包钟式长水口液面下浸入式开浇,目的降低开浇时钢水二次氧化几率。另外,长水口由直筒型优化为钟式的目的是增加长水口内部压力,防止中间包长水口浸入式开浇因中间
包内钢水压力大造成浸入式长水口内部翻钢事故。
[0018]
[转炉冶炼工序,转炉出钢后,采用铝渣和石灰对顶渣进行改质,所述铝渣和石灰加入量如下:当o
终点
≤400ppm时,铝渣和石灰加入量分别为440~460kg/吨钢、610~630kg/吨钢;当400ppm<o
终点
≤600ppm时,铝渣和石灰加入量分别为460~650kg/吨钢、680~820kg/吨钢;当600ppm<o
终点
≤850ppm时,铝渣和石灰加入量分别为650~900kg/吨钢、820~1050kg/吨钢;所述o
终点
为转炉冶炼终点钢液中氧含量]为防止转炉顶渣中氧高向钢水中传氧,产生al2o3夹杂,污染钢水,对转炉顶渣进行强改质工艺,目的降低渣中氧化性。采用动态调整顶渣强改质工艺,打破原有改质剂定量加入的方式,在转炉出钢后,根据转炉终点氧和转炉出钢下渣量,按照热力学平衡计算出合理的石灰和铝渣的加入量,进行动态式顶渣改质,顶渣改质目标,要求rh进站tfe≤4%,出站tfe≤6%。所述石灰,优选为小粒石灰。所述铝渣,粒度为5-40mm,其组分及其质量百分含量见表1:表1[转炉冶炼工序,转炉冶炼终点钢液中碳含量为0.035wt%~0.065wt%。]基于转炉碳氧积平衡原理,若转炉终点控制碳含量高对应钢水中氧含量就会较低,尤其是针对汽车o5板用钢,由于其本身工艺特点,要求钢中碳含量极低,一般要求碳含量≤0.002%以内,对应氧含量会较高,再加上汽车o5板为铝脱氧钢,铝元素极为活跃,极易与钢水中氧含量发生氧化反应,影响钢水洁净度,给连铸水口堵塞形成隐患。为从根源降低钢水中夹杂物产生几率,采用转炉高拉碳工艺,将钢水中碳含量控制在0.035%-0.065%,降低转炉终点氧含量,为高品质的钢水提供保障条件。
[0019]
采用上述技术方案所产生的有益效果在于:通过采取转炉高拉碳工艺从根源降低钢水中氧含量,控制钢中夹杂物的产生几率;利用动态顶渣强改质工艺,结合转炉终点氧含量动态调配顶渣改质剂的加入量,目标实现rh进站tfe≤4%,出站tfe≤6%,降低渣中氧化性,防止渣中氧传向钢水中;改进长水口由直筒型优化为钟式,方式由敞开式开浇优化为浸入式开浇,减少钢水二次氧化;开启阶梯式塞棒抖动功能,减少水口粘接、堵塞现象;采用动态跳跃式浸入式水口插入方式,稳态控制结晶器流场。
[0020]
采用以上措施,均可有效减少水口堵塞几率。
[0021]
同时采用以上措施,结晶器液面波动现象显著改善,汽车05面板用钢连铸过程液面波动≤
±
3mm比例由93.2%提高至98.6%。冷轧产品表面质量得到质的飞跃。
附图说明
[0022]
图1实施例1结晶器液面波动曲线图;图2实施例2结晶器液面波动曲线图;图3实施例3结晶器液面波动曲线图;图4实施例4结晶器液面波动曲线图。
具体实施方式
[0023]
为了使本发明的目的、技术方案及优点更加清楚明白,以下以汽车o5面板用钢为例,结合实施例,对本发明进行进一步详细说明。应当理解,此处所描述的具体实施例仅仅用以解释本发明,并不用于限定本发明。
[0024]
汽车o5面板用钢,化学成分及其质量百分含量见表2。
[0025]
表2实施例1冶炼1浇次6炉汽车o5板用钢,转炉按照高拉碳工艺生产,将转炉终点碳含量、终点氧含量见表3。结合转炉终点氧含量对转炉顶渣改质进行动态调整,具体改质剂的加入量如表3所示。
[0026]
表3通过以上动态顶渣改质,6炉高附加值汽车o5板的rh进、出站tfe控制良好,rh进站tfe含量平均3.8%,rh出站tfe含量平均5.2%,。
[0027]
采用钟式长水口液面下浸入式开浇,降低开浇时钢水二次氧化几率。
[0028]
包盖全程氩封,开浇准备前对包盖进行吹氧,保持包盖氩封6.8公斤,开浇稳定后中间包注入钢水53吨后,减少包盖氩封量到2.3公斤全程吹氩,保证整个浇次过程中中间包内都处在微正压状态,防止中间包内负压状态空气中的氧进入中间包内造成钢水二次氧化,污染钢水。
[0029]
浇注铸坯断面1500mm,铸坯厚度为230mm。连铸开浇时暂不开启塞棒抖动模式,当拉速涨到1.3m/min 并稳定2min后,开启塞棒上下抖动模式,抖动幅度0.5mm,抖动频率0.5hz;当浇注到第4炉时,塞棒抖动幅度增大到1.5mm,抖动频率增大到1.5hz至整个浇次6炉浇注结束。
[0030]
连铸浇注第1~3炉,浸入式水口插入深度为150mm,浇注第4炉开始调整浸入式水口插入深度为180mm至整个浇次浇注结束。
[0031]
实施例2冶炼1浇次8炉汽车o5板用钢,转炉按照高拉碳工艺生产,将转炉终点碳含量、终点氧含量见表4。结合转炉终点氧含量对转炉顶渣改质进行动态调整,具体改质剂的加入量如表4所示。
[0032]
表4
通过以上动态顶渣改质,8炉高附加值汽车o5板的rh进、出站tfe控制稳定,rh进站tfe含量平均3.25%,rh出站tfe含量平均4.7%,。
[0033]
采用钟式长水口液面下浸入式开浇,降低开浇时钢水二次氧化几率。
[0034]
包盖全程氩封,开浇准备前对包盖进行吹氧,保持包盖氩封7.2公斤,开浇稳定后中间包注入钢水51吨后,减少包盖氩封量到2.6公斤全程吹氩,保证整个浇次过程中中间包内都处在微正压状态,防止中间包内负压状态空气中的氧进入中间包内造成钢水二次氧化,污染钢水。
[0035]
浇注铸坯断面1300mm,铸坯厚度为230mm。连铸开浇时暂不开启塞棒抖动模式,当拉速涨到1.5m/min 并稳定2min后,开启塞棒上下抖动模式,抖动幅度0.6mm,抖动频率0.6hz;当浇注到第4炉时,塞棒抖动幅度增大到1.3mm,抖动频率增大到1.3hz。浇注第6炉开浇换水口,换水口后抖动幅度0.8mm,抖动频率0.8hz至整个浇次8炉浇注结束。
[0036]
连铸浇注第1~3炉,浸入式水口插入深度为145mm,浇注第4~6炉开始调整浸入式水口插入深度为175mm,连续浇注第7~8炉时将浸入式水口插入深度调整为160mm至整个浇次浇注结束。
[0037]
实施例3冶炼1浇次8炉汽车o5板用钢,转炉按照高拉碳工艺生产,将转炉终点碳含量、终点氧含量见表5。结合转炉终点氧含量对转炉顶渣改质进行动态调整,具体改质剂的加入量如表5所示。
[0038]
表5通过以上动态顶渣改质,8炉高附加值汽车o5板的rh进、出站tfe控制稳定,rh进站
tfe含量平均2.9%,rh出站tfe含量平均4.8%,。
[0039]
采用钟式长水口液面下浸入式开浇,降低开浇时钢水二次氧化几率。
[0040]
包盖全程氩封,开浇准备前对包盖进行吹氧,保持包盖氩封6.5公斤,开浇稳定后中间包注入钢水55吨后,减少包盖氩封量到1.8公斤全程吹氩,保证整个浇次过程中中间包内都处在微正压状态,防止中间包内负压状态空气中的氧进入中间包内造成钢水二次氧化,污染钢水。
[0041]
浇注铸坯断面1700mm,铸坯厚度为230mm。连铸开浇时暂不开启塞棒抖动模式,当拉速涨到1.2m/min 并稳定2min后,开启塞棒上下抖动模式,抖动幅度0.5mm,抖动频率0.5hz;当浇注到第4炉时,塞棒抖动幅度增大到1.5mm,抖动频率增大到1.5hz;浇注第5炉中期换水口,换水口后抖动幅度1.0mm,抖动频率1.0hz至整个浇次8炉浇注结束。
[0042]
连铸浇注第1~3炉,浸入式水口插入深度为155mm,浇注第4~6炉开始调整浸入式水口插入深度为185mm,连续浇注第7~8炉时将浸入式水口插入深度调整为170mm至整个浇次浇注结束。
[0043]
实施例4冶炼1浇次7炉汽车o5板用钢,转炉按照高拉碳工艺生产,将转炉终点碳含量、终点氧含量见表6。结合转炉终点氧含量对转炉顶渣改质进行动态调整,具体改质剂的加入量如表6所示。
[0044]
表6通过以上动态顶渣改质,7炉高附加值汽车o5板的rh进、出站tfe控制良好,rh进站tfe含量平均3.0%,rh出站tfe含量平均4.6%。
[0045]
采用钟式长水口液面下浸入式开浇,降低开浇时钢水二次氧化几率。
[0046]
包盖全程氩封,开浇准备前对包盖进行吹氧,保持包盖氩封7.3公斤,开浇稳定后中间包注入钢水52吨后,减少包盖氩封量到2.5公斤全程吹氩,保证整个浇次过程中中间包内都处在微正压状态,防止中间包内负压状态空气中的氧进入中间包内造成钢水二次氧化,污染钢水。
[0047]
浇注铸坯断面1450mm,铸坯厚度为230mm。连铸开浇时暂不开启塞棒抖动模式,当拉速涨到1.35m/min 并稳定2min后,开启塞棒上下抖动模式,抖动幅度0.6mm,抖动频率0.6hz;当浇注到第4炉时,塞棒抖动幅度增大到1.4mm,抖动频率增大到1.4hz至整个浇次7炉浇注结束。
[0048]
连铸浇注第1~3炉,浸入式水口插入深度为153mm,浇注第4~6炉开始调整浸入式水
口插入深度为183mm,连续浇注第7炉将浸入式水口插入深度调整为168mm至整个浇次浇注结束。
[0049]
实施例1~4结晶器液面波动曲线图见附图1~4,从附图1~4看,结晶器液面稳定,无水口堵塞情况。
[0050]
以上实施例仅用以说明而非限制本发明的技术方案,尽管参照上述实施例对本发明进行了详细说明,本领域的普通技术人员应当理解:依然可以对本发明进行修改或者等同替换,而不脱离本发明的精神和范围的任何修改或局部替换,其均应涵盖在本发明的权利要求范围当中。