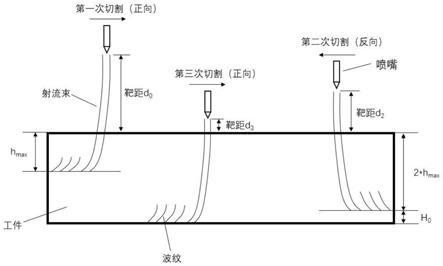
1.本发明涉及磨料水射流技术领域,涉及一种提高射流切割质量的方法,具体涉及一种提高三轴低压磨料射流切割质量的方法。
背景技术:2.磨料射流切割技术是一种以水为介质,利用高压泵获得巨大能量,然后通过供料和混合装置把磨料加入到高压水束中,形成混合射流,依靠磨料和高压水束的高速冲击实现材料去除的一种特种加工方式。与传统的接触式加工方式相比,磨料水射流切割加工具有以下优势:(1)无热应力的影响。磨料水射流切割是一种冷态切割加工,由于水介质的冷却作用,工件不会产生热应力以及热影响区,因此特别适用于铝、钛、铜等热敏性材料的切割;(2)通用性强。通过设置合适的工艺参数,如射流压力、横移速度、靶距等,磨料水射流几乎可以切割所有材质的工件;(3)环保效果好。磨料水射流切割不会产生有害气体、灰尘等污染,此外,切割完成后磨料水经水箱收集、过滤、精华处理后可循环利用,不污染环境。
3.高压泵和数控切割器是磨料射流加工系统极为重要的组成部分。高压泵所能提供的压力越大,磨料水射流的动能就越大,加工效果也就越好。但高压泵的压力越高,其制造和维护成本也越高,而且使用寿命也会大大降低。另一方面,数控切割器决定了磨料射流在加工过程中的运动方式,切割器的轴数越多,磨料射流可实现的运动程度越复杂,就可通过控制磨料射流的冲击角度等参数来提高加工质量。但切割器的轴数越多,其价格也越高,从而限制了多轴数控切割器的普及。当前,三轴数控切割器是轴数最少,也是最便宜的一种切割器。因此,利用三轴磨料射流在较低的压力下实现对工件的高质量切割,可以消除对超高压泵和多轴数控切割器的需求,从而极大降低磨料射流的加工成本,对促进磨料射流加工的应用具有重要作用。
技术实现要素:4.为了消除对超高压泵和多轴数控切割器的需求,降低磨料射流的加工成本和促进磨料射流的应用,本发明提供了一种提高三轴低压磨料射流切割质量的方法,通过在较低的压力下对目标工件进行多次正反向交替并且变靶距切割,以达到甚至优于高压磨料射流的切割质量,并实现节约能源的效果。
5.为了解决上述计算问题,本发明采用的技术方案如下:
6.一种提高三轴低压磨料射流切割质量的方法,其特征在于:包括以下步骤:
7.s1:取与待切割工件材质相同的工件样品在三轴低压磨料射流加工平台上利用三轴切割器进行切割实验,获得工件切割的门限压力p0、最大射流压力p
max
下的最大切割深度h
max
和包含靶距d0的最优切割参数;并建立切割深度h在最优切割参数下随射流压力p变化的函数关系:h=f(p,s),s表示最优切割参数组;
8.s2:将待切割的工件固定在三轴低压磨料射流加工平台上,在最大射流压力p
max
下以最优切割参数对工件进行正向第一次切割;
9.s3:当射流离开工件时立即控制三轴切割器调整最优切割参数中的靶距,并在射流压力、剩余最优切割参数不变的情况下沿原切割路径对工件进行来回交替切割,直至工件切割后剩余厚度小于h
max
;第n次切割时的靶距dn=d
n-1-h
max
,n≥2;当n=2时,靶距d2=d
0-h
max
;
10.s4:最后一次切割,计算出第n次切割后工件剩余未切割的厚度h0,再根据步骤s1中的函数关系计算出切割深度达到厚度h0时所需射流压力pn,以pn作为射流压力,以靶距以外的最优切割参数作为切割参数(即以磨料流量m0和横移速度v0作为切割参数),靶距d
n+1
=d
n-h
max
进行第n+1次切割,完成工件切割。
11.本发明调整靶距(即喷嘴出口至工件表面间的距离)过程中,每次调整量为下降一个最大切割深度h
max
。因此,实际上每次切割时,喷嘴距离切割缝中待切割表面的距离还是等于最优靶距d0,因此,每次切割时,真正靶距不变,所以本发明步骤s4中任然可以利用步骤s1中的函数关系式h计算所需射流压力。
12.进一步地,所述最优切割参数还包括磨料流量m0和横移速度v0。
13.进一步地,步骤s1中,所述最优切割参数通过正交试验方法确定,具体设计三因素四水平正交表,确定最优的磨料流量m0、靶距d0和横移速度v0组合。
14.进一步地,步骤s1中,首先通过正交试验方法确定最优切割参数组合(d0,m0,d0,v0),然后通过单因素实验方法,确定在上述最优参数组合下工件的门限压力p0。
15.进一步地,步骤s3中n的计算公式为:n=[h/h
max
],即工件厚度h除以最大切割深度h
max
后取整数。
[0016]
进一步地,步骤s4中,如果计算得到的需射流压力pn《p0时,以压力p0进行最后一次切割。
[0017]
本发明的有益效果在于:
[0018]
本发明通过在较低的压力下对目标工件进行多次正反向交替变靶距切割,以达到甚至优于高压磨料射流的切割效果,不仅在一定程度上消除了对超高压泵和多轴数控切割器的需求,同时还促进了磨料射流的应用,降低了磨料射流的加工成本,并利用最后一次更低压力的切割实现节约能源减少能耗。本发明由于射流压力越低,消耗的能源越少,因此可在保证切割质量的同时实现能源节约。
附图说明
[0019]
图1是本发明三轴低压磨料射流高质量切割工件的方法示意图。
[0020]
图2是本发明较佳实施例切割深度与射流压力的拟合曲线。
[0021]
图3是本发明较佳实施例低压与对比例高压切割完成后的表面粗糙度曲线对比图。
具体实施方式
[0022]
为详细说明本发明的技术内容、所实现的目的及效果,以下结合实施方式并配合附图详予说明,这些实施例仅起说明性作用,并不局限于本发明的具体实现方式和结构。
[0023]
如图1所示,本发明提供一种提高三轴低压磨料射流切割质量的方法,具体步骤如下:
[0024]
设该三轴低压磨料射流加工平台的工作压力为p,p
max
为最大压力,p0为待切割工件的门限压力,且p
max
》p0,三轴低压磨料射流加工平台通过三轴切割器能控制喷嘴在三个方向动作,第一个方向为调节喷嘴与工件之间的距离(图1中上下方向),第二个方向为喷嘴沿着切割路径行走进行切割(图1中左右方向),第三个方向为喷嘴在不同切割路径切换(图1中垂直于纸面方向),以进行不同路径切割。
[0025]
s1:取工件样品在三轴低压磨料射流加工平台上进行切割实验,获得切割的门限压力p0,最优切割参数以及最大压力p
max
下的最大切割深度h
max
;并建立切割深度h在最优工作参数下随p变化的函数关系;本实施例中,最优切割参数组为磨料流量m0、靶距d0和横移速度v0,因此,得到的函数关系式为:h=f(p,m0,d0,v0)。
[0026]
本发明实施例中,通过正交试验方法,设计三因素四水平正交表,确定最优的磨料流量m0、靶距d0(即喷嘴出口至工件表面间的距离)和横移速度v0组合,再通过单因素实验方法,确定在上述最优参数组合下工件的门限压力p0,完成初始参数标定。
[0027]
s2:将工件固定在三轴低压磨料射流加工平台上,在最大压力p
max
下以最优切割参数组(磨料流量m0、靶距d0和横移速度v0)对工件进行正向第一次切割(图1中从左往右)。
[0028]
s3:当射流离开工件时立即控制三轴切割器调整最优切割参数中的靶距,并在射流压力、剩余最优切割参数不变的情况下沿原切割路径对工件进行来回交替切割(图1中,从左往右为正向,从右至左为反向,正反交替切割),直至工件切割后剩余厚度小于h
max
;第n次切割时的靶距dn=d
n-1-h
max
;当n=2时,靶距d2=d
0-h
max
;n的计算公式为:n=[h/h
max
],即工件厚度h除以最大切割深度h
max
后取整数。
[0029]
s4:最后一次切割,计算出第n次切割后工件剩余未切割的厚度h0,再根据步骤s1中的函数关系计算出切割深度达到厚度h0时所需射流压力pn,以pn作为射流压力,以磨料流量m0和横移速度v0作为最优切割参数,靶距d
n+1
=d
n-h
max
进行第n+1次切割,完成工件切割;如果计算得到的需射流压力pn《p0时,以压力p0进行最后一次切割。
[0030]
下面以10mm厚的牌号为5083的铝合金板为例对本发明作进一步说明:
[0031]
为方便对比,设置对比例的切割试验,对比例实验所用磨料射流加工平台的最大压力为400mpa,其在380mpa时一次切割即可切穿该铝合金板,在切深2mm、5mm、8mm处的表面粗糙度平均值分别为3.821μm、4.140μm、4.470μm。随后,假设该加工平台的最大压力为150mpa,进行切割试验。
[0032]
s1:取工件样品在三轴低压磨料射流加工平台上进行切割实验,在本实施例中所使用的工件材料是牌号为5083铝合金板,板材尺寸大小为100mm
×
100mm
×
10mm。
[0033]
设计正交试验,其因素及水平如下表
[0034][0035]
通过正交试验获得最优加工参数组合:磨料流量m0为580g/m,靶距d0为8mm,横移速度v0为400mm/min,以及该条件下的切割门限压力p0为90mpa。通过切割实验,获得了在最大
压力p
max
即150mpa下的最大切割深度h
max
为3.47mm。通过在不同射流压力下的切割实验获得工件不同的切割深度,如图2所示,利用线性回归分析,建立切割深度h在最优工作参数下随压力p变化的函数关系:
[0036]
h=0.0113p+1.862
ꢀꢀꢀꢀ
公式(1)
[0037]
s2:将工件固定在三轴低压磨料射流加工平台上,在射流压力150mpa下,以磨料流量580g/m、靶距8mm和横移速度400mm/min对工件进行正向第一次切割(图1中,从左至右)。
[0038]
s3:当射流离开工件时立即控制三轴切割器将靶距变为d2,并在射流压力、磨料流量、横移速度不变的情况下沿原切割路径对工件进行反向第二次切割(图1中,从右至左)。
[0039]
d2=d
0-h
max
=8-3.47=4.53mm
ꢀꢀꢀꢀ
公式(2)
[0040]
s4:在本实施例中,铝合金板厚度h为10mm,则
[0041]
n=[h/h
max
]=[10/3.47]=2
ꢀꢀꢀꢀꢀꢀ
公式(3)
[0042]
即最后一次切割为第三次切割,靶距为d3[0043]
d3=d
2-h
max
=4.53-3.47=1.06mm
ꢀꢀꢀ
公式(4)
[0044]
计算工件第二次切割后剩余的厚度h0[0045]
h0=h-n
×hmax
=10-2
×
3.47=3.06mm
ꢀꢀꢀ
公式(5)
[0046]
将h0带入公式(1)中可得
[0047]
pn=(3.06-1.862)/0.0113=106.02mpa》p0ꢀꢀꢀꢀ
公式(6)
[0048]
即以射流压力107mpa进行最后一次的正向切割,完成铝合金板的彻底切穿。切割实验完成后,选取铝合金试样切割深度2mm、5mm、8mm三个位置测量粗糙度数值,同时为了减少误差,每个深度位置的水平方向按20mm等间隔选择四段测量,粗糙度数值取其平均值,结果如下
[0049]
表1为本发明实施例和对比例切割效果表
[0050][0051]
由上表可以得到,380mpa一次切割与150mpa低压三次变靶距切割相比,在切深2mm处切割面的表面粗糙度平均值降低了38.71%,在切深5mm处切割面的表面粗糙度平均值降低了35.45%,在切深8mm处切割面的表面粗糙度平均值降低了40.07%。在380mpa射流压力下一次切割的不同深度的表面粗糙度平均值的极差为1.225μm,在150mpa低压射流下三次变靶距切割的不同深度的表面粗糙度平均值的极差为0.649μm。结合附图3,150mpa低压射流状态下的多次正反向交替变靶距切割不仅可以在总体上改善切割面的表面质量,同时还在一定程度上削弱了磨料水射流切割造成的切割面上部光滑下部粗糙的现象。
[0052]
实验结果表明:采用该切割方法,可在150mpa的低压条件下超过380mpa的切割效果。
[0053]
本发明未涉及部分与现有技术相同或采用现有技术加以实现。
[0054]
以上所述仅为本发明的实施例,并非因此限制本发明的专利范围,凡是利用本发明说明书及附图内容所作的等同变换,或直接或间接运用在相关技术领域,均同理包括在本发明的专利保护范围内。