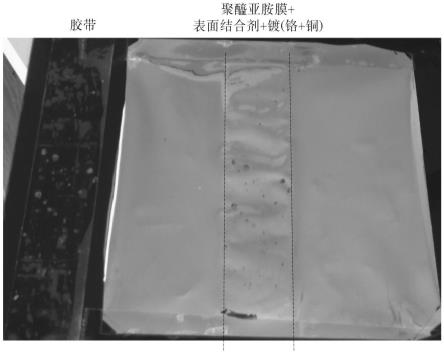
1.本发明涉及一种表面结合剂及使用其处理基材表面的方法,尤其涉及一种使用表面结合剂处理非金属面(如玻璃、硅晶、聚酰亚胺(pi)膜等的表面)及金属面(如铜与铜合金、铁铸、铝、钢、镍、锌、镍铁合金等的表面),以提升基材的表面与光刻胶、油墨或待添加的金属层(以溅镀、蒸镀等方式形成)等涂布材料之间的附着力的方法。
背景技术:2.通常,为了增进基材表面与涂布材料之间的附着力,会采用预先粗化处理基材表面的方法,例如,在印刷电路板的粗化铜箔上形成光刻胶,然后曝光使光刻胶具有特定图案形状,使部分的铜箔表面外露,接着蚀刻除去外露的铜,当除去光刻胶后,保留未被蚀刻除去的铜,形成所期望的铜线路图案于印刷电路板上。
3.然而,若采用粗化处理,表面粗糙的铜表面会保形于线路图案上,而高频高速传输的讯号传递路径通常发生于线路表面(集肤效应),若线路表面不平整,将产生讯号不良的问题。而且,粗化处理通常伴随污染废水,亦存在有环保的问题。另一方面,随着线路图案逐渐线细化、缩小化,粗化处理的铜表面和图案化光刻胶的附着力问题更趋严重。因此,在目前趋向高频高速传输时代中,业界期望以不粗化基材导体表面的方式来制作线路。
4.目前,已知有使用表面处理组合物预先处理金属表面的方法,然而先前技术所描述的表面处理组合物,仍存在有表面处理组合物过度腐蚀或不均匀腐蚀基材表面、或附着力提升效果不明显等问题。
技术实现要素:5.为了解决上述问题,本发明提供一种表面结合剂,用于提升非金属基材的表面附着力,该表面结合剂包括三唑化合物及咪唑化合物。
6.在一种实施方案中,该三唑化合物包括选自苯并三唑及5-甲基苯并三唑的至少一者,该咪唑化合物包括选自咪唑、二氢咪唑及1,2-二甲基咪唑的至少一者。
7.在一种实施方案中,表面结合剂进一步包括吡啶化合物,且在另一实施方案中,该吡啶化合物包括选自2-甲基吡啶及2-巯基吡啶的至少一者。
8.在一种实施方案中,三唑化合物、咪唑化合物以及吡啶化合物各者的浓度介于0.05g/l至50g/l之间。
9.在一种实施方案中,表面结合剂进一步包括二甲基乙酰胺,以作为催化剂,且在另一实施方案中,二甲基乙酰胺的浓度介于5ml/l至100ml/l之间。
10.在一种实施方案中,表面结合剂不包括酸类化合物。
11.在一种实施方案中,表面结合剂可进一步用于提升金属基材的表面附着力,且在另一实施方案中,表面结合剂进一步包括无机酸化合物及有机酸化合物的至少一者。
12.在一种实施方案中,无机酸化合物包括选自由硫酸、盐酸、硝酸、磷酸所组成的组的至少一者。
13.在一种实施方案中,有机酸化合物包括选自由甲酸、乙酸、丙酸、丁酸、戊酸、己酸、草酸、丙烯酸、丁烯酸、异丁烯酸、乙二酸、丙二酸、丁二酸、戊二酸、己二酸、庚二酸、顺丁烯二酸、苯甲酸、苯二甲酸、肉桂酸、乙醇酸、乳酸、苹果酸、水杨酸、甘氨酸、酒石酸、柠檬酸、胺磺酸、β-氯丙酸、烟酸、抗坏血酸、羟基三甲基乙酸及乙酰丙酸所组成的组的至少一者。
14.在一种实施方案中,表面结合剂进一步包括选自由乙醇胺、二乙二醇单丁醚、二甲氧基乙烷所组成的组的至少一者。
15.本发明还提供一种处理基材表面的方法,包括使本发明的表面结合剂与基材的表面接触,以提升该基材的表面与覆于该基材的表面上的层之间的附着力,其中,该基材为金属基材或非金属基材,且该覆于该基材的表面上的层为金属层或非金属层。
16.在一种实施方案中,金属基材与金属层的材质包括选自铜、铝、镍、锌、铁、铬及其合金所组成的组的至少一者。在一种实施方案中,非金属基材与非金属层的材质为玻璃、聚酰亚胺膜、预浸体、可成像的介电体、可成像的树脂、防焊材、蚀刻光刻胶或硅晶。
17.在一种实施方案中,表面结合剂通过旋涂、浸泡或喷洒的方式与基材的表面接触。
18.在一种实施方案中,使表面结合剂与基材的表面接触时,反应温度为介于20℃至60℃之间。
19.在一种实施方案中,使表面结合剂与基材的表面接触时,反应时间为介于30秒至900秒之间。
20.在一种实施方案中,基材的表面是未预先粗化处理的表面。
21.在一种实施方案中,表面结合剂预先稀释至10%至20%后再与基材的表面接触。
22.在一种实施方案中,本发明处理基材表面的方法进一步包括在表面结合剂与基材的表面接触后,进行水洗洗净多余的表面结合剂,之后热烘干燥该基材。
23.本发明的表面结合剂具有以下特点:
24.1.表面结合剂施用于基材的表面上形成有机层,有效提升未预先粗化处理的基材表面与覆于其上的材料之间的附着力,避免覆于其上的材料脱落、剥离;
25.2.由于可排除粗化处理(例如刷磨、喷砂、微蚀刻等)制程,避免产生粗化处理用废弃物(重金属废水、腐蚀性强酸等),同时,基材表面具有较佳的平整性;
26.3.所适用的基材及覆于其上的层的种类广泛,包括玻璃、聚酰亚胺膜、预浸体、可成像的介电体、可成像的树脂、防焊材、蚀刻光刻胶及硅晶等的非金属、以及铜、铝、镍、锌、铁、铬及其合金的金属;
27.4.表面结合剂所形成的有机层为透明无色,不会改变基材表面的颜色,于使用铜做为基材时,不会有铜面色差,有利于自动光学检查(auto-optical inspection,aoi)检测;
28.5.表面结合剂具有重工性,重复使用本发明的表面结合剂仍具有优异的效果;
29.6.基材表面经表面结合剂处理后形成的有机层具有疏水性,于使用铜作为基材时,能改善后续涂布防焊油墨于导通孔中所产生的油墨吹孔问题。
附图说明
30.图1至图3是比较例3至5的测试结果。
31.图4至图6是本发明表面结合剂实施例17至19的测试结果。
具体实施方式
32.须知,本说明书中任何比例关系的改变或大小的调整,在不影响本发明所能产生的功效及所能达成的目的下,均应仍落在本发明所描述的技术内容所能涵盖的范围内。同时,本说明书中所引用的如“上”等用语,也仅为便于叙述的明了,而非用以限定本发明可实施的范围,其相对关系的改变或调整,在无实质变更技术内容下,当亦视为本发明可实施的范畴。
33.本发明的表面结合剂包括三唑化合物以及咪唑化合物。
34.三唑化合物与咪唑化合物是提升基材表面与涂布材料之间的附着力的主要成分,其于基材表面上形成有机层。三唑化合物例如为苯并三唑及5-甲基苯并三唑等,咪唑化合物例如为咪唑、二氢咪唑及1,2-二甲基咪唑等。三唑化合物与咪唑化合物可作为桥连配体,其以n-1以及n-3为配位原子,分别连接至基材表面上的原子以及涂布材料的原子形成键结,从而达到桥接基材表面与涂布材料的效果。
35.本发明的表面结合剂进一步包括吡啶化合物,其作为提升基材表面与涂布材料之间的附着力的次要成分。吡啶化合物例如为2-甲基吡啶及2-巯基吡啶等。
36.表面结合剂中,三唑化合物、咪唑化合物以及吡啶化合物中每一种的浓度介于0.05g/l至50g/l之间、0.1g/l至40g/l之间、0.25g/l至30g/l之间、0.5g/l至25g/l之间、或者1g/l至25g/l之间,浓度例如可以是0.05、0.06、0.07、0.08、0.09、0.1、0.15、0.2、0.25、0.3、0.35、0.4、0.45、0.5、0.6、0.7、0.8、0.9、1、1.5、2、2.5、3、3.5、4、4.5、5、5.5、6、6.5、7、7.5、8、8.5、9、9.5、10、11、12、13、14、15、16、17、18、19、20、21、22、23、24、25、26、27、28、29、30、31、32、33、34、35、36、37、38、39、40、41、42、43、44、45、46、47、48、49、50g/l,但不限于此。
37.提升附着力的化合物的总浓度可介于0.05g/l至200g/l之间、0.1g/l至200g/l之间、1g/l至150g/l之间、10g/l至100g/l之间、或者25g/l至100g/l之间,浓度例如可以是0.05、0.06、0.07、0.08、0.09、0.1、0.15、0.2、0.25、0.3、0.35、0.4、0.45、0.5、0.6、0.7、0.8、0.9、1、1.5、2、2.5、3、3.5、4、4.5、5、5.5、6、6.5、7、7.5、8、8.5、9、9.5、10、11、12、13、14、15、16、17、18、19、20、21、22、23、24、25、26、27、28、29、30、31、32、33、34、35、36、37、38、39、40、41、42、43、44、45、46、47、48、49、50、55、60、65、70、75、80、85、90、95、100、105、110、115、120、125、130、135、140、145、150、155、160、165、170、175、180、185、190、195、200g/l,但不限于此。
38.使三唑化合物、咪唑化合物以及吡啶化合物溶解于溶剂中以配制成表面结合剂。溶剂的种类并无限定,只要是可使其以适当的浓度溶解的溶剂即可。在一种实施方案中溶剂为水,在其他实施方案中溶剂可为其他有机溶剂,溶剂也可以同时包含有机溶剂及水。
39.作为溶剂,例如可选用苯、甲苯、二甲苯、乙基苯、甲酚及氯苯等的芳香族类;甲醇、乙醇、正丙醇、异丙醇、正丁醇、正己醇及环己醇等脂肪族醇类;乙二醇、二乙二醇、丙二醇及二丙二醇等二醇类;丙三醇;丙酮、甲基乙基酮、二乙基酮、甲基异丁基酮、乙基异丁基酮、及环己酮等酮类;二乙醚、二丙醚、二丁醚、二己醚、苄基甲基醚、苄基乙基醚、及四氢呋喃等醚类;乙二醇单甲基醚、乙二醇单乙基醚、乙二醇单丙基醚、乙二醇单丁基醚、丙二醇单甲基醚、丙二醇单乙基醚、丙二醇单丙基醚、丙二醇单丁基醚、二乙二醇单甲基醚、二乙二醇单乙基醚、二乙二醇单丙基醚、二乙二醇单丁基醚及二乙二醇单苯基醚等二醇单醚类;乙二醇二甲基醚、乙二醇二乙基醚、乙二醇二丙基醚、丙二醇二甲基醚、丙二醇二乙基醚、丙二醇二丙
基醚、二乙二醇二甲基醚、二乙二醇二乙基醚及二乙二醇二丙基醚等二醇二醚类;乙二醇单甲基醚乙酸酯、乙二醇单乙基醚乙酸酯、乙二醇单丙基醚乙酸酯、乙二醇单丁基醚乙酸酯、乙二醇单苯基醚乙酸酯、二乙二醇单甲基醚乙酸酯及二乙二醇单乙基醚乙酸酯等二醇单乙酸酯类;二乙二醇单丙基醚乙酸酯、二乙二醇单丁基醚乙酸酯、二乙二醇单苯基醚乙酸酯、丙二醇单甲基醚乙酸酯、丙二醇单乙基醚乙酸酯、丙二醇单丙基醚乙酸酯、2-甲氧基丁基乙酸酯、3-甲氧基丁基乙酸酯、4-甲氧基丁基乙酸酯、2-甲基-3-甲氧基丁基乙酸酯、3-甲基-3-甲氧基丁基乙酸酯、3-乙基-3-甲氧基丁基乙酸酯、2-乙氧基丁基乙酸酯、4-乙氧基丁基乙酸酯、4-丙氧基丁基乙酸酯、2-甲氧基戊基乙酸酯、3-甲氧基戊基乙酸酯、4-甲氧基戊基乙酸酯、2-甲基-3-甲氧基戊基乙酸酯、3-甲基-3-甲氧基戊基乙酸酯、3-甲基-4-甲氧基戊基乙酸酯及4-甲基-4-甲氧基戊基乙酸酯等二醇类的单醚单乙酸酯类;丙酸甲酯、丙酸乙酯、丙酸丙酯、丙酸异丙酯、2-羟基丙酸甲酯、2-羟基丙酸乙酯、2-羟基-2-甲基、甲基-3-甲氧基丙酸酯、乙基-3-甲氧基丙酸酯、乙基-3-乙氧基丙酸酯、乙基-3-丙氧基丙酸酯、丙基-3-甲氧基丙酸酯、异丙基-3-甲氧基丙酸酯、乙氧基乙酸乙酯、羟基乙酸乙酯、2-羟基-3-甲基丁酸甲酯、乙酸甲酯、乙酸乙酯、乙酸丙酯、乙酸异丙酯、乙酸丁酯、乙酸异戊酯、碳酸甲酯、碳酸乙酯、碳酸丙酯、碳酸丁酯、丙酮酸甲酯、丙酮酸乙酯、丙酮酸丙酯、丙酮酸丁酯、乙酰乙酸甲酯、乙酰乙酸乙酯、乙酸苄酯、苯甲酸乙酯、草酸二乙酯、马来酸二乙酯、及γ-丁内酯等酯类;n,n,n',n'-四甲基脲、n-甲基-2-吡咯烷酮、n,n-二甲基甲酰胺、n,n-二甲基乙酰胺、六甲基磷酰胺、1,3-二甲基-2-咪唑啉酮、及二甲基亚砜等非质子性极性有机溶剂。在一种实施方案中,溶剂例如水及二乙二醇单丁醚。
40.本发明的表面结合剂还可包括催化剂,催化剂的种类并无限制,具体可举例为二甲基乙酰胺。催化剂加速表面结合剂与基材表面之间的作用,可缩短处理时间,有利于制程的控制。催化剂的浓度可介于5ml/l至100ml/l之间,浓度例如为5、6、7、8、9、10、11、12、13、14、15、16、17、18、19、20、25、30、35、40、45、50、55、60、65、70、75、80、85、90、95、100ml/l,但不限于此。
41.本发明的表面结合剂的ph值一般可介于7至8之间,但不限于此。ph值例如可为7.0、7.1、7.2、7.3、7.4、7.5、7.6、7.7、7.8、7.9、8.0。上述表面结合剂的ph值是不含有酸类化合物时所测量得到的,即本发明的表面结合剂可不含有无机酸及/或有机酸。不过,在其他实施方案中,本发明的表面结合剂还可包括无机酸化合物,其可调整表面结合剂的ph值,另一方面,无机酸化合物也可有微蚀刻的作用,使基材的表面形成极细微的腐蚀痕迹,从而增加与涂布材料的接触面积,提升附着力。
42.无机酸化合物的种类不无特别限定,例如可为选自由硫酸、盐酸、硝酸及磷酸所组成的组中的至少一者,于使用无机酸混合物时,各酸可以任何适当比例组合。在一种实施方案中,表面结合剂中包含硫酸。
43.无机酸化合物的浓度可介于50g/l至400g/l之间,浓度例如为50、55、60、65、70、75、80、85、90、95、100、105、110、115、120、125、130、135、140、145、150、155、160、165、170、175、180、185、190、195、200、210、220、230、240、250、260、270、280、290、300、310、320、330、340、350、360、370、380、390、400g/l,但不限于此。
44.在其他实施方案中,本发明的表面结合剂还可包括有机酸化合物,其如上述无机酸化合物般可调整表面结合剂的ph值,另一方面,有机酸化合物也可有微蚀刻的作用,使基
材的表面形成极细微的腐蚀痕迹,从而增加与涂布材料的接触面积,提升附着力。
45.有机酸化合物的种类不无特别限定,例如可为选自由甲酸、乙酸、丙酸、丁酸、戊酸、己酸、草酸、丙烯酸、丁烯酸、异丁烯酸、乙二酸、丙二酸、丁二酸、戊二酸、己二酸、庚二酸、顺丁烯二酸、苯甲酸、苯二甲酸、肉桂酸、乙醇酸、乳酸、苹果酸、水杨酸、甘氨酸、酒石酸、柠檬酸、胺磺酸、β-氯丙酸、烟酸、抗坏血酸、羟基三甲基乙酸及乙酰丙酸所组成的组中的至少一者,在使用有机酸混合物时,各酸可以任何适当比例组合。在一种实施方案中,表面结合剂中包含乙酸。
46.有机酸化合物的浓度可介于5g/l至100g/l之间,浓度例如为5、6、7、8、9、10、11、12、13、14、15、16、17、18、19、20、21、22、23、24、25、26、27、28、29、30、31、32、33、34、35、36、37、38、39、40、41、42、43、44、45、46、47、48、49、50、55、60、65、70、75、80、85、90、95、100g/l,但不限于此。
47.在添加有机酸化合物、无机酸化合物等酸类化合物的情况,本发明的表面结合剂的ph值大幅降低,例如ph为小于4、小于3、或小于2,但不限于此。具体地,添加有机酸及/或无机酸时的表面结合剂的ph值可为3.9、3.8、3.7、3.6、3.5、3.4、3.3、3.2、3.1、3.0、2.9、2.8、2.7、2.6、2.5、2.4、2.3、2.2、2.1、2.0、1.9、1.8、1.7、1.6、1.5、1.4、1.3、1.2、1.1、1.0。当本发明的表面结合剂不包括酸类化合物时,通常较适合用于非金属的基材表面上;当本发明的表面结合剂包括酸类化合物时,通常较适合用于金属的基材表面上,但不限于此。
48.本发明的表面结合剂还可包括选自由乙醇胺、二乙二醇单丁醚、二甲氧基乙烷所组成的组中的至少一者的其他成分。在不阻碍本发明的目的的情况下,还可添加各种添加剂,可列举例如ph调整剂、分散剂、表面活性剂、防腐剂、粘度调整剂、抗氧化剂、紫外线吸收剂、稳定剂及着色剂等。
49.本发明提供一种处理基材表面的方法,包括清洁基材的表面;使表面结合剂与基材的表面接触;任选地以水清洗多余的表面结合剂;以及进行热烘干燥或光固化以于该基材的表面上形成有机层。通过表面结合剂处理基材表面,以提升该基材与覆该基材的表面上的材料之间的附着力。
50.清洁基材的表面可通过使用有机溶剂或酸性清洁剂来达成,具体地,例如可使用硫酸、磷酸等溶液、异丙酮,但不限于此。
51.清洁完基材的表面后,使表面结合剂与基材的表面接触。接触的方法无特别限定,可采用溅镀、蒸镀、浸泡或浸渍、旋涂、或喷雾等方法,可任选地选择合适的接触方法。从形成均匀的有机层的观点来看,可优先选用浸泡或浸渍处理。
52.本发明的表面结合剂可适用基材的种类广泛,可以是金属基材或非金属基材,而后续覆于该基材的表面上的层的种类亦广泛,可以是金属层或非金属层。金属基材及金属层的材质例如铜、铝、镍、锌、铁、铬及其合金等,非金属基材及非金属层的材质例如玻璃、聚酰亚胺膜、预浸体、可成像的介电体、可成像的树脂、防焊材、蚀刻光刻胶及硅晶等。由于使用表面结合剂大幅强化了基材的表面附着力,故基材的表面可以是未预先粗化处理的表面。
53.当采用浸渍处理时,表面结合剂的温度优选介于20℃至60℃之间,更优选介于30℃至50℃之间;浸渍时间优选介于60秒至900秒之间,更优选介于60秒至600秒之间。通常在浸渍处理之后任选地进行水洗步骤,最后进行干燥步骤。
54.当采用喷雾处理时,表面结合剂的温度优选也介于20℃至60℃之间,更优选介于30℃至50℃之间。喷雾压力优选介于0.01mpa至0.3mpa之间且喷雾时间介于15至600秒的条件下进行处理,更优选为喷雾压力介于0.05mpa至0.2mpa且喷雾时间介于30至300秒的条件下进行处理。通常在浸渍处理之后任选地进行水洗步骤,以洗净多余表面结合剂,最后进行热烘干燥或光固化步骤以令该表面结合剂于基材的表面上形成有机层。
55.在一种实施方案中,本发明的表面结合剂于接触基材的表面前,可以先稀释成10%至20%的稀释浓度。
56.本发明的表面结合剂接触基材的表面后,于基材的表面上形成有机层,该有机层为透明且疏水性,由于该有机层极薄,肉眼难辨视,故可通过将水滴落在基材的表面上,观察水是否与表面具有大接触角而呈现水滴状来确定有机层是否成功形成。
57.具体地,本发明的表面结合剂可与如铜板、铜箔基板等金属基材的表面接触,例如将如铜板、铜箔基板等基材浸泡于含有本发明的表面结合剂的浴中,以于该基材的表面上形成有机层,随后再形成如光刻胶的聚合物涂覆材料于该有机层上,以令该有机层介于该涂覆材料与基材之间。另一方面,也可将表面结合剂与玻璃、聚酰亚胺膜等非金属基材的表面接触,形成有机层,随后再镀上镍、铬、铜等金属层,俾令该有机层介于该金属层与基材之间。
58.以下通过特定的具体实施例说明本发明的实施方式,本领域技术人员可由本说明书所描述的内容轻易地了解本发明的其他优点及功效。
59.测试例1
60.实施例1的表面结合剂包括苯并三唑、咪唑以及二氢咪唑等提升附着力的化合物。于室温下,将未粗化处理的铜板浸泡于实施例1的表面结合剂内15分钟,使表面结合剂处理铜表面,接着水洗、烘干,然后于铜表面上涂布/压膜干膜光刻胶(干膜光刻胶e9500,购自长兴材料工业股份有限公司)。以3%naoh溶液作为去膜液,并将涂布有光刻胶的铜板浸泡于去膜液内,操作温度为50℃,观察光刻胶自铜面上剥离的情形,当光刻胶剥离面积达到30%时记录时间。
61.实施例2至7以实施例1相同步骤进行测试,但调整表面结合剂的组成、表面结合剂浸泡时间等参数如下表1所示。而比较例1是未浸泡表面结合剂,直接使未粗化处理的铜板浸泡于去膜液内。
62.实施例1至7及比较例1的表面结合剂组成、表面结合剂浸泡时间及光刻胶剥离时间如下表1所示。表面结合剂原液组成中,苯并三唑的浓度介于3g/l至30g/l之间、咪唑的浓度介于0.5g/l至5g/l之间、二氢咪唑的浓度介于0.5g/l至5g/l之间、2-甲基吡啶的浓度介于3g/l至30g/l之间、5-甲基苯并三唑的浓度介于0.5g/l至5g/l之间、1,2-二甲基咪唑的浓度介于0.5g/l至5g/l之间、2-巯基吡啶的浓度介于0.5g/l至5g/l之间、二甲基乙酰胺的浓度介于5ml/l至50ml/l之间。以表面结合剂处理基材表面之前,将原液以水稀释为20%再进行处理。
63.表1
[0064][0065]
由上表1的结果可知,铜面经实施例1的表面结合剂处理可减缓光刻胶自铜面剥离的时间,由1分01秒延长至2分02秒,显示实施例1的表面结合剂可有效提升铜面与光刻胶之间的附着力。另一方面,随着表面结合剂中的提升附着力的化合物种类增加,铜面与光刻胶的间的附着力提升效果更加显著,实施例6的结果显示光刻胶自铜面剥离的时间已大幅延长至3分29秒,而且,即便使表面结合剂浸泡时间缩减为3分钟,如实施例7所示,光刻胶自铜面剥离的时间仍能维持在3分18秒,远远优于未使用表面结合剂的比较例1。
[0066]
测试例2
[0067]
实施例8至15是准备具有1oz厚度的铜箔基板(fr-4,购自南亚塑胶工业股份有限公司),并以酸性清洁剂清洁铜箔表面,接着于室温下使铜箔基板浸泡于表面结合剂内,其中,该表面结合剂包括苯并三唑、咪唑、二氢咪唑、2-甲基吡啶、5-甲基苯并三唑、1,2-二甲基咪唑及2-巯基吡啶等提升表面附着力的化合物以及二甲基乙酰胺,且表面结合剂原液各成分比例如测试例1所述;之后水洗、烘干;再于铜箔表面上涂布/压膜干膜光刻胶(干膜光刻胶e9500,购自长兴材料工业股份有限公司),形成25μm厚度的光刻胶;以10*10共计100个圆点图形对光刻胶曝光,其中每个圆点图形的直径为50μm,且各圆点的间距为50μm;后续以浓度1%(即10g/l)的碳酸钠溶液作为显影液,以喷洒的方式对光刻胶进行显影,温度控制为30℃、压力设置为30psi、喷洒处理时间为60秒,然后水洗、烘干;最后观察光刻胶的圆点图形的保留情况。比较例2则未浸泡表面结合剂,直接使铜箔基板涂布光刻胶后曝光、显影、水洗、烘干。实施例8至15及比较例2的参数及结果如下表2所示。
[0068]
表2
[0069][0070]
圆点数量存留的比例越高,表示铜箔表面与光刻胶的间的附着力越好。表2的结果中,未使用表面结合剂的比较例2的完整圆点数量仅有71个,而使用表面结合剂的实施例8至15的完整圆点数量达到92个以上,且随着浸泡时间的增加及稀释浓度的提升,完整圆点数量更可达到100个,拥有极佳的良率。
[0071]
测试例3
[0072]
另以表面结合剂喷洒处理玻璃基板的表面,其中,该表面结合剂包括苯并三唑、咪唑、二氢咪唑、2-甲基吡啶、5-甲基苯并三唑、1,2-二甲基咪唑及2-巯基吡啶等提升表面附着力的化合物以及二甲基乙酰胺,作为实施例16,其中,表面结合剂原液各成分比例如测试例1所述,且以水稀释原液为20%使用。接着于该玻璃基板表面上设计形成有数条并行排列且宽度为2μm、厚度为20μm的长条形光刻胶(压模参数:压膜温度90℃、压膜压力3kg,压膜速度2m/min),并以测试例2的条件进行曝光显影。结果显示显影后的光刻胶没有浮离、脱落的现象发生,即表面结合剂也能有效提升玻璃表面与光刻胶之间的附着力。
[0073]
测试例4
[0074]
将聚酰亚胺膜以异丙醇(ipa)处理5分钟后水洗烘干,接着于聚酰亚胺膜的表面上溅镀100nm厚度的铬层,再溅镀500nm厚度的铜层,作为比较例3至5。再以3m#610胶带贴附至镀层表面上,去除胶带与镀层间的气泡后,于贴附胶带后1分钟内以90度垂直拉扯的方式以小于3秒的速度快速将胶带自镀层表面撕离,观察镀层的剥落情况。其中,3m#600、3m610胶带的初期粘性为32oz/inch,约为357g/cm。
[0075]
适用:cid a-a-113,type 1,class b,3m brand premium transparent film tape 600,3m brand premium cellophane tape 610
[0076]
依据:ipc-tm-650number 2.4.1/2.4.1.1/2.4.1.3/2.4.1.4/2.4.28/2.4.28.1
[0077]
图1至图3的结果显示,在未使用表面结合剂的情形下,胶带下金属镀层的剥落面积达70至99%,表示聚酰亚胺膜与金属镀层之间的附着力不足,无法抵抗胶带的剥离力。
[0078]
另一方面,将聚酰亚胺膜以表面活性剂处理5分钟后水洗;其后浸泡于表面结合剂内5分钟后水洗烘干,使表面结合剂处理聚酰亚胺膜表面,其中,该表面结合剂包括苯并三唑、咪唑、二氢咪唑、2-甲基吡啶、5-甲基苯并三唑、1,2-二甲基咪唑及2-巯基吡啶等提升表面附着力的化合物以及二甲基乙酰胺,其中,表面结合剂原液各成分比例如测试例1所述,
且以水稀释原液为20%使用;之后水洗、烘干;接着使用直流溅镀(功率600w),溅镀100nm厚度的铬层、500nm厚度的铜层为金属镀层,作为实施例17至19。最后以3m 610胶带贴附至金属镀层以前述的方法测试金属镀层的剥落情况。
[0079]
图4至图6的结果显示使用表面结合剂处理聚酰亚胺膜表面后,胶带下金属镀层的剥落面积小于1%,此表示聚酰亚胺膜表面通过表面结合剂处理后可实现与金属层之间的优异结合,可抵抗胶带的剥离力。
[0080]
由上述可知,本发明的表面结合剂可处理基材表面,于基材表面上形成有机层,有效提升未预先粗化处理的基材表面与涂布材料之间的附着力,避免涂布材料脱落、剥离。由于可排除粗化处理制程,降低制程成本且避免产生粗化处理用废弃物(重金属废水、腐蚀性强酸等),而且,所适用的基材及涂布材料种类广泛,也具有重工性,重复使用本发明的表面结合剂仍具有优异的效果。
[0081]
上述实施例用以例示性说明本发明的原理及其功效,而非用于限制本发明。任何本领域技术人员均可在不违背本发明的精神及范畴下,对上述实施例进行修改。因此本发明的权利保护范围,应如后述的权利要求书所列。
[0082]
应当理解地,在本发明所描述的技术内容所能涵盖的范围内,各技术特征(例如实施方案及实施例所描述的)可以自由地相互组合以形成新的或更优选的技术方案,为简洁起见,在此不赘述。且本发明所述的由端值构成的数值范围中,只要数值落于上下两端值之间,即应包含在本发明所描述的范围内,且其与端点或其他数值所形成的次范围也应理所当然地包含在本发明所描述的范围内。