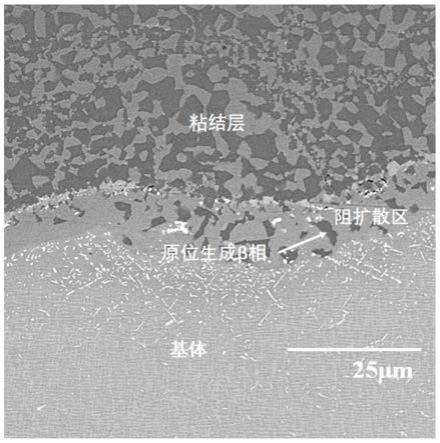
一种双界面性能强化的mcralyx粘结层和热障涂层及其制备方法
技术领域
1.本技术涉及涂层防护技术领域,更具体地说,它涉及一种双界面性能强化的mcralyx粘结层和热障涂层及其制备方法。
背景技术:2.近年来,mcraly(m=co,ni或co+ni)涂层广泛应用于抗高温氧化防护涂层和热障涂层中基体与陶瓷层间的粘结层。m表示基体元素,通常为ni与co,为了进一步提高涂层的性能,在涂层中还会添加其他元素,用x表示,进而形成mcralyx多组元合金材料。
3.但是多数的mcraly材料设计仅仅关注抗氧化防腐蚀作用,而忽略了涂层与基体的相互扩散性能以及作为粘结层时与陶瓷面层的结合性。但是在长期高温环境中,涂层与基材中的元素会发生相互扩散,容易造成基材力学性能下降,涂层中的有益元素含量降低,需要提供一种新的能够实现双界面性能强化的mcralyx粘结层。
技术实现要素:4.为了既可以实现粘结层与基材阻扩散,又可以实现粘结层与陶瓷层的强结合性,本技术提供一种双界面性能强化的mcralyx粘结层和热障涂层及其制备方法。
5.本技术提供的一种双界面性能强化的mcralyx粘结层采用如下的技术方案:一种双界面性能强化的mcralyx粘结层,包括由mcralyx粉末材料在基材上喷涂形成的高致密层和mcralyx粉末材料在高致密层上喷涂形成的高粗糙度层,所述粘结层在基材与粘结层的高致密层之间的界面处原位生成阻扩散区,所述阻扩散区内含有大量密排二次β原位析出相,所述高粗糙度层表面粗糙度ra≥7μm,所述高粗糙度层用于与陶瓷面层结合,x为hf、si、ta、re和w中的一种或多种。
6.通过采用上述技术方案,本技术中粘结层x中hf和si元素最终可以实现二次β相阻扩散区的生成,得到的阻扩散区厚度为10-40微米,阻扩散区的生成降低了粘结层与基体之间的扩散,从而缓解由于粘结层与基体之间的扩散导致基体力学性能降低问题;ta、la和w元素能够阻碍mcraly粘结层中al元素向基体扩散,进一步降低粘结层与基层之间的扩散,而且hf和si元素能使mcraly表面组织有序化,使得服役过程中粘结层与陶瓷层不易脱落。本技术中高致密层与基材之间原位获得具有阻扩散效果的二次β相区,高粗糙度层的年结合可以增强其与陶瓷层的结合力,从而获得的粘结层既可以实现粘结层与基材阻扩散,又可以实现粘结层与陶瓷层的强结合性。
7.可选的,所述mcralyx粉末材料,当ni含量≥40%时,co含量为8-30%,cr含量为10-25%,al含量为8-14%,y含量为0.1-1.5%,元素x至少含有hf、si、ta、la或w,hf与si总量为0.5~3%,ta、la、w总量为1-9%。
8.可选的,所述mcralyx粉末材料,当ni含量≥40%时,20-26%,cr含量为14-20%,al含量为10.5-14%,y含量为0.3-1.0%,元素x至少含有w,hf与si总量为0.5-2%,w总量为
2-7%。
9.通过采用上述技术方案,本技术中通过对上述元素含量的控制,尤其是al含量的控制,使得最终阻扩散区可以形成大量密排β相,申请人发现al含量低时,无法形成β相,另外本技术中w、ta和hf的添加可以使得提升β相的含量,最终得到涂层的性能更优。
10.可选的,所述高粗糙度层表面粗糙度ra为7.5-14.6μm。
11.通过采用上述技术方案,通过控制高粗糙度层表面的粗糙度,最终得到的粘结层与陶瓷表面的结合性能更好。
12.可选的,所述高致密层的厚度为50-200μm,所述高粗糙度层的厚度为90-350μm。
13.通过采用上述技术方案,通过对高致密层和高粗糙度层厚度的控制,得到的粘结层可以满足应用环境需求,而且还具有良好的抗氧化性能。
14.可选的,所述高粗糙度层通过采用大气等离子喷涂方法在高致密层表面喷涂得到。
15.可选的,采用大气等离子喷涂方法的参数为:氩气流量35-65 l/min,氢气流量7-22 l/min,电流参数为450-720a,喷距为95-170mm。
16.第二方面,本技术提供一种热障涂层,包括喷涂在基材上的mcralyx粘结层以及喷涂在所述mcralyx粘结层的高粗糙度层上的陶瓷面层。
17.通过采用上述技术方案,本技术中通过在涂层中添加其他元素x,形成的mcralyx粘结层与基材之间生成具有阻扩散效果的二次β相区,再配合w等元素的阻扩散作用,从而起到缓解基材与粘结层的元素相互扩散的效果,解决了传统mcraly材料仅关注抗氧化防腐蚀作用的时候忽略粘结层与基体的相互扩散性能,粘结层相互扩散导致基材力学性能下降的问题。另外,相较于仅采用高致密度的mcraly粘结层,在实际复杂热/力学载荷条件下,在服役过程中,由于mcraly粘结层高致密度导致表面粗糙度低,与陶瓷面层的结合力差,导致粘结层与陶瓷面层之间由于热应力失配导致陶瓷层剥落;而若是仅仅采用高粗糙度低致密度的mcraly粘结层,高粗糙度的设置虽然增强了陶瓷面层与mcraly粘结层之间的结合性,然而,由于致密度低,在长时间服役后mcraly粘结层氧化会更加严重,其表面会出少量疏松结构的尖晶石组织,使得陶瓷面层由于应力不均而脱落。本技术中粘结层选用高致密层和高粗糙度层的设置,使得高粗糙度层与陶瓷面层之间形成强结合,而且最终得到的mcralyx粘结层表面组织有序化,使得服役过程中粘结层与陶瓷层之间不易剥落。
18.第三方面,本技术提供一种热障涂层的制备方法,包括以下步骤:基材预处理:对基材进行预处理;高致密层喷涂,在基材表面采用mcralyx粉末材料喷涂制备高致密层;高粗糙度层喷涂:在高致密层表面采用mcralyx粉末材料喷涂制备高粗糙度层,得到mcralyx粘结层;陶瓷面层喷涂:在高粗糙度层表面喷涂,制得陶瓷面层;真空一次时效处理:在真空环境下进行一次时效热处理;大气二次时效热处理,在大气环境下进行二次时效处理,得到在基材上的热障涂层。
19.通过采用上述技术方案,真空一次时效处理实现了高致密层的真空高温扩散热处理,从而可以对基材与粘结层界面的组织结构进行调控,再结合mcralyx成分的设计,可以
原位获得具有阻扩散效果的二次β相区,生成的阻扩散区,为粘结层与基体界面的性能强化,高粗糙度层的设置增强与陶瓷面层的结合力,更重要的是:后续的大气低温热处理使得mcralyx粘结层表面组织有序化,生成致密连续的α-al2o3薄膜,为粘结层与陶瓷面层的性能强化,从而使得服役过程中粘结层与陶瓷层不易剥落。
20.可选的,高致密层喷涂采用超音速火焰、真空或低压等离子喷涂方法;陶瓷面层喷涂采用大气等离子喷涂方法。
21.可选的,真空一次时效热处理的控制参数为:控制真空度小于0.1pa,采用氦气、氩气、氮气中的一种或多种气体保护,热障涂层与基材共同随炉升温至1050-1400℃,保温2-22h,保温结束后,随炉降温;所述大气二次时效热处理的控制参数为:在大气环境下,随炉升温至790-1010℃,保温15-48h,然后随炉降温。
22.综上所述,本技术具有以下有益效果:1、本技术中基材与粘结层界面之间获得具有阻扩散效果的阻扩散区,阻扩散区内含有大量密排二次β原位析出相,该阻扩散区的生成再配合粘结层x元素的添加,可以实现粘结层与基材的阻扩散,高粗糙度层的设置可以增强粘结层与陶瓷面层的强结合性能,最终mcralyx粘结层既可以实现粘结层与基材的阻扩散,又可以实现粘结层与陶瓷面层的强结合性,实现双界面性能的优化;2、本技术中真空一次时效处理可以对基材与粘结层界面的组织结构进行调控,再结合mcralyx成分的设计,可以原位获得具有阻扩散效果的二次β相区,生成的阻扩散区,为粘结层与基体界面的性能强化;3、本技术高粗糙度层的设置增强与陶瓷面层的结合力,而且后续的大气低温热处理使得mcralyx粘结层表面组织有序化,生成致密连续的α-al2o3薄膜,为粘结层与陶瓷面层的性能强化,从而使得服役过程中粘结层与陶瓷层不易剥落。
附图说明
23.图1是本技术中得到的mcralyx粘结层与基材界面处生成β析出相的显微结构图;图2是本技术对比例3中得到的mcralyx粘结层与基材界面处的显微结构图。
具体实施方式
24.以下结合附图和实施例对本技术作进一步详细说明,予以特别说明的是:以下实施例中未注明具体条件者,按照常规条件或制造商建议的条件进行,以下实施例中所用原料除特殊说明外均可来源于普通市售。
25.本技术中的百分比均为质量百分比。
26.本技术中mcralyx粉末材料,当ni含量≥40%时,mcralyx粉末材料为ni基合金粉末,co含量为8-30%,cr含量为10-25%,al含量为8-14%,y含量为0.1-1.5%,元素x至少含有hf、si、ta、la或w,hf与si总量为0.5~3%,ta、la、w总量为1-9%。
27.当ni含量<40%时,co含量为30-45%,此时合金粉末为co基合金粉末,其余元素占比与上述ni基合金粉末占比相同。
28.本技术中的陶瓷面层选用本领域常用的陶瓷面层即可,如氧化钇稳定氧化锆
(ysz)、锆酸盐、镧酸盐等。
29.以下实施例中mcralyx粉末材料采用真空雾化技术得到,具体包括以下步骤:1)配料与投料:将所述nicocralyx合金所包含元素的单质或合金块材、板材或粉末按元素含量进行配置,并投入熔炼炉内;原料可以一次性投入熔炼炉,亦可选择性地在熔炼过程中间分批次投放; 2)熔炼:控制熔炼炉环境真空度小于1pa,使用氦气、氩气、氮气中的一种或多种作为保护性气体,利用感应加热原理加热炉内金属材料至其完全熔化并混合均匀; 3)喷雾造粒:控制喷雾塔的真空度小于1pa,使用氦气、氩气、氮气中的一种或多种作为保护性气体,打开与熔炼炉连接的阀门使熔液流入喷雾塔,同时采用氦气、氩气、氮气中的一种或多种气体形成的高速气流将熔液吹散,形成细小的液滴,液滴在喷雾塔中快速冷却形成固态的颗粒。
30.4)收集封装:固态颗粒落入收集料罐中,得到nicocralyx合金粉末;待粉末冷却后对粉末进行筛分,收集合适粒度段的粉末进行封装,剩余粉末可充当返料用于步骤1)。
31.步骤4)中得到的nicocralyx合金粉末为球形,流动性性优于20s/50g,粉末内氧含量小于500ppm。
32.以下实施例中高粗糙度层喷涂的时候,通过对于试验条件和mcralyx粉末粒度的调整制得的高粗糙度层的表面粗糙度ra为7.5-14.6μm。
33.本技术中高致密层的表面粗糙度ra为5.5-6.5μm。
34.实施例1一种热障涂层的制备方法,包括以下步骤:基材预处理:选用rene n5镍基单晶高温合金作为基材,对基材进行预处理,预处理包括对基材表面进行喷砂、清洗和干燥;高致密层喷涂,采用超音速火焰喷涂方法将mcralyx粉末材料沉积在基材表面,得到厚度为50μm、粗糙度ra为5.5μm的高致密层,喷涂前对基材进行预热,预热温度为150℃;高粗糙度层喷涂:采用大气等离子喷涂方法将mcralyx粉末材料沉积在高致密层表面,得到厚度为350μm、粗糙度ra为7.5μm的高粗糙度层,该步骤中大气等离子喷涂方法参数为:氩气流量35l/min,氢气流量7l/min,电流参数为450a,喷距为95mm;陶瓷面层喷涂:采用大气等离子喷涂方法在高粗糙度层表面沉积8%氧化钇稳定氧化锆,得到陶瓷面层,该步骤中大气等离子喷涂方法参数为:氩气流量30 l/min,氢气流量10l/min,电流参数为500a,喷距为75mm;真空一次时效处理:在真空炉内,控制真空度0.01pa,采用氩气作为气体保护,热障涂层与基材共同随炉升温至1050℃,保温22h,保温结束后,随炉降温,降温速率不超过10℃/min;大气二次时效热处理,在大气环境下,热障涂层与基材共同随炉升温至790℃,保温48h,保温结束后,随炉降温,降温速率不超过10℃/min。
35.本实施例中采用的mcralyx粉末材料为镍基多组元nicocralyx合金,成分为co:8%,cr:25%,al:14%,y:0 .1%,si:0 .5%,ta:3%,w:2%,其余为ni。
36.mcralyx粉末材料制备采用真空雾化方法完成,具体包括以下步骤:1)配料与投料:将所述nicocralyx合金所包含元素的粉末按元素含量进行配置,
并投入熔炼炉内;al、y、si原料在熔炼中间投放; 2)熔炼:控制熔炼炉环境真空度0.1pa,使用氦气作为保护性气体,将加热炉内金属材料至其完全熔化并混合均匀; 3)喷雾造粒:控制喷雾塔的真空度小于1pa,使用氩气作为保护性气体,打开与熔炼炉连接的阀门使熔液流入喷雾塔,同时采用氩气形成的高速气流将熔液吹散,形成细小的液滴,液滴在喷雾塔中快速冷却形成固态的颗粒。
37.4)收集封装:固态颗粒落入收集料罐中,得到nicocralyx合金粉末。
38.实施例2一种热障涂层的制备方法,包括以下步骤:基材预处理:选用rene n5镍基单晶高温合金作为基材,对基材进行预处理,预处理包括对基材表面进行喷砂、清洗和干燥;高致密层喷涂,采用超音速火焰喷涂方法将mcralyx粉末材料沉积在基材表面,得到厚度为100μm、粗糙度ra为6μm的高致密层,喷涂前对基材进行预热,预热温度为500℃;高粗糙度层喷涂:采用大气等离子喷涂方法将mcralyx粉末材料沉积在高致密层表面,得到厚度为150μm、粗糙度ra为10.5μm的高粗糙度层,该步骤中大气等离子喷涂方法参数为:氩气流量50 l/min,氢气流量15 l/min,电流参数为550a,喷距为140mm;陶瓷面层喷涂:采用大气等离子喷涂方法在高粗糙度层表面沉积8%氧化钇稳定氧化锆,得到陶瓷面层,该步骤中大气等离子喷涂方法参数为:氩气流量45 l/min,氢气流量20 l/min,电流参数为650a,喷距为150mm;真空一次时效处理:在真空炉内,控制真空度0.001pa,采用氦气作为气体保护,热障涂层与基材共同随炉升温至1250℃,保温10h,保温结束后,随炉降温,降温速率不超过10℃/min;大气二次时效热处理,在大气环境下,热障涂层与基材共同随炉升温至850℃,保温28h,保温结束后,随炉降温,降温速率不超过10℃/min。
39.本实施例中采用的mcralyx粉末材料为镍基多组元nicocralyx合金,成分为co:15%,cr:15%,al:10%,y:1%,hf:2%,ta:1%,w:5%,其余为ni。
40.mcralyx粉末材料制备采用真空雾化方法完成,具体包括以下步骤:1)配料与投料:将所述nicocralyx合金所包含元素的粉末按元素含量进行配置,并投入熔炼炉内;al、y、si原料在熔炼中间投放; 2)熔炼:控制熔炼炉环境真空度0.1pa,使用氦气作为保护性气体,将加热炉内金属材料至其完全熔化并混合均匀; 3)喷雾造粒:控制喷雾塔的真空度小于1pa,使用氩气作为保护性气体,打开与熔炼炉连接的阀门使熔液流入喷雾塔,同时采用氩气形成的高速气流将熔液吹散,形成细小的液滴,液滴在喷雾塔中快速冷却形成固态的颗粒。
41.4)收集封装:固态颗粒落入收集料罐中,得到nicocralyx合金粉末。
42.实施例3一种热障涂层的制备方法,包括以下步骤:基材预处理:选用rene n5镍基单晶高温合金作为基材,对基材进行预处理,预处理包括对基材表面进行喷砂、清洗和干燥;
高致密层喷涂,采用超音速火焰喷涂方法将mcralyx粉末材料沉积在基材表面,得到厚度为200μm、粗糙度ra为7.5μm的高致密层,喷涂前对基材进行预热,预热温度为800℃;高粗糙度层喷涂:采用大气等离子喷涂方法将mcralyx粉末材料沉积在高致密层表面,得到厚度为90μm、粗糙度ra为14.5μm的高粗糙度层,该步骤中大气等离子喷涂方法参数为:氩气流量65 l/min,氢气流量22 l/min,电流参数为720a,喷距为170mm;陶瓷面层喷涂:采用大气等离子喷涂方法在高粗糙度层表面沉积8%氧化钇稳定氧化锆,得到陶瓷面层,该步骤中大气等离子喷涂方法参数为:氩气流量60 l/min,氢气流量25 l/min,电流参数为750a,喷距为190mm;真空一次时效处理:在真空炉内,控制真空度0.05pa,采用氮气气体保护,热障涂层与基材共同随炉升温至1400℃,保温2h,保温结束后,随炉降温,降温速率不超过10℃/min;大气二次时效热处理,在大气环境下,热障涂层与基材共同随炉升温至1010℃,保温15h,保温结束后,随炉降温,降温速率不超过10℃/min。
43.本实施例中采用的mcralyx粉末材料为镍基多组元nicocralyx合金,成分为co:30%,cr:10%,al:8%,y:1.5%,hf:1.5%,ta:2%,w:7%,其余为ni。
44.mcralyx粉末材料制备采用真空雾化方法完成,具体包括以下步骤:1)配料与投料:将所述nicocralyx合金所包含元素的粉末按元素含量进行配置,并投入熔炼炉内;al、y、si原料在熔炼中间投放; 2)熔炼:控制熔炼炉环境真空度0.1pa,使用氦气作为保护性气体,将加热炉内金属材料至其完全熔化并混合均匀; 3)喷雾造粒:控制喷雾塔的真空度小于1pa,使用氩气作为保护性气体,打开与熔炼炉连接的阀门使熔液流入喷雾塔,同时采用氩气形成的高速气流将熔液吹散,形成细小的液滴,液滴在喷雾塔中快速冷却形成固态的颗粒。
45.4)收集封装:固态颗粒落入收集料罐中,得到nicocralyx合金粉末。
46.实施例4一种热障涂层的制备方法,按照实施例2中的方法进行,不同之处在于,本实施例中采用的mcralyx粉末材料为镍基多组元nicocralyx合金,成分为co:45%,cr:25%,al:14%,y:0 .1%,si:0 .3%,hf:0 .2%,ta:3%,ta:1%,w:2%,其余为ni。
47.实施例5一种热障涂层的制备方法,按照实施例2中的方法进行,不同之处在于,mcralyx粉末材料中al含量为10.5%。
48.实施例6一种热障涂层的制备方法,按照实施例2中的方法进行,不同之处在于,mcralyx粉末材料中al含量为14%。
49.实施例7一种热障涂层的制备方法,按照实施例2中的方法进行,不同之处在于,mcralyx粉末材料中未添加ta,且w的添加含量为6%。
50.实施例8一种热障涂层的制备方法,按照实施例2中的方法进行,不同之处在于,mcralyx粉
末材料中未添加w,且ta的添加含量为6%。
51.实施例9一种热障涂层的制备方法,按照实施例2中的方法进行,不同之处在于,mcralyx粉末材料中未添加ta和w。
52.实施例10一种热障涂层的制备方法,按照实施例2中的方法进行,不同之处在于,高粗糙度层的表面粗糙度ra为15.5μm。
53.实施例11一种热障涂层的制备方法,按照实施例2中的方法进行,不同之处在于,二次时效热处理在真空环境下进行,在真空炉内,控制真空度0.001pa,采用氦气作为气体保护。
54.对比例1一种热障涂层的制备方法,按照实施例2中的方法进行,不同之处在于,未进行高粗糙度喷涂步骤,高致密层喷涂厚度为250μm,且高致密层喷涂步骤操作后直接进行陶瓷面层喷涂步骤。
55.对比例2一种热障涂层的制备方法,按照实施例2中的方法进行,不同之处在于,未进行高致密层喷涂步骤,基材预处理后直接进行高粗糙度层喷涂步骤,且高粗糙度层喷涂厚度为250μm。
56.对比例3一种热障涂层的制备方法,按照实施例2中的方法进行,不同之处在于,mcralyx粉末材料中al元素含量为7%。
57.对比例4一种热障涂层的制备方法,按照实施例2中的方法进行,不同之处在于,高粗糙度层喷涂采用超音速火焰喷涂方法(hvaf),得到高粗糙度层的表面粗糙度ra为6.5μm。
58.对比例5一种热障涂层的制备方法,按照实施例2中的方法进行,不同之处在于,高粗糙度层喷涂采用低压等离子喷涂方法(lpps)。
59.性能检测1、陶瓷面层与粘结层结合性能检测采用热震试验评价热障涂层的1150℃热震性能,且采用空冷热震方法,具体的:将上述实施例1-11和对比例1-4中的热障涂层在3min内升温至1150℃,保温5min后在室温空气气流的冲击下迅速冷却,1min内风冷至50℃,检测热障涂层在1150℃下的热震寿命,检测结果如下表1所示。
60.表1:
检测项目实施例1实施例2实施例3实施例4实施例5实施例6实施例7实施例8热震寿命/次851908870895923987811892检测项目实施例9实施例10实施例11对比例1对比例2对比例3对比例4—热震寿命/次788605722152654206220—
通过上表1,可知,采用本技术中的制备方法得到的热障涂层相较于对比例1中仅
仅只有高致密层直接作为粘结层得到的热障涂层在1150℃下的热震寿命从150次以下提成至900次及以上。
61.参照本技术实施例2与实施例5-6的检测结果,可以看出,随着al含量占比的增大,最终得到涂层的热震寿命更长,再结合对比例3的检测结果,可以看出,对比例3中al含量过低的时候,得到的热障涂层的热震寿命较低。
62.再结合本技术实施例2与实施例7-9的检测结果,可以看出,ta和w的添加可以提升其热震寿命,而且本技术实施例1中同时添加w和ta与仅添加ta时性能相当,但是w的成本低于ta,本技术中w的添加在达到具有优异热震性能的同时成本更低。
63.再参照实施例2与实施例10的检测结果,可知,实施例10中表面粗糙度太高的时候,涂层表面有较多的喷涂缺陷(表面有未熔颗粒,孔隙较大),最终涂层结合性能有所降低,热震寿命为600次左右。
64.而对比例4和对比例5中分别采用超音速火焰喷涂方法(hvaf)或低压等离子喷涂方法(lpps)喷涂时,得到高粗糙度层的粗糙度为3.5-6.5μm,无法达到7.5-14.6μm表面粗糙度,尤其是采用超音速火焰喷涂方法时,其表面粗糙度也仅能达到6.5左右,无法达到7.5,而低压等离子喷涂方法喷涂得到的高粗糙度层的表面粗糙度更低,仅为3左右。再结合对比例4的检测结果,可以看出,对比例4中高粗糙度层的表面粗糙度过低的时候,粘结层与陶瓷面层的结合性能弱,热震寿命仅仅只有200次左右。
65.参照实施例2与实施例11中的检测结果,实施例2中采用大气二次时效处理,实施例11中采用真空二次时效处理,可以看出,相较于二次时效处理在真空环境下进行,本技术中采用低温大气热处理,使得粘结层表面有氧参与,粘结层表面组织有序化,形成致密连续的α-al2o3薄膜。最终实施例2中得到的热障涂层不仅可以达到1150℃完全抗氧化级,抗氧化性能更优,而且实施例2中的热震寿命更长,而实施例11中的涂层仅仅只能达到1150℃抗氧化级,而且热震寿命有所降低。
66.再参照本技术实施例2与对比例1和对比例2的检测结果,可以看出,对比例1中仅喷涂形成高致密层的时候,其热震寿命为150次左右,粘结层与陶瓷面层结合性弱,而对比例2中仅喷涂形成高粗糙度层的时候,形成的α-al2o3不致密,易氧化,其仅仅只能达到1150℃抗氧化级。
67.2、力学性能检测首先对本技术实施例和对比例中的rene n5镍基单晶高温合金基材进行基材抗拉强度的检测,其抗拉强度为1100左右,为了排除陶瓷面层对于力学性能的影响,将上述rene n5镍基单晶高温合金基材按照本技术实施例和对比例中的方法依次喷涂高致密层和高粗糙度层后直接进行一次时效和二次时效热处理,然后在1150℃下服役100h后进行基材+粘结层材料的抗拉强度进行检测,检测结果如下表2所示。
68.表2:检测项目实施例1实施例2实施例3实施例4实施例5实施例6抗拉强度/mpa100810251020101810421058检测项目实施例7实施例8实施例9实施例11对比例1对比例2抗拉强度/mpa101010269681018 1012880由上表2可以看出,基材抗拉强度为1100mpa左右,采用本技术实施例2中方法形成
阻扩散区,对复合材料进行抗拉强度的检测,其抗拉强度随有所损失,但是仍然在1000mpa以上。
69.另外,对本技术实施例2中经过大气二次时效处理后的热障涂层进行微观结构的观察如图1所示,可以观察到材料经过长期氧化后,经过本技术处理后得到的粘结层与基材界面处生成阻扩散区,阻扩散区内含有大量密排原位生成的β相。同理,对对比例3中的热障涂层进行微观结构观察如图2所示,可以观察到材料经过长期氧化后,采用对比例3中al含量低的mcralyx粉末材料喷涂得到的粘结层与基材界面处未生成β相。
70.参照本技术实施例2与实施例5-6的检测结果,可以看出,随着al含量占比的增大,可能是由于生成阻扩散区内β相含量更高,经过处理基材力学损失更低。
71.再结合本技术实施例2与实施例7-9的检测结果,可以看出,ta和w的添加可以提升其抗拉强度,而且本技术实施例1中同时添加w和ta与仅添加ta时性能相当,但是w的成本低于ta,本技术中w的添加在达到具有优异力学性能的同时成本更低。
72.再参照实施例2与对比例2中的检测结果,可以看出,仅仅喷涂高粗糙度层作为粘结层的时候,热障涂层的力学性能较小,力学性能损失较大。
73.综上,可以看出,本技术中以高致密层和高粗糙度形成粘结层,高致密层与基材之间形成阻扩散区,可以改善高致密层与基材之间的性能,尤其是al含量提高的设置以及x元素的添加,可以进一步改善形成β相的数量和分布,进而获得更好的性能;高粗糙度层的设置可以增强粘结层与陶瓷面层的强结合性能,改善高粗糙度层与粘结层之间的性能,尤其是表面粗糙度的控制,可以进一步提高其结合强度,而且大气环境下的二次时效热处理使得mcralyx粘结层表面组织有序化,生成致密连续的α-al2o3薄膜,得到抗氧化性能更好的热障涂层,而且粘结层与陶瓷面层之间的结合性能更优,最终实现双界面性能强化。
74.本具体实施例仅仅是对本技术的解释,其并不是对本技术的限制,本领域技术人员在阅读完本说明书后可以根据需要对本实施例做出没有创造性贡献的修改,但只要在本技术的权利要求范围内都受到专利法的保护。