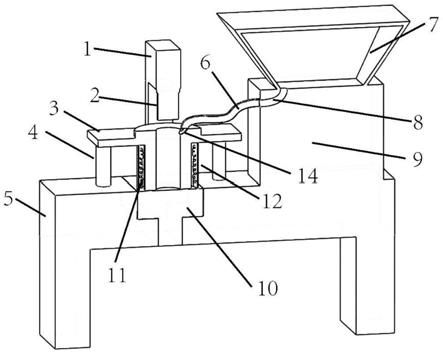
1.本发明设计双金属复合材料的制备技术领域,具体涉及一种固-液复合铸造的双金属材料的制备装置及制备方法。
背景技术:2.随着国家高新技术的不断发展,对于材料的性能要求越发的严格,单一材料的性能目前已难以满足某些领域的要求,因此双金属复合材料已是近年来的研究热点。双金属复合材料兼具了两种金属材料的优良性能,弥补了单一金属材料在使用性能上的不足,具有着独特的“相补效应”,可以改善单一材料由于个别性能缺陷所致应用领域受限的应用现状。
3.对于双金属复合材料的制备,目前存在的制备技术主要有固-固复合,固-液复合和液-液复合三大类。这些技术方法普遍存在生产成本高、效率低、界面粘结强度不均等问题。目前国内对于双金属复合材料的制备主要采用轧制复合技术,但这种方法界面结合强度相对较低,所制备产品性能满足航空航天等尖端领域的要求;国外双金属复合材料的生产主要以美国诺威力公司自主研发的诺威力复合法为主,该方法解决了双金属复合材料界面结合强度相对较低的状况,但双金属复合材料产品制备的成本过高,仅制备过程中温度变量的控制就花费上亿美圆。
技术实现要素:4.针对上述技术问题,本发明提供了一种双金属复合材料的制备装置。
5.本发明采用下述技术方案:
6.一种双金属复合材料的制备装置,该装置包括加压系统、液态金属加热系统、固态金属预热系统、控制系统和压力模腔固定板、压力模腔固定柱、装置基台、可移动压力模腔底座、液态金属导流槽a、液态金属导流槽b、液态金属导流管。
7.其中加压系统包括压力机主体,压力冲头;液态金属加热系统包括液态金属保温室,液态金属加热底座;固态金属预热系统包括固态金属预热模腔,加热电阻。
8.压力机主体位于装置基台上;压力冲头安装于压力机主体顶端,并且与固态金属预热模腔同轴心;液态金属加热底座位于装置基台上方;液态金属保温室位于液态金属加热底座上方;液态金属导流槽a位于液态金属保温室正下方,位于液态金属加热底座内部;液态金属导流槽b位于固态金属预热模腔内部,液态金属导流槽b的两端口分别与固态金属预热模腔上表面和内腔壁相切;压力模固定板与固态金属预热模腔固定在一起;压力模腔固定柱分别位于压力模腔固定板的四周并与之固定,压力模腔固定柱下端与装置基台固定;加热电阻位于固态金属预热模腔外腔;液态金属导流管两端口分别与液态金属导流槽a和液态金属导流槽b相连接;可移动压力模腔底座位于固态金属预热模腔正下方;控制系统放置于装置基台外表面上。
9.采用上述装置制备双金属复合材料的方法如下:
10.步骤一:通过控制系统调节液态金属加热底座加热,使液态金属保温室内液态金属熔化并在一定温度内保温;
11.步骤二:将固态金属放入固态金属预热模腔之中,通过控制系统使固态金属模腔内加热电阻加热,并设置保温温度;
12.步骤三:待液态金属保温室内液态金属和固态金属预热膜腔内固态金属均达到预定制备温度时,通过控制系统调节液态金属导流槽a和液态金属导流槽b为开放状态,使得液态金属经液态金属导流管均匀浇注在固态金属表面。与此同时,通过控制系统调节压力冲头向下压入固态金属预热模腔,待达到设定压力后停止下压并保压;
13.步骤四:待保压结束后,通过控制系统调节压力冲头退出固态金属预热模腔;
14.步骤五:通过控制系统调节可移动压力模腔底座,使固态金属预热模下端处于无底座状态;
15.步骤六:通过控制系统再次调节压力冲头,使压力冲头将双金属复合材料从固态金属预热膜腔中顶出,实现脱模。
16.步骤七:通过控制系统将可移动压力模腔底座调回初始位置,并将其他系统关闭,双金属复合材料制备完成。
17.本发明相对现有技术,具有如下优点及效果:
18.本发明采用固-液复合铸造制备双金属复合材料,在双金属复合材料铸造完成后通过压力系统对双金属复合材料进行加压并保压,有效的进一步提高了双金属复合材料的界面结合强度;采用多系统协同进行的铸造方式,使得双金属复合材料的制备更高效、更简便易操作,减少了材料制备过程中的安全隐患;采用可移动式压力模腔底座结构,与压力系统协同作用,实现了双金属复合材料快速脱模,提高了生产效率。
附图说明
19.图1为发明装置的整体机械结构图。
20.图2为发明装置的剖面机械结构图。
21.图3为实施例1的扫描电镜图。
22.图4为实施例2的扫描电镜图。
具体实施方式
23.下面结合具体实施例对本发明做进一步详细描述。
24.在本发明的描述中,需要理解的是,术语“外侧”、“内侧”、“前端”、“顶部”、“上部”、“左”、“右”、“中间”、“周围”等指示的方位或位置关系为基于附图所示的方位或位置关系,仅是为了便于描述本发明和简化描述,而不是指示或暗示所指的装置或元件必须具有特定的方位、以特定的方位构造和操作,因此不能理解为对本发明的限制。在本发明的描述中,“多个”的含义是两个或两个以上,除非另有明确具体的限定。本发明描述中,术语“安装”、“固定”等术语应做广义理解,例如,可以是固定连接,也可以是可拆卸连接,或一体地连接。对于本领域的普通技术人员而言,可以根据具体情况理解上述术语在本发明中的具体含义。
25.实施例1
26.如图1,图2所示,本发明公开了一种双金属复合材料的制备装置,该装置由加压系统、液态金属加热系统、固态金属预热系统和控制系统四个部分构成。其中加压系统主要有压力机主体1,压力冲头2;液态金属加热系统主要有液态金属保温室7,液态金属加热底座9;固态金属预热系统主要有固态金属预热模腔12,加热电阻11。此装置还包括控制系统13、压力模腔固定板3、压力模腔固定柱4、装置基台5、可移动压力模腔底座10、液态金属导流槽a 8、液态金属导流槽b 14、液态金属导流管6。
27.压力机主体位于装置基台5上;压力冲头2安装于压力机主体1顶端,并且与固态金属预热模腔12同轴心;液态金属加热底座9位于装置基台5上方;液态金属保温室7位于液态金属加热底座9上方;液态金属导流槽a 8位于液态金属保温室7正下方,处于液态金属加热底座9内部;液态金属导流槽b 14位于固态金属预热模腔12内部,液态金属导流槽b的端口分别与固态金属预热模腔12上表面和内腔壁相切;压力模固定板3与固态金属预热模腔12固定在一起;压力模腔固定柱4分别位于压力模腔固定板12的四周并与之固定,而且其下端与装置基台5固定;加热电阻11位于固态金属预热模腔12外腔;液态金属导流管6两端口分别于液态金属导流槽a 8和液态金属导流槽b 14相连接;可移动压力模腔底座10位于固态金属预热模腔12正下方;控制系统13放置于装置基台5外表面上。
28.采用上述装置制备7075/6061铝合金双金属复合材料的方法通过下述步骤实现:
29.步骤一:通过控制系统13调节液态金属加热底座9加热,使液态金属保温室7内6061铝合金熔化并在720℃保温;
30.步骤二:将7075铝合金基板放入固态金属压力模腔12之中,通过控制系统13使固态金属模腔12内加热电阻11加热,并设置保温温度为450℃;
31.步骤三:待液态金属保温室7内6061铝合金和固态金属预热膜腔12内7075铝合金基板均达到预定制备温度时,通过控制系统13调节液态金属导流槽a 8和液态金属导流槽b 14为开放状态,使得6061铝合金金属液经液态金属导流管6均匀浇注在7075铝合金基板表面,控制6061铝合金金属液浇入量为7075铝合金基板体积的四分之一。与此同时,通过控制系统13调节压力冲头2向下压入固态金属预热模腔12,待压力达到60mpa时停止加压并保压5分钟;
32.步骤四:待保压结束后,通过控制系统12调节压力冲头2退出固态金属预热模腔12;
33.步骤五:通过控制系统12调节可移动压力模腔底座10,使固态金属预热模12下端处于无底座状态;
34.步骤六:通过控制系统12再次调节压力冲头2,使压力冲头2将7075/6061铝合金双金属复合材料从固态金属预热膜腔12中顶出,实现脱模。
35.步骤七:通过控制系统12将可移动压力模腔底座10调回初始位置,并将其他系统关闭,7075/6061铝合金双金属复合材料制备完成。
36.将所得材料在扫描电镜下进行组织观察,发现复合材料界面结合良好,无明显缺陷其结果如图3所示。
37.实施例2
38.如图1,图2所示,本发明公开了一种双金属复合材料的制备装置,该装置由加压系统、液态金属加热系统、固态金属预热系统和控制系统四个部分构成。其中加压系统主要有
压力机主体1,压力冲头2;液态金属加热系统主要有液态金属保温室7,液态金属加热底座9;固态金属预热系统主要有固态金属预热模腔12,加热电阻11。此装置还包括控制系统13、压力模腔固定板3、压力模腔固定柱4、装置基台5、可移动压力模腔底座10、液态金属导流槽a 8、液态金属导流槽b 14、液态金属导流管6。
39.压力机主体位于装置基台5上;压力冲头2安装于压力机主体1顶端,并且与固态金属预热模腔12同轴心;液态金属加热底座9位于装置基台5上方;液态金属保温室7位于液态金属加热底座9上方;液态金属导流槽a 8位于液态金属保温室7正下方,处于液态金属加热底座9内部;液态金属导流槽b 14位于固态金属预热模腔12内部,液态金属导流槽b 14两端口分别与固态金属预热模腔12上表面和内腔壁相切;压力模固定板3与固态金属预热模腔12固定在一起;压力模腔固定柱4分别位于压力模腔固定板12的四周并与之固定,而且其下端与装置基台5固定;加热电阻11位于固态金属预热模腔12外腔;液态金属导流管6两端口分别于液态金属导流槽a 8和液态金属导流槽b 14相连接;可移动压力模腔底座10位于固态金属预热模腔12正下方;控制系统13放置于装置基台5外表面上。
40.采用上述装置制备al/cu双金属复合材料的方法通过下述步骤实现:
41.步骤一:通过控制系统13调节液态金属加热底座9加热,使液态金属保温室7内纯铝熔化并在700℃保温;
42.步骤二:将纯铜基板放入固态金属压力模腔12之中,通过控制系统13使固态金属模腔12内加热电阻11加热,并设置保温温度为400℃;
43.步骤三:待液态金属保温室7内纯铝和固态金属预热膜腔12内纯铜基板均达到预定制备温度时,通过控制系统13调节液态金属导流槽a 8和液态金属导流槽b 14为开放状态,使得纯铝金属液经液态金属导流管6均匀浇注在纯铜基板表面,控制纯铝金属液浇入量为纯铜基板体积的四分之一。与此同时,通过控制系统13调节压力冲头2向下压入固态金属预热模腔12,待压力达到55mpa时停止加压并保压6分钟;
44.步骤四:待保压结束后,通过控制系统12调节压力冲头2退出固态金属预热模腔12;
45.步骤五:通过控制系统12调节可移动压力模腔底座10,使固态金属预热模12下端处于无底座状态;
46.步骤六:通过控制系统12再次调节压力冲头2,使压力冲头2将al/cu双金属复合材料从固态金属预热膜腔12中顶出,实现脱模。
47.步骤七:通过控制系统12将可移动压力模腔底座10调回初始位置,并将其他系统关闭,al/cu双金属复合材料制备完成。
48.将所得材料在扫描电镜下进行组织观察,发现复合材料界面结合良好,无明显缺陷,其结果如图4所示。
49.将上述实例中制备的双金属复合材料进行剪切强度测试,采用型号为gb/t228-2010金属材料室温拉伸试验机进行测试,其中拉伸速率为1mm/min,测试结果如表1所示。
50.表1不同实施例的极限剪切强度
51.名称极限剪切强度(mpa)实施例182实施例264
52.将上述实例中制备的双金属复合材料进行显微硬度测试,采用型号为fm-ars900的全自动显微硬度仪进行测试,其中试验载荷重为100g,持续时间为15s,测量结果如表2所示,其中如上所示实验数据须进行测量7次且取平均值将最后的平均值作为最后的实验值。可见采用本装置制备的复合材料硬度有明显的提升。
53.表2不同实施例的显微硬度
[0054][0055][0056]
如上所述实施例可知,采用本发明的装置可以制备出界面结合强度良好的双金属复合材料。
[0057]
本发明的实施方式并不受上述实施例的限制其他任何未背离本发明的精神实质与原理下所作的改变、修饰、替代、组合、简化均应为等效的置换方式都包含在本发明的保护范围之内。