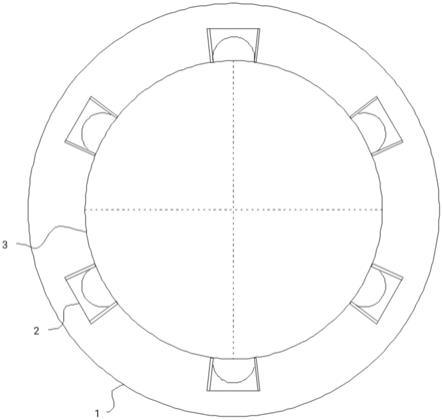
1.本实用新型涉及小颗粒物体磨削领域,更具体地说,涉及一种用于小颗粒物体表面磨削的磨削结构。
背景技术:2.对于小颗粒物体(谷类、豆类、坚果类等种子的小颗粒物体的表面研磨和清洁木材、塑料、矿物或金属等的粒料)的研磨结构通常壳体、驱动结构、转筒、辊筒、处理腔室(相当于本实用新型中的导料室)、待研磨物的入口部、研磨后的小颗粒物体的出口部等;研磨时,驱动结构驱动转筒和辊筒转动,在辊筒的转动作用下,小颗粒物体沿着处理腔室的可预测路径环行,使得小颗粒物体重复地接触辊筒以去掉物品的外层。
3.参阅图4,现有技术中的处理腔室为矩形结构,进而小颗粒物体的可预测路径为矩形。因矩形结构左壁和右壁平行,当右壁与辊筒或砂带的圆弧面相交,这时右壁与辊筒或砂带圆弧切线相交测得夹角84
°
。由于角度小于90
°
,使得小颗粒物体在腔室的右上角,形成较大的死角,又因为辊筒或砂带向右方转动,这样就造成小颗粒物因流动不畅而造成损耗,这种损耗是前赴后继式的,只要辊筒或砂带继续向右转动,这损耗就不停止。矩形结构左壁与辊筒或砂带圆弧切线相交夹角84
°
,因为辊筒或砂带向右转动会导致处理腔室内的空间没有被充分利用,造成浪费,小颗粒物体可能不经过拐角处而直接被导入。
4.参阅图5,现有技术中为解决小颗粒物体被磨削下的外层与被磨削后的小颗粒物体分离的问题,在处理腔室的其中一个开口部留出了可供小颗粒物体外层与小颗粒物体分离的通道。实际上因辊筒或砂带上粘满了砂粒,假设砂粒是三角形,那么它们在辊筒或砂带上的排列是一个个小的三角形且尖锐角放射向外,因此也就存在反向的三角形空隙图5,因此开口不设也可。主要是在制造工艺装备上的不足造成零部件质量的一致性难控制和旋轴件跳动,无奈设置这个开口。应尽可能装配后通过自身磨削左壁或右壁来获得更高的精度。
技术实现要素:5.1.要解决的技术问题
6.针对现有技术中存在的问题,本实用新型的目的在于提供一种用于小颗粒物体表面磨削的磨削结构,它可以实现小颗粒物体被导入或导出导料室工作区的过程中,减少能量损耗,减少颗粒物的损耗,同时导料室内空间能够被充分利用。
7.2.技术方案
8.为解决上述问题,本实用新型采用如下的技术方案。
9.一种用于小颗粒物体表面磨削的磨削结构,包括辊筒、导料室和壳体;
10.辊筒设于壳体内,且辊筒与壳体同轴;
11.导料室设于辊筒的外圆周面上;
12.导料室的数量为至少一个,导料室的开口端与辊筒相邻;
13.导料室包括外导料部和内导料部;
14.外导料部包括左挡板和右挡板;左挡板固定连接在内导料部的左端;右挡板固定连接在内导料部的右端;
15.内导料部的俯视图形为上底小下底大的等腰梯形,且两腰夹角为10
‑
15
°
;
16.内导料部开口朝向辊筒;
17.导料室的俯视图形的端部与辊筒的俯视图形之间具有两个相交点,相交点处辊筒的外圆周面切线与导料室的端部延长线之间的夹角大于90
°
;
18.内导料部可使小颗粒物体无滞留的被导入和导出工作面。
19.进一步的,内导料部上具有第二导料段;第二导料段的俯视图形为弯曲状,使小颗粒物体进入内导料部内被辊筒磨削时不易存在磨削死角;左挡板的右上部为第一导料段;右挡板的左上部为第三导料段;第二导料段、第一导料段和第三导料段组成小颗粒物体的磨削工作面;小颗粒物体经第一导料段导入工作面磨削,在辊筒的转动作用带动下向右运动到第三导料段被导出工作面。
20.进一步的,第一导料段与第二导料段以及第二导料段与第三导料段之间平滑连接,使第一导料段与第二导料段之间的衔接处以及第二导料段与第三导料段之间的衔接处不易有小颗粒物体卡住,进而使得小颗粒物体的流动顺畅。
21.进一步的,辊筒的俯视图形中与导料室两个相交点之间的圆弧段的弧线长为65
‑
70mm,两个相交点即为辊筒的俯视图形中与第一导料段的相交点以及辊筒的俯视图形中与第三导料段的相交点。
22.3.有益效果
23.相比于现有技术,本实用新型的优点在于:
24.(一)本方案可以实现小颗粒物体被导入或导出导料室加工区的过程中,不易出现卡顿的情况,减少能量损耗,减少物料损耗,同时导料室内空间能够被充分利用,减少空间的浪费。
25.(二)第一导料段与第二导料段以及第二导料段与第三导料段之间一体平滑连接,使第一导料段与第二导料段之间的衔接处不易有小颗粒物体卡住,进而使得小颗粒物体的流动顺畅。
附图说明
26.图1为本实用新型的俯视结构示意图;
27.图2为本实用新型的辊筒和导料室部分的结构示意图;
28.图3为本实用新型的导料室部分的结构示意图;
29.图4为现有技术中的辊筒和导料室部分的结构示意图;
30.图5为现有技术中的辊筒上粘有三角形砂粒时的结构示意图。
31.图中标号说明:
32.1辊筒;
33.2导料室、2
‑
1左挡板、2
‑
2内导料部、2
‑2‑
1第一导料段、2
‑2‑
2第二导料段、2
‑2‑
3第三导料段、2
‑
3右挡板;
34.3壳体。
具体实施方式
35.请参阅图1
‑
3的一种用于小颗粒物体表面磨削的磨削结构,它一种用于小颗粒物体表面磨削的磨削结构,包括辊筒1、导料室2和壳体3。
36.辊筒1设于壳体3内,且辊筒1与壳体3同轴,壳体3和辊筒1都为圆柱形结构。
37.辊筒1由驱动结构驱动转动,例如旋转电机(未图示)。
38.辊筒1的外圆周面上电镀上金刚砂轮或胶粘上陶瓷砂粒。
39.导料室2设于辊筒1的外圆周面上,导料室2为长度方向布置在辊筒1外径周围且辊筒1只能按垂直方向布置。
40.导料室2的数量为至少一个,当导料室2的数量为多个时,多个导料室2呈圆周状间隔分布在辊筒1外侧。
41.导料室2包括外导料部和内导料部2
‑
2。
42.外导料部包括左挡板2
‑
1和右挡板2
‑
3;左挡板2
‑
1固定连接在内导料部2
‑
2的左端;右挡板2
‑
3固定连接在内导料部2
‑
2的右端。
43.内导料部2
‑
2的俯视图形为上底小下底大的等腰梯形,且两腰夹角为10
‑
15
°
,具体可为10
°
。
44.内导料部2
‑
2开口朝向辊筒1。
45.导料室2的俯视图形的端部与辊筒1的俯视图形之间具有两个相交点,相交点处辊筒1的外圆周面切线与导料室2的端部延长线之间的夹角大于90
°
,相比于现有技术中的矩形结构的夹角大了至少6
°
。
46.内导料部2
‑
2可使小颗粒物体无滞留的被导入和导出工作面。
47.左挡板2
‑
1、内导料部2
‑
2、右挡板2
‑
3和辊筒1外圆周面之间形成的区域为工作面,具体为第一导料段2
‑2‑
1、第二导料段2
‑2‑
2、第三导料段2
‑2‑
3和辊筒1外圆周面之间形成的区域。
48.内导料部2
‑
2上具有第二导料段2
‑2‑
2;第二导料段2
‑2‑
2的俯视图形为弯曲状,使小颗粒物体进入内导料部2
‑
2内被辊筒1研磨时不易存在研磨死角;左挡板2
‑
1的右上部为第一导料段2
‑2‑
1;右挡板2
‑
3的左上部为第三导料段2
‑2‑
3;第二导料段2
‑2‑
2、第一导料段2
‑2‑
1和第三导料段2
‑2‑
3组成小颗粒物体的磨削工作面;小颗粒物体经第一导料段2
‑2‑
1导入工作面磨削,在辊筒1的转动作用带动下向右运动到第三导料段2
‑2‑
3被导出工作面。
49.第一导料段2
‑2‑
1与第二导料段2
‑2‑
2以及第二导料段2
‑2‑
2与第三导料段2
‑2‑
3之间平滑连接,使第一导料段2
‑2‑
1与第二导料段2
‑2‑
2之间的衔接处以及第二导料段2
‑2‑
2与第三导料段2
‑2‑
3之间的连接处不易有小颗粒物体卡住,进而使得小颗粒物体的流动顺畅。
50.辊筒1的俯视图形中与导料室2两个相交点之间的圆弧段的弧线长为65
‑
70mm,两个相交点即为辊筒1的俯视图形中与第一导料段2
‑2‑
1的相交点以及辊筒1的俯视图形中与第三导料段2
‑2‑
3的相交点。
51.小颗粒物体送入内导料部2
‑
2内,同时辊筒1由驱动结构带动转动,辊筒1转动过程中驱动小颗粒物体沿内导料部2
‑
2的可预测路径流动。
52.可以实现小颗粒物体被导入或导出导料室2的过程中,不易出现卡顿的情况,减少能量损耗,同时导料室2内空间能够被充分利用,减少空间的浪费。