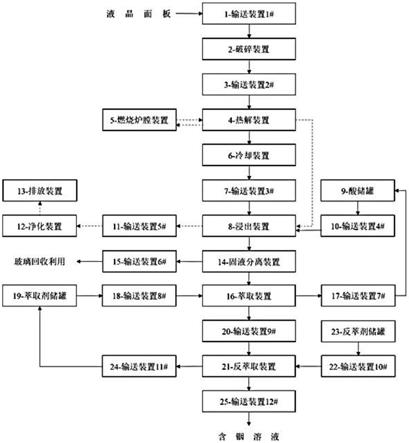
1.本实用新型涉及电子废弃物无害化处理领域,尤其是一种液晶面板萃取回收铟的装置。
背景技术:2.随着生活水平的提高,智能化技术需求越来越大,液晶电视、电脑显示器、手机、投影仪、导航仪等产品皆采用液晶显示元件。液晶显示元件一般使用寿命为5~8年,已经成为我国电子垃圾处理的主要对象。废弃的液晶面板中的铟含量高,铟毒性比铅还要大,毒性不可轻视,会对环境及人类的健康造成严重威胁。另一方面,由于目前铟原料短缺,价格昂贵,研究液晶面板无害化处理时回收铟对合理利用资源和保护资源有着重要意义。
3.专利申请cn101722169a公开了将含有液晶的玻璃面板破碎后在氮气条件下进行加热分解处理并将分解气体高温燃烧处理后排放,该方法仅涉及液晶面板的无害化处理,不涉及贵金属回收工艺。
4.专利申请cn101133172a提供了一种从废弃液晶显示器中铟的回收方法及其装置,利用酸直接溶解液晶面板中的铟,生成含铟溶液后,利用锌或铝颗粒(0.1-8mm)进行置换,再利用超声波振荡等方式将铟从金属表面剥离,最后通过添加碱去除其它金属杂质后回收铟,整体工艺复杂且不易控制。
5.鉴于目前液晶面板处理的局限,开发先进的液晶面板无害化处理工艺及系统,对资源回收利用、保障人民健康和生态安全等具有重要意义。
技术实现要素:6.本实用新型的目的是为了克服现有的液晶面板回收铟中存在的不足,提供一种液晶面板萃取回收铟的装置。
7.发明人前期研究液晶面板无害化处理,采用的方法参见cn104498721a,其中采用丙酮浸泡的方式操作反锁、时间长,且萃取和反萃取效果有限。经过不断摸索,发明人发现,采用特定条件下的加热处理,可以使液晶面板中的偏光膜与玻璃面板分离,而附着在玻璃面板的铟暴露出来,可以快速实现酸性浸出,从而提出了新的液晶面板萃取回收铟的装置。
8.该装置主要包括绝氧热解、萃取和反萃取等几个工序段。现有的液晶面板回收技术中,通常采用有机溶剂如丙酮对液晶面板进行浸泡,目的是利用丙酮将液晶面板中危废液晶浸出,然后通过蒸馏的方法进行无害化处理,步骤繁琐,成本高。但是,实用新型人反复试验发现,通过绝氧热解的条件,使得液晶显示屏表面的偏光膜、液晶等有机废弃物彻底与显示屏分离,通过热解的方式使其转化为可燃气用于液晶面板热解,从而快速实现液晶面板的无害化处理;再在酸性条件下,使铟高效地进入溶液中,得到富集铟的浸泡液,利用萃取剂和反萃取条件下得到含铟的溶液可直接作为化工原料,也可以经过锌片或铝片置换处理后可得到铟,实现资源回收。
9.具体方案如下:
10.一种液晶面板萃取回收铟的装置,包括:
11.输送装置1#(1)、破碎装置(2)、输送装置2#(3)、热解装置(4)、燃烧炉膛装置(5)、冷却装置(6)、输送装置3#(7)、浸出装置(8)、酸储罐(9)、输送装置4#(10)、输送装置5#(11)、净化装置(12)、排放装置(13)、固液分离装置(14)、输送装置6#(15)、萃取装置(16)、输送装置7#(17)、输送装置8#(18)、萃取剂储罐(19)、输送装置9#(20)、反萃取装置(21)、输送装置10#(22)、反萃取储罐(23)、输送装置11#(24)和输送装置12#(25),
12.其中,所述输送装置1#(1)出口与所述破碎装置(2)入口相连,所述破碎装置(2)出口与所述输送装置2#(3)入口相连,所述输送装置2#(3)出口与所述热解装置(4)入口相连,所述热解装置(4)出口与所述燃烧炉膛装置(5)、冷却装置(6)和浸出装置(8)入口相连,所述燃烧炉膛装置(5)出口与所述热解装置(4)入口相连,所述冷却装置(6)出口与所述输送装置3#(7)入口相连,所述输送装置3#(7)出口与所述浸出装置(8)入口相连,所述酸储罐(9)出口与所述输送装置4#(10)入口相连,所述输送装置4#(10)出口与所述浸出装置(8)入口相连,所述浸出装置(8)出口与所述输送装置5#(11)和固液分离装置(14)入口相连,所述输送装置5#(11)出口与所述净化装置(12)入口相连,所述净化装置(12)出口与所述排放装置(13)入口相连,所述固液分离装置(14)出口与所述输送装置6#(15)和萃取装置(16)入口相连,所述萃取装置(16)出口与所述输送装置7#(17)和输送装置9#(20)入口相连,所述输送装置7#(17)出口与所述酸储罐(9)入口相连,所述输送装置9#(20)出口与所述反萃取装置(21)入口相连,所述反萃取储罐(23)出口与所述输送装置10#(22)入口相连,所述输送装置10#(22)出口与所述反萃取装置(21)入口相连,所述反萃取装置(21)出口与所述输送装置11#(24)和输送装置12#(25)入口相连,所述输送装置11#(24)出口与所述萃取剂储罐(19)入口相连,所述萃取剂储罐(19)出口与所述输送装置8#(18)入口相连,所述输送装置8#(18)出口与萃取装置(16)入口相连。
13.进一步的,所述输送装置1#(1)为铲车;所述破碎装置(2)为剪切式破碎机。
14.进一步的,所述输送装置2#(3)、输送装置3#(7)或输送装置6#(15)为螺旋输送机、皮带输送机、斜溜槽或刮板输送机。
15.进一步的,所述热解装置(4)为间接加热式滚筒热解炉。
16.进一步的,所述冷却装置(6)为间接滚筒冷却装置;
17.所述浸出装置(8)、萃取装置(16)或反萃取装置(21)为带电磁搅拌或超声波搅拌的不锈钢罐;
18.所述酸储罐(9)、萃取剂储罐(19)或反萃取储罐(23)为不锈钢罐。
19.进一步的,所述输送装置4#(10)、输送装置7#(17)、输送装置8#(18)、输送装置9#(20)、输送装置10#(22)、输送装置11#(24)或输送装置12#(25)为液体泵。
20.进一步的,所述输送装置5#(11)为风机。
21.进一步的,所述净化装置(12)为湿法或干法烟气净化装置。
22.进一步的,所述排放装置(13)为混凝土质烟囱或钢质烟囱。
23.进一步的,所述固液分离装置(14)为真空带式抽滤机、带式压滤机或板框压滤机。
24.有益效果:
25.(1)本实用新型所述装置在实现液晶面板中液晶与偏光膜快速热解无害化处理的同时,达到回收金属铟的目的,具有环保意义和经济价值;
26.(2)本实用新型所属装置回收铟的工艺流程简捷,操作简单,自动化程度高,成本低,经济效益良好;
27.(3)本实用新型所述装置处理过程干净整洁,不产生二次污染,为液晶面板实现完全资源化利用提供了新方案,环境效益显著。
28.总之,本实用新型开发液晶面板热解耦合萃取回收铟的装置,回收效率高,得到含铟的纯净溶液,可极大改善目前铟的回收技术。
附图说明
29.为了更清楚地说明本实用新型的技术方案,下面将对附图作简单的介绍,显而易见地,下面描述中的附图仅仅涉及本实用新型的一些实施例,而非对本实用新型的限制。
30.图1是本实用新型一个实施例提供的液晶面板萃取回收铟的装置结构示意图。
具体实施方式
31.下面将更详细地描述本实用新型的优选实施方式。虽然以下描述了本实用新型的优选实施方式,然而应该理解,可以以各种形式实现本实用新型而不应被这里阐述的实施方式所限制。实施例中未注明具体技术或条件者,按照本领域内的文献所描述的技术或条件或者按照产品说明书进行。所用试剂或仪器未注明生产厂商者,均为可以通过市购获得的常规产品。在下面的实施例中,如未明确说明,“%”均指重量百分比。
32.实施例1
33.制备萃取剂(d2ehag),优选的步骤如下:
34.a:制备萃取剂前驱物
35.(1)向250ml圆底烧瓶中加入50ml二氯甲烷和10.10g三乙胺(0.1mol),冰水浴(5℃)搅拌1min;加入24.20g二异辛胺(0.1mol)于上述溶液中,冰水浴(5℃)搅拌5min;
36.(2)称取13.66g氯乙酰氯(0.12mol)于50ml烧杯中,转移至恒压漏斗中,逐滴(约14s/滴)滴加到二异辛胺溶液中,并在冰水浴中持续搅拌(搅拌5h);
37.(3)用35ml二氯甲烷冲刷烧瓶壁上的反应产物,再次搅拌45min,转移至250ml的分液漏斗中,加入15ml盐酸溶液(0.01mol/l),去除三乙胺,用ph试纸测上清液呈酸性;
38.(4)去离子水清洗有机物,直至上清液呈中性(前3次加水100ml,接着2次加水150ml,最后2次加水200ml),若出现乳化现象,滴加适量的二氯甲烷;
39.(5)用32.59g无水硫酸钠干燥30min,接着真空抽滤;旋蒸去除二氯甲烷(-0.06mpa,30℃);真空干燥48h至恒重(-0.08mpa,75℃)即可得到萃取剂前驱物。
40.b:制备萃取剂(d2ehag)
41.(1)向250ml圆底烧瓶加入3.19g粒状氢氧化钠(0.08mol)、60ml甲醇和6.05g甘氨酸(0.08mol),并于60℃水浴中搅拌均匀得到甘氨酸溶液;
42.(2)使用恒压漏斗,将21.04g萃取剂前驱物(0.066mol)逐滴滴加到甘氨酸溶液中(用15ml甲醇将尖底烧瓶中的前驱物完全加入漏斗中),30min后滴加完毕,并持续60℃水浴搅拌27h;
43.(3)搅拌结束后,旋蒸去除甲醇(-0.06mpa,65℃),向烧瓶中加入50ml二氯甲烷,搅拌均匀立即加入1mol/l的硫酸溶液(20ml),去除多余的甘氨酸和氢氧化钠(上清液呈酸
性);
44.(4)将反应物转移到分液漏斗中,并用适量二氯甲烷(10ml)将残余物倒入漏斗中;用去离子水清洗有机物,去除杂质,直至上清液呈中性(每次加水量200ml,共计6次),乳化时,加入适量二氯甲烷(32.5ml);用50.09g无水硫酸钠干燥60min,接着真空抽滤去除无水硫酸钠;
45.(5)将产物旋蒸去除二氯甲烷(-0.06mpa,40℃);真空干燥48h至恒重(-0.08mpa,75℃)即可得到萃取剂。
46.经检测,确认该萃取剂为d2ehag,分子式为c
20h40
n2o3。
47.实施例2
48.采用实施例1制备的萃取剂用于液晶面板萃取回收铟,方法如下:
49.s1:将液晶面板进行破碎,粒度《1cm;将液晶面板破碎物置于热解炉中进行绝氧热解,实现液晶屏与偏光膜完全分解;
50.s2:将热解后所得液晶面板破碎物放入硫酸溶液中浸泡,过滤得到硫酸溶液浸泡液,回收浸泡后玻璃残渣,用于后续资源化利用;硫酸溶液的浓度为0.5~2mol/l。
51.s3:将硫酸溶液浸泡液进行萃取与反萃取处理,回收获得含铟的纯净溶液。
52.具体包括:
53.1)在硫酸浸泡液中添加有机萃取剂进行萃取,萃取方式为超声波+强制搅拌,静置分层;上层有机相溶液用于反萃取;
54.2)在萃取后有机相溶液中添加反萃取剂进行反萃取,反萃取方式为强制搅拌,静置分层;下层液体即为含铟的纯净溶液。
55.其中,步骤1)中,下层硫酸溶液循环使用;步骤2)中,上层有机相溶液循环使用。
56.其中,所述的萃取剂与萃取液的体积比为1:3~1:1;所述的反萃取剂为盐酸,反萃取剂与反萃取液的体积比为3:1~1:1。
57.实施例3
58.一种液晶面板萃取回收铟的装置,参考图1,包括:输送装置1#(1)、破碎装置(2)、输送装置2#(3)、热解装置(4)、燃烧炉膛装置(5)、冷却装置(6)、输送装置3#(7)、浸出装置(8)、酸储罐(9)、输送装置4#(10)、输送装置5#(11)、净化装置(12)、排放装置(13)、固液分离装置(14)、输送装置6#(15)、萃取装置(16)、输送装置7#(17)、输送装置8#(18)、萃取剂储罐(19)、输送装置9#(20)、反萃取装置(21)、输送装置10#(22)、反萃取储罐(23)、输送装置11#(24)和输送装置12#(25)。
59.其中,设备的连接顺序如下:
60.所述输送装置1#(1)出口与所述破碎装置(2)入口相连,所述破碎装置(2)出口与所述输送装置2#(3)入口相连,所述输送装置2#(3)出口与所述热解装置(4)入口相连,所述热解装置(4)出口与所述燃烧炉膛装置(5)、冷却装置(6)和浸出装置(8)入口相连,所述燃烧炉膛装置(5)出口与所述热解装置(4)入口相连,所述冷却装置(6)出口与所述输送装置3#(7)入口相连,所述输送装置3#(7)出口与所述浸出装置(8)入口相连,所述酸储罐(9)出口与所述输送装置4#(10)入口相连,所述输送装置4#(10)出口与所述浸出装置(8)入口相连,所述浸出装置(8)出口与所述输送装置5#(11)和固液分离装置(14)入口相连,所述输送装置5#(11)出口与所述净化装置(12)入口相连,所述净化装置(12)出口与所述排放装置
(13)入口相连,所述固液分离装置(14)出口与所述输送装置6#(15)和萃取装置(16)入口相连,所述萃取装置(16)出口与所述输送装置7#(17)和输送装置9#(20)入口相连,所述输送装置7#(17)出口与所述酸储罐(9)入口相连,所述输送装置9#(20)出口与所述反萃取装置(21)入口相连,所述反萃取储罐(23)出口与所述输送装置10#(22)入口相连,所述输送装置10#(22)出口与所述反萃取装置(21)入口相连,所述反萃取装置(21)出口与所述输送装置11#(24)和输送装置12#(25)入口相连,所述输送装置11#(24)出口与所述萃取剂储罐(19)入口相连,所述萃取剂储罐(19)出口与所述输送装置8#(18)入口相连,所述输送装置8#(18)出口与萃取装置(16)入口相连。
61.结合设备描述的详细处理过程如下:
62.液晶面板原料由输送装置1#(1)进入破碎装置(2),破碎至粒度《1cm后由输送装置2#(3)进入热解装置(4),将液晶面板破碎物置于热解装置(4)中进行绝氧热解,实现液晶与偏光膜完全分解。将热解后所得液晶面板破碎物经冷却装置(6)冷却至室温,然后通过输送装置3#(7)进入浸出装置(8)。
63.酸储罐(9)里的硫酸经由输送装置4#(10)输送到浸出装置(8)中与热解后所得液晶面板破碎物浸泡。浸泡完全后利用固液分离装置(14)分离,将分离后的固相通过输送装置6#(15)进行玻璃残渣回收,用于后续资源化利用;而液相组分
‑‑
硫酸溶液浸泡液则进入萃取装置(16),与从萃取剂储罐(19)经由输送装置8#(18)输送过来的萃取剂混合,萃取之后,上层有机相溶液经由输送装置9#(20)用于反萃取,而下层酸溶液由输送装置7#(17)送至酸储罐(9)循环利用;在萃取后有机相溶液中添加由输送装置10#(22)送来的反萃取储罐(23)的反萃取剂在反萃取装置(21)进行反萃取,反萃取的上层有机相溶液由输送装置11#(24)送至萃取剂储罐(19)循环使用,而反萃取的下层液体即为含铟的纯净溶液,由输送装置12#(25)输送。
64.热解产生的烟气为燃烧炉膛装置(5)供热,并且燃烧炉膛装置(5)的烟气反过来供应热解装置(4)的热量,由热解装置(4)的余热提供给浸出装置(8),浸出装置(8)过程产生的尾气经过输送装置5#(11)送入净化装置(12)充分净化处理后由排放装置(13)排至空气中。
65.实施例4
66.采用实施例2中的方法,将液晶面板在577℃热解,残渣利用硫酸在超声条件下进行浸出,获取含铟的浸提液,研究浸提效果。结果如表1所示。
67.表1:浸提正交实验记录表
[0068][0069]
表1说明,热解后采用本实用新型开发的超声结合硫酸浸出,铟浸出率均大于92%,有利于后续的铟回收利用。
[0070]
实施例5:萃取剂对in2(so4)3、in(no3)3、incl3的萃取效果
[0071]
制备不同ph值的硝酸铟、硫酸铟、三氯化铟溶液;向50ml离心管中加入15ml含in溶液和15ml萃取剂(10mm),以200rpm速度振荡1h,萃取剂为实施例1制备的萃取剂。对比检测萃取前后液相中in的浓度,分析萃取剂对不同含铟溶液的效果。
[0072]
表2萃取剂对不同ph的纯硝酸铟、硫酸铟、三氯化铟溶液的萃取效果
[0073][0074][0075]
从表2可以看出,ph调整到ph=3-6,可以有效保证较好的萃取效果。
[0076]
对比例1
[0077]
采用有机溶液浸泡液晶面板进行回收,操作如下:
[0078]
(1)预处理:手工拆解液晶面板的偏光膜,并用丙酮浸泡60min;
[0079]
(2)取9.23g处理后的液晶面板,加入0.35g的二氧化锰,并加入50ml的硫酸溶液(2mol/l),在超声波功率为700w、500rpm搅拌速度、70℃水浴加热100min;
[0080]
用icp-oes测试其浸提能力为0.119mg/g,浸提残渣铟含量为0.019mg/g,浸提效率为86.12%;
[0081]
(3)萃取:用氨水将浸提液调至3.32,向50ml离心管中加入10ml萃取剂(浓度为0.1mol/l,稀释剂为磺化煤油)和10ml浸提液;
[0082]
室温下,以200rpm振荡速度振荡60min;
[0083]
用icp-oes测萃取原液浓度为14.02mg/l,萃取后液相浓度为1.34mg/l,萃取效率为90.4%。
[0084]
对比例2:
[0085]
研究常规萃取剂进行液晶面板回收,步骤如下:
[0086]
s1:将液晶面板进行破碎,粒度《1cm;将液晶面板破碎物置于热解炉中进行绝氧热解,温度为577℃,实现液晶屏与偏光膜完全分解;
[0087]
s2:将热解后所得液晶面板破碎物放入硫酸溶液中浸泡,过滤得到硫酸溶液浸泡液,回收浸泡后玻璃残渣,用于后续资源化利用;硫酸溶液的浓度为1mol/l,获取含铟的浸提液,调整ph调至2.93;
[0088]
s3:将硫酸溶液浸泡液进行萃取与反萃取处理,在50ml离心管中加入10ml萃取剂
(浓度为0.1mol/l,稀释剂为磺化煤油)和10ml浸提液;室温下,以200rpm振荡速度振荡60min;
[0089]
使用icp-oes测试浸提前后液相中铟的含量;测试结果为:硫酸铟溶液(ph=2.93)原始浓度为16.00mg/l,萃取后液相浓度为0.38mg/l,萃取效率为97.63%。
[0090]
以上详细描述了本实用新型的优选实施方式,但是,本实用新型并不限于上述实施方式中的具体细节,在本实用新型的技术构思范围内,可以对本实用新型的技术方案进行多种简单变型,这些简单变型均属于本实用新型的保护范围。
[0091]
另外需要说明的是,在上述具体实施方式中所描述的各个具体技术特征,在不矛盾的情况下,可以通过任何合适的方式进行组合。为了避免不必要的重复,本实用新型对各种可能的组合方式不再另行说明。
[0092]
此外,本实用新型的各种不同的实施方式之间也可以进行任意组合,只要其不违背本实用新型的思想,其同样应当视为本实用新型所公开的内容。