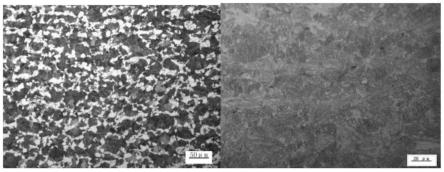
一种38crmoal氮化钢盘条的生产方法
技术领域
1.本发明涉及一种38crmoal氮化钢盘条的生产方法。
背景技术:2.38crmoal钢是一种常用的渗氮钢,经渗氮处理后能获得极高的表面硬度、良好的耐磨性、高的疲劳强度和较低的缺口敏感性,在工业上有广泛的应用。该钢种氮化速度较快,能够在较短的时间内得到较深的氮化层深度,经热处理后工件具有较高的强韧性、表面硬度和高耐磨性,常用于制造承受冲击载荷及在往复磨损条件下工件的机械零件如镗杆、磨床主轴、自动车床主轴,螺杆、精密丝杆、精密齿轮、橡胶及塑料挤压机上的各种耐磨件等。在实际生产中,由于客户对盘条的拉拔性能有一定要求,这需要对热轧盘条的显微组织进行控制,故有必要对38crmoal连续冷却相变行为进行研究,为生产中制订控冷制度提供理论支持。
技术实现要素:3.为了解决上所述技术问题,本发明的目的是提供一种38crmoal氮化钢盘条的生产方法,解决在生产过程中对热轧盘条的显微组织进行控制,充分了解每个相变区域对应的温度的问题。
4.为解决上述技术问题,本发明采用如下技术方案:
5.本发明一种38crmoal氮化钢盘条的生产方法,生产步骤主要包括以下工艺:铁水预处理—转炉—精炼—vd真空处理—连铸—开坯—轧制;其中:
6.铁水脱硫采用kr法脱硫,脱硫剂是以石灰石为主,再配入少许萤石、铝为助熔剂;
7.转炉采用复吹转炉冶炼,采用单渣操作,终渣碱度按3.0控制,为保证较低的出钢磷、合适的出钢温度和相对稳定的出钢碳,转炉采用低拉碳工艺,转炉终点控制目标c不大于0.06%,出钢温度控制不小于1630℃;
8.精炼采用锰铁、金属锰、低碳铬铁、钼铁、镍板合金化,终脱氧采用无铝脱氧;连铸钢水在保护气体下浇铸,拉速控制在2.3~2.5m/min,连铸二冷配水采用弱冷冷;
9.铸坯加热温度控制在1100~1200℃,钢坯出炉温度1050~1150℃,开轧温度990~1050℃,终轧温度820~850℃;起步辊道速度0.76m/s,1-5架风机开启度100%,6、7架关,8架风机开启度50%,9、10架风机关,保温罩全开。
10.进一步的,化学成分为以质量百分比计为:c:0.38-0.42%,si:0.25-0.35%,mn:0.45-0.55%,cr:1.45-1.55%,al:0.7-1.10%,余量为fe和不可避免的杂质,杂质中的p≤0.030%,所述杂质中的s≤0.030%。
11.进一步的,生产方法具体包括:
12.铁水脱硫:脱硫前扒除高炉渣,以提高脱硫效率;取铁矿石熔融为铁水,铁水采用kr法脱硫,即将所述铁水采用转速为90r/min的搅拌桨搅拌,搅拌2min后,加入脱硫剂,脱硫剂为9:1的质量比混合的石灰粉与萤石,搅拌反应10min,静置5min;铁水脱硫静置后扒除脱
硫渣,稳定脱硫效果,防止脱硫渣进入转炉造成转炉回硫,保证钢中硫含量控制在0.01%以下;转炉:采用顶底复吹进行脱碳、脱磷,1650℃下冶炼至钢液中碳含量低于0.05%、磷含量低于0.01%出钢,出钢过程中采用保护气体以0.5mpa的压力搅拌钢液,出钢进行至1/4时加入硅铁、硅锰合金脱氧,加入碳粉和造渣料,出钢时防止大量下渣,同时,所述保护气体压力随出钢量逐渐减小;精炼:采用lf炉外精炼,1575℃下脱氧至钢液中含氧量为0.002%,加入锰铁、镍板及铬铁、钒的合金元素,精炼结束后喂sicaba合金线,同时保证软吹时间不小于10min;连铸:尽量保证恒拉速进行拉钢,拉速控制在2.3m/min,铸坯断面为150mm
×
150mm,铸坯长度为11.5m;轧制:将连铸坯加热至1200℃,出炉测温1200℃左右,高压水除鳞后进行轧制,轧制温度1050
±
20℃,经粗轧、终轧后,控制终轧温度820
±
20℃;
13.轧制加热炉加热温度控制为:预热850
±
50℃、加热段1030
±
50℃、均热段1060
±
420℃,残氧控制在1%
‑‑
4%,加热时间为90
±
5min;开轧温度990
±
15℃,精轧入口温度为910
±
20℃,吐丝温度870
±
20℃,起步辊道速度0.76m/s,1-5架风机开启度100%,6、7架关,8架风机开启度50%,9、10架风机关,保温罩全开。
14.与现有技术相比,本发明的有益技术效果:
15.对生产过程中的轧制和控冷工艺来说,控制较低的吐丝温度(900℃或以下),以细化相变前的奥氏体晶粒;同时通过风机风量的调节和合理的辊道速度,控制盘条在750~620℃范围内的低冷却速率(≤0.2℃/s),可以保证盘条获得以铁素体+珠光体为主的高温相变组织,适应客户对该牌号盘条的塑性要求。
附图说明
16.下面结合附图说明对本发明作进一步说明。
17.图1为38crmoal氮化钢盘条的金相组织照片;
18.图2为连续冷却转变曲线。
具体实施方式
19.本发明的目的是提供一种改善38crmoal钢盘条轧态组织的生产工艺,通过合理设计成分和工艺参数,使其硬度、组织均匀性、晶粒度得到大幅改善,同时降低钢材轧后冷却的初始温度,使38crmoal钢盘条轧态组织的组织形态由原铁素体+珠光体+贝氏体+马氏体组织,改善为平衡态的铁素体和珠光体组织,且晶粒度可提升2个级别以上。
20.本实例中38crmoal氮化钢用盘条的化学成分如表1所示。该盘条的主要制备工艺为:铁水脱硫—转炉—lf精炼—连铸—轧制。铁水脱硫:脱硫前扒除高炉渣,以提高脱硫效率;取铁矿石熔融为铁水,铁水采用kr法脱硫,即将所述铁水采用转速为90r/min的搅拌桨搅拌,搅拌2min后,加入脱硫剂,脱硫剂为9:1的质量比混合的石灰粉与萤石,搅拌反应10min,静置5min。铁水脱硫静置后扒除脱硫渣,稳定脱硫效果,防止脱硫渣进入转炉造成转炉回硫,保证钢中硫含量控制在0.01%以下。转炉:采用顶底复吹进行脱碳、脱磷,1650℃下冶炼至钢液中碳含量低于0.05%、磷含量低于0.01%出钢,出钢过程中采用保护气体以0.5mpa的压力搅拌钢液,出钢进行至1/4时加入硅铁、硅锰合金脱氧,加入碳粉和造渣料,出钢时防止大量下渣,同时,所述保护气体压力随出钢量逐渐减小。精炼:采用lf炉外精炼,1575℃下脱氧至钢液中含氧量为0.002%,加入锰铁、镍板及铬铁、钒的合金元素,精炼结束
后喂sicaba合金线,同时保证软吹时间不小于10min。连铸:尽量保证恒拉速进行拉钢,拉速控制在2.3m/min,铸坯断面为150mm
×
150mm,铸坯长度为11.5m。轧制:具体轧制工艺如表2所示,将连铸坯加热至1200℃,出炉测温1200℃左右,高压水除鳞后进行轧制,轧制温度1050
±
20℃,经粗轧、中轧后,控制终轧温度820
±
20℃。
21.轧制加热炉加热温度控制为:预热850
±
50℃、加热段1030
±
50℃、均热段1060
±
420℃,残氧控制在1%
‑‑
4%,加热时间为90
±
5min;开轧温度990
±
15℃,精轧入口温度为910
±
20℃,吐丝温度870
±
20℃,起步辊道速度0.76m/s,1-5架风机开启度100%,6、7架关,8架风机开启度50%,9、10架风机关,保温罩全开。氮化钢用盘条的力学性能检验结果见表4。轧制后的盘条一部分热处理后进行力学性能检验,热处理工艺为淬火温度940℃,介质为水,回火温度是640℃,介质为水。具体热处理后的力学性能检验结果见表4。
22.利用mms-200热力模拟试验机测定了试验钢不同冷速(0.1℃/s、0.2℃/s、0.5℃/s、1℃/s、2℃/s、5℃/s、10℃/s、20℃/s)下的热膨胀曲线,并根据曲线测定出相变温度范围;利用imagerd1m金相显微镜对相变后的组织进行分析。根据实验采集的热膨胀曲线,利用切线法获得曲线上的相变开始和结束点;再结合各个冷速下的相变组织,利用origin软件作出试验钢的连续冷却转变曲线(cct曲线),结果见图2。
23.表1氮化钢用盘条的化学成分/%
24.实施例csimnpscrmoal实施例10.3890.4620.6490.02650.0101.520.2120.830实施例20.4020.4640.5970.02020.0121.600.200.864实施例30.3760.340.420.02010.0111.470.2110.87
25.表2.氮化钢用盘条的轧制工艺
[0026][0027]
表3氮化钢用盘条的力学性能检验结果
[0028]
实施例抗拉强度/mpa屈服强度/mpa面缩率/%延伸率/%实施例173160222.556实施例27326832347实施例37716412442
[0029]
表4氮化钢用盘条的力学性能检验结果(热处理后)
[0030]
实施例抗拉强度/mpa屈服强度/mpa面缩率/%延伸率/%实施例110019012576实施例210098783074实施例310328932663
[0031]
以上所述的实施例仅是对本发明的优选方式进行描述,并非对本发明的范围进行限定,在不脱离本发明设计精神的前提下,本领域普通技术人员对本发明的技术方案做出的各种变形和改进,均应落入本发明权利要求书确定的保护范围内。