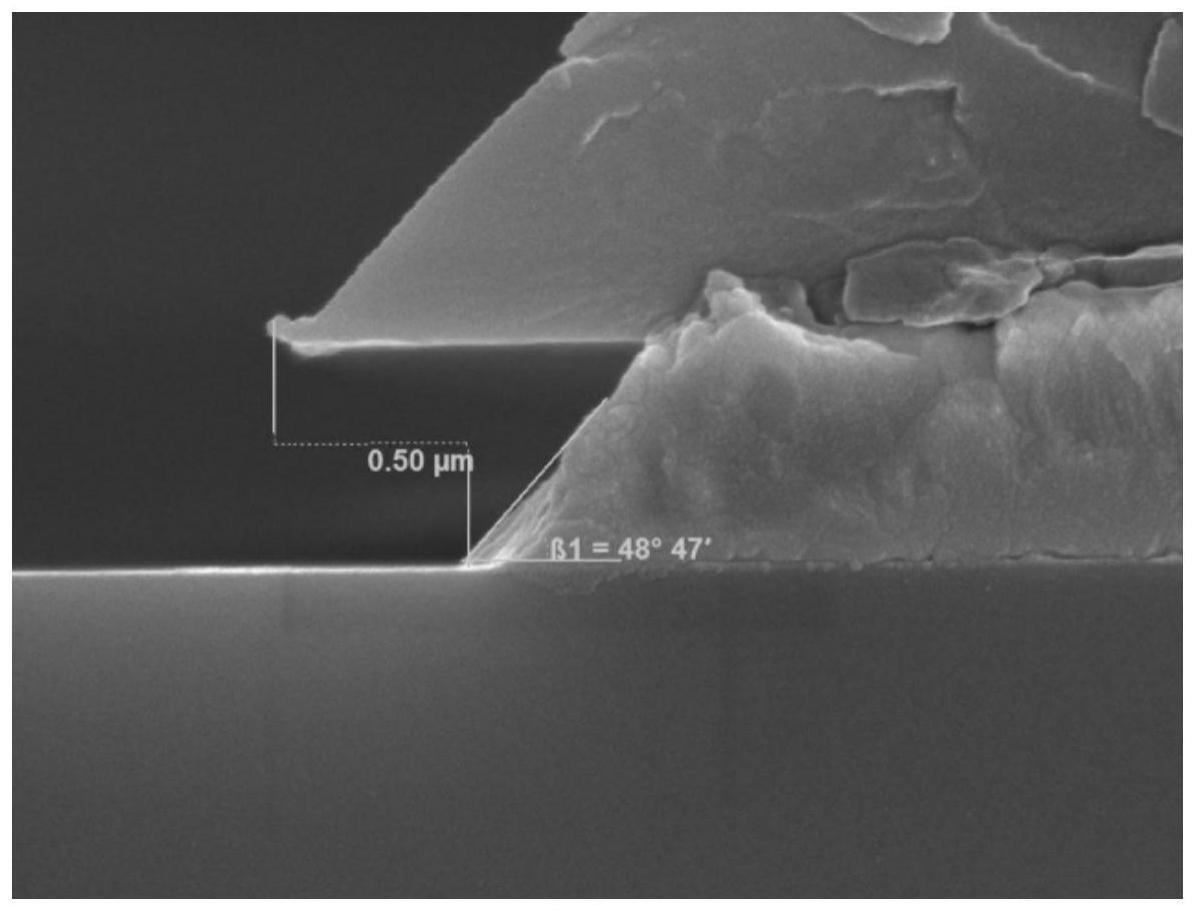
1.本发明涉及铜钼蚀刻液技术,尤其涉及一种一剂型高效长寿命铜钼蚀刻液、其制备方法及应用。
背景技术:2.目前tft-lcd(thin flim transistor-liquid crystal display)显示技术早已深入人们生活的方方面面,尤其是在电视等大尺寸显示器上,人们对于电视尺寸的要求越来愈大。在大尺寸显示器件上,目前其制作源漏极以及栅极的工艺大多选择铜制程,这是因为铜金属的导电性能比铝金属更好,更加适合高分辨率的大尺寸面板的制作。由于铜原子性质较活泼,容易往其他膜层扩散,且铜层与玻璃基板的粘接性较差。因此在制作铜导线时通常需要在铜层下方与玻璃或其他膜层接触的部位会镀上一层钼或者钼铌合金。从而在制作这类铜导线时,就需要使用到一种可以同时蚀刻铜层及钼或钼铌层金属的铜钼蚀刻液,并且还能保证蚀刻完后得到特定锥角的坡度、各金属层蚀刻量较为统一、无底切现象的蚀刻形貌。
3.目前最常使用的铜钼蚀刻液一般由双氧水、无机酸或有机酸、抑制剂等组分构成,在蚀刻的过程中一方面会产生大量的铜离子,铜离子浓度的增高会加速双氧水的分解,双氧水过量分解会导致蚀刻不均匀。另一方面,随着蚀刻的进行也会导致溶液中氢根离子不断消耗,产生水,从而导致溶液的ph值不断上升,影响到蚀刻后期的蚀刻性能。其次,该类蚀刻液往往使用氮唑类化合物的抑制剂,以抑制不同金属层之间的电极效应,得到良好的蚀刻锥角。但此类氮唑类抑制剂的成本相当高(目前市价约1000-1200元/公斤),其成本可占蚀刻液总成本的30%-50%。
4.因此,开发出一种具备高效的铜离子耐受性能、蚀刻过程不需要添加补充剂液能保持较稳定ph值,同时尽可能使用较少的氮唑类抑制剂以保证良好经济效益的高寿命铜钼蚀刻液就显得尤为必要。
技术实现要素:5.本发明的目的在于,针对目前铜钼蚀刻液蚀刻效果不佳,后期蚀刻性能不稳定及成本较高的问题,提出一种一剂型高效长寿命铜钼蚀刻液,该铜钼蚀刻液能应用在tft-lcd面板制造所涉及的铜制程领域中,在蚀刻过程中不需要补充抑制剂,即可实现高效蚀刻,其稳定的使用寿命可达到10000ppm溶铜量,并且仅在添加极少量氮唑类抑制剂的基础上,即可以保证极为可靠的蚀刻效果。
6.为实现上述目的,本发明采用的技术方案是:一剂型高效长寿命铜钼蚀刻液,包括质量配比如下的各组分:
[0007][0008]
进一步地,所述氧化剂为h2o2和/或过硫酸盐,所述过硫酸盐选自过硫酸钾、过硫酸钠、过硫酸铵中的一种或多种,所述氧化剂优选h2o2和过硫酸铵。所述氧化剂优选质量份为6-8份。氧化剂能将金属铜和钼分别氧化成氧化铜和氧化钼。
[0009]
进一步地,所述三元无机酸为h3po4和/或h3aso4,优选h3po4和h3aso4。所述三元无机酸优选质量份为1.5-3份。三元无机酸可较其他一元或二元酸提供更多h
+
离子,能起到溶解氧化铜及氧化钼的作用。
[0010]
进一步地,所述有机酸选自酒石酸、丙二酸、二乙醇酸、马来酸、乙醇酸、羟基丁酸、乳酸、琥珀酸、苹果酸、柠檬酸、邻苯二甲酸和水杨酸中的一种或多种的混合,优选柠檬酸、苹果酸、乙醇酸、二乙醇酸和水杨酸中的一种或多种的混合。所述有机酸优选质量份为6-8份。有机酸起到提供h
+
离子溶解氧化铜及氧化钼作用,同时螯合铜、钼离子。
[0011]
进一步地,所述有机碱选自乙醇胺、二乙醇胺、三乙醇胺、异丙醇胺、n-乙基乙醇胺、二甘醇胺、三异丙醇胺、n,n-二甲基乙醇胺和n,n-二乙基乙醇胺中的一种或多种的混合。所述有机碱优选质量份为6-9份。有机碱可起到络合铜离子及钼离子的作用。
[0012]
进一步地,所述磷酸二氢盐为磷酸经过一次电离析出一个h
+
离子后的盐类物质,此盐类物质中还含有两个h
+
。所述磷酸二氢盐为磷酸二氢钾、磷酸二氢钠、磷酸二氢铵和磷酸二氢钙中的一种或多种的混合,加入优选质量份为0.2-0.8份。所述砷酸二氢盐为砷酸经过一次电离析出一个h
+
离子后的盐类物质,此盐类物质中还含有两个h
+
。所述砷酸二氢盐为砷酸二氢钾、砷酸二氢钠和砷酸二氢铵中的一种或多种的混合,加入优选质量份为0.2-0.5份。所述磷酸二氢盐和/或砷酸二氢盐一方面可起到缓冲溶液的ph值作用,避免在蚀刻过程中ph值出现比较大的波动。另外,加入磷酸二氢盐和/或砷酸二氢盐协同三元无机酸使用可极大的提升蚀刻寿命,溶铜量达到10000ppm以上,推测机理为在蚀刻后期,磷酸二氢盐和/或砷酸二氢盐由于含两个氢根,还可起到二次电离补充溶液中h
+
离子的作用,保持蚀刻均匀性。
[0013]
进一步地,所述有机金属盐为苯甲酸盐,选自苯甲酸钠、苯甲酸钾、苯甲酸钙和苯甲酸铵中的一种或多种的混合。所述有机金属盐优选质量份为0.07-0.1份。有机金属盐起到金属缓蚀的作用,可以抑制金属阳极极化反应,调节蚀刻速率,从而得到较好的蚀刻锥角。
[0014]
进一步地,所述蚀刻抑制剂为氮唑类抑制剂,优选为2-氨基噻唑、2-氨基-5-硝基噻唑、3-氨基-1,2,4-三唑和苯并三唑中一种或多种的混合。经研究,蚀刻抑制剂在协同有
机金属盐使用时,仅需加入质量份为0.001-0.005份的氮唑类抑制剂,即可起到较好的抑制金属层电位极化的作用,保证蚀刻无底切或tail(tail指蚀刻后金属层出现拖尾现象,属于一种不良蚀刻锥角的形态),可得到控制在30
°‑
70
°
的蚀刻锥角。所述蚀刻抑制剂加入优选质量份为0.001-0.004份。
[0015]
进一步地,所述去离子水优选质量份为70-78份。
[0016]
进一步地,所述蚀刻液的ph为3.5~5.5。
[0017]
本发明的另一个目的还公开了一种一剂型高效长寿命铜钼蚀刻液的制备方法,包括以下步骤:
[0018]
步骤1:按照重量配比称取各组份;
[0019]
步骤2:将三元无机酸、有机酸、磷酸二氢盐和/或砷酸二氢盐、有机金属盐、蚀刻抑制剂和去离子水搅拌混合至所有物料溶解完全;
[0020]
步骤3:保持搅拌同时加入有机碱,此时反应为放热反应,溶液温度升温;
[0021]
步骤4:待溶解温度降低至常温时,在搅拌下加入氧化剂,搅拌至均匀透明,即得所述一剂型高效长寿命铜钼蚀刻液。
[0022]
上述制备方法中步骤2溶解固体,反应为吸热,溶液温度降低;步骤3加入液体碱液,放热,溶液温度升高。本分明将吸热反应和放热分开便于采用外界加热或冷却装置控温,加快温度调节至常温条件。本发明步骤2和步骤3采用的混合容器设置有加热装置和冷却装置。
[0023]
进一步地,步骤4所述常温为20-25℃,搅拌时间为30min-1h。
[0024]
本发明的另一个目的还公开了一剂型高效长寿命铜钼蚀刻液在铜钼金属层蚀刻领域的应用。具体适用于液晶显示面板制造过程中铜钼金属层的蚀刻。
[0025]
进一步地,所述铜钼金属层中,铜金属层厚度为钼金属层厚度为
[0026]
进一步地,采用一剂型高效长寿命铜钼蚀刻液刻蚀铜钼膜层的方法,包括如下步骤:
[0027]
步骤a:将铜粉溶于所述一剂型高效长寿命铜钼蚀刻液中,控制初始溶铜量为200ppm-500ppm,以完成对铜钼蚀刻液的预处理;
[0028]
步骤b:控制溶液温度为30℃-40℃,以所述完成预处理后的铜钼蚀刻液对镀有铜钼金属膜层的基板进行蚀刻,直到得到所述铜钼金属膜层的理想蚀刻形貌及图案;
[0029]
步骤c:以初始溶铜量为起点,按每10min溶解400-600ppm铜粉(优选为500ppm),逐步提高蚀刻液中的溶铜量至2000-10000ppm,再分别针对铜钼金属层基板进行蚀刻,得到理想的铜钼金属膜层蚀刻形貌及图案。
[0030]
本发明一剂型高效长寿命铜钼蚀刻液、其制备方法及应用,与现有技术相比较具有以下优点:
[0031]
1、本发明铜钼蚀刻液不添加任何含氟物质,使用更安全、环保、无污染。同时在蚀刻完毕后,本发明蚀刻液废液的处理方式简单、对水土污染小,更经济、环保,对环境和人体无伤害。
[0032]
2、本发明三元无机酸与磷酸二氢盐和/或砷酸二氢盐协同复配,从而使该铜钼蚀
刻液在具备优良高效的蚀刻性能同时,保证可耐受更高的溶铜量,在不添加补充液时,使用寿命就可达到10000ppm,因而使用成本更经济。
[0033]
3、本发明苯甲酸盐在配合氮唑类抑制剂使用时,起到优良的电位抑制作用,苯甲酸盐缓蚀作用主要是起到阳极极化作用,从而使腐蚀电位正移,即苯甲酸根阴离子可移向金属阳极而使金属层钝化,有效控制原电池电极效应,防止各金属膜层出现过刻底切或缓蚀的tail现象,达到30
°‑
70
°
的锥角。
[0034]
4、同时本发明苯甲酸盐的加入,还可以有效减少氮唑类抑制剂的加入量,仅加入0.001-0.005份的氮唑类抑制剂即可起到上述抑制电极效应的作用,减少了高成本材料的加入量。苯甲酸盐的加入之所以可以有效减少氮唑类抑制剂的加入量,是因为苯甲酸盐可起到有效钝化金属阳极、减缓其蚀刻速率的作用。而氮唑类抑制剂的加入可利用其自身的n-n键与铜络合,从而在铜层表面形成不溶性的表面保护膜,进而抑制铜层的继续蚀刻。二者所起到的抑制作用是相辅相成、相互互补的。因此该蚀刻液生产成本低廉、经济效益明显,可大规模生产应用。
[0035]
因此,本发明一剂型高效长寿命铜钼蚀刻液在tft-lcd铜制程领域具有非常良好的应用前景和大规模工业化推广潜力。
附图说明
[0036]
图1是实施例3铜钼蚀刻液蚀刻后的铜钼膜层截面放大9万倍的显微镜截面图片。
[0037]
图2是实施例3铜钼蚀刻液蚀刻后的铜钼膜层截面放大9万倍的显微镜俯拍图片。
[0038]
图3是对比例1铜钼蚀刻液蚀刻后的铜钼膜层截面放大9万倍的显微镜图片。
[0039]
图4是对比例6铜钼蚀刻液蚀刻后的铜钼膜层截面放大9万倍的显微镜图片。
具体实施方式
[0040]
以下结合实施例对本发明进一步说明:
[0041]
实施例1-12
[0042]
实施例1-12公开了多种一剂型高效长寿命铜钼蚀刻液,其组分及质量配比如表1所示:
[0043]
表1实施例1-12
[0044][0045][0046]
实施例1-12所述一剂型高效长寿命铜钼蚀刻液的制备方法,包括以下步骤:
[0047]
步骤1:按照重量配比称取各组份;
[0048]
步骤2:将三元无机酸、有机酸、磷酸二氢盐和/或砷酸二氢盐、有机金属盐、蚀刻抑制剂和去离子水搅拌混合至所有物料溶解完全;
[0049]
步骤3:保持搅拌同时加入有机碱,此时反应为放热反应,溶液温度升温;
[0050]
步骤4:待溶解温度降低至常温时,在搅拌下加入氧化剂,搅拌至均匀透明,即得所述一剂型高效长寿命铜钼蚀刻液。
[0051]
对比例1-7
[0052]
对比例1-7铜钼蚀刻液的组分及质量配比如表2所示:
[0053]
表2对比例1-7
[0054][0055][0056]
所述对比例1-7铜钼蚀刻液的制备方法,包括以下步骤:
[0057]
步骤1:按照表中重量配比称取各组份;
[0058]
步骤2:将三元无机酸、固体组分和去离子水搅拌混合至所有物料溶解完全;
[0059]
步骤3:保持搅拌同时加入有机碱,此时反应为放热反应,溶液温度升温;
[0060]
步骤4:待溶解温度降低至常温时,在搅拌下加入氧化剂,搅拌至均匀透明,即得所述一剂型高效长寿命铜钼蚀刻液。
[0061]
实施例1-12和对比例1-7性能测试对比如表3所述:
[0062]
表3实施例1-12和对比例1-7性能测试结果
[0063][0064][0065]
采用实施例1-12制备的铜钼蚀刻液进行蚀刻,其可在溶铜量为7000-10000ppm的使用寿命下蚀刻,其图形锥角可稳定在35
°‑
70
°
的范围内,且无金属层拖尾或者底切现象发生,且蚀刻后基板表面干净无残留,实施例3铜钼蚀刻液蚀刻后的铜钼膜层见图1、图2。采用对比例1和对比例2在仅加入0.75份磷酸或0.75份砷酸时,因可提供h
+
离子不足,所以其使用寿命仅分别为4000ppm及2000ppm的溶铜量,蚀刻容易出现图3所示的金属层拖尾严重的现象。而对比例3因未加入磷酸二氢盐其使用寿命仅达4000ppm的溶铜量,且出现了金属层拖尾现象。对比例4和对比例5只采用一种过氧化氢或过硫酸铵氧化剂,制约了溶液的氧化能力,进而限制了三元无机酸溶解由氧化剂氧化生成的金属氧化物的效应发生,因此蚀刻
寿命仅分别为6000ppm及4000ppm。对比例6在不加入苯甲酸盐类抑制剂时,因其缓蚀能力不足,因此较容易出现图4所示的底切现象,这种底切现象需加入适量苯甲酸盐或多量的氮唑类抑制剂方能得到较好的控制。对比例7未加入蚀刻抑制剂,也容易在蚀刻时出现底切现象。
[0066]
其中:
[0067]
性能1存储的测试方法为:
[0068]
本发明蚀刻液中,通过添加三元无机酸(磷酸和或砷酸)、使用磷酸二氢盐和或砷酸二氢盐(nah2po4、kh2po4、nh4h2po4、ash2nao4、ash2ko4、ash6no4等)即可达到不含氟蚀刻之目的。因该蚀刻液中加入了较多量的双氧水,双氧水储存不当易分解,因此配制溶液后需静置于阴凉处,当溶液中开始持续产生较多气泡时,即已变质,储存失效。
[0069]
性能2蚀刻寿命的测试方法为:
[0070]
步骤1:提供一种镀有前述厚度的铜钼金属膜层的基板;
[0071]
步骤2:将铜粉溶于所述铜钼蚀刻液中,控制初始溶铜量为200-500ppm,以完成对铜钼蚀刻液的预处理;
[0072]
步骤3:控制溶液温度为30℃-40℃,以所述完成预处理后的铜钼蚀刻液对镀有铜钼金属膜层的基板进行蚀刻,直到得到所述铜钼金属膜层的理想蚀刻形貌及图案;
[0073]
步骤4:以初始溶铜量为起点,逐步提高蚀刻液中的溶铜量至2000ppm-10000ppm,再分别针对铜钼金属层基板进行蚀刻,得到理想的铜钼金属膜层蚀刻形貌及图案。
[0074]
性能3蚀刻抑制剂添加量的测试方法为:
[0075]
步骤1:配制不同抑制剂添加种类及添加量的铜钼蚀刻液;
[0076]
步骤2:提供一种镀有前述厚度的铜钼金属膜层的基板;
[0077]
步骤3:将铜粉溶于所述铜钼蚀刻液中,控制初始溶铜量为200-500ppm,以完成对铜钼蚀刻液的预处理;
[0078]
步骤4:控制溶液温度为30℃-40℃,以所述完成预处理后的添加有不同抑制剂的铜钼蚀刻液对镀有铜钼金属膜层的基板进行蚀刻,直到得到所述铜钼金属膜层的理想蚀刻形貌及图案。
[0079]
最后应说明的是:以上各实施例仅用以说明本发明的技术方案,而非对其限制;尽管参照前述各实施例对本发明进行了详细的说明,本领域的普通技术人员应当理解:其依然可以对前述各实施例所记载的技术方案进行修改,或者对其中部分或者全部技术特征进行等同替换;而这些修改或者替换,并不使相应技术方案的本质脱离本发明各实施例技术方案的范围。