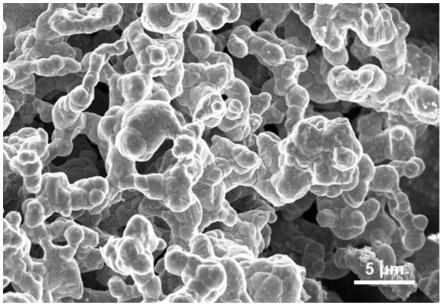
1.本发明涉及一种微米孔径泡沫铜的制备方法,属于泡沫金属技术领域。
背景技术:2.泡沫铜是一种以铜为基体的具有大量连通或者不连通孔隙的多功能材料,其具有密度小、孔隙率高、热导率好、消音效果好等优势,被广泛应用于建筑、电化学和能源领域。现有泡沫铜的制备方法主要分为定向凝固法、渗流铸造法、去合金化法、电沉积法和粉末冶金法,然而定向凝固法存在泡沫铜的孔径分布不均匀、孔径尺寸不一致以及参数控制困难等问题;渗流铸造法存在泡沫铜结构不连续、孔隙率不均匀以及容易受外界渗流压力和温度影响等问题;去合金化法存在污染严重和回收困难等问题;电沉积法存在对环境污染大、生产时间长、能源消耗高等问题;粉末冶金法存在工艺流程多、设备要求高以及泡沫铜孔径较大等不足。
技术实现要素:3.有鉴于此,本发明的目的在于提供一种微米孔径泡沫铜的制备方法,所述方法制备得到的泡沫铜同时具有结构完整、孔结构分布均匀、孔径具有微米尺寸以及厚度可控的优势。
4.为实现上述目的,本发明的技术方案如下:
5.一种微米孔径泡沫铜的制备方法,所述方法步骤如下:
6.将纯铜颗粒与溶剂混合研磨后得到纯铜颗粒浆料,将所述纯铜颗粒浆料涂布于光滑平面载体上,干燥后得到纯铜颗粒涂层,热处理使纯铜颗粒熔融粘结,在所述载体上得到一种微米孔径泡沫铜;
7.或,将氧化铜颗粒与溶剂混合研磨后得到氧化铜颗粒浆料,将所述氧化铜颗粒浆料涂布于光滑平面载体上,干燥后得到氧化铜颗粒涂层,热还原处理使氧化铜颗粒还原并熔融粘结,在所述载体上得到一种微米孔径泡沫铜;
8.其中,所述纯铜颗粒的粒径为20纳米~20微米;所述氧化铜颗粒的粒径为20纳米~20微米;
9.热处理时在保护气体氛围下进行;热处理温度为700℃~900℃,保温时间为1h~3h;
10.热还原处理时在氢气和保护气体的混合气氛下进行,氢气占混合气体的体积分数为5%~15%;热还原处理温度为700℃~900℃,保温时间为1h~3h;
11.所述浆料中固含量为40%~70%;浆料涂布厚度为8微米~200微米。
12.优选的,所述溶剂为n-甲基吡咯烷酮、乙醇或h2o。更优选的,所述溶剂为n-甲基吡咯烷酮。
13.优选的,所述浆料涂布厚度为10微米~100微米。
14.优选的,所述浆料涂布采用刮刀刮涂。
15.优选的,所述光滑平面载体为单晶硅片、多晶硅片或者石英玻璃片。
16.优选的,混合研磨时间为10min~60min。
17.优选的,采用真空干燥,干燥温度为100℃~120℃,干燥时间为8h~12h。
18.优选的,所述保护气体为氮气或惰性气体。
19.优选的,热处理或热还原处理的升温速率为2℃/min~10℃/min。
20.有益效果
21.本发明提供了一种微米孔径泡沫铜的制备方法,首先以特定粒径大小的纯铜颗粒或氧化铜颗粒为原料,与溶剂混合后得到浆料;随后将纯铜浆料或者氧化铜浆料涂布于载体上;浆料干燥后进行热处理或热还原处理,得到具有微米孔径的泡沫铜。所述方法的原料来源广泛,操作步骤少,操作过程简单可控,热处理过程时间短,热处理过程中气体使用量低。因此,本发明具有生产成本低、制备工艺简单、能源消耗少、生产效率高以及环境友好的优势。本发明中的制备方法具有制备工艺简单、原材料成本低、能源消耗少的优势。
22.本发明所述泡沫铜具有结构完整、孔结构分布均匀、孔径为微米尺寸且厚度可控的优势,所述泡沫铜可广泛应用于电池负极材料、催化载体材料、相变储能装置材料、电磁屏蔽材料或者阻燃材料中。相对于现有常规泡沫铜,具有更广泛的应用前景。
附图说明
23.图1为实施例1所述材料的扫描电子显微镜(sem)平面图。
24.图2为实施例2所述材料的sem平面图。
25.图3为实施例2所述材料的sem剖面图。
26.图4为实施例3所述材料的sem平面图。
27.图5为对比例1所述材料的sem平面图。
28.图6为对比例2所述材料的sem平面图。
29.图7为对比例3所述材料的sem平面图。
具体实施方式
30.下面结合具体实施例对本发明作进一步详细的说明。
31.实施例1
32.制备浆料:称取0.4g粒径为10微米的氧化铜粉末,转移到玛瑙研钵中;然后加入0.25g n-甲基吡咯烷酮,混合研磨20min,得到氧化铜颗粒浆料,浆料中固含量为61.5%。
33.浆料涂布:将所述氧化铜颗粒浆料转移到石英玻璃片上,使用刮刀将浆料均匀涂布于石英玻璃片表面,浆料涂布厚度为80微米。
34.浆料干燥:将涂布有氧化铜颗粒浆料的石英玻璃片转移到100℃真空烘箱中,抽真空并维持在-1bar,加热干燥10h,石英玻璃片上的氧化铜颗粒浆料得到充分干燥,在所述载体上得到氧化铜颗粒涂层。
35.热还原处理:将所述负载有氧化铜颗粒涂层的石英玻璃片转移到管式炉中,通入氢气占体积含量10%的h2/ar2混合气体30min排除空气,混合气体流量为100sccm,然后设置升温速度为7℃/min,温度升至750℃,保温2h,保温结束后自然降温,在所述载体上得到一种微米孔径泡沫铜。
36.所述材料的sem测试结果如图1所示,所述泡沫铜结构完整、厚度均一并且具有均匀分布的微米孔径,孔径大小介于5微米~20微米。
37.实施例2
38.制备浆料:称取0.3g粒径为2微米的纯铜粉末,转移到玛瑙研钵中;然后加入0.2g n-甲基吡咯烷酮,混合研磨20min,得到纯铜颗粒浆料,浆料中固含量为60%。
39.浆料涂布:将所述纯铜颗粒浆料转移到石英玻璃片上,使用刮刀将浆料均匀涂布于石英玻璃片表面,浆料涂布厚度为40微米。
40.浆料干燥:将涂布有纯铜颗粒浆料的石英玻璃片转移到100℃真空烘箱中,抽真空并维持在-1bar,加热干燥10h,石英玻璃片上的纯铜颗粒浆料得到充分干燥,在所述载体上得到纯铜颗粒涂层。
41.热处理:将所述负载有纯铜颗粒涂层的多晶硅片转移到管式炉中,通入氩气30min排除空气,混合气体流量为100sccm,然后设置升温速度为5℃/min,温度升至750℃,保温2h,保温结束后自然降温,在所述载体上得到一种微米孔径泡沫铜。
42.所述材料的sem测试结果如图2-3所示,所述泡沫铜结构完整、厚度均一并且具有均匀分布的微米孔径,孔径大小介于10微米~40微米。
43.实施例3
44.制备浆料:称取0.3g粒径为40纳米的氧化铜粉末,转移到玛瑙研钵中;然后加入0.4g n-甲基吡咯烷酮,混合研磨20min,得到氧化铜颗粒浆料,浆料中固含量为42.8%。
45.浆料涂布:将所述氧化铜颗粒浆料转移到多晶硅片上,使用刮刀将浆料均匀涂布于多晶硅片表面,浆料涂布厚度为20微米。
46.浆料干燥:将涂布有氧化铜颗粒浆料的多晶硅片转移到100℃真空烘箱中,抽真空并维持在-1bar,加热干燥10h,多晶硅片上的氧化铜颗粒浆料涂层得到充分干燥,在所述载体上得到氧化铜涂层。
47.热还原处理:将所述负载有氧化铜颗粒涂层的石英玻璃片转移到管式炉中,通入氢气占体积含量10%的h2/ar2混合气体30min排除空气,混合气体流量为100sccm,然后设置升温速度为3℃/min,温度升至850℃,保温2h,保温结束后自然降温,在所述载体上得到一种微米孔径泡沫铜。
48.所述材料的sem测试结果如图4所示,所述泡沫铜结构完整、厚度均一并且具有均匀分布的微米孔径,孔径大小介于1微米~4微米。
49.对比例1
50.本对比例中热还原处理温度为600℃,其余同实施例1。
51.所述材料的sem测试结果如图5所示,由于烧结温度低无法获得完整的含有微孔结构的泡沫铜。
52.对比例2
53.本对比例中热还原处理温度为950℃,其余同实施例2。
54.所述材料的sem测试结果如图6所示,由于烧结温度过高,获得铜材料无法保留微米孔结构。
55.对比例3
56.本对比例中,浆料涂覆厚度为5微米,其余同实施例3。
57.所述材料的sem测试结果如图7所示,由于浆料涂布厚度小,获得铜材料显示为片状,不具有微孔结构。
58.对比例4
59.制备浆料:称取0.4g粒径为10微米的氧化铜粉末,转移到玛瑙研钵中;然后加入0.15g n-甲基吡咯烷酮,混合研磨20min,得到氧化铜颗粒浆料,浆料中固含量为72.7%。
60.浆料涂布:将所述氧化铜颗粒浆料转移到石英玻璃片上,使用刮刀将浆料均匀涂布于石英玻璃片表面,浆料涂布厚度为80微米。
61.本对比例中,由于浆料固含量过高(》70%),氧化铜颗粒浆料容易团聚,无法获得完整的氧化铜颗粒浆料涂布层。
62.对比例5
63.制备浆料:称取0.3g粒径为40纳米的氧化铜粉末,转移到玛瑙研钵中;然后加入0.5g n-甲基吡咯烷酮,混合研磨20min,得到氧化铜颗粒浆料,浆料中固含量为37.5%。
64.浆料涂布:将所述氧化铜颗粒浆料转移到多晶硅片上,使用刮刀将浆料均匀涂布于多晶硅片表面,浆料涂布厚度为20微米。
65.本对比例中,由于浆料固含量过低(《40%),浆料粘稠度不足,无法获得完整的氧化铜颗粒浆料涂布层。
66.综上所述,发明包括但不限于以上实施例,凡是在本发明的精神和原则之下进行的任何等同替换或局部改进,都将视为在本发明的保护范围之内。