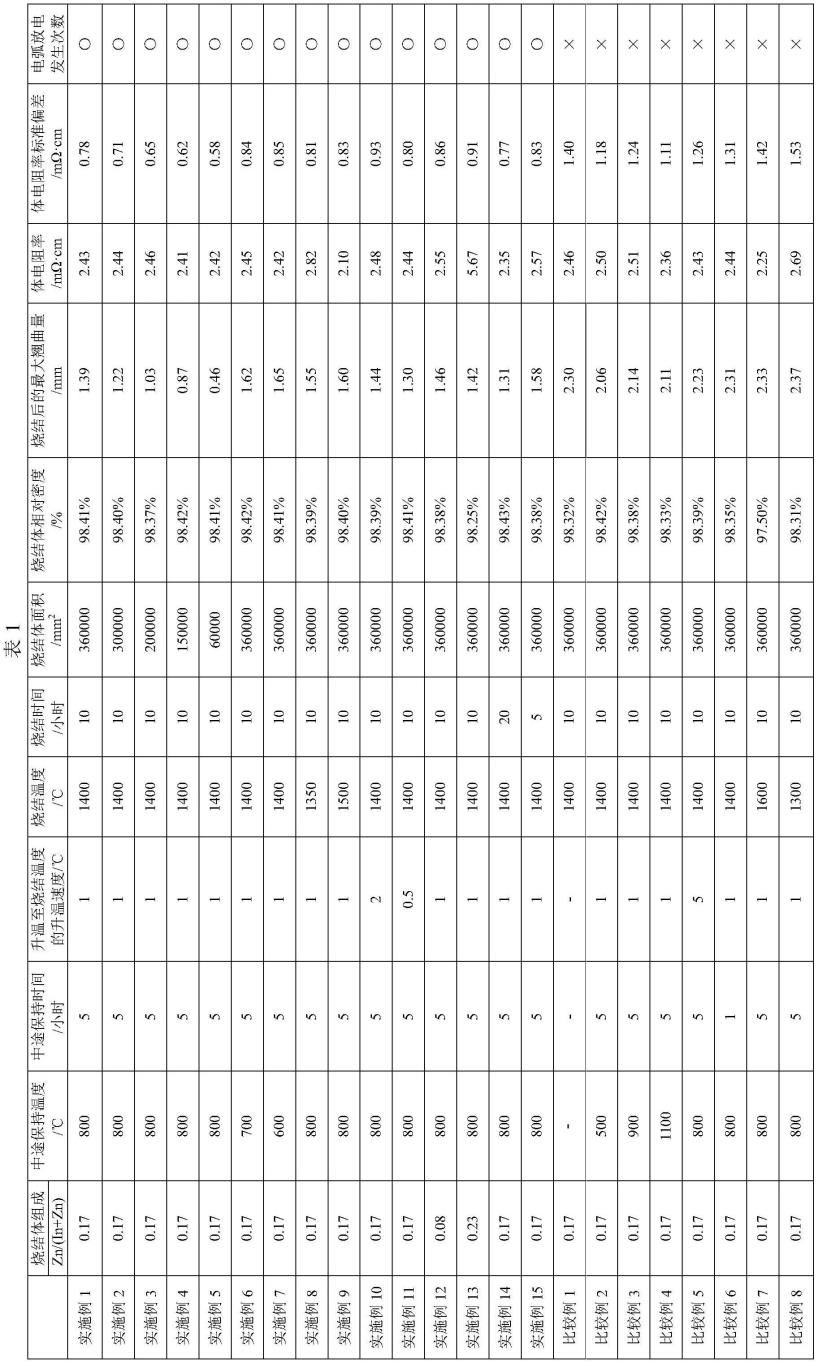
氧化铟-氧化锌类(izo)溅射靶及其制造方法
1.本技术是申请日为2016年12月28日、申请号为201611242711.5的中国专利申请的分案申请。
技术领域
2.本发明涉及氧化铟-氧化锌类(izo)溅射靶及其制造方法,特别是涉及靶的溅射面内的体电阻率的差小、适合于膜的形成的溅射靶及其制造方法。
背景技术:3.一些包含金属复合氧化物的透明导电膜具有高导电性和可见光透射性,因此可以用于液晶显示装置、薄膜电致发光显示装置、有机电致发光(el)、放射性检测装置、终端设备的透明输入板、窗玻璃的防结露用发热膜、防静电膜或太阳能集热器用选择性透射膜、触控面板的电极等多种多样的用途。在这样的包含金属复合氧化物的透明导电膜中,最普及的是被称为ito的包含氧化铟-氧化锡的透明导电膜。
4.另一方面,蚀刻速度比ito膜快的、以铟和锌的复合氧化物(称为“izo”)作为主要成分的透明导电膜的需求不断增加。制造izo膜时,使用烧结体溅射靶,但是该izo烧结体存在烧结过程中发生翘曲的问题。对于发生翘曲的靶,为了修整产品形状,需要对其两面进行磨削以形成平面,通过磨削处理,靶面内的体电阻率显著变化,存在溅射时发生异常放电等的问题。
5.接着,对涉及izo烧结体溅射的现有技术进行说明。专利文献1公开了将氧化铟和氧化锌混合,将其通过冷压和冷等静压成形,然后在氧气气氛中或大气中在1300℃~1500℃下进行加热烧结的技术。另外,专利文献2公开了在将in2o3与zno的粉末混合之前,仅对zno粉末进行煅烧的技术。
6.专利文献3记载了将氧化铟粉末与氧化锌粉末制成特定的性状的技术。另外,专利文献4记载了烧结izo时,直到达到1200℃为止,使氧浓度为21体积%以上,在1200℃~1450℃下,在氧浓度小于21体积%的气氛中进行烧结的技术。专利文献5记载了通过将原料粉末微细粉碎来控制靶的晶粒尺寸的技术。
7.然而,根据这些现有的制造工序,伴随着由烧结时的加热造成的热膨胀、热收缩,所制作的烧结体发生翘曲。将翘曲大的烧结体加工成靶形状时,有时靶的溅射面内的电阻率的差变大。这样的靶面内的电阻率的偏差在溅射时引起电弧放电(异常放电)等,存在使产品的成品率降低的问题。特别是伴随着近年来的溅射靶的大面积化,如上所述的问题变得显著。
8.现有技术文献
9.专利文献
10.专利文献1:日本特开2001-131736号公报
11.专利文献2:日本特开平9-111444号公报
12.专利文献3:日本特开2007-8780号公报
13.专利文献4:日本特开2007-8772号公报
14.专利文献5:国际公开第2001/038599号
技术实现要素:15.发明所要解决的问题
16.本发明为为了解决上述问题而作出的发明,本发明的课题在于,提供一种可以抑制溅射时电弧放电(异常放电)的发生、溅射面内的体电阻率的差小的溅射靶及其制造方法。特别是,本发明的课题在于,提供一种即使为大面积、体电阻率的面内的差也小的溅射靶。
17.用于解决问题的手段
18.为了解决上述的问题,本发明人进行了深入研究,结果发现:在izo的收缩即将开始或刚开始时暂时保持温度,从而减小烧结体内的温度分布,由此可以显著抑制烧结体的翘曲量。其结果是得到了以下发现:即使为了修整靶形状而对其两面进行磨削等以形成平面,也能够得到面内的体电阻率的差小的溅射靶。
19.基于这样的发现,本技术提供以下的发明。
20.1)一种溅射靶,其为包含in、zn、o的溅射靶,其特征在于,zn和in的原子比满足0.05≤zn/(in+zn)≤0.30,并且该靶的溅射面内的体电阻率的标准偏差为1.0mω
·
cm以下。
21.2)如上述1)所述的溅射靶,其特征在于,所述溅射靶的体电阻率为1.0mω
·
cm~10mω
·
cm。
22.3)如上述1)或2)所述的溅射靶,其特征在于,所述溅射靶的相对密度为98%以上。
23.4)如上述1)至3)中任一项所述的溅射靶,其特征在于,溅射面的面积为60000mm2~400000mm2。
24.5)一种izo烧结体,其为包含in、zn、o的烧结体,其特征在于,zn和in的原子比满足0.05≤zn/(in+zn)≤0.30,并且翘曲量为2.0mm以内。
25.6)一种溅射靶的制造方法,其为包含通过对将原料粉末压制成形而得到的成形体进行烧结而制造的izo烧结体的溅射靶的制造方法,其特征在于,在从室温升温至烧结温度的工序中,包含以下工序:将中途保持温度设定为600℃~800℃,并保持1小时~10小时的工序;以0.2℃/分钟~2.0℃/分钟的速度从该中途保持温度升温至烧结温度的工序;将烧结温度设定为1350℃~1500℃,并以1小时~100小时的烧结保持时间进行烧结的工序。
26.7)如上述6)所述的溅射靶的制造方法,其特征在于,将烧结温度设定为1380℃~1420℃。
27.8)如上述6)或7)所述的溅射靶的制造方法,其特征在于,以5小时~30小时的烧结保持时间进行烧结。
28.9)如上述6)至8)中任一项所述的溅射靶的制造方法,其特征在于,以1.0℃/分钟~5.0℃/分钟的速度进行降温。
29.10)如上述6)至9)中任一项所述的溅射靶的制造方法,其特征在于,以0.5℃/分钟~1.5℃/分钟的速度从中途保持温度升温至烧结温度。
30.发明效果
31.本发明发现在氧化铟-氧化锌类氧化物(izo)烧结体的制造方法中,在与以往不同的制造条件、即烧结条件中,在特定的温度下保持对于减少翘曲是有效的,具有以下优良效果:可以制作溅射面内的体电阻率差小的靶,其结果是能够实现电弧放电等的发生少的良好的溅射,并且能够提高所形成的膜的特性。本发明特别是在大面积的izo溅射靶方面有效。
附图说明
32.图1为表示本发明的溅射靶(方形)的体电阻率的测定位置的图。
33.图2为表示本发明的溅射靶(圆盘形)的体电阻率的测定位置的图。
34.图3为表示本发明的溅射靶的翘曲量的测定的示意图。
具体实施方式
35.本发明的溅射靶的成分组成如下:包含铟(in)、锌(zn)、氧(o),并且zn和in的原子比满足0.05≤zn/(in+zn)≤0.30的条件。本发明的靶主要由铟和锌的复合氧化物构成,但是可以含有氧化铟或氧化锌这样的单一氧化物。另外,在不损害本发明的特性的范围内,可以含有其它元素。上述zn的原子比是从使用靶形成的膜的导电性等的观点考虑而确定的,超出该范围时,无法得到所期望的特性。
36.本发明的特征在于,所述溅射靶的溅射面内的体电阻率的标准偏差为1.0mω
·
cm以下。烧结体的翘曲大的情况下,靶的溅射面的体电阻率的偏差变大,因此存在阻碍所形成的膜特性(特别是膜电阻)的均匀性的问题。本发明中,通过调节烧结条件来显著减少烧结体的翘曲,由此能够将溅射面内的体电阻率的标准偏差减小至1.0mω
·
cm以下。需要说明的是,溅射面是指对烧结体进行磨削并加工为溅射靶后、在溅射装置中被溅射的面。
37.本发明的体电阻率优选为1.0mω
·
cm以上且10mω
·
cm以下。体电阻率高时,有时使溅射放电不稳定。对于本发明的体电阻率,利用四探针法,对靶的溅射面以等间隔测定16个点以上(方形靶的情况)或9个点以上(圆盘形靶的情况),计算其平均值和标准偏差。例如,如图1、2所示,对距靶端部20mm以上的内侧部分以50mm~60mm的等间隔对15mm见方的部位进行三次测定,将其平均值作为该部位的体电阻率。但是,在靶的面积小的情况下,通过缩小测定间隔,保证测定点数为9个点以上或16个点以上。需要说明的是,测定靶的体电阻率时,可以根据需要进行磨削。
38.一般而言,烧结体的面积越大,翘曲量也越大。本发明的特征在于,即使为大面积的烧结体,也能够将其翘曲量抑制在2.0mm以内。特别是,即使靶的溅射面的面积为60000mm2~400000mm2的大面积,也能够将溅射面内的电阻率差抑制在上述范围内,本发明在这一方面是优良的。在此,翘曲的测定如下进行:使用激光式位移传感器,将该激光作为探针,根据烧结体的尺寸,以图2所示的方式用激光扫描烧结体的任意一侧的面,同时测定其高度。然后,将面内的最大高度和最小高度的差作为最大翘曲量。
39.另外,本发明的溅射靶的特征在于,相对密度为98%以上的高密度。高密度靶可以减少溅射时的粉粒等,并且能够形成具有良好的特性的膜。相对密度由下式表示:(通过阿基米德法测定得到的烧结体的实际密度)/(由氧化物的组成计算出的理论密度)
×
100=相对密度(%)。在此,由氧化物的组成计算出的理论密度是指由构成原料的元素计算出的理
论密度,例如以氧化铟(in2o3)粉、氧化锌(zno)粉作为原料,将氧化铟:氧化锌的重量比设定为90重量%:10重量%时,通过以下方式进行计算:由氧化物的组成计算出的理论密度=(氧化铟的理论密度
×
90+氧化锌的理论密度
×
10)/100(g/cm3)。
40.本发明的氧化铟-氧化锌类氧化物(izo)烧结体靶可以经过以下的原料的混合、粉碎、成型、烧结的各步骤来制作。
41.(原料的混合、粉碎、造粒、成型的条件)
42.准备氧化铟(in2o3)粉、氧化锌(zno)粉作为原料粉。原料粉优选使用比表面积为约5m2/g的原料粉。
43.具体而言,使用体积密度:0.5g/cm3~0.7g/cm3、中值粒径(d
50
):1.0μm~2.1μm、比表面积:4.0m2/g~5.7m2/g的氧化铟粉;体积密度:0.2g/cm3~0.6g/cm3、中值粒径(d
50
):1.0μm~2.5μm、比表面积:3.0m2/g~6.0m2/g的氧化锌粉。
44.接着,称量各原料粉以达到所期望的组成比,然后进行混合粉碎。作为粉碎方法,根据所要求的粒度、被粉碎物质而存在各种方法,珠磨机等湿式介质搅拌磨机是适合的。其为将使粉末分散于水中而得到的浆料与作为高硬度材料的氧化锆、氧化铝等粉碎介质一起强制搅拌的方法,可以高效地得到粉碎粉。但是,此时,由于粉碎介质也磨损,粉碎介质自身以杂质的形式混入粉碎粉中,因此不优选长时间的处理。
45.如果用粉碎前后的比表面积的差来定义粉碎量,在湿式介质搅拌磨机中粉碎量与对粉末的输入能量大致成比例。因此,在进行粉碎时,控制湿式介质搅拌磨机的累计功率是重要的。将粉碎前后的比表面积之差(δbet)调节为0.5m2/g~3.0m2/g,将粉碎后的中值粒径(d
50
)调节为1.0μm以下。
46.接着,进行微粉碎后的浆料的造粒。这是为了通过造粒提高粉末的流动性,由此在下一工序的压制成型时将粉末均匀地填充至模具中,从而得到均质的成形体。造粒有各种方式,作为得到适合于压制成型的造粒粉的方法之一,存在使用喷雾式干燥装置(喷雾干燥器)的方法。其为将粉末制成浆料,以液滴的形式分散在热风中并使其瞬间干燥的方法,能够连续地得到10μm~500μm的球形的造粒粉。
47.在使用喷雾干燥器进行的干燥中,控制热风的入口温度和出口温度是重要的。如果入口和出口的温度差大,则每单位时间的干燥量增加、生产率提高,但是入口温度过高时,有时粉末和所添加的粘结剂由于热而变质,从而无法得到期望的特性。另外,出口温度过低时,有时造粒粉无法充分干燥。
48.另外,通过在浆料中添加聚乙烯醇(pva)等粘结剂并使其包含于造粒粉中,能够提高成形体的强度。pva的添加量为相对于原料粉添加50cc/kg~250cc/kg的含有6重量%pva的水溶液。此外,也可以通过添加适合作为粘结剂的增塑剂来调节压制成型时的造粒粉的压碎强度。另外,也有通过将少量的水添加到所得到的造粒粉中使其湿润来提高成形体强度的方法。
49.接着,进行压制成型。将造粒粉填充于模具中,保持400kgf/cm2~1000kgf/cm2的压力1分钟~3分钟而进行成形。压力小于400kgf/cm2时,无法得到具有足够的强度和密度的成形体,另外,压力为1000kgf/cm2以上时,将成形体从模具中取出时,有时成形体自身由于解除压力造成的变形而破坏,生产上不优选。
50.(烧结工序)
51.使用电炉在氧气气氛中对成形体进行烧结,从而得到烧结体。升温至烧结温度1350℃~1500℃。在升温过程中,为了减小烧结体内的温度分布而引入保持工序。关于中途保持温度,为了在反应开始前的温度区域内减小烧结体内的温度分布,以600℃~800℃的温度引入即可。低于600℃的情况下,温度过低而看不到效果,温度高于900℃的情况下,由于反应已经进行到一定程度,因此无法得到减小翘曲的效果。中途保持时间设定为1小时~10小时,优选设定为4小时~6小时。保持时间过短时,无法充分抑制反应的进行,另一方面,保持时间过长时,生产率降低,因此不优选。
52.然后,以0.2℃/分钟~2.0℃/分钟的速度从中途保持温度升温至烧结温度。从中途保持温度到烧结温度的升温速度小于0.2℃/分钟时,有时为了达到规定的温度需要不必要的时间,并且密度不会增大,升温速度大于2.0℃/分钟时,烧结体内的温度分布产生不均匀而不会减小,或者烧结体破裂。优选为0.5℃/分钟~1.5℃/分钟。
53.烧结温度设定为1350℃~1500℃,保持约1小时~约100小时,然后,随炉冷却或者以1.0℃/分钟~5.0℃/分钟的降温速度降温。烧结温度低于1350℃时,无法得到高密度的烧结体。另外,1500℃以上的烧结温度下,由于氧化锌的挥发,产生烧结密度的降低或组成偏差,另外,也存在炉加热器寿命减少的成本问题,因此优选将上限设定为1500℃。优选为1380℃~1420℃。另外,烧结温度下的保持时间短于1小时时,烧结未充分进行,烧结体的密度无法充分提高或者烧结体发生翘曲。即使保持时间超过100小时,也仅产生需要不必要的能量和时间的浪费,生产上不优选。优选为5小时~30小时。
54.实施例
55.接着,对本发明的实施例进行说明。实施例、比较例中,在上述记载的条件下实施了制作将氧化铟-氧化锌类氧化物(izo)烧结体的原料粉末压制成形而得到的成形体的工序,此外,在上述记载的条件的范围内适当设定并实施烧结工序。各烧结体的组成如表1所示。
56.实施例等中的电弧放电试验使用synchron制造的磁控溅射装置(型号:bsc7011),在直流功率密度:2.3w/cm2、气压:0.6pa、气体流量300sccm的条件下,在氩气气氛中进行了35小时连续溅射,研究了电弧放电的发生状态。对于电弧放电的检测,使用landmark technology制造的微电弧监控器(mam genesis)测定了电弧放电(微电弧)发生次数(次)。电弧放电的判断基准为对检测电压100v以上、释放能量(发生电弧放电时的溅射电压
×
溅射电流
×
发生时间)为20mj以下的电弧放电进行计数,若为10次以下则记为〇,若超过10次则记为
×
。
57.(实施例1)
58.实施例1中,将最高烧结温度设定为1400℃,将烧结保持时间设定为10小时、将中途保持温度设定为800℃。其结果是烧结体的密度为98.41%,最大翘曲值为1.39mm。另外,为了将烧结体修整为靶形状而对其两面进行磨削以形成平面,结果靶的体电阻率为2.43mω
·
cm,其标准偏差为0.78mω
·
cm。实施例1中得到了像这样烧结体的翘曲量小、靶的体电阻率的偏差小的良好的结果。另外,使用以这样的方式制作的靶进行溅射,结果几乎观察不到电弧放电的发生。将以上结果示于表1。
[0059][0060]
(实施例2-15)
[0061]
在实施例2-15中,分别改变了以下各条件:烧结体的组成、最高烧结温度、烧结保
持时间、中途保持温度、中途保持时间、从中途保持温度到烧结保持温度的升温速度、烧结体的面积。其结果如表1所示,烧结体的密度均为98%以上,最大翘曲值均为2.0mm以内。另外,为了将烧结体修整为靶形状而对其两面进行磨削以形成平面,结果靶的体电阻率均为1.0mω
·
cm~10mω
·
cm,其标准偏差均为1.0mω
·
cm以内。实施例2-15中得到了像这样烧结体的翘曲量小、靶的体电阻率的偏差小的良好的结果。另外,使用这些靶进行溅射,结果几乎观察不到电弧放电的发生。
[0062]
(比较例1)
[0063]
比较例1中,将最高烧结温度设定为1400℃,将烧结保持时间设定为10小时,未进行中途保持。其结果是烧结体的最大翘曲值为2.30mm。另外,为了将烧结体修整为靶形状而对其两面进行磨削以形成平面,结果靶的体电阻率的标准偏差为1.40mω
·
cm。比较例1中,得到了像这样烧结体的翘曲量大、靶的体电阻率的偏差大的结果。另外,使用以这样的方式制作的靶进行溅射,结果电弧放电的发生多。
[0064]
(比较例2)
[0065]
比较例2中,将最高烧结温度设定为1400℃,将烧结保持时间设定为10小时,将中途保持温度降低至500℃。其结果是烧结体的最大翘曲值为2.06mm。另外,为了将烧结体修整为靶形状而对其两面进行磨削以形成平面,结果靶的体电阻率的标准偏差为1.18mω
·
cm。比较例2中,得到了像这样烧结体的翘曲量大、靶的体电阻率的偏差大的结果。另外,使用以这样的方式制作的靶进行溅射,结果电弧放电的发生多。
[0066]
(比较例3)
[0067]
比较例3中,将最高烧结温度设定为1400℃,将烧结保持时间设定为10小时,将中途保持温度升高至900℃。其结果是烧结体的最大翘曲值为2.14mm。另外,为了将烧结体修整为靶形状而对其两面进行磨削以形成平面,结果靶的体电阻率的标准偏差为1.24mω
·
cm。比较例3中,得到了像这样烧结体的翘曲量大、靶的体电阻率的偏差大的结果。另外,使用以这样的方式制作的靶进行溅射,结果电弧放电的发生多。
[0068]
(比较例4)
[0069]
比较例4中,将最高烧结温度设定为1400℃,将烧结保持时间设定为10小时,将中途保持温度升高至1100℃。其结果是烧结体的最大翘曲值为2.11mm。另外,为了将烧结体修整为靶形状而对其两面进行磨削以形成平面,结果靶的体电阻率的标准偏差为1.11mω
·
cm。比较例4中,得到了像这样烧结体的翘曲量大、靶的体电阻率的偏差大的结果。另外,使用以这样的方式制作的靶进行溅射,结果电弧放电的发生多。
[0070]
(比较例5)
[0071]
比较例5中,将最高烧结温度设定为1400℃,将烧结保持时间设定为10小时、将中途保持温度设定为800℃,将从中途保持温度到最高烧结温度的升温速度提高至5℃/分钟。其结果是烧结体的最大翘曲值为2.23mm。另外,为了将烧结体修整为靶形状而对其两面进行磨削以形成平面,结果靶的体电阻率的标准偏差为1.26mω
·
cm。比较例5中,得到了像这样烧结体的翘曲量大、靶的体电阻率的偏差大的结果。另外,使用以这样的方式制作的靶进行溅射,结果电弧放电的发生多。
[0072]
(比较例6)
[0073]
比较例6中,将最高烧结温度设定为1400℃,将烧结保持时间设定为10小时,将中
途保持温度设定为800℃,将中途保持时间缩短至1小时。其结果是烧结体的最大翘曲值为2.31mm。另外,为了将烧结体修整为靶形状而对其两面进行磨削以形成平面,结果靶的体电阻率的标准偏差为1.31mω
·
cm。比较例6中,得到了像这样烧结体的翘曲量大、靶的体电阻率的偏差大的结果。另外,使用以这样的方式制作的靶进行溅射,结果电弧放电的发生多。
[0074]
(比较例7)
[0075]
比较例7中,将中途保持温度设定为800℃,将最高烧结温度升高至1600℃。其结果是烧结体的最大翘曲量为2.33mm,相对密度为97.5%。另外,为了将烧结体修整为靶形状而对其两面进行磨削以形成平面,结果靶的体电阻率的标准偏差为1.42mω
·
cm。比较例7中,得到了像这样烧结体的翘曲量大、靶的体电阻率的偏差大的结果。另外,使用以这样的方式制作的靶进行溅射,结果电弧放电的发生多。
[0076]
(比较例8)
[0077]
比较例8中,将中途保持温度设定为800℃,将最高烧结温度升高至1500℃。其结果是烧结体的最大翘曲量为2.37mm。另外,为了将烧结体修整为靶形状而对其两面进行磨削以形成平面,结果靶的体电阻率的标准偏差为1.53mω
·
cm。比较例8中,得到了像这样烧结体的翘曲量大、靶的体电阻率的偏差大的结果。另外,使用以这样的方式制作的靶进行溅射,结果电弧放电的发生多。
[0078]
产业实用性
[0079]
如上所述,本发明利用与以往不同的烧结条件,能够以良好的成品率制作翘曲小的烧结体,由此,具有能够显著提高生产率的优良效果。另外,本发明通过减小烧结体的翘曲,具有以下优良效果:可以减小对该烧结体进行加工后的靶的溅射面的体电阻率的偏差,可以形成特性均匀的膜。本发明的溅射靶在用于液晶显示装置、薄膜电致发光显示装置、有机电致发光(el)等的透明导电膜的形成中有用。