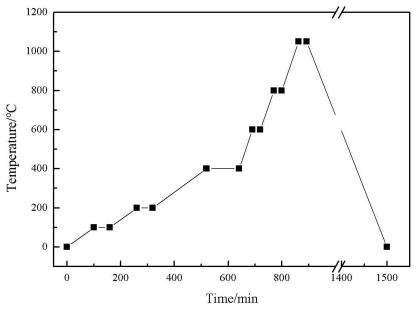
1.本发明涉及一种用于轻合金熔模铸造的热压铸水溶性陶瓷型芯及其制备方法,属于熔模精密铸造领域。
背景技术:2.随着汽车、航空以及船舶等工业的快速发展,对具有复杂结构的负载件和结构件需求量日益增加,这对铸造生产提出了更高的要求。采用铝、镁轻合金熔模精密铸件代替组合零件,有助于提高装备的可靠性,但也使得铸件结构变得更加复杂,给铸造生产带来一定的难度,尤其是对于具有复杂结构的薄壁铸件,其形成内腔所用型芯的选择和应用是获得优质铸件的关键。铝、位合金强度低,型芯去除不能采用大机械力去除型芯,而且在许多此类铸件中,型芯与外界相通的部分尺寸较小,不易施加机械力,此外,铸件内腔往往具有不规则的形状作用力很难传递到整个型芯。采用具有良好水溶溃散性能的型芯,是解决此类具有复杂内腔轻合金熔模铸件成形制造的关键。
3.近年来,以在水中具有良好溶解性能的盐制备的盐芯受到较多的关注,并在实际生产中得到一定的应用。但在使用中发现。水溶性盐芯存在强度低、收缩大、脆性大、吸湿强等缺点,在熔模铸造长时间的制壳制造过程中易吸湿潮解发生脱落,影响铸件的形状和尺寸精度,甚至过早溃散,使制壳失败,制约了水溶性盐芯在熔模精密铸造中的应用,也影响了相关合金铸件的开发与应用。
4.与单纯水溶性盐制备的盐芯相比,以耐火材料为基体,水溶性盐为粘结剂的水溶性陶瓷型芯,在保证良好水溶溃散性的同时,不仅具有良好的尺寸精度和在潮湿环境中更高的稳定性,而且水溶性盐的用量显著减少,对型芯材料的回收再利用更为有利。
5.水溶性陶瓷型芯可以采用多种成形工艺制造,但不同的方法有各自的局限性,如压制成形,适用于形状简单型芯的制造;注浆成形,可用于复杂形状型芯的制造,但由于浆料含有较多水分,存在干燥、烧结耗时长,收缩大的不足;热压铸成形,可用于复杂形状型芯的制造,但也存在生产周期长的不足。当然,为满足不同成形工艺的特点,陶瓷型芯的原料组成也不同。
技术实现要素:6.发明目的:本发明的第一目的在于提供一种用于轻合金熔模铸造的热压铸水溶性陶瓷型芯,可用于具有复杂空腔结构的铝、镁合金熔模精密铸件生产;本发明的第二目的在于提供一种该热压铸水溶性陶瓷型芯的热压铸的成型方法,指导热压铸水溶性陶瓷型芯的实际应用。
7.技术方案:本发明的所述一种用于轻合金熔模铸造的热压铸水溶性陶瓷型芯,所述热压铸水溶性陶瓷型芯包括电熔刚玉粉、硫酸钾、增塑剂、润滑剂和表面活性剂,其重量比为60~80:7.7~30:10~15:1~2:1~2。
8.其中,所述增塑剂包括石蜡、蜂蜡、聚乙烯、硬脂酸和油酸,其重量比为90~95:2~4:2~4:1~2:1~2。
9.其中,所述润滑剂为石墨粉或丙三醇。
10.其中,所述表面活性剂为十二烷基硫酸钠或硬脂酰胺。
11.本发明所述用于轻合金熔模铸造的热压铸水溶性陶瓷型芯的制备方法,采用热压铸成型方法成型,再通过高温烧结制成,包括以下步骤:
12.(1)将电熔刚玉粉、硫酸钾和表面活性剂混合、烘干,球磨,得到混合陶瓷粉料;
13.(2)将增塑剂和润滑剂搅拌混合,并在搅拌条件下分批加入混合陶瓷粉料,继续搅拌,得到具有一定流动性的浆料;
14.(3)预热模具,将浆料压入模具中,保压热压铸,待浆料凝固后打开模具,得到生坯;
15.(4)将生坯烧结,得到热压铸水溶性陶瓷型芯。
16.优选地,步骤(1)中,烘干的温度为110~120℃,烘干的时间为1~3h。
17.优选地,步骤(1)中,球磨时球磨机的转速为250~350r/min,球磨的时间为1.5~2h。
18.优选地,步骤(2)中,搅拌时的温度为70~80℃,搅拌时搅拌器的转速为200~300r/min,连续搅拌的时间为10-12h。
19.优选地,步骤(3)中,保压热压铸工艺参数:温度为70~80℃,压力为0.2~0.4mpa,保压的时间为6~8s。
20.优选地,步骤(3)中,预热模具是将模具预热到40~50℃。
21.优选地,步骤(4)中,包括在空气气氛中以1℃/min的速度缓慢升至400℃,保温2h,以4℃/min的速度升至1000~1100℃,保温0.5~1.0h。
22.优选地,步骤(4)中,烧结的温度为1000~1100℃,烧结的时间为0.5~1.5h。
23.本发明以电熔刚玉粉为耐火骨料,硫酸钾为水溶性盐粘结剂,添加适量增塑剂、润滑剂和表面活性剂,采用热压铸工艺制备陶瓷型芯坯体,再经高温烧结得到水溶性陶瓷型芯。由于电熔刚玉粉为两性氧化物,高温烧结时会与碱性或者酸性粘结剂发生反应,生成难溶于水的物质,影响陶瓷型芯的溃散性能,而采用中性的硫酸钾为粘结剂,制备得到的具有良好溃散性的氧化铝基陶瓷型芯不仅具有良好的尺寸精度和适宜的强度,而且清砂的方式绿色环保。以电熔刚玉粉为耐火骨料,硫酸钾为无机粘结剂的陶瓷型芯很好的解决了可溶性盐芯脆性大、吸湿能力强以及成形时收缩大等不足,且具有良好的水溶溃散性,采用热压铸成形方法可以满足实际生产对复杂形状型芯的需要。
24.有益效果:与现有技术相比,本发明具有如下显著优点:本发明制备得到的具有良好溃散性的氧化铝基陶瓷型芯不仅具有良好的尺寸精度和适宜的强度,而且稳定性强、精度高的优点,降低了水溶性盐的用量,且保持了良好的水溶溃散性,清砂的方式绿色环保。通过热压铸成型得到水溶性氧化铝基陶瓷型芯,可以制备复杂的精密铸件,满足实际生产对复杂形状型芯的需要。
附图说明
25.图1为实施例1陶瓷型芯烧结程序图;
26.图2为陶瓷型芯抗弯强度与硫酸钾添加量的关系图;
27.图3为陶瓷型芯收缩率与硫酸钾添加量的关系图;
28.图4为陶瓷型芯溶解后质量损失率与硫酸钾添加量的关系图。
具体实施方式
29.下面结合附图对本发明的技术方案作进一步说明。
30.本发明采用微机控制电子万能试验机,使用三点弯曲法测试室温抗弯强度,参数为:标距为30mm,加载速率为0.5mm/min。
31.测量试样烧结前后的长度,按照公式测量陶瓷型芯烧结前后的收缩率s
l
,其中,l
0-烧结前的长度(mm),l
1-烧结后的长度(mm)。
32.用称量的方法测量陶瓷型芯溶解前后质量,计算陶瓷型芯溶解质量损失率,具体步骤为:在浸泡前称取样品的重量,m1,在80℃的水中浸泡3h后超声清洗3min,然后洗净表面的小颗粒,在120℃烘箱中烘干5h,称取剩余的样品的质量m2,按公式计算陶瓷型芯的质量损失率w。
33.实施例1
34.(1)按照下列重量份称取电熔刚玉粉、硫酸钾、十二烷基硫酸钠、石蜡、蜂蜡、聚乙烯、硬脂酸、石墨粉和油酸,其中,电熔刚玉粉70重量份,硫酸钾30重量份,十二烷基硫酸钠1重量份,增塑剂13重量份,石墨粉1重量份;增塑剂包括90重量份的石蜡、4重量份的蜂蜡、4重量份的聚乙烯、1重量份的硬脂酸和2重量份的油酸;
35.(2)将称量好的电熔刚玉粉、硫酸钾和十二烷基硫酸钠放入烘箱中,在110℃的温度下1h烘干,将烘干的混合料装入行星式球磨机的球磨罐中,在250r/min的转速下球磨1.5h,得到混合陶瓷粉料;
36.(3)将石蜡、蜂蜡、聚乙烯、硬脂酸、石墨粉以及油酸依次加入不锈钢搅拌罐内,混合的温度为70℃,待增塑剂和润滑剂混合均匀后,分批加入混合好的混合陶瓷粉料,搅拌器的转速为200r/min,待混合陶瓷粉料全部加入后,将混合物料连续搅拌10h,得到具有一定流动性的浆料;
37.(4)将模具在40℃的鼓风烘箱中预热1h,用注蜡机将浆料压入模具中,采用热压铸的方法制备陶瓷型芯,保压热压铸工艺参数为:注蜡机温度为70℃,热压铸压力为0.2mpa,保压时间为6s,待浆料凝固后打开模具取出生坯;
38.(5)将制得的生坯放入箱式炉中,按照设定的烧结程序:在空气气氛中以1℃/min的速度缓慢升至100℃,保温1h,然后以1℃/min的速度缓慢升至200℃,保温1h,接着以1℃/min的速度缓慢升至400℃,保温2h,除去坯料中的有机挥发物,随后以4℃/min的速度升至600℃,保温0.5h,再以4℃/min的速度升至800℃,保温0.5h,最后以4℃/min的速度升至1050℃,保温1.0h,得到热压铸水溶性陶瓷型芯,采用微机控制电子万能试验机测定其抗弯强度,抗弯强度为4.01mpa,热压铸陶瓷型芯的收缩率为-1.34%,用称量的方法测量压铸水溶性陶瓷型芯溶解前后质量,计算压铸水溶性陶瓷型芯溶解质量损失率,80℃水浴溶解6h,压铸水溶性陶瓷型芯完全溃散。
39.实施例2
40.研究硫酸钾添加量对热压铸陶瓷型芯性能影响,具体制备过程同实施例1,其他重量份不变,硫酸钾分别为硫酸钾30重量份、23.3重量份、17.5重量份、12.3重量份和7.7重量份,热压铸陶瓷型芯的抗弯强度如图2所示,收缩率如图3所示,80℃水浴溶解6h的质量损失率如图4所示。
41.图2为陶瓷型芯抗弯强度与硫酸钾添加量的关系图,由图2可以看出,随着硫酸钾添加量的增加,陶瓷型芯的抗弯强度不断下降;可以根据实际需求进行调节。
42.图3为陶瓷型芯收缩率与硫酸钾添加量的关系图,由图3可以看出,随着硫酸钾添加量的增加,陶瓷型芯的收缩率不断下降;
43.图4为陶瓷型芯溶解后质量损失率与硫酸钾添加量的关系图,由图4可以看出,随着硫酸钾添加量的增加,陶瓷型芯的溶解后质量损失率不断上升。
44.实施例3
45.(1)按照下列重量份称取电熔刚玉粉、硫酸钾、十二烷基硫酸钠、石蜡、蜂蜡、聚乙烯、硬脂酸、石墨粉和油酸,其中,电熔刚玉粉80重量份,硫酸钾20重量份,十二烷基硫酸钠2重量份,增塑剂12重量份,石墨粉1重量份;增塑剂包括90重量份的石蜡、2重量份的蜂蜡、2重量份的聚乙烯、2重量份的硬脂酸和1重量份的油酸;
46.(2)将称量好的电熔刚玉粉、硫酸钾和十二烷基硫酸钠放入烘箱中,在120℃的温度下1h烘干,将烘干的混合料装入行星式球磨机的球磨罐中,在300r/min的转速下球磨2h,得到混合陶瓷粉料;
47.(3)将石蜡、蜂蜡、聚乙烯、硬脂酸、石墨粉以及油酸依次加入不锈钢搅拌罐内,混合的温度为70℃,待增塑剂和润滑剂混合均匀后,分批加入混合陶瓷粉料,搅拌器的转速为250r/min,待混合陶瓷粉料全部加入后,将混合物料连续搅拌10h,得到具有一定流动性的浆料;
48.(4)将模具在50℃的鼓风烘箱中预热1h,用注蜡机将浆料压入模具中,采用热压铸的方法制备陶瓷型芯,保压热压铸工艺参数为:注蜡机温度为70℃,热压铸压力为0.4mpa,保压时间为7s,,待浆料凝固后打开模具取出生坯;
49.(5)将制得的生坯放入箱式炉中,具体的烧结程序:最终的烧结温度为1000℃,保温时间为1h,其他升温程序同实施例1,得到压铸水溶性陶瓷型芯。采用微机控制电子万能试验机测定其抗弯强度,抗弯强度为7.42mpa,热压铸陶瓷型芯的收缩率为-1.44%,用称量的方法测量压铸水溶性陶瓷型芯溶解前后质量,计算压铸水溶性陶瓷型芯溶解质量损失率,80℃水浴溶解6h,压铸水溶性陶瓷型芯质量损失率为59.93%。
50.实施例4
51.(1)按照下列重量份称取电熔刚玉粉、硫酸钾、十二烷基硫酸钠、石蜡、蜂蜡、聚乙烯、硬脂酸、石墨粉和油酸,其中,电熔刚玉粉60重量份,硫酸钾20重量份,十二烷基硫酸钠1重量份,增塑剂14重量份,石墨粉1重量份;增塑剂包括95重量份的石蜡、4重量份的蜂蜡、2重量份的聚乙烯、1重量份的硬脂酸和2重量份油酸。
52.(2)将称量好的电熔刚玉粉、硫酸钾和十二烷基硫酸钠放入烘箱中,在120℃的温度下3h烘干,将烘干的混合料装入行星式球磨机的球磨罐中,在350r/min的转速下球磨1.5h,得到混合陶瓷粉料;
53.(3)将石蜡、蜂蜡、聚乙烯、硬脂酸、石墨粉以及油酸依次加入不锈钢搅拌罐内,混
合的温度为80℃,待增塑剂和润滑剂混合均匀后,分批加入混合陶瓷粉料,搅拌器的转速为300r/min,待混合陶瓷粉料全部加入后,将混合物料连续搅拌12h,得到具有一定流动性的浆料;
54.(4)将模具在45℃的鼓风烘箱中预热1h,用注蜡机将浆料压入模具中,采用热压铸的方法制备陶瓷型芯,保压热压铸工艺参数为:注蜡机温度为80℃,热压铸压力为0.2mpa,保压时间为7s,待浆料凝固后打开模具取出生坯;
55.(5)将制得的生坯放入箱式炉中,具体的烧结程序:最终的烧结温度为1100℃,保温时间为1h,其他升温程序同实施例1,得到压铸水溶性陶瓷型芯。采用微机控制电子万能试验机测定其抗弯强度,抗弯强度为5.01mpa,热压铸陶瓷型芯的收缩率为-0.64%,用称量的方法测量压铸水溶性陶瓷型芯溶解前后质量,计算压铸水溶性陶瓷型芯溶解质量损失率,80℃水浴溶解6h,压铸水溶性陶瓷型芯质量损失率为31.78%。
56.实施例5
57.(1)按照下列重量份称取电熔刚玉粉、硫酸钾、十二烷基硫酸钠、石蜡、蜂蜡、聚乙烯、硬脂酸、石墨粉和油酸,其中,电熔刚玉粉60重量份,硫酸钾10重量份,十二烷基硫酸钠1重量份,增塑剂12重量份,石墨粉1重量份;增塑剂包括90重量份的石蜡、4重量份的蜂蜡、2重量份的聚乙烯、1重量份的硬脂酸和2重量份的油酸;
58.(2)将称量好的电熔刚玉粉、硫酸钾和十二烷基硫酸钠放入烘箱中,在120℃的温度下1h烘干,将烘干的混合料装入行星式球磨机的球磨罐中,在300r/min的转速下球磨2h,得到混合陶瓷粉料;
59.(3)将石蜡、蜂蜡、聚乙烯、硬脂酸、石墨粉以及油酸依次加入不锈钢搅拌罐内,混合的温度为70℃,待增塑剂和润滑剂混合均匀后,分批加入混合陶瓷粉料,搅拌器的转速为250r/min,待混合陶瓷粉料全部加入后,将混合物料连续搅拌10h,得到具有一定流动性的浆料;
60.(4)将模具在50℃的鼓风烘箱中预热1h,用注蜡机将浆料压入模具中,采用热压铸的方法制备陶瓷型芯,保压热压铸工艺参数为:注蜡机温度为70℃,热压铸压力为0.4mpa,保压时间为7s,待浆料凝固后打开模具取出生坯;
61.(5)将制得的生坯放入箱式炉中,具体的烧结程序:最终的烧结温度为1000℃,保温时间为1h,其他升温程序同实施例1,得到压铸水溶性陶瓷型芯。采用微机控制电子万能试验机测定其抗弯强度,抗弯强度为10.29mpa,热压铸陶瓷型芯的收缩率为-1.68%,用称量的方法测量压铸水溶性陶瓷型芯溶解前后质量,计算压铸水溶性陶瓷型芯溶解质量损失率,80℃水浴溶解6h,压铸水溶性陶瓷型芯质量损失率为31.23%。
62.对比例1
63.对比粘结剂种类对陶瓷型芯性能影响,具体工艺同实施例1,不同之处在于粘结剂为碳酸钠,得到陶瓷型芯抗弯强度为5.01mpa,80℃水浴6h后陶瓷型芯质量损失率为20%。相对于实施例1中陶瓷型芯80℃水浴溶解6h,陶瓷型芯完全溃散,以硫酸钾为粘结剂的陶瓷型芯的水溶溃散性能更好。
64.对比例2
65.研究耐火骨料对陶瓷型芯性能影响,具体工艺同实施例1,不同之处在于耐火骨料为莫来石粉,得到陶瓷型芯抗弯强度为12.43mpa,80℃水浴6h后陶瓷型芯质量损失率为
10%。相对于实施例1中陶瓷型芯80℃水浴溶解6h,陶瓷型芯完全溃散,以电熔刚玉粉为耐火骨料的陶瓷型芯的水溶溃散性能更好。
66.对比例3
67.研究烧结温度对陶瓷型芯的性能影响,具体工艺同实施例1,不同之处在于陶瓷型芯的最终烧结温度为1200℃,得到陶瓷型芯抗弯强度为1.53mpa,80℃水浴6h后陶瓷型芯质量损失率为20.23%,随着烧结温度的增加,型芯在烧结过程中硫酸钾的烧损量增加,型芯的强度和质量损失都下降。