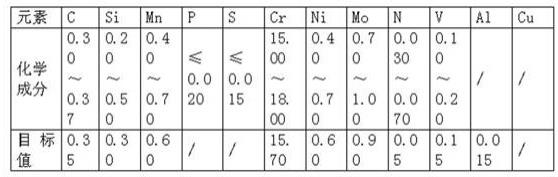
1.本发明属大型马氏体不锈钢主轴锻件制造技术领域,具体涉及一种不仅能够提高向钢液中吹氮气的成功率,而且能够获得组织性能优良和化学成分均匀的冲击性能高的马氏体不锈钢主轴及其生产方法。
背景技术:2.马氏体不锈钢主轴应用于大型聚酯反应釜的制造,根据聚酯工业规模化生产需要,超长主轴的需求日益增加,但因其合金含量高,导热性差,锻件细长比大,化学成分极易不均匀,产生成分偏析,冲击性能不稳定;在锻造生产过程中,因加热及变形过程温度控制不当极易产生δ铁素体,碳化物液析、网状组织加剧,甚至锻造开裂无法使用等问题,传统生产工艺流程难以实现该产品的稳定批量生产,产品使用性能提升困难。
技术实现要素:3.本发明的目的在于克服现有技术中存在的不足而提供一种冲击性能高的马氏体不锈钢主轴及其生产方法,通过化学成分配比优化设计,采用电炉冶炼+感应炉冶炼-lf钢包精炼-vd真空脱气-浇注电极坯-热切冒口、热焊假电极-氩气保护电渣重熔-热送加热-1180℃~1220℃温度范围内压机开坯+精锻机锻造成型-锻后正火+回火-粗加表面-调质处理的生产方法,生产出满足冲击性能要求的不锈钢主轴锻件。
4.本发明的目的是这样实现的:一种冲击性能高的马氏体不锈钢主轴,采用电炉冶炼+感应炉冶炼-lf钢包精炼-vd真空脱气-浇注电极坯-热切冒口、热焊假电极-氩气保护电渣重熔-热送加热-1180℃~1220℃温度范围内压机开坯+精锻机锻造成型-锻后正火+回火-粗加表面-调质处理;按照质量百分比马氏体不锈钢主轴的化学成分为:[c]:0.30-0.37%、[si]:0.20-0.50%、[mn]:0.40-0.70%、[p]≤0.020、[s]≤0.015、[cr]:15.00-18.00%、[ni]:0.40-0.70%、[mo]:0.70-1.00%、[v]:0.10-0.30%、[n]:0.030-0.07%,余量为铁。
[0005]
一种所述的冲击性能高的马氏体不锈钢主轴的生产方法,具体生产方法如下:步骤1)、进行电炉冶炼和感应炉冶炼:电炉炉料包括废钢25t、钢屑10t、生铁10t,加料前炉内提前加入0.5~1.0t增碳剂及0.5~1.5t石灰;熔清后造泡沫渣,边吹氧边流渣测温t=1590℃,取样检测化学成分:[c]=1.13%、[p]=0.042%、[as]=0.008%、[sn]=0.002%、[pb]=0.001%、[sb]=0.002%、[bi]=0.001%,期间继续吹氧进行脱碳、脱磷操作;测温t=1652℃,取样检测化学成分:[c]=0.09%、[p]=0.002%,满足出钢条件电炉出钢,出钢过程中严禁下渣;出钢1/4~3/4过程中向钢包中加入铝块80kg、石灰240kg及350kg锰铁;感应炉炉料包括对应的低磷中高合金钢返回料头和钢屑3t、中碳铬铁4t、低碳铬铁15t、钼铁700kg、镍板300kg炉料,料头表面干净无油污,料头直径≤φ800mm,长度≤1500mm;料头及钢屑使用前,采用便携式光谱仪确认成分,确保入炉料头、钢屑成分、尺寸符
合使用要求,保证兑钢后合金元素及c、p不超出工艺要求上限;在感应炉炉底垫入20kg石灰,石灰无碳块、杂物,装料下紧上松,料的方向与炉子纵向一致,长料不允许横放或斜放;感应炉炉料熔清,测温t=1587℃,取样[c]=0.69%、[p]=0.033%、[cr]=39.7%,感应炉出钢,出钢前加入铝线66kg脱氧;步骤2)、进行lf钢包精炼、vd真空脱气、浇注电极坯和热切冒口、热焊假电极:精炼钢包中兑入40t的电炉钢水和23t的感应炉钢水,在精炼工位接通氩气,分3批加入800kg石灰后送电化渣,前期加入电石60kg和硅铁粉或硅钙粉250kg进行脱氧,精炼造好白渣后取样分析:[c]=0.31%、[p]=0.013%、[cr]=15.04%、[mo]=0.62%、[mn]=0.41%、[ni]=0.47%、[v]=0.07%;期间按照20kg/批次加入硅铁粉或硅钙粉粉状脱氧剂共120kg,精炼过程加入中碳锰铁160kg、中碳铬铁1.7t、钼铁400kg、镍板90kg、钒铁132kg调整成分,整个过程保持白渣至出钢,温度1632℃转入真空罐脱气;脱气后取样检测:[c]=0.35%、[p]=0.015%、[s]=0.003%、[si]=0.47%、[cr]=15.71%、[mo]=0.89%、[mn]=0.60%、[ni]=0.62%、[v]=0.15%;将氩气改为氮气,采用600nl/min吹氮20min后取样检测氮含量0.050-0.080%,温度1610~1640℃自lf炉吊包转入真空罐脱气,在≤0.7mbar下保持时间12分钟,切换氮气吹氮8分钟,抬盖、测温、取样,分析氮含量0.042%,出钢浇注ф800规格电极坯;电极坯脱模后使用火焰切割机将冒口切除,然后在≥400℃的温度下热焊假电极;步骤3)、进行氩气保护电渣重熔:重熔前对电极坯表面氧化皮进行清理,对焊缝处焊渣进行清理,在30分钟内将电极坯放入预热炉内进行预热,在450℃以上预热4h以上;采用氩气保护电渣重熔,氩气流量为70-20nm3/h;化渣开始前先吹氩气5-10min,流量为40-20nm3/h,停电后炉口继续密封20min以上;渣料采用caf2:al2o3:cao=65:30:5,渣量为700kg,渣料放置烘烤炉内,在600℃以上烘烤4小时后降温至400℃保温,随取随用;重熔时加脱氧剂100-110克/5分钟,补缩期加45-55克/5分钟,控制熔化率750-940kg/h,重熔为15.8吨的电渣锭,电渣锭热送下道工序加热;步骤4)、进行热送加热并在1180℃~1220℃温度范围内压机开坯,然后精锻机锻造成型,具体如下:电渣锭温度650-750℃时热送燃气炉,保温7.5小时后以5.5℃/h的速度升温至1200℃
±
10℃,保温25小时后吊出燃气炉,第一次锻造使用5000吨油压快锻机,采用宽度700mm的上平下v型砧子,每道次变形量控制在80~150mm,将尾端拔长至φ610mm;坯料返回燃气炉加热至1180℃后保温3小时吊出燃气炉,第二次锻造使用5000吨油压快锻机,采用宽度700mm的上平下v型砧子,每道次变形量控制在100~150mm,将冒端拔长至φ610mm;坯料返回燃气炉加热至1050℃后保温3小时吊出燃气炉,第三次锻造采用rf70型号精锻机以90mm的下锤量锻打成型;步骤5)、锻后进行正火和回火:锻坯温度700-750℃℃,吊至电炉,以60℃/h的速度升温至860℃
±
10℃,均温和保温34小时后,以15℃/h的速度降温至小于等于120℃后出炉检测;步骤6)、粗加表面并进行调质处理:调质处理前对坯料表面黑色氧化皮进行机加工,加工后检查表面无裂纹缺陷时,装入卧式电阻炉中,在500℃温度下预热2小时后,最大功率升温至800℃后预热1小时,然后
再升温至1000℃
±
10℃保温8小时后,吊出工件进行淬火处理,淬火介质选用水基淬火液,水基液初始温度小于等于30℃,浓度12%,冷却方式采用空冷-水基淬火液冷-空冷-水基淬火液冷-空冷-水基淬火液冷冷却方式,工件淬火后装入卧式电阻炉中,升温至688-692℃后保温25小时,出炉空冷至室温后取样检测力学性能,工件装入卧式电阻炉中,升温至658
±
10℃后保温25小时后出炉空冷。
[0006]
本发明具有如下积极效果:本发明提供的一种马氏体不锈钢主轴应用于大型聚酯反应釜的制造,根据聚酯工业规模化生产需要,超长主轴的需求日益增加,但因其合金含量高,导热性差,锻件细长比大,化学成分极易不均匀,产生成分偏析,δ铁素体、碳化物液析、网状组织加剧,产品使用性能难以提升。
[0007]
本发明提供的不锈钢主轴的化学成分设计为:[c]:0.30-0.37%、[si]:0.20-0.50%、[mn]:0.40-0.70%、[cr]:15.00-18.00%、[ni]:0.40-0.70%、[mo]:0.70-1.00%、[v]:0.10-0.30%、[n]:0.030-0.07%。本发明通过对马氏体不锈钢主轴的化学成分配比进行优化设计,减少δ铁素体的析出;在成分设计基础上,对冶炼过程成分均匀性控制和加热、变形过程温度进行创造性研究,进一步改善主轴碳化物液析和网状组织,最终获得成分组织均匀性好,冲击性能优的主轴锻件。采用该成分生产出的主轴锻件,解决了δ铁素体及碳化物的析出等问题,获得金相组织优良、冲击性能满足使用要求的主轴产品。本发明不仅能够提高向钢液中吹氮气的成功率,而且能够获得化学成分均匀性高和组织、冲击性能优良主轴锻件,同时本发明提高马氏体不锈钢主轴冲击性能的生产方法,具有如下优点:1、采用氮气替代氮化合金来调整成分,可以降低冶炼生产成本。
[0008]
2、氮气可直接溶入不饱和的钢液中,减少钢液二次污染,提高冶炼生产效率;3、通过不同阶段氮气吹入时机和吹入量的控制,实现对钢液的连续搅拌,达到均匀成分和温度的目的。
[0009]
4、通过氮气合金化进行化学成分优化后,可减少δ铁素体的析出,改善碳化物液析,从而达到提高冲击性能的目的。
附图说明
[0010]
图1为本发明的锻造加热工艺曲线。
[0011]
图2为本发明的锻后退火工艺曲线。
[0012]
图3为本发明的调质热处理工艺曲线。
具体实施方式
[0013]
实施例1:12.3吨主轴及其生产工艺如下:以该产品60吨钢水冶炼工艺为例,冶炼工艺化学成分设计如下表1:表1化学成分设计(余量为铁)
步骤1)、冶炼工艺:步骤1.1)、电炉炉料包括废钢25t、钢屑10t、生铁10t,加料前炉内提前加入0.5~1.0t增碳剂及0.5~1.5t石灰;熔清后造泡沫渣,边吹氧边流渣测温t=1590℃,取样检测化学成分:[c]=1.13%、[p]=0.042%、[as]=0.008%、[sn]=0.002%、[pb]=0.001%、[sb]=0.002%、[bi]=0.001%,期间继续吹氧进行脱碳、脱磷操作;测温t=1652℃,取样检测化学成分:[c]=0.09%、[p]=0.002%,满足出钢条件电炉出钢,出钢过程中严禁下渣;出钢1/4~3/4过程中向钢包中加入铝块80kg、石灰240kg及350kg锰铁。
[0014]
感应炉炉料包括对应的低磷中高合金钢返回料头和钢屑3t、中碳铬铁4t、低碳铬铁15t、钼铁700kg、镍板300kg等炉料,料头表面干净无油污,料头直径≤φ800mm,长度≤1500mm;料头及钢屑使用前,采用便携式光谱仪确认成分,确保入炉料头、钢屑成分、尺寸符合使用要求,保证兑钢后合金元素及c、p不超出工艺要求上限。
[0015]
感应炉炉底垫入20kg石灰,石灰无碳块、杂物,装料下紧上松,料的方向与炉子纵向一致,长料不允许横放或斜放。感应炉炉料熔清,测温t=1587℃,取样[c]=0.69%、[p]=0.033%、[cr]=39.7%,感应炉出钢,出钢前加入铝线66kg脱氧。
[0016]
步骤1.2)、在精炼钢包中兑入42t的电炉钢水和22.7t的感应炉钢水,在精炼工位接通氩气,分3批加入800kg石灰后送电化渣,前期加入电石60kg,硅铁粉(或硅钙粉)250kg进行脱氧,精炼造好白渣后取样分析:[c]=0.31%、[p]=0.013%、[cr]=15.04%、[mo]=0.62%、[mn]=0.41%、[ni]=0.47%、[v]=0.07%;期间按照20kg/批次加入硅铁粉(或硅钙粉)等粉状脱氧剂共120kg,精炼过程加入中碳锰铁160kg、中碳铬铁1.7t、钼铁400kg、镍板90kg、钒铁132kg调整成分,整个过程保持白渣至出钢,温度1632℃转入真空罐脱气;脱气后取样检测:[c]=0.35%、[p]=0.015%、[s]=0.003%、[si]=0.47%、[cr]=15.71%、[mo]=0.89%、[mn]=0.60%、[ni]=0.62%、[v]=0.15%。 将氩气改为氮气,采用600nl/min吹氮20min后取样检测氮含量0.050-0.080%,温度1610~1640℃自lf炉吊包转入真空罐脱气,在≤0.7mbar下保持时间12分钟,切换氮气吹氮8分钟,抬盖、测温、取样,分析氮含量0.042%,出钢浇注ф800规格电极坯;电极坯脱模后使用火焰切割机将冒口切除,然后在≥400℃的温度下热焊假电极。
[0017]
步骤2)、电渣重熔工艺:重熔前对电极坯表面氧化皮进行清理,电极坯与假电极焊接完成后,对焊缝处焊渣进行清理,在30分钟内将电极坯放入预热炉内进行预热,在450℃以上预热4h以上;采用氩气保护电渣重熔,氩气流量为70-20nm3/h;化渣开始前先吹氩气5-10min,流量为40-20nm3/h,停电后炉口继续密封20min以上;渣料采用caf2:al2o3:cao=65:30:5,渣量为700kg,渣料放置烘烤炉内,在600℃以上烘烤4小时后降温至400℃保温,随取随用;重熔时
加脱氧剂100-110克/5分钟,补缩期加45-55克/5分钟,控制熔化率750-940kg/h,重熔为15.8吨的电渣锭,电渣锭热送下道工序加热。
[0018]
步骤3)、加热及锻造工艺:如图1所示,电渣锭温度650-750℃时热送燃气炉,保温7.5小时后以5.5℃/h的速度升温至1200℃
±
10℃,保温25小时后吊出燃气炉,第一次锻造使用5000吨油压快锻机,采用宽度700mm的上平下v型砧子,每道次变形量控制在80~150mm,将尾端拔长至φ610mm;坯料返回燃气炉加热至1180℃后保温3小时吊出燃气炉;第二次锻造使用5000吨油压快锻机,采用宽度700mm的上平下v型砧子,每道次变形量控制在100~150mm,将冒端拔长至φ610mm;坯料返回燃气炉加热至1050℃后保温3小时吊出燃气炉;如图2所示,第三次锻造采用rf70型号精锻机以90mm的下锤量锻打成型;锻坯温度700-750℃,吊至电炉,以60℃/h的速度升温至860℃
±
10℃,均温和保温34小时后,以15℃/h的速度降温至小于等于120℃后出炉检测。
[0019]
步骤4)、调质热处理工艺:如图3所示,调质处理前对坯料表面黑色氧化皮进行机加工,加工后检查表面无裂纹缺陷时,装入卧式电阻炉中,在500℃温度下预热2小时后,最大功率升温至800℃后预热1小时,然后再升温至1000℃
±
10℃保温8小时后,吊出工件进行淬火处理,淬火介质选用水基淬火液,水基液初始温度小于等于30℃,浓度12%,冷却方式采用空冷-水基淬火液冷-空冷-水基淬火液冷-空冷-水基淬火液冷冷却方式,工件淬火后装入卧式电阻炉中,升温至688-692℃后保温25小时,出炉空冷至室温后取样检测力学性能,工件装入卧式电阻炉中,升温至658
±
10℃后保温25小时后出炉空冷。
[0020]
表2调质后力学性能结果炉锭号屈服强度拉伸强度延伸率面缩冲击功ku2akv标准要求≥550750-950≥14≥40≥20 10a21218-冒59079020.545.523/28/251510a21218-尾59080023.54727/29/2517