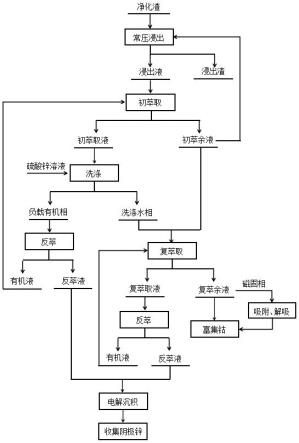
1.本发明属于金属回收技术领域,具体涉及一种从湿法炼锌净化渣中富集钴的方法。
背景技术:2.金属钴广泛用于航空航天、机械制造、化学和陶瓷等行业。随着我国经济的发展,钴的消费量在持续增加,但我国钴资源稀缺,大型含钴矿床稀少,大部分钴是以较低品位伴生于其他金属矿床之中。目前在对金属锌的开采利用过程中发现,锌矿石中伴生的少量钴在锌矿石的选矿过程中得以富集,然后在湿法炼锌过程中以净化渣的形式分离出来。随着我国湿法炼锌产能的不断扩大,湿法炼锌产生的净化渣(含钴废渣)也在不断增多,且含钴废渣由于会造成一定的环境污染而不能任意排放,因此,对湿法炼锌净化渣中的钴进行提取利用,不仅可以减轻企业环保压力,还能回收稀缺的金属钴,提高资源利用率。
3.目前,对该含钴废渣的处理一般采用以下方法:(1)选择性浸出法:该工艺在一定条件下浸出含钴渣,使大部分的锌溶解于溶液中,而将钴留在浸出渣中,达到锌和钴分离富集的目的,但该工艺在实际应用中只能部分分离锌、钴,达不到锌、钴高效分离回收的目的;(2)氨-硫酸铵法:现有论文(赵延凯,唐谟堂.湿法炼锌净化钴渣新处理工艺[j].中南工业大学学报,2001,32(4):371-375.)采用氨水和硫酸铵体系,在氧化剂的作用下浸出烘烤过的含钴渣,再采用锌粉净化法对浸出上清液进行深度净化并进行锌与镉、钴、铜等的分离,除钴后的溶液采用铵溶液电解法生产电解锌,而对含钴渣再进行进一步的处理,该方法并没有对钴进行有效富集及回收利用。申请号为cn201811319116.6的中国专利公开了一种从锌粉净化渣中回收钴的方法,是将锌粉净化渣通过湿法球磨得到浆料;浆料采用磁选分离,磁性成分即为富钴渣,磁选尾渣返回炼锌系统回收锌;该方法虽然工艺简单、无三废产生,但是净化渣中金属成分复杂,并不能很好地解离出纯钴组分。
[0004]
由于湿法炼锌净化渣中锌元素的含量远高于钴,对钴的回收利用会造成严重干扰,因此,从含锌、钴溶液中实现锌、钴的有效分离是回收钴要解决的主要难题。
技术实现要素:[0005]
基于现有技术的不足,本发明的目的在于提供了一种从湿法炼锌净化渣中富集钴的方法,经过硫酸浸出、初萃取及复萃取后,分离出锌,经反萃、电解沉积实现回收,萃余液经磁固相萃取达到富集钴的目的,工艺流程短,节省了人力物力。
[0006]
为了实现上述目的,本发明采用的技术方案为:一种从湿法炼锌净化渣中富集钴的方法,包括以下步骤:(1)采用10~15%硫酸常压浸出处理净化渣,浸出温度为40~60℃、浸出时间20~40 min,液固比(3~7):1,经固液分离,得到含锌、钴的浸出液及含锌、铜、镉的浸出渣;(2)将步骤(1)所得含锌、钴的浸出液的ph调节为2.5~5,采用二(2-乙基己基)磷酸酯(p204)和磺化煤油(260号航空煤油)组成萃取有机相,对步骤(1)所得含锌、钴的浸出液
进行初萃取,得到初萃取液与初萃余液;(3)将步骤(2)所得初萃取液经过含锌盐溶液洗涤,得到负载有机相和洗涤水相;将步骤(2)所得初萃余液返回浸出处理中,循环浸出和初萃取处理,将循环两次以上后得到的初萃余液与洗涤水相合并,得到含锌、钴的萃余液;(4)采用2-乙基己基磷酸单2-乙基己基脂(p507)、磷酸三丁酯(tbp)及磺化煤油组成复合萃取剂,对步骤(3)所得含锌、钴的萃余液进行复萃取,得到复萃取液与复萃余液;所述复合萃取剂中,2-乙基己基磷酸单2-乙基己基脂所占的质量百分数为20~30%、磷酸三丁酯所占的质量百分数为3~10%;(5)将步骤(3)所得负载有机相及步骤(4)所得复萃取液分别经反萃后,合并反萃液,将反萃液直接电解沉积,回收锌;(6)对步骤(4)所得复萃余液采用磁固相富集钴;其中,所述磁固相是以铁氧体为磁性内核、表面依次经硅烷化及胺基接枝而成。
[0007]
优选地,步骤(2)所述萃取有机相中二(2-乙基己基)磷酸酯所占的质量百分数为10~20%;萃取有机相的使用量为含锌、钴的浸出液体积的0.8~3倍。
[0008]
优选地,步骤(3)中所述含锌盐溶液为0.3~0.6 mol/l的硫酸锌溶液,含锌盐溶液的使用量为初萃取液体积的0.05~0.2倍,洗涤时间为3~10分钟。
[0009]
优选地,步骤(4)中所述复合萃取剂的使用量为含锌、钴的萃余液体积的0.8~2倍。
[0010]
优选地,步骤(2)中所述初萃取及步骤(4)中所述复萃取采用震荡方式,震荡时间为5~15分钟。
[0011]
优选地,步骤(5)中所述反萃采用10~20%的稀硫酸作为反萃剂,进行2~3级反萃,每级反萃的时间为3~10分钟,反萃剂的总使用量为负载有机相及复萃取液总体积的1~2倍。
[0012]
优选地,步骤(5)中所述电解沉积采用反萃之后的溶液直接电解,控制条件为:温度25~40℃、电流密度为300~500 a/m2、电压3.0~5.0 v,处理效率为0.3~0.8 l/h。
[0013]
优选地,步骤(6)中所述磁固相通过震荡的方式从复萃余液中萃取钴,再在外部磁场作用下,将磁固相转移至洗脱溶剂中洗脱,从而达到富集钴的作用。
[0014]
优选地,所述磁固相的烷基化采用γ-氨丙基三乙氧基硅烷进行处理,所述磁固相的胺基接枝采用二亚乙基三胺进行处理,所述洗脱溶剂为温度35~50℃、质量百分数1.5~2.5%的稀硫酸。
[0015]
优选地,初萃取液经反萃后得到的有机液返回初萃取循环,复萃取液经反萃后得到的有机液返回复萃取循环。
[0016]
当含锌、钴溶液中钴浓度较低时,无论氧化沉淀还是置换脱除效果均不理想,且可能引入其他杂质。因此,本发明采用溶剂萃取法从溶液中萃取锌,再从萃取后的溶液中富集钴,通过对萃取过程中ph、有机相等条件的控制,实现锌、钴的分离,有机相在多次循环使用中性能稳定,萃取过程中没有出现乳化和第三相的现象。初萃取时,选择萃取能力强的p204,p204萃取锌时析出的h
+
会使溶液的ph下降,故初萃取前将含锌、钴溶液调节呈酸性,但ph不易过低,这样可以保证锌有较高的萃取率;复萃取时,采用选择性好的p507,通过加入少量的tbp形成良好协同作用的萃取体系,抑制第三相的生成,进一步完成锌的萃取。
[0017]
本发明工艺简单、无特殊装备要求,易于实现产业化,萃取周期短,且在萃取等工序中不会引入新的杂质,萃取中所用的有机液可返回重新使用,初萃余液中的硫酸也可以
循环重用,节省了成本投入,回收的锌纯度高、杂质少,同时钴的富集为其有效利用创造有利条件,具有很好的经济价值。
附图说明
[0018]
图1为本发明所述从湿法炼锌净化渣中富集钴的工艺流程图。
具体实施方式
[0019]
为了使本发明的技术目的、技术方案和有益效果更加清楚,下面结合具体实施例对本发明的技术方案作出进一步的说明,但所述实施例旨在解释本发明,而不能理解为对本发明的限制,实施例中未注明具体技术或条件者,按照本领域内的文献所描述的技术或条件或者按照产品说明书进行。
[0020]
实施例1一种从湿法炼锌净化渣中富集钴的方法,如图1所示,包括以下步骤:(1)采用10%硫酸常压浸出处理净化渣(主要含zn、cd、cu、co,其中含zn 25.36%、co 4.40%),浸出温度为45℃、浸出时间30 min,液固比5:1,经固液分离,得到含锌、钴的浸出液及含锌、铜、镉的浸出渣(返回湿法炼锌);利用原子吸收光谱法测定含锌、钴的浸出液,锌的浸出率为83.5%、钴的浸出率为92.3%;(2)用naoh溶液将步骤(1)所得含锌、钴的浸出液的ph调节为4,采用p204和260号航空煤油组成萃取有机相(15wt% p204),萃取有机相与含锌、钴的浸出液的体积比(即相比o/a)为1:1,震荡10 min进行初萃取,得到初萃取液与初萃余液;(3)将步骤(2)所得初萃取液用0.4 mol/l的硫酸锌溶液洗涤,硫酸锌溶液与初萃取液的体积比(即相比a/o)为1:10,洗涤5分钟后,得到负载有机相和洗涤水相;将步骤(2)所得初萃余液返回浸出处理中,循环浸出和初萃取处理,将循环两次后(经浸出-初萃取-再浸出-再初萃取),得到的初萃余液与洗涤水相合并,得到含锌、钴的萃余液;(4)采用p507、tbp和260号航空煤油组成复合萃取剂(25wt% p507、5wt% tbp),对步骤(3)所得含锌、钴的萃余液进行复萃取,复合萃取剂与含锌、钴的萃余液体积相同(相比o/a 1:1),震荡8 min进行复萃取,得到复萃取液与复萃余液;(5)将步骤(3)所得负载有机相及步骤(4)所得复萃取液分别采用15%的稀硫酸作为反萃剂,进行三级反萃,每次反萃剂的使用量按照相比a/o为0.5:1(即反萃剂的总使用量为负载有机相及复萃取液总体积1.5倍),每级反萃的时间为4分钟;初萃取液经反萃后得到的有机液返回初萃取循环,复萃取液经反萃后得到的有机液返回复萃取循环,合并初萃取液与复萃取液经反萃后得到的反萃液;将反萃液采用电解沉积直接电解,收集阴极锌;控制条件为:温度30℃、电流密度为400 a/m2、电压3.0~5.0 v,处理效率为0.6 l/h;(6)将步骤(4)所得复萃余液中加入磁固相(使用量1 g/l),震荡萃取10 min,再在外部磁场作用下,将磁固相转移至洗脱溶剂中解吸,达到富集钴的作用。
[0021]
下面分别从步骤(2)中ph的调节及p204的占比、步骤(4)中p507及tbp的占比作为影响因子,通过检测锌、钴含量讨论各参数调整对效果的影响,其中一个影响因子调整时,另外两个影响因子仍按照实施例1中给出的参数保持不动。
[0022]
a)步骤(1)中ph的调节:分别调节含锌、钴的浸出液的ph为2、3、4、5、6,检测初萃取
液中锌、钴含量,然后计算锌和钴的萃取率(用初萃取液中的含量除以含锌、钴的浸出液中的含量),结果为:ph=2时,锌萃取率31.47%、钴萃取率0.56%;ph=3时,锌萃取率39.51%、钴萃取率0.57%;ph=4时,锌萃取率45.01%、钴萃取率0.71%;ph=5时,锌萃取率39.22%、钴萃取率1.04%;ph=6时,锌萃取率26.32%、钴萃取率2.27%。
[0023]
b)步骤(2)中p204的占比分别调整为10wt%、15wt%、20wt%、25wt%,检测初萃取液中锌、钴含量,然后计算锌和钴的萃取率,结果为:p204占比10wt%时,锌萃取率37.39%、钴萃取率0.66%;p204占比15wt%时,锌萃取率44.34%、钴萃取率0.72%;p204占比20wt%时,锌萃取率47.19%、钴萃取率1.14%;p204占比25wt%时,锌萃取率49.00%、钴萃取率2.21%。
[0024]
c)步骤(4)中p507的占比分别调整为15wt%、20wt%、25wt%、30wt%,检测复萃取液中锌含量,然后计算锌的累积萃取率(用复萃取液中锌的含量除以含锌、钴的浸出液中锌的含量),结果为:p507占比15wt%时,锌累积萃取率73.62%;p507占比20wt%时,锌累积萃取率89.88%;p507占比25wt%时,锌累积萃取率94.93%;p507占比30wt%时,锌累积萃取率96.14%。
[0025]
d)步骤(4)中tbp的占比分别调整为0、3wt%、5wt%、10wt%,检测复萃取液中锌含量,然后计算锌的累积萃取率,结果为:不含tbp时,锌累积萃取率65.36%;tbp占比3wt%时,锌累积萃取率80.95%;tbp占比5wt%时,锌累积萃取率93.70%;tbp占比10wt%时,锌累积萃取率86.24%。
[0026]
从上述检测结果可以看出,p204作为萃取剂时,钴的萃取率远低于锌,虽然p204萃取锌需要在酸性条件下进行,但是萃取过程中析出的h
+
会使溶液的ph下降,故初萃取前ph不易过低;在萃取水相ph为4时,锌与钴的萃取率相差最大,此时锌的萃取率最大,通过初萃取就能将锌分离出去近一半,而钴绝大部分仍保留于水溶液中。p204浓度越高,锌与钴的萃取率均增加,考虑到萃取剂用量与成本的问题,同时减少初萃取中钴的流失,选择15wt% p204(260号航空煤油作为稀释溶剂)。另外,从p507和tbp的检测数据中可以看出,tbp的加入可以极大地增加p507的萃取率,经过复萃取后,锌的累积萃取率最高可达96.14%。
[0027]
实施例2在实施例1的基础上,步骤(6)中所述磁固相采用以铁氧体为磁性内核、表面依次经硅烷化及胺基接枝而成,具体如下:将铁氧体粉碎、过筛,得到粒度1250目的铁氧体粉(采用普通市售产品,比饱和磁矩约为10~70 am/kg、矫顽力80~600 a/m),经水洗后控干水份,真空干燥2 h;然后将15 g铁氧体粉分散于250 ml乙醇与丙酮(v:v=7:3)的混合液中,在氮气气氛下,升温至60℃,再加入10 ml γ-氨丙基三甲氧基硅烷,保持溶液体系的密闭回流,恒温搅拌8小时,然后固液分离,取固体用乙醇洗涤,于90℃真空干燥4 h,得到硅烷化磁粉;取10 g硅烷化磁粉分散于225 ml 乙醇与水(v:v=7:3)的混合液中,在氮气气氛下,升温至80℃,加入11.3 ml二亚乙基三胺,保持溶液体系的密闭回流,恒温搅拌8小时,然后固液分离,取固体用乙醇、水交替洗涤,控干水份后,于90℃真空干燥3 h,得到胺基接枝磁粉,即磁固相。通过γ-氨丙基三甲氧基硅烷的架桥作用,将二亚乙基三胺偶联接枝到铁氧体表面,提高铁氧体的耐酸性、离子交换性和亲和能力,能够与钴形成配位键合,从而萃取溶液中的钴。磁固相萃取钴后解吸时,采用温度为40℃、2%的稀硫酸作为洗脱溶剂,洗脱溶剂与复萃余液的体积比(即相比a/o)为1:20。
[0028]
本发明实现了锌、钴的有效分离,通过计算本发明得到的阴极锌的质量与净化渣
中锌的质量的比值,得出整个工艺中锌的回收率约为80%;通过检测洗脱后的溶液中钴浓度及含锌、钴的浸出液中钴浓度,得出钴的浓度被提高了约16.5倍。
[0029]
最后应说明的是:以上各实施例仅用以说明本发明的技术方案,而非对其限制;尽管参照前述各实施例对本发明进行了详细的说明,本领域的普通技术人员应当理解:其依然可以对前述各实施例所记载的技术方案进行修改,或者对其中部分或者全部技术特征进行等同替换;而这些修改或者替换,并不使相应技术方案的本质脱离本发明各实施例技术方案的范围。