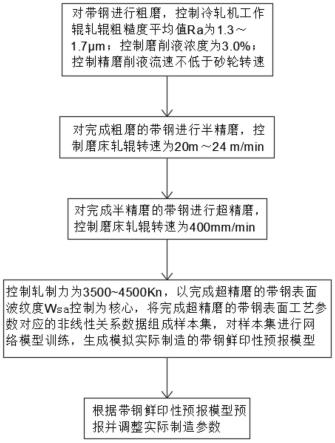
1.本技术涉及金属的轧制技术领域,尤其涉及一种冷轧带钢的光整制造方法及设备。
背景技术:2.冷轧带钢是指以薄钢板为原料,在常温下经光整机轧制成的带状钢材。光整工艺是指不切除或从工件上切除极薄材料层,以减小工件表面粗糙度为目的的加工方法。高鲜印性是指镀层均匀,表面平坦,没有厚边缺陷和气刀条痕缺陷,且在涂漆后漆膜光亮。带钢表面鲜印性的高低关系到带钢制品的表面形貌、光洁度及涂装性能。影响带钢表面鲜印性的因素主要有工作辊波纹度wca、工作辊粗糙度值ra,工作辊粗糙度峰值rpc。由于实际生产中对冷轧带钢鲜印性难以预测和调控,目前市场上大量的带钢制品都无法满足汽车合资主机厂对外板高鲜印性的要求。
技术实现要素:3.为了准确预测并控制制造出的冷轧带钢的鲜印性参数,
4.一方面,本技术提供一种冷轧带钢的光整制造方法,包括以下步骤:
5.对带钢进行粗磨,控制光整机工作辊粗糙度平均值ra为1.3~1.7μm;控制磨削液浓度为3.0%;控制精磨削液流速不低于砂轮转速;
6.对完成粗磨的带钢进行半精磨,控制磨床工作辊转速为20m~24m/min;
7.对完成半精磨的带钢进行超精磨,控制磨床工作辊转速为400mm/min;
8.控制轧制力为3500~4500kn,以完成超精磨的带钢表面波纹度wsa控制为核心,将完成超精磨的带钢表面工艺参数对应的非线性关系数据组成样本集,对样本集进行网络模型训练,生成模拟实际制造的带钢鲜印性预报模型;
9.根据带钢鲜印性预报模型预报并调整实际制造参数。
10.进一步,所述带钢表面工艺参数包括轧制力、工作辊粗糙度、磨床工作辊转速、砂轮直径、精磨液流速。
11.进一步,所述带钢鲜印性预报模型包括误差修正、网络模型训练,预报计算。
12.进一步,所述误差修正包括以下步骤:
13.计算错误函数e;
14.判断是否收敛判断,当结果为是时,输出网络参数;
15.当判断结果为否时,重新计算网络参数;
16.将计算结果输入网络模型训练。
17.进一步,所述网络模型训练包括以下步骤:
18.将训练样本作为学习样本输入;
19.对学习样本数据归一化;
20.判断是否进行学习训练;
21.当判断结果为是时,进入网络模型训练;
22.当判断结果为否时,将归一化的数据作为赋值预报模型参数。
23.进一步,所述预报计算包括以下步骤:
24.验证样本;
25.对验证样本数据归一化;
26.输入赋值预报模型参数;
27.判断是否执行预报,当判断结果为否时,结束命令;
28.当判断结果为是时,对赋值预报模型参数和归一化的验证样本数据进行预报计算,输出结果后结束命令。
29.进一步,砂轮粒度采用100#,砂轮直径为800~900mm。
30.进一步,光整机工作最优辊工作辊粗糙度ra为1.5μm,精磨削液最优流速为14m/min。
31.另一方面,本技术还提供一种冷轧带钢的光整制造设备,包括:
32.第一制造单元,用于对带钢进行粗磨,粗磨过程控制光整机工作辊粗糙度平均值ra为1.3~1.7μm;
33.第二制造单元,用于对完成粗磨的带钢进行半精磨,半精磨过程控制磨床工作辊转速为20m~24m/min,磨削液浓度为3.0%;控制精磨削液流速不低于砂轮转速;
34.第三制造单元,用于对完成半精磨的带钢进行超精磨,控制磨床工作辊转速为400mm/min;控制精磨削液流速不低于砂轮转速;
35.第四制造单元,用于根据超精磨表面工艺参数生成模拟实际制造的带钢鲜印性预报模型;
36.第五制造单元,用于根据带钢鲜印性预报模型预报并调整实际制造参数。
37.进一步,所述所述第四制造单元用于根据超精磨表面工艺参数生成模拟实际制造的带钢鲜印性预报模型,包括控制带钢鲜印性预报模型轧制力为3500~4500kn,以完成超精磨的带钢表面波纹度wsa控制为核心,将完成超精磨的带钢表面工艺参数对应的非线性关系数据组成样本集,对样本集进行网络模型训练。
38.有益效果:
39.本技术通过模拟冷轧带钢的制造过程,在冷轧前期控制带钢制造参数,依次对带钢进行粗磨、半精磨、超精磨,获得超精磨的带钢;根据经过超精磨的带钢表面参数,以完成超精磨的带钢表面波纹度wsa控制为核心,将完成超精磨的带钢表面工艺参数对应的非线性关系数据组成样本集,对样本集进行网络模型训练,生成模拟实际制造的带钢鲜印性预报模型;根据带钢鲜印性预报模型预报的带钢鲜印性制造结果,选择最优制造参数集,调整冷轧带钢制造设备的实际制造参数,获得满足市场高鲜印性要求的带钢。
附图说明
40.为了更清楚地说明本技术实施例技术方案,下面将对实施例描述中所需要使用的附图作简单地介绍,显而易见地,下面描述中的附图是本技术的一些实施例,对于本领域普通技术人员来讲,在不付出创造性劳动的前提下,还可以根据这些附图获得其他的附图。
41.图1是本技术实施例1提供的一种冷轧带钢的光整方法流程图;
42.图2是本技术实施例2提供的一种冷轧带钢的光整设备图;
43.图3是本技术实施例3提供的带钢鲜印性预报模型工作逻辑图;
具体实施方式
44.下面将结合本技术实施例中的附图,对本技术实施例中的技术方案进行清楚、完整地描述。
45.实施例1
46.结合附图1,实施例1提供一种冷轧带钢的光整制造方法,包括以下步骤,
47.步骤1,对带钢进行粗磨,控制光整机工作辊粗糙度平均值ra为1.3~1.7μm,优选值为1.4~1.6μm。实施例1采用工作辊磨削、毛化等工艺,由于控制带钢表面波纹度wsa中长波的关键因素在于控制工作辊波纹度wca,实施例1采用低波纹度工作辊轧制的平整机,以获得低波纹度wsa的带钢。为了降低带钢波纹度wsa,实施例1采用低粗糙度wca的磨削辊和高粒度砂轮,控制精磨削液流速不低于砂轮转速。通过提高磨削液浓度至3.0%,优化磨削毛化工艺,将光整机工作辊粗糙度值ra从2.2μm降低至1.5μm。
48.步骤2,对完成粗磨的带钢进行半精磨,降低砂轮的线速度,控制磨床工作辊转速为20m~24m/min,采用的砂轮粒度为100#,采用的砂轮直径为800~900mm。通过降低线速度以降低磨削过程中的磨床振动。针对减少工作辊振纹的磨削过程拟合方程为:走刀纹严重程度=13.0786-0.0194z轴速度-2.971电流压力+0.00009012z轴速度2+0.3865电流电压2+0.002z轴速度
×
电流电压,由此制备出无走刀纹的低粗糙度磨削基辊。
49.磨削过程中,设置其它工艺参数为常数,当砂轮粒度越大,工作辊表面磨削粗糙度就越低;砂轮直径越大,工作辊表面磨削粗糙度也越低。随着砂轮使用周期的增长,砂轮直径受到磨损,变得越来越小,导致砂轮磨削效率逐步降低,由于砂轮直径大小对工作辊表面质量及工艺要求有较大影响,针对不同砂轮直径使用不同磨削工艺参数。
50.步骤3,对完成半精磨的带钢进行超精磨,控制磨床工作辊转速为400mm/min,将精磨削液流速调整至14m/min。带钢表面波纹度wsa除了与工作辊的形状误差、工作辊粗糙度、轧制力等参数有关,也和轧机振动存在关系,因此减少光整过程中的振动也尤为必要。通过超精磨工艺能够减缓工作辊表面的起伏,进而降低带钢表面波纹度wsa。毛化工作辊的粗糙度值ra越低,对应的工作辊波纹度wca也越低,如此传递到带钢上的波纹度wsa也随之降低,鲜印性随之提高。
51.步骤4,实施例1采用钢种为180bd+z的烘烤硬化钢,控制轧制力为3500~4500kn,以完成超精磨的带钢表面波纹度wsa控制为核心,将完成超精磨的带钢表面工艺参数对应的非线性关系数据组成样本集,对样本集进行网络模型训练,生成模拟实际制造的带钢鲜印性预报模型,如下表所示:
[0052][0053]
通过使用预报模型的预测结果,当ra为1.0μm时,轧制力从5881kn降低至4036kn,wsa1-5从0.47μm降低至0.36μm,wca0.8从0.6μm降低至0.57μm。分析对应关系
△
wsa1-5/
△
f=0.08μm/1000kn。
[0054]
随着轧制力降低,带钢表面波纹度wsa也降低。当采用180bd+z的钢种,当轧制力降低1000kn,对应的带钢表面波纹度wsa1-5降低0.3;当采用dx54d+z的钢种,当轧制力降低200kn,对应的带钢表面波纹度wsa1-5降低0.4。
[0055]
步骤5,根据带钢鲜印性预报模型预报并调整实际制造参数。
[0056]
目前市场上汽车合资主机厂对外板的要求如下:外板粗糙度分钢种控制在ra 0.7~1.1μm或ra1.0~1.4μm,粗糙度范围
±
ra 0.2μm,rpc值≧85。高等级双面o5外板瓶颈因素为粗糙度、rpc值分布不均匀,镀锌板表面缺陷多。高鲜印性免中涂外板用户针对涂装工序和漆膜鲜印性要求较高,低波纹度的钢板具有高鲜印性,要求wsa1-5≤0.35μm,wca0.8≤0.5μm。目前提供的180bd+z和dx54d+z的wsa1-5=0.44μm,在成型后均无法满足合资主机厂wsa1-5<0.35μm的要求,且合资主机厂对高鲜映性汽车外板的低波纹度要求与冲压的高粗糙度要求对汽车板生产的工艺控制提出了即为复杂的要求。
[0057]
经过以上步骤,实施例1获得的带钢表面工作辊粗糙度值ra≤0.1μm,工作辊粗糙度峰值rpc≥100,带钢表面波纹度wsa1-5<0.3μm,外板表面形貌合格率>98%。带钢鲜印性得到显著提高。使用本方法制造的带钢,提高带钢表面光洁度,增加了对镀锌表面缺陷的掩盖能力,同时能够提高工作辊表面微观形貌反印到外板上的复制效率,提高了免中涂外板的鲜映性,降低了带钢表面波纹度wsa,和储油性以及涂油的均匀性。表面形貌控制指标优于同行业领先企业。用以上方法作用于dx54d+z等外板,实验结果证明,加工后的180bd+z,dx54d+z等带钢的表面波纹度wsa控制均值低于同行业领先企业,产品涂装效果更佳。
[0058]
实施例2
[0059]
结合附图2,本实施例提供一种冷轧带钢的光整装置,包括,
[0060]
第一制造单元,用于对带钢进行粗磨,粗磨过程控制光整机工作辊粗糙度平均值ra为1.3~1.7μm,优选值设为1.5μm;
[0061]
第二制造单元,用于对完成粗磨的带钢进行半精磨,半精磨过程控制磨床工作辊
转速为20m~24m/min,磨削液浓度为3.0%;控制精磨削液流速不低于砂轮转速;
[0062]
第三制造单元,用于对完成半精磨的带钢进行超精磨,控制磨床工作辊转速为400mm/min;控制精磨削液流速不低于砂轮转速;
[0063]
第四制造单元,用于根据超精磨表面工艺参数生成模拟实际制造的带钢鲜印性预报模型;
[0064]
第五制造单元,用于根据带钢鲜印性预报模型预报并调整实际制造参数。
[0065]
实施例3
[0066]
结合附图3,实施例3中的带钢鲜印性预报模型包括误差修正、网络模型训练,预报计算,
[0067]
误差修正包括以下步骤:
[0068]
s1.1,计算错误函数e;
[0069]
s1.2,判断是否收敛判断,当结果为是时,输出网络参数;
[0070]
s1.3,当判断结果为否时,重新计算网络参数;
[0071]
s1.4,将计算结果输入网络模型训练。
[0072]
网络模型训练包括以下步骤:
[0073]
s2.1,将轧制力、工作辊粗糙度、磨床工作辊转速、砂轮直径、精磨液流速等作为训练样本作为学习样本输入网络训练模型;
[0074]
s2.2,对学习样本数据归一化;
[0075]
s2.3,判断是否进行学习训练;
[0076]
s2.4,当判断结果为是时,进入网络模型训练;
[0077]
s2.5,当判断结果为否时,将归一化的数据作为赋值预报模型参数。
[0078]
预报计算包括以下步骤:
[0079]
s3.1,验证样本;
[0080]
s3.2,对验证样本数据归一化;
[0081]
s3.3,输入赋值预报模型参数;
[0082]
s3.4,判断是否执行预报,当判断结果为否时,结束命令;
[0083]
s3.5,当判断结果为是时,对赋值预报模型参数和归一化的验证样本数据进行预报计算;输出结果后结束命令。
[0084]
以上所述的仅是本技术的实施例,方案中公知的具体结构及特性等常识在此未作过多描述,所属领域普通技术人员知晓申请日或者优先权日之前发明所属技术领域所有的普通技术知识,能够获知该领域中所有的现有技术,并且具有应用该日期之前常规实验手段的能力,所属领域普通技术人员可以在本技术给出的启示下,结合自身能力完善并实施本方案,一些典型的公知结构或者公知方法不应当成为所属领域普通技术人员实施本技术的障碍。应当指出,对于本领域的技术人员来说,在不脱离本技术结构的前提下,还可以作出若干变形和改进,这些也应该视为本技术的保护范围,这些都不会影响本技术实施的效果和专利的实用性。本技术要求的保护范围应当以其权利要求的内容为准,说明书中的具体实施方式等记载可以用于解释权利要求的内容。