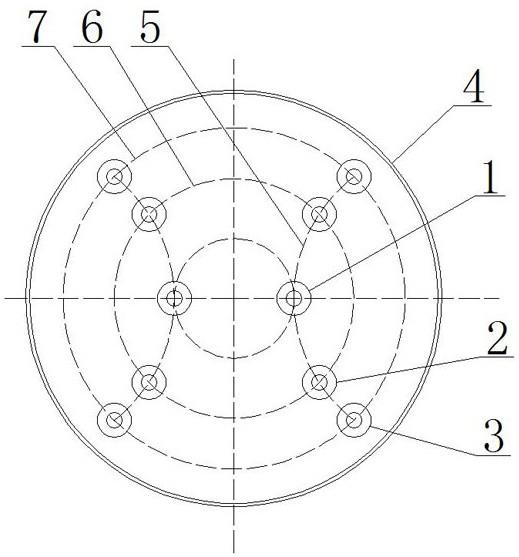
1.本发明涉及一种底吹孔分布结构及底吹方法,特别是一种转炉底吹孔分布结构及其底吹方法,属于炼钢技术领域。
背景技术:2.近几年来,市场对钢的品质要求逐步提高,钢水转炉终点各项指标,如钢水氧含量、磷含量及温度等,是控制成品各项性能的源头,钢水氧含量是钢水内生夹杂物的主要来源,是决定炼钢后续工序稳定及生产高品质钢的直接影响因素。
3.中国专利授权公告号 cn211199267u公开一种转炉,该专利的底吹孔分布是在炉底为圆心的两个同心圆上。该技术两圈底吹孔分布距离圆心很近,存在底吹死区,例如熔池边缘。而且采用同心圆的均分分布结构,越外层的同心圆所要开设的底吹孔的数量越多,加大了底吹成本。
技术实现要素:4.本发明所要解决的技术问题是提供一种转炉底吹孔分布结构及其底吹方法,底吹孔能够覆盖熔池边缘,消除了底吹死区,并且以较少的底吹孔数量即实现了良好的底吹效果。
5.为解决上述技术问题,本发明所采用的技术方案是:一种转炉底吹孔分布结构,其特征在于:包含两个中心底吹孔、四个中间底吹孔和四个熔池边缘底吹孔,两个中心底吹孔、四个中间底吹孔和四个熔池边缘底吹孔均分布在以转炉炉体底部圆心为中心的双曲线上,其中两个中心底吹孔位于双曲线的两个顶点,四个中间底吹孔位于第一圆形与双曲线的交点处,四个熔池边缘底吹孔位于第二圆形与双曲线的交点处,第一圆形和第二圆形与转炉炉体底部同心设置。
6.进一步地,所述转炉炉体底部的直径为d,两个中心底吹孔与转炉炉体底部圆心距离为0.29d,四个中间底吹孔与转炉炉体底部圆心距离为0.58d,四个熔池边缘底吹孔与转炉炉体底部圆心距离为0.83d。
7.进一步地,所述两个中心底吹孔、四个中间底吹孔和四个熔池边缘底吹孔分别设置有独立供气。
8.进一步地,所述两个中心底吹孔、四个中间底吹孔和四个熔池边缘底吹孔的供气气源为氮气或惰性气体。
9.进一步地,所述惰性气体为氩气。
10.进一步地,所述两个中心底吹孔、四个中间底吹孔和四个熔池边缘底吹孔总底吹流量控制在300~1000nm3/h范围内。
11.一种转炉底吹孔分布结构的底吹方法,其特征在于包含以下步骤:将转炉吹炼分为三个阶段:吹炼前期、吹炼中期和吹炼后期;吹炼前期两个中心底吹孔、四个中间底吹孔和四个熔池边缘底吹孔总底吹流量控
制在550nm3/h;吹炼中期两个中心底吹孔、四个中间底吹孔和四个熔池边缘底吹孔总底吹流量控制在300nm3/h;吹炼后期两个中心底吹孔、四个中间底吹孔和四个熔池边缘底吹孔总底吹流量控制在700nm3/h。
12.进一步地,所述四个中间底吹孔和四个熔池边缘底吹孔的流量是两个中心底吹孔的2倍。
13.进一步地,吹炼前期两个中心底吹孔的流量控制在110 nm3/h,四个中间底吹孔的流量控制在220 nm3/h,四个熔池边缘底吹孔的流量控制在220nm3/h;吹炼中期两个中心底吹孔的流量控制在60nm3/h,四个中间底吹孔的流量控制在120 nm3/h,四个熔池边缘底吹孔的流量控制在120nm3/h;吹炼后期两个中心底吹孔的流量控制在140 nm3/h,四个中间底吹孔的流量控制在280 nm3/h,四个熔池边缘底吹孔的流量控制在280nm3/h。
14.进一步地,所述吹炼前期为兑铁开始至5min60s,吹炼中期为6min至11min60s,吹炼后期为12min至吹炼结束。
15.本发明与现有技术相比,具有以下优点和效果:1、本发明的转轮底吹孔沿着双曲线进行分布,与传统的圆形均匀分布的方式相比,能够有效加强对熔池中心和边缘的搅拌效果,减少熔池内的底吹死区,促进钢渣充分混合,降低转炉炉内氧含量,从而提高转炉脱磷率;2、本发明的双曲线分布结构相比于传统的环形分布结构,在同样的转炉径向分布范围下,所需开设的底吹孔的数量更少,降低了底吹成本也更加容易进行底吹控制;3、本发明通过合理分布各位置底吹孔的流量,从而与转炉顶部吹氧相互配合,两个中心底吹孔可以缓和氧枪的对冲作用,放置吹炼过程喷溅,四个中间底吹孔和四个熔池边缘底吹孔可以有效弥补氧枪吹氧搅拌的不足,减少熔池拾取,促进熔池反应,降低碳氧积。
附图说明
16.图1是本发明的一种转炉底吹孔分布结构的示意图。
17.图2是本发明的一种转炉底吹孔分布结构的吹炼阶段各时期流量表。
18.图3是本发明的对比例1的底吹孔分布结构示意图。
19.图4是本发明的对比例1的吹炼阶段各时期流量表。
20.图5是本发明的对比例2的底吹孔分布结构示意图。
21.图6是本发明的对比例2的吹炼阶段各时期流量表。
22.图7是本发明的实施例与对比例1、2的对比效果表。
具体实施方式
23.为了详细阐述本发明为达到预定技术目的而所采取的技术方案,下面将结合本发明实施例中的附图,对本发明实施例中的技术方案进行清晰、完整地描述,显然,所描述的实施例仅仅是本发明的部分实施例,而不是全部的实施例,并且,在不付出创造性劳动的前
提下,本发明的实施例中的技术手段或技术特征可以替换,下面将参考附图并结合实施例来详细说明本发明。
24.如图1所示,本发明的一种转炉底吹孔分布结构,包含两个中心底吹孔1、四个中间底吹孔2和四个熔池边缘底吹孔3,两个中心底吹孔1、四个中间底吹孔2和四个熔池边缘底吹孔3均分布在以转炉炉体底部4圆心为中心的双曲线5上,其中两个中心底吹孔1位于双曲线5的两个顶点,四个中间底吹孔2位于第一圆形6与双曲线5的交点处,四个熔池边缘底吹孔3位于第二圆形7与双曲线5的交点处,第一圆形6和第二圆形7与转炉炉体底部4同心设置。
25.转炉炉体底部4的直径为d,两个中心底吹孔1与转炉炉体底部4圆心距离为0.29d,四个中间底吹孔2与转炉炉体底部4圆心距离为0.58d,四个熔池边缘底吹孔3与转炉炉体底部4圆心距离为0.83d。本实施例中底吹孔一共10个,每条双曲线上分布5个底吹孔。所有的底吹孔以转炉炉体底部4的圆心呈中心对称。熔池中心0.29d处设置2个中心底吹孔可减缓和氧枪对冲作用,防止吹炼过程喷溅,0.58d和0.83d与双曲线交点的处设置的8个底吹孔,可以弥补氧枪吹氧搅拌的不足,减少熔池死区,促进熔池反应,提高脱磷率,降低碳氧积。
26.两个中心底吹孔1、四个中间底吹孔2和四个熔池边缘底吹孔3分别设置有独立供气。两个中心底吹孔1、四个中间底吹孔2和四个熔池边缘底吹孔3的供气气源为氮气或惰性气体。惰性气体为氩气。
27.两个中心底吹孔1、四个中间底吹孔2和四个熔池边缘底吹孔3总底吹流量控制在300~1000nm3/h范围内,在转炉熔池内形成小环流,促进熔池碳氧反应。
28.一种转炉底吹孔分布结构的底吹方法,包含以下步骤:将转炉吹炼分为三个阶段:吹炼前期、吹炼中期和吹炼后期;吹炼前期为兑铁开始至5min60s,吹炼中期为6min至11min60s,吹炼后期为12min至吹炼结束。
29.吹炼前期两个中心底吹孔、四个中间底吹孔和四个熔池边缘底吹孔总底吹流量控制在550nm3/h;吹炼前期两个中心底吹孔的流量控制在110 nm3/h,四个中间底吹孔的流量控制在220 nm3/h,四个熔池边缘底吹孔的流量控制在220nm3/h。
30.吹炼中期两个中心底吹孔、四个中间底吹孔和四个熔池边缘底吹孔总底吹流量控制在300nm3/h;吹炼中期两个中心底吹孔的流量控制在60nm3/h,四个中间底吹孔的流量控制在120 nm3/h,四个熔池边缘底吹孔的流量控制在120nm3/h。
31.吹炼后期两个中心底吹孔、四个中间底吹孔和四个熔池边缘底吹孔总底吹流量控制在700nm3/h。吹炼后期两个中心底吹孔的流量控制在140 nm3/h,四个中间底吹孔的流量控制在280 nm3/h,四个熔池边缘底吹孔的流量控制在280nm3/h。
32.四个中间底吹孔和四个熔池边缘底吹孔的流量是两个中心底吹孔的2倍。
33.本实施例以公称容量120t转炉吹炼gcr15为例,原料组成的重量百分比为:铁水70~95%,其余为废钢及生铁。各冶炼50炉的数据,吹炼阶段各时期流量如图2所示。
34.对比例1:如图3所示,对比例1的底吹孔呈圆形分布。公称容量120t转炉吹炼gcr15为例,原料组成的重量百分比为:铁水70~95%,其余为废钢及生铁。各冶炼50炉的数据,吹炼阶段各时期流量如图4所示。
35.对比例2:如图5所示,对比例2的底吹孔呈两圈圆形分布。公称容量120t转炉吹炼gcr15为例,原料组成的重量百分比为:铁水70~95%,其余为废钢及生铁。各冶炼50炉的数
据,吹炼阶段各时期流量如图6所示。
36.通过碳氧积、脱磷率、转炉终点氧含量对比两种底吹孔分布模式的效果,如图7所示。从图7表格可以看出,本发明实施后相比于现有技术,碳氧积分别降低了4.3
×
10-4
、3.3
×
10-4
,脱磷率分别提高了1.3%、2.0%,转炉终点氧含量分别降低了200ppm、170ppm。
37.以上所述,仅是本发明的较佳实施例而已,并非对本发明作任何形式上的限制,虽然本发明已以较佳实施例揭露如上,然而并非用以限定本发明,任何熟悉本专业的技术人员,在不脱离本发明技术方案范围内,当可利用上述揭示的技术内容做出些许更动或修饰为等同变化的等效实施例,但凡是未脱离本发明技术方案内容,依据本发明的技术实质,在本发明的精神和原则之内,对以上实施例所作的任何简单的修改、等同替换与改进等,均仍属于本发明技术方案的保护范围之内。