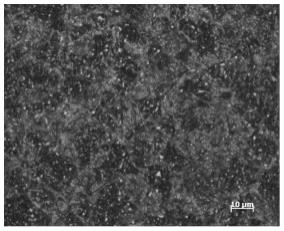
1.本发明属于钢铁冶炼技术领域,具体涉及一种铸坯生产泵车用高耐磨性热轧带钢和钢管及其制造方法。
背景技术:2.随着社会的大力发展,摩天大楼在城市各处随处可见,这些现代超高层建筑都是用混凝土浇筑高楼骨架,混凝土采用高压泵通过输送管道输送到浇筑高度,输送管内压力大,内壁极易磨损。
3.目前混凝土输送管品种主要采用单层淬硬耐磨管,单层淬硬耐磨管由于需要兼顾硬度和韧性,寿命较短,造成资源较大浪费。为避免单层耐磨钢管缺陷,目前开始研发双金属复合耐磨钢管,将硬度和韧性分成两部分,由相互独立的内管和外管组成。内管硬度高、耐磨性好,但韧性较低,用于承受混凝土的冲蚀和磨损,外管硬度低、韧性好以保证输送管整体的韧性。薄规格内管设计,势必影响管道寿命,从而增加混凝土输送的成本。厚规格内管设计会造成输送骨架支撑断裂造成安全事故,因此,合适的管道厚度也即合适的带钢厚度选择显得尤为重要。
4.目前国内混凝土泵车输送管道一般采用65mn、nm600无缝管生产或在此基础上添加合金cr、ti、re元素。生产工艺流程主要包括钢管、冷拔、冷拔(复合)、去应力退火、下料、焊接、热处理、喷砂、镶套。但由于生产所得钢管的耐磨性差,平均耐磨寿命只在1.5-3万立方米。
5.国内很多钢厂均在研究热轧板带钢的生产工艺,大部分研究都集中在板带钢生产中的应力、板带钢的常规力学性能等,但对热轧带钢的高耐磨性以及带钢制成产品的使用性能的研究则较少,已公布的专利文献中的产品在实际工程中的应用更是微乎其微。
6.经检索,公开号为:cn111974801a的申请案公开了一种热轧带钢的生产方法,其通过合理的热轧生产工艺,得到了较好力学性能,但该申请案通篇未阐述其成分设计理念,且轧制工艺重点描述了加热冷却工艺,以改善窄带钢应力分布。
7.公开号为:cn105239011a的申请案公开了一种混凝土泵车用耐磨无缝钢管的制造方法,其制造方法包括以下步骤:(1)炼钢:铁水脱硫
→
转炉/电炉
→
lf精练炉
→
vd真空处理
→
连铸圆坯;(2)轧管:管坯在环形炉加热,按1150~1230℃加热后,经穿孔、连轧管机轧制、张减机定减径、矫直,完成管坯的轧制;(3)钢管去应力退火:采用连续炉进行退火处理。该申请案采用“vd连铸坯
→
热轧
→
去应力退火
→
探伤
→
后序处理”工艺可以稳定生产混凝土泵车输送用耐磨无缝钢管,大大提高了产品成材率,降低生产成本,且生产所得无缝钢管具有高硬度高耐磨性。但该申请案所用的原料是圆坯,生产难度较大。
技术实现要素:8.1.要解决的问题
9.本发明的目的在于提供一种铸坯生产泵车用高耐磨性热轧带钢和钢管及其制造
方法,以满足大规格(厚度5mm)泵车用热轧带钢焊管后对表面硬度和耐磨性等力学性能的要求,为高寿命的泵车输送管的制造提供指导意义。
10.2.技术方案
11.为了解决上述问题,本发明所采用的技术方案如下:
12.本发明的一种铸坯生产泵车用高耐磨性热轧带钢,其原料包括如下质量百分比的组分:c:1.0-1.2,si:0.20-0.40,mn:0.20-0.35,cr:1.20-1.40,alt:0.010-0.020,p≤0.010,s≤0.002,且c+mn/6+(cr+mo+v)/5+(cu+ni)/15≤1.48。
13.本发明通过对热轧带钢的元素组成及质量配比进行优化,即通过高碳+低锰+1.30%cr的合金化成分设计,并控制c+mn/6+(cr+mo+v)/5+(cu+ni)/15≤1.48,从而可以有效保证带钢的硬度和耐磨性,并使其焊管后的韧性之间达到良好匹配,进而保证该带钢能够有效满足较大规格(5mm)泵车用管道对耐磨性及使用寿命的要求。
14.进一步优选的,控制带钢中cr元素的质量百分比为1.30%。
15.本发明的一种铸坯生产泵车用高耐磨性热轧带钢,该钢管采用上述热轧带钢取样焊接成管制成,热轧带钢的厚度为5mm,其金相组织为低温回火马氏体+碳化物,表面硬度≥70hrc,泵送方量≥7万立方米。
16.本发明的铸坯生产泵车用高耐磨性热轧带钢的制造方法,其生产工艺包括冶炼、连铸、铸坯加热、轧制、卷曲、退火、焊接和焊后热处理,其中轧制采用控制粗轧+精轧连轧+在线控冷工艺,粗轧终轧温度≥1000℃,精轧终轧温度为850-895℃,通过在线控冷控制卷曲温度为700-850℃。
17.本发明通过对带钢的组分进行合金化设计,同时对其制备工艺进行优化控制,尤其是采用控轧控冷工艺,对粗轧与精轧终轧温度以及卷曲温度进行严格控制,从而可以有效保证所得大规格(厚度为5mm)带钢的力学性能,使其达到技术标准要求,保证焊管后具有良好的淬透性以及较高的耐磨性。
18.更进一步的,采用在线辊底式退火炉进行退火处理,退火温度为740-780℃,退火时间为13-15小时;焊管后热处理采用淬火+回火工艺,其中淬火温度为850-870℃,保温时间为20-30min,淬火介质为40-50℃机械油,回火温度为135-145℃,保温时间为120min。
19.通过控轧控冷、在线退火及随后的淬火+低温回火热处理的共同配合,有利于进一步保证所得焊管后的使用性能。其中,经在线退火后产品单边总脱碳层深度≤0.02mm,表面硬度在40-45hrc,带状碳化物≤0.5级,网状碳化物≤0.5级;试样焊成钢管后,经淬火+低温回火热处理后,所得钢管的金相组织为低温回火马氏体+碳化物,表面硬度≥70hrc,泵送方量≥7万立方米。
20.更进一步的,铸坯加热的加热温度为1120-1200℃,出钢温度≥1100℃,坯料在炉总时间为234-286min。
21.更进一步的,粗轧终轧温度为1000-1020℃,铸坯加热的出钢温度为1100-1155℃。
22.更进一步的,坯料出炉后,经过1次17mpa的除鳞,然后开始粗轧;粗轧结束后,经过1次12mpa的除鳞,然后进入10台平立连轧机组进行精轧,精轧终轧前再经过1次7mpa除鳞,精轧结束后打开在线风冷机组进行控冷。
23.更进一步的,连铸后对铸坯进行堆垛缓冷,缓冷温度控制在≥700℃,缓冷时间为48小时,同时确保出缓冷坑温度为300-350℃。
24.3.有益效果
25.综上所述,相比于现有技术,本发明的有益效果为:
26.(1)本发明通过合金化设计对带钢的元素组成及配比进行优化,从而可以满足大规格(5mm厚度)铸坯生产泵车用管道对使用性能,尤其是对硬度、耐磨性和使用寿命的要求,从而有效克服了5mm厚度热轧带钢在焊接成管服役要求下,难以达到高耐磨性、单边总低脱碳层、低网带状碳化物、高使用寿命的技术难点。
27.(2)本发明在合金化成分设计的基础上,对钢管生产工艺进行优化设计,通过控轧控冷+在线退火+淬火-低温回火焊后热处理的工艺配合,从而可以进一步保证所得钢管的力学性能和使用寿命,且其生产工序简单、快捷交付、成本低廉。该生产工艺已在国内某钢厂采用2辊粗轧机+10架平立连轧可逆轧机生产线生产试行,所得钢管性能经验证可以满足5mm厚度泵车用管道的要求,具有高耐磨性、高淬透性、高寿命。
附图说明
28.图1为实施例4经焊后热处理所得钢管的金相组织。
具体实施方式
29.考虑到城市建设需要高质量的混凝土泵车,高耐磨性热轧带钢作为原材料,为延长高压高输送的泵车服役寿命,除常规低倍夹杂物控制优良外,还需要有优良的高耐磨性能,同时还要易于生产且成本较低。因此,本发明的发明人针对铸坯生产的泵车用高耐磨性热轧带钢化学成分设计和生产工艺进行了大量研究,从而得到本技术的方案。
30.虽然公开号为:cn113913705a的申请案公开了一种混凝土泵车用耐磨钢管及其制备方法,其通过合理的冶炼成分设计,采用连铸坯生产(2.7-3.7)*285mm窄带钢,并对热轧工艺、退火工艺及淬火+回火工艺进行了改善,从而可以得到较好的硬度性能和泵送方量情况,但其制备所得钢管的最大尺寸仅为3.7mm,不能很好适用于更大规格钢管的生产,且其表面硬度和泵送方量也有很大的差距。
31.本发明的大厚度铸坯生产泵车用高耐磨性热轧带钢的制造方法,主要包括以下工序:铁水脱硫预处理
→
电炉冶炼
→
lf+vd精炼
→
连铸
→
铸坯堆垛缓冷
→
铸坯检验
→
铸坯判定
→
铸坯验收
→
铸坯加热
→
除鳞
→
2台粗轧+10架平立连轧+在线控冷
→
卷曲
→
检验
→
在线退火热处理
→
切割、取样
→
检验
→
焊管
→
淬火+回火
→
检测
→
挂牌标识
→
入库。其中:
32.(1)炼钢成分设计:其化学成分按重量百分比计,包括,c:1.0-1.2,si:0.20-0.40,mn:0.20-0.35,p≤0.010,s≤0.002,cr:1.20-1.40,alt:0.010-0.020,pb:≤0.002,cu、ni、mo等为残余元素,不刻意添加,c+mn/6+(cr+mo+v)/5+(cu+ni)/15≤1.48,余量为fe及不可避免的杂质。
33.(2)坯料缓冷工艺:因成分设计属于高碳高铬,碳当量也很高,因此坯料必须入缓冷坑缓冷。缓冷温度控制在≥700℃,缓冷时间为48小时,同时要确保出缓冷坑温度:300-350℃。
34.(3)加热轧制工艺:坯料加热温度:1120-1200℃,出钢温度均≥1100℃,采用150mm
×
260mm矩形铸坯:轧成5mm*225mm带钢,坯料在炉总时间为234-286min,坯料出炉后,经过1次17mpa的除鳞,开始粗轧,粗轧终轧温度为≥1000℃,粗轧结束后,经过1次12mpa的除鳞,
然后快速进入10台平立连轧机精轧,精轧终轧前再经过1次7mpa除鳞,确保表面无氧化铁皮压入,精轧终轧温度:850-900℃。精轧结束,打开多组在线风冷机进行控冷(优选为3组),以确保卷曲温度:700-850℃。
35.由于高耐磨性热轧带钢需要耐磨性能优良,因此本生产方法除成分设计采用高碳高铬外,还采用精轧连轧,同时采用了风冷作为控冷手段,从而解决了带钢卷曲温度控制生产办法。
36.(4)热处理工艺:为了控制热轧态网带状碳化物大小,卷曲后进入在线辊底式退火炉,退火温度:740-780℃,退火时间:13-15小时,优选15小时;取样检测网带状碳化物大小及表面硬度。同时为便于后续加工检测,取样后,试样焊接成钢管,对钢管进行淬火+回火热处理。淬火温度:850-870℃,保温时间:20-30min,优选30min;淬火介质:50℃机械油;回火温度:135-145℃,保温120min。
37.经在线退火后产品单边总脱碳层深度≤0.02mm,表面硬度在40-45hrc,带状碳化物≤0.5级,网状碳化物≤0.5级。试样焊成钢管后,淬火+低温回火热处理后,金相组织为低温回火马氏体+碳化物,表面硬度≥70hrc,泵送方量≥7万立方米,具有良好的淬透性,同时具有很高的耐磨性性能。
38.下面结合具体实施例对本发明进一步进行描述。
39.实施例1-5
40.实施例1-5中大厚度铸坯生产泵车用高耐磨性热轧带钢钢管的制造方法,主要包括冶炼
→
lf+vd精炼
→
连铸
→
铸坯堆垛缓冷
→
铸坯加热
→
除鳞
→
2台粗轧+10架平立连轧+在线控冷
→
卷曲
→
在线退火热处理
→
取样
→
焊管
→
淬火+回火工艺,其中:
41.(1)铸坯生产泵车用高耐磨性热轧带钢的化学成分分别如下表1所示。其中,实施例1-5中c+mn/6+(cr+mo+v)/5+(cu+ni)/15分别为1.32、1.43、1.48、1.39和1.48。
42.表1实施例1-5中化学成分(wt%)
[0043] csimnpsnicrmoaltcu实施例11.00.250.300.0080.0010.031.380.020.010.06实施例21.150.200.250.0080.0020.051.20.030.0150.05实施例31.20.380.200.0100.0010.031.220.050.020.05实施例41.050.400.350.0080.0010.031.40.030.0130.04实施例51.180.250.280.0080.0010.051.250.050.0180.05
[0044]
(2)铸坯加热工艺
[0045]
实施例1-5中的铸坯加热工艺参数分别如下表2所示。
[0046]
表2铸坯加热工艺参数
[0047][0048]
由于实验钢具有高耐磨性能特征,坯料选用150*260矩形铸坯尺寸,为减小铸坯心部网带状碳化物大小,钢板采用控制粗轧+精轧连轧以及风冷控制卷曲温度轧制模式,降低高温状态下晶粒长大速度,本生产方法选用的坯料出炉温度采用高温出炉即温度≥1100℃,因合金只有铬和少量的锰,在炉时间按照坯料最大厚度的0.9-1.1min/mm加热系数控制,以确保坯料钢温整体均匀,增加轧制渗透至心部的能力,从而提高心部变形能力,降低心部组织晶粒尺寸。
[0049]
(3)控轧工艺
[0050]
实施例1-5中的轧制工艺参数分别如下表3所示。
[0051]
表3轧制工艺参数
[0052][0053]
(4)在线退火工艺
[0054]
实施例1-5中的在线退火工艺参数分别如下表4所示。
[0055]
表4在线退火工艺参数
[0056][0057]
经在线退火后的带钢性能参数如下表5所示。
[0058]
表5在线退火后的性能参数
[0059][0060][0061]
(5)试样焊成5mm(管厚)*225mm(管高)钢管后,进行淬火+回火热处理,实施例1-5的淬火和回火工艺参数分别如下表6、表7所示。
[0062]
表6淬火工艺参数
[0063][0064]
表7回火工艺参数
[0065][0066]
试样焊管后淬火+回火后的性能参数如下表8所示。结合表格可以看出,本发明通过合金化成分设计,并经过控轧控冷、在线退火及随后的淬火+低温回火热处理后,所得钢管的金相组织为低温回火马氏体+碳化物(实施例4中焊后热处理后的金相组织如图1所示),表面硬度≥70hrc,泵送方量≥7万立方米,具有良好的淬透性,同时具有很高的耐磨性能,所得钢管的网带状碳化物等级、表面硬度、泵送方量指标均达到技术标准要求。由于高耐磨性热轧带钢受矩形铸坯冶炼质量发展影响,网带状碳化物尺寸、高硬度与高耐磨性一致性能要求,在实际工业化大生产过程中,为避免在生产过程中出现加热开裂,轧制形变不足,易造成原始晶粒尺寸粗大,甚至出现混晶现象,从而严重影响表面硬度性能,故对坯料的缓冷工艺、卷曲温度控制工艺、在线退火工艺,试样焊管后,管件淬火+回火工艺进行了摸索优化,并进行了规定,从而实现工业化大生产采用较低的生产装备条件即能够生产高耐磨性泵车用带钢。
[0067]
表8淬火+回火后的性能参数
[0068]