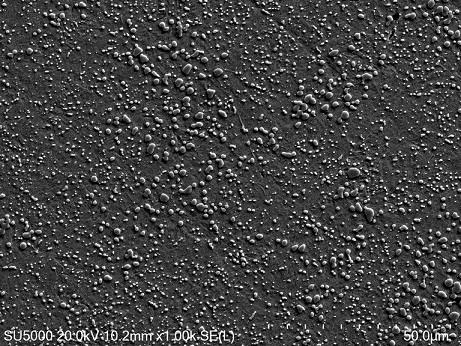
1.本发明涉及钢铁冶炼技术领域,具体为一种高碳高铬含氮马氏体不锈钢及其碳化物细化方法。
2.
背景技术:3.高碳高铬马氏体不锈钢(如,9cr18mo)具有良好的高温抗氧化性、低的热膨胀性和高的抗蠕变强度,作为高温轴承钢在航空、航天等领域应用。由于碳、铬和其它合金元素的含量较高,高碳高铬马氏体不锈钢的铸态凝固组织中析出大量粗大甚至网状的一次碳化物。这些碳化物中含有大量的合金元素,结果基体中合金元素含量降低,导致回火二次硬化效应减弱,高温强度和耐磨性降低。由于组织的遗传性,即使经后续热塑性变形和热处理,粗大碳化物也很难完全消除,依然存在局部分布不均的碳化物,这些碳化物是高碳高铬马氏体不锈钢服役发生塑性变形过程中的微裂纹源,材料的耐蚀性能和力学性能下降。因此,通过调控铸坯铸态组织,细化一次碳化物是高碳高铬马氏体不锈钢生产过程中需要解决的关键共性技术问题。
4.目前常用的方法是通过反复的热塑性变形机械破碎一次碳化物,并结合后续的热处理改善碳化物的分布。这种方法虽然有效,但生成效率低、成本高,且碳化物在局部仍然分布不均匀。电渣重熔和精炼能够显著净化钢液,减少夹杂,在一定程度上抑制了碳化物的析出和团聚,且电渣重熔方法增加了工序,提高了成本。
5.
技术实现要素:6.本发明的主要目的是提出一种高碳高铬含氮马氏体不锈钢及其碳化物细化方法,通过以n元素部分替代高碳高铬马氏体不锈钢中的c元素,调控c/n值,利用碳和氮的相互作用影响钢液凝固过程中碳化物的形核与长大行为,从而达到改善高碳高铬含氮马氏体不锈钢组织、细化一次碳化物的目的。
7.为解决上述技术问题,根据本发明的一个方面,本发明提供了如下技术方案:一种高碳高铬含氮马氏体不锈钢的碳化物细化方法,包括如下步骤:s1、钢液冶炼;s2、钢液成分调整,将钢液c/n值控制为c/n=1~15;s3、浇铸。
8.作为本发明所述的一种高碳高铬含氮马氏体不锈钢的碳化物细化方法的优选方案,其中:所述步骤s1中,采用感应炉、转炉、电炉、中频炉等冶炼方式实现钢液冶炼;作为本发明所述的一种高碳高铬含氮马氏体不锈钢的碳化物细化方法的优选方案,其中:所述步骤s2中,所述钢液成分调整通过添加氮化铬铁、氮化锰铁和氮化钼铁中的任意一种或多种调整钢液n元素含量,实现钢液c/n值的控制。
9.作为本发明所述的一种高碳高铬含氮马氏体不锈钢的碳化物细化方法的优选方案,其中:所述步骤s2中,所述钢液成分调整在氮气和/或氩气气体保护下进行。
10.作为本发明所述的一种高碳高铬含氮马氏体不锈钢的碳化物细化方法的优选方案,其中:所述步骤s2中,所述钢液成分调整期间,炉体内氮气和/或氩气气体的压力不小于0.7 atm。
11.作为本发明所述的一种高碳高铬含氮马氏体不锈钢的碳化物细化方法的优选方案,其中:所述步骤s2中,所述钢液成分调整在精炼炉内精炼剂覆盖保护下进行。
12.作为本发明所述的一种高碳高铬含氮马氏体不锈钢的碳化物细化方法的优选方案,其中:所述步骤s2中,所述精炼炉采用碱度为1~4的精炼渣;精炼渣包括以下重量百分比的成分:10~60%cao、15~50%sio2、10~30%al2o3、5~15%mgo,精炼时间为10~60 min。
13.作为本发明所述的一种高碳高铬含氮马氏体不锈钢的碳化物细化方法的优选方案,其中:所述步骤s2中,所述钢液成分调整达到要求后,炉底继续吹入氮气和/或氩气弱搅拌软吹,时间控制在5~20 min。
14.作为本发明所述的一种高碳高铬含氮马氏体不锈钢的碳化物细化方法的优选方案,其中:所述步骤s3中,所述浇铸采用模铸或连铸工艺。
15.为解决上述技术问题,根据本发明的另一个方面,本发明提供了如下技术方案:一种高碳高铬含氮马氏体不锈钢,按重量百分比计,其组成为c 0.6~1.5%,si≤0.1%,mn 0.1~1.0%,cr 13~25%,n 0.1~0.5%,m 0.5~2.0%,余量为铁和不可避免的杂质,其中m为w、v、mo、cu、nb中的任意一种或多种,c/n=1~15。
16.作为本发明所述的一种高碳高铬含氮马氏体不锈钢的优选方案,其中:所述高碳高铬含氮马氏体不锈钢的硬度≥55 hrc,抗拉强度≥1850 mpa;优选地,所述高碳高铬含氮马氏体不锈钢的硬度≥60 hrc,抗拉强度≥2000 mpa。
17.本发明的有益效果如下:本发明提出一种高碳高铬含氮马氏体不锈钢及其碳化物细化方法,通过以n元素部分替代高碳高铬马氏体不锈钢中的c元素,调控c/n值,通过碳与氮的相互作用有效控制钢液凝固过程中碳化物的形核与长大行为,改善铸坯凝固组织,细化一次碳化物,提高成分均匀性。利用本发明方法生产的高碳高铬含氮马氏体不锈钢铸坯经后续的热塑性变形和热处理,在细小碳化物和含氮相的协同强化作用下,获得优良的综合力学性能,所述高碳高铬含氮马氏体不锈钢的硬度≥55 hrc,抗拉强度≥1850 mpa。
18.附图说明
19.为了更清楚地说明本发明实施例或现有技术中的技术方案,下面将对实施例或现有技术描述中所需要使用的附图作简单地介绍,显而易见地,下面描述中的附图仅仅是本发明的一些实施例,对于本领域普通技术人员来讲,在不付出创造性劳动的前提下,还可以根据这些附图示出的结构获得其他的附图。
20.图1为对比例1中9cr18mo高碳高铬含氮马氏体不锈钢铸坯金相组织;图2为本发明实施例1高碳高铬含氮马氏体不锈钢铸坯金相组织;图3为本发明实施例2高碳高铬含氮马氏体不锈钢铸坯金相组织;
图4为本发明实施例3高碳高铬含氮马氏体不锈钢铸坯金相组织;图5为本发明实施例2高碳高铬含氮马氏体不锈钢热处理后的sem图。
21.本发明目的的实现、功能特点及优点将结合实施例,参照附图做进一步说明。
22.具体实施方式
23.下面将结合实施例中的技术方案进行清楚、完整地描述,显然,所描述的实施例仅仅是本发明的一部分实施例,而不是全部的实施例。基于本发明中的实施例,本领域普通技术人员在没有作出创造性劳动前提下所获得的所有其他实施例,都属于本发明保护的范围。
24.本发明提供一种高碳高铬含氮马氏体不锈钢及其碳化物细化方法,改善铸坯凝固组织,细化一次碳化物,提高成分均匀性。通过以n元素部分替代高碳高铬马氏体不锈钢中的c元素,调控c/n值,通过碳与氮的相互作用有效控制钢液凝固过程中碳化物的形核与长大行为,利用本发明方法生产的高碳高铬含氮马氏体不锈钢铸坯经后续的热塑性变形和热处理,在细小碳化物和含氮相的协同强化作用下,获得优良的综合力学性能。
25.根据本发明的一个方面,本发明提供了如下技术方案:一种高碳高铬含氮马氏体不锈钢,按重量百分比计,其组成c 0.6~1.5%,si≤0.1%,mn 0.1~1.0%,cr 13~25%,n 0.1~0.5%,m 0.5~2.0%,余量为铁和不可避免的杂质,其中m为w、v、mo、cu、nb中的任意一种或多种合金元素,c/n= 1~15;与碳一样,氮作为间隙原子在不锈钢中具有很强的固溶强化作用,有利于改善不锈钢的高温力学性能、高温耐磨性能和疲劳寿命,并且能能够明显改善不锈钢的耐腐蚀性能。因此,添加氮是改善不锈钢组织和性能有效的方法之一。碳与氮作为合金元素同时存在于不锈钢中,二者的相互作用将会影响钢液的凝固行为,进而影响含氮不锈钢的铸态凝固组织。
26.优选地,所述c/n=3~12;更进一步优选地,所述c/n=5~10;通过以n元素部分替代高碳高铬马氏体不锈钢中的c元素,调控c/n值,通过碳与氮的相互作用有效控制钢液凝固过程中碳化物的形核与长大行为;具体地,所述c/n为例如但不限于3、3.5、4、4.5、5、5.5、6、6.5、7、7.5、8、8.5、9、9.5、10、10.5、11、11.5、12中的任意一者或任意两者之间的范围;所述高碳高铬含氮马氏体不锈钢的硬度≥55hrc,抗拉强度≥1850 mpa;优选地,所述高碳高铬含氮马氏体不锈钢的硬度≥60 hrc,抗拉强度≥2000 mpa。
27.一种所述高碳高铬含氮马氏体不锈钢组织的控制方法,包括如下步骤:s1、钢液冶炼;s2、钢液成分调整,将钢液c/n值控制为c/n=1~15;s3、浇铸。
28.所述步骤s1中,采用本发明常用的冶炼方式实现钢液冶炼,例如但不限于感应炉、转炉、电炉、中频炉等冶炼方式;通过步骤s1冶炼出成分符合要求的钢液,钢液中除氮元素外,其它合金成分在考虑后续调控c/n值阶段增加量的基础上控制在合理范围之内;优选地,所述c/n=3~12;更进一步优选地,所述c/n=5~10;通过以n元素部分替代高碳高铬马氏体不锈钢中的c元素,调控c/n值,通过碳与氮的相互作用有效控制钢液凝固过
程中碳化物的形核与长大行为;具体地,所述c/n为例如但不限于3、3.5、4、4.5、5、5.5、6、6.5、7、7.5、8、8.5、9、9.5、10、10.5、11、11.5、12中的任意一者或任意两者之间的范围;所述步骤s2中,所述钢液成分调整通过合金化调控的方式实现,例如但不限于通过添加氮化铬铁、氮化锰铁、氮化钼铁等含氮合金调整钢液n元素含量,实现钢液c/n值的控制,所述含氮合金的加入量以钢液要求的n元素含量为基准进行确定。
29.所述步骤s2中,根据钢种的要求选择是否采用精炼工艺:若采用精炼工艺,所述钢液成分调整在精炼炉内精炼剂覆盖保护下进行,优选的,所述精炼炉采用碱度为1~4的精炼渣;精炼渣可以采用例如但不限于以下重量百分比的成分的精炼渣:10~60%cao、15~50%sio2、10~30%al2o3、5~15%mgo,精炼时间为10~60 min。具体地,所述精炼时间为例如但不限于10min、20min、30min、40min、50min、60min中的任意一者或任意两者之间的范围;钢液成分调整期间精炼炉持续吹入氮气和/或氩气,氮气和/或氩气流量处于软吹搅拌状态,保证渣面微动、钢液不裸露;若不采用精炼工艺,所述钢液成分调整在氮气和/或氩气气体保护下进行,所述钢液成分调整期间,炉体内氮气和/或氩气气体的压力不小于0.7 atm。
30.所述步骤s2中,所述钢液成分调整达到要求后,炉底继续吹入氮气和/或氩气弱搅拌软吹,时间控制在5~20 min。具体地,所述精炼时间为例如但不限于5min、10min、15min、20min中的任意一者或任意两者之间的范围;作为本发明所述的一种高碳高铬含氮马氏体不锈钢的碳化物细化方法的优选方案,其中:所述步骤s3中,所述浇铸采用模铸或连铸工艺。
31.对所述高碳高铬含氮马氏体不锈钢铸坯进行热塑性变形和热处理,在细小碳化物和含氮相的协同强化作用下,获得优良的综合力学性能,所述高碳高铬含氮马氏体不锈钢的硬度≥55 hrc,抗拉强度≥1850 mpa。优选地,所述高碳高铬含氮马氏体不锈钢的硬度≥60 hrc,抗拉强度≥2000 mpa。
32.所述热塑性变形为例如但不限于锻造、轧制、挤压等变形方式;所述热处理为淬火+回火处理,所述淬火温度为950~1150℃,淬火保温时间为0.6~0.8 min/mm
×
d,其中d为钢件的的最大厚度或直径(mm);具体地,所述淬火温度为例如但不限于950℃、1000℃、1050℃、1100℃、1150℃中的任意一者或任意两者之间的范围;所述回火温度为150~300℃,回火时间为3~6 min/mm
×
d,其中d为钢件的的最大厚度或直径(mm)。具体地,所述回火温度为例如但不限于150℃、180℃、200℃、220℃、250℃、270℃、300℃中的任意一者或任意两者之间的范围。
33.以下结合具体实施例对本发明技术方案进行详细说明。
34.实施例18.5cr18mo0.1n高碳高铬含氮马氏体不锈钢组织的控制方法,采用氮化铬铁合金化实现钢液成分调整,包括如下步骤:s1、钢液冶炼;采用50 kg中频炉在大气环境下冶炼50 kg钢水,cr含量控制在:cr 16.5%,除n、cr元素以外,其他元素控制到符合表1所述成分范围;s2、钢液成分调整,钢液c/n值控制为8左右;
在中频炉内精炼钢液,精炼渣的各组分重量百分比为:38%cao、30%sio2、25%al2o3、4%mgo及3%的钙。在精炼剂覆盖保护下进行钢液成分调整,加入2 kg的fencr10-b调整n和cr的含量,以符合表1所述成分范围。
35.精炼期间炉体底部持续吹入氮气和/或氩气,氮气和/或氩气流量处于软吹搅拌状态,保证渣面微动、钢液不裸露;成分调整达到要求后,炉底继续吹入惰性气体弱搅拌软吹,时间控制在10 min;s3、浇铸;钢液成分调整结束后,加热至浇铸温度,保温5 min,扒渣后浇入钢模,自然冷却得到铸坯,铸坯的实际检测成分如表2所示,铸坯金相组织如图2所示。
36.本实施例铸坯经锻造后制备成直径为50 mm的圆坯,进行1000℃保温30 min淬火+200℃保温 150min回火,其力学性能如表3所示。
37.实施例28.0cr18mo0.15n高碳高铬含氮马氏体不锈钢组织的控制方法,采用氮化锰铁合金化实现钢液成分调整,包括如下步骤:s1、钢液冶炼;采用50 kg中频炉在大气环境下冶炼50 kg钢水,cr含量控制在:cr 16.0%,除n、cr元素以外,其他元素控制到符合表1所述成分范围;s2、钢液成分调整,将钢液c/n值控制为5左右;在中频炉内精炼钢液,精炼渣的各组分重量百分比为:46%cao、20%sio2、22%al2o3、10%mgo。在精炼剂覆盖保护下进行钢液成分调整,加入3 kg的fencr10-b调整n和cr的含量,调整n和cr的含量,以符合表1所述成分范围;精炼期间炉体底部持续吹入氮气和/或氩气,氮气和/或氩气流量处于软吹搅拌状态,保证渣面微动、钢液不裸露;成分调整达到要求后,炉底继续吹入惰性气体弱搅拌软吹,时间控制在5min。
38.s3、浇铸;钢液成分调整结束后,加热至浇铸温度,保温5 min,扒渣后浇入钢模,自然冷却得到铸坯,铸坯的实际检测成分如表2所示,铸坯金相组织如图3所示。
39.本实施例铸坯经锻造后制备成直径为50 mm的圆坯,进行1000℃保温30min淬火+200℃保温150 min回火,其力学性能如表3所示,sem图如图5所示。
40.实施例37.0cr18mo0.25n高碳高铬含氮马氏体不锈钢组织的控制方法,采用氮化钼铁合金化实现钢液成分调整,包括如下步骤:s1、钢液冶炼;采用50 kg中频炉在大气环境下冶炼50kg钢水,cr含量控制在:cr 15.5 %,除n、cr元素以外,其他元素控制到符合表1所述成分范围;s2、钢液成分调整,将钢液c/n值控制为3左右;本实施例不进行精炼,所述钢液成分调整在氮气和/或氩气气体保护下进行,加入5 kg的fencr10-b调整n和cr的含量,调整n和cr的含量,以符合表1所述成分范围,所述钢液成分调整期间,炉体内惰性气体的压力为0.9atm;成分调整达到要求后,炉底继续吹入惰性
气体弱搅拌软吹,时间控制在10 min。
41.s3、浇铸;钢液成分调整结束后,加热至浇铸温度,保温6 min,扒渣后浇入钢模,自然冷却得到铸坯,铸坯的实际检测成分如表2所示,铸坯金相组织如图4所示;本实施例铸坯经锻造制备成直径为50 mm的圆坯,进行1000℃保温30 min淬火+200℃保温150 min回火,其力学性能如表3所示。
42.对比例19cr18mo高碳高铬含氮马氏体不锈钢的制备方法,包括如下步骤:s1、钢液冶炼;采用50 kg中频炉在大气环境下冶炼50kg钢水,元素控制到符合表1所述成分范围;s2、精炼熔炼结束后,在中频感应炉内精炼钢液,精炼渣系的各组分重量百分比为:28%cao、40%sio2、25%al2o3、4%mgo及3%的钙。精炼期间,炉底吹氩精炼钢液,时间控制在10 min。精炼结束后调整氩气流量处于软吹搅拌状态,软吹状态为渣面微动,钢液不裸露。
43.s3、浇铸;精炼结束后,加热至浇铸温度,保温6 min,扒渣后浇入钢模,自然冷却得到铸坯,铸坯的实际检测成分如表2所示,铸坯金相组织如图1所示。
44.对比例1铸坯经锻造制备成直径为50 mm的圆坯,进行1000℃保温30 min淬火+200℃保温150 min回火,其力学性能如表3所示。
45.表1 本发明各实施例和对比例钢的设计成分控制范围(wt%)表2 本发明各实施例和对比例钢的实际检测成分(wt%)表3 本发明各实施例和对比例钢的力学性能
根据本发明实施例1-3可以看出,与对比例1相比,采用本发明的方法,以氮部分替代碳后,铸坯组织得到改善,晶界处的一次碳化物明显减少与细化;调控c/n值明显影响铸坯凝固组织,本发明实施例2高碳高铬含氮马氏体不锈钢铸坯中的碳化物最为细小;图5为本发明实施例2高碳高铬含氮马氏体不锈钢经锻造后,进行1000℃保温30 min淬火+200℃保温150min回火的sem图,可以看出,经锻造和热处理后,基体中弥散分布有细小碳化物和其它含氮析出相,在这些细小析出相的协同强化作用下,本发明不锈钢可以获得优良的综合力学性能,其硬度≥55 hrc,抗拉强度≥1850 mpa;在较优实施例中,本发明不锈钢可以获得优良的综合力学性能,其硬度≥60 hrc,抗拉强度≥2000 mpa。
46.以上所述仅为本发明的优选实施例,并非因此限制本发明的专利范围,凡是在本发明的发明构思下,利用本发明说明书内容所作的等效结构变换,或直接/间接运用在其他相关的技术领域均包括在本发明的专利保护范围内。