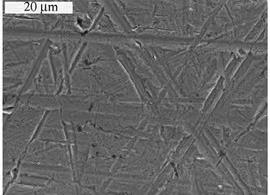
1.本发明涉及一种铝合金表面磷化处理方法,属于金属表面处理技术领域。
背景技术:2.铝合金经化学转化膜处理,可以改善其耐蚀性,也可作为涂装底层和润滑底层,其中涂装底层处理主要有三种方法:铬酸(或硫酸)阳极化、阿洛丁化学氧化和磷化处理。阳极化处理需要电解槽、电源等设施,投资较大,同时阳极化处理也会降低铝合金的机械性能,尤其对抗疲劳性能影响最大;阿洛丁处理对工件表面的前、后处理要求严,工序复杂。而且这两种处理方法都将产生含铬的有毒工业废水,对环境污染严重。磷化处理对环境污染小,成本低,是具有长远前景的表面防腐蚀处理方法。
3.中国专利cn105862025a公开了一种铝合金压铸件磷化表面处理工艺,所述工艺包括以下步骤:1.提供铝合金压铸件;2.对铝合金压铸件进行表面预处理;3.对铝合金压铸件进行冷喷涂;4.对铝合金压铸件进行磷化处理。所述铝合金压铸件表面处理工艺,克服了铝合金压铸件表面的缺陷,得到表面质量较高的铝合金压铸产品。该专利磷化处理后的铝合金件,耐腐蚀性能差,表面耐磨性也比较差。
4.中国专利cn105463432a公开了一种铝合金表面磷化处理用处理液的制备方法,首先向容器中加入7份马来酸酐和40份去离子水,搅拌5分钟;接着缓慢加入5份水杨酸,边加边搅拌,添加完毕后搅拌5分钟;接着缓慢加入6份钼酸铵和20份去离子水,边加边搅拌,添加完毕后搅拌5分钟;然后缓慢加入0.5份黄酮甙,边加边搅拌,添加完毕后搅拌10分钟;最后快速加入5份硝酸胍和30份去离子水,搅拌10分钟。该专利所述磷化液处理得到的铝合金表面耐磨性差,耐腐蚀性也比较差。
5.以上可以看到,目前铝合金的磷化处理仍存在处理后铝合金表面耐腐蚀性差,耐磨性差等问题。
技术实现要素:6.针对上述现有技术存在的不足,本发明提供一种铝合金表面磷化处理方法,实现以下发明目的:磷化处理后得到表面耐磨性好,耐腐蚀性好的铝合金件。
7.为实现上述发明目的,本发明采取以下技术方案:一种铝合金表面磷化处理方法,包括表面清洗,表面活化,磷化处理,磷化膜后处理。
8.以下是对上述技术方案的进一步改进:步骤1、表面清洗用100~300目砂纸将铝合金件表面打磨干净后,用清水冲洗除去表面碎屑,自然晾干,然后浸没入清洗液中,将清洗液加热至60~85℃,恒温浸渍20~40分钟后,取出,用清水冲洗3~5次后,自然晾干,得到表面清洗后的铝合金件,备用;所述清洗液由三聚磷酸钠、酒石酸、六亚甲基四胺、苯甲酸钠、去离子水组成;
所述三聚磷酸钠、酒石酸、六亚甲基四胺、苯甲酸钠、去离子水的质量比为5~9:8~13:1.5~4:1~3:70~100。
9.步骤2、表面活化将表面清洗后的铝合金件浸没入活化液中,将活化液加热至85~105℃,恒温浸渍5~13分钟后,取出铝合金件,用清水冲洗3~6次后,自然晾干得到表面活化后的铝合金件;所述活化液由过硫酸钠、焦磷酸钠、1-(2-羟乙基)-2-烷基-咪唑啉、亚硝酸钠、去离子水组成;所述过硫酸钠、焦磷酸钠、1-(2-羟乙基)-2-烷基-咪唑啉、亚硝酸钠、去离子水的质量比为2~9:3~10:1~4:2~5:75~100。
10.步骤3、磷化处理将表面活化后的铝合金件浸没入磷化液中,加热至65~90℃,恒温浸渍15~30分钟,取出,用清水冲洗4~6次后,自然晾干,得到磷化处理的铝合金件;所述磷化液由zn( h2po4) 2
、磷酸锰、磷酸、酒石酸铜、高氯酸钴、2-萘磺酸钠、去离子水组成;所述zn( h2po4) 2
、磷酸锰、磷酸、酒石酸铜、高氯酸钴、2-萘磺酸钠、去离子水的质量比为5~14:2~7:8~13:1~4:0.5~1.4:1~3.5:75~90。
11.步骤4、磷化膜后处理将磷化处理的铝合金件浸没入105~120℃的后处理液中,恒温浸渍20~40分钟,取出降至室温,用清水冲洗5~7次后,自然晾干,得到表面附有磷化膜的铝合金件;所述后处理液由钼酸钠、磷酸氢二钠、丙烯基硫脲、钨酸钠、去离子水组成;所述钼酸钠、磷酸氢二钠、丙烯基硫脲、钨酸钠、去离子水的质量比为1~5:4~9:3~6:1~3.5:65~100。
12.与现有技术相比,本发明取得以下有益效果:1、采用本发明所述磷化处理方法,得到了表面耐磨性好,耐腐蚀性好的铝合金件,所得铝合金件的自腐蚀电位为-0.818~-0.831v,自腐蚀电流密度为0.013~0.016a/cm2,磨损量为0.0276~0.0297mg/cm2;2、本发明通过自主设计的活化液对铝合金件进行了表面活化处理,这种活化处理能够积极提升磷化处理时磷化液的反应程度,进而生成耐磨性好,耐腐蚀性好的磷化膜,活化液中的过硫酸钠提供强氧化作用,用来氧化腐蚀铝合金表面,焦磷酸钠能够起到ph缓冲作用,以维持活化过程中ph值的稳定,1-(2-羟乙基)-2-烷基-咪唑啉和亚硝酸钠为表面活性剂和润湿剂,能对铝合金表面起到润湿、吸附和沉积作用,以提高反应过程中,反应物与铝合金表面的接触面积,同时促进铝合金表面反应物吸附和结晶体的沉积;3、本发明所述磷化液中,加入了共成膜助剂磷酸锰和酒石酸铜,这两者能有效促进磷化膜的结晶细化,提高磷化膜的致密度,同时加入高氯酸钴、2-萘磺酸钠两种磷化促进剂,提升了磷化反应程度,使磷化膜的耐磨性和致密度同时得到提高;4、本发明设计的磷化膜后处理步骤,能够进一步提升磷化膜的耐磨性和耐腐蚀性,其中钼酸钠和钨酸钠在磷酸氢二钠和丙烯基硫脲提供的碱性环境中,能够进一步封闭磷化膜表面的缺陷,使磷化膜变的更为致密,这能够极大提升磷化膜的综合性能。
附图说明
13.图1为本发明实施例1表面磷化处理后铝合金的sem图;图2为本发明实施例2表面磷化处理后铝合金的sem图;图3为本发明实施例3表面磷化处理后铝合金的sem图。
具体实施方式
14.以下对本发明的优选实施例进行说明,应当理解,此处所描述的优选实施例仅用于说明和解释本发明,并不用于限定本发明。
15.实施例1:一种铝合金表面磷化处理方法包括以下步骤:1、表面清洗用200目砂纸将铝合金件表面打磨干净后,用清水冲洗除去表面碎屑,自然晾干,然后浸没入清洗液中,将清洗液加热至75℃,恒温浸渍30分钟后,取出,用清水冲洗4次后,自然晾干,得到表面清洗后的铝合金件,备用;所述清洗液由三聚磷酸钠、酒石酸、六亚甲基四胺、苯甲酸钠、去离子水组成;所述三聚磷酸钠、酒石酸、六亚甲基四胺、苯甲酸钠、去离子水的质量比为7:11:3:2:85。
16.2、表面活化将表面清洗后的铝合金件浸没入活化液中,将活化液加热至95℃,恒温浸渍10分钟后,取出铝合金件,用清水冲洗5次后,自然晾干得到表面活化后的铝合金件;所述活化液由过硫酸钠、焦磷酸钠、1-(2-羟乙基)-2-烷基-咪唑啉、亚硝酸钠、去离子水组成;所述过硫酸钠、焦磷酸钠、1-(2-羟乙基)-2-烷基-咪唑啉、亚硝酸钠、去离子水的质量比为7:6:3:4:90。
17.3、磷化处理将表面活化后的铝合金件浸没入磷化液中,加热至80℃,恒温浸渍25分钟,取出,用清水冲洗5次后,自然晾干,得到磷化处理的铝合金件;所述磷化液由zn( h2po4) 2
、磷酸锰、磷酸、酒石酸铜、高氯酸钴、2-萘磺酸钠、去离子水组成;所述zn( h2po4) 2
、磷酸锰、磷酸、酒石酸铜、高氯酸钴、2-萘磺酸钠、去离子水的质量比为9:4:10:2:0.9:2.5:85。
18.4、磷化膜后处理将磷化处理的铝合金件浸没入110℃的后处理液中,恒温浸渍30分钟,取出降至室温,用清水冲洗6次后,自然晾干,得到表面附有磷化膜的铝合金件;所述后处理液由钼酸钠、磷酸氢二钠、丙烯基硫脲、钨酸钠、去离子水组成;所述钼酸钠、磷酸氢二钠、丙烯基硫脲、钨酸钠、去离子水的质量比为3:6:5:2:80。
19.实施例2:一种铝合金表面磷化处理方法包括以下步骤:1、表面清洗
用100目砂纸将铝合金件表面打磨干净后,用清水冲洗除去表面碎屑,自然晾干,然后浸没入清洗液中,将清洗液加热至60℃,恒温浸渍20分钟后,取出,用清水冲洗3次后,自然晾干,得到表面清洗后的铝合金件,备用;所述清洗液由三聚磷酸钠、酒石酸、六亚甲基四胺、苯甲酸钠、去离子水组成;所述三聚磷酸钠、酒石酸、六亚甲基四胺、苯甲酸钠、去离子水的质量比为5:8:1.5:1:70。
20.2、表面活化将表面清洗后的铝合金件浸没入活化液中,将活化液加热至85℃,恒温浸渍5分钟后,取出铝合金件,用清水冲洗3次后,自然晾干得到表面活化后的铝合金件;所述活化液由过硫酸钠、焦磷酸钠、1-(2-羟乙基)-2-烷基-咪唑啉、亚硝酸钠、去离子水组成;所述过硫酸钠、焦磷酸钠、1-(2-羟乙基)-2-烷基-咪唑啉、亚硝酸钠、去离子水的质量比为2:3:1:2:75。
21.3、磷化处理将表面活化后的铝合金件浸没入磷化液中,加热至65℃,恒温浸渍15分钟,取出,用清水冲洗4次后,自然晾干,得到磷化处理的铝合金件;所述磷化液由zn( h2po4) 2
、磷酸锰、磷酸、酒石酸铜、高氯酸钴、2-萘磺酸钠、去离子水组成;所述zn( h2po4) 2
、磷酸锰、磷酸、酒石酸铜、高氯酸钴、2-萘磺酸钠、去离子水的质量比为5:2:8:1:0.5:1:75。
22.4、磷化膜后处理将磷化处理的铝合金件浸没入105℃的后处理液中,恒温浸渍20分钟,取出降至室温,用清水冲洗5次后,自然晾干,得到表面附有磷化膜的铝合金件;所述后处理液由钼酸钠、磷酸氢二钠、丙烯基硫脲、钨酸钠、去离子水组成;所述钼酸钠、磷酸氢二钠、丙烯基硫脲、钨酸钠、去离子水的质量比为1:4:3:1:65。
23.实施例3:一种铝合金表面磷化处理方法包括以下步骤:1、表面清洗用300目砂纸将铝合金件表面打磨干净后,用清水冲洗除去表面碎屑,自然晾干,然后浸没入清洗液中,将清洗液加热至85℃,恒温浸渍40分钟后,取出,用清水冲洗5次后,自然晾干,得到表面清洗后的铝合金件,备用;所述清洗液由三聚磷酸钠、酒石酸、六亚甲基四胺、苯甲酸钠、去离子水组成;所述三聚磷酸钠、酒石酸、六亚甲基四胺、苯甲酸钠、去离子水的质量比为9:13:4:3:100。
24.2、表面活化将表面清洗后的铝合金件浸没入活化液中,将活化液加热至105℃,恒温浸渍13分钟后,取出铝合金件,用清水冲洗6次后,自然晾干得到表面活化后的铝合金件;所述活化液由过硫酸钠、焦磷酸钠、1-(2-羟乙基)-2-烷基-咪唑啉、亚硝酸钠、去离子水组成;
所述过硫酸钠、焦磷酸钠、1-(2-羟乙基)-2-烷基-咪唑啉、亚硝酸钠、去离子水的质量比为9:10:4:5:100。
25.3、磷化处理将表面活化后的铝合金件浸没入磷化液中,加热至90℃,恒温浸渍30分钟,取出,用清水冲洗6次后,自然晾干,得到磷化处理的铝合金件;所述磷化液由zn( h2po4) 2
、磷酸锰、磷酸、酒石酸铜、高氯酸钴、2-萘磺酸钠、去离子水组成;所述zn( h2po4) 2
、磷酸锰、磷酸、酒石酸铜、高氯酸钴、2-萘磺酸钠、去离子水的质量比为14:7:13:4:1.4:3.5:90。
26.4、磷化膜后处理将磷化处理的铝合金件浸没入120℃的后处理液中,恒温浸渍40分钟,取出降至室温,用清水冲洗7次后,自然晾干,得到表面附有磷化膜的铝合金件;所述后处理液由钼酸钠、磷酸氢二钠、丙烯基硫脲、钨酸钠、去离子水组成;所述钼酸钠、磷酸氢二钠、丙烯基硫脲、钨酸钠、去离子水的质量比为5:9:6:3.5:100。
27.实施例1-3表面磷化处理后铝合金的sem图见附图1-3;由附图1-3可见,磷化膜的表面均呈现一定的纹理结构,且磷化膜的平整度较好,未观察到有明显的凸起或凹陷区域,另外磷化膜的孔隙缺陷也极少,致密度较高,这表明磷化处理的工艺过程中,磷化物晶体生成和沉积的速率非常平稳,晶体间内聚力较强,所以能够最终得到致密度较高的磷化膜层。
28.对比例1:在实施例1基础上,不进行步骤2表面活化步骤1同于实施例1操作;步骤2中,在实施例1基础上将清洗后的铝合金件浸没入磷化液中,其它操作同于实施例1中的步骤3;步骤3中操作同于实施例1中的步骤4。
29.对比例2:在实施例1基础上,步骤3中将磷酸锰、酒石酸铜等量替换为去离子水步骤1、2的操作同于实施例1;步骤3中,在实施例1基础上,将4份磷酸锰和2份酒石酸铜等量替换为6份去离子水,其它操作同于实施例1;步骤4操作同于实施例1。
30.对比例3:在实施例1基础上,步骤3中将高氯酸钴、2-萘磺酸钠等量替换为去离子水步骤1、2的操作同于实施例1;步骤3中,在实施例1基础上,将0.9份高氯酸钴和2.5份2-萘磺酸钠等量替换为3.4份去离子水,其它操作同于实施例1;步骤4操作同于实施例1。
31.对比例4:在实施例1基础上,不进行步骤4磷化膜后处理步骤1、2、3操作同于实施例1操作,得到磷化处理的铝合金件即为最终磷化处理的铝合金件。
32.耐腐蚀性测试:
将实施例1、2、3和对比例1、2、3、4得到的铝合金件作为工作电极,以铂电极作为辅助电极,以氧化汞电极和饱和甘汞电极作为参比电极,电解溶液为质量分数3 .5%的nacl溶液,测量不同铝合金电极试样的塔菲尔曲线,控制测试电位的扫面范围是开路电位
±ꢀ
1 .5v,扫描频率设置为 0 .5mv/s,由此得出自腐蚀电位和自腐蚀电流密度,具体测试数值见表1,自腐蚀电位越高,自腐蚀电流密度越低,耐腐蚀性越好;表1由表1中数据可以看到,与实施例1、2、3相比,不进行表面活化的对比例1,自腐蚀电位有所降低,自腐蚀电流也有所增大,耐腐蚀性变差,这是因为不进行表面活化,磷化处理时,铝合金表面难以和磷化液中的有效成分充分反应,得到的磷化膜耐腐蚀性变差;对比例2中不加入磷酸锰、酒石酸铜这两种能减小磷化膜结晶尺寸的物质,导致形成的磷化膜结晶度降低,进而影响了抗腐蚀效果;对比例3中,不加入高氯酸钴、2-萘磺酸钠这两种促进剂,自腐蚀电位降幅最大,同时自腐蚀电流也增幅最大,可见高氯酸钴、2-萘磺酸钠对提升磷化膜的抗腐蚀性能有显著作用;对比例4中,不进行磷化膜后处理,自腐蚀电位显著降低,同时自腐蚀电流也相应增大很多,这是因为后处理能够进一步增强磷化膜的致密程度,提高抗腐蚀性。
33.耐磨性测试:在1kg压力下,将实施例1、2、3和对比例1、2、3、4得到的铝合金件,在1000目20cm长砂纸上往复30次打磨后测量其磨损量,结果见表2:表2
由表2中数据可以看到,与实施例1、2、3相比,不进行表面活化的对比例1,耐磨性显著降低,这是因为不进行表面活化,磷化膜与基体金属的反应程度会降低,这使得磷化膜较为蓬松,耐磨性相应降低;对比例2中不加入磷酸锰、酒石酸铜会导致形成的磷化膜结晶度降低,耐磨性会大幅降低;对比例3中,不加入高氯酸钴、2-萘磺酸钠这两种促进剂,耐磨性也有非常明显的降低,这是因为促进剂对磷化膜的生成至关重要,不加促进剂,磷化膜的沉积会受到影响,进而影响耐磨性;对比例4中,不进行磷化膜后处理,耐磨性下降最为严重,可见后处理能够显著提升磷化膜的致密度和附着力。