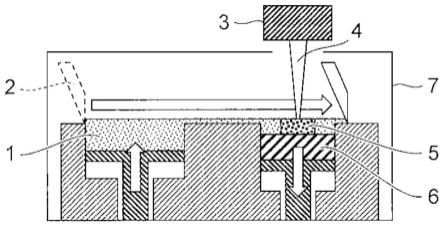
1.本发明涉及包含由铁或铁合金构成的基质和分散于该基质中的微细的硼化钛的高刚性铁基合金、以及采用层叠造型法来制造该高刚性铁基合金的方法。
背景技术:2.目前,作为结构用金属材料,最广泛地利用钢或铁合金。这些金属材料通过合金元素添加、热处理来显示出极多样的组织变化,能够宽幅地控制强度及塑韧性等机械性质。
3.然而,在实际部件的设计中变得重要的刚性是与原子间的结合力直接相关的物质固有的值,因此认为使刚性大幅地提高是困难的。
4.在这样的状况下,为了高刚性化曾进行了在铁或铁合金中使高杨氏模量的硼化物等化合物粒子分散的研究开发,例如,在日本特开2002-285303中记载了一种高刚性铁基合金,其特征在于,由基质、和分散于该基质中且粒径为1~100μm的以4a族元素为主体的硼化物中的至少一种以上构成,该基质由铁或铁合金构成,该以4a族元素为主体的硼化物在该基质中在热力学上稳定。
技术实现要素:5.然而,例如在日本特开2002-285303等所记载的高刚性铁基合金中,分散于由铁或铁合金构成的基质中的高硬度的粗大的硼化物有可能在切削加工等机械加工时破坏切削工具。
6.因此,本发明的课题是提供能够容易地进行机械加工的高刚性铁基合金及其制造方法。
7.作为高刚性铁基合金中的硼化物粗大化的主要原因,可举出:难以将构成高刚性铁基合金的基质的铁或铁合金的粉末与粒径小的硼化物、例如具有1μm以下的平均粒径的硼化物的粉末混合来得到均质的混合物;进而,在将粉末混合物熔化(熔融)时,原本微细的硼化物彼此凝聚、结合而变大;等等。
8.本发明人对用于解决上述课题的手段进行了各种研究,结果发现,通过在由铁或铁合金构成的基质中生成硼化物,且控制热过程以使得生成的硼化物不过度地结晶生长,能够在该基质中生成粒径小的硼化物。
9.于是,本发明人进一步进行了研究,结果发现,将铁钛金属间化合物(feti)的粉末、硼化铁金属间化合物(feb)的粉末、和根据情况添加的铁(fe)系粉末混合而得到混合粉末,采用伴有激光照射的层叠造型法对得到的混合粉末进行处理,通过in-situ反应(原位反应)而生成硼化钛,由此能够制造包含由铁或铁合金构成的基质和分散于该基质中的微细的硼化钛的高刚性铁基合金,从而完成了本发明。
10.即,本发明的要旨如下。
11.(1)一种高刚性铁基合金,是包含由铁或铁合金构成的基质和分散于该基质中的硼化钛的高刚性铁基合金,
12.硼化钛的基于sem图像的等效圆平均粒径为0.2μm~0.6μm。
13.(2)根据(1)所述的高刚性铁基合金,硼化钛的基于sem图像的等效圆平均粒径为0.2μm~0.4μm。
14.(3)一种制造高刚性铁基合金的方法,包含:
15.(i)将铁钛金属间化合物的粉末和硼化铁金属间化合物的粉末混合而得到混合粉末的工序;和
16.(ii)采用伴有激光照射的层叠造型法对在(i)工序中得到的混合粉末进行处理而得到高刚性铁基合金的工序。
17.(4)根据(3)所述的制造高刚性铁基合金的方法,
18.(i)工序是(i-2)将铁钛金属间化合物的粉末、硼化铁金属间化合物的粉末和铁系粉末混合而得到混合粉末的工序。
19.(5)根据(3)或(4)所述的制造高刚性铁基合金的方法,
20.在(ii)工序中,层叠造型时的冷却速度为10000k/秒以上。
21.(6)根据(3)~(5)的任一项所述的制造高刚性铁基合金的方法,在(ii)工序中,伴有激光照射的层叠造型法为pbf方式。
22.(7)根据(3)~(5)的任一项所述的制造高刚性铁基合金的方法,
23.在(ii)工序中,伴有激光照射的层叠造型法为ded方式,使铁从用于制造高刚性铁基合金的基底熔入到铁基合金中。
24.根据本发明,能提供能够容易地进行机械加工的高刚性铁基合金及其制造方法。
附图说明
25.以下参照附图来说明本发明的示例性实施方式的特征、优点、以及技术和产业上的显著性,同样的标记表示同样的要素,其中:
26.图1是示出用于实施基于pbf方式的层叠造型法的装置的一例的示意图。
27.图2是示出用于实施基于ded方式的层叠造型法的装置的一例的示意图。
28.图3是在比较例1及实施例1~3中得到的试样的示意图。
29.图4是比较例1的sem图像。
30.图5是实施例1的sem图像。
31.图6是实施例2的sem图像。
32.图7是实施例3的sem图像。
具体实施方式
33.以下,对本发明的优选的实施方式进行详细说明。
34.在本说明书中,适当参照附图对本发明的特征进行说明。在附图中,为了明确化而夸张地表示各部分的尺寸及形状,并未准确地描绘实际的尺寸及形状。因此,本发明的技术范围并不限定于这些附图中所示的各部份的尺寸及形状。再者,本发明的高刚性铁基合金及其制造方法并不限定于下述实施方式,能够在不脱离本发明的主旨的范围内以实施了本领域技术人员能够进行的变更、改良等的各种的方式来实施。
35.本发明涉及一种高刚性铁基合金,其是包含由铁或铁合金构成的基质和分散于该
基质中的硼化钛的高刚性铁基合金,硼化钛的粒径为特定的范围。
36.在此,本发明的高刚性铁基合金,具有在由铁或铁合金构成的基质中均匀地分散有微细的硼化钛的结构。
37.作为构成本发明的高刚性铁基合金的基质的铁合金,能够使用铁素体系、奥氏体系、马氏体系等的宽范围的铁合金,从热力学稳定性的观点出发,优选碳含量为0.1重量%以下的铁合金。
38.在本发明的高刚性铁基合金中,由铁或铁合金构成的基质的基于ipf图像的晶粒的等效圆平均粒径不被限定,通常超过1μm,优选是超过1μm且为5μm以下。
39.由铁或铁合金构成的基质的基于ipf图像的晶粒的等效圆平均粒径的测定方法,能够通过首先拍摄3个成为测定对象的高刚性铁基合金的ebsd法(electron back scattered diffraction pattern)(电子背散射衍射)-ipf(inverse pole figure)图像(反极点图),其次,在各图像中随机地选择30个晶粒,接着,对所选择的各晶粒算出面积,根据算出的面积来算出等效圆直径,最后,根据算出的等效圆直径取算术平均值来实施。
40.通过由铁或铁合金构成的基质的晶粒的平均粒径为上述范围,成为具有高强度及高刚性的铁基合金。
41.均匀地分散于本发明的高刚性铁基合金的由铁或铁合金构成的基质中的硼化钛,是用化学式tib2表示的二硼化物。
42.本发明的高刚性铁基合金中含有的硼化钛,是具有规则的晶体结构且构成原子牢固地结合的化合物,因此直接反映其结合力的杨氏模量是极高的。另外,硼化钛在铁合金中在热力学上稳定,因此不会引起异种原子的侵入、置换、或者其他的复合化合物的形成等的、起因于硼化钛与由铁或铁合金构成的基质的反应的结晶学上的变化。其结果,硼化钛作为即使在铁合金中也维持牢固的结合力、保持高杨氏模量而不变化、有助于铁基合金的高刚性化的强化粒子能够充分地发挥其优异的特性。因此,本发明的铁基合金能够具有极高的杨氏模量。
43.作为基于sem图像的等效圆直径,硼化钛的平均粒径为0.2μm~0.9μm,优选为0.2μm~0.6μm,更优选为0.2μm~0.4μm。
44.硼化钛的基于sem图像的等效圆平均粒径的测定方法,能够通过首先拍摄3个成为测定对象的高刚性铁基合金的bse-sem图像(反射电子图像),在各图像中随机地选择300个硼化钛,接着,针对所选择的各硼化钛算出面积,根据算出的面积算出等效圆直径,最后,根据算出的等效圆直径取算术平均值来实施。
45.通过硼化钛的平均粒径为上述范围,在高刚性铁基合金的加工时,在高硬度的硼化钛的切断中的施加于切削工具的应力被分散,降低了切削工具的破坏,在维持高刚性的状态下被切削性提高。
46.硼化钛的粒度优选一致。硼化钛的粒度不被限定,例如在硼化钛的粒子遵从正态分布时,硼化钛的粒子数的68%的粒子通常处于平均粒径
±
0.20μm、优选处于平均粒径
±
0.17μm的范围内。
47.通过硼化钛的粒度一致,在高刚性铁基合金的加工时,在高硬度的硼化钛的切断中的施加于切削工具的应力被分散,降低了切削工具的破坏,在维持高刚性的状态下被切削性提高。
48.硼化钛的含量,相对于高刚性铁基合金的总重量,通常为3重量%~40重量%,优选为7重量%~35重量%。
49.通过硼化钛的含量为上述范围,硼化钛不会发生硼化物彼此的凝聚、合体的形成,在高刚性铁基合金中能够发挥充分的机械特性、特别是高刚性。
50.因此,本发明的高刚性铁基合金,显示出由具有硼化钛带来的充分的机械特性、特别是高刚性,而且,通过该硼化钛是微细的,在切削工序中能够不破坏切削工具而容易地进行切削。
51.本发明的高刚性铁基合金,除了硼化钛以外,也可以根据最终得到的高刚性铁基合金中所要求的成分来包含一种以上的其他元素、例如镍、钴、铬、镁、钼、碳、锰、以及它们的化合物、例如硼化物等。
52.而且,本发明也涉及上述说明的本发明的高刚性铁基合金的制造方法。即,本发明涉及一种制造高刚性铁基合金的方法,其包含:(i)将铁钛金属间化合物的粉末和硼化铁金属间化合物的粉末混合而得到混合粉末的工序;和(ii)采用伴有激光照射的层叠造型法对在(i)工序中得到的混合粉末进行处理而得到高刚性铁基合金的工序。
53.以下对(i)~(ii)的各工序进行说明。
54.(i)将铁钛金属间化合物的粉末和硼化铁金属间化合物的粉末混合而得到混合粉末的工序
55.在本发明的(i)工序中,将铁钛金属间化合物的粉末和硼化铁金属间化合物的粉末混合而得到混合粉末。
56.铁钛金属间化合物的粉末是包含铁和钛的合金(feti)的粉碎粉末。
57.铁钛金属间化合物的粉末的平均粒径不被限定,例如作为通过激光衍射-散射法测定出的体积基准的粒度分布中的d50,通常为25μm~200μm,优选为45μm~140μm。
58.通过铁钛金属间化合物的粉末的平均粒径为上述范围,能够容易且均匀地进行与硼化铁金属间化合物的粉末的混合。
59.铁钛金属间化合物的组成能够依所制造的高刚性铁基合金中所包含的硼化钛的量而变更,但以使得铁与钛的重量比(fe:ti)通常成为80:20~25:75、优选成为70:30~50:50的方式进行调整。
60.通过铁钛金属间化合物的组成为上述范围,能够得到稳定的铁钛金属间化合物,通过与硼化铁金属间化合物的反应,能够在最终得到的高刚性铁基合金中确保上述说明的量的硼化钛。
61.硼化铁金属间化合物的粉末是包含铁和硼的合金(feb)的粉碎粉末。
62.硼化铁金属间化合物的粉末的平均粒径不被限定,例如作为通过激光衍射-散射法测定出的体积基准的粒度分布中的d50,通常为25μm~200μm,优选为45μm~140μm。
63.通过硼化铁金属间化合物的粉末的平均粒径为上述范围,能够容易且均匀地进行与铁钛金属间化合物的粉末的混合。
64.硼化铁金属间化合物的组成能够依所制造的高刚性铁基合金中所包含的硼化钛的量而变更,但以使得铁与硼的重量比(fe:b)通常成为95:5~70:30、优选成为85:15~75:25的方式进行调整。
65.通过硼化铁金属间化合物的组成为上述范围,能够得到稳定的硼化铁金属间化合
物,通过与铁钛金属间化合物的反应,能够在最终得到的高刚性铁基合金中确保上述说明的量的硼化钛。
66.再者,铁钛金属间化合物的粉末及硼化铁金属间化合物的粉末,也可以根据最终得到的高刚性铁基合金中所要求的成分来包含一种以上的其他元素、例如镍、钴、铬、镁、钼、碳、锰等。
67.铁钛金属间化合物的粉末与硼化铁金属间化合物的粉末的混合比,能够依各材料的组成、所制造的高刚性铁基合金中所包含的硼化钛的量而变更。例如,铁钛金属间化合物的粉末与硼化铁金属间化合物的粉末的重量比(feti:feb)通常为75:25~25:75,优选为60:40~40:60。或者,铁钛金属间化合物的粉末与硼化铁金属间化合物的粉末的混合比以使得钛与硼的重量比(ti:b)通常成为1:1~10:1、优选成为1.5:1~2.5:1的方式进行调整。
68.通过铁钛金属间化合物的粉末与硼化铁金属间化合物的粉末的混合比为上述范围,在由铁或铁合金构成的基质中,铁钛金属间化合物和硼化铁金属间化合物充分地反应,能够在最终得到的高刚性铁基合金中确保上述说明的量的硼化钛。
69.在铁钛金属间化合物的粉末与硼化铁金属间化合物的粉末的混合中,也可以作为材料进一步混合铁系粉末。
70.因此,本发明的(i)工序可以是(i-2)将铁钛金属间化合物的粉末、硼化铁金属间化合物的粉末和铁系粉末混合而得到混合粉末的工序。
71.铁系粉末不被限定,能够使用例如铁的粉碎粉末、例如铁的水雾化粉。另外,铁系粉末可以是铁的合金、例如铁与一种以上的其他元素例如镍、钴、铬、镁、钼、碳、锰的合金的粉末。
72.铁系粉末的平均粒径不被限定,例如作为通过激光衍射-散射法测定出的体积基准的粒度分布中的d50,通常为25μm~250μm,优选为25μm~140μm。
73.通过铁系粉末的平均粒径为上述范围,能够容易且均匀地进行铁系粉末和铁钛金属间化合物的粉末及硼化铁金属间化合物的粉末的混合。
74.作为铁系粉末,能够使用例如
ヘガネス
公司制的asc100.29。
75.能追加到混合粉末中的铁系粉末的量不被限定,相对于混合粉末的总重量,通常为5重量%~50重量%,优选为15重量%~35重量%。或者,能追加到混合粉末中的铁系粉末的量以使得铁钛金属间化合物的粉末及硼化铁金属间化合物的粉末与铁系粉末的重量比(feti+feb:fe)通常成为95:5~50:50的方式进行调整。或者,能追加到混合粉末中的铁系粉末的量以所制造的高刚性铁基合金中所包含的硼化钛的量成为上述范围的方式进行调整。
76.通过在得到混合粉末的工序中添加铁系粉末,能够抑制所制造的高刚性铁基合金中所包含的硼化钛的凝聚、生长,硼化钛的平均粒径进一步变小,且分散性提高。
77.再者,在(i)或(i-2)工序中,也可以根据最终得到的高刚性铁基合金中所要求的成分来混合包含一种以上的其他元素例如镍、钴、铬、镁、钼、碳、锰等的粉末。
78.各粉末、即铁钛金属间化合物的粉末、硼化铁金属间化合物的粉末、根据情况添加的铁系粉末、和根据情况添加的包含一种以上的其他元素的粉末的混合顺序、混合方法不被限定,能够使用在本技术领域中公知的混合手段进行混合。例如,在混合粉末包含铁系粉末的情况下,可以在将铁钛金属间化合物的粉末和硼化铁金属间化合物的粉末混合后将铁
系粉末混合,可以在将铁钛金属间化合物的粉末和铁系粉末混合后将硼化铁金属间化合物混合,可以在将硼化铁金属间化合物的粉末和铁系粉末混合后将铁钛金属间化合物混合,可以将全部的粉末同时地混合。作为各粉末的混合方法,可列举例如v型混合机(v型混粉器)、球磨机、振动磨机等。再者,各粉末也可以通过湿式混合来进行混合。
79.通过本发明的(i)工序,能够得到铁钛金属间化合物的粉末、硼化铁金属间化合物的粉末、根据情况添加的铁系粉末和根据情况添加的包含一种以上的其他元素的粉末均匀地分散的混合粉末。
80.(ii)采用伴有激光照射的层叠造型法对在(i)工序中得到的混合粉末进行处理而得到高刚性铁基合金的工序
81.在(ii)工序中,采用伴有激光照射的层叠造型法对在(i)工序中得到的混合粉末进行处理而得到高刚性铁基合金。
82.在本发明的(ii)工序中,伴有激光照射的层叠造型法是如下方法:对成为原料的混合粉末照射激光,仅将特定的部位熔化、固化,反复进行该过程从而以无模具的方式使合金成型。再者,激光的照射可以基于从3d数据变换的切片数据(slice data)来实施。
83.在伴有激光照射的层叠造型法中,能够进行混合粉末的急速加热、对流搅拌及急速冷却。
84.在使用铁钛金属间化合物的粉末和硼化铁金属间化合物的粉末作为原料而在由铁或铁合金构成的基质中形成硼化钛的铁基合金的制造方法中,在使用烧结的情况下,在混合粉末的烧结中的升温、烧结工序中,通过固相扩散形成硼化钛,其后进行生长。关于粒子,属于该粒子能够生长的环境的时间越长则越生长,因此为了得到微细的硼化钛,优选缩短在硼化钛的核形成后硼化钛能够生长的时间。因此,在本发明中,为了使用铁钛金属间化合物的粉末和硼化铁金属间化合物的粉末而在由铁或铁合金构成的基质中形成硼化钛,通过使用伴有激光照射的层叠造型法,能够加快粉末熔融后的冷却速度,即,能够缩短硼化钛的核形成后的粒子(晶体)生长时间,其结果,能够形成微细的硼化钛。
85.伴有激光照射的层叠造型法,包含例如粉末床熔融结合方式(powder bed fusion:pbf)及指向性能量堆积方式(directed energy deposition:ded)。
86.pbf是将混合粉末铺满,对进行造型的部分照射激光,使其熔融、凝固并进行层叠而使合金成型的方法。
87.在pbf中,通过照射激光而熔融的合金前驱体,以通常10000k/秒以上的速度被急速地冷却而能够制造合金。
88.图1示出用于实施基于pbf方式的层叠造型法的装置的一例的示意图。在图1中,在进行了氩气置换的罩7之中,首先,装填于原料容器中的混合粉末1被上推,被上推了的部分的混合粉末1被刮板2铺满。其次,利用激光发生器3对被刮板2铺满的混合粉末1照射激光4。当对混合粉末1照射激光4时,混合粉末1中的粉末彼此熔融结合而在基板(base plate)6上形成铁基合金5。通过一边使基板6下降一边反复实施这些工序(层叠造型),来成型出铁基合金5。
89.ded是向造型部分同时地进行混合粉末的堆积和激光的照射,熔融、层叠来造型的方法,也被称为堆焊。
90.在ded中,通过照射激光而熔融的合金前驱体以通常10000k/秒左右的速度被急速
地冷却而能够制造合金。
91.图2示出用于实施基于ded方式的层叠造型法的装置的一例的示意图。在图2中,包含混合粉末1及运送气体的含粉末气体10被放出、堆积于基底11上,与含粉末气体10的放出、堆积同时地利用激光发生器3照射激光4。当对所堆积的混合粉末1及基底11照射激光4时,混合粉末1中的粉末彼此、进而基底11熔融结合而在基底11上形成铁基合金5。通过一边降低造型平台9一边反复实施这些工序(层叠造型),来成型出铁基合金5。再者,在该方式中,为了混合粉末的飞散、外部气体的隔断及根据情况而熔融的合金前驱体的冷却而导入保护气体8。另外,在该方式中,如前所述,能够利用激光4来使基底11中所包含的铁成分熔入到铁基合金5中。因此,通过将铁或铁合金使用于基底11,代替(i-2)工序中的铁系粉末的混合、或者与(i-2)工序中的铁系粉末的混合一起而使铁熔入到铁基合金5中,关于铁基合金5中所包含的硼化钛,能够进一步减小平均粒径,并且提高分散性。
92.通过本发明的(ii)工序,铁钛金属间化合物的粉末、硼化铁金属间化合物的粉末和根据情况添加的铁系粉末通过in-situ反应以均匀地分散于由铁或铁合金构成的基质中的状态生成微细的硼化钛,其结果,能够得到被切削性优异的高刚性铁基合金。
93.以下,对关于本发明的几个实施例进行说明,但并不意图将本发明限定于这样的实施例中所示的内容。
94.1.样品制备
95.比较例1
96.通过以下的(i)及(ii)工序来制造了铁基合金。
97.(i)将铁钛金属间化合物的粉末和硼化铁金属间化合物的粉末混合而得到混合粉末的工序
98.在(i)工序中,作为铁钛金属间化合物(feti)的粉末,使用fe为57重量%、ti为43重量%的粉碎粉末(基于激光衍射-散射法的粒径(d50):45μm~140μm),作为硼化铁金属间化合物(feb)的粉末,使用fe为78重量%、b为22重量%的粉碎粉末(基于激光衍射-散射法的粒径(d50):45μm~140μm),以feti与feb的重量比成为6:4的方式调整这些粉末,通过采用v型混粉器混粉30分钟来进行混合,得到了混合粉末。
99.(ii)通过烧结来对在(i)工序中得到的混合粉末进行处理而得到铁基合金的工序
100.在(ii)工序中,将在(i)工序中得到的混合粉末以8t/cm2的压力进行压制成型,将所得到的压制成型品在1280℃、在真空气氛下烧结60分钟,其后,以15℃/分钟的速度进行冷却,得到图3中示意性地示出的单边为10mm的立方体的铁基合金。
101.实施例1
102.通过以下的(i)及(ii)工序来制造了铁基合金。
103.(i)将铁钛金属间化合物的粉末和硼化铁金属间化合物的粉末混合而得到混合粉末的工序
104.在(i)工序中,作为铁钛金属间化合物(feti)的粉末,使用fe为57重量%、ti为43重量%的粉碎粉末(基于激光衍射-散射法的粒径(d50):45μm~140μm),作为硼化铁金属间化合物(feb)的粉末,使用fe为78重量%、b为22重量%的粉碎粉末(基于激光衍射-散射法的粒径(d50):45μm~140μm),以feti与feb的重量比成为6:4的方式调整这些粉末,通过采用v型混粉器混粉30分钟来进行混合,得到了混合粉末。
105.(ii)采用伴有激光照射的层叠造型法(ded方式)对在(i)工序中得到的混合粉末进行处理而得到铁基合金的工序
106.在(ii)工序中,使用图2中所记载的装置,在下述条件下对在(i)工序中得到的混合粉末进行处理,得到图3中示意性地示出的单边为10mm的立方体的铁基合金。再者,作为基底,使用了scm435,结果在所得到的铁基合金中观测到来自基底的铁的熔入。
107.ded条件
108.激光输出:3000w
109.速度:500mm/分钟
110.1道堆焊(one bead overlay):100mm
111.冷却速度:10000k/秒
112.实施例2
113.通过以下的(i)及(ii)工序来制造了铁基合金。
114.(i)将铁钛金属间化合物的粉末和硼化铁金属间化合物的粉末混合而得到混合粉末的工序
115.在(i)工序中,作为铁钛金属间化合物(feti)的粉末,使用fe为57重量%、ti为43重量%的粉碎粉末(基于激光衍射-散射法的粒径(d50):45μm~140μm),作为硼化铁金属间化合物(feb)的粉末,使用fe为78重量%、b为22重量%的粉碎粉末(基于激光衍射-散射法的粒径(d50):45μm~140μm),以feti与feb的重量比成为1:1的方式调整这些粉末,通过采用v型混粉器混粉30分钟来进行混合,得到了混合粉末。
116.(ii)采用伴有激光照射的层叠造型法(pbf方式)对在(i)工序中得到的混合粉末进行处理而得到铁基合金的工序
117.在(ii)工序中,使用图1中所记载的装置,在下述条件下对在(i)工序中得到的混合粉末进行处理,得到图3中示意性地示出的单边为10mm的立方体的铁基合金。再者,实施例2的铁基合金的杨氏模量为300gpa。
118.pbf条件
119.激光输出:900w
120.扫描速度:1000mm/秒
121.光束直径:0.1mm
122.扫描间距:0.2mm
123.层叠厚度:0.3mm
124.冷却速度:10000k/秒以上
125.在此,所谓扫描间距是激光束的扫描间隔,所谓层叠厚度是每1层的厚度。
126.实施例3
127.通过以下的(i-2)及(ii)工序来制造了铁基合金。
128.(i-2)将铁钛金属间化合物的粉末、硼化铁金属间化合物的粉末和铁系粉末混合而得到混合粉末的工序
129.在(i-2)工序中,作为铁钛金属间化合物(feti)的粉末,使用fe为57重量%、ti为43重量%的粉碎粉末(基于激光衍射-散射法的粒径(d50):45μm~140μm),作为硼化铁金属间化合物(feb)的粉末,使用fe为78重量%、b为22重量%的粉碎粉末(基于激光衍射-散射
法的粒径(d50):45μm~140μm),作为铁(fe)系粉末,使用水雾化粉(基于激光衍射-散射法的粒径(d50):25μm~250μm),以feti、feb、fe的重量比成为1:1:1的方式调整这些粉末,通过采用v型混粉器混粉30分钟来进行混合,得到了混合粉末。
130.(ii)采用伴有激光照射的层叠造型法(pbf方式)对在(i-2)工序中得到的混合粉末进行处理而得到铁基合金的工序
131.在(ii)工序中,使用图1中所记载的装置,在下述条件下对在(i-2)工序中得到的混合粉末进行处理,得到图3中示意性地示出的单边为10mm的立方体的铁基合金。再者,实施例3的铁基合金的杨氏模量为280gpa。
132.pbf条件
133.激光输出:900w
134.扫描速度:1000mm/秒
135.光束直径:0.1mm
136.扫描间距:0.2mm
137.层叠厚度:0.3mm
138.冷却速度:10000k/秒以上
139.在此,所谓扫描间距是激光束的扫描间隔,所谓层叠厚度是每1层的厚度。
140.2.sem评价
141.拍摄了在比较例1及实施例1~3中得到的铁基合金的sem图像。将结果示于图4~7。图4是比较例1的sem图像,图5是实施例1的sem图像,图6是实施例2的sem图像,图7是实施例3的sem图像。
142.在图4~7中,12(相对地白的部分)表示由铁或铁合金构成的基质,13(相对地黑的部分)表示硼化钛。由图4可知,在比较例1中通过烧结而制造的铁基合金具有大的硼化钛。另一方面,由图5~7可知,在实施例1~3中采用层叠造型法制造的铁基合金具有小且均匀地分散于基质中的硼化钛。而且,通过图6与图7的比较可知,通过向混合粉末中进一步混合铁系粉末,硼化钛的平均粒径进一步变小,并且硼化钛的分散性提高。
143.3.被切削性评价
144.利用通用磨石切割机(湿式)来对在比较例1及实施例1~3中得到的铁基合金进行了切削。比较例1的铁基合金,阻力大,切削困难,但是,实施例1~3的铁基合金,阻力小,能够无问题地进行切削。