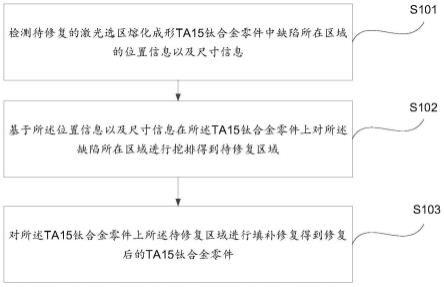
一种激光选区熔化成形ta15钛合金零件的缺陷修复方法
技术领域
1.本技术涉及材料加工技术领域,尤其涉及一种激光选区熔化成形ta15钛合金零件的缺陷修复方法。
背景技术:2.随着航天产品对零部件“轻量化、一体化、高强度”需求的提升,增材制造技术在航天制造领域的重要性突显。增材制造技术可以为产品结构创新设计带来更大的自由度,摆脱传统制造工艺的约束,实现轻量化结构设计、结构的整体或部分整体制造,减少制造工序,缩短制造周期,显著提高原材料利用率。激光选区熔化技术是一种利用高能激光逐层熔化粉末薄层,可以成形任意复杂形状的高致密度构件的增材制造技术。由于其成形精度高,对特殊复杂结构(如悬臂结构、薄壁结构、复杂曲面、空间点阵结构)制造的适用程度高,在航空航天领域得到了广泛的应用。
3.ta15钛合金具有良好的热强性和可焊接性,特别适合于制造各种焊接零部件,广泛应用于在航天领域。通常可采用激光选区熔化技术加工得到ta15钛合金零件,然而,由于激光选区熔化成形是在惰性气体保护舱的惰性气体保护下进行,基于粉床逐层精细铺粉,高能激光束熔化粉末薄层逐层熔凝堆积的过程。零件成形完毕从成形舱内取出后,无法再次铺粉进行沉积增材。因此,对于零件表面或近表面出现的局部缺陷,区别于激光熔融沉积增材制造,激光选区熔化成形无法实现缺陷的原位修复。也即,由于激光选区熔化技术本身的特性会使得加工得到的ta15钛合金零件表面或近表表面局部缺陷,而激光选区熔化成形技术无法实现对该缺陷的原位修复。
技术实现要素:4.本技术解决的技术问题是:针对现有技术中对激光选区熔化ta15钛合金零件缺陷修复不能满足实际需求,本技术提供了一种激光选区熔化成形ta15钛合金零件的缺陷修复方法,本技术实施例所提供的方案中,提供对ta15钛合金零件局部缺陷修复方案,可以解决激光选区熔化ta15钛合金零件局部缺陷无法采用原方法进行修复的问题,从而避免因零件的局部缺陷导致的整体报废。
5.第一方面,本技术实施例提供一种激光选区熔化成形ta15钛合金零件的缺陷修复方法,该方法包括:
6.检测待修复的激光选区熔化成形ta15钛合金零件中缺陷所在区域的位置信息以及尺寸信息;
7.基于所述位置信息以及尺寸信息在所述ta15钛合金零件上对所述缺陷所在区域进行挖排得到待修复区域;
8.对所述ta15钛合金零件上所述待修复区域进行填补修复得到修复后的ta15钛合金零件。
9.可选地,基于所述位置信息以及尺寸信息在所述ta15钛合金零件上对所述缺陷所
在区域进行挖排得到待修复区域,包括:
10.根据预设需求选择填补修复方式,基于所述填补修复方式确定挖排所得到的所述待修复区域的工艺坡口形状;
11.基于所述工艺坡口形状、所述位置信息以及尺寸信息对所述缺陷所在区域进行挖排得到所述修复区域。
12.可选地,所述填补修复方式包括激光熔覆修复方式以及氩弧焊修复方式;
13.基于所述填补修复方式确定挖排的工艺坡口形状,包括:
14.若所述填补修复方式为激光熔覆修复方式,所述待修复区域的工艺坡口形状为v型;或
15.若所述填补修复方式为氩弧焊修复方式,所述待修复区域的工艺坡口形状为u型。
16.可选地,其中,对于所述激光熔覆修复方式,所述工艺坡口的开口角度为45
°
~60
°
,所述工艺坡口的开口向上;或
17.对于所述氩弧焊修复方式,所述u型工艺坡口的开口角度为70
°
~80
°
所述u型工艺坡口的开口向上。
18.可选地,其中,还包括:若所述填补修复方式包括激光熔覆修复方式,设置激光熔覆修复路径,其中,所述激光熔覆修复路径中多道激光熔覆修复搭接量为单道激光熔覆修复宽度的三分之一至二分之一,且所述激光熔覆修复路径为蛇形排布。
19.可选地,对所述ta15钛合金零件上所述待修复区域进行填补修复得到修复后的ta15钛合金零件之前,还包括:
20.对所述ta15钛合金零件进行酸洗,并将所述ta15钛合金零件酸洗后用清水冲洗残留在其表面的酸洗液,以及将冲洗后的所述ta15钛合金零件放入烘箱中进行烘干处理;
21.对所述工艺坡口及其周围预设范围内的区域进行擦拭清理。
22.可选地,还包括:检测对所述待修复区域的修复效果是否满足预设要求;若不满足,则新对所述缺陷所在区域重进行挖排得到新的待修复区域,对所述新的待修复区域进行填补修复,直到修复效果满足所述预设要求或者挖排次数达到预设阈值为止。
23.可选地,还包括:在检测所述工艺坡口的修复效果满足预设要求时,对所述修复后的ta15钛合金零件进行真空热处理退火;以及对所述待修复区域表面的余高进行打磨修饰或者对所述待修复区域表面的余高去除及补充加工。
24.可选地,还包括:对所述ta15钛合金零件上所述待修复区域进行填补修复得到修复后的ta15钛合金零件之前,将所述ta15钛合金零件固定到预设的惰性气体保护舱内,并在所述ta15钛合金零件修复完成并完全冷却后,移除惰性气体保护。
25.可选地,其中,所述缺陷所对应的所述ta15钛合金零件壁厚度不小于2毫米,所述缺陷的深度小于7毫米。
附图说明
26.图1为本技术实施例所提供的一种激光选区熔化成形ta15钛合金零件的缺陷修复方法的流程示意图;
27.图2为本技术实施例所提供的一种v型工艺坡口的结构示意图;
28.图3为本技术实施例所提供的一种u型工艺坡口的结构示意图;
29.图4为本技术实施例所提供的另一种激光选区熔化成形ta15钛合金零件的缺陷修复方法的流程示意图。
具体实施方式
30.本技术实施例提供的方案中,所描述的实施例仅是本技术一部分实施例,而不是全部的实施例。基于本技术中的实施例,本领域普通技术人员在没有做出创造性劳动前提下所获得的所有其它实施例,都属于本技术保护的范围。
31.为了更好的理解上述技术方案,下面通过附图以及具体实施例对本技术技术方案做详细的说明,应当理解本技术实施例以及实施例中的具体特征是对本技术技术方案的详细的说明,而不是对本技术技术方案的限定,在不冲突的情况下,本技术实施例以及实施例中的技术特征可以相互组合。
32.以下结合说明书附图对本技术实施例所提供的一种激光选区熔化成形ta15钛合金零件的缺陷修复方法做进一步详细的说明,该方法具体实现方式可以包括以下步骤(方法流程如图1所示):
33.步骤101,检测待修复的激光选区熔化成形ta15钛合金零件中缺陷所在区域的位置信息以及尺寸信息。
34.由于采用激光选区熔化技术所成形的产品形成完毕后从惰性气体保护舱中取出后,无法对其再次铺粉进行沉积增材,故激光选取熔化技术所成形的产品可能会存在缺陷,例如,激光选取熔化技术所成形的产品的表面或者近表面可能存在气泡或者空洞等缺陷,进而影响产品的性能。
35.进一步,由于缺陷可能会存在产品的表面,也可能会存在产品的近表面,为了对产品所存在的缺陷进行修复。本技术实施例所提供的方案中,需要将缺陷所在区域进行挖排,例如,对缺陷所在区域使用小铣刀等工具进行挖除,保证将缺陷全部去除的基础上,挖排的工艺坡口(参见下文)尽量小。为了准确对缺陷所在区域进行挖排,在挖排之前需先对缺陷所在区域的位置信息以及尺寸信息进行检测。位置信息例如激光选区熔化技术所成形的零件上存在缺陷的零件壁信息或者缺陷在该零件壁上的位置等(如表面或仅表面);尺寸信息例如缺陷的深度、长度、宽度或者半径等。例如,对出现缺陷的部位采用x射线检测或超声波检测等方法进行无损检测,根据检测结果判断缺陷的位置、尺寸。
36.作为举例,缺陷所对应的ta15钛合金零件壁厚度不小于2毫米,所述缺陷的深度小于7毫米。
37.应理解,本技术实施例所提供的方案虽然针对激光选区熔化成形at15钛合金零件来对修复过程进行说明,但是只要是通过该方法对激光选区熔化成零件或产品缺陷进行修复的方案均适用本技术实施例的方案,在对此不做具体限制。
38.步骤102,基于所述位置信息以及尺寸信息在所述ta15钛合金零件上对所述缺陷所在区域进行挖排得到待修复区域。
39.在本技术实施例所提供的方案中,在确定出缺陷所在区域的位置信息和尺寸信息之后,基于位置信息和尺寸信息将ta15钛合金零件上缺陷所在区域进行挖排得到待修复区域。
40.进一步,在本技术实施例所提供的方案中,对于待修复区域可以选择不同的填补
修复方式来进行修复,其中,填补修复方式例如激光熔覆修复方式或者氩弧焊修复方式等。作为举例,根据资源情况、零件结构特或者缺陷的实际情况来选择填补修复方式。为了便于修复对于不同的填补修复方式在挖排时挖排的待修复区域的工艺坡口形状不同。即待修复区域的工艺坡口形状与后续所选择的填补修复方式有关。
41.作为举例,根据预设需求选择填补修复方式,基于所述填补修复方式确定挖排所得到的所述待修复区域的工艺坡口形状;基于所述工艺坡口形状、所述位置信息以及尺寸信息对所述缺陷所在区域进行挖排得到所述修复区域。
42.又作为举例,如图2所示,若所述填补修复方式为激光熔覆修复方式,所述待修复区域的工艺坡口形状为v型。如图3所示,若所述填补修复方式为氩弧焊修复方式,所述待修复区域的工艺坡口形状为u型。
43.进一步,对于不同的填补修复方式待修复区域的工艺坡口参数也不同,作为举例,对于所述激光熔覆修复方式,所述工艺坡口的开口角度为45
°
~60
°
,所述工艺坡口的开口向上,其中,向上例如指工艺坡口的开口指向缺陷所在零件壁的上表面。应理解,工艺坡口的具体深度及开口角度可由本领域技术人员根据实际缺陷尺寸、所在位置结构特点以及激光熔覆单道成形尺寸进行设置,本技术实施例中对此不做具体限制。
44.又作为举例,对于所述氩弧焊修复方式,所述u型工艺坡口的开口角度为70
°
~80
°
所述u型工艺坡口的开口向上。应理解,对于采用氩弧焊修复方式进行修复,挖排形成的工艺坡口为近u型工艺坡口,工艺坡口的具体深度及开口角度可由本领域技术人员根据实际需求进行设置,本技术实施例中对此不做具体限制。
45.步骤103,对所述ta15钛合金零件上所述待修复区域进行填补修复得到修复后的ta15钛合金零件。
46.执行对所述ta15钛合金零件上所述待修复区域进行填补修复得到修复后的ta15钛合金零件。而由于对所述ta15钛合金零件上所述待修复区域进行填补修复的方式有多种,不同填补修复方式的原理不同,下面以激光熔覆修复方式以及氩弧焊修复方式为了对待修复区域进行填补修复过程进行简要介绍。
47.一、激光熔覆修复方式
48.对于采用激光熔覆修复方式进行修复,将所述ta15钛合金零件固定到预设的惰性气体保护舱内,并设置所述惰性气体保护舱内氧含量不大于100ppm。固定ta15钛合金零件,保证工艺坡口开口与水平面垂直,开口向上,粉斑熔化后形成的熔池垂直进入工艺坡口。具体采用的激光功率、送粉速度、扫描速度等激光熔覆工艺参数可由本领域技术人员和操作人员根据实际需求进行设置,本技术实施例中对此不做具体限制。
49.进一步,设置熔覆修复路径,其中,所述激光熔覆修复路径中多道激光熔覆修复搭接量为单道激光熔覆修复宽度的三分之一至二分之一,且所述激光熔覆修复路径为蛇形排布。
50.二、氩弧焊修复方式
51.对于采用氩弧焊修复方式进行修复,需在充氩箱内进行,采用ta15焊丝,具体焊丝直径、钨极直径、焊接电流等氩弧焊工艺参数可由本领域技术人员和操作人员根据实际需求进行设置,本技术实施例中对此不做具体限制。另外,当填补体积较大时(如,待修复区域的体积大于预设阈值)应注意控制热输入,例如,较常见的控制热输入的方法为多层焊接,
需前一层焊接金属完全冷却后再进行下一层焊接。在补焊接近结束时,逐渐减少焊接电流,减小熔区。进一步,在氩弧焊修复过程中,需严格惰性气体保护。并且在氩弧焊修复完成后,保持在惰性气氛中直至零件完全冷却。
52.本技术实施例所提供的方案中,可以根据实际情况选择氩弧焊接或激光熔覆修复方式,以提高修复后的零件效果。
53.参见图4,本技术实施例所提供的方案中,在对待修复区域进行修复之前,即在执行步骤103之前,还包括步骤104:对待修复区域(如工艺坡口部位)进行x射线检测或超声检测,检查原缺陷是否全部去除,需确保缺陷排除干净。
54.进一步,在确定缺陷排除干净后,对缺陷所对应的待修复区域进行填补修复之前,还包括步骤105:对所述ta15钛合金零件进行酸洗,并将所述ta15钛合金零件酸洗后用清水冲洗残留在其表面的酸洗液,以及将冲洗后的所述ta15钛合金零件放入烘箱中进行烘干处理;以及对所述工艺坡口及其周围预设范围内的区域进行擦拭清理。
55.作为举例,使用氢氟酸和硝酸将待修复零件进行酸洗。酸洗后用清水将残留在零件表面的酸洗液冲洗干净,放入烘箱中进行烘干处理。具体烘干时间和温度根据产品情况制定,本技术实施例中对此不做具体限制。修复前,使用无水乙醇对待修复的工艺坡口及周围区域进行擦拭清理,清理后不可用手直接触摸。
56.进一步,在本技术实施例所提供的方案中,在对待修复区域填补修复后,还需要对待修复区域的修复效果进行检测,即执行步骤103之后,还要执行步骤106:对待修复区域的修复效果进行检测。
57.作为举例,修复完成后,检测对所述待修复区域的修复效果是否满足预设要求。若不满足,则新对所述缺陷所在区域重进行挖排得到新的待修复区域,对所述新的待修复区域进行填补修复,直到修复效果满足所述预设要求或者挖排次数达到预设阈值为止。例如,对修复后不满足要求的部位可重复挖排修复,但同一位置的修复次数不超过2次。
58.进一步,执行步骤106之后,还需要执行步骤107,修复后去应力热处理;以及执行步骤108,修复区域表面修饰处理。作为举例,若待修复区域的修复效果满足预设要求,将修复后的零件进行真空热处理退火,例如,真空热处理退火在激光熔覆修复后8h内入炉。以及若待修复区域的修复效果满足预设要求,对修复后的待修复区域表面的余高进行打磨修饰,或采用机械加工的方式进行其表面余高的去除及补充加工。
59.本技术实施例所提供的方案,提供对ta15钛合金零件局部缺陷修复方案,可以解决激光选区熔化ta15钛合金零件局部缺陷无法采用原方法进行修复的问题。
60.为了便于理解上述对ta15钛合金零件缺陷修复方案的效果,下面以举例的形式对其效果进行说明。
61.实例一
62.采用本技术提供的修复方法进行激光选区熔化ta15钛合金零件局部缺陷的修复。某钛合金端框类零件激光选区熔化成形后,经x射线检测发现端面存在裂纹缺陷,裂纹总长度约5mm,该处结构壁厚15mm,裂纹所处位置距离侧壁端面大于2mm,采用激光熔覆的方法进行修复。比对x射线检测影像,对裂纹缺陷进行挖排,制作深度为5mm,开口角度45
°
的梯形工艺坡口槽,修复的工艺坡口槽开口方向需保证零件放置时,激光熔覆送粉能够垂直入射。工艺坡口制作完成后再次进行x射线检测,检查内部质量需保证裂纹缺陷全部排除干净。对零
件进行酸洗,酸洗完成后用洁净清水将残留的酸洗液冲洗干净。冲洗完成后使用高压气枪将表面残留的水分吹干,然后至于烘箱干燥,烘干温度为100℃~120℃,烘干时间0.5h。激光熔覆修复前对待修复的工艺坡口进行打磨清理,并用白绸布蘸取无水乙醇擦洗干净,清理后不得赤手触摸待修复工艺坡口表面。将待修复的零件置于惰性气体保护舱,使用夹具与基板固定,保证激光熔覆修复送粉能向工艺坡口垂直入射。进行ta15粉末材料准备、设备准备、程序准备。进行惰性气体保护舱洗气,保证氧含量小于或等于100ppm。进行ta15钛合金激光熔覆修复,激光功率2300w-2500w,光斑直径2mm,行走速度10mm/s,保护气流量16l/min-23l/min,偏移量1.5mm,单层提升量1mm,行走路径为蛇形往复,保证激光熔覆修复最后一层沉积层高于基体表面,防止表面余高打磨修饰后局部尺寸亏损。进一步,梯形工艺坡口槽端面若存在尺寸缺损问题,可将端面翻转90
°
,制作工艺坡口进行补充熔覆修复。
63.修复完成后持续进行惰性气体保护,待零件完全冷却后移出惰性气体保护舱。采用钢丝刷将表面多余物清理干净,对修复区域进行x射线检测。内部质量检测满足《qj 1666a钛及钛合金熔焊技术条件》标准中ii级接头内部质量要求。然后按照零件原沉积态热处理制度进行真空退火热处理。真空热处理退火后,对修复表面进行打磨修饰处理,将余高打磨平整,与周围母材光滑过渡。完成ta15钛合金零件激光熔覆修复工作。
64.实例二
65.采用本技术提供的修复方法进行激光选区熔化ta15钛合金零件局部缺陷的修复。某钛合金箱体类零件激光选区熔化成形后,经x射线检测发现端面存在夹杂缺陷,比对x射线检测影像位置,进行缺陷的挖排,形成深度约4mm,开口角度约70
°
的“u”形工艺坡口。对零件进行酸洗,酸洗完成后用洁净清水将残留的酸洗液冲洗干净。冲洗完成后使用高压气枪将表面残留的水分吹干,然后至于烘箱干燥,烘干温度为100℃~120℃,烘干时间0.5h。氩弧焊修复前对待修复的工艺坡口进行打磨清理,并用白绸布蘸取无水乙醇擦洗干净,清理后不得赤手触摸待修复工艺坡口表面。由于待修复零件体积较大,使用惰性气体保护拖罩进行惰性气体保护。使用合适的氩弧焊补焊工艺参数,包括气体流量、焊丝直径、钨极直径、焊接电流,对工艺坡口进行氩弧焊填补。焊接完成后持续进行惰性气体保护至零件完全冷却。然后对补焊区域进行x射线检测,检查补焊区域内部质量,满足要求后按照ta15钛合金零件沉积态热处理制度进行真空退火热处理。真空热处理退火后,对修复表面进行打磨修饰处理,将余高打磨平整,与周围母材光滑过渡。完成ta15钛合金零件氩弧焊修复工作。
66.本领域内的技术人员应明白,本技术的实施例可提供为方法、系统、或计算机程序产品。因此,本技术可采用完全硬件实施例、完全软件实施例、或结合软件和硬件方面的实施例的形式。而且,本技术可采用在一个或多个其中包含有计算机可用程序代码的计算机可用存储介质(包括但不限于磁盘存储器和光学存储器等)上实施的计算机程序产品的形式。
67.本技术是参照根据本技术实施例的方法、设备(系统)、和计算机程序产品的流程图和/或方框图来描述的。应理解可由计算机程序指令实现流程图和/或方框图中的每一流程和/或方框、以及流程图和/或方框图中的流程和/或方框的结合。可提供这些计算机程序指令到通用计算机、专用计算机、嵌入式处理机或其他可编程数据处理设备的处理器以产生一个机器,使得通过计算机或其他可编程数据处理设备的处理器执行的指令产生用于实现在流程图一个流程或多个流程和/或方框图一个方框或多个方框中指定的功能的装置。
68.这些计算机程序指令也可存储在能引导计算机或其他可编程数据处理设备以特定方式工作的计算机可读存储器中,使得存储在该计算机可读存储器中的指令产生包括指令装置的制造品,该指令装置实现在流程图一个流程或多个流程和/或方框图一个方框或多个方框中指定的功能。
69.这些计算机程序指令也可装载到计算机或其他可编程数据处理设备上,使得在计算机或其他可编程设备上执行一系列操作步骤以产生计算机实现的处理,从而在计算机或其他可编程设备上执行的指令提供用于实现在流程图一个流程或多个流程和/或方框图一个方框或多个方框中指定的功能的步骤。
70.显然,本领域的技术人员可以对本技术进行各种改动和变型而不脱离本技术的精神和范围。这样,倘若本技术的这些修改和变型属于本技术权利要求及其等同技术的范围之内,则本技术也意图包含这些改动和变型在内。