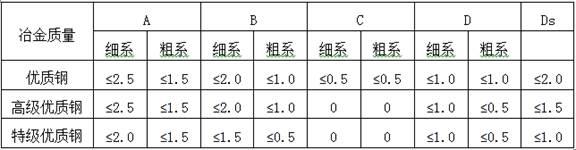
一种高碳铬轴承钢中b类夹杂物的控制方法
技术领域
1.本发明属于冶金技术领域,具体涉及一种高碳铬轴承钢中b类夹杂物的控制方法。
背景技术:2.国际上素有轴承是“工业的心脏”,轴承工业是“国民经济的武装部”之称。轴承渗透到国民经济各个部门,每个国家轴承的需求量与国民生产总值总保持一定的关系。而且在合金钢领域内,轴承钢是检验项目最多、质量要求最严、生产难度最大的钢种之一。
3.高碳铬轴承钢是目前应用最广泛的轴承钢系列,主要是用于制造轴承套圈、滚动体的重要材料。而轴承钢中的非金属夹杂物,破坏了金属的连续性,在轴承工作过程中所产生的交变应力的作用下,易于引起应力集中,成为疲劳裂纹源,降低轴承钢的疲劳寿命。因此,减少钢中的夹杂物含量是提高轴承钢的疲劳寿命的主要途径。同时,由于不同的夹杂物类型、不同的夹杂物形态、数量、尺寸和分布,对疲劳寿命的影响是不相同的,在降低夹杂物含量的同时还把夹杂物的变性处理作为降低夹杂物危害的有效手段。
4.目前轴承钢生产过程采用铝脱氧工艺,不可避免的会在钢水中加入铝制品,在钢水中经过脱氧后产生al2o3夹杂物(即b类夹杂物),若不能有效去除则影响产品质量,且目前轴承钢的夹杂物超标降级绝大部分为al2o3夹杂引起,而al2o3夹杂为脆性夹杂物,严重制约轴承的疲劳寿命,因此急需对轴承钢中的b类夹杂物进行攻关,使夹杂物达到特级优质轴承钢的水平,减少夹杂物降级并提高下游产品的疲劳寿命。gb/t 18254-2016标准中对轴承钢夹杂物要求如表1’所示:表1’:轴承钢非金属夹杂物级别要求因此,如何在不增加成本的前提下控制b类夹杂物至b粗≤0.5级,b细≤1.5级,是高碳铬轴承钢生产中亟待解决的技术问题。
技术实现要素:5.为解决上述技术问题,本发明提供一种高碳铬轴承钢中b类夹杂物的控制方法,本发明采用的技术方案是:一种高碳铬轴承钢中b类夹杂物的控制方法包括转炉、lf精炼、rh精炼和连铸工序;(1)转炉工序:吹炼过程底吹流量采用中
→
小
→
大的底吹模式,出钢钢水成分质量百分含量为:c:0.08~0.20%、p≤0.015%、s≤0.015%,出钢钢水温度1620
±
20℃,出钢氧≤
350ppm,出钢时间3.5~6.0min;出钢过程中向钢包内加入依次加入:增碳剂
→
铝粒
→
硅铁
→
锰铁
→
剩余增碳剂
→
低钛铬铁
→
预熔渣,出钢过程利用三挡出钢,出钢后钢包样成分c:0.90~0.95%,si:0.05~0.10%,mn:0.22~0.30%,p≤0.015%,s≤0.015%,al:0.050~0.070%,cr:1.35~1.45%;(2)lf精炼工序:lf精炼前期加入30~50kg碳化硅,并加入石灰、萤石、预熔渣进行造渣,加热10~15min后取样、检测,根据检测结果对mn、cr、al含量进行调整,若al≥0.040%则无需调整,若al<0.040%则一次性喂入铝线,喂入量按照钢水中al的目标含量0.050%控制;精炼中后期钢水中s≤0.005%后,一次性加入硅铁进行合金化,钢水温度及c元素以外的成分合格后,静吹5~10min;(3)rh精炼工序:真空降至100pa以下保持2min后一次性加入碳粉进行c含量调整,加入碳粉后继续保持真空≥12min,破空后喂入硅钡线200~300m,钢水软吹15~30min;rh精炼过程不向钢水加入铝制品;(4)连铸工序:连铸采用吹氩塞棒和浸入式水口,大包开浇后,中包液面高度达到350mm时,向中包投入150~200kg轴承钢专用保护渣,然后再加入足量的覆盖剂,保证钢液面不裸漏,开浇成功后打开塞棒吹氩。
6.所述转炉工序,中
→
小
→
大的底吹模式对应的底吹流量为0.06
→
0.04
→
0.08m3/(min*t)。
7.所述转炉工序,首批增碳剂加入时机为出钢1/5时,加入量为100
±
10kg;铝粒加入时机为首批增碳剂加入10~20s后;预熔渣的加入量为6~9kg/t钢。
8.所述转炉工序,预熔渣的组分及重量百分含量为:cao 40~55%、sio2≤10%、al2o
3 30~45%、mgo≤8%、al 3~8%。
9.所述lf精炼工序,精炼渣成分中al2o3重量含量控制在28~35%。
10.所述rh精炼工序,真空度≤100pa,真空保持时间≥15min;rh精炼工序仅进行碳含量调整,其余元素均在lf精炼工序调整完成。
11.所述连铸工序,轴承钢专用保护渣为一次性加入,后续不再补加;塞棒吹氩流量为0.5~0.8l/min。
12.所述高碳铬轴承钢成分要求为:c 0.95~1.05wt%,si 0.15~0.35wt%,mn 0.25~0.45wt%,cr 1.40~1.65wt%,p≤0.020wt%,s≤0.015wt%,o≤0.0012wt%,ti≤0.0015wt%,ca≤0.00010wt%。
13.所述控制方法得到的高碳铬轴承钢中b类夹杂物b粗≤0.5级、b细≤1.5级。
14.本发明的设计原理为:1、转炉采用大底吹和高拉碳相结合的方式,可有效降低钢水中的初始氧含量,减少出钢过程中脱氧剂加入量及其氧化形成的夹杂物;2、转炉采用先加部分增碳剂,对钢水进行预脱氧,增碳剂中的碳与氧反应生成co和co2气泡,生产的产物以气泡的方式离开钢液,不会对钢液产生污染,且产生的气泡在钢水表面还可以减少钢液面与空气的接触,减少钢水二次氧化及增氮,气泡溢出时还可以加强钢液搅拌,促进后续加入合金的快速融化,可有效降低钢水氧化性并净化钢液。
15.3、转炉采用三挡操作,减少转炉下渣量,防止氧化性炉渣进入钢包导致的夹杂物增加。
16.4、转炉炉后铝按照0.050-0.070%控制,在铝制品大量反应时利用出钢时的良好的动力学条件,促进al2o3夹杂聚集上浮去除,并可减少lf炉铝线喂入量甚至不需要调整。
17.5、lf精炼炉铝含量一次喂入,提前形成al2o3夹杂物,使其有充足的时间上浮去除,避免后期补铝造成al2o3夹杂物难于去除,且渣中al2o3含量根据相似相容原理,有利吸收钢水中上浮的al2o3夹杂物。
18.6、硅铁在s≤0.005%以后一次加入,主要是利用硅铁中的微量钙元素对没有去除的al2o3夹杂物进行变性处理,使其变成低熔点的复合夹杂物,容易在rh循环过程中碰撞长大去除。
19.7、rh在高真空循环稳定后加入碳粉可与钢水充分混合,利用高真空下碳的强还原性对rh真空槽盖住的少量炉渣及钢水中的微量自由氧进行反应生产co气泡,co气泡可加速夹杂物在钢液循环过程中的碰撞长大去除,净化钢液;轴承钢中各元素含量注:标准要求al≤0.050%, c:0.95%-1.05%;轴承钢中各元素活度相互作业系数根据轴承钢中各元素含量及各元素活度相互作业系数可计算出c、al、o的活度系数为lgfc=0.082,lgf
al
=0.132,lgfo=-0.747;2[al]+3[o]=al2o3(s)
ꢀꢀꢀꢀ∆gθ
=-1225000+393.8t(j/mol)[c]+[o]=co(g)
ꢀꢀꢀꢀꢀꢀꢀ∆gθ
=-22200-38.34t(j/mol)进rh炉时进站温度一般在之间1560-1570℃,出站温度在1515-1525℃之间,真空度按100pa进出测算,进站时按1560℃测算;
∆
g(al2o3)=-26575.3j/mol;
∆
g(co)=-68516.8j/mol;出站时间按1515℃进行测算:
∆
g(al2o3)=-55996.6j/mol;
∆
g(co)=-67379.8j/mol;因此,在rh精炼过程的温度范围内,始终存在
∆
g(al2o3)<
∆
g(co);且实际生产中高真空度约30-60pa,钢水中铝约0.015%-0.025%,因此碳的氧化反应总是远远强于铝的氧化反应,因此利用真空内的c的还原性生产co气泡,并加速夹杂物的去除反应是成立的。
[0020]
8、rh破空利用ba元素对钢水进行处理,对钢水中剩余的al2o3进行变性处理,并利用静吹去除al2o3夹杂物。
[0021]
9、连铸开浇利用保护渣的弱酸性对钢水中的碱性氧化物进行吸附,且保护渣熔点较低,在钢液面具有较好的融化效果及吸附性,可有效减少夹杂物进入铸坯。
[0022]
10、塞棒吹氩可减少微小的al2o3夹杂物在塞棒聚集,使微小的al2o3均匀进入钢液,微小尺寸的al2o3夹杂物还可起到氧化物冶金的效果。
[0023]
采用上述技术方案所产生的有益效果在于:1、转炉采用大底吹高拉碳,可有效降
低钢水中的初始氧含量,并采用先加部分增碳剂对钢水进行预脱氧,采用三挡出钢操作,可有减少钢水中al2o3夹杂物的初始含量;2、将al2o3夹杂的产生时间尽量前移,延长al2o3夹杂物的去除时间;3、对剩余细小的夹杂物进行改质处理;4、本发明工艺简单、操作性强、效果显著,解决了al2o3夹杂的超标问题,可以实现连铸生产轴承钢稳定生产;且该方法生产操作简单,对周期的影响较小,并降低了生产成本,提高了企业的效益,在本行业中有极好的推广应用价值。
[0024]
本发明在小方坯连铸机生产高碳铬轴承钢时,al2o3夹杂的级别稳定控制在b粗≤0.5级,b细≤1.5级,合格比例达到99.9%以上,有效地提升产品质量,保证生产过程稳定受控。
具体实施方式
[0025]
一种高碳铬轴承钢中b类夹杂物的控制方法,其适用于高碳铬轴承钢gcr15的生产,其成分要求为:c 0.95~1.05wt%,si 0.15~0.35wt%,mn 0.25~0.45wt%,cr 1.40~1.65wt%,p≤0.020wt%,s≤0.015wt%,o≤0.0012wt%,ti≤0.0015wt%,ca≤0.00010wt%。
[0026]
设备工艺参数为:转炉为120t顶底复吹转炉,装入量在155
±
2t、钢水量145
±
2t;lf精炼炉为电极旋转式双工位;rh精炼炉为双工位;小方坯连铸机为8机8流的200mm
×
200mm方坯连铸机,一个中包,中包液面高度350mm时对应的钢水重量20t,中包液面高度700mm时对应的钢水重量39t(正常浇钢液面高度)。
[0027]
该高碳铬轴承钢中b类夹杂物的控制方法包括转炉、lf精炼、rh精炼和连铸工序,各工序步骤如下所述:(1)转炉工序:吹炼过程底吹流量采用中
→
小
→
大的底吹模式,底吹流量为0.06
→
0.04
→
0.08m3/(min*t)。出钢钢水成分质量百分含量为:c:0.08~0.20%、p≤0.015%、s≤0.015%,出钢钢水温度1620
±
20℃,出钢氧≤350ppm,出钢时间3.5~6.0min。出钢过程中向钢包内加入依次加入:增碳剂
→
铝粒
→
硅铁
→
锰铁
→
剩余增碳剂
→
低钛铬铁
→
预熔渣,首批增碳剂加入时机为出钢1/5时,加入量为100
±
10kg;铝粒加入时机为首批增碳剂加入10~20s后;预熔渣的加入量为6~9kg/t钢,预熔渣的组分及重量百分含量为:cao 40~55%、sio2≤10%、al2o
3 30~45%、mgo≤8%、al 3~8%。出钢过程利用三挡出钢,出钢后钢包样成分c:0.90~0.95%,si:0.05~0.10%,mn:0.22~0.30%,p≤0.015%,s≤0.015%,al:0.050~0.070%,cr:1.35~1.45%。
[0028]
(2)lf精炼工序:lf精炼前期加入30~50kg碳化硅,并加入石灰、萤石、预熔渣进行造渣,加热10~15min后取样、检测,根据检测结果对mn、cr、al含量进行调整,若al≥0.040%则无需调整,若al<0.040%则一次性喂入铝线,喂入量按照钢水中al的目标含量0.050%控制;精炼中后期钢水中s≤0.005%后,一次性加入硅铁进行合金化,钢水温度及c元素以外的成分合格后,静吹5~10min;精炼渣成分中al2o3重量含量控制在28~35%。
[0029]
(3)rh精炼工序:真空度≤100pa,真空保持时间≥15min;真空2min后一次性加入碳粉进行c含量调整,加入碳粉后继续保持真空≥12min,破空后喂入硅钡线200~300m,钢水软吹15~30min;rh精炼过程不向钢水加入铝制品;rh精炼工序仅进行碳含量调整,其余元素均在lf精炼工序调整完成。
[0030]
(4)连铸工序:连铸采用吹氩塞棒和浸入式水口,大包开浇后,中包液面高度达到
350mm时,向中包投入150~200kg轴承钢专用保护渣,保护渣为一次性加入,后续不再补加;然后再加入足量的覆盖剂,保证钢液面不裸漏,实现“黑面”浇注,开浇成功后打开塞棒吹氩,塞棒吹氩流量为0.5~0.8l/min。
[0031]
经过上述方法得到的高碳铬轴承钢中b类夹杂物b粗≤0.5级、b细≤1.5级。
[0032]
各实施例转炉工序的工艺参数见表1,转炉工序出钢后钢包样的组分见表2;各实施例lf精炼工序的工艺参数见表3;各实施例rh精炼、连铸工序的工艺参数及所得高碳铬轴承钢中b类夹杂物的检测数据见表4。
[0033]
表1:转炉工序的工艺参数表2:转炉工序出钢后钢包样的组分(wt%)表3:lf精炼工序的工艺参数
表4:rh精炼、连铸工序的工艺参数及轴承钢中b类夹杂物的检测数据。