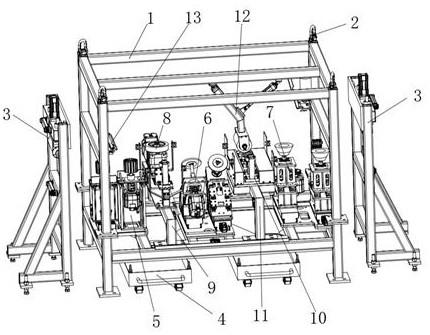
一种u型大梁钢全自动打磨设备
技术领域
1.本发明涉及汽车制造技术领域,具体涉及一种u型大梁钢全自动打磨设备。
背景技术:2.随着经济的稳定发展和人民生活水平的提高,汽车销量每年保持稳定增长,汽车保有量不断攀升。u型大梁钢作为载货汽车大梁的主要材料,几乎承载着货物的全部重量,其质量的好坏直接影响整车的使用寿命与行车安全。成为汽车大梁之前,大梁钢需经过很多加工工序,打磨就是其中一道工序。
3.目前,大梁钢打磨是由半自动打磨设备完成,半自动打磨设备无法适用于各种规格梁宽的自动调整,无法配套整条生产线的要求,打磨效率低。
技术实现要素:4.针对以上现有技术的不足,本发明的目的在于提供一种u型大梁钢全自动打磨设备,能够解决现有的半自动打磨设备无法适用于各种规格梁宽的自动调整,无法配套整条生产线要求的技术问题。
5.为了实现上述目的,本发明提供如下技术方案:一种u型大梁钢全自动打磨设备,包括机架,所述机架是由多根横杆和竖杆焊接而成的方形框架结构,所述机架顶部四角设有吊钩,所述机架左右两侧均设有压料检测装置,所述机架底部设有粉尘收集装置,所述机架内部从左到右依次设有翼面打磨机构、r角打磨机构和腹面打磨机构,所述翼面打磨机构、r角打磨机构和腹面打磨机构均通过螺栓固定连接在机架底框架上,所述翼面打磨机构和r角打磨机构之间设有驱动机构,所述驱动机构通过第一支架固定安装在机架底框架上,所述r角打磨机构和腹面打磨机构之间设有上料支撑机构,所述上料支撑机构通过第二支架固定安装在机架底框架上,还包括上压机构和风刀,所述上压机构位于上料支撑机构的上方且与机架顶部框架固定连接,所述风刀位于翼面打磨机构的上方且与机架左侧框架固定连接。
6.优选地,所述压料检测装置包括固定支架,所述固定支架上端设有一空心方梁,所述空心方梁的两端分别与固定支架的两个立柱焊接,所述空心方梁顶部设有压料气缸,所述压料气缸的杆部延伸至空心方梁内且其头部连接有连接轴,所述连接轴的下端延伸出空心方梁且焊接有第一连接板,所述第一连接板的底部通过安装座连接有辊筒,所述安装座一侧连接有编码器支座,所述编码器支座内安装有编码器。
7.优选地,所述翼面打磨机构包括翼面底板,所述翼面底板顶部设有两个结构相同的翼面打磨构件,其中一个翼面打磨构件固定连接在翼面底板顶面上,另一个翼面打磨构件底部连接有翼面直线模组,所述翼面直线模组固定连接在翼面底板顶面上。
8.优选地,所述翼面打磨构件包括翼面底座,所述翼面底座顶部两侧均设置有翼面导轨,所述翼面导轨上滑动连接有翼面导轨连接板,所述翼面底座内部设有翼面伺服电机,所述翼面伺服电机通过翼面伺服电机固定座连接在翼面导轨连接板上,所述翼面伺服电机
的输出轴上通过第一联轴器连接有花键轴,所述花键轴上连接有翼面打磨头。
9.优选地,还包括翼面气缸,所述翼面气缸安装在翼面气缸固定座上,所述翼面气缸固定座固定连接在翼面底座上,所述翼面气缸的杆部前端连接有翼面浮动接头,所述翼面浮动接头与翼面导轨连接板连接。
10.优选地,所述r角打磨机构包括r角支撑底板,所述r角支撑底板顶部设有两组结构相同的r角打磨构件,所述两组r角打磨构件并列设置且方向相反。
11.优选地,所述r角打磨构件包括r角直线模组,所述r角直线模组固定连接在r角支撑底板上,所述r角直线模组顶部连接有模组连接板,所述模组连接板顶部连接有r角底板连接组件,所述r角底板连接组件上设有主导轨和辅导轨,所述主导轨和辅导轨倾斜设置且二者相互平行,所述主导轨和辅导轨上分别通过第一r角滑块和第二r角滑块滑动连接有主导轨连接板和辅导轨连接板,还包括r角气缸,所述r角气缸位于主导轨和辅导轨之间,所述r角气缸的杆部前端连接有r角浮动接头,所述r角浮动接头上连接有r角轴承固定座,所述主导轨连接板和辅导轨连接板均与r角轴承固定座连接,所述r角轴承固定座上连接有法兰型带座轴承,所述法兰型带座轴承内设有r角转轴,所述r角转轴一端通过第二联轴器连接有r角伺服电机,另一端连接有r角打磨头。
12.优选地,所述腹面打磨机构包括腹面打磨安装底板,所述腹面打磨安装底板上设置有两台结构相同的腹面打磨构件,所述两台腹面打磨构件交错设置。
13.优选地,所述腹面打磨构件包括固定安装在腹面打磨安装底板上的腹面直线模组,所述腹面直线模组顶部连接有腹面连接板,所述腹面连接板顶部设有气缸连接座,所述气缸连接座顶部设有轴承固定板,所述轴承固定板上安装有带座轴承,所述气缸连接座内固定连接有腹面气缸,所述腹面气缸的杆部前端连接有腹面浮动接头,所述腹面浮动接头固定连接在轴承固定板底部,所述腹面气缸一侧设有腹面伺服电机,所述腹面伺服电机通过腹面电机固定座安装在轴承固定板上,所述腹面伺服电机的输出轴上连接有主动轮,所述主动轮通过同步带连接有从动轮,所述从动轮固定安装在带座轴承底部且其内部设置有腹面转轴,所述腹面转轴上连接有腹面打磨头。优选地,所述上压机构包括辊轮手臂和上压气缸,所述辊轮手臂的顶部和上压气缸的尾部均连接有用于将其固定在机架顶部框架上的固定装置,所述辊轮手臂的底部两端均连接有侧板,两个侧板之间设有上压辊,所述上压气缸的杆部前端连接有上压浮动接头,所述上压浮动接头上通过第一销轴连接有单耳朵,所述单耳朵连接在单耳座上,所述单耳座连接在辊轮手臂上。
14.与现有技术相比,本发明的有益效果为:本发明的一种u型大梁钢全自动打磨设备,机架两侧的压料检测装置用于实现压料同时通过编码器测量u型梁的长度,通过设置翼面打磨机构、r角打磨机构和腹面打磨机构能够分别对u型梁的翼面、r角和腹面进行自动打磨,且各打磨机构上通过设置直线模组利于调整各打磨构件之间的距离,以便适用于不同u型梁的梁宽,驱动机构中的固定侧通过气缸驱动电机安装板移动来实现绝缘脂辊轮对不同梁宽的u型梁进行夹紧和传送,基准侧通过调整第二螺柱来实现辅助辊轮与上料支撑机构中第四辊轮组件上的第二上料支撑辊轮在同一直线上,防止u型梁在运动的过程中走偏,上料支撑机构通过气缸驱动辊轮组件移动来实现调宽,以便能够实现对不同梁宽的u型梁进行支撑和传送,上压机构与上料支撑机构相配合实现u型梁的稳定传输,风刀能够将打磨后
滞留在u型梁顶面上的粉尘吹走,粉尘收集装置能够对打磨过程中产生的粉尘统一收集,且粉尘收集盒布置在整个机架的底部,收集面积覆盖了整个打磨过程,减少外泄。
附图说明
15.为了更清楚地说明本技术实施例或现有技术中的技术方案,下面将对实施例中所需要使用的附图作简单地介绍,显而易见地,下面描述中的附图仅仅是本发明中记载的一些实施例,对于本领域普通技术人员来讲,还可以根据这些附图获得其他的附图。
16.图1是本发明提出的一种u型大梁钢全自动打磨设备的整体结构示意图;图2是本发明提出的一种u型大梁钢全自动打磨设备的压料检测装置结构示意图;图3是本发明提出的一种u型大梁钢全自动打磨设备的粉尘收集装置结构示意图;图4是本发明提出的一种u型大梁钢全自动打磨设备的翼面打磨机构结构示意图;图5是本发明提出的一种u型大梁钢全自动打磨设备的r角打磨机构结构示意图;图6是本发明提出的一种u型大梁钢全自动打磨设备的腹面打磨机构结构示意图;图7是本发明提出的一种u型大梁钢全自动打磨设备中驱动机构固定侧的结构示意图;图8是本发明提出的一种u型大梁钢全自动打磨设备中驱动机构基准侧结构示意图;图9是本发明提出的一种u型大梁钢全自动打磨设备的上料支撑机构结构示意图(一);图10是本发明提出的一种u型大梁钢全自动打磨设备的上料支撑机构结构示意图(二);图11是本发明提出的一种u型大梁钢全自动打磨设备的上压机构结构示意图。
17.附图标记说明:1-机架;2-吊钩;3-压料检测装置、301-固定支架、302-空心方梁、303-压料气缸、304-连接轴、305-第一连接板、306-安装座、307-辊筒、308-编码器支座、309-编码器、310-底板、311-第一螺柱、312-螺母、313-预埋板、314-减震弹簧、315-导管、316-导向柱、317-垫板;4-粉尘收集装置、401-粉尘收集盒、402-粉尘收集小车、403-拉手;5-翼面打磨机构、501-翼面底板、502-翼面直线模组、503-翼面底座、504-翼面导轨、505-翼面导轨连接板、506-翼面伺服电机、507-翼面伺服电机固定座、508-第一联轴器、509-花键轴、510-翼面打磨头、511-翼面气缸、512-翼面气缸固定座、513-翼面浮动接头、514-翼面滑块、515-轴承、516-打磨垫片;6-r角打磨机构、601-r角支撑底板、602-r角直线模组、603-模组连接板、604-r角底板连接组件、605-主导轨、606-辅导轨、607-第一r角滑块、608-主导轨连接板、609-第二r角滑块、610-辅导轨连接板、611-r角气缸、612-r角浮动接头、613-r角轴承固定座、614-法兰型带座轴承、615-r角转轴、616-第二联轴器、617-r角伺服电机、618-r角打磨头、619-气缸连接法兰、620-调速阀;7-腹面打磨机构、701-腹面打磨安装底板、702-腹面直线模组、703-腹面连接板、
704-气缸连接座、705-轴承固定板、706-带座轴承、707-腹面气缸、708-腹面浮动接头、709-腹面伺服电机、710-腹面电机固定座、711-主动轮、712-同步带、713-从动轮、714-腹面转轴、715-腹面打磨头、716-法兰轴、717-无油衬套、718-带轮挡圈;8-驱动机构、801-气缸外罩、802-气缸、803-连接套、804-第二连接板、805-滑块、806-导轨、807-过渡板、808-电机安装板、809-减速电机、810-内套、811-绝缘脂辊轮、812-压盖、813-弹簧垫圈、814-光电支架、815-第一管夹、816-第一对射开关、817-辅助辊安装座、818-光电架子、819-第二管夹、820-第二对射开关、821-滑槽、822-辊轮座、823-调节块、824-第二螺柱、825-横盖板、826-辊轮轴、827-辅助辊轮;9-第一支架;10-上料支撑机构、1001-上料支撑底板、1002-上料支撑导轨、1003-第一上料支撑滑块、1004-第二上料支撑滑块、1005-第一气缸支架、1006-第二气缸支架、1007-第一气缸、1008-第一连接套、1009-第一叉板、1010-第二气缸、1011-第二连接套、1012-第二叉板、1013-第一上料支撑辊轮座、1014-上料支撑竖盖板、1015-第一上料支撑辊轮轴、1016-第一上料支撑辊轮、1017-第二上料支撑辊轮座、1018-上料支撑横盖板、1019-第二上料支撑辊轮轴、1020-第二上料支撑辊轮、1021-弹性柱、1022-接头式压注油杯、1023-立板、1024-第三对射开关、1025-加强筋、1026-第一罩基体、1027-第二罩基体;11-第二支架;12-上压机构、1201-辊轮手臂、1202-上压气缸、1203-侧板、1204-上压辊、1205-上压螺母、1206-上压浮动接头、1207-第一销轴、1208-单耳朵、1209-单耳座、1210-中耳座、1211-第二销轴、1212-双耳座、1213-平垫圈、1214-铜套;13-风刀。
具体实施方式
18.下面结合说明书附图,以举例的方式对本发明创造的内容作出详细描述,显然,所描述的实施例仅仅是本发明一部分实施例,而不是全部的实施例。
19.如图1所示,一种u型大梁钢全自动打磨设备,包括机架1,所述机架1是由多根横杆和竖杆焊接而成的方形框架结构,所述机架1顶部四角设有吊钩2,设置吊钩2便于移动机架1;所述机架1左右两侧均设有压料检测装置3,所述机架1底部设有粉尘收集装置4,所述机架1内部从左到右依次设有翼面打磨机构5、r角打磨机构6和腹面打磨机构7,所述翼面打磨机构5、r角打磨机构6和腹面打磨机构7均通过螺栓固定连接在机架1底框架上,所述翼面打磨机构5和r角打磨机构6之间设有驱动机构8,所述驱动机构8通过第一支架9固定安装在机架1底框架上,所述r角打磨机构6和腹面打磨机构7之间设有上料支撑机构10,所述上料支撑机构10通过第二支架11固定安装在机架1底框架上,还包括上压机构12和风刀13,所述上压机构12位于上料支撑机构10的上方且与机架1顶部框架固定连接,所述风刀13位于翼面打磨机构5的上方且与机架1左侧框架固定连接。
20.本发明的工作流程为:u型梁经左侧的压料检测装置3进入机架1内,依次经翼面打磨机构5、驱动机构8、r角打磨机构6、上料支撑机构10、腹面打磨机构7后再经右侧的压料检测装置3进入下一工序中,在打磨过程中,上压机构12与上料支撑机构10配合完成u型梁的稳定传输,风刀13能够将u型梁顶面上的粉尘吹落,粉尘统一落到粉尘收集装置4内收集并
处理。
21.如图2所示,所述压料检测装置3包括固定支架301,所述固定支架301上端设有一空心方梁302,所述空心方梁302的两端分别与固定支架301的两个立柱焊接,所述空心方梁302顶部通过螺钉连接有压料气缸303,所述压料气缸303的杆部延伸至空心方梁302内且其头部螺纹连接有连接轴304,所述连接轴304的下端延伸出空心方梁302且焊接有第一连接板305,所述第一连接板305的底部通过安装座306连接有辊筒307,所述安装座306一侧通过螺钉连接有编码器支座308,所述编码器支座308内安装有编码器309;在本技术方案中,通过压料气缸303带动第一连接板305向下运动,进而带动辊筒307向下运动实现对u型梁进行压紧,保证u型梁稳定前行,通过设置编码器309利于对u型梁的长度进行测量。
22.进一步地,所述固定支架301的支腿底部均焊接有底板310,所述底板310中部开设有通孔,所述通孔内设有第一螺柱311,所述第一螺柱311上螺纹连接有两个螺母312,所述两个螺母312分别设置在底板310的顶部和底部,同侧的两个第一螺柱311底部焊接在同一块预埋板上313。
23.在本技术方案中,通过拧动底板310下方的螺母312来调整固定支架301的高度,而底板310上方的螺母312是锁紧螺母,用于将底板310与第一螺柱311锁紧,避免发生晃动,影响压料效果。
24.再进一步地,所述连接轴304外侧套设有减震弹簧314,所述减震弹簧314上端与压料气缸303杆部前端相抵触,下端与第一连接板305顶面相抵触;更进一步地,所述空心方梁302上焊接有导管315,所述导管315对称设置在压料气缸303的两侧,所述导管315两端均延伸出空心方梁302,所述导管315内安装有导向柱316,所述导向柱316的底部焊接有垫板317,所述垫板317通过螺钉连接在第一连接板305上。通过设置导管315、导向柱316和垫板317,利于对辊筒307的运动轨迹进行导向,避免发生偏移。
25.如图3所示,所述粉尘收集装置4包括粉尘收集盒401和粉尘收集小车402,所述粉尘收集盒401呈漏斗形,其上端开口处通过螺栓固定连接在机架1底部,所述粉尘收集小车402位于粉尘收集盒401的下方,所述粉尘收集小车402上设有拉手403。
26.在本技术方案中,漏斗形状的粉尘收集盒401便于粉尘自动下落至粉尘收集小车402内,拉动拉手403将粉尘收集小车402拉出,方便处理粉尘收集小车402内的粉尘。
27.进一步地,所述粉尘收集盒401的数量为两个,所述两个粉尘收集盒401并列设置在机架1底部,所述粉尘收集小车402的数量与粉尘收集盒401的数量相匹配。
28.如图4所示,所述翼面打磨机构5包括翼面底板501,所述翼面底板501顶部设有两个结构相同的翼面打磨构件,其中一个翼面打磨构件通过螺钉固定连接在翼面底板501顶面上,另一个翼面打磨构件底部通过螺钉连接有翼面直线模组502,所述翼面直线模组502通过螺钉固定连接在翼面底板501顶面上;进一步地,所述翼面打磨构件包括翼面底座503,所述翼面底座503顶部两侧均通过螺钉连接有翼面导轨504,所述翼面导轨504上滑动连接有翼面导轨连接板505,所述翼面底座503内部设有翼面伺服电机506,所述翼面伺服电机506通过螺钉固定连接在翼面伺服电机固定座507上,所述翼面伺服电机固定座507通过螺钉固定连接在翼面导轨连接板505
上,所述翼面伺服电机506的输出轴上通过第一联轴器508连接有花键轴509,所述花键轴509上连接有翼面打磨头510,所述翼面打磨头510采用镀铜钢丝轮或千叶轮;在本技术方案中,两个翼面打磨构件分别对u型梁的两个翼面进行打磨,具体工作时,通过翼面直线模组502调整两个翼面打磨构件之间的距离,以便适用于不同u型梁的梁宽,调整完毕后,翼面伺服电机506驱动翼面打磨头510旋转进行打磨。
29.还包括翼面气缸511,所述翼面气缸511固定连接在翼面气缸固定座512上,所述翼面气缸固定座512通过螺栓固定连接在翼面底座503上,所述翼面气缸511的杆部前端螺纹连接有翼面浮动接头513,所述翼面浮动接头513通过螺钉与翼面导轨连接板505连接。
30.在本技术方案中,翼面气缸511驱动翼面导轨连接板505沿翼面导轨504滑动,便于对u型梁翼面的局部进行打磨,打磨完毕后翼面气缸511收缩。
31.再进一步地,所述翼面导轨连接板505底部两侧均通过螺钉连接有翼面滑块514,两个翼面滑块514分别滑动连接在两个翼面导轨504上,所述花键轴509与翼面导轨连接板505之间设有轴承515,所述轴承515通过螺栓固定连接在翼面导轨连接板505上;更进一步地,所述翼面打磨头510内槽顶端通过螺钉连接有打磨垫片516,所述打磨垫片516通过螺钉与花键轴509连接,通过设置打磨垫片516,利于避免打磨头510上下窜动。
32.如图5所示,所述r角打磨机构6包括r角支撑底板601,所述r角支撑底板601顶部设有两组结构相同的r角打磨构件,所述两组r角打磨构件并列设置且方向相反;进一步地,所述r角打磨构件包括r角直线模组602,所述r角直线模组602通过螺钉固定连接在r角支撑底板601上,所述r角直线模组602顶部通过螺钉连接有模组连接板603,所述模组连接板603顶部通过螺钉连接有r角底板连接组件604,所述r角底板连接组件604上通过螺钉连接有主导轨605和辅导轨606,所述主导轨605和辅导轨606倾斜设置且二者相互平行,所述主导轨605上滑动连接有第一r角滑块607,所述第一r角滑块607顶部通过螺钉连接有主导轨连接板608,所述辅导轨606上滑动连接有第二r角滑块609,所述第二r角滑块609顶部通过螺钉连接有辅导轨连接板610,还包括r角气缸611,所述r角气缸611位于主导轨605和辅导轨606之间,所述r角气缸611的杆部前端螺纹连接有r角浮动接头612,所述r角浮动接头612上连接有r角轴承固定座613,所述主导轨连接板608和辅导轨连接板610均与r角轴承固定座613连接,所述r角轴承固定座613上通过螺栓连接有法兰型带座轴承614,所述法兰型带座轴承614内设有r角转轴615,所述r角转轴615一端通过第二联轴器616连接有r角伺服电机617,另一端通过螺钉连接有r角打磨头618,所述r角打磨头618采用镀铜钢丝轮或千叶轮;在本技术方案中,两个r角打磨构件分别对u型梁的两个r角进行打磨,具体工作时,通过r角直线模组602调整两个r角打磨构件之间的距离,以便适用于不同u型梁的梁宽,调整完毕后,r角伺服电机617驱动r角打磨头618旋转打磨。
33.r角气缸611通过r角轴承固定座613驱动主导轨连接板608和辅导轨连接板610同时运动,便于对u型梁r角的局部进行打磨,打磨完毕后r角气缸611收缩。
34.再进一步地,所述r角气缸611通过螺钉连接在气缸连接法兰619上,所述气缸连接法兰619通过螺钉固定连接在r角底板连接组件604上;更进一步地,所述r角气缸611的调速接口上连接有调速阀620,通过设置调速阀
620便于调节r角气缸611的进气速度。
35.如图6所示,所述腹面打磨机构7包括腹面打磨安装底板701,所述腹面打磨安装底板701上设置有两台结构相同的腹面打磨构件,所述两台腹面打磨构件交错设置;所述腹面打磨构件包括固定安装在腹面打磨安装底板701上的腹面直线模组702,所述腹面直线模组702顶部通过螺钉连接有腹面连接板703,所述腹面连接板703顶部设有气缸连接座704,所述气缸连接座704通过螺栓与腹面连接板703连接,所述气缸连接座704顶部设有轴承固定板705,所述轴承固定板705上安装有带座轴承706,所述气缸连接座704内通过螺钉固定连接有腹面气缸707,所述腹面气缸707的杆部前端连接有腹面浮动接头708,所述腹面浮动接头708通过螺钉固定在轴承固定板705底部,所述腹面气缸707一侧设有腹面伺服电机709,所述腹面伺服电机709通过腹面电机固定座710安装在轴承固定板705上,所述腹面伺服电机709的输出轴上连接有主动轮711,所述主动轮711通过同步带712连接有从动轮713,所述从动轮713固定安装在带座轴承706底部且其内部设置有腹面转轴714,所述腹面转轴714上连接有腹面打磨头715,所述腹面打磨头715通过螺母固定连接在腹面转轴714上,所述腹面打磨头715采用镀铜钢丝轮或千叶轮。
36.在本技术方案中,两个腹面打磨构件同时对u型梁的腹面进行打磨,具体工作时,通过腹面直线模组702调整两个腹面打磨构件之间的距离,以便适用于不同u型梁的梁宽,调整完毕后,腹面伺服电机709驱动腹面打磨头715旋转打磨。
37.腹面气缸707驱动轴承固定板705运动,便于对u型梁腹面的局部进行打磨,打磨完毕后腹面气缸707收缩。
38.进一步地,还包括法兰轴716,所述法兰轴716起支撑和导向的作用,所述法兰轴716通过无油衬套717将轴承固定板705和气缸连接座704连接;再进一步地,所述从动轮713底部通过螺钉连接有带轮挡圈718,所述带轮挡圈718用于固定从动轮713,防止从动轮713在打磨过程中脱落;更进一步地,所述同步带712采用弧齿同步带或梯形齿同步带。
39.如图7-8所示,所述驱动机构8包括固定侧和基准侧,所述固定侧和基准侧对应安装在第一支架9上。具体地,如图7所示,所述固定侧包括通过螺钉连接在第一支架9上的气缸外罩801,所述气缸外罩801内通过气缸角座连接有气缸802,所述气缸802的杆部前端螺纹连接有连接套803,所述连接套803上连接有第二连接板804,所述第二连接板804与连接套803过盈配合,所述气缸外罩801顶部通过螺钉连接有两个并列设置的滑块805,所述两个滑块805内滑动连接有同一个导轨806,所述导轨806通过螺钉连接在过渡板807上,所述过渡板807顶部通过螺钉连接有电机安装板808,所述电机安装板808顶部通过螺钉连接有减速电机809,所述减速电机809的输出轴上连接有内套810,所述内套810与输出轴过盈配合,所述内套810外侧浇筑有绝缘脂辊轮811,所述内套810顶部通过螺钉连接有压盖812,所述压盖812与螺钉之间设有弹簧垫圈813;进一步地,所述第二连接板804上端通过螺钉分别与同侧的导轨806和电机安装板808连接;在本技术方案中,固定侧用于调整宽度,以便适用于不同梁宽的u型梁,具体工作时,气缸802通过第二连接板804驱动导轨806和电机安装板808移动,电机安装板808带动减
速电机809移动,从而使得绝缘脂辊轮811位置发生变动,实现宽度调整,调整完毕后,减速电机809驱动绝缘脂辊轮811旋转,配合基准侧的辅助辊轮827驱动u型梁前行。
40.再进一步地,所述气缸外罩801的两侧均通过螺钉连接有光电支架814,所述光电支架814上通过第一管夹815连接有第一对射开关816,所述第一管夹815通过螺钉连接在光电支架814上;如图8所示,所述基准侧包括通过螺钉连接在第一支架9上的辅助辊安装座817,所述辅助辊安装座817上通过螺钉连接有光电架子818,所述光电架子818对称安装在辅助辊安装座817的两侧,所述光电架子818上通过第二管夹819连接有第二对射开关820,所述第二管夹819通过螺钉连接在光电架子818上;进一步地,所述辅助辊安装座817顶部开设有一组滑槽821,所述滑槽821内通过螺钉连接有辊轮座822,所述辊轮座822的下端一侧设置有调节块823,所述调节块823通过螺钉连接在辅助辊安装座817的顶部,所述调节块823上螺纹连接有第二螺柱824,所述第二螺柱824与辊轮座822下端固定连接,所述辊轮座822顶部通过螺钉连接有横盖板825,所述横盖板825上连接有辊轮轴826,所述辊轮轴826一端与横盖板825上的通孔过盈配合,另一端与辊轮座822螺纹连接,所述辊轮轴826的外侧连接有辅助辊轮827。
41.在本技术方案中,基准侧用于调整辅助辊轮827与上料支撑机构中10第四辊轮组件上的第二上料支撑辊轮1020在同一直线上,防止u型梁在运动的过程中走偏,具体应用时,拧动第二螺柱824,第二螺柱824带动辊轮座822在滑槽821内来回移动实现位置调整。
42.如图9-10所示,所述上料支撑机构10包括上料支撑底板1001,所述上料支撑底板1001顶部一侧通过螺钉连接有上料支撑导轨1002,所述上料支撑导轨1002上滑动连接有第一上料支撑滑块1003和第二上料支撑滑块1004,所述第一上料支撑滑块1003顶部通过螺钉连接有第一辊轮组件,所述第二上料支撑滑块1004顶部通过螺钉连接有第二辊轮组件,所述上料支撑底板1001顶部另一侧通过螺钉连接有第三辊轮组件和第四辊轮组件,所述第三辊轮组件、第四辊轮组件和上料支撑导轨1002在同一直线上且第三辊轮组件位于第四辊轮组件和上料支撑导轨1002之间;所述上料支撑导轨1002两侧分别设有第一气缸支架1005和第二气缸支架1006,所述第一气缸支架1005和第二气缸支架1006均通过螺钉连接在上料支撑底板1001上,所述第一气缸支架1005上通过螺钉连接有第一气缸1007,所述第一气缸1007的杆部前端螺纹连接有第一连接套1008,所述第一连接套1008上连接有第一叉板1009,所述第一叉板1009与第一连接套1008过盈配合,所述第一叉板1009通过螺钉与第一辊轮组件连接,所述第二气缸支架1006上通过螺钉连接有第二气缸1010,所述第二气缸1010的杆部前端螺纹连接有第二连接套1011,所述第二连接套1011上连接有第二叉板1012,所述第二叉板1012与第二连接套1011过盈配合,所述第二叉板1012通过螺钉与第二辊轮组件连接;在本技术方案中,上料支撑机构10通过气缸驱动辊轮组件移动来实现调宽,以便能够实现对不同梁宽的u型梁进行支撑和传送。第三辊轮组件和第四辊轮组件作为固定端,调宽工作是通过第一辊轮组件实现的,第二辊轮组件用于配合不同梁宽起到支撑的作用。具体应用时,第一气缸1007驱动第一辊轮组件移动实现调宽,调整完毕后,第二气缸1010驱动第二辊轮组件移动,第二辊轮组件用于支撑u型梁。
43.进一步地,所述第二辊轮组件和第三辊轮组件结构相同,包括第一上料支撑辊轮
座1013,所述第一上料支撑辊轮座1013上通过螺钉连接有上料支撑竖盖板1014,所述上料支撑竖盖板1014上连接有第一上料支撑辊轮轴1015,所述第一上料支撑辊轮轴1015一端与上料支撑竖盖板1014上的通孔过盈配合,另一端与第一上料支撑辊轮座1013螺纹连接,所述第一上料支撑辊轮轴1015的外侧连接有第一上料支撑辊轮1016;所述第一辊轮组件和第四辊轮组件结构相同,包括第二上料支撑辊轮座1017,所述第二上料支撑辊轮座1017上通过螺钉连接有上料支撑横盖板1018,所述上料支撑横盖板1018上连接有第二上料支撑辊轮轴1019,所述第二上料支撑辊轮轴1019一端与上料支撑横盖板1018上的通孔过盈配合,另一端与第二上料支撑辊轮座1017螺纹连接,所述第二上料支撑辊轮轴1019的外侧连接有第二上料支撑辊轮1020;再进一步地,所述第一辊轮组件与第二辊轮组件相对的一侧通过螺钉连接有弹性柱1021,通过设置弹性柱1021用于防止第一辊轮组件与第二辊轮组件发生碰撞,优选地,所述弹性柱1021的材质为绝缘脂;所述第一上料支撑滑块1003和第二上料支撑滑块1004的外侧均安装有接头式压注油杯1022,所述第一上料支撑滑块1003和第二上料支撑滑块1004的内部开设有用于流通润滑油的流道,通过设置接头式压注油杯1022用于注入润滑油,对上料支撑导轨1002进行润滑;所述上料支撑底板1001的前后两侧均通过螺钉连接有立板1023,所述立板1023为u型结构,所述立板1023外壁上通过螺钉连接有第三对射开关1024;所述立板1023与上料支撑底板1001之间还设有加强筋1025,所述加强筋1025用于加强立板1023与上料支撑底板1001之间的稳固性能;更进一步地,还包括并列设置的第一罩基体1026和第二罩基体1027,所述第一罩基体1026和第二罩基体1027的两侧均通过螺钉连接在上料支撑底板1001的左右两侧,所述第一罩基体1026用于罩住第一气缸1007,所述第二罩基体1027用于罩住第二气缸1010,所述第一罩基体1026和第二罩基体1027的高度与u型立板1023的中间边平齐。
44.在本技术方案中,立板1023用于固定用于检测来料的第三对射开关1024,同时两个立板1023分别与第一罩基体1026和第二罩基体1027配合形成完整的罩体罩住第一气缸1007和第二气缸1010,防止灰尘进入。
45.如图11所示,所述上压机构12包括辊轮手臂1201和上压气缸1202,所述辊轮手臂1201的顶部和上压气缸1202的尾部均通过螺钉连接有固定装置,所述辊轮手臂1201的底部两端均通过螺钉连接有侧板1203,两个侧板1203之间设有上压辊1204,所述上压辊1204的中心轴两端通过上压螺母1205固定连接在侧板1203上,所述上压气缸1202的杆部前端螺纹连接有上压浮动接头1206,所述上压浮动接头1206上通过第一销轴1207连接有单耳朵1208,所述单耳朵1208通过螺钉连接在单耳座1209上,所述单耳座1209通过螺钉连接在辊轮手臂1201上;在本技术方案中,通过上压气缸1202驱动辊轮手臂1201伸出实现对u型梁的压紧工作,不工作时,上压气缸1202带动辊轮手臂1201收回。
46.进一步地,所述固定装置包括中耳座1210,所述中耳座1210通过螺钉分别与辊轮手臂1201的顶部和上压气缸1202的尾部连接,所述中耳座1210上通过第二销轴1211连接有双耳座1212,所述双耳座1212通过螺钉连接在机架1顶部框架上;通过设置固定装置利于将
辊轮手臂1201和上压气缸1202固定连接在机架1的顶部框架上,且固定装置中的第二销轴1211利于实现辊轮手臂1201和上压气缸1202旋转。
47.再进一步地,所述上压螺母1205与侧板1203之间还设有平垫圈1213,平垫圈1213能够增加上压螺母1205的紧固性能;更进一步地,所述第一销轴1207上套设有铜套1214,通过设置铜套1214利于减轻第一销轴1207转动时产生的磨损。
48.以上所述,仅为本发明较佳的具体实施方式,但本发明的保护范围并不局限于此,任何熟悉本技术领域的技术人员在本发明揭露的技术范围内,根据本发明的技术方案及其申请构思加以等同替换或改变,都应涵盖在本发明的保护范围之内。