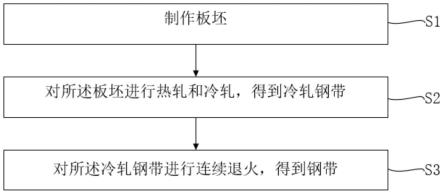
1.本技术涉及汽车外板用钢材技术领域,尤其涉及一种钢带其制备方法、汽车外板。
背景技术:2.汽车轻量化推进和安全性提升是汽车发展的方向之一,研究表明约75%的油耗与整车质量有关,降低汽车质量就可有效降低油耗以及排放,具体为:汽车质量每下降10%,油耗下降8%,排放下降4%。而这一研究带动了汽车用高强钢的发展,进入21世纪以来,高强汽车用钢研究和应用迅猛,980mpa、1180mpa甚至1500mpa级的双相钢,trip钢,m钢,热成型钢快速应用于汽车结构件和安全件,但对于汽车覆盖件用钢主要集中在if软钢和bh钢,强度级别主要在300mpa及其以下。
3.目前为了提高钢板的强度,一般采用固溶强化、沉淀强化、细晶强化和相变强度这四种强化机制,但是这四种常规的强化机制在外板强度、成形性和表面质量综合提升方面存在较大的矛盾和冲突,为此亟需寻求一种全新的外板高强化的途径。
技术实现要素:4.本技术实施例提供了一种钢带其制备方法、汽车外板,以解决现有强化机制难以综合改善汽车用钢的强度、成形性和表面质量的技术问题。
5.第一方面,本技术实施例提供了一种钢带,所述钢带的化学成分以质量分数计为:c:0.003%~0.01%,nb:0.02%~1.0%,si≤0.03%,a1t:0.02%~0.06%,mn≤1.0%,p≤
6.0.05%,s≤0.015%,n≤0.004%,b≤0.0005%,其余为fe及不可避免的杂质。
7.进一步地,所述钢带的微观组织包括细小析出物和稀疏粗大析出物;所述细小析出物的粒径为10nm~30nm,所述稀疏粗大析出物的粒径为100nm~500nm。
8.第二方面,本技术实施例提供了一种第一方面所述的钢带的制备方法、汽车外板,所述制备方法包括:
9.制作板坯;
10.对所述板坯进行热轧和冷轧,得到冷轧钢带;
11.对所述冷轧钢带进行连续退火,得到钢带;
12.其中,所述热轧包括轧制前加热、轧制和轧制后冷却;所述连续退火包括退火冷却、均热后冷却、过时效处理和平整处理。
13.进一步地,所述轧制前加热的出炉温度为1150℃~1230℃,在炉时间140~220min。
14.进一步地,所述轧制的终轧温度为870℃~920℃,卷取温度为610℃~710℃。
15.进一步地,所述轧制后冷却包括第一冷却和第二冷却;其中,所述第一冷却的冷却速度≥
16.15℃/s,冷却时间为1s~10s;所述第二冷却的冷却速度为5℃/s~20℃/s,冷却时
间为3s~20s。
17.进一步地,所述退火冷却的温度为760℃~830℃,速度为150℃/min~250℃/min。
18.进一步地,所述均热后冷却包括第三冷却和第四冷却;其中,所述第三冷却的冷却速度为5℃/s~15℃/s,终点温度为640℃~660℃;所述第四冷却的冷却速度为30℃/s~50℃/s,终点温度为440℃~460℃。
19.进一步地,所述过时效处理包括在过时效温度为370℃~430℃的条件下处理3min~5min,其终冷温度为170℃~180℃。
20.第三方面,本技术实施例提供了一种汽车外板,所述汽车外板由第一方面所述的钢带制成。
21.本技术实施例提供的上述技术方案与现有技术相比具有如下优点:
22.本技术实施例提供了一种钢带,通过控制钢带的原料成分中的si含量在0.03%以下,并采用微量的nb、c和n,形成微小的nb(c,n)物来得到弥散分布的析出物并细化铁素晶粒,使得到的钢带的晶粒尺寸细小,从而能够改善冷轧再结晶组织并促进{111}织构的发展成型,有利于深冲性提升,同时综合改善抗凹性和成形性。因此,本技术实施例提供的汽车面板用钢带可综合提高外板的强度、成形性、抗凹性,实现轻量化。
附图说明
23.此处的附图被并入说明书中并构成本说明书的一部分,示出了符合本发明的实施例,并与说明书一起用于解释本发明的原理。
24.为了更清楚地说明本发明实施例或现有技术中的技术方案,下面将对实施例或现有技术描述中所需要使用的附图作简单地介绍,显而易见地,对于本领域普通技术人员而言,在不付出创造性劳动性的前提下,还可以根据这些附图获得其他的附图。
25.图1为本技术实施例提供的一种钢带的制备方法的流程示意图。
具体实施方式
26.下面将结合具体实施方式和实施例,具体阐述本发明,本发明的优点和各种效果将由此更加清楚地呈现。本领域技术人员应理解,这些具体实施方式和实施例是用于说明本发明,而非限制本发明。
27.在整个说明书中,除非另有特别说明,本文使用的术语应理解为如本领域中通常所使用的含义。因此,除非另有定义,本文使用的所有技术和科学术语具有与本发明所属领域技术人员的一般理解相同的含义。若存在矛盾,本说明书优先。
28.除非另有特别说明,本发明中用到的各种原材料、试剂、仪器和设备等,均可通过市场购买得到或者可通过现有方法制备得到。
29.汽车轻量化和绿色化是汽车行业未来发展方向,目前常用汽车外板用钢主要集中在if软钢和bh钢两大类,强度级别主要在300mpa及其以下。这两类钢在汽车行业轻量化绿色化行业发展存在短板与不足:减薄轻量化后抗凹性不足;复杂设计外板件成形性不足;材料集采后存储时效性问题。
30.目前为了提高钢板的强度,一般采用固溶强化、沉淀强化、细晶强化和相变强度这四种强化机制,但是这四种常规的强化机制在外板强度、成形性和表面质量综合提升方面
存在较大的矛盾和冲突,为此亟需寻求一种全新的外板高强化的途径。
31.本发明实施例提供的技术方案为解决上述技术问题,总体思路如下:
32.第一方面,本技术实施例提供了一种钢带,所述钢带的化学成分以质量分数计为:c:0.003%~0.01%,nb:0.02%~1.0%,si≤0.03%,a1t:0.02%~0.06%,mn≤1.0%,p≤
33.0.05%,s≤0.015%,n≤0.004%,b≤0.0005%,其余为fe及不可避免的杂质。
34.本技术实施例提供了一种钢带,通过控制钢带卷的原料成分中的si含量在0.03%以下,并采用微量的nb、c和n,形成微小的nb(c,n)物来得到弥散分布的析出物并细化铁素晶粒,使得到的钢带卷的晶粒尺寸细小,从而能够改善冷轧再结晶组织并促进{111}织构的发展成型,有利于深冲性提升,同时综合改善抗凹性和成形性。因此,本技术实施例提供的汽车面板用钢带可综合提高外板的强度、成形性、抗凹性,实现轻量化。
35.作为本发明实施例的一种实施方式,所述钢带的微观组织包括细小析出物和稀疏粗大析出物;所述细小析出物的粒径为10nm~30nm,所述稀疏粗大析出物的粒径为100nm~500nm。
36.通过控制钢带的原料成分可得到晶粒尺寸在10μm的超细晶组织(利用nbc在奥氏体中对于晶粒长大的拖曳,轧制时动态再结晶区对于再结晶推迟,以及nbc在再结晶退火时对于组织长大抑制作用得到了10μm左右细小均匀的组织),进而在晶内形成微小的30nm以下的nbc析出物和晶界尺寸在100nm以上的析出物,这种晶内弥散析出、晶界粗大析出可综合提升钢带的强度和深冲性。
37.第二方面,本技术实施例提供了一种第一方面所述的钢带的制备方法,所述制备方法包括:
38.制作板坯;
39.对所述板坯进行热轧和冷轧,得到冷轧钢带;
40.对所述冷轧钢带进行连续退火,得到钢带;
41.其中,所述热轧包括轧制前加热、轧制和轧制后冷却;所述连续退火包括退火冷却、均热后冷却、过时效处理和平整处理。
42.本技术中,所述轧制前加热的出炉温度为1150℃~1230℃,在炉时间140~220min。
43.本技术中,所述轧制的终轧温度为870℃~920℃,卷取温度为610℃~710℃。
44.利用低温出钢、轧制时合理的压下率、温度匹配和形变诱导相变机制,细化组织。
45.本技术中,所述轧制后冷却包括第一冷却和第二冷却;其中,所述第一冷却的冷却速度≥
46.15℃/s,冷却时间为1s~10s;所述第二冷却的冷却速度为5℃/s~20℃/s,冷却时间为3s~20s。
47.利用轧后快冷和合理的卷取温度匹配得到细小的nbc析出。
48.本技术中,所述退火冷却的温度为760℃~830℃,速度为150℃/min~250℃/min。
49.利用退火温度和退火速度的匹配,实现晶内和晶界差异化的析出物形态控制,使晶体内部保持了70%的析出物控制在30nm以下,晶界80%析出物发生熟化和长大,析出物尺寸在80nm以上,实现了通过晶内粒子析出强化提高强度和抗凹性,通过晶界的沉淀自由
析出区提高成形性和低温韧性。
50.本技术中,所述均热后冷却包括第三冷却和第四冷却;其中,所述第三冷却的冷却速度为5℃/s~15℃/s,终点温度为640℃~660℃;所述第四冷却的冷却速度为30℃/s~50℃/s,终点温度为440℃~460℃。
51.本技术中,所述过时效处理包括在过时效温度为370℃~430℃的条件下处理3min~5min,其终冷温度为170℃~180℃。
52.本技术中,所述平整处理的延伸率为0.6%~1.4%。
53.第三方面,本技术实施例提供了一种汽车外板,所述汽车外板由第一方面所述的钢带制成。
54.经测试,本技术中钢带的屈服强度为220mpa~300mpa,抗拉强度为370mpa~470mpa,伸长率为30%~42%,平面应变塑性比r值为1.8~2.5。基于低屈服、高抗拉、高r值、及在4%~6%小变形量下具有高的加工硬化指数的力学特征,实现了该钢带的高抗凹性和高成形性的最佳匹配。
55.下面结合具体实施例,进一步阐述本发明。应理解,这些实施例仅用于说明本发明而不用于限制本发明的范围。下列实施例中未注明具体条件的实验方法,通常按照国家标准测定。若没有相应的国家标准,则按照通用的国际标准、常规条件、或按照制造厂商所建议的条件进行。
56.实施例1:
57.一种钢带及其制备方法,其特征包括如下步骤:
58.(1)原料选取:c:0.006%,nb:0.06%,si:0.01%,a1t:0.04%,mn:0.5%,p:0.02%,s:0.005%,n:0.001%,b:0.0001%,其余为fe及不可避免的杂质;
59.(2)板坯制作:通过连铸获取含上述化学成分的板坯;
60.(3)轧制前加热:将板坯置于炉中加热180min,并使其出炉温度为1190℃;
61.(4)轧制:对加热后的板坯进行轧制,并使其终轧温度为890℃,卷取温度为660℃;
62.(5)轧制后冷却:以20℃/s的冷却速度将轧制后的板坯冷却5s,再以15℃/s的冷却速度冷却15s;
63.(6)退火冷却:将轧制后冷却的板坯以200℃/min的速度加热至790℃;
64.(7)均热后冷却:将退火冷却后的板坯以10℃/s的速度冷却至650℃,再以40℃/s的速度冷却至450℃;
65.(8)过时效处理:将均热后冷却的板坯于400℃保持4min,其后冷却至175℃;
66.(9)平整处理:将过时效处理后的板坯进行平整处理,使其延伸率为1%。
67.实施例2:
68.一种钢带及其制备方法,其特征包括如下步骤:
69.(1)原料选取:c:0.003%,nb:0.02%,a1t:0.02%,其余为fe及不可避免的杂质;
70.(2)板坯制作:通过连铸获取含上述化学成分的板坯;
71.(3)轧制前加热:将板坯置于炉中加热140min,并使其出炉温度为1150℃;
72.(4)轧制:对加热后的板坯进行轧制,并使其终轧温度为870℃,卷取温度为610℃;
73.(5)轧制后冷却:以15℃/s的冷却速度将轧制后的板坯冷却10s,再以5℃/s的冷却速度冷却20s;
74.(6)退火冷却:将轧制后冷却的板坯以150℃/min的速度加热至760℃;
75.(7)均热后冷却:将退火冷却后的板坯以5℃/s的速度冷却至640℃,再以30℃/s的速度冷却至440℃;
76.(8)过时效处理:将均热后冷却的板坯于370℃保持5min,其后冷却至170℃;
77.(9)平整处理:将过时效处理后的板坯进行平整处理,使其延伸率为0.6%。
78.实施例3:
79.一种钢带及其制备方法,其特征包括如下步骤:
80.(1)原料选取:c:0.01%,nb:1%,a1t:0.06%,mn:1.0%,p:0.05%,s:0.015%,n:0.004%,b:0.0005%,其余为fe及不可避免的杂质;
81.(2)板坯制作:通过连铸获取含上述化学成分的板坯;
82.(3)轧制前加热:将板坯置于炉中加热220min,并使其出炉温度为1230℃;
83.(4)轧制:对加热后的板坯进行轧制,并使其终轧温度为920℃,卷取温度为710℃;
84.(5)轧制后冷却:以25℃/s的冷却速度将轧制后的板坯冷却1s,再以20℃/s的冷却速度冷却3s;
85.(6)退火冷却:将轧制后冷却的板坯以250℃/min的速度加热至830℃;
86.(7)均热后冷却:将退火冷却后的板坯以15℃/s的速度冷却至660℃,再以50℃/s的速度冷却至460℃;
87.(8)过时效处理:将均热后冷却的板坯于430℃保持3min,其后冷却至180℃;
88.(9)平整处理:将过时效处理后的板坯进行平整处理,使其延伸率为1.4%。
89.综上所述,本技术实施例提供了一种钢带,应用于汽车面板时,可提高汽车外板的强度、成形性和抗凹性,达到汽车轻量化目标。
90.应该理解,在本文中所披露的范围的端点和任何值都不限于该精确的范围或值,这些范围或值应当理解为包含接近这些范围或值的值。对于数值范围来说,各个范围的端点值之间、各个范围的端点值和单独的点值之间,以及单独的点值之间可以彼此组合而得到一个或多个新的数值范围,这些数值范围应被视为在本文中具体公开。
91.需要说明的是,在本文中,诸如“第一”和“第二”等之类的关系术语仅仅用来将一个实体或者操作与另一个实体或操作区分开来,而不一定要求或者暗示这些实体或操作之间存在任何这种实际的关系或者顺序。而且,术语“包括”、“包含”或者任何其他变体意在涵盖非排他性地包含,从而使得包括一系列要素的过程、方法、物品或者设备不仅包括那些要素,而且还包括没有明确列出的其他要素,或者还包括为这种过程、方法、物品或者设备所固有的要素。另外,本文中出现的术语“和/或”,仅仅是一种描述关联对象的关联关系,表示可以存在三种关系,例如,a和/或b,可以表示:单独存在a,同时存在a和b,单独存在b这三种情况。
92.以上所述仅是本发明的具体实施方式,使本领域技术人员能够理解或实现本发明。对这些实施例的多种修改对本领域的技术人员来说将是显而易见的,本文中所定义的一般原理可以在不脱离本发明的精神或范围的情况下,在其它实施例中实现。因此,本发明将不会被限制于本文所示的这些实施例,而是要符合与本文所申请的原理和新颖特点相一致的最宽的范围。