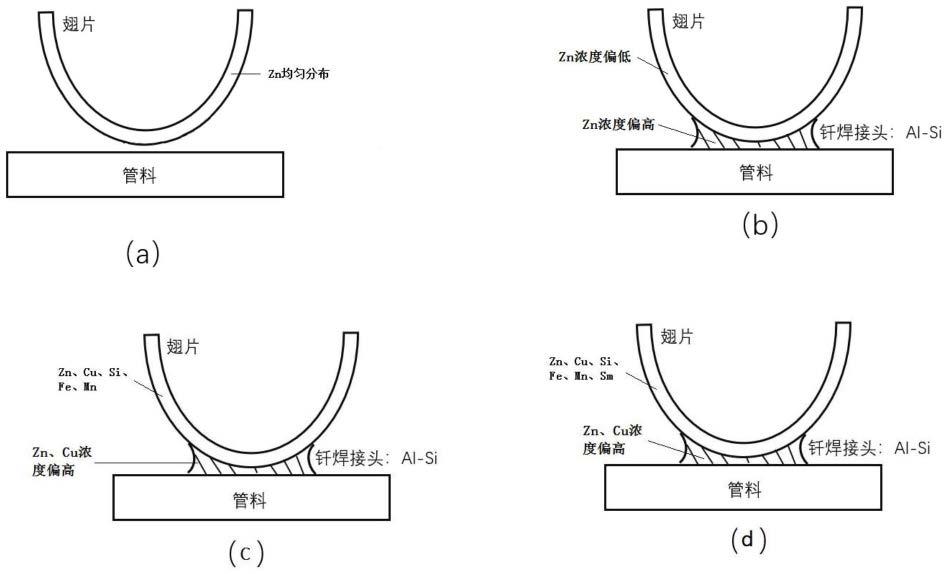
1.本发明属于铝合金技术领域,涉及一种高耐腐蚀热交换器翅片及其制备方法,具体涉及一种能够不另外复合钎料而通过其自身的接合性实现与管板料的钎焊接合的高耐腐蚀热交换器翅片。
背景技术:2.常规的不同铝合金构件结合时,通常在两类合金构件之间添加一层钎料层,钎料层在两个合金构件之间熔融润湿实现两者的接合。为获得上述的效果不可避免的需要进行额外的在其中一个合金表面复合一定厚度的钎料层。通常钎料层为4系铝硅合金,一般选用含硅量6-10wt%的al-si合金。通过复合的方式,一方面芯层起到了维持强度、抗塌等功能性要求,钎料层则主要起到钎焊结合两个构件的作用。复合的过程往往导致加工流程十分拢长,加工成本高,工艺耗时长,生产效率低。近年来业内致力于开发一种新型热交换器翅用铝合金材料,采用单层的铝合金材料即可实现与另一个铝合金部件的接合,即所述铝合金翅片材料自身还承担着钎料的功能。钎焊时,铝合金翅片与管料形成钎焊结合。例如在cn103906852a热交换器翅用铝合金材料及其制造方法、以及使用该铝合金材料的热交换器,披露了一种铝合金含有si为1~5wt%,fe为0.1~2wt%,mn为0.1~2wt%,并且具有特定的si系金属间化合物个数和al-fe-mn-si系金属间化合物个数,自钎焊的过程和原理可参照专利文献cn103906852a说明书披露的内容;在另一项发明cn112195375a中披露了一种自钎焊铝合金箔材,由以下质量百分比组分组成:fe:0.2~0.4%,si:2.1~2.3%,mn:1.25~1.45%,zn:1.4~1.6%,cu:0.3~0.4%,ti:0.01~0.02%,re:0.03~0.07%,zr:0.03~0.07%,其余为al,所述自钎焊铝合金箔材的厚度0.05~0.10mm。在上述的单层铝合金翅用材料中,材料配方所基于的共性特征在于对si、fe、mn元素的控制,以及对高温性能的改良,然而对于这类新型的单层铝合金翅用材料中,翅片局部自腐蚀和牺牲阳极腐蚀的速度过快问题仍然存在,使得该类铝合金制得的翅片在实际应用过程中仍然受限制。
技术实现要素:3.本发明的目的是解决现有技术中存在的上述问题,提供一种高耐腐蚀热交换器翅片及其制备方法。
4.为达到上述目的,本发明采用的技术方案如下:
5.一种高耐腐蚀热交换器翅片,所述高耐腐蚀热交换器翅片材质为铝合金箔,所述铝合金箔包含si:1.5~3.0wt%;fe:≤2wt%;mn:1.0~1.82wt%;zn:1.5~2.0wt%;cu:≤0.25wt%;sm:≥0.1wt%;余量为al和不可避免的杂质;
6.zn元素与cu元素的合金组分含量的配比关系应满足:0.6wt≤zn-4*cu≤1.2wt%;
7.采用所述高耐腐蚀热交换器翅片进行自钎焊后,在钎焊接头处与翅片中心的电位的差值≤30mv。
8.作为优选的技术方案:
9.如上所述的一种高耐腐蚀热交换器翅片,将高耐腐蚀热交换器翅片与aa3003材质的管材进行钎焊,焊后按照astm g85-a3试验后测得的翅片接头脱落比为16~38%,翅片失重比为28~41%。需要注意的是,使用aa3003材质的管材仅是为了相对的评价翅片的腐蚀情况,并不必然一定要选择aa3003的材质,也可以使用其他的材质作为管料评价翅片的腐蚀情况,当以aa3003管料作为与翅片钎焊的对象时,测定焊后翅片接头脱落比为16~38%,翅片失重比为28~41%。
10.如上所述的一种高耐腐蚀热交换器翅片,所述高耐腐蚀热交换器翅片中si的含量为2.5~3wt%,在常规热交换器气氛保护焊条件下,钎焊接头长度可达400μm以上,当si元素含量在该范围时耐腐蚀性更佳,当si含量在1.5~2wt%时,虽然也可以成功的形成钎焊接头,然而钎焊接头相对过小时,相对的容易造成腐蚀脱落。
11.如上所述的一种高耐腐蚀热交换器翅片,所述高耐腐蚀热交换器翅片中fe的含量≤0.2wt%,sm的含量为0.1~0.3wt%。
12.如上所述的一种高耐腐蚀热交换器翅片,焊后所述高耐腐蚀热交换器翅片的表面晶粒平均尺寸≥600μm。
13.如上所述的一种高耐腐蚀热交换器翅片,所述高耐腐蚀热交换器翅片的厚度为0.05~0.10mm。
14.本发明还提供如上所述的一种高耐腐蚀热交换器翅片的制备方法,包括如下步骤:
15.(1)按照所述高耐腐蚀热交换器翅用铝合金箔中各组分及重量百分比进行配料后,采用铸轧工艺得到铸轧成品;
16.(2)对步骤(1)的产物进行冷轧后进行第一次完全再结晶退火;
17.(3)对步骤(2)的产物继续进行冷轧后进行第二次完全再结晶退火;
18.(4)对步骤(3)的产物进行冷轧至0.05~0.10mm厚度得到所述高耐腐蚀热交换器翅用铝合金箔;
19.(5)对步骤(4)的铝合金箔压制变形,制得目标形状的高耐腐蚀热交换器翅片。
20.作为优选的技术方案:
21.如上所述的一种高耐腐蚀热交换器翅片的制备方法,步骤(1)中所述铸轧工艺的工艺参数为:保温炉和除气箱温度740~770℃,前箱温度730~760℃,铸轧区长度55~65mm,冷却水温≤32℃,铸轧速度550~650mm/min。
22.如上所述的一种高耐腐蚀热交换器翅片的制备方法,步骤(1)中铸轧成品厚度为6.9~7.5mm。
23.如上所述的一种高耐腐蚀热交换器翅片的制备方法,步骤(2)中冷轧至厚度为3~4mm后进行第一次完全再结晶退火,退火温度为400~500℃,退火时间为1~3h。
24.如上所述的一种高耐腐蚀热交换器翅片的制备方法,步骤(3)中冷轧至厚度为0.1~0.15mm后进行第二次完全再结晶退火,退火温度为270~370℃,退火时间为1~3h。
25.铝合金压制成翅片是常规技术,具体为铝合金箔经过滚轮/辊刀滚压成波形翅片,还可以增加常规的开窗设计,用来增加散热面积。
26.本发明的原理如下:
27.基于现有已经公开的自钎焊的翅用铝合金技术,翅用铝合金箔含有si为1~
5wt%,fe为0.1~2wt%,mn为0.1~2wt%,al-fe-mn-si自钎焊翅片通过al-si共晶扩散,翅片在固液共存状态实现自我钎焊,体系获得适量的si系金属间化合物个数和al-fe-mn-si系金属间化合物,能够确保材料在实现钎焊的同时,保持形状不坍塌。然而,具体实验中表明,至少需要1.5wt%的si才能实现成功的接合。
28.基于公知常识通常采用zn元素降低腐蚀电位,在常规翅片中通常添加zn元素来获得腐蚀电位,以使得翅片与管料存在一定的电位差,通过翅片料作为牺牲阳极来保护管料不被腐蚀,从而提高管料的寿命,即称为牺牲阳极腐蚀特性。上述常规翅片是指在钎焊工艺下,利用钎料熔融润湿翅片与管料的表面,来使得翅片与管料接合,通常在翅片料的表面复合al-si钎料,还包括在管料表面复合钎料,利用钎料将翅片与管料钎焊复合,而翅片本身不能直接通过钎焊焊接到管料表面的翅片材料。在现有技术中未提及用于自钎焊的翅片均是在钎焊过程中不参与形成液相的常规翅片。
29.同理,本发明的翅片料中添加一定量的zn元素,使得翅片与管料之间形成腐蚀电位差,通过翅片料的牺牲阳极腐蚀特性,作为牺牲阳极来保护管料不被腐蚀,从而提高管料的寿命。zn元素的添加量控制在1.5~2wt%为宜,由于添加zn元素是为了使得在腐蚀环境下,翅片相对于管料能够更优先的在翅片上发生腐蚀进而保护管料,因此我们期望翅片具有优先于管料腐蚀的牺牲阳极腐蚀特性,又期望这种牺牲阳极腐蚀的过程能够以缓慢的速度进行,这样可以更长期的保护管料。翅片一旦腐蚀过快、甚至是翅片直接脱腐蚀落则不能再发挥其功效,因此翅片料的牺牲阳极腐蚀特性能力的调节,是提高管料耐腐蚀问题是影响材料长期使用功能至关重要的物性。zn元素的添加并非越多越好,zn元素含量的多少直接影响铝合金的电位特性,进而影响翅片的腐蚀能力和腐蚀速度,应根据腐蚀的结果,控制zn元素不至于过少,也不至于过多。
30.在适于自钎焊铝合金箔材钎焊的温度下,al-si共晶向钎焊表面流动(原理见cn103906852a)以实现翅片与管料的接合。常规翅片料的钎焊过程利用铝硅钎料层的熔融进行钎焊接合,翅片料本身并不会存在al-si共晶向钎焊表面流动的情况。然而,相比于常规翅片料,本技术的自钎焊铝合金箔材目前遇到的困境是:自钎焊的过程加速了zn元素向钎焊接头扩散的程度,zn元素通过al-si共晶沿晶界等通道快速扩散至钎焊接头,使得在接头富集大量的zn元素,导致接头处的zn元素浓度远大于翅片中zn元素的浓度(图1(a)),以此形成了接头处的腐蚀电位与翅片的腐蚀电位相差很大。当翅片本身产生局部铝基体的电位差时,会造成局部自腐蚀,随着zn元素的流动而产生翅片内部与翅片接头处的电位差。接头处zn元素分布浓度越高,腐蚀速度越快,接头处极容易产生翅片的局部自腐蚀而脱落。因此,我们期望在确保翅片具有一定zn浓度的同时,解决接头提前脱落的问题,也就是说我们期望接头处的zn浓度不至于过高,能够与翅片内的zn浓度保持同等的浓度水平。可见,相较于翅片整体过快的牺牲阳极腐蚀特性而言,zn元素通过al-si共晶沿晶界等通道快速扩散至钎焊接头,导致翅片接头处的电位过低(图1(b)),在接头处会优先于翅片发生腐蚀,而致使翅片脱落,是导致翅片更快的丧失对管料耐腐蚀性保护的原因。
31.cu元素与zn元素的功能相反,cu元素可以提高铝合金的腐蚀电位。通常情况下,cu元素会导致zn元素降低电位的功能失效,当铝合金作为牺牲阳极时,在含zn铝合金体系中通常不会再添加cu元素。本发明通过cu元素的加入,利用钎焊时cu元素同样具有扩散到钎焊接头的特性,可以显著地中和zn元素扩散至钎焊接头所带来的影响(图1(c)),解决钎焊
接头的腐蚀电位过低的问题。然而,对cu元素含量控制是十分谨慎的。首先cu元素应总体上控制在0.5wt%以内,过多的cu元素会导致对铝合金熔点产生较大的影响,进而热交换器翅片在自钎焊时难以保持翅片结构不塌陷。其次,cu元素的添加应匹配zn元素的添加量,限定0.6wt%≤zn-4cu≤1.2wt%,以实现cu元素中和钎焊接头中zn元素的低电位,又不至于过多的cu元素停留在翅片中影响翅片的牺牲阳极腐蚀特性。
32.另一方面,发明人发现sm元素的加入可以减少高si相带来的与铝基体产生电位差导致的另一个方面的局部自腐蚀问题。非自钎焊的普通翅片中很少或基本没有高si相/初生硅,但是当si超过2%甚至2.5%,高si相/初生硅与铝基体产生显著电位差,导致翅片内部的局部自腐蚀。因si元素、cu元素向sm的球状相偏聚而形成al-si-cu-sm化合物的腐蚀电位和基体腐蚀电位接近(图2(b)),两者的电位接近,可以有效的避免高si相带来的局部自腐蚀的问题;也可以消除翅片内部引入的cu元素带来的不利影响。
33.所述的高si相是指si含量高达2wt%以上时,形成与铝基体显著的电位差,而导致翅片内部局部自腐蚀的产生。
34.通过zn、cu、sm元素的特定的调配最终实现既确保翅片具有zn元素降低电位的功能以获得牺牲阳极腐蚀特性,作为牺牲阳极保护管料,又不至于zn元素富集于钎焊接头,导致翅片在钎焊接头处产生局部自腐蚀,同时避免内部高硅相、cu相与铝基体产生的局部电偶腐蚀。
35.除了控制zn元素在钎焊接头富集而导致翅片脱落外,发明人致力于研究在确保翅片料牺牲阳极腐蚀特性的基础上,如何降低作为牺牲阳极腐蚀的速度,研究发现,现有技术提供的铝合金翅片料的牺牲阳极腐蚀的速度过快而导致耐腐蚀性较差的原因包括以下几个方面:
36.①
晶粒控制对降低翅片腐蚀速度的影响
37.发明人发现合理的控制晶粒大小来压缩晶界区域的大小,可以提高材料的耐腐蚀性,晶界相较晶内原子能量更大更不稳定,在我们通过侵蚀的方法看晶粒大小可见晶界被快速的腐蚀,晶界内形成了轮廓分明的一颗颗晶粒。晶粒越小,晶界面积越大,翅片牺牲阳极腐蚀的速度越快。当焊后晶粒平均尺寸≥600μm时,显著的降低了翅片的腐蚀速度。对于晶粒尺寸的调节,在配方上通常需要限制fe、sm这类具有细化晶粒功能的合金元素,fe≤0.2wt%,sm≤0.3wt%;在工艺上,本技术采用铸造冷却速度快的连续铸轧工艺,根据本合金的特点,铸轧速度应匹配在500mm/min以上,确保一定的铸轧速度是获得大尺寸晶粒的关键,特别优选的将铸轧速度控制在550~650mm/min。
38.②
粗大化合物对腐蚀速度的影响
39.过多的mn元素影响产品的耐腐蚀性,mn元素超过1.82wt%容易生产粗大化合物,粗大针状化合物会割裂铝基体,降低产品的耐腐蚀性能。
40.有益效果:
41.(1)本发明克服了自钎焊的翅片在钎焊时,zn元素向钎焊接头富集,钎焊接头处zn元素相对浓度过高,而导致的钎焊接头处腐蚀加速提前脱落的问题。通过同时引入cu、sm,利用cu元素扩散的特性,在钎焊时cu元素向钎焊接头扩散一定程度的中和zn元素对电位的影响,最终自钎焊后,使得钎焊接头处与翅片中心的电位的差值≤30mv,以确保翅片具有牺牲阳极腐蚀特性的同时不至于钎焊接头过早的脱落。
42.(2)在翅片内部,利用sm元素,si、cu元素向sm的球状相偏聚而形成al-si-cu-sm化合物的腐蚀电位和基体腐蚀电位接近,消除翅片内部cu元素、si元素导致的局部腐蚀电位差,消除腐蚀电位的影响而导致的翅片内部产生局部腐蚀。
43.(3)本发明通过调节晶粒大小来控制翅片的牺牲阳极腐蚀的速度,以此可以更久的保护管材不被腐蚀。
附图说明
44.图1为cu、sm元素共同调节钎焊后翅片与钎焊接头电位的机理图,(a)为未进行钎焊时的翅片;(b)为进行钎焊的翅片,翅片合金中同时含si、fe、mn、zn合金元素;(c)为进行钎焊的翅片,翅片合金中同时含si、fe、mn、zn、cu合金元素;(d)为进行钎焊的翅片,翅片合金中同时含si、fe、mn、zn、cu、sm合金元素;
45.图2为翅片内部高si,高cu相的分布,(a)为没有sm元素,高si,高cu相的分布,(b)为引入sm元素后相的分布;
46.图3为钎焊接头处与翅片中心的电位的差值点位示意图;
47.图4为铝箔通过辊压制成翅片形态的实物图;
48.图5为常规热交换器芯体钎焊工艺;
49.图6为翅片与管材组装成冷凝器芯体的示意图。
具体实施方式
50.下面结合具体实施方式,进一步阐述本发明。应理解,这些实施例仅用于说明本发明而不用于限制本发明的范围。此外应理解,在阅读了本发明讲授的内容之后,本领域技术人员可以对本发明作各种改动或修改,这些等价形式同样落于本技术所附权利要求书所限定的范围。
51.一般定义及术语
52.除非另外定义,本发明中使用的所有技术和科学术语具有本发明所属领域普通技术人员通常所理解的同样含义。在抵触的情况下,以本说明书包括定义为准。
53.除非另外说明,所有的百分数、份数、比例等都以重量计。
54.本文所使用的术语“不可避免的杂质”指在合金生产过程中并非刻意添加的,而是由于例如与生产设备接触等原因不可避免地引入的其他元素;对于杂质的管控按照一般要求确定,即单种杂质小于等于0.05wt%,杂质总和≤0.15wt%。
55.本技术所使用的术语“自钎焊”是指一种能够不另外复合钎料而通过其自身的接合性实现与非复合管板料的钎焊接合的铝合金翅片料本身具有的一种钎焊能力,具体为所述翅片在钎焊温度下,翅片中的al-si共晶向钎焊表面流动形成钎焊接头。
56.本技术所使用的术语“牺牲阳极腐蚀”是指当翅片与铝合金管钎焊结合后,由于翅片具有低腐蚀电位,而在腐蚀环境下,优先于管料腐蚀的特性,以此保护管料不被腐蚀。
57.本技术所使用的术语“局部自腐蚀”是指由于翅片自身内部的不同区域产生电位差,造成局部的电偶腐蚀,例如当翅片的接头处的电位低于翅片内部时,在接头处会产生加速腐蚀,而导致接头提前脱落,例如内部高si相、高cu相带来的局部自腐蚀问题。
58.实验与检测手段
59.1.钎焊工艺:
60.设备为常规氮气保护隧道炉,常规热交换器芯体钎焊工艺如图5所示,前五分钟为喷淋钎剂和保温干燥阶段,温度为200~250℃。然后10~15分钟升温至605℃左右,保温3~5min,后以40~60℃/min冷却至室温。实验中采用的管料材质为a3003铝合金,测定管料的电位为-700mv,在如上所述的钎焊工艺下将翅片与管料钎焊结合,本技术实施例制得的翅片,未经如上钎焊处理的样品记为ai,经如上钎焊处理的样品记为bi;将翅片成型所用的铝合金箔材记为样品ci;
61.2.电位测试:对样品bi的翅片采用万通电化学工作站进行电位的测定,钎焊接头处与翅片中心的电位的差值点位如图3所示,测试参照标准astm-g69实施。
62.3.晶粒尺寸评价:对样品bi的翅片采用gb/t 6394-2017《金属平均晶粒度测定方法》标准方法,通过蔡司偏光显微镜测定样品的平均晶粒尺寸,由于翅片太薄,截面不容易分析晶粒尺寸,因此测试的部位为样品表面。
63.4.耐腐蚀性能的评判:
64.将铝合金箔压制成相同尺寸形状的翅片试样,翅片试样的尺寸形状规格如下:
65.宽度为12
±
0.1mm,长度为665
±
0.1mm,翅片上下波峰数共计380个,波距为3.5
±
0.1mm(即两个波峰之间的距离);
66.将上述翅片与aa3003材质的管材进行钎焊,管材的宽度、高度与翅片相同,即通常的适配于相应翅片的管材规格。
67.将上述翅片与管材组装成冷凝器芯体,如图6所示,通过如上的钎焊工艺钎焊连接在一起。将焊后的芯体按照astm g85-a3进55天的swaat盐雾试验后,将芯体取出。做完腐蚀试验后的芯体需要用5%质量浓度的草酸,将芯体表面的腐蚀产物清洗干净。
68.1)翅片接头脱落比
69.用金相显微镜观察脱落接头的数量,除以做腐蚀前的接头总数量(边部接头不计算在实验中),为翅片接头脱落比。
70.2)翅片失重比
71.将清洗后的芯体上的翅片以及接头全部切下来,并进行称重,除以钎焊前翅片的总重量。
72.实施例1
73.一种高耐腐蚀热交换器翅片的制备方法,包括如下步骤:
74.(1)合金元素按照si:3wt%、fe:0.1wt%、mn:1.5wt%、zn:1.6wt%、cu:0.2wt%、sm:0.2wt%进行配料,其余为铝,检测杂质含量控制合格;然后采用铸轧工艺得到厚度为7.2mm的铸轧成品;
75.其中,铸轧工艺的工艺参数为:保温炉和除气箱温度760℃,前箱温度745℃,铸轧区长度60mm,冷却水温30℃,铸轧速度600mm/min;
76.(2)对步骤(1)的产物进行冷轧至厚度为3.5mm后进行第一次完全再结晶退火,退火温度为450℃,退火时间为2h;
77.(3)对步骤(2)的产物继续进行冷轧至厚度为0.12mm后进行第二次完全再结晶退火,退火温度为320℃,退火时间为2h;
78.(4)对步骤(3)的产物进行冷轧至0.08mm厚度,得到铝合金箔;
79.(5)如图4所示,将步骤(4)的铝合金箔压制变形,得到高耐腐蚀热交换器翅片。
80.采用制得的高耐腐蚀热交换器翅片进行自钎焊后,翅片中心的电位为-760.7mv,钎焊接头处的电位为-782.6mv,在钎焊接头处与翅片中心的电位的差值为21.9mv;焊后高耐腐蚀热交换器翅片的表面晶粒平均尺寸为703μm;将高耐腐蚀热交换器翅片与aa3003材质的管材进行钎焊,焊后按照astm g85-a3试验后测得的翅片失重比为31%,翅片接头脱落比为20%。
81.对比例1
82.一种热交换器翅片的制备方法,具体步骤基本同实施例1,不同之处仅在于步骤(1)中不含cu和sm;
83.采用对比例1制得的热交换器翅片进行自钎焊后,翅片中心的电位为-812.1mv,钎焊接头处的电位为-873.2mv,在钎焊接头处与翅片中心的电位的差值为61.1mv;焊后热交换器翅片的表面晶粒平均尺寸为943μm;将热交换器翅片与aa3003材质的管材进行钎焊,焊后按照astm g85-a3试验后测得的翅片失重比为53%,翅片接头脱落比为46%。
84.将对比例1与实施例1进行对比,可以发现对比例1在钎焊接头处与翅片中心的电位的差值、焊后晶粒平均尺寸、翅片质量损失百分比及芯材翅片脱落百分比明显高于实施例1,这是因为不加cu和sm,在钎焊接头处与翅片中心的电位差大,内部和接头均产生局部自腐蚀。
85.对比例2
86.一种热交换器翅片的制备方法,具体步骤基本同实施例1,不同之处仅在于步骤(1)中不含sm;制得的热交换器翅片内部的si、cu相的分布如图2(a)所示;
87.采用对比例2制得的热交换器翅片进行自钎焊后,翅片中心的电位为-756.7mv,钎焊接头处的电位为-782.5mv,在钎焊接头处与翅片中心的电位的差值为25.8mv;焊后热交换器翅片的表面晶粒平均尺寸为929μm;将热交换器翅片与aa3003材质的管材进行钎焊,焊后按照astm g85-a3试验后测得的翅片失重比为63%,翅片接头脱落比为23%。
88.将对比例2与实施例1进行对比,可以发现对比例2的翅片焊后晶粒平均尺寸明显高于实施例1,这是因为实施例1中加入sm会导致晶粒更为细化;同时可以发现对比例2的翅片失重比明显高于实施例1,这是因为加cu不加sm,内部局部自腐蚀。
89.实施例1与对比例1和对比例2为基于不同合金添加的翅片,在翅片未进行自钎焊时,实施例1、对比例1和对比例2对应的翅片上的zn元素均是均匀分布的,如图1(a)所示;随着钎焊的进行,al-si共晶向钎焊接头流动以形成钎焊接头,zn元素随之扩散到钎焊接头,使得接头处zn元素浓度增高,如图1(b)所示;当进一步在体系中添加cu元素时,cu元素和zn元素共同扩散至钎焊接头,如图1(c)所示,cu元素会提高电位,在接头处cu元素可以极大的削弱zn元素所导致的电负性,然而翅片内的电位亦受到cu元素的影响,这不是我们期望的,一方面使得两者的差值仍然较大,另一方面如果添加的cu元素过度,反而导致翅片的电位严重偏高,失去牺牲阳极腐蚀的特性,影响翅片相对于管料优先腐蚀能力的获得;进一步在体系中添加sm元素,翅片中的sm元素不会扩散到钎焊接头,如图1(d)所示,匹配一定量sm元素的加入可以使得翅片中的cu、si元素形成al-si-cu-sm化合物,该化合物的腐蚀电位和基体腐蚀电位接近,避免因翅片内部存留的cu、si元素导致翅片内部产生局部自腐蚀。
90.对比例3
91.一种热交换器翅片的制备方法,具体步骤基本同实施例1,不同之处仅在于步骤(1)中cu的含量为0.08wt%;
92.采用对比例3制得的热交换器翅片进行自钎焊后,翅片中心的电位为-777.54mv,钎焊接头处的电位为-827mv,在钎焊接头处与翅片中心的电位的差值为49.46mv;焊后热交换器翅片的表面晶粒平均尺寸为696μm;将热交换器翅片与aa3003材质的管材进行钎焊,焊后按照astm g85-a3试验后测得的翅片失重比为49%,翅片接头脱落比为40%。
93.将对比例3与实施例1进行对比,可以发现对比例3在钎焊接头处与翅片中心的电位的差值、翅片质量损失百分比及芯材翅片脱落百分比明显高于实施例1,这是因为zn-4*cu的含量太高,cu元素扩散到接头太少,从而导致在钎焊接头处与翅片中心的电位差大。
94.对比例4
95.一种热交换器翅片的制备方法,具体步骤基本同实施例1,不同之处仅在于步骤(1)中cu的含量为0.35wt%;
96.采用对比例4制得的热交换器翅片进行自钎焊后,翅片中心的电位为-728.7mv,钎焊接头处的电位为-738.6mv,在钎焊接头处与翅片中心的电位的差值为9.9mv;焊后晶粒平均尺寸为712μm;管料腐蚀发生泄露。
97.将对比例4与实施例1进行对比,可以发现对比例4翅片中心的电位变化到-728.7mv,这是因为zn-4*cu太低,cu元素添加过多时,虽然进一步降低了钎焊接头与翅片中心的电位差,但同时也严重的影响了翅片整体的电位电负性,对翅片电位水平产生严重的影响。
98.实施例2
99.一种高耐腐蚀热交换器翅片的制备方法,包括如下步骤:
100.(1)合金元素按照si:2.5wt%、fe:0.2wt%、mn:1wt%、zn:2wt%、cu:0.2wt%、sm:0.3wt%、进行配料,其余为铝,检测杂质含量控制合格;然后采用铸轧工艺得到厚度为6.9mm的铸轧成品;
101.其中,铸轧工艺的工艺参数为:保温炉和除气箱温度770℃,前箱温度730℃,铸轧区长度55mm,冷却水温32℃,铸轧速度550mm/min;
102.(2)对步骤(1)的产物进行冷轧至厚度为4mm后进行第一次完全再结晶退火,退火温度为500℃,退火时间为3h;
103.(3)对步骤(2)的产物继续进行冷轧至厚度为0.15mm后进行第二次完全再结晶退火,退火温度为270℃,退火时间为1h;
104.(4)对步骤(3)的产物进行冷轧至0.05mm厚度,得到铝合金箔;
105.(5)如图4所示,将步骤(4)的铝合金箔压制变形,得到高耐腐蚀热交换器翅片。
106.采用制得的高耐腐蚀热交换器翅片进行自钎焊后,翅片中心的电位为-783.8mv,钎焊接头处的电位为-805.2mv,在钎焊接头处与翅片中心的电位的差值为21.4mv;焊后高耐腐蚀热交换器翅片的表面晶粒平均尺寸为663μm;将高耐腐蚀热交换器翅片与aa3003材质的管材进行钎焊,焊后按照astm g85-a3试验后测得的翅片失重比为31%,翅片接头脱落比为16%。
107.对比例5
108.一种热交换器翅片的制备方法,具体步骤基本同实施例2,不同之处仅在于步骤
(1)中si的含量为1wt%;
109.采用对比例5制得的热交换器翅片进行自钎焊后,不能形成有效的钎焊接头,这是因为si含量添加过少时,在钎焊时能够生成的液相不足,进而表现为无法形成有效的钎焊接头。
110.实施例3
111.一种高耐腐蚀热交换器翅片的制备方法,包括如下步骤:
112.(1)合金元素按照si:2.5wt%、fe:0.3wt%、mn:1wt%、zn:2wt%、cu:0.2wt%、sm:0.3wt%、进行配料,其余为铝,检测杂质含量控制合格;然后采用铸轧工艺得到厚度为6.9mm的铸轧成品;
113.其中,铸轧工艺的工艺参数为:保温炉和除气箱温度770℃,前箱温度730℃,铸轧区长度55mm,冷却水温32℃,铸轧速度550mm/min;
114.(2)对步骤(1)的产物进行冷轧至厚度为4mm后进行第一次完全再结晶退火,退火温度为500℃,退火时间为3h;
115.(3)对步骤(2)的产物继续进行冷轧至厚度为0.15mm后进行第二次完全再结晶退火,退火温度为270℃,退火时间为1h;
116.(4)对步骤(3)的产物进行冷轧至0.05mm厚度,得到铝合金箔;
117.(5)如图4所示,将步骤(4)的铝合金箔压制变形,得到高耐腐蚀热交换器翅片。
118.采用制得的高耐腐蚀热交换器翅片进行自钎焊后,翅片中心的电位为-793.6mv,钎焊接头处的电位为-809.4mv,在钎焊接头处与翅片中心的电位的差值为15.8mv;焊后高耐腐蚀热交换器翅片的表面晶粒平均尺寸为558μm;将高耐腐蚀热交换器翅片与aa3003材质的管材进行钎焊,焊后按照astm g85-a3试验后测得的翅片失重比为41%,翅片接头脱落比为22%。
119.将实施例3与实施例2进行对比,可以发现实施例3在钎焊接头处与翅片中心的电位的差值及焊后晶粒平均尺寸低于实施例2,而翅片质量损失百分比和芯材翅片脱落百分比高于实施例2,这是因为fe元素能够影响晶粒生长,过多的添加fe元素会导致晶粒过细,过细的晶粒会导致晶界变大,腐蚀易在晶界开始,致使一定程度上影响耐腐蚀性能。
120.实施例4
121.一种高耐腐蚀热交换器翅片的制备方法,包括如下步骤:
122.(1)合金元素按照si:2.5wt%、fe:0.2wt%、mn:1wt%、zn:2wt%、cu:0.2wt%、sm:0.3wt%、进行配料,其余为铝,检测杂质含量控制合格;然后采用铸轧工艺得到厚度为6.9mm的铸轧成品;
123.其中,铸轧工艺的工艺参数为:保温炉和除气箱温度770℃,前箱温度730℃,铸轧区长度55mm,冷却水温32℃,铸轧速度400mm/min;
124.(2)对步骤(1)的产物进行冷轧至厚度为4mm后进行第一次完全再结晶退火,退火温度为500℃,退火时间为3h;
125.(3)对步骤(2)的产物继续进行冷轧至厚度为0.15mm后进行第二次完全再结晶退火,退火温度为270℃,退火时间为1h;
126.(4)对步骤(3)的产物进行冷轧至0.05mm厚度,得到铝合金箔;
127.(5)如图4所示,将步骤(4)的铝合金箔压制变形,得到高耐腐蚀热交换器翅片。
128.采用制得的高耐腐蚀热交换器翅片进行自钎焊后,翅片中心的电位为-782.1mv,钎焊接头处的电位为-801.4mv,在钎焊接头处与翅片中心的电位的差值为19.3mv;焊后高耐腐蚀热交换器翅片的表面晶粒平均尺寸为517μm;将高耐腐蚀热交换器翅片与aa3003材质的管材进行钎焊,焊后按照astm g85-a3试验后测得的翅片失重比为40%,翅片接头脱落比为25%。
129.将实施例4与实施例2进行对比,可以发现实施例4在钎焊接头处与翅片中心的电位的差值及焊后晶粒平均尺寸低于实施例2,而翅片质量损失百分比和芯材翅片脱落百分比高于实施例2,这是因为选择过慢的铸轧速度导致晶粒过细,过细的晶粒会导致晶界变大,腐蚀易在晶界开始,致使一定程度上影响耐腐蚀性能。
130.实施例5
131.一种高耐腐蚀热交换器翅片的制备方法,包括如下步骤:
132.(1)合金元素按照si:1.5wt%、fe:0.2wt%、mn:1wt%、zn:2wt%、cu:0.2wt%、sm:0.3wt%、进行配料,其余为铝,检测杂质含量控制合格;然后采用铸轧工艺得到厚度为6.9mm的铸轧成品;
133.其中,铸轧工艺的工艺参数为:保温炉和除气箱温度770℃,前箱温度730℃,铸轧区长度55mm,冷却水温32℃,铸轧速度550mm/min;
134.(2)对步骤(1)的产物进行冷轧至厚度为4mm后进行第一次完全再结晶退火,退火温度为500℃,退火时间为3h;
135.(3)对步骤(2)的产物继续进行冷轧至厚度为0.15mm后进行第二次完全再结晶退火,退火温度为270℃,退火时间为1h;
136.(4)对步骤(3)的产物进行冷轧至0.05mm厚度,得到铝合金箔;
137.(5)如图4所示,将步骤(4)的铝合金箔压制变形,得到高耐腐蚀热交换器翅片。
138.采用制得的高耐腐蚀热交换器翅片进行自钎焊后,翅片中心的电位为-787.2mv,钎焊接头处的电位为-807.3mv,在钎焊接头处与翅片中心的电位的差值为20.1mv;焊后高耐腐蚀热交换器翅片的表面晶粒平均尺寸为649μm;将高耐腐蚀热交换器翅片与aa3003材质的管材进行钎焊,焊后按照astm g85-a3试验后测得的翅片失重比为29%,翅片接头脱落比为38%。
139.实施例6
140.一种高耐腐蚀热交换器翅片的制备方法,包括如下步骤:
141.(1)合金元素按照si:2wt%、fe:0.2wt%、mn:1wt%、zn:2wt%、cu:0.2wt%、sm:0.3wt%、进行配料,其余为铝,检测杂质含量控制合格;然后采用铸轧工艺得到厚度为6.9mm的铸轧成品;
142.其中,铸轧工艺的工艺参数为:保温炉和除气箱温度770℃,前箱温度730℃,铸轧区长度55mm,冷却水温32℃,铸轧速度550mm/min;
143.(2)对步骤(1)的产物进行冷轧至厚度为4mm后进行第一次完全再结晶退火,退火温度为500℃,退火时间为3h;
144.(3)对步骤(2)的产物继续进行冷轧至厚度为0.15mm后进行第二次完全再结晶退火,退火温度为270℃,退火时间为1h;
145.(4)对步骤(3)的产物进行冷轧至0.05mm厚度,得到铝合金箔;
146.(5)如图4所示,将步骤(4)的铝合金箔压制变形,得到高耐腐蚀热交换器翅片。
147.采用制得的高耐腐蚀热交换器翅片进行自钎焊后,翅片中心的电位为-784.7mv,钎焊接头处的电位为-807.2mv,在钎焊接头处与翅片中心的电位的差值为22.5mv;焊后高耐腐蚀热交换器翅片的表面晶粒平均尺寸为679μm;将高耐腐蚀热交换器翅片与aa3003材质的管材进行钎焊,焊后按照astm g85-a3试验后测得的翅片失重比为32%,翅片接头脱落比为32%。
148.实施例7
149.一种高耐腐蚀热交换器翅片的制备方法,包括如下步骤:
150.(1)合金元素按照si:2.7wt%、fe:0.15wt%、mn:1.2wt%、zn:1.6wt%、cu:0.2wt%、sm:0.25wt%进行配料,其余为铝,检测杂质含量控制合格;然后采用铸轧工艺得到厚度为7.3mm的铸轧成品;
151.其中,铸轧工艺的工艺参数为:保温炉和除气箱温度750℃,前箱温度750℃,铸轧区长度62mm,冷却水温20℃,铸轧速度620mm/min;
152.(2)对步骤(1)的产物进行冷轧至厚度为3.6mm后进行第一次完全再结晶退火,退火温度为450℃,退火时间为2h;
153.(3)对步骤(2)的产物继续进行冷轧至厚度为0.12mm后进行第二次完全再结晶退火,退火温度为350℃,退火时间为1h;
154.(4)对步骤(3)的产物进行冷轧至0.07mm厚度,得到铝合金箔;
155.(5)如图4所示,将步骤(4)的铝合金箔压制变形,得到高耐腐蚀热交换器翅片。
156.采用制得的高耐腐蚀热交换器翅片进行自钎焊后,翅片中心的电位为-761.75mv,钎焊接头处的电位为-779.5mv,在钎焊接头处与翅片中心的电位的差值为17.75mv;焊后高耐腐蚀热交换器翅片的表面晶粒平均尺寸为745μm;将高耐腐蚀热交换器翅片与aa3003材质的管材进行钎焊,焊后按照astm g85-a3试验后测得的翅片失重比为30%,翅片接头脱落比为18%。
157.实施例8
158.一种高耐腐蚀热交换器翅片的制备方法,包括如下步骤:
159.(1)合金元素按照si:2.8wt%、fe:0.12wt%、mn:1.7wt%、zn:1.7wt%、cu:0.25wt%、sm:0.2wt%进行配料,其余为铝,检测杂质含量控制合格;然后采用铸轧工艺得到厚度为7.4mm的铸轧成品;
160.其中,铸轧工艺的工艺参数为:保温炉和除气箱温度755℃,前箱温度740℃,铸轧区长度60mm,冷却水温25℃,铸轧速度600mm/min;
161.(2)对步骤(1)的产物进行冷轧至厚度为3.8mm后进行第一次完全再结晶退火,退火温度为480℃,退火时间为1h;
162.(3)对步骤(2)的产物继续进行冷轧至厚度为0.1mm后进行第二次完全再结晶退火,退火温度为360℃,退火时间为2h;
163.(4)对步骤(3)的产物进行冷轧至0.09mm厚度,得到铝合金箔;
164.(5)如图4所示,将步骤(4)的铝合金箔压制变形,得到高耐腐蚀热交换器翅片。
165.采用制得的高耐腐蚀热交换器翅片进行自钎焊后,翅片中心的电位为-753.62mv,钎焊接头处的电位为-781.4mv,在钎焊接头处与翅片中心的电位的差值为27.78mv;焊后高
耐腐蚀热交换器翅片的表面晶粒平均尺寸为834μm;将高耐腐蚀热交换器翅片与aa3003材质的管材进行钎焊,焊后按照astm g85-a3试验后测得的翅片失重比为33%,翅片接头脱落比为18%。
166.实施例9
167.一种高耐腐蚀热交换器翅片的制备方法,包括如下步骤:
168.(1)合金元素按照si:2.6wt%、fe:0.15wt%、mn:1.82wt%、zn:1.5wt%、cu:0.225wt%、sm:0.1wt%进行配料,其余为铝,检测杂质含量控制合格;然后采用铸轧工艺得到厚度为7.5mm的铸轧成品;
169.其中,铸轧工艺的工艺参数为:保温炉和除气箱温度740℃,前箱温度760℃,铸轧区长度65mm,冷却水温28℃,铸轧速度650mm/min;
170.(2)对步骤(1)的产物进行冷轧至厚度为3mm后进行第一次完全再结晶退火,退火温度为400℃,退火时间为1.5h;
171.(3)对步骤(2)的产物继续进行冷轧至厚度为0.1mm后进行第二次完全再结晶退火,退火温度为370℃,退火时间为2h;
172.(4)对步骤(3)的产物进行冷轧至0.1mm厚度,得到铝合金箔;
173.(5)如图4所示,将步骤(4)的铝合金箔压制变形,得到高耐腐蚀热交换器翅片。
174.采用制得的高耐腐蚀热交换器翅片进行自钎焊后,翅片中心的电位为-765.05mv,钎焊接头处的电位为-785.2mv,在钎焊接头处与翅片中心的电位的差值为20.15mv;焊后高耐腐蚀热交换器翅片的表面晶粒平均尺寸为873μm;将高耐腐蚀热交换器翅片与aa3003材质的管材进行钎焊,焊后按照astm g85-a3试验后测得的翅片失重比为28%,翅片接头脱落比为21%。