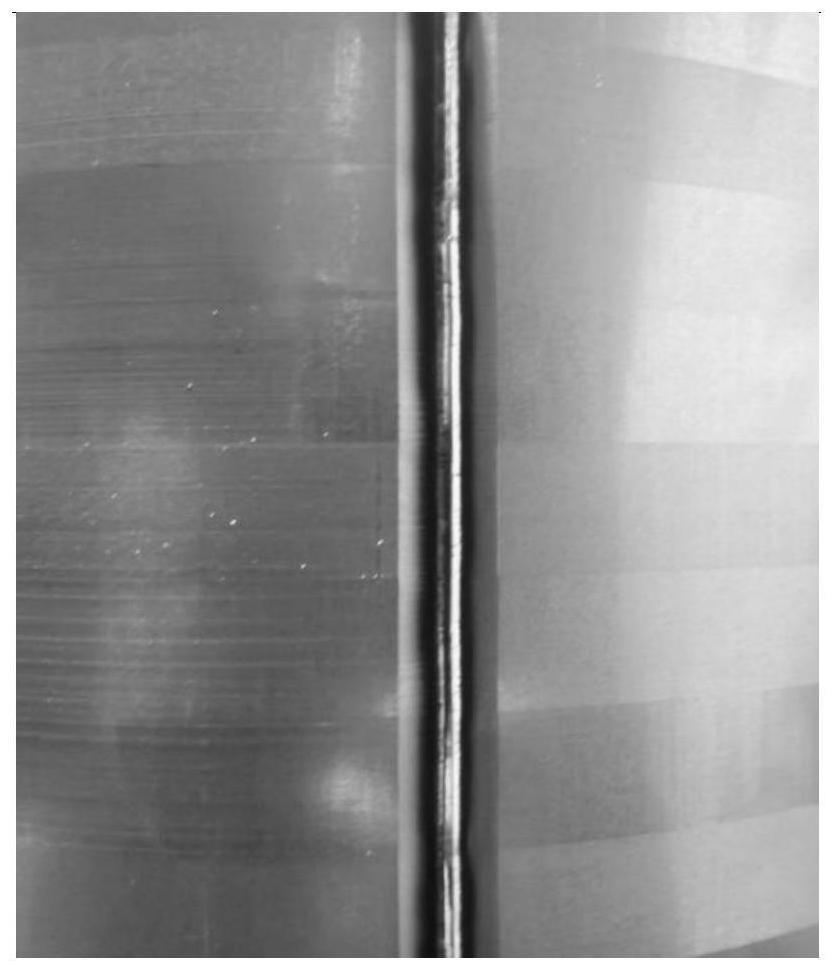
1.本发明属于冶金技术领域,具体涉及一种无取向硅钢生产方法。
背景技术:2.随着电器生产的发展,焊接作为固定硅钢叠片的一种工艺,取代铆接、扣压、灌注填料等传统方法,显示出明显的优点。铁芯叠片的焊接,对某些电机电器产品,不但可以减少工序,易于实现生产机械化、自动化,而且在改善质量方面,也有着显而易见的效果。在新能源汽车驱动电机生产方面,基本都是采用氩弧tig焊或激光焊对硅钢定子叠片铁芯进行固定。
3.电弧在硅钢叠片上燃烧会比较不稳定,主要是因为硅钢片表面上有一层绝缘漆及油膜。漆、油在焊接过程被加热到一定温度时,将会蒸发、分解并燃烧,因而产生大量气体,易造成焊接气泡、断裂,并在焊接区形成一股气浪,干扰保护气体对电弧区的保护,危害电弧燃烧的稳定性,致使电弧飘忽,焊缝成形性不好。涂层越厚或有机物固含量越高,则对焊接影响越大。
4.目前新能源汽车驱动电机用无取向硅钢生产一般只专注于如何提高磁性能、力学性能、涂层性能上,鲜有关注后续用户加工性能的,至于如何改善硅钢叠片焊接性能更是少见提及。
5.cn107723591a、cn106435358a、cn113981329a、cn108570595a、cn111206192a、cn114196887a、cn105950960a、cn107587039a、cn114107799 a等专利主要通过成分、工艺设计优化,以达到降低铁损、提高磁感和强度的目的,满足新能源汽车驱动电机对无取向硅钢磁性能及力学性能的要求。
6.cn109337419a、cn114262547a、cn110240832a、cn107216764a等专利聚焦于开发绝缘性、附着性、耐蚀性、耐热性、冲片性优良的无取向硅钢用无铬环保绝缘涂料,未涉及到硅钢叠片焊接性能的提升和改善。
7.其他关于无取向硅钢的专利也大多以磁性能、力学性能控制为主,未见有专门关注无取向硅钢叠片焊接性能的专利,但随着厚涂层及无铬环保涂层产品越来越广泛的应用,尤其是表面涂覆无铬环保绝缘涂层的新能源汽车驱动电机用无取向硅钢近年来需求成倍激增,现有新能源汽车驱动电机用无铬环保涂层无取向硅钢由于表面涂层较厚、有机物含量较高,导致叠片铁芯焊接性能变差,尤其是氩弧焊接(tig焊)容易出现气泡、断焊、成型性不佳等焊接问题,制约了用户加工效率和产品应用。用户反馈的叠片铁芯焊接气泡、断焊、焊缝歪扭等焊接问题越来越多,影响了用户加工效率及产品质量,制约了环保涂层产品的放量使用,亟需解决。
技术实现要素:8.针对现有产品焊接性能不佳,焊接缺陷较多的问题,本发明目的在于提供一种叠片焊接性能优良的无取向硅钢生产方法,通过关键元素控制及生产工艺优化,达到既保持
产品原有的磁性能和力学性能,还能有效改善产品的涂层附着性能及叠片焊接性能的目的。
9.为达到上述目的,采用技术方案如下:
10.一种叠片焊接性能优良的无取向硅钢生产方法,包括如下步骤:
11.1)采用洁净钢的冶炼方法进行冶炼,并连铸成坯,钢水中各组分及重量百分比含量为:c:≤0.004%,si:1.50%~3.50%,al:0.40~1.5%,mn:0.40~1.50%,p:≤0.050%,s:≤0.0025%,n:≤0.0025%,sb或sn或sb+sn:≤0.15%,cu:≤0.04%,其余为fe及不可避免的杂质;
12.2)将连铸坯加热至1080~1180℃,保温0.5~1.0h后进行热轧,终轧温度控制在800~900℃,卷取温度在620~670℃;
13.3)经常规常化、酸洗后冷轧至成品厚度;
14.4)冷轧带钢经开卷、焊接后依次连续通过碱喷淋装置、碱刷洗装置、电解清洗装置、高压水喷淋装置、水刷洗装置、热水喷淋装置、气刀装置及热风干燥装置,得到表面清洁干燥的带钢;
15.5)进入卧式连续退火炉,控制一段均热温度750~950℃,均热时间为15~30s,退火气氛为h2和n2混合气或全n2增湿气氛,h2比例控制≤40%,露点控制在-10~60℃,对基板表面做改性处理,改性后的基板表面覆盖有氧化膜层,其平均厚度范围为0.03~0.5μm;控制二段均热温度900~1000℃,均热时间为20~45s,退火气氛为h2和n2混合气或全n2干式气氛,h2比例控制≤50%,进行再结晶退火;
16.6)采用两辊或三辊涂机进行辊涂,涂层干膜厚度控制在0.3~4.0μm/面,且单面干膜厚度最大值h与带钢成品厚度d满足以下关系式:h≤d/150;
17.7)烘烤固化。
18.按上述方案,步骤2中热轧板厚度控制在1.8~2.5mm,凸度控制≤40μm。
19.按上述方案,步骤3中冷轧板表面粗糙度控制在0.4~1.0μm,同板差控制≤7μm。
20.按上述方案,步骤4中碱喷淋及碱刷洗的碱液为温度50~80℃的氢氧化钠溶液,氢氧化钠重量百分比含量为15~30%;电解液温度控制在50~70℃,通过带钢的电流强度控制在2000~3000a;水刷洗及水漂洗的水温在55~85℃。
21.按上述方案,步骤6涂敷时的带钢温度≤40℃,涂液温度≤25℃。
22.按上述方案,步骤6所用涂液为不含铬环保涂液,且有机树脂含量≤35wt%。
23.按上述方案,步骤7中烘烤炉温度350~650℃,钢板温度200~350℃,烘烤时间20~110s。
24.相对于现有技术,本发明有益效果如下:
25.新能源汽车驱动电机用无取向硅钢,特别是高效高牌号产品,往往添加sb或sn等晶界偏聚元素,以改善组织织构,提高磁性能,但过量添加一方面容易造成冲压断面发生晶间氧化,另一方面杂质元素在晶界偏聚会降低基材表面自由能,基材对涂液的亲和力因此降低,涂层附着性和稳定性变差,最终导致焊接性能变差。本发明控制sb或sn或sb+sn:≤0.15%。
26.热轧工序的关键点是控制热轧板凸度≤40μm,以利于后续冷轧板型及同板差控制。
27.提高冷轧板表面粗糙度,可以有效增加铁芯叠片之间的空隙,有利于焊接时涂层受热分解、气化所产生的气体能够快速的从焊道周边区域释放到大气中,避免过多的气体进入焊道熔池形成焊接气泡,或使熔池沸腾、流动性过大,导致焊道发生流挂现象,焊缝不连续、歪扭,但粗糙度越高,则冷轧变形抗力也越大,增加轧制难度,本发明冷轧板表面粗糙度控制在0.4~1.0μm;控制同板差是为了减小叠片铁芯各个方向的高度差,叠片铁芯焊接完成后释放叠压力时,叠片之间会产生反弹应力,如果各方向叠片高度不一致,则可能存在局部反弹应力过大,当应力大于焊接强度时,焊缝容易断裂,结合轧机能力,本发明同板差控制≤7μm。
28.表面除油脱脂最终目的是为了得到表面清洁干燥的带钢,提高涂层均匀性和附着性,减小涂层对焊接性能的不利影响。
29.在涂层工序前对基板作表面改性处理,可进一步有效提高基板表面粗糙度,增加的表面凹凸点起到表面毛化效果,可提高涂层与基板间的界面结合力,利于涂层附着性;另外,在厚涂层烘烤成膜过程中,无机氧化膜可将基板-涂层界面的热量部分反射回涂层本体,提高厚涂层在界面处的交联固化程度;进一步的有益效果是可以减少涂液中有机树脂的添加,从而减小对焊接性能的影响。本发明控制改性后的基板表面氧化膜层平均厚度范围为0.03~0.5μm,氧化膜厚度过薄,则效果不明显,且容易导致膜层不连续,涂层性能的均匀性会受到影响;氧化膜过厚,则对基板的磁性能劣化到不可接受,同时硬脆膜层非常不利于后续的剪切和冲压。
30.在半无机硅钢涂层液中添加适量树脂能有效的改善涂层对硅钢基体的附着性,但另一方面树脂容易受热分解,尤其是焊接时的高热会导致焊道周边涂层中的树脂发生热分解和气化,生成co,co在熔池中被分解,变为溶解c和o,熔池冷却凝固时重新生成co,如果焊接速度过快气体会冲破熔池,在释放到大气之前熔池便凝固,从而形成焊接气泡;如果热分解产生的气体过多,还会使熔池沸腾,熔液流动性过大,并在焊接区形成一股气浪,干扰保护气体对电弧区的保护,危害电弧燃烧的稳定性,致使电弧飘忽,易造成焊道歪扭,成形性不好。同时,树脂含量提高后,也就降低了无机盐的含量,使得无机盐量在烧结固化时不足以形成完整的三维网状结构的致密坚固的玻璃态膜层,使得涂层耐蚀性和耐热性能下降。因此涂液中的树脂含量应控制在35%以内。
31.由于有机树脂都是热固化性树脂,因此应对涂敷时的带钢温度和涂液温度加以控制,否则会发生热固化反应,大大削减涂液对带钢的亲和力,不利于以后的成膜反应和涂膜质量,本发明控制涂敷时的带钢温度≤40℃,涂液配制及涂敷时温度≤25℃。
32.涂层越厚,一方面焊接时的树脂分解和气化更多,更容易造成焊接气泡;另一方面由于硅钢叠片焊接时均会施加一定的叠压力,涂层越厚,则焊接完成后叠压力释放时硅钢叠片之间的反弹应力更大,更容易造成焊道断裂。因此在满足绝缘、耐蚀和冲压性能要求的前提下,涂层应尽可能薄,本发明涂层干膜厚度控制在0.3~4.0μm/面。同时,硅钢片厚度越小,则叠成同等高度的铁芯需要的硅钢片数越多,单位体积内的涂层含量也越高,对焊接不利,因此,为了获得良好的焊接性能,单面干膜厚度最大值h与带钢成品厚度d应满足以下关系式:h≤d/150。
33.环保绝缘涂层(以磷酸盐系涂层为例)的烧结固化工艺与含铬涂层有较大差异,涂层的主要成膜物al(h2po4)3是p-o四面体结构,在高温下脱水形成三聚磷酸铝及其水合物,
在高温下,进一步发生脱水缩合反应,通过共用顶角氧原子生成偏磷酸铝或聚磷酸铝,在更高的温度下,进一步缩合成坚固致密的聚偏磷酸铝玻璃膜层。磷酸盐系无取向硅钢涂层开始固化的温度为220℃左右,完全固化温度必须达到260℃,同时固化温度应当控制在350℃以下,不能超过400℃,否则会造成有机树脂的完全分解。因此要对烘烤温度及时间进行严格控制,烘烤温度过低或时间过短,则固化不完全,涂层致密性差、发粘、吸水性大,耐蚀性得不到充分发挥,稳定性也不佳,进而影响叠片焊接性能;如果烘烤温度过高或时间过长,则涂层可能过固化,发生氧化分解,完整性被破坏,附着力及耐蚀性下降。
附图说明
34.图1:实施例1所得无取向硅钢叠片铁芯焊接质量实物图。
35.图2:对比例2所得无取向硅钢叠片铁芯焊接质量实物图。
36.图3:对比例3所得无取向硅钢叠片铁芯焊接质量实物图。
37.图4:对比例7所得无取向硅钢叠片铁芯焊接质量实物图。
38.(请将附图中的情形与实施例或对比例产品建立对应的关系。)
具体实施方式
39.以下实施例进一步阐释本发明的技术方案,但不作为对本发明保护范围的限制。
40.具体实施方式提供了一种叠片焊接性能优良的无取向硅钢生产方法:
41.1)采用洁净钢的冶炼方法进行冶炼,并连铸成坯,钢水中各组分及重量百分比含量为:c:≤0.004%,si:1.50%~3.50%,al:0.40~1.5%,mn:0.40~1.50%,p:≤0.050%,s:≤0.0025%,n:≤0.0025%,sb或sn或sb+sn:≤0.15%,cu:≤0.04%,其余为fe及不可避免的杂质;
42.2)将连铸坯加热至1080~1180℃,保温0.5~1.0h后进行热轧,终轧温度控制在800~900℃,卷取温度在620~670℃,热轧板厚度控制在1.8~2.5mm,凸度控制≤40μm;
43.3)经常规常化、酸洗后冷轧至成品厚度,冷轧板表面粗糙度控制在0.4~1.0μm,同板差控制≤7μm;
44.4)表面除油脱脂,冷轧带钢经开卷、焊接后依次连续通过碱喷淋装置、碱刷洗装置、电解清洗装置、高压水喷淋装置、水刷洗装置、热水喷淋装置、气刀装置及热风干燥装置,得到表面清洁干燥的带钢;所述碱喷淋及碱刷洗的碱液为温度50~80℃的氢氧化钠溶液,氢氧化钠重量百分比含量为15~30%;电解液温度控制在50~70℃,通过带钢的电流强度控制在2000~3000a;水刷洗及水漂洗的水温在55~85℃。
45.5)连续退火,采用卧式连续退火炉,控制一段均热温度750~950℃,均热时间为15~30s,退火气氛为h2和n2混合气或全n2增湿气氛,h2比例控制≤40%,露点控制在-10~60℃,对基板表面做改性处理,改性后的基板表面覆盖有氧化膜层,其平均厚度范围为0.03~0.5μm;控制二段均热温度900~1000℃,均热时间为20~45s,退火气氛为h2和n2混合气或全n2干式气氛,h2比例控制≤50%,进行再结晶退火;
46.6)涂层,涂液为不含铬环保涂液,且有机树脂含量按质量百分比算≤35%,采用两辊或三辊涂机进行辊涂,涂敷时的带钢温度确保≤40℃,涂液配制及涂敷时温度≤25℃,涂层干膜厚度控制在0.3~4.0μm/面,且单面干膜厚度最大值h与带钢成品厚度d满足以下关
系式:h≤d/150;
47.7)烘烤固化,烘烤炉温度350~650℃,钢板温度200~350℃,烘烤时间20~110s。
48.实施例1-6叠片焊接性能优良的无取向硅钢生产方法中主要参数具体取值见表1。对比例1-9的生产步骤与实施例相同,主要参数具体取值见表1。
49.表1
[0050][0051]
对实施例1~6及对比例1~9生产的硅钢带的涂层性能及焊接性能进行检测,结果见表2。其中涂层附着性测试条件为:gb/t 2522-2017,弯曲直径10mm;叠片铁芯焊接性测试条件:钨极氩气保护焊(tig),电流值100a,焊接速度400mm/min,氩气流量15l/min,叠压力100kg/cm2。
[0052]
表2
[0053]
[0054][0055]
综合表1、2可以看出,采用本发明提供的方法生产的无取向硅钢涂层附着性、外观质量优良,叠片铁芯焊接性能良好,无明显焊接缺陷,参照附图1所示;对比例1由于添加了过量的晶界偏聚元素,冲压断面容易锈蚀,同时涂层附着性不佳,冲压时涂层容易剥落粘附在在冲压断面处,进而造成焊接气泡和断焊缺陷;对比例2由于热轧凸度控制不佳,造成冷轧同板差过大,铁芯叠压焊接后释放叠压力时焊道断裂,参照附图2所示;对比例3冷轧粗糙度较小,不利于叠片焊接时涂层热分解产生的气体释放到大气中,容易造成焊接气泡缺陷,参照附图3所示;对比例4有机树脂含量过高,焊接时涂层热分解产生的气体较多,焊道熔池沸腾,熔液流动性过大,容易造成焊接气泡和焊道歪扭缺陷;对比例5、6由于涂覆时带钢温度或涂液温度过高,有机树脂发生热固化反应,削减了涂液对带钢的亲和力,成膜反应和涂膜质量不佳,容易造成断焊缺陷;对比例7涂层干膜过厚,焊接时涂层热分解产生的气体较多,焊道熔池沸腾,熔液流动性过大,造成焊接气泡、焊道歪扭、断焊缺陷,参照附图4所示;对比例8涂层烘烤温度过低,固化不完全,涂层致密性差、发粘发涩、吸水性大,容易产生焊接气泡、焊道歪扭缺陷;对比例9涂层烘烤时间过长,涂层过固化,发生氧化分解,完整性被破坏,附着性下降,容易产生断焊缺陷。