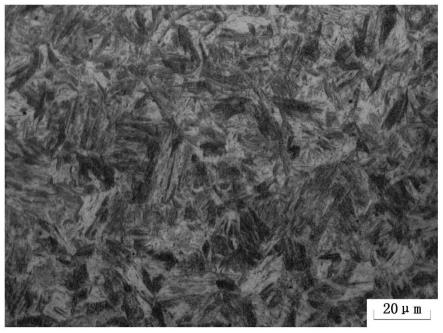
1.本发明属于合金钢领域,更具体地说,涉及一种高强韧高接触疲劳大功率风电偏航轴承圈用钢、轴承圈及生产工艺。
背景技术:[0002][0003]
风电大型化导致风电关键部件轴承的尺寸增加,据调研,1.5mw风电偏航轴承圈外径约 2.1m,而6mw风电偏航轴承圈外径达4.5米,外径扩大2.1倍。另外轴承尺寸增大的同时轴承圈的壁厚增加,导致轴承圈截面性能的一致性不好,因此大功率风电轴承圈对强韧性、均匀性的要求均增加。jb/t 10705也指出“可采用性能相当或更优的材料”制造风电偏航轴承圈。我国海洋风电发展迅速,但目前普遍低于6mw,主要由于关键装备材料不能完全自给。因此开发大功率海洋风电偏航轴承圈用钢已十分迫切。
[0004]
专利cn 101230441a指出用42crmovnb钢制造风电偏航、变桨轴承圈,材料在-40℃v 型冲击功≥91j,抗拉强度≥835mpa。但该专利并未阐述该钢应用于风电轴承圈的功率,由性能值推断只可应用于3mw以下风电机组,材料的性能未明确是轴承圈实物解剖值还是采用小试样测试值。
[0005]
专利cn 104178695a公开了采用中碳硼微合金钢制造风电轴承套圈,经热处理在轴承圈上抗拉强度≥1090mpa,-20℃v型冲击功≥29j。该发明的材料整体强韧性不高,实施热处理淬火保温时间为50-130min,所生产的轴承圈厚度较薄,不能满足大功率风电轴承圈厚壁性能的需要。其并未对海洋风电轴承的疲劳性能等进行测试评价,对材料的应用支持不足。
技术实现要素:[0006]
1.要解决的问题
[0007]
针对现有大尺寸的风电轴承圈强韧性和抗接触疲劳性能差的问题,本发明提供一种高强韧高接触疲劳大功率风电偏航轴承圈用钢、轴承圈及生产工艺,制得的轴承圈强韧性和抗接触疲劳性能高。
[0008]
2.技术方案
[0009]
为了解决上述问题,本发明所采用的技术方案如下:
[0010]
本发明公开了一种高强韧高接触疲劳大功率风电偏航轴承圈用钢,按重量百分比含有: c 0.47%~0.57%、si 0.40%~0.70%、mn 1.30%~1.50%、cr 0.50%~0.70%、mo 0.35%~ 0.45%、ni 0.25%~0.35%、cu 0.030%~0.050%、v 0.035%~0.075%、ti 0.0040%~ 0.0060%、al 0.015%~0.025%、p≤0.015%、s≤0.010%、n 0.0060%~0.0120%、b 0.0020%~ 0.0040%、o≤0.0040%,其余为fe和其它不可避免的杂质。化学成分配比应符合:
[0011]
1)13.0≤(0.54
×
c%)
×
(1+3.34
×
mn%)
×
(1+0.7
×
si%)
×
(1.2+0.36
×
cu%)
×
(1+0.37
×
ni%)
×
[0012]
(1+2.61
×
cr%)
×
(1+3
×
mo%)
×
(1+0.6
×
v%)
×
(1+ti%+n%)≤19.0;
[0013]
2)0.55%≤c%+(mn%+10
×
n%+15
×
b%)/6-(cr%+mo%+v%+ti%)/5+(ni%+cu%)/15
[0014]
≤0.62%。
[0015]
热处理工艺参数应符合:
[0016]
1)正火,s-t1/20≤t1≤s-t1/80,其中,t1(℃)为正火加热温度,为1000~1100℃,t
1 (min)为保温时间,s(mm)为轴承圈壁厚;
[0017]
2)调质:淬火,s-t2/10≤t2≤s-t2/50,其中,t2(℃)为淬火加热温度,为800~900 ℃,t2(min)为淬火保温时间,s(mm)为轴承圈壁厚;
[0018]
回火,1.5
×
s-t3/10≤t3≤1.5
×
s-t3/50,其中,t3(℃)为正火加热温度,为600~700 ℃,t3(min)为保温时间,s(mm)为轴承圈壁厚。
[0019]
本发明提供了该钢的热处理方法,制得的钢具有优秀的强韧性和接触疲劳性能,适用于制造大功率风电用偏航轴承(轴圈壁厚≥300mm)。本发明还公开了利用该钢生产轴承圈的工艺。
[0020]
c:c是钢中最低廉的强化元素,每提高0.1%的固溶c,可使强度提高约450mpa,c与钢中的合金元素形成析出相,起到析出强化作用。c能够显著提高淬透性,使大壁厚周期圈心部获得马氏体组织。但随着其含量增大,塑性和韧性降低,故c含量控制在0.47%~ 0.57%。
[0021]
si:si是钢中有效的固溶强化元素,提高钢的强硬度,si在炼钢时能够起到脱氧作用,是常用的脱氧剂。但si易偏聚有奥氏体晶界,降低晶界结合力,引发脆性。另外si易引起钢中元素偏析。因此,si含量控制在0.40%~0.70%。
[0022]
mn:mn能够起到固溶强化作用,固溶强化能力弱于si,mn是奥氏体稳定化元素能显著提高钢的淬透性,还能够减少钢的脱碳,mn与s结合能够防止s引起的热脆性。但过量的mn会降低钢的塑性。所以,mn含量控制在1.30%~1.50%。
[0023]
cr:cr是碳化物形成元素,cr能够使钢的淬透性和强度均提高,但易引起回火脆性。 cr能够提高钢的抗氧化性能,增加耐蚀性,但cr含量过高时将增加裂纹敏感性。应将cr含量控制在0.50%~0.70%。
[0024]
mo:mo主要提高钢的淬透性和耐热性,固溶于基体的mo能够使钢的组织在回火过程中保持较高的稳定性,且能有效降低p、s和as等杂质元素在晶界处偏聚,从而提高钢的韧性,降低回火脆性。mo能降低m7c3的稳定性,当mo含量较高时将形成针状mo2c,将导致基体mo含量减少。mo能够通过固溶强化和沉淀强化的共同作用提高钢的强度,也能通过改变碳化物的析出来改变钢的韧性。故mo控制在0.35%~0.45%。
[0025]
ni:ni能与fe生成无限互溶的固溶体,是奥氏体稳定化元素,具有扩大相区的作用,增加过冷奥氏体的稳定性,使c曲线右移,提高钢的淬透性。ni能够细化马氏体板条宽度,提高强度。ni能显著降低钢的韧脆转变温度,提高低温韧性。但ni元素是贵金属元素,过量加入导致成本过高。将ni含量控制在0.25%~0.35%。
[0026]
v:v是强c、n化合物形成元素,v(c、n)形成细小弥散,且与基体保持共格关系,能够
起到强化和细化组织的作用。v含量控制在0.035%~0.075%。
[0027]
ti:ti在钢中作用广泛,ti可以作为脱氧剂进行脱氧,ti与c以及n能够形成碳氮化合物,在钢中析出,起到析出强化作用,还可以钉扎晶界阻碍晶粒长大。ti含量控制在 0.0040%~0.0060%。
[0028]
cu:cu能扩大奥氏体相区,cu单质作为第二相能显著提升强度,提升组织回火稳定性和强度。但cu过高将导致cu脆。因此cu含量控制在0.030%~0.050%。
[0029]
al:al是炼钢的主要脱氧剂,al与n结合形成细小弥散分布的aln,且与基体保持共格关系,能够起到强化和细化组织的作用,能够使疲劳裂纹萌生和扩展抗力增加,从而提高钢的持久强度。al含量控制在0.015%~0.035%。
[0030]
b:b是原子尺寸较小的元素,在钢中易与碳元素的晶格发生交互作用,使钢的晶格发生畸变从而提高钢的马氏体获得能力,添加b能够使大尺寸风电轴承心部的强韧性及疲劳性能得到提升。但b含量添加过多会导致b在界面偏聚(晶界、相界等),降低界面结合力导致脆性断裂。故限制b含量在0.0020-0.0040%。
[0031]
o和n:t.o在钢中形成氧化物夹杂,控制t.o≤0.0040%;n在钢中能形成氮化物,形成细小析出相细化组织,又能析出fe4n,扩散速度慢,导致钢产生时效性,降低加工性能,因此将n控制在0.0060%~0.0120%。
[0032]
大功率风电偏航轴承尺寸大,需保证足够的强韧性。通过合金元素的添加能够有效提高淬透性从而提高强韧性。
[0033]
本发明通过加入微合金v和ti,并结合b和n,共同作用提高钢的强度及韧性。ti元素是较强的碳氮化合物元素,能够钉扎晶界细化晶粒,提高强韧性,ti形成的碳氮化合物具有较为规范的立方体结构,与钢的基体形成半共格或共格结构,结合力好,融合度高,有利于提高钢的强韧性,但ti的碳氮化合物硬度高,虽然有利于提高材料的耐磨性,但存在硬质物脱落的风险,降低了接触疲劳性能。为发挥ti的有利作用并消除ti的有害作用,一方面对ti的含量进行限制,另一方面通过热处理工艺调控ti化物的尺寸,使ti化物的尺寸细小,从而避免大颗粒硬质相,降低对接触疲劳性能的不利影响。其主要作用机理是,v和ti能够与c和 n形成碳氮化合物,形成的碳氮化合物细小弥散分布在钢中能够增加位错通过阻力,使韧性提高,同时碳氮化物能够钉扎晶界阻碍晶界迁移,细化晶粒,提高强韧性及疲劳性能。其次,b元素的原子尺寸小且与钢中的碳元素的质量分数、电子结构类似,在钢中极易与c形成交互作用引起晶格改变,提高钢得到马氏体组织的能力,从而提高大尺寸轴承心部的韧性,因此通过限定n和b的含量,将n+b总含量在0.0080-0.016%之间,保证其与v和ti的结合,以促进元素有益作用的协同发挥,综合提高钢的强韧性及疲劳性能。
[0034]
通过研究,在合金元素中mn提高淬透性及强度最有效,系数为3.34;mo通过提高回火稳定性及与mn的交互作用对淬透性及强度贡献也较大,系数为3.0;cr是主要的置换固溶元素,和碳化物形成元素对强度的贡献系数为2.16;ni和cu在钢中不形成碳化物,通过固溶强化改变晶格形态从而对钢的淬透性及强度提高,系数分别为0.37和0.36;c为非金属元素,是钢中最主要的间隙固溶强化元素,对强度和韧性都有影响,故系数为0.54;si是非金属元素,也是钢中主要的固溶强化元素,对钢的性能贡献为0.70。由于钢的强度与塑性和韧性具有反比例关系,即强度高时会导致塑性及韧性降低,为保证钢的综合性能不能一味提高强度。令钢中的强化因素用a表示,则13.0≤a≤19.0,
[0035]
a=(0.54
×
c%)
×
(1+3.34
×
mn%)
×
(1+0.7
×
si%)
×
(1.2+0.36
×
cu%)
×
(1+0.37
×
ni%)
×
(1+2.61
×
cr%)
ꢀ×
(1+3
×
mo%)
×
(1+0.6
×
v%)
×
(1+ti%+n%)。
[0036]
轴承在服役过程中需要较好的接触疲劳性能,因此需对c、mn、cr、mo、ni、cu、v 的配比进行限定。由于c、mn、n、b能较显著提高钢浅层硬度、提高耐磨性从而提高接触疲劳性能;cr、mo、v能够与钢中的c、n形成第二相,第二相在钢中虽然能增加强度,但仍然与钢的基体不同,若尺寸较大可形成接触疲劳裂纹源,故对接触疲劳不利;ni、cu通过固溶强化与基体实现原子尺度结合对接触疲劳性能有利,令钢中的接触疲劳因素用y表示,则0.55%≤y≤0.62%,
[0037]
y=c%+(mn%+10
×
n%+15
×
b%)/6-(cr%+mo%+v%+ti%)/5+(ni%+cu%)/15。
[0038]
本发明还公开了上述偏航轴承圈用钢及偏航轴承圈的生产工艺:电弧炉或转炉冶炼
→
lf炉精炼
→
rh或vd真空脱气
→
φ380mm~φ700mm圆坯连铸
→
圆坯加热
→
锻造
→
冲孔
→
辗环(半成品)
→
热处理
→
机加工
→
探伤
→
包装入库。
[0039]
所述偏航轴承圈采用正火+调质热处理,热处理工艺为:
[0040]
正火:辗环后的偏航轴承圈半成品入炉温度≤600℃,正火加热温度(t1,℃)为 1000~1100℃,正火保温时间(t1,min)由轴承圈壁厚(s,mm)和正火加热温度(t1,℃)决定,满足s-t1/20≤t1≤s-t1/80,水冷。
[0041]
调质:淬火加热温度(t2,℃)为800~900℃,淬火保温时间(t2,min)由轴承圈壁厚(s,mm)和淬火加热温度(t2,℃)决定,满足s-t2/10≤t2≤s-t2/50,水冷;回火温度 (t3,℃)600~700℃,回火保温时间(t3,min)由轴承圈壁厚(s,mm)和回火温度 (t3,℃)决定,满足1.5
×
s-t3/10≤t3≤1.5
×
s-t3/50,水冷。
[0042]
奥氏体相变点受成分影响,由奥氏体相变点确定正火温度和调质温度,由所需要的析出相种类、含量及尺寸选择回火温度。
[0043]
本发明将正火加热温度控制在900-1000℃,保证轴承圈在此温度下完全奥氏体化,同时控制加热温度不高于1000℃,保证钢在锻造过程中析出第二相的尺寸不过于粗大,从而有助于后续产品韧性提高,正火后可以为后续调质做组织准备。
[0044]
调质处理选择加热温度为800-900℃,一方面保证温度达到奥氏体化温度以上,使钢在正火基础上发生重结晶,晶粒进一步细化;另一方面确保在正火中生成的mx型析出相的尺寸在调质过程中不粗大,从而有利于提高强韧性及疲劳性能。采用600-700℃的回火温度,保证析出相种类的同时控制析出相尺寸,使钢中的主要析出相为m
23
c6和mx型,提高韧性及疲劳性能。
[0045]
制得的轴承圈1/2壁厚(壁厚≥300mm)处抗拉强度≥950mpa、屈服强度≥850mpa、-40 ℃kv2≥120j;2000mpa接触应力作用下,接触疲劳寿命≥110万次,满足大功率风电服役 20年需要。
[0046]
3.有益效果
[0047]
相比于现有技术,本发明的有益效果为:
[0048]
本发明的一种高强韧高接触疲劳大功率风电偏航轴承圈用钢强韧性和抗接触疲劳性能好,制得的轴承圈1/2壁厚(壁厚≥300mm)处抗拉强度≥950mpa、屈服强度≥850mpa、-40 ℃kv2≥120j;在2000mpa接触应力作用下,接触疲劳寿命≥110万次,满足大功
率风电服役20年需要。
附图说明
[0049]
以下将结合附图和实施例来对本发明的技术方案作进一步的详细描述,但是应当知道,这些附图仅是为解释目的而设计的,因此不作为本发明范围的限定。此外,除非特别指出,这些附图仅意在概念性地说明此处描述的结构构造,而不必要依比例进行绘制。
[0050]
图1为本发明实施例2淬火后轴承圈表层12.5mm处组织图;
[0051]
图2为本发明对比例2淬火后轴承圈表层12.5mm处组织图;
[0052]
图3为本发明实施例2轴承圈1/2壁厚处微观结构图;
[0053]
图4为本发明对比例2轴承圈1/2壁厚处微观结构图;
[0054]
图5为本发明实施例2轴承圈1/2厚度处透射分析图;
[0055]
图6为本发明对比例2轴承圈1/2厚度处透射分析图。
具体实施方式
[0056]
下文对本发明的示例性实施例的详细描述参考了附图,该附图形成描述的一部分,在该附图中作为示例示出了本发明可实施的示例性实施例。尽管这些示例性实施例被充分详细地描述以使得本领域技术人员能够实施本发明,但应当理解可实现其他实施例且可在不脱离本发明的精神和范围的情况下对本发明作各种改变。下文对本发明的实施例的更详细的描述并不用于限制所要求的本发明的范围,而仅仅为了进行举例说明且不限制对本发明的特点和特征的描述,以提出执行本发明的最佳方式,并足以使得本领域技术人员能够实施本发明。因此,本发明的范围仅由所附权利要求来限定。
[0057]
本发明公开了一种高强韧高接触疲劳大功率风电偏航轴承圈用钢,按重量百分比含有: c 0.47%~0.57%、si 0.40%~0.70%、mn 1.30%~1.50%、cr 0.50%~0.70%、mo 0.35%~ 0.45%、ni 0.25%~0.35%、cu 0.030%~0.050%、v 0.035%~0.075%、ti 0.0040~0.0060%、 al 0.015%~0.025%、p≤0.015%、s≤0.010%、n 0.0060%~0.0120%、b 0.0020%~0.0040%、 o≤0.0040%。其余为fe和其它不可避免的杂质。化学成分配比应符合:
[0058]
1)13.0≤(0.54
×
c%)
×
(1+3.34
×
mn%)
×
(1+0.7
×
si%)
×
(1.2+0.36
×
cu%)
×
(1+0.37
×
ni%)
×
[0059]
(1+2.61
×
cr%)
×
(1+3
×
mo%)
×
(1+0.6
×
v%)
×
(1+ti%+n%)≤19.0;
[0060]
2)0.55%≤c%+(mn%+10
×
n%+15
×
b%)/6-(cr%+mo%+v%+ti%)/5+(ni%+cu%)/15
[0061]
≤0.62%。
[0062]
热处理工艺参数应符合:
[0063]
1)正火,s-t1/20≤t1≤s-t1/80,其中,t1(℃)为正火加热温度,为1000~1100℃,t
1 (min)为保温时间,s(mm)为轴承圈壁厚;
[0064]
2)调质:淬火,s-t2/10≤t2≤s-t2/50,其中,t2(℃)为淬火加热温度,为800~900 ℃,t2(min)为淬火保温时间,s(mm)为轴承圈壁厚;
[0065]
回火,1.5
×
s-t3/10≤t3≤1.5
×
s-t3/50,其中,t3(℃)为正火加热温度,为600~
700℃,t3(min)为保温时间,s(mm)为轴承圈壁厚。
[0066]
本发明提供了该钢的热处理方法,制得的钢具有优秀的强韧性和接触疲劳性能,适用于制造大功率风电用偏航轴承(轴圈壁厚≥300mm)。本发明还公开了利用该钢生产轴承圈的工艺。
[0067]
本发明采用特定成分的钢种,实施例和对比例的钢种成分见表1。
[0068]
表1本发明实施例化学成分(wt%)
[0069]
钢种实施例1实施例2实施例3对比例1对比例2对比例3c0.490.510.550.540.520.48si0.530.480.550.650.590.49mn1.351.411.461.481.431.32cr0.550.510.630.650.530.59ni0.280.330.310.320.260.31mo0.380.390.420.440.380.41v0.0420.0540.0710.0650.0390.072ti0.00430.00570.00560.00550.00440.0054cu0.0350.0420.0380.0450.0380.049al0.0190.020.0230.0230.0180.021p0.0090.0130.010.0120.0080.007s0.0090.0070.0090.0020.0040.005n0.00620.00760.01050.00840.00970.0114b0.00250.00350.00220.00250.00280.0032o0.00360.00310.00290.00320.00260.0032a值13.1413.918.6920.414.7313.97y值0.560.60.610.60.610.54
[0070]
本发明的钢的生产工艺如下:
[0071]
电炉冶炼:出钢前定氧,出钢过程采用留钢操作,避免下渣;
[0072]
lf炉:将c、si、mn、cr、ni、mo、v、ti、cu等元素调至目标值;
[0073]
真空脱气:纯脱气时间≥15分钟,保证真空处理后[h]含量≤1.5ppm,避免钢中出现白点,引起氢脆现象;
[0074]
连铸:中包钢水目标温度控制在液相线温度以上10~40℃,连铸φ380mm~φ700mm圆坯。
[0075]
轴承圈制造路线:圆坯(直径600及700mm)加热
→
锻造
→
冲孔
→
辗环(半成品)。
[0076]
轴承圈热处理:台车炉加热
→
保温
→
正火
→
淬火
→
回火
→
保温
→
水冷。
[0077]
轴承圈加工路线:轴承圈粗车
→
探伤
→
阀体精车
→
修磨
→
探伤
→
包装入库。
[0078]
性能检测方法如下:
[0079]
组织:在轴承圈延长体上取样,在延长体的表层12.5mm处和1/2厚度(厚度为 300mm)位置内取样进行金相、晶粒尺寸分析。
[0080]
性能:在轴承圈延长体上取样,在延长体的表层12.5mm处和1/2厚度(厚度为 300mm)位置内取样取拉伸、冲击、接触疲劳试样,参照gb/t228、gb/t229、jb/t 10510 进行
力学性能试验。热处理工艺如表2所示,力学性能如表3所示。其中,rm为抗拉强度,r
p0.2
为屈服强度,接触疲劳寿命在2000mpa接触应力作用下测得。
[0081]
表2本发明实施例及对比例的锻造工艺情况列表
[0082][0083]
表3本发明实施例及对比例的疲劳性能检测情况列表
[0084]
[0085][0086]
实施例1~3的钢化学成分组成、生产方法均得到适当控制,其化学成分保证了 13.0≤a≤19.0,0.55%≤y≤0.62%钢的强度、塑性、韧性及接触疲劳性能均较好。对比例1和对比例3中化学组分不合适,对比例3化学成分控制不当,导致材料强度过低,塑韧性不足,热处理工艺不当导致整体性能不理想;对比例2成分设计合理,但是热处理工艺不当,导致材料的强度、韧性不足,且抗接触疲劳性能不足。
[0087]
在合理的组分配比和热处理工艺,本发明的大功率风电偏航轴承圈用钢组织均匀细小,没有出现铁素体,如图1和图2所示,图1为本发明实施例2淬火后轴承圈表层12.5mm处的组织图,为全马氏体,回火后为全索氏体,图2为对比例2淬火后轴承圈表层12.5mm处组织图,存在9%的铁素体,铁素体的存在一方面降低材料的强度,另一方面铁素体与回火索氏体结合力较差,在受到外力时,易在结合界面出行断裂,降低韧性。铁素体作为软质点,在进行接触疲劳实验时,易发生变形,导致软点从而使疲劳在此处产生,降低疲劳性能。
[0088]
图3与图4分别为实施例2和对比例2轴承圈1/2壁厚处微观结构图,对比可知实施例 2在1/2壁厚处的晶粒细小均匀,而对比例2在1/2壁厚处的晶粒存在个别尺寸较大的晶粒,晶粒尺寸不均匀。晶粒尺寸不均匀会导致材料受到外力变形不协调,易在大晶粒处发生断裂,使材料韧性降低。且大晶粒的晶粒周长过大,使界面力结合度降低,在接触疲劳试验过程中在界面处产生实效,降低疲劳性能。
[0089]
图5与图6分别为实施例2和对比例2轴承圈1/2壁厚处透射分析图,对比可知,实施例2轴承圈1/2厚度处析出相细小分布在板条内,对比例2析出相交大分布在板条内及板条间,通过控制成分与工艺可对钢中析出相产生影响,通过工艺控制,使得钢种的析出相细小,避免大尺寸析出相,提高材料的疲劳性能。