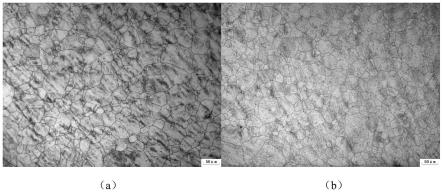
0.030%~ 0.050%、al 0.015%~0.025%、p≤0.015%、s≤0.010%、o≤0.0040%,n≤0.0080%,其余为fe 和其它不可避免的杂质。化学成分配比应符合:
12.1)10.5≤(0.54
×
c%)
×
(1+3.34
×
mn%)
×
(1+0.7
×
si%)
×
(1.2+0.36
×
cu%)
×
(1+0.37
×
ni%)
×
13.(1+2.61
×
cr%)
×
(1+3
×
mo%)
×
(1+0.6
×
v%)
×
(1+0.7nb%)≤13.8;
14.2)0.24%≤c%+(mn%)/6-(cr%+mo%+v%+ti%)/5+(c%u)/15;
15.3)0.60%≤(-3)
×
si%+0.8
×
mn%+1.2
×
mo%+1
×
cu%+2
×
v%+2
×
nb%。
16.热处理工艺参数应符合:
17.1)一次调质的淬火,s-t1/20≤t1≤s-t1/80;一次调质的回火,s-t2/10≤t2≤s-t2/50;
18.2)二次调质的淬火,s-t3/10≤t3≤s-t3/50;二次调质的回火,1.5
×
s-t4/10≤t4≤1.5
×s‑ꢀ
t4/50。
19.本发明提供了该钢的热处理方法,制得的钢具有优秀的强韧性和接触疲劳性能,适用于制造大功率风电用偏航轴承(轴圈壁厚≥240mm)。本发明还公开了利用该钢生产轴承圈的工艺。
20.c:c是钢中最低廉的强化元素,每提高0.1%的固溶c,可使强度提高约450mpa,c 与钢中的合金元素形成析出相,起到析出强化作用。c能够显著提高淬透性,使大壁厚周期圈心部获得马氏体组织。但随着其含量增大,塑性和韧性降低,故c含量控制在0.47%~ 0.57%。
21.si:si是钢中有效的固溶强化元素,提高钢的强硬度,si在炼钢时能够起到脱氧作用,是常用的脱氧剂。但si易偏聚有奥氏体晶界,降低晶界结合力,引发脆性。另外si易引起钢中元素偏析。因此,si含量控制在0.10%~0.30%。
22.mn:mn能够起到固溶强化作用,固溶强化能力弱于si,mn是奥氏体稳定化元素能显著提高钢的淬透性,还能够减少钢的脱碳,mn与s结合能够防止s引起的热脆性。但过量的mn会降低钢的塑性。所以,mn含量控制在0.70%~0.90%。
23.cr:cr是碳化物形成元素,cr能够使钢的淬透性和强度均提高,但易引起回火脆性。cr能够提高钢的抗氧化性能,增加耐蚀性,但cr含量过高时将增加裂纹敏感性。应将cr含量控制在1.30%~1.50%。
24.mo:mo主要提高钢的淬透性和耐热性,固溶于基体的mo能够使钢的组织在回火过程中保持较高的稳定性,且能有效降低p、s和as等杂质元素在晶界处偏聚,从而提高钢的韧性,降低回火脆性。mo能降低m7c3的稳定性,当mo含量较高时将形成针状mo2c,将导致基体mo含量减少。mo能够通过固溶强化和沉淀强化的共同作用提高钢的强度,也能通过改变碳化物的析出来改变钢的韧性。故mo控制在0.30%~0.50%。
25.v:v是强c、n化合物形成元素,v(c、n)形成细小弥散,且与基体保持共格关系,能够起到强化和细化组织的作用。v含量控制在0.035%~0.075%。
26.nb:nb是钢中主要的微合金元素,其在钢中以置换溶质原子存在,nb原子比铁原子尺寸大,易在位错线上偏聚,对位错攀移产生强烈的拖曳作用,从而达到细化奥氏体晶粒的目的,晶粒细化不仅能提高钢材的强韧性,nb少量添加能够稳定细化晶粒,提高强韧性及疲劳性能。nb的碳氮化合物与基体的错配度适中,有利于钢的强化及韧化作用。nb含量过少,
低于0.010%时,所产生的位错拖曳作用极其微小,不能起到提高韧性的作用。nb添加过多会导致碳氮化合物尺寸大,形成大尺寸夹杂从而失去强韧化作用,且nb价格较贵,故 nb的范围可控制在0.010%~0.030%。
27.cu:cu是扩大奥氏体相区,cu单质可以作为第二相显著提升强度,能提升组织回火稳定性和强度。但cu过高将导致cu脆。因此cu含量控制在0.030%~0.050%。
28.al:al是炼钢的主要脱氧剂,al与n结合形成细小弥散分布的aln,且与基体保持共格关系,能够起到强化和细化组织的作用,能够使疲劳裂纹萌生和扩展抗力增加,从而提高钢的持久强度。al含量控制在0.015%~0.035%。
29.o和n:t.o在钢中形成氧化物夹杂,控制t.o≤0.0040%;n在钢中能形成氮化物,形成细小析出相细化组织,又能析出fe4n,扩散速度慢,导致钢产生时效性,降低加工性能,因此将n控制在0.0080%内。
30.大功率风电偏航轴承尺寸大,需保证足够的强韧性。通过合金元素的添加能够有效提高淬透性从而提高强韧性。通过研究在合金元素中mn提高淬透性及强度最为有效,系数为 3.34;mo通过提高回火稳定性及与mn的交互左右对淬透性及强度贡献也较大,系数为 3.0;cr是主要的置换固溶元素和碳化物形成元素对强度的贡献系数为2.16;cu在钢中不形成碳化物,通过固溶强化改变晶格形态从而对钢的淬透性及强度提高,系数分别为0.37和 0.36;c为非金属元素,是钢中最主要的间隙固溶强化元素,对强度和韧性都有影响,故系数为0.54;si是非金属元素,也是钢中主要的固溶强化元素,对钢的性能贡献为0.70。由于钢的强度与塑性和韧性具有反比例关系,即强度高时会导致塑性及韧性降低,为保证钢的综合性能不能一味提高强度。令钢中的强化因素用a表示,则10.5≤a≤13.8,
31.a=(0.54
×
c%)
×
(1+3.34
×
mn%)
×
(1+0.7
×
si%)
×
(1.2+0.36
×
cu%)
×
(1+0.37
×
ni%)
×
(1+2.61
×
cr%)
ꢀ×
(1+3
×
mo%)
×
(1+0.6
×
v%)
×
(1+0.7nb%)。
32.轴承在服役过程中需要较好的接触疲劳性能,因此需对c、mn、cr、mo、cu、v、nb 的配比进行限定。由于c、mn能显著提高钢浅层硬度、提高耐磨性从而提高接触疲劳性能;cr、mo、v、nb能够与钢中的c、n形成第二相,第二相在钢中虽然能增加强度,但仍然与钢的基体不同,若尺寸较大可形成接触疲劳裂纹源,故对接触疲劳不利;cu通过固溶强化与基体实现原子尺度结合对接触疲劳性能有利。但nb在钢中形成的碳氮化合物具有硬度高的特点,且尺寸难以控制,易造成剥离从而降低接触疲劳性能。因此本发明一方面通过控制nb的含量,另一方面通过热处理两次回火调质调控nb碳氮化合物的尺寸,令钢中的接触疲劳因素用y表示,则y≥0.24%,
33.y=c%+(mn%)/6-(cr%+mo%+v%+nb%)/5+(cu%)/15。
34.为获更好的低温韧性,满足轴承在低温环境工作需要。本专利没有添加贵金属ni,通过合金元素及微合金元素合理配比达到低温环境对韧性需求,由于钢中减少了贵金属ni的添加,而ni对低温韧性有利,为了保证钢的低温韧性需对si、mn、cr、mo、cu等元素的配合进行控制。si显著恶化低温韧性,增加回火脆性,故si的系数为(-3)。mn能够显著影响相变过程中的变体选择,增加相变中变体种类,从而提高低温韧性,但mn易发生偏聚,故mn的系数为0.8。mo主要通过提高回火稳定性来提高低温韧性,对低温韧性的贡献有限,故mo的系数为1.2。cu能够提高与钢的基体实现原子程度结合对韧性有利,故系数为1。v、nb通过第二相钉扎位错阻碍受到冲击后裂纹扩展路径,故系数均为2;即 z≥0.60%,
240mm)处抗拉强度≥950mpa、屈服强度≥850mpa、-40℃kv2≥80j,2000mpa接触应力作用下,接触疲劳寿命≥100万次,满足大功率风电服役20年需要。
附图说明
49.以下将结合附图和实施例来对本发明的技术方案作进一步的详细描述,但是应当知道,这些附图仅是为解释目的而设计的,因此不作为本发明范围的限定。此外,除非特别指出,这些附图仅意在概念性地说明此处描述的结构构造,而不必要依比例进行绘制。
50.图1为本发明实施例1制得的轴承圈1/2壁厚处的微观形貌图,(a)一次淬火;b)二次淬火后;
51.图2为本发明对比例2制得的轴承圈1/2壁厚处的微观形貌图,(a)一次淬火;(b)二次淬火后;
52.图3为实施例1制得的轴承圈1/2壁厚处ebsd分析图;
53.图4为对比例2制得的轴承圈1/2壁厚处ebsd分析图。
具体实施方式
54.下文对本发明的示例性实施例的详细描述参考了附图,该附图形成描述的一部分,在该附图中作为示例示出了本发明可实施的示例性实施例。尽管这些示例性实施例被充分详细地描述以使得本领域技术人员能够实施本发明,但应当理解可实现其他实施例且可在不脱离本发明的精神和范围的情况下对本发明作各种改变。下文对本发明的实施例的更详细的描述并不用于限制所要求的本发明的范围,而仅仅为了进行举例说明且不限制对本发明的特点和特征的描述,以提出执行本发明的最佳方式,并足以使得本领域技术人员能够实施本发明。因此,本发明的范围仅由所附权利要求来限定。
55.本发明公开了一种经济性高寿命大功率风电偏航轴承圈用钢,按重量百分比含有:c 0.47%~0.57%、si 0.10%~0.30%、mn 0.70%~0.90%、cr 1.30%~1.50%、mo 0.30%~ 0.50%、cu 0.030%~0.050%、v 0.035%~0.075%、nb 0.010%~0.030%、cu 0.030%~ 0.050%、al 0.015%~0.025%、p≤0.015%、s≤0.010%、o≤0.0040%。其余为fe和其它不可避免的杂质。化学成分配比应符合:
56.1)10.5≤(0.54
×
c%)
×
(1+3.34
×
mn%)
×
(1+0.7
×
si%)
×
(1.2+0.36
×
cu%)
×
(1+0.37
×
ni%)
×
57.(1+2.61
×
cr%)
×
(1+3
×
mo%)
×
(1+0.6
×
v%)
×
(1+0.7nb%)≤13.8;
58.2)0.24%≤c%+(mn%)/6-(cr%+mo%+v%+nb%)/5+(cu%)/15;
59.3)0.60%≤(-3)
×
si%+0.8
×
mn%+1.2
×
mo%+1
×
cu%+2
×
v%+2
×
nb%。
60.热处理工艺参数应符合:
61.1)一次调质的淬火,s-t1/20≤t1≤s-t1/80;一次调质的回火,s-t2/10≤t2≤s-t2/50。
62.2)二次调质的淬火,s-t3/10≤t3≤s-t3/50;二次调质的回火,1.5
×
s-t4/10≤t4≤1.5
×s‑ꢀ
t4/50。
63.本发明提供了该钢的热处理方法,制得的钢具有优秀的强韧性和接触疲劳性能,适用于制造大功率风电用偏航轴承(轴圈壁厚≥240mm)。本发明还公开了利用该钢生产轴
承圈的工艺。
64.本发明采用特定成分的钢种,实施例和对比例的钢种成分见表1。
65.表1本发明实施例化学成分(wt%)
66.钢种实施例1实施例2实施例3对比例1对比例2对比例3c0.490.520.520.540.510.48si0.130.120.250.250.280.19mn0.740.790.720.820.780.76cr1.451.391.341.411.321.42mo0.370.390.480.420.390.42v0.0420.0390.0710.0650.0540.072nb0.0130.0270.0280.0180.0250.025cu0.0350.0380.0380.0450.0420.049al0.0190.020.0230.0230.0180.021p0.0090.0130.010.0120.0080.007s0.0090.0070.0090.0020.0040.005n0.00620.00760.00550.00440.00670.0064o0.00360.00310.00290.00320.00260.0032a值10.9612.1713.7814.9812.6712.34y值0.240.290.260.290.290.22z值0.790.910.640.620.450.79
67.本发明的钢的生产工艺如下:
68.电炉冶炼:出钢前定氧,出钢过程采用留钢操作,避免下渣;
69.lf炉:将c、si、mn、cr、mo、v、nb、cu等元素调至目标值;
70.真空脱气:纯脱气时间≥15分钟,保证真空处理后[h]含量≤1.5ppm,避免钢中出现白点,引起氢脆现象;
[0071]
连铸:中包钢水目标温度控制在液相线温度以上10~40℃,连铸φ380mm~φ700mm圆坯。
[0072]
轴承圈制造路线:圆坯(直径600及700mm)加热
→
锻造
→
冲孔
→
辗环(半成品)。
[0073]
轴承圈热处理:台车炉加热
→
保温
→
正火
→
淬火
→
回火
→
保温
→
水冷。
[0074]
轴承圈加工路线:轴承圈粗车
→
探伤
→
阀体精车
→
修磨
→
探伤
→
包装入库。
[0075]
性能检测方法如下:
[0076]
组织:在轴承圈延长体上取样,在延长体的表层12.5mm处和1/2厚度(厚度为 240mm)位置内取样进行金相、晶粒尺寸分析。
[0077]
表2本发明实施例及对比例的锻造工艺情况列表
[0078][0079]
性能:在轴承圈延长体上取样,在延长体的表层12.5mm处和1/2厚度(厚度为 240mm)位置内取样取拉伸、冲击、接触疲劳试样,参照gb/t228、gb/t229、jb/t 10510 进行力学性能试验。热处理工艺如表2所示,力学性能如表3所示。
[0080]
表3本发明实施例及对比例的疲劳性能检测情况列表
[0081]
[0082][0083]
实施例1~3的钢化学成分组成、生产方法均得到适当控制,其化学成分保证了 17.0≤a≤20.3,0.17%≤y,0.30%≤z钢的强度、塑性、韧性及接触疲劳性能均较好。对比例 1、2是化学组分配比不合适,其中对比例2化学成分控制不当,导致材料强度过低,塑韧性不足,热处理工艺不当导致整体性能不理想;对比例3成分设计合理,但是热处理工艺不当,导致材料的强度、韧性不足,且抗接触疲劳性能不足。
[0084]
图1为实施例1制得的轴承圈1/2壁厚处的微观形貌图,一次淬火后晶粒尺寸约为34微米,经过2次淬火晶粒细化为26.6微米。通过相应的热处理使晶粒细化,晶粒细化后能有效提高材料的强度、低温韧性和疲劳性能。
[0085]
而对比例2中的钢虽然采用了2次调质,但是化学组分和工艺配合不恰当,如图2所示,晶粒并未显著细化,晶粒尺寸达33.9微米,导致性能较差。
[0086]
图3和图4进一步说明了组分及工艺造成性能差距的微观原因。实施例1中的ebsd分析显示,微观组织细小,均匀。而对比例2的微观组织粗大。细小的组织一方面能够使材料在受到外界作用冲击时,裂纹扩展的路径增加、消耗冲击能力,提高低温韧性;另一方面提高材料的内应力及协调变形能力,从而提高材料的疲劳性能。