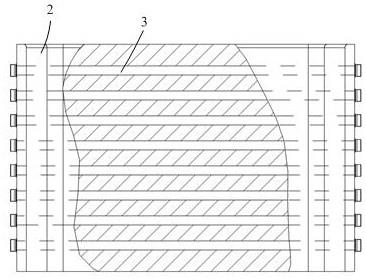
1.本发明总体而言涉及冶金工业领域,具体而言,涉及一种用于铁合金浇铸快速成型的方法。
2.
背景技术:3.目前铁合金或者金属硅的冶炼由液态变为固态的浇铸过程是由钢包将液态铁合金或者金属硅浇注到固定铸铁锭模中,在浇铸前需要在模具上表面喷涂脱模材料,防止高温金属和模具粘连,等待自然冷却和凝固成较大的块状,然后再转运破碎。
4.这种方法铁合金由液态变为固态的过程需要空气自然冷却,需要时间长,占用厂房空间大,高温的液态铁合金会对模具造成灼伤,造成模具的快速损坏。
5.因此,如何实现铁合金快速降温成型,且过程安全可靠,为目前急需解决的技术问题。
6.
技术实现要素:7.本发明的一个主要目的在于克服上述现有技术的至少一种缺陷,提供一种可以安全可靠地快速降温成型的铁合金浇铸成型方法。
8.为实现上述发明目的,本发明采用如下技术方案:根据本发明的一个方面,提供了一种铁合金浇铸成型方法,包括:使用两个以上冷床,其中在第一冷床上,液体铁合金流动过程中变为片状固态,第二冷床入口与第一冷床出口之间具有高度差,从而片状固态铁合金在进入第二冷床时碎裂为多个小片状,小片状铁合金在第二冷床上通过气膜滑动降温;所述冷床均使用两个以上敞口模具,所述两个以上敞口模具阶梯状依次从高至低叠放,上一模具出口端对应下一模具入口端。浇铸铁合金时,从最高的模具入口端浇入,铁合金液在振动和自重作用下沿所述三个以上敞口模具由上至下流动;每一所述模具均包括:座体,所述座体下部为便于放置的安放位,上部为模具体,所述座体设置有液冷结构和振动推送机构;模具体,所述模具体下部连接所述座体,上部为类u型敞口结构,所述敞口结构中间为前后开放的成型平面,两侧为具有倾斜向上的翼部。
9.根据本发明的一实施方式,所述液冷结构包括并排设置的多个通道,所述多个通道中通冷却液,所述多个通道的延伸方向垂直于铁合金液流方向,所述多个通道的数量是6-12个,直径为25-50毫米。
10.根据本发明的一实施方式,第二冷床入口与第一冷床出口之间高度差为400-500毫米。
11.根据本发明的一实施方式,所述第一冷床振动频率为20-30hz,振幅为2-5mm,第二冷床振动频率为10-20hz,振幅为10-20毫米。
12.根据本发明的一实施方式,所述成型平面包括有镍钴合金镀层,所述镀层厚度为1-3毫米。
13.根据本发明的一实施方式,所述模具体的材料为含gr和zr的合金铜。
14.根据本发明的一实施方式,所述gr和zr的含量在0.1-0.8%,并采用基材锻打的加工工艺形成。
15.根据本发明的一实施方式,所述模具数量为6~10个,浇入铁合金液初始温度为1400~1700℃,在第二模具排出时温度降低380-400
°
c,并凝固为固态。
16.根据本发明的一实施方式,所述冷却液为水,流量为500-1200立方/每小时。
17.根据本发明的一实施方式,铁合金浇铸成型后的块状厚度为20-45毫米,各模具安装在固定平台上,并在浇铸时进行振动。
18.由上述技术方案可知,本发明的铁合金浇铸成型方法的优点和积极效果在于:本发明中,采用两个以上冷床,第一冷床上液体铁合金快速降温并凝固,通过冷床落差碎裂固态铁合金,在第二冷床上通过气膜滑送小片固态铁合金进一步降温,模具座体上设置液冷结构,模具体u型敞口结构,因此铁合金液可以在敞口流动中快速降温和成型,并且不会飞溅和泄露,非常安全可靠。
19.附图说明
20.通过结合附图考虑以下对本发明的优选实施例的详细说明,本发明的各种目标、特征和优点将变得更加显而易见。附图仅为本发明的示范性图解,并非一定是按比例绘制。在附图中,同样的附图标记始终表示相同或类似的部件。其中:图1是一示例性实施例中示出的本发明铁合金浇铸成型方法中使用的模具结构示意图。
21.图2是图1中模具的液冷结构示意图。
22.图3是一示例性实施例中示出的本发明铁合金浇铸成型方法中模具布局示意图。
23.图4是一示例性实施例中示出的本发明铁合金浇铸成型方法中使用的设备整体结构示意图。
24.具体实施方式
25.现在将参考附图更全面地描述示例实施方式。然而,示例实施方式能够以多种形式实施,且不应被理解为限于在此阐述的实施方式;相反,提供这些实施方式使得本发明将全面和完整,并将示例实施方式的构思全面地传达给本领域的技术人员。图中相同的附图标记表示相同或类似的结构,因而将省略它们的详细描述。
26.在对本发明的不同示例的下面描述中,参照附图进行,所述附图形成本发明的一部分,并且其中以示例方式显示了可实现本发明的多个方面的不同示例性结构、系统和步骤。应理解,可以使用部件、结构、示例性装置、系统和步骤的其他特定方案,并且可在不偏
离本发明范围的情况下进行结构和功能性修改。而且,虽然本说明书中可使用术语“顶部”、“底部”、“前部”、“后部”、“侧部”等来描述本发明的不同示例性特征和元件,但是这些术语用于本文中仅出于方便,例如根据附图中所述的示例的方向。本说明书中的任何内容都不应理解为需要结构的特定三维方向才落入本发明的范围内。
27.图1是一示例性实施例中示出的本发明铁合金浇铸成型方法中使用的模具结构示意图。
28.图2是图1中模具的液冷结构示意图。
29.图3是一示例性实施例中示出的本发明铁合金浇铸成型方法中模具布局示意图。
30.图4是一示例性实施例中示出的本发明铁合金浇铸成型方法中使用的设备整体结构示意图。
31.如图1至图4所示,本实施例的铁合金浇铸成型方法,包括:使用两个以上冷床,其中在第一冷床上,液体铁合金流动过程中变为片状固态,第二冷床入口与第一冷床出口之间具有高度差,从而片状固态铁合金在进入第二冷床时碎裂为多个小片状,小片状铁合金在第二冷床上通过气膜滑动降温。冷床均使用两个以上敞口模具,两个以上敞口模具阶梯状依次从高至低叠放,上一模具出口端对应下一模具入口端,形成阶梯状,并具有一定落差,在滑落过程中可以起到降温和折断作用。其中第二个模具长度较长,该模具上铁合金液由液态向固态转化,为维持铁合金成型厚度达到30-40毫米,后部固态起到止挡作用。该实施例中,每一模具均包括:座体2,座体2下部为便于放置的安放位,上部为模具体1,座体2设置有液冷结构3,座体2可以和模具体1一体成型。座体2上还设置有振动推送机构(图中未示出),振动推送机构使得座体产生振动,从而使得其上的铁合金液在自重和振动共同作用下快速流动。
32.模具体1,模具体1下部连接座体2,上部为类u型敞口结构,敞口结构中间为前后开放的成型平面11,两侧为具有倾斜向上的翼部12、13。
33.本实施例中,液冷结构3包括并排设置的多个通道,多个通道中通冷却液,多个通道的延伸方向垂直于铁合金液流方向。
34.本实施例中,多个通道的数量是6-12个,直径为25-50毫米,为了防止冷却液联结过渡接头和模具脱落造成冷却液的外漏,过渡接头和模具采用焊接的结构。具体地来说,通道可以是管道,数量可以是8个、10个,直径是30毫米、40毫米。
35.本实施例中,翼部12、13与成型平面11之间具有圆角。
36.本实施例中,第二冷床入口与第一冷床出口之间高度差为400-500毫米,以通过自重作用将片状固态铁合金碎裂为多个小片状固态。
37.本实施例中,第一冷床振动频率为20-30hz,振幅为2-5mm,第二冷床振动频率为10-20hz,振幅为10-20毫米。
38.本实施例中,为了防止温度为1500-1600
°
c液态铁合金材料灼伤模具表面,或者浇注时对表面造成冲刷而损坏模具表面,模具表面采用耐高温的镍钴合金镀层设计,成型平面包括有镍钴合金镀层4,镀层4厚度为1-3毫米。
39.本实施例中,通过改变模具的材质来提高模具的热传导效率和强度和防止模具开裂,模具体的材料为含gr和zr的合金铜。
40.本实施例中,gr和zr的含量在0.1-0.8%,并采用基材锻打的加工工艺形成,根据浇
铸的铁合金材料的不同材质,来调整gr和zr的含量。
41.本实施例中,模具数量为6-10个,浇入铁合金液初始温度为1400-1700℃。在必要时可以顺序使用两次成型结构,并加振动结构,第一次成型为片状,第二次片状继续冷却并在滑落过程中破碎。具体案例中,模具数量可以为9个,浇入铁合金液初始温度为1500℃,在到达第二块模具出口端时变成固态,结束温度为600℃,形状为片状,在第二模具排出时温度降低380-400
°
c,并凝固为固态,本实施例中,冷却液为水,流量为500-1200立方/每小时。具体可以是800立方/每小时、1000立方/每小时。
42.本实施例中,铁合金浇铸成型后的块状厚度为25-45毫米,各模具安装在固定平台5上,并在浇铸时进行振动。具体块状厚度可以是30-40毫米。
43.如图4所示,该实施例的设备中,包括钢包倾倒结构91、冷床5和破碎箱8。其中,钢包倾倒结构91安装在底架92上,钢包9设置于钢包倾倒结构91上,钢包倾倒结构91用于倾倒钢包9。
44.在钢包9与冷床5之间还设置有摆动溜槽6和挡渣溜槽7。其中,摆动溜槽6承接钢包9中倾倒出的铁合金液,在垂直方向上设有一定的高度差,摆动角度为15-25度。挡渣溜槽7设置于摆动溜槽6与冷床5之间,出口位置设置横向的耐高温材料挡板,用于过滤铁合金液中料渣。
45.冷床5可以是一个、两个,也可以是多个。在本实施例的具体展示中,包括第一冷床51和第二冷床52。在第二模具排出时温度降低约400
°
c,并凝固为固态,经过冷却模具的继续振动冷却及上下模具之间高度差破碎在出口处变为片状固态。第一冷床51靠近钢包9设置,入口对应挡渣溜槽7。本实施例中,第一冷床51和第二冷床52均连接激振器53,激振器53使得两冷床51、52上的模具的承载面发生振动。第一冷床激振器53的振动频率为20-30hz,振幅为2-5mm,第二冷床激振器的振动频率为10-20hz,振幅为10-20毫米。
46.第一冷床51将从入口进入的铁合金熔液,经过振动降温凝固,在出口处变为片状固态,第二冷床52位于第一冷床的下游,并和第一冷床保持400-500毫米高度差,态铁合金从第一冷床流入第二冷床时,在重力作用下大块状铁合金出现破碎,所述第二冷床将从入口进入的片状固态铁合金,经过逐级冷却模具的降温、振动及模具之间落差破碎,在出口处变为小片固态,第二冷床同时采用了风冷机构10,鼓风机将大流量的冷空气吹入高温固态铁合金的底部和冷却模具表面,形成流动性的气膜,气膜厚度在2-5毫米,对固态铁合金加速冷却并保护冷床减小摩擦。
47.由上述技术方案可知,本发明的铁合金浇铸成型方法的优点和积极效果在于:本发明中,采用两个以上冷床5,第一冷床51上液体铁合金快速降温并凝固,通过冷床落差碎裂固态铁合金,在第二冷床52上通过气膜滑送小片固态铁合金进一步降温,模具座体2上设置液冷结构,模具体1u型敞口结构,因此铁合金液可以在敞口流动中快速降温和成型,并且不会飞溅和泄露,非常安全可靠。
48.本发明所属技术领域的普通技术人员应当理解,上述具体实施方式部分中所示出的具体结构和工艺过程仅仅为示例性的,而非限制性的。而且,本发明所属技术领域的普通技术人员可对以上所述所示的各种技术特征按照各种可能的方式进行组合以构成新的技术方案,或者进行其它改动,而都属于本发明的范围之内。