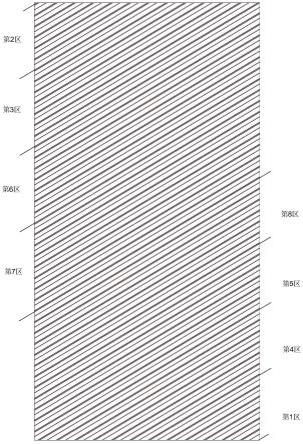
1.本发明涉及玻璃深加工技术领域,特别是涉及一种大幅面平板玻璃的刻宽槽加工方法。
背景技术:2.刻槽玻璃属于艺术玻璃的一种,刻槽玻璃就是通过车刻工具对玻璃进行雕刻、抛光,从而使玻璃表面产生出晶莹剔透的立体线条或图案纹路,构成简洁明快的现代画面,广泛用于门窗、墙面装饰。书柜、酒柜,起到点缀装饰作用的建筑材料,同时也可以在进一步加工成具有高强度节能玻璃。此种玻璃市场需求量大一般适应于内装行业。
3.刻槽即车刻,是采用机械方式通过数控机床或智能化自动设备装入刀具对玻璃表面进行刻槽加工抛光,从而使玻璃表面产生不同的形状和线条,是玻璃表面产生光影效果图案或立体线条。一般常规刻槽产品玻璃厚度为6mm、8mm或10mm,刻槽宽度≤30mm,深度≤3mm,槽间距一般在3mm以上,主要是考虑到刻槽加工误差和定位误差,在加工时一般采用1道120目金钢轮刻槽1遍,使用bd轮抛光1遍,就达到槽内抛光通透光亮的效果。国内外对刻槽工艺加工一般采用单机机械化加工,玻璃最大宽度1900mm,最大高度3000mm。然而大板面玻璃超宽槽加工难度较大,磨削阻力大,光泽度较差,超宽刻槽内存在白点缺陷;非对称槽加工难度及成品率更低,还存在刻槽抛光不一致,同时由于刻宽槽后,玻璃厚薄不同,刻槽轮磨削量不同因此导致槽宽不一致,刻槽加工过程玻璃易产生向上的弓形翘曲导致玻璃平整度变差,刻槽宽度偏差大,加工过程不易控制,产品一致性差。特别是对于大幅面平板玻璃弓形缺陷明显而且影响后续加工和安装应用。
技术实现要素:4.针对上述缺陷,本发明提供一种大幅面平板玻璃的刻宽槽加工方法,通过改变刻槽方向解决玻璃弓形翘曲问题,同时在原来的刻槽工艺基础上增加2道金钢轮磨削,新增加树脂轮磨削,采用bd轮进行一次或多次抛光并添加抛光液充分冷却同时提高抛光质量,使刻槽玻璃达到光洁均匀一致、目视通透的光影刻槽效果。
5.一种大幅面平板玻璃的刻宽槽加工方法,其特征在于包括如下步骤:
6.(1)选用刻宽槽磨轮:依次采用三道金刚轮、一道树脂轮、一道bd抛光轮;
7.(2)刻槽划区及确定刻槽方向:将大幅面平板玻璃在与槽垂直方向上划分为多个区,先从底部往上刻槽一个区,完成此区后再从顶部往下刻槽一个区;再从下往上刻槽一个区,然后依次轮换,并在中间区域刻槽合拢。
8.所述刻槽宽度为40mm-60mm。
9.其中1号金钢轮同道槽加工一次,2号金钢轮同道槽加工一次,3号金钢轮同道槽加工二次;4号树脂轮同道槽加工三次,5号bd抛光轮同道槽加工三次。
10.所述刻槽宽度为40.0mm;所述1号金钢轮应为60目或80目,2号金钢轮为120目或140目,3号金钢轮240目;第4道树脂轮300目;最后采用bd进行抛光。
11.其中,第1道金钢轮金钢砂目数60目,轮宽35.6mm,第1道刻槽宽度为:34mm;第2道金钢轮金钢砂目数120目,轮宽为38mm,第1道刻槽宽度为:37.5;第3道金钢轮金钢砂目数240目,轮宽38.80mm,第1道刻槽宽度为38.5mm;第4道树脂轮粗糙度300目,轮宽39.5mm,第1道刻槽宽度:39.5mm;第5道bd抛光轮,轮宽40.20mm,第1刀刻槽宽度:40.00mm。
12.所述刻槽宽度为60.0mm;第1道金钢轮金钢砂目数100目,轮宽55.50mm,第1道刻槽宽度54.00mm;第2道金钢轮金钢砂目数200目,轮宽58.50mm,第1道刻槽宽度57.5mm;第3道金钢轮金钢砂目数240目,轮宽59.50mm,第1道刻槽宽度59.00mm,刻槽加工二遍;第4道树脂轮粗糙度300目,轮宽59.80mm,第1道刻槽宽度59.50mm,刻槽加工三遍;第5道bd抛光轮,轮宽60.5mm,第1刀刻槽宽度60.0mm,刻槽加工三遍。
13.所述步骤(2)为在与槽垂直方向划分为8个区,先从底部第1区开始往上刻,然后从顶部的第2区、第3区往下刻,再从下部的第4区、第5区往上刻,依次轮换,并在中间合拢。
14.其中bd抛光轮磨削时,加入抛光液。
15.所述抛光液为5%氧化铈(质量比)抛光粉水悬浊液,抛光过程中要使用抛光液和冷却水同时对刻槽磨轮和刻槽玻璃前进方向上呈45
°
向磨轮磨削部位喷水和喷液。采用万向旋转水管与抽水泵联通,通过水泵将混合后的抛光液注入水管,由水管根据磨削角度和行走速度沿抛光轮旋转的前进方向呈45
°
向磨削部位喷水和抛光液,提高刻槽面的亮度。
16.常规刻槽加工方法由于加工玻璃版面小、槽宽窄、深度小,因此刻槽后玻璃不易产生上弯现象,加工过程相对单一和稳定。常规刻槽通常从底边或玻璃的1边开始依次排序刻槽加工(即:图1),刻槽过程中因玻璃应力释放现象,造成边部刻槽宽度超标或者产生抛光不亮,甚至不定时发生抛光轮损坏或者玻璃破裂等现象。在这种情况下每加工600延米左右需对整套磨轮进行1次整形与校正。为了解决大幅面平板玻璃刻宽槽后玻璃应力释放而产生的弓形翘曲问题,本技术对刻槽玻璃进行分区刻槽,以保证刻槽的同时磨轮磨削量以自适应的方式进行自动修轮。其方法是:将整块刻槽玻璃进行分区刻槽(刻槽分多少个区,各区大小依据设备规格确定区域单元)(即:图2中的8个区与图1中的8个区划分不同),加工顺序不同:从底部的第1区-上部的第2区-上部的第3区-底部的第4区-底部的第5区
……
上、下循环刻槽,至中部合拢,这样就减少了大板玻璃超宽刻槽、超深度刻槽因加工过程应力释放造成的上弯翘曲现象,。本发明方法不但可以减小刻槽后原片玻璃表面应力释放造成的弯曲,同时还可提高生产效率,节省时间,避免修磨轮的时间和费用。
17.本发明由于单道槽比较宽,磨削量较大,磨削速度慢,因此考虑在常规刻槽的工艺流程上增加2道金钢轮磨削,新增加树脂轮磨削,树脂轮磨削为bd轮抛光提供了良好的基础条件,bd轮抛光时加入氧化铈混合抛光液促使提高抛光效果的光泽度。
18.本发明不仅适用于单一同槽宽的刻槽,也适用于组合变换槽的刻槽,为避免来回换磨轮,同槽宽的刻槽为一组刻蚀,刻槽方向与本发明相同,刻槽完成后,再换另一组槽宽继续刻槽。
19.金属合金烧结的金刚石磨轮俗称金钢轮。金钢轮含有金刚石部分称为工作层,工作层高度称为工高,工作宽度称为环宽。磨轮直径内侧称为内环,外侧称为外环。金刚石颗粒直径大小称为粒度或目数。在加工刻槽玻璃时常规(刻槽宽度≤20mm)加工一般选择1至2道金钢轮加工车刻。根据刻槽图的刻槽宽度及深度,每个刻槽轮刻槽加工一遍,定购车刻磨轮时要注意刻槽单道槽的槽宽公差,金钢轮厚度与刻槽理论值宽度大0.2mm,方可加工出理
想宽度的刻槽玻璃。
20.树脂轮属于磨轮的一种,是采用树脂粉将金钢石、cbn砂轮进行粘合在加入填充材料,经过热压、硬化等加工而成的用于磨削玻璃的磨轮,通常对玻璃精细研磨起到很好的磨削效果,通常使用在金钢轮后面,起到去痕、精磨、修复的作用,为抛光提供良好的基础条件。针对超宽刻槽玻璃必须使用金钢石树脂轮进行车刻磨削,根据槽宽及槽深树脂轮磨削遍数1-3次,每次磨削后对加工面进行检查,确保整道槽均要被磨削。
21.bd轮是一种玻璃抛光磨轮,也叫土轮、泥巴轮,主要用在异形机上抛光。bd轮是由特殊的高分子材料与很锋利的氧化铝和碳化硅进行混合反应而制作,具有优良的弹性和抛光效率。其特点是形状保持长久,经抛光后的玻璃边光亮度非常好,是典型的玻璃边加工应用材料。轮的适用范围:异形机上的抛光轮类型:外圆玻璃抛光圆柱度:《180(μm)工作线速:25m/s转速:3000/min,稀土抛光沙等材质。bd轮磨削锋利,抛光效果好,适用于加工异形和超厚玻璃磨边抛光,即使在精度不高的设备上使用也不会发颤和存在抛光不良的现象。
22.在使用bd轮抛光过程中,需要对bd轮与玻璃接触位置进行冷却,常规情况下选用过滤水进行冷却即可。针对超宽槽的抛光,原则上使用冷却液,但是为了提高超宽刻槽玻璃的抛光亮度,本发明采用冷却水+5%的氧化铈抛光粉混合成抛光液。在抛光的同时采用外接水管向抛光轮与玻璃接触的位置45
°
喷水。这样当抛光轮自动接触玻璃表面时抛光效果更好更亮。
23.本发明通过改变刻槽方向,减少了大板玻璃超宽刻槽、超深度刻槽加工过程中应力释放造成的上弯翘曲现象。本发明方法不但可以减小刻槽后原片玻璃表面应力释放后造成的弯曲,同时还提高生产效率,节省时间,同时在原来的刻槽工艺基础上增加2道金钢轮磨削,新加树脂轮磨削,采用bd轮进行一次或多次抛光并添加抛光液,使刻槽玻璃达到光洁均匀一致、亮度统一的外观效果。
附图说明
24.图1为现有技术中刻槽方向,图中箭头为刻槽方向
25.图2为本发明中玻璃刻槽分区示意图,
26.图3为本实施例1槽剖视示意图(局部图),
27.图4为本实施例2玻璃刻槽分区示意图,
28.图5为本实施例2槽剖视示意图(局部图)。
具体实施方式
29.下面结合实施例对本发明作进一步的详细说明。
30.实施例1
31.配置:10mm超白刻槽,单道槽宽40mm,槽深3mm,槽间距3mm,刻槽角度与底边呈23.5
°
布局,槽底r角3mm,见图3。
32.玻璃规格:1900mm*8000mm
33.1、在刻槽前打开水、电、气设备,确保畅通,检查设备x轴、y轴、z轴原点,测量并输入预使用磨轮的直径、转速及旋转方向和入刀方向。然后输入刻槽图或拷贝cad图并复核与订单的一致性。根据图纸与实际设定参数模拟刻槽加工流程,进行刻槽测试。
34.2、检查玻璃与图纸一致性,然后在玻璃下表面贴平整的雕刻纸或贴膜,无论是贴雕刻纸还是贴膜必须贴平整无气泡和折痕,如果贴膜的宽度或雕刻纸的宽度不够宽(即不能够一次100%全面覆盖玻璃面)则应进行拼接,拼接位置不应重合,应对齐贴平整。主要是防止玻璃面直接接触刻槽平台防止表面划伤和刻槽过程中水印的产生,同时也考虑雕刻纸厚度对刻槽精度的影响。
35.3、然后进行上片,上片过程中要注意测量玻璃左右侧及前后端玻璃的厚薄差,要根据刻槽玻璃的入刀端和出刀端玻璃的厚度设定刻槽参数(主要是z轴数据)。上片后测量玻璃尺寸核对原点与起刀点的位置,检查程序及使用的磨轮复核相关参数。刻槽玻璃的起始点位于设备原点必须具备相对应的数据关系后方可进行刻槽加工。在遇到特殊形状的玻璃或特殊刻槽加工时应在起始点位置和起刀位置增加与成品刻槽玻璃相同厚度的玻璃边条,主要是弥补刻槽磨轮起始点位置受力均匀同时保证刻槽边部区域质量稳定性及一致性。
36.4、刻槽磨轮的选用见下表:
[0037][0038]
将整块刻槽玻璃进行分区刻槽,见图2中的8个区,先从底部的第1区-上部的第2区-上部的第3区-底部的第4区-底部的第5区
……
上、下循环刻槽,至中部合拢。
[0039]
5、刻槽加工时根据磨轮直径大小调节刻槽喷水管的位置,确保冷却水喷水到位。每次更换磨轮时要实际测量磨轮的直径并核对输入参数是否一致。刻槽加工第1道槽后应暂停刻槽加工,应检查落刀位置和起刀位置及玻璃中间位置的刻槽宽度数据并与设定刻槽宽度值对比进行调整参数,然后再继续进行刻槽加工。每道轮加工后要测量起刀位置和落刀位置的槽宽、槽边距偏差、槽间距偏差、刻槽区域的总宽度、槽深等相关数据并判定是否符合设定要求。当树脂轮磨削后宽度不符合设定宽度时则需要在使用同道磨轮再次刻槽加工一遍。抛光过程中要使用抛光液和冷却水同时对刻槽磨轮和刻槽玻璃前进方向上呈45度进行喷水。直至抛光符合要求为止,若抛光过程中遇到刻槽轴线抛光不亮则要加大压力或减小磨轮半径,继续进行抛光同时减小抛光轮的压力。如果遇到边部一侧抛光不符合要求时则采取偏移x轴或y轴数据来偏移刻槽公差弥补抛光的亮度和均匀性。
[0040]
6、刻槽完成后应采用最小刻度为0.2mm钢板尺或游标卡尺测量槽边距、槽间距、槽宽度、槽深度、玻璃厚度等相关数据值。测量刻槽区域总宽度和总长度,包括检查刻槽数量,逐一检查每道刻槽玻璃抛光质量和刻槽外观质量。完全符合要求后则进行下片操作,下片后采用直径不大于0.4mm的细线绳+钢板尺测量刻槽玻璃的弓形翘曲,然后检查刻槽玻璃的外观质量(刻槽内点状白点、刻槽爆边、玻璃表面水印、玻璃面硬伤、抛光亮度,与封样对比),合格后方可进行下片操作。
[0041]
7、刻槽玻璃不应进行平放或平抬(平放搬运),由平放转向立放状态则需要采用专
用的翻转装置进行立放,立放后将玻璃底面的膜或者雕刻纸进行去除并检查外观,然后进行清洗干净,清洗时应将刻槽面和玻璃均要进行清洗干净。由于刻槽面浸水时间长且与刻槽玻璃的水、玻璃粉、抛光液长时间接触,清洁时需采用抛光级钢丝棉进行外力擦拭去除,清洗干净后在刻槽玻璃上按照要求张贴标签并进行立架转下道工序。
[0042]
对比例1
[0043]
刻槽轮选择与实施例1相同,只是刻槽方向按图2所示方向。
[0044]
实施例2
[0045]
配置:19mm超白刻槽,槽宽60mm,槽深6.5mm,槽间距设计值0mm(槽边与槽边对接),刻槽角度与底边垂直刻槽(与底边呈90
°
),槽底r角3mm,见图5所示。
[0046]
玻璃规格:1900mm*8000mm。
[0047]
加工方法如实施例1,仅选刻槽轮不同。玻璃刻槽分区见图4。
[0048]
选用刻槽轮要求:
[0049]
第1道1#金钢轮金钢砂目数100目,轮宽55.50mm,第1道刻槽宽度54.00mm,刻槽加工一遍。第2道2#金钢轮金钢砂目数200目,轮宽58.50mm,第1道刻槽宽度57.5mm,刻槽加工一遍。第3道3#金钢轮金钢砂目数240目,轮宽59.50mm,第1道刻槽宽度59.00mm,刻槽加工二遍。第4道4#树脂轮目数300目,轮宽59.80mm,第1道刻槽宽度59.50mm,刻槽加工三遍。第5道5#bd抛光轮(不含金刚石目数),轮宽60.5mm,第1道刻槽宽度60.0mm,刻槽加工三遍。
[0050]
对比例2
[0051]
刻槽轮选择与实施例2相同,只是刻槽方向为从左往左或从右向左依次加工。
[0052]
玻璃检验结果:
[0053]
对比例1:未分区刻槽玻璃刻槽后长边(高度边)弓形弯曲数值≥3.0mm,短边(宽度边)弓形数值≥2.0mm;
[0054]
实施例1:经分区刻槽后测量同一块玻璃长边(高度边)弓形弯曲≤1.0mm,短边(宽度边)弓形数据≤1.0mm。
[0055]
对比例2:未分区刻槽玻璃刻槽后长边(高度边)弓形弯曲数值≥6mm,短边(宽度边)弓形数值≥2.0mm;
[0056]
实施例2:经分区刻槽后测量同一块玻璃长边(高度边)弓形弯曲≤2.0mm,短边(宽度边)弓形数据≤1.0mm。
[0057]
检验结果说明分区刻槽确实减小了玻璃应力释放速度并减小玻璃因应力释放引起的刻槽弓形翘曲。