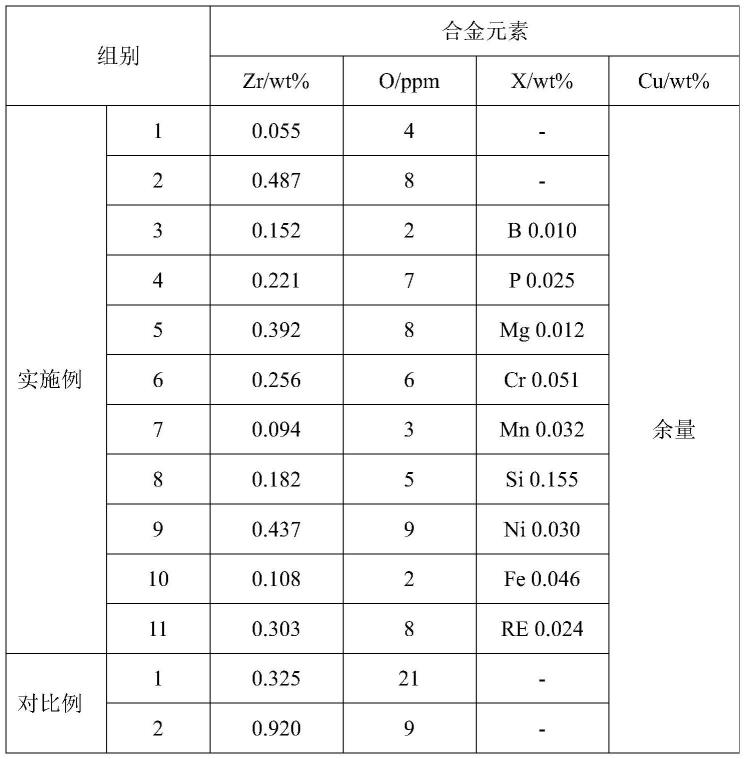
1.本发明属于铜合金技术领域,具体涉及一种铜锆合金板带材及其制备方法。
背景技术:2.铜基合金具有较好的导电性能、导热性能和耐腐蚀性能等物化性能,在电子电气等领域应用十分广泛,尤其涉及连接器、引线端子、开关等电子零件的多种用途。随着科学技术的发展,电子电气元件逐渐小型化、轻量化,元件在使用过程中流动的电流密度也越来越高,同时伴随着元件的发热,需要在高温工况下具有更长的使用寿命,这对材料的导电性能和耐高温性能提出了相当高的要求。
3.铜锆合金作为一种高导铜合金,具有良好的耐高温性能,但难以在确保上述性能的前提下保持良好的强度和冷加工性能,原因在于:一方面,对于铜合金而言,导电性能和强度是相互排斥的,例如铜锆合金为沉淀强化型合金,在制备过程中会在铜基体中形成细小分散的金属间化合物颗粒,从而改善合金的力学性能,同时会引起导电性能的降低;另一方面,由于各组成元素的熔点的不同,在化合物形成的过程中,不均匀的应变会产生局部的应力集中,在进行后续的冷加工时,可能会导致缺陷乃至裂纹的出现。
4.目前急需开发一种高导耐热的铜合金材料,要求具有良好的强度和冷加工性能,能够满足电子电气元件日益增长的性能需求,同时在冷加工过程中不易产生裂纹。鉴于此目的,本发明提出一种铜锆合金板带材及其制备方法。
技术实现要素:5.本发明所要解决的第一个技术问题是提供一种铜锆合金板带材,该铜锆合金板带材具有优异的耐高温性能和良好的导电性能、强度和冷加工性能。
6.本发明解决第一个技术问题所采用的技术方案为:一种铜锆合金板带材,该铜锆合金板带材的质量百分比组成包括zr:0.05wt%~0.5wt%、o:≤10ppm,余量为cu和不可避免的杂质;该铜锆合金板带材的垂直于轧制方向的截面上,将含o的析出相粒子的个数记为a,a≤5个/μm2。
7.本发明中zr作为主要的合金元素,通过固溶处理溶入铜基体中形成过饱和固溶体,之后固溶体在热处理过程中分解为弥散分布的析出相。适量的zr元素能够大大降低晶界能,并产生溶质拖曳和第二相钉扎晶界,从而提升耐热性和强度;且zr在cu基体中的溶解度很低,低溶解度的合金元素zr对合金整体的导电性能影响十分有限,能够保证合金良好的导电性能。若zr含量过高,则析出相的尺寸随之增大并会产生富集,不仅会使得合金的导电率急剧降低,还会对合金的冷加工性能产生恶化效果;若zr含量过低,则无法起到析出强化的效果。因此,本发明铜锆合金板带材中的zr含量控制在0.05wt%~0.5wt%范围内。
8.o元素在合金中超过一定含量会产生不利的作用,由于高铜合金在熔炼过程中出现吸气现象的倾向较大,造成合金熔体的氧含量超标,一方面会加剧合金元素的过度烧损,另一方面会产生夹杂物等缺陷,影响后续的加工。此外,若o含量过高对合金的机械性能也
会产生不利的影响,故可通过真空熔铸、高纯度覆盖剂或脱氧剂等方式,将本发明铜锆合金板带材的o含量严格控制在10ppm以下。
9.本发明铜锆合金板带材通过合金元素引入弥散的析出相粒子以及其带来的沉淀和弥散强化作用,在尽可能低地影响合金的导电性能和耐高温性能的同时,可提高板带材的强度和冷加工性能。合金中zr元素在时效热处理后会形成形貌尺寸不均的析出相分布于基体的晶内和晶界。其中分布于晶内的析出物尺寸相对细小而均匀,多为圆形或针状的结构;而分布于晶界处的析出物尺寸较大,且伴随一定程度o元素的富集,在晶界连接处形成许多三角晶界,过多的三角晶界会在热变形过程中加剧开裂倾向,引起冷加工性能的恶化,因此应控制含o析出相粒子的数量尽可能少。本发明控制铜锆合金板带材的垂直于轧制方向的截面上的含o的析出相粒子的个数a≤5个/μm2,晶界富集的析出相减少,析出相整体更加均匀弥散于晶内。当a值处于较低水平时,合金发生不均匀应变以及局部应力集中的倾向降低,反之当a值过高时,会导致合金冷加工时出现明显缺陷,甚至发生开裂。
10.作为优选,该铜锆合金板带材的微观组织中的平均晶粒尺寸≤50μm。本发明铜锆合金板带材具有较高程度的细晶微观组织,晶粒未发生完全长大,能够在不降低韧性的前提下,获得良好的强度,配合弥散分布的析出相能够有效提高合金的综合力学性能。
11.作为优选,该铜锆合金板带材的微观组织中的高斯织构的面积占比sg、黄铜织构的面积占比sb和铜型织构的面积占比sc满足0.5≤(sg+sb)/sc≤1.5。当塑性相对较低的铜型织构的面积占比过高,而具有良好塑性的高斯织构和黄铜织构的面积占比过低时,合金出现不均匀应变的倾向增大,表现为冷加工时延伸率的各向异性大,严重的可能会引起断裂;反之当铜型织构的面积占比过低而高斯织构和黄铜织构的面积占比过高时,虽然合金的塑性得到了改善,但强度和导电性能随之劣化。对本发明铜锆合金板带材的微观组织中的高斯织构、黄铜织构和铜型织构的面积占比进行控制,能够在获得良好的强度和优异的耐高温性能的同时,使得合金板带材的不均匀应变程度降低,应力集中情况缓解,从而确保其具有良好的冷加工性能。因此需控制本发明铜锆合金板带材的微观组织中的高斯织构的面积占比sg、黄铜织构的面积占比sb和铜型织构的面积占比sc满足0.5≤(sg+sb)/sc≤1.5。
12.作为优选,该铜锆合金板带材的质量百分比组成中还包括总量0.01wt%~1.0wt%的x,x选自mg、cr、mn、si、ni、fe、b、p、re中的至少一种。
13.x元素可起到一定程度的强化效果,在熔铸过程中,x元素可以起到脱氧剂的作用,或作为形核中心而提高合金的形核率,从而达到净化熔体、细化晶粒的目的。合金熔体的氧含量降低,会降低出现氧化夹杂物的倾向;晶粒细小的铸锭为加工板带材成品提供了良好的初始条件,有助于提升本发明铜锆合金板带材的机械性能和冷加工性能。当可选元素x的含量低于0.01wt%时,净化熔体、细化晶粒的效果不明显;当其含量高于1.0wt%时,过量的x元素对合金的导电性能会产生较大的负面影响,因此本发明将x元素的含量控制在0.01wt%~1.0wt%。
14.本发明铜锆合金板带材的抗拉强度在350mpa以上,导电率在85%iacs以上,软化温度≥500℃;该铜锆合金板带材宽度方向的延伸率为δw,长度方向的延伸率为δ
l
,两者满足δw/δ
l
≥0.6。
15.本发明所要解决的第二个技术问题是提供一种铜锆合金板带材的制备方法。
16.本发明解决第二个技术问题所采用的技术方案为:一种铜锆合金板带材的制备方
法,包括以下工艺流程:熔铸
→
热轧
→
粗轧
→
一次时效热处理
→
中轧
→
二次时效热处理
→
精轧;所述的一次时效热处理的温度为440~600℃,所述的二次时效热处理的温度为300~440℃。
17.本发明控制一次时效热处理的温度为440~600℃,二次时效热处理的温度为300~440℃。一次时效热处理采用较高的温度440~600℃,时效初期合金的溶质原子过饱和度较大,且有大量的位错和变形带在基体中形成高度均匀的形核区域,变形带来的驱动力使溶质原子逐渐在晶界和晶内聚集生成析出相,较高的一次时效热处理温度提供足够的内能,使得析出相在晶粒不发生明显粗化的前提下以较快的速度扩散,析出量增多,分布更均匀,同时以粗大的含o析出相形式产生的倾向更低,对位错的钉扎作用更明显。二次时效热处理较一次时效热处理的温度进一步降低,这是由于中轧后的二次时效热处理可以一定程度上消除加工硬化的影响,使剧烈塑性变形所积累的能量得以释放,同时使得析出相能够充分析出并在合金基体中弥散分布,且大小更加均匀而细小,从而在保持较高导电率的前提下改善合金强度和塑性。
18.作为优选,所述的一次时效热处理和所述的二次时效热处理的总保温时间不低于10h。为使得合金基体中的溶质原子析出得更加彻底,需给予足够的保温时间以保证溶质原子得到有效扩散,从而避免铜锆合金板带材成品的导电性能以及冷加工性能出现恶化。
19.作为优选,所述的热轧的初始温度为880~1000℃,所述的热轧的总加工率在90%以上。热轧的初始温度控制在880~1000℃,以确保合金元素充分溶入铜基体且晶粒不发生长大现象。当热轧的初始温度低于880℃时,金属熔体的流动性差,溶质扩散不充分,在热轧过程中变形的受阻增大,容易引起开裂;当热轧的初始温度高于1000℃时,会引起合金元素的氧化或过度烧损,导致热轧坯的质量受到严重影响。热轧的总加工率控制在90%以上,以进一步为后续板带材成品中形成析出相做准备,减少晶界处粗大析出相的富集倾向。同时提供足够的畸变能以促进热轧坯中铜型织构的转化,以控制成品中的织构比例满足要求。
20.由于粗轧设置在热轧与一次时效热处理的中间,所起到的作用除了初步调整板带材尺寸外还能够为后续的时效热处理提供驱动力。随着粗轧冷变形程度的增加,晶粒发生破碎,尺寸逐渐减小,晶粒内部位错不断积累,从内提高合金时效析出的驱动力,有效促进析出相的生成。中轧和精轧设置在一次时效热处理之后,析出相在时效热处理过程中逐渐生成,进一步的冷变形使位错运动的阻力增加,出现加工硬化现象,进一步强化合金的机械性能。如果粗轧的总加工率低于中轧的总加工率与精轧的总加工率之和,则无法为时效热处理提供足够的驱动力,导致析出相的扩散不充分,发生局部富集,板带材的冷加工性能降低,同时板带材加工硬化的效果过大,对电子散射效应加剧,导致最终板带材成品的导电性能急剧下降。因此,作为优选,所述的粗轧的总加工率不小于所述的中轧的总加工率与所述的精轧的总加工率之和。
21.与现有技术相比,本发明具有如下优点:本发明通过调整zr的添加量以及o元素的含量,控制铜锆合金板带材的垂直于轧制方向的截面上,含o的析出相粒子的个数a≤5个/μm2,在保证铜锆合金板带材具有良好的导电性能和优异的耐高温性能的同时,能够提高其强度和冷加工性能。本发明铜锆合金板带材的抗拉强度在350mpa以上,导电率在85%iacs以上,软化温度≥500℃;该铜锆合金板带材宽度方向的延伸率为δw,长度方向的延伸率为δ
l
,两者满足δw/δ
l
≥0.6,冷加工性能良好,在冷加工过程中不易产生裂纹。
具体实施方式
22.以下结合实施例对本发明作进一步详细描述。
23.首先,提供11个实施例和2个对比例,具体合金成分见表1,分别制备为带材试样。
24.以实施例1的合金为例,制备为带材试样,制备流程为:熔铸
→
热轧
→
粗轧
→
一次时效热处理
→
中轧
→
二次时效热处理
→
精轧,具体包括以下步骤:
25.按照所需成分进行配料,采用感应炉进行熔炼,熔铸温度为1200℃,经检测成分符合要求并经由充分除气、除渣后进行铸造铸锭;对上述铸锭以920℃的初始温度保温3h后进行热轧开坯,热轧的总加工率为95%;将热轧处理后的带材进行铣面去除表面氧化膜后粗轧加工,粗轧的总加工率为70%;以500℃对粗轧后的带材进行一次时效热处理,保温6h;一次时效热处理后的带材在清洗后,施加加工率50%的中轧加工;对中轧后的带材进行二次时效热处理,时效温度和保温时间分别为400℃和6h;二次时效热处理后对带材进行精轧加工,精轧加工的总加工率为10%,制成实施例1的带材试样。
26.对各实施例和对比例的带材试样进行以下检测:
27.抗拉强度:按照《gb/t 228.1-2010金属材料拉伸试验第1部分:室温试验方法》在电子万能力学性能试验机上进行室温拉伸试验,拉伸速度为5mm/min。
28.导电率:采用《gb/t 32791-2016铜及铜合金导电率涡流测试方法》测试带材试样的导电率。
29.延伸率各向异性:按照《gb/t 228.1-2010金属材料拉伸试验第1部分:室温试验方法》测量试样的宽度和长度方向上的延伸率,宽度方向的延伸率为δw,长度方向的延伸率为δ
l
,利用δw/δ
l
的计算式计算出表示带材试样宽度方向w的延伸率与长度方向l的延伸率之比值,作为延伸率各向异性的参数。
30.平均晶粒尺寸:试样打磨抛光后,利用扫描电镜观察晶粒大小,每个试样随机采集5个视场,使用电镜分析软件测量晶粒尺寸计算平均值。
31.含o的析出相粒子:采用透射型电子显微镜在带材试样截面上观察的视野内随机地设置观察区域,上述观察区域为400nm
×
250nm的矩形。在该观察区域内的铜基体部分中随机取五个点对其进行eds分析,测定o元素的检测强度取平均值设为ia。下一步对该观察区域中对比度与铜基体不同的粒状物作为检测对象并以相同测试条件进行eds分析,测定上述ia的10倍以上的o元素检测强度的粒状物的个数并计为a。
32.织构:采用ebsd分析带材试样的织构类型及面积占比,所谓的各取向织构的面积占比是指,各取向偏离角度15
°
以内的面积除以测定面积的比值,{110}《112》黄铜织构的面积占比为sb,{011}《100》高斯织构的面积占比为sg,{112}《111》铜型织构的面积占比为sc,计算(sg+sb)/sc值。
33.实施例1~实施例11和对比例1~对比例2的带材试样的微观组织及性能的检测结果见表2。从表2可以看出,实施例1~实施例11的带材试样的微观组织中含o的析出相粒子的个数a≤5个/μm2,且高斯织构的面积占比sg、黄铜织构的面积占比sb和铜型织构的面积占比sc满足0.5≤(sg+sb)/sc≤1.5;实施例1~实施例11的带材试样的软化温度≥500℃,且带材宽度方向的延伸率δw与长度方向的延伸率δ
l
满足δw/δ
l
≥0.6,表现出优异的耐高温性能与良好的导电率的同时,能够保证良好的强度和冷加工性能。
34.作为对照的对比例1和对比例2,含o的析出相粒子的个数过高,在强度、导电率、软
化温度和延伸率各向异性等性能上并不能完全达到本发明的目标值。
35.表1:实施例1~实施例11和对比例1~对比例2的合金成分
[0036][0037]
表2:实施例1~实施例11和对比例1~对比例2的带材试样的微观组织及性能
[0038][0039]
*:{110}《112》黄铜织构的面积占比为sb,{011}《100》高斯织构的面积占比为sg,{112}《111》铜型织构的面积占比为sc。
[0040]
实施例12:采用上述实施例3中粗轧后的带材,以450℃对粗轧后的带材进行一次时效热处理,保温6h;一次时效热处理后的带材在清洗后,施加加工率50%的中轧加工;对中轧带材进行二次时效热处理,时效温度和保温时间分别为300℃和6h;二次时效热处理后对带材进行精轧加工,精轧加工的总加工率为10%,制成实施例12的带材试样。
[0041]
实施例13:与实施例12的区别在于,实施例13中的一次时效热处理的温度为600℃,保温时间为6h;二次时效的温度为420℃,保温时间为6h。
[0042]
对比例3:与实施例12的区别在于,对比例3中的一次时效热处理的温度为400℃,保温时间为6h;二次时效的温度为500℃,保温时间为6h。
[0043]
对比例4:与实施例12的区别在于,对比例4中的一次时效热处理的温度为500℃,保温时间为4h;二次时效的温度为400℃,保温时间为4h。
[0044]
实施例3、实施例12~实施例13和对比例3~对比例4的带材试样的微观组织及性能的检测结果见表3。从表3可以看出,对比例3~对比例4由于采用了不同的时效工艺,在导电率或延伸率各向异性上出现明显降低。
[0045]
表3:实施例3、实施例12~实施例13和对比例3~对比例4的带材试样的微观组织及性能
[0046][0047]
实施例14:采用上述实施例3中的铸锭,以880℃的初始温度保温3h后进行热轧开坯,热轧的总加工率为95%;将热轧处理后的带材进行铣面去除表面氧化膜后粗轧加工,粗轧的总加工率为70%;以500℃温度对粗轧带材进行一次时效热处理,保温6h;一次时效热处理后的带材在清洗后,施加加工率50%的中轧加工;对中轧带材进行二次时效热处理,时效温度和保温时间分别为400℃和6h;二次时效热处理后对带材进行精轧加工,精轧加工的总加工率为10%,制成实施例14的带材试样。
[0048]
实施例15:与实施例14的区别在于,实施例15中的粗轧初始温度为980℃,加工率为90%。
[0049]
对比例5:与实施例14的区别在于,对比例5中的粗轧初始温度为920℃,加工率为70%。
[0050]
实施例3、实施例14~实施例15和对比例5的带材试样的微观组织及性能的检测结果见表4。从表4可以看出,对比例5由于粗轧加工率较低,制得的带材的微观组织中织构的比例与本发明存在较大差异,延伸率各向异性不满足要求。
[0051]
表4:实施例3、实施例14~实施例15和对比例5的带材试样的微观组织及性能
[0052][0053]
实施例16:采用上述实施例3中的一次时效热处理后的带材,在清洗后,施加加工率30%的中轧加工;对中轧带材进行二次时效热处理,时效温度和保温时间分别为400℃和6h;二次时效热处理后对带材进行精轧加工,精轧加工的总加工率为30%,制成实施例16的带材试样。
[0054]
对比例6:与实施例16的区别在于,中轧的加工率为30%,精轧的加工率为50%。
[0055]
对比例7:与实施例16的区别在于,中轧的加工率为50%,精轧的加工率为30%。
[0056]
实施例3、实施例6和对比例6~对比例7的带材试样的微观组织及性能的检测结果
见表5。从表5可以看出,对比例6和对比例7采用较大的中轧或精轧加工率,两者之和大于粗轧的加工率,制得的带材的导电性能急剧下降,且带材的微观组织中织构的比例与本发明存在较大差异,延伸率各向异性不满足要求。
[0057]
表5:实施例3、实施例16和对比例6~对比例7的带材试样的微观组织及性能
[0058]