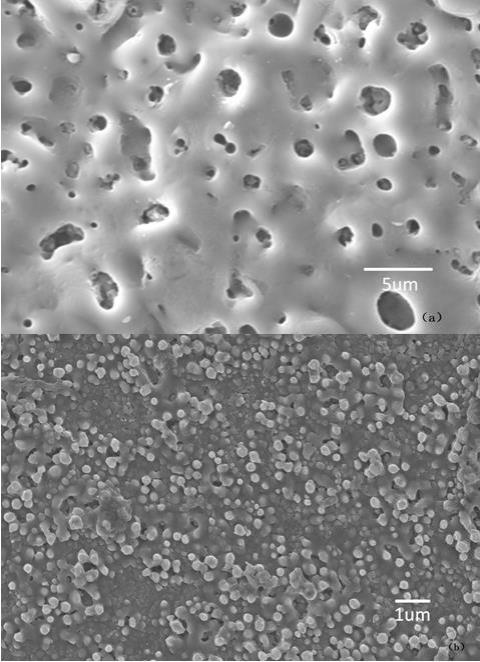
1.本发明涉及镁合金表面处理技术领域,具体涉及一种镁合金表面超疏水复合膜层及其制备方法。
背景技术:2.镁合金质量轻,其密度只有1.7kg/m3,是铝的2/3,钢的1/4,具有良好的铸造性和尺寸稳定性,容易加工,废品率低,具有良好的阻尼系数,减振量大于铝合金和铸铁,非常适合用于汽车的生产中,同时在航空航天、便携电脑、手机、电器、运动器材等领域也有着广泛的应用空间。然而,由于其化学活性高,易氧化,使用过程中表面很容易发生腐蚀,极大地限制了镁合金在航空航天、便携电脑、手机、电器、运动器材等领域的广泛应用。
3.因镁合金的耐腐蚀性能较差,通常需要采用一定的表面处理工艺来提高其表面耐蚀性能。镁合金常用的表面处理方法包括电镀、化学转化、阳极氧化、微弧氧化等,其中微弧氧化(mao)作为一种较新的表面处理工艺,由于可以在镁合金表面原位生成一层陶瓷膜层,在一定程度可以提高镁合金的耐蚀性能。但是,由于微弧氧化膜层表面存在一定的孔隙,且粗糙度较大,具有较大的亲水性,因此在提高镁合金耐腐蚀性能方面有一定的限制。
4.而通过在镁合金表面制备一层具有超疏水性的膜层,在其超疏水的作用下,该膜层将使得镁合金表面有更好的耐蚀能力,除此之外,超疏水复合膜层的制备,也将促进镁合金在超疏水领域其他方面的应用。
技术实现要素:5.针对上述现有技术,本发明的目的是提供一种镁合金表面超疏水复合膜层及其制备方法。采用磁控溅射法,依次在镁合金表面溅射沉积alsi层及sio2层,形成alsi/sio2复合膜层,所述alsi/sio2膜层具有良好的超疏水性能,不仅能提高镁合金的耐腐蚀性能,也能促进镁合金在超疏水领域其他方面的应用。
6.为实现上述目的,本发明采用如下技术方案:本发明的第一方面,提供了一种镁合金表面超疏水复合膜层的制备方法,包括以下步骤:(1)镁合金试样进行表面预处理;(2)采用al靶材和si靶材,在步骤(1)表面预处理后的镁合金试样上溅射alsi层;(3)将al靶材更换为si靶材,在步骤(2)表面附着alsi层的镁合金试样上溅射sio2层,取出镁合金试样,即得镁合金表面超疏水复合膜层。
7.优选的,步骤(1)中,所述镁合金为az31、am60、az91d或we43中的一种。
8.优选的,步骤(1)中,镁合金试样表面预处理的方法为:将镁合金试样依次用400#、800#、1500#的砂纸打磨,再经抛光处理后,依次放入丙酮、去离子水和无水乙醇中各超声波清洗3~10min,吹干。
9.优选的,al靶材和si靶材的纯度≥99.99%。
10.优选的,步骤(2)中,溅射alsi层的方法为:将步骤(1)得到的表面预处理后的镁合金试样放入磁控溅射真空室中,四个靶位交替放入两个al靶材和两个si靶材,调节靶材与镁合金试样的距离为80mm后,抽真空,通氩气,对靶材进行溅射清洗,待靶材溅射清洗结束后,调节氩气流量和真空室气压,结合氩离子刻蚀,在镁合金试样表面磁控溅射alsi层。
11.进一步优选的,氩气纯度≥99.999%。
12.进一步优选的,靶材溅射清洗参数为:真空度1
×
10-4
~5
×
10-4
pa,氩气流量为100~250sccm,溅射清洗时间5~30min。
13.进一步优选的,溅射alsi层的参数为:氩气流量30~60sccm,真空室气压0.8~1.5pa,溅射功率30~150w,溅射温度为室温。
14.进一步优选的,氩离子刻蚀的处理为:先溅射alsi10~20min,后氩离子溅射1~5min,然后继续溅射alsi10~20min,再氩离子溅射1~5min,如此反复5~10次。
15.优选的,步骤(3)中,磁控溅射sio2层的方法为:调节靶材与步骤(2)制得的表面附有alsi层的镁合金试样的距离为100mm,抽真空,通氩气,对靶材进行溅射清洗,待靶材溅射清洗结束后,调节氩气流量和真空室气压,同时再通氧气,在步骤(2)制得的表面附有alsi层的镁合金试样的表面磁控溅射sio2层。
16.进一步优选的,氩气纯度≥99.999%。
17.进一步优选的,靶材溅射清洗参数为:真空度1
×
10-4
~5
×
10-4
pa,氩气流量为100~250sccm,溅射清洗时间5~30min。
18.进一步优选的,氧气纯度≥99.999%。
19.进一步优选的,溅射sio2层的参数为:氩气流量20~40sccm,氩气和氧气的流量比(5~10):1,真空室气压0.7~2.0pa,溅射功率40~200w,溅射温度为室温,溅射时间为50~150min。
20.本发明的第二方面,提供了一种镁合金表面超疏水复合膜层,所述超疏水复合膜层为在镁合金基体上,由内向外,依次设置alsi层和sio2层,形成alsi/sio2复合膜层。
21.本发明的有益效果:1.本发明采用磁控溅射法在镁合金表面沉积生成具有超疏水性的alsi/sio2膜层。由于磁控溅射形成alsi层的过程中结合了氩离子刻蚀,以及al、si本身原子结构上易与基体mg原子及o原子结合的特点,不仅使得膜层与镁合金基体有良好的结合,同时也保证了膜层内部良好的结合。
22.2.本发明采用磁控溅射法制备的alsi/sio2膜层表面无明显的孔隙,表面粗糙度较小,同时生成纳米级的sio2微结构,膜层润湿接触角明显较大,达到157.5
°
,使得膜层表面具有较好的超疏水性能,因此,可以很好地阻碍环境中腐蚀介质对镁合金基体的腐蚀,同时也促进了镁合金在超疏水领域的其他应用。
附图说明
23.图1:实施例1所得alsi/sio2膜层及对比例1所得mao膜层的扫描电镜照片,其中a为mao膜层表面微观形貌,b为alsi/sio2膜层表面微观形貌;图2:实施例1所得alsi/sio2膜层及对比例1所得mao膜层表面微观三维轮廓;图3:实施例2所得alsi/sio2膜层、对比例1所得mao膜层、对比例2所得alsi膜层及
对比例3所得sio2膜层表面润湿性接触角的测试结果;图4:实施例2所得alsi/sio2膜层、对比例1所得mao膜层、对比例2所得alsi膜层、对比例3所得sio2膜层及对照组镁合金基体的动电位极化测试曲线。
实施方式
24.应该指出,以下详细说明都是例示性的,旨在对本技术提供进一步的说明。除非另有指明,本文使用的所有技术和科学术语具有与本技术所属技术领域的普通技术人员通常理解的相同含义。
25.正如背景技术所述,由于镁合金化学活性高,易氧化,在使用过程中极易发生腐蚀,在实际使用过程中,需要采用一定的表面处理工艺来提高其表面耐腐蚀性能,现有技术中,常常采用微弧氧化(mao)在镁合金表现生成一层膜,但微弧氧化膜层表面存在一定的孔隙,且粗糙度大,亲水性大,限制了镁合金耐腐蚀性能的进一步提高。
26.基于此,本发明提供了一种基于磁控溅射的镁合金表面超疏水复合膜层及其制备方法。在磁控溅射过程中结合氩离子刻蚀,制得镁合金表面alsi/sio2超疏水复合膜层,膜层表面无明显孔隙,表面粗糙度小,且生成纳米级的sio2微结构,alsi/sio2超疏水复合膜层的润湿接触角可达157.5
°
。
27.为了使得本领域技术人员能够更加清楚地了解本技术的技术方案,以下将结合具体的实施例详细说明本技术的技术方案。
28.本发明实施例中所用的试验材料均为本领域常规的试验材料,均可通过商业渠道购买得到。
29.实施例1:镁合金表面超疏水复合膜层的制备(1)将az91d镁合金试样依次用400#、800#、1500#的砂纸打磨,再经抛光处理后,依次放入丙酮、去离子水和无水乙醇中各超声波清洗5min,吹干,备用;(2)将步骤(1)表面预处理后的镁合金放入磁控溅射真空室中,四个靶位交替放入两个纯度为99.99%的al靶材和两个纯度为99.99%的si靶材,调节靶材与镁合金试样的距离为80mm后,抽真空至真空度为1.5
×
10-4
pa,通入纯度为99.999%的氩气,氩气流量为150sccm,对al靶材和si靶材进行溅射清洗15min;待靶材溅射清洗结束后,调节真空室气压为1.0pa,氩气流量为40sccm,并结合氩离子刻蚀,于40w的溅射功率和室温下,在步骤(1)表面处理后的镁合金磁控溅射上一层alsi层;其中,氩离子刻蚀处理为:先溅射alsi10min,后氩离子溅射2min,然后继续溅射alsi10min,再氩离子溅射2min,如此反复6次;(3)打开磁控溅射真空室,将两个al靶更换为纯度为99.99%的si靶,调节靶材与步骤(2)制得的表面附有alsi层的镁合金试样的距离为100mm,抽真空至为1.5
×
10-4
pa,通入纯度为99.999%的氩气,氩气流量为150sccm,对si靶材进行溅射清洗15min;待靶材溅射清洗结束后,调节真空室气压为1.0pa,氩气流量为40sccm,同时再通入纯度为99.999%的氧气,保证氩气和氧气的流量比5:1,于室温和溅射功率为65w的条件下,在步骤(2)表面附着alsi层的镁合金试样的表面磁控溅射sio2层,磁控溅射时间为60min,取出镁合金试样,即得镁合金表面超疏水复合膜层。
30.实施例2:镁合金表面超疏水复合膜层的制备(1)将az91d镁合金试样依次用400#、800#、1500#的砂纸打磨,再经抛光处理后,依次放入丙酮、去离子水和无水乙醇中各超声波清洗4min,吹干,备用;(2)将步骤(1)表面预处理后的镁合金放入磁控溅射真空室中,四个靶位放入两个纯度为99.99%的al靶材和两个纯度为99.99%的si靶材,调节靶材与镁合金试样的距离为80mm后,抽真空至真空度为2
×
10-4
pa,通入纯度为99.999%的氩气,氩气流量为130sccm,对al靶材和si靶材进行溅射清洗20min;待靶材溅射清洗结束后,调节真空室气压为1.0pa,氩气流量为35sccm,并结合氩离子刻蚀,于50w的溅射功率和室温下,对表面处理后的镁合金磁控溅射上alsi层;其中,氩离子刻蚀处理为:先溅射alsi15min,后氩离子溅射3min,然后继续溅射alsi 15min,再氩离子溅射3min,如此反复5次;(3)打开磁控溅射真空室,将两个al靶更换为纯度为99.99%的si靶,调节靶材与步骤(2)制得的表面附有alsi层的镁合金试样的距离为100mm,抽真空至为2
×
10-4
pa,通入纯度为99.999%的氩气,氩气流量为130sccm,对si靶材进行溅射清洗20min;待靶材溅射清洗结束后,调节真空室气压为1.0pa,氩气流量为40sccm,同时再通入纯度为99.999%的氧气,保证氩气和氧气的流量比6:1,于室温和溅射功率为80w下,在步骤(2)表面附着alsi膜的镁合金试样的表面磁控溅射一层sio2层,磁控溅射时间为70min,取出镁合金试样,即得镁合金表面超疏水复合膜层。
31.实施例3:镁合金表面超疏水复合膜层的制备(1)将az91d镁合金试样依次用400#、800#、1500#的砂纸打磨,再经抛光处理后,依次放入丙酮、去离子水和无水乙醇中各超声波清洗3min,吹干,备用;(2)将步骤(1)表面预处理后的镁合金放入磁控溅射真空室中,四个靶位放入两个纯度为99.99%的al靶材和两个纯度为99.99%的si靶材,调节靶材与镁合金试样的距离为80mm后,抽真空至真空度为3
×
10-4
pa,通入纯度为99.999%的氩气,氩气流量为120sccm,对al靶材和si靶材进行溅射清洗15min;待靶材溅射清洗结束后,调节真空室气压为1.1pa,氩气流量为45sccm,并结合氩离子刻蚀,于60w的溅射功率和室温下,对表面处理后的镁合金磁控溅射上alsi层;其中,氩离子刻蚀处理为:先溅射alsi10min,后氩离子溅射4min,然后继续溅射alsi10min,再氩离子溅射4min,如此反复5次;(3)打开磁控溅射真空室,将两个al靶更换为纯度为99.99%的si靶,调节靶材与步骤(2)制得的表面附有alsi层的镁合金试样的距离为100mm,抽真空至为3
×
10-4
pa,通入纯度为99.999%的氩气,氩气流量为120sccm,对si靶材进行溅射清洗15min;待靶材溅射清洗结束后,调节真空室气压为1.0pa,氩气流量为30sccm,同时再通入纯度为99.999%的氧气,保证氩气和氧气的流量比7:1,于室温和溅射功率为100w下,在步骤(2)表面附着alsi膜的镁合金试样的表面磁控溅射sio2层,磁控溅射时间为70min,取出镁合金试样,即得镁合金表面超疏水复合膜层。
32.实施例4:镁合金表面超疏水复合膜层的制备(1)将az31镁合金试样依次用400#、800#、1500#的砂纸打磨,再经抛光处理后,依次放入丙酮、去离子水和无水乙醇中各超声波清洗3min,吹干,备用;
(2)将步骤(1)表面预处理后的镁合金放入磁控溅射真空室中,四个靶位放入两个纯度为99.99%的al靶材和两个纯度为99.99%的si靶材,调节靶材与镁合金试样的距离为80mm后,抽真空至真空度为5
×
10-4
pa,通入纯度为99.999%的氩气,氩气流量为250sccm,对al靶材和si靶材进行溅射清洗5min;待靶材溅射清洗结束后,调节真空室气压为1.5pa,氩气流量为60sccm,并结合氩离子刻蚀,于150w的溅射功率和室温下,对表面处理后的镁合金磁控溅射上一层alsi层;其中,氩离子刻蚀处理为:先溅射alsi20min,后氩离子溅射1min,然后继续溅射alsi20min,再氩离子溅射1min,如此反复10次;(3)打开磁控溅射真空室,将两个al靶更换为纯度为99.99%的si靶,调节靶材与步骤(2)制得的表面附有alsi层的镁合金试样的距离为100mm,抽真空至为5
×
10-4
pa,通入纯度为99.999%的氩气,氩气流量为250sccm,对si靶材进行溅射清洗5min;待靶材溅射清洗结束后,调节真空室气压为2.0pa,氩气流量为40sccm,同时再通入纯度为99.999%的氧气,保证氩气和氧气的流量比10:1,于室温和溅射功率为200w下,在步骤(2)表面附着alsi膜的镁合金试样的表面磁控溅射一层sio2膜,磁控溅射时间为50min,取出镁合金试样,即得镁合金表面超疏水复合膜层。
33.实施例5:镁合金表面超疏水复合膜层的制备(1)将am60镁合金试样依次用400#、800#、1500#的砂纸打磨,再经抛光处理后,依次放入丙酮、去离子水和无水乙醇中各超声波清洗10min,吹干,备用;(2)将步骤(1)表面预处理后的镁合金放入磁控溅射真空室中,四个靶位放入两个纯度为99.99%的al靶材和两个纯度为99.99%的si靶材,调节靶材与镁合金试样的距离为80mm后,抽真空至真空度为1
×
10-4
pa,通入纯度为99.999%的氩气,氩气流量为100sccm,对al靶材和si靶材进行溅射清洗30min;待靶材溅射清洗结束后,调节真空室气压为0.8pa,氩气流量为30sccm,并结合氩离子刻蚀,于30w的溅射功率和室温下,对表面处理后的镁合金磁控溅射上一层alsi层;其中,氩离子刻蚀处理为:先溅射alsi20min,后氩离子溅射5min,然后继续溅射alsi20min,再氩离子溅射5min,如此反复5次;(3)打开磁控溅射真空室,将两个al靶更换为纯度为99.99%的si靶,调节靶材与步骤(2)制得的表面附有alsi层的镁合金试样的距离为100mm,抽真空至为1
×
10-4
pa,通入纯度为99.999%的氩气,氩气流量为100sccm,对si靶材进行溅射清洗30min;待靶材溅射清洗结束后,调节真空室气压为0.7pa,氩气流量为20sccm,同时再通入纯度为99.999%的氧气,保证氩气和氧气的流量比5:1,于室温和溅射功率为40w下,在步骤(2)表面附着alsi膜的镁合金试样的表面磁控溅射一层sio2膜,磁控溅射时间为150min,取出镁合金试样,即得镁合金表面超疏水复合膜层。
34.实施例6:镁合金表面超疏水复合膜层的制备(1)将we43镁合金试样依次用400#、800#、1500#的砂纸打磨,再经抛光处理后,依次放入丙酮、去离子水和无水乙醇中各超声波清洗6min,吹干,备用;(2)将步骤(1)表面预处理后的镁合金放入磁控溅射真空室中,四个靶位交替放入两个纯度为99.99%的al靶材和两个纯度为99.99%的si靶材,调节靶材与镁合金试样的距离为80mm后,抽真空至真空度为3
×
10-4
pa,通入纯度为99.999%的氩气,氩气流量为175sccm,
对al靶材和si靶材进行溅射清洗18min;待靶材溅射清洗结束后,调节真空室气压为1.1pa,氩气流量为45sccm,并结合氩离子刻蚀,于90w的溅射功率和室温下,对表面处理后的镁合金磁控溅射上一层alsi层;其中,氩离子刻蚀处理为:先溅射alsi15min,后氩离子溅射3min,然后继续溅射alsi15min,再氩离子溅射3min,如此反复7次;(3)打开磁控溅射真空室,将两个al靶更换为纯度为99.99%的si靶,调节靶材与步骤(2)制得的表面附有alsi层的镁合金试样的距离为100mm,抽真空至为3
×
10-4
pa,通入纯度为99.999%的氩气,氩气流量为175sccm,对si靶材进行溅射清洗18min;待靶材溅射清洗结束后,调节真空室气压为1.3pa,氩气流量为30sccm,同时再通入纯度为99.999%的氧气,保证氩气和氧气的流量比7:1,于室温和溅射功率为120w下,在步骤(2)表面附着alsi膜的镁合金试样的表面磁控溅射一层sio2层,磁控溅射时间为60min,取出镁合金试样,即得镁合金表面超疏水复合膜层。
35.对比例1:采用微弧氧化法制备镁合金表面mao膜层(1)镁合金试样进行表面预处理,依次用400#、800#、1500#砂纸打磨,然后进行抛光处理,随后依次放入丙酮、去离子水、无水乙醇中各超声波清洗4min,最后吹干。
36.(2)镁合金试样浸入15g/l硅酸钠、12g/l氟化钾、3g/l氢氧化钠、10ml/l甘油所组成电解液中进行处理,电源脉冲频率700hz,占空比25%,电压400v,处理20min,即得镁合金表面mao膜层。
37.对比例2:磁控溅射制备镁合金表面alsi膜层(1)将az91d镁合金试样依次用400#、800#、1500#的砂纸打磨,再经抛光处理后,依次放入丙酮、去离子水和无水乙醇中各超声波清洗4min,吹干,备用;(2)将步骤(1)表面预处理后的镁合金放入磁控溅射真空室中,四个靶位放入两个纯度为99.99%的al靶材和两个纯度为99.99%的si靶材,调节靶材与镁合金试样的距离为80mm后,抽真空至真空度为2
×
10-4
pa,通入纯度为99.999%的氩气,氩气流量为130sccm,对al靶材和si靶材进行溅射清洗20min;待靶材溅射清洗结束后,调节真空室气压为1.0pa,氩气流量为35sccm,并结合氩离子刻蚀,于50w的溅射功率和室温下,对镁合金表面磁控溅射上一层alsi层,取出镁合金试样,即得镁合金表面alsi膜;其中,氩离子刻蚀处理为:先溅射alsi15min,后氩离子溅射3min,然后继续溅射alsi15min,再氩离子溅射3min,如此反复5次。
38.对比例3:磁控溅射制备镁合金表面sio2膜层(1)将az91d镁合金试样依次用400#、800#、1500#的砂纸打磨,再经抛光处理后,依次放入丙酮、去离子水和无水乙醇中各超声波清洗4min,吹干,备用;(2)将步骤(1)表面预处理后的镁合金放入磁控溅射真空室中,四个靶位均放入纯度为99.99%的si靶材,调节靶材与步骤(1)制得的表面预处理后的镁合金试样的距离为100mm,抽真空至为2
×
10-4
pa,通入纯度为99.999%的氩气,氩气流量为130sccm,对si靶材进行溅射清洗20min;待靶材溅射清洗结束后,调节真空室气压为1.0pa,氩气流量为40sccm,同时再通入纯度为99.999%的氧气,保证氩气和氧气的流量比6:1,于室温和溅射功率为80w下,在镁
实施例2(alsi/sio2复合膜)-1.246.76
×
10-8
7.12
×
105对比例1(mao膜层)-1.267.33
×
10-7
7.50
×
104对比例2(alsi膜层)-1.312.45
×
10-7
2.31
×
105对比例3(sio2膜层)-1.392.23
×
10-5
3.06
×
103根据电化学相关理论可知,腐蚀电位越正,发生腐蚀的热力学可能性越小,而腐蚀电流密度越小、极化电阻越大,发生腐蚀的动力学可能性越小,表明材料的耐蚀性能越好。从图4及表1可以看出,与镁合金基体相比,对比例1基于微弧氧化制得镁合金mao膜、对比例2磁控溅射所得alsi膜层、对比例3磁控溅射所得sio2膜层及本发明制备的镁合金表面alsi/sio2超疏水复合膜层均使得腐蚀电位正移,腐蚀电流密度减小,同时极化电阻增大,说明四个膜层均增大了镁合金基体的耐腐蚀性能。
49.而进一步比较四个膜层可以看出,相较于无疏水性能的对比例1所得mao膜层和对比例2所得alsi膜层,本发明所得镁合金表面alsi/sio2超疏水复合膜层使得腐蚀电流密度的减小程度更大,均多减小了1个数量级,同时,极化电阻增大的程度也更大,分别多增加了1个数量级及2倍多,这说明本发明制备的镁合金表面alsi/sio2超疏水复合膜层由于其优异的超疏水性,显著提高了镁合金的耐腐蚀性能;而与有一定疏水性能的对比例3所得sio2膜层相比,本发明所得复合膜层的耐蚀优势更加明显,腐蚀电流密度减少程度达3个数量级,极化电阻增大了2个数量级,原因是对比例3所得sio2膜虽然具有一定的疏水性能,但由于缺少alsi膜层的协同作用,腐蚀介质较容易穿透sio2膜到达镁合金基体,因而其耐蚀性能提升幅度很小,这更充分地体现了本发明所得alsi/sio2复合膜层的性能优势。
50.综上所述,本发明提供了一种镁合金表面制备超疏水复合膜层的方法。所制备的膜层表面分布有纳米级微结构及较小的表面粗糙度,超疏水性能十分优异。
51.以上所述仅为本技术的优选实施例而已,并不用于限制本技术,对于本领域的技术人员来说,本技术可以有各种更改和变化。凡在本技术的精神和原则之内,所作的任何修改、等同替换、改进等,均应包含在本技术的保护范围之内。