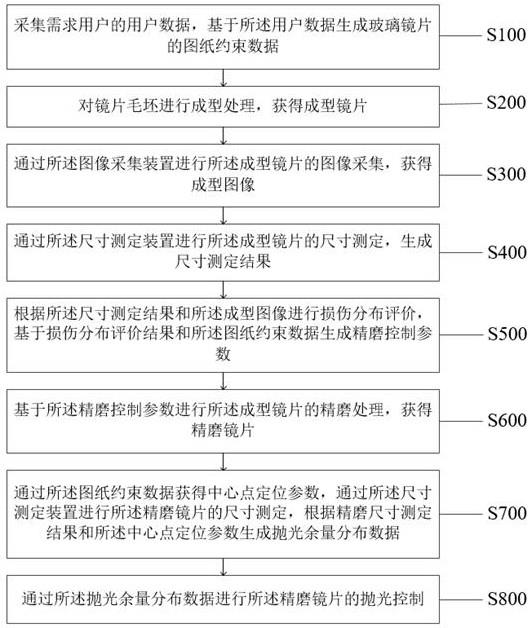
1.本技术涉及镜片生产控制技术领域,尤其涉尺寸及一种提高光学玻璃镜片打磨精度的方法及系统。
背景技术:2.随着高新技术的不断研发,以及人们对于镜片材料的研究不断升入,光学镜片研发不断取得突破。同时,随着消费需求的不断升级,人们越来越重视镜片质量,因此,研究光学玻璃镜片的打磨情况对于提升人们生活质量有着十分重要的意义。
3.目前,通过对镜片毛坯进行打磨,通过对成型后的镜片进行质量检测,然后通过人工分析镜片打磨的情况,得到反馈结果,主要是通过技术人员人工对打磨过程进行控制,来实现保证镜片的打磨精度。然而,在镜片打磨的过程中需要控制的参数众多,仅仅通过人工控制无法保证镜片打磨精度。现有技术中存在玻璃镜片打磨精度低,镜片质量低的技术问题。
技术实现要素:4.本技术的目的是提供一种提高光学玻璃镜片打磨精度的方法及系统,用以解决现有技术中存在玻璃镜片打磨精度低,镜片质量低的技术问题。
5.鉴于上述问题,本技术提供了一种提高光学玻璃镜片打磨精度的方法及系统。
6.第一方面,本技术提供了一种提高光学玻璃镜片打磨精度的方法,其中,所述方法应用于智能控制系统,所述智能控制系统与图像采集装置、尺寸测定装置通信连接,所述方法包括:采集需求用户的用户数据,基于所述用户数据生成玻璃镜片的图纸约束数据;对镜片毛坯进行成型处理,获得成型镜片;通过所述图像采集装置进行所述成型镜片的图像采集,获得成型图像;通过所述尺寸测定装置进行所述成型镜片的尺寸测定,生成尺寸测定结果;根据所述尺寸测定结果和所述成型图像进行损伤分布评价,基于损伤分布评价结果和所述图纸约束数据生成精磨控制参数;基于所述精磨控制参数进行所述成型镜片的精磨处理,获得精磨镜片;通过所述图纸约束数据获得中心点定位参数,通过所述尺寸测定装置进行所述精磨镜片的尺寸测定,根据精磨尺寸测定结果和所述中心点定位参数生成抛光余量分布数据;通过所述抛光余量分布数据进行所述精磨镜片的抛光控制。
7.另一方面,本技术还提供了一种提高光学玻璃镜片打磨精度的系统,其中,所述系统包括:约束数据采集模块,所述约束数据采集模块用于采集需求用户的用户数据,基于所述用户数据生成玻璃镜片的图纸约束数据;成型镜片获得模块,所述成型镜片获得模块用于对镜片毛坯进行成型处理,获得成型镜片;成型图像获得模块,所述成型图像获得模块用于通过图像采集装置进行所述成型镜片的图像采集,获得成型图像;尺寸测定模块,所述尺寸测定模块用于通过尺寸测定装置进行所述成型镜片的尺寸测定,生成尺寸测定结果;精磨参数获得模块,所述精磨参数获得模块用于根据所述尺寸测定结果和所述成型图像进行损伤分布评价,基于损伤分布评价结果和所述图纸约束数据生成精磨控制参数;精磨镜片
获得模块,所述精磨镜片获得模块用于基于所述精磨控制参数进行所述成型镜片的精磨处理,获得精磨镜片;分布数据获得模块,所述分布数据获得模块用于通过所述图纸约束数据获得中心点定位参数,通过所述尺寸测定装置进行所述精磨镜片的尺寸测定,根据精磨尺寸测定结果和所述中心点定位参数生成抛光余量分布数据;抛光控制模块,所述抛光控制模块用于通过所述抛光余量分布数据进行所述精磨镜片的抛光控制。
8.本技术中提供的一个或多个技术方案,至少具有如下技术效果或优点:本技术通过对需求用户的用户数据进行采集,基于用户数据得到玻璃镜片的图纸约束数据,进而对镜片毛坯进行成型处理,获得成型镜片,采集成型镜片的图像,获得成型图像,通过尺寸测定装置对成型镜片的尺寸进行测定,得到尺寸测定结果,然后根据尺寸测定结果和成型图像对镜片的损伤分布进行评价,进而基于根据损伤分布评价结果,结合图纸约束数据得到精磨控制参数,然后根据精磨控制参数对成型镜片进行精磨处理,得到精磨镜片,通过根据图纸约束数据获得中心点定位参数,对精磨镜片的尺寸进行测定,根据精磨尺寸测定结果和中心点定位参数得到抛光余量分布数据,从而根据抛光余量分布数据进行精磨镜片的抛光控制。达到了对玻璃镜片进行打磨控制,提高打磨精度,保证镜片质量的技术效果。
附图说明
9.为了更清楚地说明本技术或现有技术中的技术方案,下面将对实施例或现有技术描述中所需要使用的附图作简单地介绍,显而易见地,下面描述中的附图仅仅是示例性的,对于本领域普通技术人员来讲,在不付出创造性劳动的前提下,还可以根据提供的附图获得其他的附图。
10.图1为本技术实施例提供的一种提高光学玻璃镜片打磨精度的方法的流程示意图;图2为本技术实施例提供的一种提高光学玻璃镜片打磨精度的方法中获得损伤分布评价结果的流程示意图;图3为本技术实施例提供的一种提高光学玻璃镜片打磨精度的方法中根据权重约束结果生成精磨设备的精磨去除量数据的流程示意图;图4为本技术一种提高光学玻璃镜片打磨精度的系统的结构示意图。
11.附图标记说明:约束数据采集模块11,成型镜片获得模块12,成型图像获得模块13,尺寸测定模块14,精磨参数获得模块15,精磨镜片获得模块16,分布数据获得模块17,抛光控制模块18。
具体实施方式
12.本技术通过提供一种提高光学玻璃镜片打磨精度的方法及系统,解决了现有技术中存在玻璃镜片打磨精度低,镜片质量低的技术问题,达到了提高玻璃镜片打磨精度控制质量,提高打磨参数控制参数准确度的技术效果。
13.本技术技术方案中对数据的获取、存储、使用、处理等均符合法律法规的相关规定。
14.下面,将参考附图对本技术中的技术方案进行清楚、完整地描述,显然,所描述的
实施例仅是本技术的一部分实施例,而不是本技术的全部实施例,应理解,本技术不受这里描述的示例实施例的限制。基于本技术的实施例,本领域普通技术人员在没有做出创造性劳动前提下所获得的所有其他实施例,都属于本技术保护的范围。另外还需要说明的是,为了便于描述,附图中仅示出了与本技术相关的部分而非全部。
15.实施例一如图1所示,本技术提供了一种提高光学玻璃镜片打磨精度的方法,其中,所述方法应用于智能控制系统,所述智能控制系统与图像采集装置、尺寸测定装置通信连接,所述方法包括:步骤s100:采集需求用户的用户数据,基于所述用户数据生成玻璃镜片的图纸约束数据;具体而言,所述需求用户是指需要光学玻璃镜片作为眼镜的材料的用户。所述用户数据是指反映需求用户的眼睛情况,与玻璃镜片的需求相关的数据,包括:瞳高、总瞳距、镜片度数,镜片轴位等。所述图纸约束数据是根据用户数据得到玻璃镜片的图纸上反映镜片结构的相关数据,包括:镜片厚度、镜片直径、镜片中心点位置等。由此,达到了为后续根据图纸约束数据对镜片的中心点进行定位提供参考依据的技术效果。
16.步骤s200:对镜片毛坯进行成型处理,获得成型镜片;进一步的,本技术实施例步骤s200还包括:步骤s210:获得成型处理的成型设置数据;步骤s220:根据所述损伤分布评价结果和所述尺寸测定结果生成成型控制评价数据;步骤s230:根据所述成型控制评价数据和所述成型设置数据进行成型控制偏离评价,生成偏离控制评价结果;步骤s240:通过所述偏离控制评价结果进行后续成型处理的控制优化。
17.具体而言,通过对所述镜片毛坯进行成型处理,通过将铸形透镜毛坯安装在绕玻璃圆盘的机械中心旋转的卡盘内,用内嵌金刚石的环形工具去除毛坯材料并研磨毛坯的表面,得到成型镜片。所述成型设置数据是通过对镜片毛坯进行成型处理时的操作数据,包括研磨参数、成型直径、成型厚度等。根据获得的损伤分布评价结果和尺寸测定结果可以对成型镜片的成型情况进行评价,得到所述成型控制评价数据。其中,所述成型控制评价数据是对成型后的镜片情况进行评价得到的。通过对比所述成型控制评价数据和所述成型设置数据,可以得到成型处理时结果与预设结果的偏离程度,通过对各项参数进行对比,可以得到所述偏离控制评价结果。其中,所述偏离控制评价结果是指成型过程中由于内部因素和外部因素导致成型结果与预期结果之间的偏离程度。所述内部因素是指由于镜片材质,导致按照原有的设置参数无法将镜片处理成预期结果。所述外部因素是指由于成型设备的因素导致存在加工误差。进而,根据所述偏离控制评价结果可以对后续成型过程进行优化调整,达到了提高成型质量的技术效果。
18.步骤s300:通过所述图像采集装置进行所述成型镜片的图像采集,获得成型图像;步骤s400:通过所述尺寸测定装置进行所述成型镜片的尺寸测定,生成尺寸测定结果;具体而言,所述图像采集装置是指对成型镜片的图像进行采集的装置,包括摄像
机、照相机、红外摄像仪等。所述成型图像是对所述成型镜片进行多角度图像采集后得到能够反映镜片加工情况的图像。所述尺寸测定装置是指对成型镜片的尺寸进行测定的装置,包括卡尺、卷尺等。所述尺寸测定结果是反映成型镜片的成型情况,对各个结构的尺寸进行采集后得到的,包括镜片厚度、镜片直径、镜片规整度等。通过对成型镜片的图像和尺寸进行采集,达到了后续分析成型镜片的成型情况提供基础分析数据的技术效果。
19.步骤s500:根据所述尺寸测定结果和所述成型图像进行损伤分布评价,基于损伤分布评价结果和所述图纸约束数据生成精磨控制参数;进一步的,如图2所示,本技术实施例步骤s500还包括:步骤s510:构建缺陷识别特征集合;步骤s520:通过所述缺陷识别特征集合进行所述成型图像的缺陷匹配,获得缺陷匹配结果;步骤s530:根据所述缺陷匹配结果生成缺陷分布位置和缺陷深度参数;步骤s540:根据所述尺寸测定结果、所述缺陷分布位置和所述缺陷深度参数进行损伤分布评价,获得所述损伤分布评价结果。
20.具体而言,所述损伤分布评价是指经过成型处理中的粗磨后,镜片与最终要达到的镜片效果之间存在差距的点的分布情况,为后续的精磨提供依据。根据损伤分布评价结果可以获得需要进行精磨的位置,通过根据所述图纸约束数据可以获得精磨要达到的镜片效果,进而通过损伤分布评价结果和图纸约束数据可以得到所述精磨控制参数。其中,所述精磨控制参数是指对成型镜片进行精磨时的相关控制参数,包括镜片去除量、中心点、镜片倒角度数等。
21.具体的,所述缺陷识别特征集合是指镜片表面的镜片损伤特征集合,包括划痕、麻点、缺口等。通过根据所述缺陷识别特征集合对所述成型图像进行识别,对成型图像中的缺陷进行匹配,得到所述缺陷匹配结果。其中,所述缺陷匹配结果是指成型镜片中所包含的需要处理的缺陷情况。进而,在获得所述缺陷匹配结果后,对缺陷的位置进行确定得到所述缺陷分布位置,对缺陷深度进行采集得到所述缺陷深度参数。通过根据所述尺寸测定结果、所述缺陷分布位置和所述缺陷深度参数对损伤分布情况进行评价,得到所述损伤分布评价结果。其中,所述损伤分布评价结果是指对成型镜片不同位置的缺陷进行分析确定得到的。达到了为后续精磨提供打磨数据的技术效果。
22.进一步的,如图3所示,本技术实施例步骤s510还包括:步骤s550:获得精磨设备的测试样品的样品去除量数据;步骤s560:获得所述精磨设备的历史去除量数据,其中,所述历史去除量数据带有时间标识;步骤s570:根据所述时间标识进行所述历史去除量数据的权重约束,根据权重约束结果生成精磨设备的精磨去除量数据;步骤s580:根据所述样品去除量数据进行所述精磨去除量数据的去除修正,根据去除修正结果、所述损伤分布评价结果和所述图纸约束数据生成所述精磨控制参数。
23.进一步的,本技术实施例步骤s570还包括:步骤s571:获得所述精磨设备的预设评价周期;步骤s572:通过所述预设评价周期进行所述历史去除量数据的权重分布,获得时
间权重分布结果;步骤s573:根据所述时间权重分布结果进行所述历史去除量数据的权重约束,获得权重约束结果。
24.具体而言,所述精磨设备是用于对成型镜片进行精细研磨的设备。所述测试样品是用于对精磨设备的研磨性能进行测试的样本玻璃镜片。所述样品去除量数据是指经过所述精磨设备对测试样品进行研磨后,测试样品加工前后相差的数据。所述历史去除量数据是指所述精磨设备在历史使用过程中对加工镜片的去除量,其中,所述历史去除量数据带有时间标识,时间标识与所述历史去除量数据一一对应。因为,精磨设备在使用过程中由于零部件的磨损、老化,导致设备性能随着使用时间的延长而下降。因此,对历史去除量数据进行分析,数据的可靠性随着时间的远近而有所不同,距离当前时间越久的历史去除量数据,可靠性越低。
25.具体的,所述预设评价周期是指对所述精磨设备的性能进行周期性评价的时间段,一般按照工作面的数量乘以研磨工作时的使用时长得到。按照所述预设评价周期,以及根据所述历史去除量数据对应的时间标识,获得所述时间权重分布结果。其中,所述时间权重分布结果是根据历史去除量数据以时间为依据进行权重分配得到的。所述权重约束结果是根据所述时间权重分布结果与对应的历史去除量数据分别进行加权得到的。进而,根据所述权重约束结果可以得到所述精磨设备的精磨去除量数据。其中,所述精磨去除量数据反映了精磨设备整体的加工性能。通过根据所述样品去除量数据与所述精磨去除量数据进行对比计算,得到所述去除修正结果。其中,所述去除修正结果可以准确反映所述精磨设备对镜片的去除情况。进而,根据精磨设备的加工性能即所述去除修正结果,以及能够反映镜片需要精磨加工情况的所述损伤分布评价结果和反映镜片加工需求的所述图纸约束数据得到所述精磨控制参数。由此,达到了对玻璃镜片的精磨控制参数进行准确设定,提高精磨精度,进而提高打磨质量的技术效果。
26.步骤s600:基于所述精磨控制参数进行所述成型镜片的精磨处理,获得精磨镜片;步骤s700:通过所述图纸约束数据获得中心点定位参数,通过所述尺寸测定装置进行所述精磨镜片的尺寸测定,根据精磨尺寸测定结果和所述中心点定位参数生成抛光余量分布数据;具体而言,通过所述精磨控制参数控制精磨设备对所述成型镜片进行加工,得到所述精磨镜片。所述中心点定位参数是镜片的中心点,可以使镜片的光轴和机械轴重合。所述精磨尺寸测定结果是指精磨镜片的尺寸情况。所述抛光余量分布数据是通过根据所述中心点定位参数进行镜片定中心,在定中心后根据所述精磨尺寸测定结果确定将镜片研磨至最终直径时的镜片各个部位的抛光余量数据。
27.步骤s800:通过所述抛光余量分布数据进行所述精磨镜片的抛光控制。
28.进一步的,本技术实施例步骤s800还包括:步骤s810:获得预设抛光频次信息;步骤s820:根据所述预设抛光频次信息进行所述抛光余量分布数据的单次抛光量评价,生成单次抛光量评价分布结果;步骤s830:判断所述单次抛光量评价分布结果中的抛光量差值是否存在不满足预设去除阈值的结果;
步骤s840:当存在时,则根据不满足预设去除阈值的结果的数量进行抛光频次新增,基于新增后的抛光频次和所述预设去除阈值进行抛光控制。
29.进一步的,本技术实施例步骤s800还包括:步骤s850:设定处理精度和处理成本的平衡参数;步骤s860:将所述平衡参数、所述抛光余量分布数据输入抛光控制模型,获得模型输出结果,其中,所述模型输出结果包括抛光频次和抛光量数据;步骤s870:基于所述模型输出结果进行所述精磨镜片的抛光控制。
30.具体而言,所述预设抛光频次信息是根据抛光设备的性能以及抛光余量分布数据得到对所述精磨镜片进行抛光的预设次数。进而,根据所述预设抛光频次信息确定单次抛光量分布情况,按照所述抛光余量分布数据,得到每一次对所述精磨镜片进行抛光后镜片的单次抛光量评价分布结果。由于抛光设备的单次抛光去除量是一定的,但是由于镜片余量分布的位置不同,因此,每次抛光后,镜片不同位置的抛光量差值不同。所述预设去除阈值时按照抛光余量分布数据确定的单次抛光需要去除的最低值。当所述单次抛光量评价分布结果中的抛光量差值存在不满足预设去除阈值的结果时,按照不满足的数量和与预设去除阈值的差值情况,增加抛光频次,从而根据新增后的抛光频次和所述预设去除阈值对所述精磨镜片进行抛光控制。
31.具体的,在进行镜片抛光的过程中,抛光次数的增加虽然可以提高镜片打磨精度,但是经济成本和时间成本也会随之增加,因此,在进行抛光处理的过程中,既需要考虑处理进度,也要考虑处理成本。所述抛光控制模型是用来对抛光过程中的参数进行控制的功能模型。所述平衡参数是指在处理精度和处理成本中取一相对比较平衡的控制参数。进而,通过将所述平衡参数、所述抛光余量分布数据输入所述抛光模型中,得到所述模型输出结果,即抛光频次和抛光量数据。其中,所述抛光频次是抛光处理的次数,所述抛光量数据是指单次抛光量和抛光总量。
32.具体的,获取抛光处理的历史时间段内的历史数据,包括历史平衡参数和历史抛光余量分布数据,历史抛光频次和历史抛光量数据。将所述平衡参数和所述抛光余量分布数据,所述历史抛光频次和所述历史抛光量数据作为训练数据,对所述抛光控制模型进行监督训练、验证和测试,直至模型的准确度满足要求,得到所述抛光控制模型。由此,达到了提高抛光控制参数的精准度,提高抛光参数的设置效率,进而提高镜片打磨质量的技术效果。
33.综上所述,本技术所提供的一种提高光学玻璃镜片打磨精度的方法具有如下技术效果:本技术通过获取需求用户的用户数据,进而得到玻璃镜片的图纸约束数据,实现了根据需求用户的情况进行特定化的镜片数据设定的目标,然后通过对镜片毛坯进行成型处理,进行成型镜片的图像采集和尺寸测定,根据尺寸测定结果和成型图像对成型镜片中的损伤分布进行评价,实现对成型镜片的损伤情况进行分析评价的目标,然后根据损伤分布评价结果和图纸约束数据得到精磨控制参数,对成型镜片进行精磨处理,根据图纸约束数据得到中心点定位参数,进一步的对精磨镜片进行尺寸测定,按照精磨尺寸测定结果结合中心点定位参数得到抛光余量分布数据,对精磨镜片进行抛光控制。达到了提高镜片打磨质量,提高镜片打磨精度的技术效果。
34.实施例二基于与前述实施例中一种提高光学玻璃镜片打磨精度的方法同样的发明构思,如图4所示,本技术还提供了一种提高光学玻璃镜片打磨精度的系统,其中,所述系统包括:约束数据采集模块11,所述约束数据采集模块11用于采集需求用户的用户数据,基于所述用户数据生成玻璃镜片的图纸约束数据;成型镜片获得模块12,所述成型镜片获得模块12用于对镜片毛坯进行成型处理,获得成型镜片;成型图像获得模块13,所述成型图像获得模块13用于通过图像采集装置进行所述成型镜片的图像采集,获得成型图像;尺寸测定模块14,所述尺寸测定模块14用于通过尺寸测定装置进行所述成型镜片的尺寸测定,生成尺寸测定结果;精磨参数获得模块15,所述精磨参数获得模块15用于根据所述尺寸测定结果和所述成型图像进行损伤分布评价,基于损伤分布评价结果和所述图纸约束数据生成精磨控制参数;精磨镜片获得模块16,所述精磨镜片获得模块16用于基于所述精磨控制参数进行所述成型镜片的精磨处理,获得精磨镜片;分布数据获得模块17,所述分布数据获得模块17用于通过所述图纸约束数据获得中心点定位参数,通过所述尺寸测定装置进行所述精磨镜片的尺寸测定,根据精磨尺寸测定结果和所述中心点定位参数生成抛光余量分布数据;抛光控制模块18,所述抛光控制模块18用于通过所述抛光余量分布数据进行所述精磨镜片的抛光控制。
35.进一步的,所述系统还包括:识别特征构建单元,所述识别特征构建单元用于构建缺陷识别特征集合;缺陷匹配单元,所述缺陷匹配单元用于通过所述缺陷识别特征集合进行所述成型图像的缺陷匹配,获得缺陷匹配结果;分布位置生成单元,所述分布位置生成单元用于根据所述缺陷匹配结果生成缺陷分布位置和缺陷深度参数;损伤分布评价单元,所述损伤分布评价单元用于根据所述尺寸测定结果、所述缺陷分布位置和所述缺陷深度参数进行损伤分布评价,获得所述损伤分布评价结果。
36.进一步的,所述系统还包括:去除量数据获得单元,所述去除量数据获得单元用于获得精磨设备的测试样品的样品去除量数据;历史去除量数据获得单元,所述历史去除量数据获得单元用于获得所述精磨设备的历史去除量数据,其中,所述历史去除量数据带有时间标识;权重约束单元,所述权重约束单元用于根据所述时间标识进行所述历史去除量数据的权重约束,根据权重约束结果生成精磨设备的精磨去除量数据;去除修正单元,所述去除修正单元用于根据所述样品去除量数据进行所述精磨去除量数据的去除修正,根据去除修正结果、所述损伤分布评价结果和所述图纸约束数据生成所述精磨控制参数。
37.进一步的,所述系统还包括:评价周期获得单元,所述评价周期获得单元用于获得所述精磨设备的预设评价周期;权重分布单元,所述权重分布单元用于通过所述预设评价周期进行所述历史去除量数据的权重分布,获得时间权重分布结果;权重约束单元,所述权重约束单元用于根据所述时间权重分布结果进行所述历史去除量数据的权重约束,获得权重约束结果。
38.进一步的,所述系统还包括:成型设置数据获得单元,所述成型设置数据获得单元用于获得成型处理的成型设置数据;控制评价数据获得单元,所述控制评价数据获得单元用于根据所述损伤分布评价结果和所述尺寸测定结果生成成型控制评价数据;控制偏离评价单元,所述控制偏离评价单元用于根据所述成型控制评价数据和所述成型设置数据进行成型控制偏离评价,生成偏离控制评价结果;控制优化单元,所述控制优化单元用于通过所述偏离控制评价结果进行后续成型处理的控制优化。
39.进一步的,所述系统还包括:抛光频次信息获得单元,所述抛光频次信息获得单元用于获得预设抛光频次信息;评价分布结果生成单元,所述评价分布结果生成单元用于根据所述预设抛光频次信息进行所述抛光余量分布数据的单次抛光量评价,生成单次抛光量评价分布结果;差值判断单元,所述差值判断单元用于判断所述单次抛光量评价分布结果中的抛光量差值是否存在不满足预设去除阈值的结果;抛光控制单元,所述抛光控制单元用于当存在时,则根据不满足预设去除阈值的结果的数量进行抛光频次新增,基于新增后的抛光频次和所述预设去除阈值进行抛光控制。
40.进一步的,所述系统还包括:平衡参数设定单元,所述平衡参数设定单元用于设定处理精度和处理成本的平衡参数;模型输出结果获得单元,所述模型输出结果获得单元用于将所述平衡参数、所述抛光余量分布数据输入抛光控制模型,获得模型输出结果,其中,所述模型输出结果包括抛光频次和抛光量数据;精磨抛光控制单元,所述精磨抛光控制单元用于基于所述模型输出结果进行所述精磨镜片的抛光控制。
41.本说明书中各个实施例采用递进的方式描述,每个实施例重点说明的都是与其他实施例的不同之处,前述图1实施例一中的一种提高光学玻璃镜片打磨精度的方法和具体实例同样适用于本实施例的一种提高光学玻璃镜片打磨精度的系统,通过前述对一种提高光学玻璃镜片打磨精度的方法的详细描述,本领域技术人员可以清楚的知道本实施例中一种提高光学玻璃镜片打磨精度的系统,所以为了说明书的简洁,在此不再详述。对于实施例
公开的装置而言,由于其与实施例公开的方法相对应,所以描述的比较简单,相关之处参见方法部分说明即可。
42.对所公开的实施例的上述说明,使本领域专业技术人员能够实现或使用本技术。对这些实施例的多种修改对本领域的专业技术人员来说将是显而易见的,本文中所定义的一般原理可以在不脱离本技术的精神或范围的情况下,在其它实施例中实现。因此,本技术将不会被限制于本文所示的这些实施例,而是要符合与本文所公开的原理和新颖特点相一致的最宽的范围。