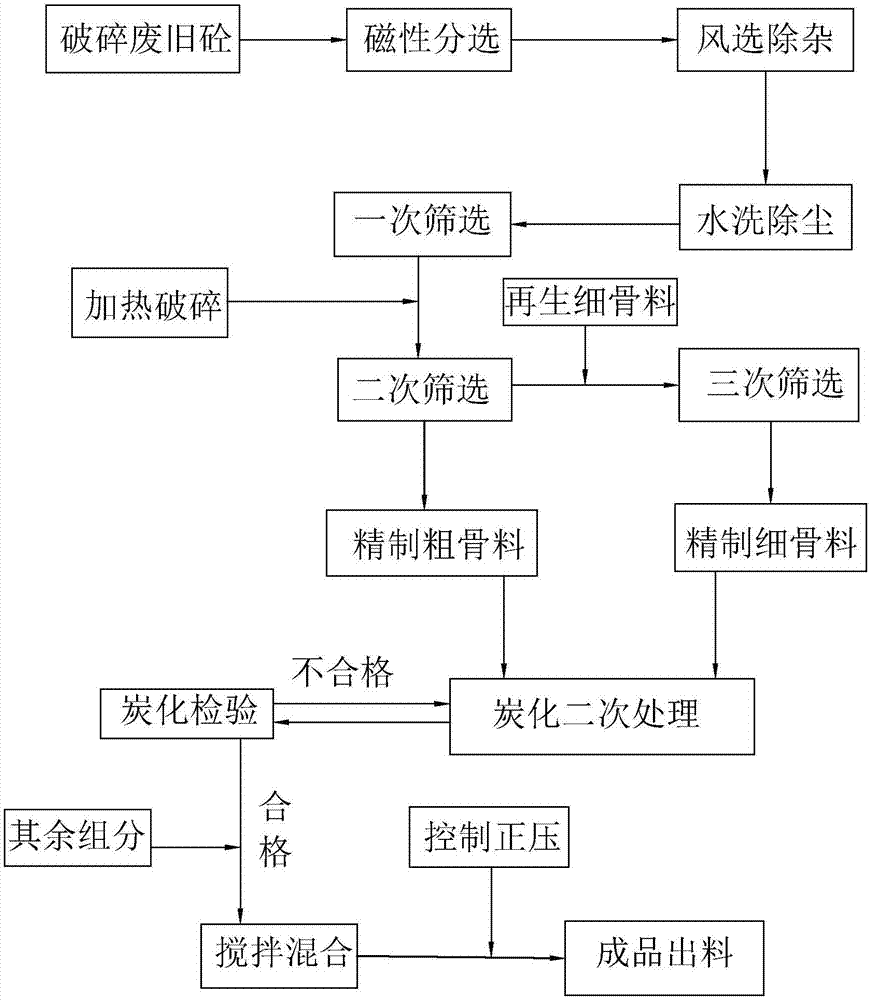
本发明涉及建筑材料生产
技术领域:
,特别涉及一种再生混凝土及其生产工艺。
背景技术:
混凝土是建筑工程中的重要材料,目前全世界的建筑材料中混凝土材料占70-80%,因此每年对于混凝土的需求和由于更替而产生的废旧混凝土数量十分可观。再生混凝土是将废旧混凝土建筑物经过破碎、筛分和清理后按一定比例相互配合后得到的骨料,再将骨料与其他建筑材料混合制得的混凝土,通过再生混凝土技术可实现对废旧混凝土的再加工和再利用,不仅既能使有限的资源得以再利用,又解决了部分环保的问题,因此,再生混凝土是非常制得推广的一项建筑材料生产技术。申请公布号为cn105254241a的中国专利文件中公开了一种提高再生混凝土抗渗性能的方法,首先采用粉煤灰和矿渣粉部分取代水泥,再限制再生混凝土的含量,并添加适量的外加剂改善性能,最后再制备成成品的混凝土。但是再生混凝土由于其自身骨料的原因,与原生骨料相比具有各个方面的缺点,由于再生混凝土内部的大孔隙,导致吸水率是原生混凝土的多倍,从而导致后期的干缩性及徐变的程度也相对较高,因此产生较多的裂缝,不仅影响抗渗性,也会影响强度和整体使用寿命。技术实现要素:针对现有技术存在的不足,本发明的目的在于提供一种再生混凝土的制作工艺,具有减少后期干缩性和徐变的效果,减少裂缝的数量和发育程度,增强结构强度和使用寿命。本发明的上述技术目的是通过以下技术方案得以实现的:一种再生混凝土制作工艺,包括如下步骤:s1,制备再生骨料,将废旧混凝土破碎、一次筛分、清洗,得到再生粗骨料和再生细骨料;s2,再生骨料预处理,将经过s1处理得到的再生粗骨料和再生细骨料加热至300-400℃,再次进行破碎,并在破碎后进行二次筛分得到精制粗骨料和再生细骨料;s3,再生骨料二次处理,将经过s1和s2处理得到的精制粗骨料和再生细骨料放置于密闭容器中炭化,控制相对湿度为40-85%、co2浓度为30-75%,直至未炭化的再生骨料重量≤5%;s4,制备再生混凝土,将经过s3处理的再生骨料与原生骨料、胶黏材料、填充料、外加剂搅拌混合,制得成品。通过采用上述技术方案,对于废旧混凝土多层次的处理,得到较为合格的再生骨料,且力学性能也大为提高,同时经过炭化后具备缓释二氧化碳的效果,二氧化碳与混凝土中特别是再生骨料中的氢氧化钙发生化学反应生成碳酸钙,而碳酸钙的生成会伴随体积变大的变化,从而进一步的改善混凝土内部的孔隙结构,使得混凝土整体更加密实,能够减缓后期的干缩和徐变,提高再生混凝土的受力和抗渗以及使用寿命。本发明的进一步设置为:s1中对废旧混凝土进行破碎后,将破碎的混凝土块经过磁选筛分,除去含有的金属杂质。通过采用上述技术方案,破碎废旧混凝土时,会掺入大量的金属或铁锈,因此通过磁选后能够提高再生骨料的力学性能。本发明的进一步设置为:进行一次筛分后,得到的再生粗骨料粒径为5-40mm,再生细骨料粒径小于5mm;s2中经过二次筛分后得到的精制粗骨料粒径为5-20mm,再生细骨料粒径小于5mm,再对再生细骨料进行三次分筛,得到粒径为0.15-5mm的精制细骨料。通过采用上述技术方案,设置多层筛分,将再生骨料细分成精制粗骨料和精制细骨料,更加符合配制混凝土时的级配要求,同时在筛分过程中也进一步的除去杂质,提高再生骨料的纯净度。本发明的进一步设置为:s3中再生骨料二次处理炭化完成后,取部分再生骨料研磨成粉均匀铺开,均匀喷涂酚酞指示剂,观察是否出现红色,若红色部分体积大于5%,则将再生骨料重新进行炭化,直至未炭化的再生骨料重量≤5%。通过采用上述技术方案,能够准确的知道再生骨料的炭化是否达到要求。本发明的进一步设置为,制备的再生混凝土包括如下重量份数的组分:原生骨料965-1328份;精制粗骨料331-528份;精制细骨料268-488份;水泥566-720份;粉煤灰231-322份;高炉矿渣118-266份;减水剂25-55份;水221-308份;孔隙调节剂18-45份。本发明的进一步设置为:所述减水剂由重量比为1:1.5-3.5的亚甲基二甲基二萘磺酸钠聚合物和β基萘磺酸盐甲醛缩合物组成;所述空隙调节剂包括重量比为1:0.5-0.8的能够释放二氧化碳的缓释剂和膨胀剂。通过采用上述技术方案,减水剂中的亚甲基二甲基二萘磺酸钠聚合物能够降低水泥水化热峰值,对水泥颗粒有分散作用,能改善其工作性,减少单位用水量,从而减少混凝土中水分后期蒸发形成的孔隙量,降低孔隙比,进一步提高了混凝土的抗渗性能;而β基萘磺酸盐甲醛缩合物属于非引气型减水剂,降低水灰比的同时,也能够改善混净土的流动性;而缓释剂的设置使得其能够缓释出二氧化碳,二氧化碳与混凝土中特别是再生骨料中的氢氧化钙发生化学反应生成碳酸钙,而碳酸钙的生成会伴随体积变大的变化,从而进一步的改善混凝土内部的孔隙结构,使得混凝土整体更加密实,也提高混凝土成品的受力强度和耐久性,即加强了再生混凝土构件的性能和质量;最后,膨胀剂的设置一方面调节水泥水化热变化及干缩时产生的应变,另一方面也进一步的可以改善混凝土内部的孔隙结构,加强再生混凝土的受力强度和使用寿命。本发明的进一步设置为:所述缓释剂为经过二氧化碳浸没处理的铝硅酸盐。通过采用上述技术方案,铝硅酸盐是硅酸盐中的sio4四面体的一部分由alo4四面体取代组成的,如正长石、钙长石等,其中的钙长石分子式为caal2sio8,一半是alo4四面体,另一半是sio4四面体。正是由于上述的分子结构,使得其具有优良的吸附作用,可以吸附大量的气体,因此可以作为优异的二氧化碳载体。本发明的进一步设置为:所述膨胀剂包括氧化钙、硫铝酸钙和氧化镁,且氧化钙、硫铝酸钙和氧化镁之间的重量比为2-3:1:1。通过采用上述技术方案,氧化钙膨胀能高,膨胀爆发力强,早期膨胀量大,而混凝土构件早期因为水泥水化热带来大量热量从而产生大量温度应力,通过氧化钙能够抵消早期的大部分内部应力,减少裂缝的产生;硫铝酸钙具有膨胀缓和,作用周期较长,可以适用于混凝土构件中期的裂缝发育,能够有效抑制特别是伸缩应力引起的裂缝的发育,加强混凝土内部的密实度,进一步加强防水性能;氧化镁的水化反应和膨胀效应出现的时间较长,一般需要一段时间以后才能体现其膨胀的作用,因此可以用于对由于建筑物内外部温度变化而引起的收缩裂缝以及混凝土构件本身徐变而引起的裂缝的抑制和阻塞作用,因此通过上述三种膨胀源的组合能够在混凝土构件的全生命周期中提供稳定的消除内部各种形变应力的膨胀力,尽可能的减少混凝土构件中裂缝的产生,极大的提升了混凝土构件的抗渗能力。而且,设置上述三种膨胀剂的合理配比,能够与再生混凝土后期的徐变及干缩相匹配,尽量减少后期产生的形变或裂缝,延长混凝土的使用寿命。本发明的进一步设置为:还包括引气剂,所述引气剂为重量份数为43-66份的差皂素。通过采用上述技术方案,差皂素能够在混凝土搅拌的过程中引入大量均匀、稳定而封闭的微小气泡,微小的气泡增加了浆体体积且如滚珠一样对拌合料产生润滑的作用,同时这些微小气泡也改变了混凝土内部的孔隙结构,封闭了大量的毛细孔通道,进一步的提升混凝土的抗渗性。本发明的进一步设置为:s4中进行搅拌时,先将精制粗骨料、精制细骨料、水泥和水进行混合并搅拌,搅拌均匀后再加入剩余组分并维持各组分混合时均处于正压环境中。通过采用上述技术方案,先将精制粗骨料、精制细骨料、水泥和水进行混合并搅拌,使得水泥先将再生骨料包裹完全,进而能够填补一部分再生骨料外部的孔隙,同时也减缓再生骨料内部二氧化碳的逸出速度,从而逸出的二氧化碳更多的能够与混凝土后期的徐变相适应,而同样的设置搅拌时为正压,也能够减缓再生骨料和缓释剂中其他的逸出。综上所述,本发明具有以下有益效果:对于再生骨料原料的处理,层层筛分多次除杂,达到精细化高标准的效果,增强再生骨料原料的力学性能;再设置将再生骨料炭化的过程以及添加的缓释剂,进一步的改善了再生混凝土的内部孔隙结构,减少后期裂缝的发育,提升整体强度和抗渗能力,延长使用寿命。附图说明图1为本发明的流程示意图。具体实施方式实施例1-5,一种再生混凝土,包含的组分及对应的含量如表1所示。其中,水泥为强度等级为32.5的普通硅酸盐水泥;精制粗骨料的粒径为5-20mm,精制细骨料粒径为1.5-4mm;减水剂由重量比为1:3的亚甲基二甲基二萘磺酸钠聚合物和β基萘磺酸盐甲醛缩合物组成;空隙调节剂包括重量比为1:0.5的缓释剂和膨胀剂,缓释剂为经过二氧化碳浸没处理过的铝硅酸盐,膨胀剂由重量比为3:1:1的氧化钙、硫铝酸钙和氧化镁组成。表1实施例1-5中各组分及其对应含量表(kg)实施例6,一种再生混凝土,与实施例1的区别在于,不含有差皂素。实施例7,一种再生混凝土的生产工艺,含有的组分及对应的含量参照实施例1,包含的步骤如下:s1,制备再生骨料,将废旧混凝土块破碎,除去钢筋并筛分,得到再生骨料,将再生骨料依次经过磁性分选除去金属杂质及铁锈、风选除杂减少树叶植物和水洗除尘洗去泥土,得到合格的再生骨料,此时进行一次筛分,得到再生粗骨料和再生细骨料,且再生粗骨料粒径为5-40mm,再生细骨料粒径小于5mm;s2,再生骨料预处理,将经过s1处理得到的再生粗骨料和再生细骨料加热至300℃,再次进行破碎,并在破碎后进行二次筛分得到精制粗骨料和再生细骨料,精制粗骨料粒径为5-20mm,再生细骨料粒径小于5mm,同时对再生细骨料也进行第三次筛分,得到精制细骨料,精制细骨料的粒径为0.15-5mm;s3,再生骨料二次处理,将经过s1和s2处理得到的再生骨料放置于密闭容器中炭化,控制相对湿度为85%、co2浓度为75%,直至未炭化的再生骨料重量≤5%,再生骨料二次处理炭化完成后,取部分再生骨料研磨成粉均匀铺开,均匀喷涂酚酞指示剂,观察是否出现红色,若红色部分体积大于5%,则将再生骨料重新进行炭化,直至未炭化的再生骨料重量≤5%;s4,再生混凝土的制备,将经过s3处理后的再生骨料与其他各组分加入搅拌釜中,混合并搅拌均匀,且保持搅拌釜中气压为1.2-1.5mpa,从而尽量保持铝硅酸盐和再生骨料中的二氧化碳在搅拌过程中较少的逸出,减缓再生混凝土中二氧化碳逸出的速度。实施例8,一种再生混凝土的生产工艺,与实施例7的区别在于,s3中进行炭化时,控制相对湿度为55%、co2浓度为45%。对比例1-7,一种再生混凝土,与实施例1的区别在于,包含的组分及对应的含量如表2所示,其中水泥为强度等级为32.5的普通硅酸盐水泥;精制粗骨料的粒径为5-20mm,精制细骨料的粒径为1.5-5mm;减水剂由重量比为1:3的亚甲基二甲基二萘磺酸钠聚合物和β基萘磺酸盐甲醛缩合物组成;空隙调节剂包括重量比为1:0.5的缓释剂和膨胀剂,缓释剂为经过二氧化碳浸没处理过的铝硅酸盐,膨胀剂由重量比为3:1:1的氧化钙、硫铝酸钙和氧化镁组成。表2对比例1-7中各组分及其对应含量表(kg)对比例8,一种再生混凝土的生产方法,与实施例7的区别在于:破碎得到的再生骨料未经过s3中预处理直接制备得到再生混凝土。对比例9,一种再生混凝土的生产方法,与实施例7的区别在于:进行s4中搅拌时,搅拌釜中为常压。表征实验实验1、抗压强度实验实验对象:实施例1-7、对比例1-9中各组分制备得到的混凝土产品,制备成标准尺寸10cm*10cm*10cm的块状,分别测试7天和28天的抗压强度。实验结果:记录入表3中。表3抗压强度表(mpa)组7天28天组7天28天实施例125.336.4对比例221.026.5实施例226.434.5对比例325.627.3实施例324.935.2对比例423.227.5实施例427.136.6对比例519.324.4实施例526.435.6对比例620.625.1实施例624.735.5对比例719.524.2实施例728.836.5对比例822.425.3对比例122.428.3对比例924.628.9实验2、抗渗性实验实验对象:实施例1-7、对比例1-9中各组分制备得到的混凝土产品,制备成标准尺寸10cm*10cm*10cm的块状试件,每组制备6个试件。实验内容:清理试件表面达到清洁后,在试件侧面滚涂一层熔化的密封材料,并装入抗渗仪中按照标准抗渗试验。试验时,水压从0.2mpa开始,每隔2h增加0.025mpa水压并随时记录试块端面渗水情况,一直加到6个试块中有3个试块表面发现渗水,记下此时的水压力即为当前试件组的抗渗等级。实验结果:记录入表4中。表4抗渗水压力汇总表(mpa)当前第1页12